摘 要:探讨了在金属材料韧脆转变温度检测过程中遇到的一些问题及解决方法.结果表明:试验数据处理时采用不同的函数拟合会对最终检测结果产生较大影响,Boltzmann函数的拟合结果更贴合实际;判定韧脆转变温度的4种方法各有特点,在检测时应根据实际情况灵活运用;试样晶状区域轮廓、断口平整度特别是韧脆断面类型会直接影响剪切断面率的评价,另在检测报告中还应注明取样位置和方向;在试样数量受限的情况下,应将试样尽量分配在靠近30%~70%剪切断面率的区间来获取韧脆转变温度.
关键词:韧脆转变温度;剪切断面率;冲击吸收能量;侧膨胀值;拟合函数;断口形貌
中图分类号:TG115.5+6 文献标志码:A 文章编号:1001G4012(2017)06G0422G06
工程 应 用 领 域 中,金 属 材 料 的 韧 脆 转 变 温 度(DuctileGBrittelTransitionTemperature,DBTT),作为衡量金属材料低温特性的主要性能参数之一,能够比较真实地反映出材料在不同温度下的断裂形式,从而可对一些工件在低温环境下的服役能力和事故风险作出预先评估.金属材料韧脆转变温度检测试验看似简单,但实际检测过程中却会出现很多状况,其中包含了诸多需要关注的细节和尚待思考的问题.为此,笔者从检测工作不断完善和规范化的角度,结合自身实际工作中遇到的一些关键问题进行探讨和分析,以供相关人员参考.
1 拟合函数的选择
众所周知,冲击吸收能量与试验温度存在一定的函数关系,通常可以用连续单点拟合的方式获得DBTT 曲线.试验数据的曲线拟合是材料韧脆转变温度检测中至关重要的一环,直接关系到最终特征点的选 取,然 而 BSENIOS148G1:2016[1],GB/T229-2007[2],ASTM E23-16b[3]中均未对此作出明确规定,只是均以资料性附的形式给出了冲击吸收能量和温度(KGT)曲线示意图,并附上了“用以确定转变温度的方法应在相关产品标准中规定,或通过协议规定”的说明,仅是对 DBTT 的4种规定方法选择的说明,即冲击吸收能量具体值、冲击吸收能量百分比、剪切断面率百分比和侧膨胀值具体值.笔者认为,无论选用哪种方法,出于严谨和规范化要求的考虑,都应当先利用函数对试验数据进行拟合,因此有必要研究不同的拟合函数对 KGT 曲线最终的走 势 以 及 特 征 点 选 取 的 影 响. 为 此,对 一 组34CrNiMo6合金钢的系列温度冲击试验结果(表1)分别选用Boltzmann,Weibull,Gompertz,Richards等4种具有S形增长模型的回归函数进行拟合,所得曲线如图1所示,以50%剪切断面率对应的温度表示的韧脆转变温度T50%FAT测试结果见表2.
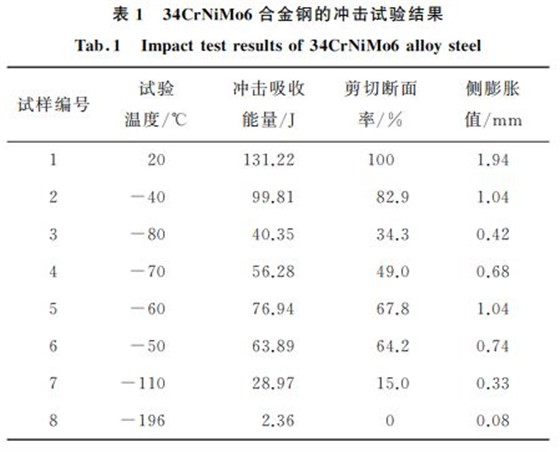
由上述结果可以看出,前3种函数拟合的结果基本一致,但经 Richards函数拟合后的曲线与实际情况严重不符.通常来讲,在数据点分散不严重的情况下,利 用 Boltzmann,Weibull,Gompertz函 数拟合都可以得到相对可靠的试验结果.采用不同的函数拟合得到的试验结果肯定会存在一定差异,但目前业内人士普遍认为采用Boltzmann函数拟合的曲线具有更高的相关系数,在数据点分散性较大的情况下依然可以较好地拟合出曲线,同时其拟合曲线的上、下平台以及转折点物理意义相对更为明确.另外,Boltzmann函数对各类不同变化趋势的曲线都能进行较好地拟合,如图2所示.
