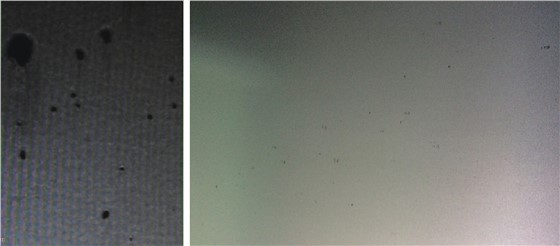
-
首钢京唐钢铁联合有限责任公司,河北 唐山 063200
漏镀缺陷是连续热镀锌产线产品的严重缺陷,直接造成产品质量降级,客户无法使用。造成漏镀缺陷的成因较多,其中最重要的成因是锌锅温度偏低和锌液Si含量偏高,其次是基板清洗不彻底或板面元素含量超标[1-2]。本文分析了一种少见的退火炉润滑成因造成漏镀的情况,以2#镀锌机组发现带钢上表面断续漏镀缺陷为例,对油脂加注的作业方法、影响及操作标准、造成漏镀的成因进行进一步讨论,提出了改进措施和控制方法。
1. 漏镀缺陷发生情况
缺陷分布与钢种、规格及带钢的位置无关,主要出现在带钢上表面,操作侧和驱动侧也有分布,无方向,与非漏镀位置界限明显,呈现团簇状和分散分布的特征(图1)。
2. 缺陷成因分析
2.1 基板质量
对缺陷位置进行酸洗,发现原料钢板未见明显硌伤、翘皮等对应性缺陷,说明基板质量较好(图2)。
2.2 炉区气氛
分析退火炉内生产气氛,炉内均热段、加热段、快冷段和缓冷段氧质量分数均控制在10×10−6以下,各段露点亦保持在−20 ℃以下,未见明显的氧含量波动。
2.3 缺陷成分
对缺陷位置进行能谱分析,从检验结果来看,缺陷位置主要是Fe和C元素,由此确定此缺陷为漏镀缺陷。
对镀前通道线进行排查未发现异常,结合电镜分析结果,敲击加热段入口炉壁以及炉辊,敲击过程漏镀缺陷明显增多,敲击后缺陷呈减少趋势,遂锁定漏镀为加热段入口防辐射屏积碳所致。每敲击一次能保证5卷质量正常,通过4轮敲击后带钢漏镀频次逐渐增多,无法稳定运行超过6 h,为减少批量质量问题,需进行停车开炉检查。
如图3所示,开炉后发现炉辊附近积碳严重,辐射屏、喇叭口、此辊对应位置的炉壁和炉底盖等位置均存在不同程度的积碳。检查11#辊之后的辊子及炉壁,未发现异常。加之后续检查确认炉内其他各段均正常,由此判断问题主要出在5#、7#、9#辊处,判断此处炉辊油封出现问题,导致润滑油流入炉内。对炉内取样的碳粉检验,主要成分为碳,进一步验证了漏镀缺陷成因,见图4和表1。
3. 成因分析
炉辊轴承座内部润滑油脂渗入炉辊膨胀节、部分润滑油被炉墙保温棉吸收,在炉内高温的作用下,润滑油汽化后融入炉内氮氢混合气。正常生产状态下,炉底的气体从出口向入口方向流动,在温度相对较低的预热段和加热段交接部位形成积碳,附着在防辐射屏上,积碳聚积到一定程度掉落在带钢上造成漏镀缺陷[3-5]。
炉辊轴承座油镜1/2处为运行低液位,如果油位超过油镜上限,密封唇口与辊轴接触部位出现密封不严现象,润滑油可以进入膨胀节,与炉内高温气体直接接触。轴承座结构如图5所示。部分轴承座加油位超过油镜上沿,造成油位超标,是润滑油进入炉内主要原因。
4. 结束语
(1)点检发现个别轴承座油位降低,采用临时补油的措施,未将油位异常的轴承座纳入隐患管理并利用检修进行排查,是造成润滑油进入炉内的管理原因。(2)原有的给油脂表中“油位不低于油镜中位”不具备可执行性,该措施的执行效果无法验证,是造成该缺陷的根本原因。采用有刻度的加油器进行加油并明确加油量上下限,可以有效提高加油精度,避免溢油造成漏镀的问题。措施执行后漏镀缺陷消失,因而固化到操作规程中。
来源:金属世界