分享:轧制态Mg-xZn-0.5Er合金板材组织及室温成形性能
娄峰1, 刘轲,1, 刘金学2, 董含武3, 李淑波1, 杜文博1
1.
2.
3.
研究了Mg-xZn-0.5Er (x = 0.5、2.0、3.0、4.0,质量分数,%)合金板材在轧制过程中微观组织及织构的演变规律,并探讨了织构及第二相对合金室温成形性能的影响规律。结果表明,随着Zn含量的增加,合金提前发生了完全动态再结晶,在后续轧制过程中细小的动态再结晶晶粒长大并在应力的作用下被拉长,其显微组织由细小的等轴晶粒和粗大的变形晶粒组成,织构强度增大。当合金组织内仅存在细小弥散的第二相时,板材成形性能主要受板材基面织构影响;当合金组织内存在粗大第二相时,板材成形性能受板材基面织构和第二相共同影响,且当第二相含量较高时,第二相对成形性能的恶化作用会大于织构弱化所带来的积极作用。
关键词:
随着交通运输、航空航天等领域对轻量化要求的不断提高,镁合金作为最轻的金属结构材料之一,具有很大的应用前景[1,2]。然而,镁合金的室温成形能力差,导致其应用领域受限。镁合金室温成形性能较差的原因主要有以下2个方面。首先,大部分镁合金具有hcp晶体结构,在室温下可启动的滑移系较少[3,4];其次,在变形加工过程中,镁合金形成了强烈的基面织构,进而恶化室温成形性能[5,6]。研究[7~9]表明,合金化可显著弱化镁合金的基面织构,提高镁合金的室温成形能力。如Nakata等[7]开发了Mg-3Al-0.4Mn (质量分数,%,下同)合金轧制板材,其具有特殊的织构特征且室温成形良好;Wang等[8]发现Mg-0.4Sn-0.7Y合金经过轧制加工后,其基面织构强度明显降低,与AZ31镁合金板材相比其室温成形性能大幅提高;Bian等[9]发现向Mg-Zn合金中添加少量Sc元素可显著降低基面织构,显著提升了合金的室温成形性能。由此可见,合金化是降低镁合金基面织构、提高其成形性能的有效方法之一。
然而,合金化元素添加量过高极易导致在合金凝固过程中产生大量第二相。根据文献[10~12]报道,向Mg-Zn系合金中添加稀土元素(RE)可形成二十面体准晶I相(Mg3Zn6RE1)、fcc结构W相(Mg3Zn3RE2)及长周期堆垛有序结构相(LPSO相,Mg12ZnRE或Mg10ZnRE)等多种Mg-Zn-RE三元相,其中I相、LPSO相因独特的晶体结构及突出的强韧化效果而备受关注。除了强化、韧化合金外,这些热稳定的三元相可凭借颗粒诱导形核动态再结晶(PSN-DRX)机制,形成大量不同取向的动态再结晶(DRX)组织,可吞并大量变形晶粒从而弱化基面织构[13]。Wang等[14]发现I相可通过颗粒诱导形核(PSN)促进DRX发生,显著细化晶粒,弱化基面织构;Meng等[15]发现LPSO相亦可由PSN-DRX机制提高合金组织的DRX程度,弱化基面织构。研究[16]表明,DRX动力学很大程度上取决于第二相的体积分数(Fv)和晶粒半径(r),如果Fv / r的值大于0.2 μm-1,则第二相的存在明显抑制再结晶的发生。另外,在合金变形过程中,第二相颗粒可能会成为孔洞形核位点,继而裂纹萌生,导致成形性能变差。
目前,在富含第二相的变形镁合金中,鲜有关于织构和第二相对室温成形性能影响的报道,影响室温成形性能的主导性因素尚不明确。因此,评价第二相对织构和成形的作用效果,研究织构、第二相等对成形性能的作用规律,进而揭示主导镁合金室温成形的关键因素,将有益于综合性能优良的镁合金冲压产品的开发和应用。本课题组前期工作[17]对退火前后Mg-xZn-0.5Er (x = 0.5、2.0、3.0、4.0)合金板材组织及室温成形性能进行了研究,结果表明退火过程中产生的纳米第二相显著弱化了合金板材的室温成形能力。但没有研究Zn添加量在不同变形量时对合金板材组织的影响,同时缺乏合金室温杯突失效机理性分析。本工作分别选择含有I相或W相的Mg-xZn-0.5Er (x = 0.5、2.0、3.0、4.0)合金,系统分析了在不同变形量下Zn含量对合金组织、第二相及织构的影响规律,结合Mg-Zn-Er合金板材的室温杯突实验结果,对合金室温杯突失效进行分析,揭示织构、第二相对镁合金板材室温成形性能的影响规律。
1 实验方法