Boltzman函数表达式为A =A1 -A21+e(T-T0)/dT +A2 (1)式中:A 为剪切断面率;A1,A2 为待定系数;T 为温度;T0 为拐点温度.由式(1)可见:当 T 趋于+∞时,A 趋于 A2,因此A2 可以作为韧脆转变曲线的上平台;当 T 趋于-∞时,A 趋于A1,A1 可以作为韧脆转变曲线的下平台;而(T-T0)/dT反映出的是曲线过渡区域的变化趋势,dT 可以表示材料在塑性和韧性之间随温度变化的难易程度,dT 越小,则表示塑性区更易向脆性区转变,T0 对应曲线的拐点,当拟合后的曲线上、下平台明显且过渡区域分布较均匀的情况下,该值非常接近50%剪切断面率对应的实际温度,此时可直接选用T0 值作为T50%FAT.因此,目前有不少学者建议将Boltzmann函数纳入冲击试验标准中作为数据处理的统一手段,以此增加数据之间的可比性.
2 判定方法的选择
韧脆转变温度曲线陡峭上升的区域覆盖的温度范围较宽,标准中列出了4种方法来规范转变温度特征点选取的问题,分别是:冲击吸收能量达到某一特征值;冲击吸收能量达到上平台能量某一百分数;切断面率达到某一百分数;侧膨胀值达到某一个量.笔者针对各个判定方法,采用 Boltzmann函数进行曲线拟合,为避免过多地引入人为不确定因素,“冲击吸收能量达到某一特征值”和“侧膨胀值达到某一个量”的规定方法暂不作讨论,可根据材料实际情况由经验确定.
表4给出的是以“冲击吸收能量达到上平台能量50%”作以判据对应的韧脆转变温度T50%ET.利用冲击吸收能量G温度曲线拟合来获得转变温度时,建议将上平台冲击吸收能量的50%作为衡量依据,可以
较为实际地反映出材料的韧脆转变特性,但需注意的是,试样冲击吸收能量在达到上平台后,随着温度的升高还会有一定的上浮空间,为过渡性转折,所以试验过程中上平台数据点的选取有一定的讲究,理论上应将冲击吸收能量G温度曲线上刚好达到100%剪切断面率时所对应的冲击吸收能量作为上平台能量,以此值的50%作为基准来确定 T50%ET 更贴合实际,否则选择更高的上平台点会直接导致T50%ET的升高.因各组试验数据取自工件的不同部位,笔者认为单纯依照某个指定的侧膨胀值来统一衡量韧脆转变温度是不合适的.因此,表5是在参照T50%FAT和T50%ET的基础上,基于各测试位置的侧膨胀值G温度曲线以“侧膨胀值达到上平台侧膨胀值50%”作以判据对应的韧脆转变温度 T50%LE,同样侧膨胀值在上平台区域随着温度的升高还有一定的上浮趋势,试验过程中也可以适当参考冲击吸收能量的稳定程度来确定上平台侧膨胀值.由上述3种不同判定方法得到的韧脆转变温度可以看出,在统一采用 Boltzmann函数进行曲线拟合的情况下,不同的判定方法得出的结果还是有所差异的,偏差范围基本在10 ℃之内,个别也有相差近20 ℃的情况,例如1号试样的 B位置,T50%FAT与T50%LE 相 差 20 ℃. 暂 且 抛 开 人 为 引 入 的 误 差,表3~5的试验结果在一定程度上说明由不同判定方法确定得到的试验结果在总体上还是可以互相参考比较的,这从另一方面也论证了冲击吸收能量G剪切断面率G侧膨胀值之间的内在联系.笔者认为,虽然不能断言利用哪一种判定方法得到的试验结果更好,但可以肯定的是,3种方法各有优势,在特殊情况下可以灵活选用,例如碰到混合断面材料时,通过T50%FAT的判定方法来确定韧脆转变温度就行不通,那么在供 需 双 方 均 认 可 的 前 提 下,可 以 考 虑 使 用T50%ET甚至T50%LE作为判据来确定韧脆转变温度.
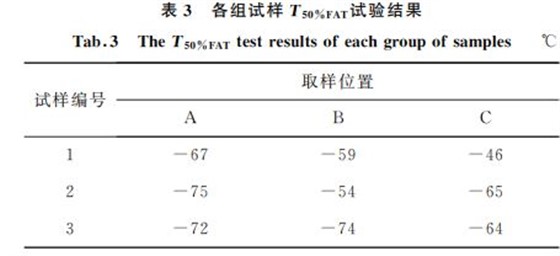
3 材料断面情况的影响
理想情况下,针对某一材料能以T50%FAT作为判据来测定其韧脆转变温度的前提是,冲断后的试样韧性区域和脆性区域特征明显、轮廓规则且分界清晰,然而实际工作中很难碰到完全符合这些条件的情形.因此,在这些不利条件的影响下,如何尽可能地提高T50%FAT检测的精度具有重要意义.
3.1 断面类型
一些低合金高强度结构钢的冲击试样断口形貌呈混合型,即韧性和脆性没有明确的边界区分,甚至韧性和脆性以混合形态存在,这就导致无法直接通过手工测量或者肉眼目测的方式来获得剪切断面率,ASTM E23-16b 中 也 特 意 强 调 了 SAE4340(对应国内牌号 4CrNiMoA)钢对此方法不适用.在该种情况下,可以采用仪器化冲击方法来获取该类材料在不同温度下的力G位移曲线,经后续处理拾取特征点来获得不稳定裂纹扩展的起始和终止阶段,然后计算得到不稳定裂纹扩展吸收能量及剪切断面率,从而解决混合型断面材料无法通过剪切断面率评价的方式获得韧脆转变温度的问题,国内已有部分学者开展了该方面的研究工作,笔者在后续的工作中也会对此进行进一步的探讨.通常情况下典型的(韧脆区域分明)及混合型的冲击断口形貌如图3所示.
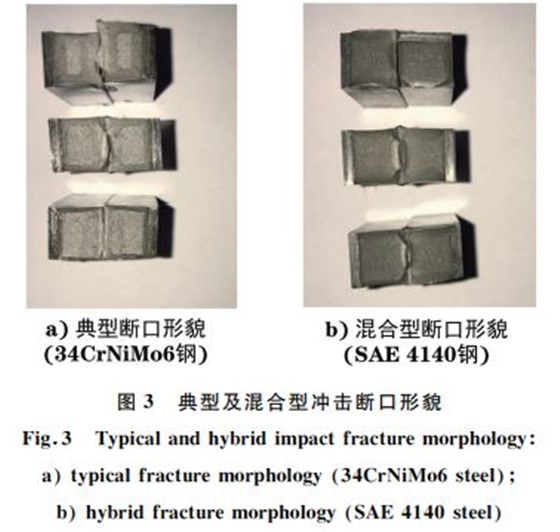
3.2 断面轮廓形状
不同材料试样冲击断裂后,晶状区域的轮廓不全相同,有长条形的、四方形的、梯形的,甚至有分段的、不规则的等.针对规则形状,可以采用最接近的数学求积公式来近似求得其面积;如果是分段型的,则只能通过将各个分散的区域单独计算然后相加的方法求得,但导致的问题是,各微小区域的面积计算与实际情况的误差如何缩小? 凭借肉眼直接去“估算”的度如何把握? 近些年来,国内外一些知名试验机厂商已将微机自动压痕测量系统集成到了布氏硬度计上,可以更加便捷地得到材料的硬度.笔者认为可以尝试将技术运用至冲击试样断面形貌的尺寸测量上,从而推动材料韧脆转变性能评价的自动化测试进程.当然,压痕自动测量系统能够准确完成测量的前提条件是压痕边界清晰,压痕与周边的色差明显,这对于对表面粗糙度有固定要求的硬度试样相对而言比较容易满足,但将其运用至评价冲击试样的自然断口形貌时,情况则比较复杂,需要克服断口表面不平整导致的对焦问题,形状不规则导致的面积积分问题,韧脆区域色差不明显导致的边界判定等问题.
3.3 断面平整度
部分试样冲击断裂后的断面未必是平整的表面,有可能是台阶状的,甚至出现中间脆性区域横跨两个以上台阶的情形.这种情况下就不能直观地利用量具去手工测量了,笔者建议对断面进行拍摄投处理,利用计算机辅助工具计算其剪切断面率.
4 取样位置及方向的影响
4.1 取样位置
同样,采 用 上 述 试 验 结 果,3 件 工 件 A,B,C3个位置获得的共计9组试验数据拟合后得到的剪切断面率 G温度曲线及韧脆转变温度 T50%FAT 如图4所示.
结合表1的试验结果可以看出,不同取样位置的T50%FAT相差还是比较明显的,整体来看,由 A 位置经 B位置再到 C位置,其韧脆转变温度呈升高的趋势,即工件表面的韧脆转变温度要低于内部的,相对而言其韧性更好,这是由于零件在热处理工艺过程中各部位承受条件不均匀导致的.试样的取样位置会直接影响力学性能的试验结果,在冲击试验中尤为明显.若是较大的构件,应当凭借经验考虑到热处理工艺不均匀性导致的各部位性能的差异,单套T50%FAT的检测必须限制在“一定区域”内,并且只能用来评价这一区域的韧脆转变性能,而不能代表整个工件的,而这个“一定区域”,必须人为地把关,需要 双 方 遵 循 相 应 的 取 样 标 准,如 GB/T2975-1998«钢及钢产品 力学性能试验取样位置及试样制备»,也可以依照双方的协议要求或者通过相关的经验判断等手段,其目的都是为了获得工件稳定真实的韧脆转变性能.
4.2 取样方向
取样方向 的 选 择 也 是 较 为 重 要 的 一 环,板 材轧制过程中会产生织构、表层受力、晶粒流动等现象,使一些中 厚 板 横 向 和 纵 向 的 性 能 差 异 非 常 明显,甚至断口类型完全不一样.如图5a)和图5b)所示分别为 SAE4140 合 金 钢(正 火 + 调 质 处 理)纵向和横向试样在-30 ℃冲击试验后断口的宏观形貌,可以看 出 横 向 与 纵 向 试 样 的 冲 击 断 口 形 貌存在明显的 差 异,纵 向 断 口 呈 灰 暗 的 韧 脆 混 合 断裂特征,而横 向 断 口 则 呈 现 出 明 显 的 亮 白 色 脆 性断裂特征,且具有一定的方向性,虽韧脆区域差别明显,但分界处形状极不规则,给剪切断面率的评价带来一定困难.因此,建议在 T50%FAT 检测报告中注明取样方向.
5 其他问题
5.1 数值修约问题
GB/T229-2007基本照搬了BSENISO148G1:2006的内容,与 ASTM E23-16b一样,3者都未对报告中剪切断面率的数值修约情况进行规范,但在各自 的 附 录 中 都 以 表 格 的 形 式 呈 现 了 1% ~100%剪切断面率的计算对照方法,并为肉眼估量的方法提供了“断口形貌和剪切断面率对照表”及“估计断口形貌用指南”,该“指南”中基本以10%的区间为分隔进行评价,摆动幅度较大,这就要求检测人员在分析判断韧脆区域面积的时候十分小心,因为标准中的对照表只针对试样断面脆性区域呈矩形状的理想情况,其他形状的试样则需要结合自身的判断和相关的检测工作经验进行判断.笔者建议检测报告中应当将剪切断面率的数值修约分为两种情况:经量具 测 量 后 计 算 得 到 的 数 值 结 果 应 精 确 到1%;而试验过程中以肉眼对照评价所得的试验结果应尽量精确到5%.这为 T50%FAT 检测过程中复杂的断面形貌剪切断面率计算问题提供了规范化要求,特别是在剪切断面率G温度曲线的过渡区域,肉眼估算的准确性会直接影响剪切断面率G温度曲线的走势及最终试验结果与实际相符合的程度.
5.2 试样分配问题
在评价材料韧脆转变温度的过程中,如果需要了解该材料在各个温度区间的韧脆特性,就必须对剪切断面率G温度曲线的上、下平台及过渡区域不断地补充完善,得出的试验曲线才可以准确地反映出材料剪切断面率随温度的变化趋势,并可以通过拟合曲线获得任一温度下剪切断面率,这样做的目的是要获取一条完整的剪切断面率G温度曲线.但如果只是要检测 T50%FAT,即韧脆区域各占50%的转变温度,可以根据实际情况进行处理.如果试件有条件允许取出足够多的试样,则可以按照上述方法完善整条曲线得出试验结果,尽量减少分散性带来的不利影响.如果试件本身尺寸有限,或者形状不规则,可以判断热处理工艺会带来性能不均匀的情况下,能够取出的试样本身就非常有限,在这种情况 下,应 当 遵 循 的 原 则 是:首 先 尽 可 能 地 满 足40%~60%剪切断面率过渡区域的试样分配,其次是20%~40%和60%~80%的转折区域,最后才是曲线的上、下平台.试样数量有限的情况下,要获取T50%FAT可以将试样尽量地分配在靠近30%~70%剪切断面率的区间,一味地追求剪切断面率G温度曲线的对称及趋势的平滑、美观是不合理的,材料在高、低温区域的韧脆变化趋势很有可能是不一样的,甚至会有较大的差别,且试样数量也经常会受限制,
最终实际获得的曲线不一定美观,问题的关键是检测目的.依据上述方法获得的T50%FAT,即使最终拟合出的曲线是非常“难看”的,但是它能够在有限的试验条件下得出尽可能贴近实际的结果.
5.3 组织变化问题
理论上讲,只要金属材料内部组织保持稳定,其对应的韧脆转变温度就应该是恒定的,但实际情况下,材料所处环境温度的变化,有可能会引起材料内部组织的变化,导致材料本身的特性发生改变.例如一些马氏体钢,淬火过程中转变不完全是马氏体相变的主要特点,导致金属材料在室温下仍会保留部分残余奥氏体,经低温条件下的保温处理后,这些残余奥氏体会转变成更稳定的马氏体[5],导致材料力学性能发生改变,类似于工业生产中的“深冷处理”.该因素或许影响有限,但在检测时也需要注意,这也是除了试样加工精度、性能不均匀、人为引入误差等因素外导致转变曲线上出现分散带的另一个原因.
6 结论
(1)在进行金属材料韧脆转变温度检测时,选用不同的拟合函数会影响最终的特征点选取,普遍认为选用Boltzmann函数能够更好地对各类曲线进行拟合,且物理意义更明确,选取的特征点也更贴合实际.
(2)选用不同的判定方法对最终测得的韧脆转变温度有一定的影响,但每种判定方法各有优势,在检测时可根据实际情况合理选取.
(3)冲击试样的断口形貌即断面类型、断面轮廓、断面平整度对韧脆区域所占比例的判定有较大影响,如何解决复杂断口剪切断面率的评价问题需要一个不断积累和完善的过程.
(4)冲击试样的取样位置和取样方向也是影响韧脆转变温度检测结果的不可忽视的一个重要因素,对于某些材料(诸如 SAE4140,4340合金钢一类的混合型断面材料),不同的取样方向得到的冲击断面类型截然不同.
(5)建议在对剪切断面率进行数值修约时按照以下间隔进行修约:利用肉眼对照评价时应尽量精确至5%,而手工测量计算时应修约至1%.
(6)在试样数量受限、单纯获取T50%FAT 的情况下,可以将试样尽量地分配在靠近30%~70%剪切断面率的区间内,不必刻意追求转变曲线的平滑及对称性.
场中1mm2 面积内的晶粒数等于 NAE 的15.5倍,那么 NAE为7.0,再根据式(2),可以计算出该试样的晶粒级别指数G=3.8.试验用铝合金试样晶粒级别指数,采用标准推荐的截距法的计算结果为G=3.8±0.5.通过比较可见,采用平面晶粒计算法使用iTEM 软件计算的结果,与该试样的标准值符合良好.
3 结论
铝合金晶粒级别指数的测定,无论是采用比较法、平面晶粒计算法,还是截距法,都需要考虑到真实倍率的问题.比较法需要与标准图片进行对比,结果只能保留整数,不确定度较大.后两种方法需要在显微镜的毛玻璃片上划圆或直线,操作起来不方便,而且当晶粒级别指数较大时,晶粒数过多会造成计数的极度不便,甚至错误.iTEM 软件具备强大的测量功能,可以很方便地计数.无论金相图片的实际倍率是多少,都能通过改变标尺的名义尺寸,使图片在名义上处于100倍,然后直接根据晶粒级别指数的定义公式,无需对比和查阅标准中的表格数据,就能获取到准确、可靠的晶粒级别指数测定结果.
文章来源:材料与测试网