使用原材料纯Mg (99.99%)、纯Zn (99.99%)和Mg-30Er中间合金制备Mg-xZn-0.5Er (x = 0.5、2.0、3.0、4.0)合金。熔炼在井式电阻炉内进行,坩埚为铸铁坩埚,熔炼过程中利用99%N2 + 1%SF6 (体积分数)进行气体保护。为了消除成分偏析和热稳定性较低的Mg-Zn相,将铸态Mg-xZn-0.5Er合金进行固溶处理(440℃保温10 h,放入75℃水中冷却)。随后将固溶态方坯进行切削加工,获得尺寸为5 mm (高) × 80 mm (长) × 80 mm (宽)的规则样品。本实验采用交叉轧制,每轧制三道次后将板材旋转90°再进行轧制,轧向(RD)和横向(TD)交替变化,且每道次轧制完成后在400℃的节能箱式电阻炉中退火保温5 min。轧制温度为400℃,轧制速率为7 m/min,单道次变形量为7%~15%,终态变形量为78%。
利用Axio imager A2m光学显微镜(OM)观察合金RD-TD面的显微组织;利用QUANTA FEG 650热场发射扫描电镜(SEM)配备的电子背散射衍射(EBSD)信息采集系统观察合金RD-ND (法向)面的微区织构;利用JEM-2100透射电子显微镜(TEM)观察合金的微观组织并利用其自带的能谱仪(EDS)进行第二相成分的分析。杯突胀形(erichsen test)是薄板胀形成形性能测试实验中最常用的一种方法,借助球头凸模把金属薄板顶入凹模并形成半球鼓包直至出现裂纹。鼓包顶部产生裂纹时凸模压入深度为实验指标,称为杯突值或IE值。室温成形实验在ECT1604自动杯突试验机上进行,按照国标GB/T 4156—2007,设计尺寸为60 mm × 60 mm的正方形板料试样(板材厚度为1.1 mm),冲头为半球状,其直径为20 mm,冲头速率约为4 mm/min,压边力为10 kN。
2 实验结果
2.1 Mg-Zn-Er合金板材显微组织演变
图1为轧制态Mg-xZn-0.5Er合金不同变形量下的RD-TD面微观组织的OM像。从图1a可以看出,变形初期(变形量为25%) Mg-0.5Zn-0.5Er合金内部形成了大量的孪晶组织,同时有二次孪晶产生,未观察到明显的DRX现象;当变形量增至44%时,从图1d可以看出Mg-0.5Zn-0.5Er合金中的孪晶数量减少,且有大量DRX晶粒产生;当变形量增至54%时,合金中的DRX晶粒明显增多,且呈长大趋势(图1g);当变形量为64%时,合金中发生了比较完全的DRX,晶粒明显细化(图1j)。对比发现,随着Zn含量的增加,Mg-2.0Zn-0.5Er和Mg-4.0Zn-0.5Er合金在变形初期也形成了大量的孪晶组织,其形貌与Mg-0.5Zn-0.5Er合金中的显著不同,如在合金Mg-4.0Zn-0.5Er中有大量的细小孪晶组织形成(图1c);且随着Zn含量的增加合金的DRX显著提前,合金Mg-2.0Zn-0.5Er在变形量为54%时发生了完全的DRX (图1h),合金Mg-4.0Zn-0.5Er在变形量为44%时发生了完全的DRX (图1f)。
图1
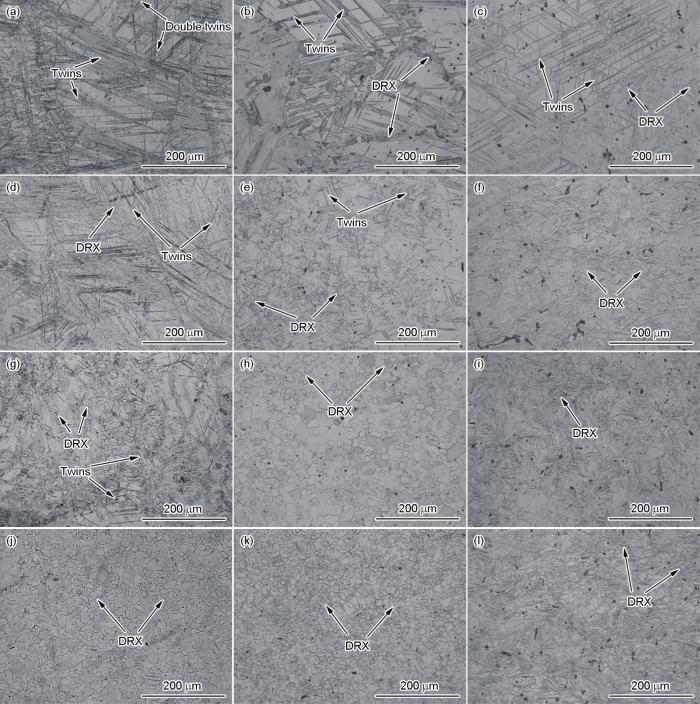
图1 轧制态Mg-xZn-0.5Er (x = 0.5、2.0、4.0)合金不同变形量下轧向-横向(RD-TD)面微观组织的OM像
Fig.1 OM images of as-rolled Mg-0.5Zn-0.5Er (a, d, g, j), Mg-2.0Zn-0.5Er (b, e, h, k), and Mg-4.0Zn-0.5Er (c, f, i, l) alloys on the rolling direction-transverse direction (RD-TD) plane with thickness reductions of 25% (a-c), 44% (d-f), 54% (g-i), and 64% (j-l) (DRX—dynamic recrystallization)
2.2 Mg-Zn-Er合金板材动态再结晶机制
图2为变形初期(变形量25%) Mg-2.0Zn-0.5Er合金RD-ND面的EBSD分析。从图2a可以看出,合金中存在孪晶、DRX晶粒和大尺寸的原始晶粒。为了分析其DRX机制,对图2a中的不同区域进行分析。图2b1表明在粗大的孪晶内部存在大量的DRX晶粒,图2b2表明孪晶相对于具有基面取向的原始晶粒发生了一定偏转,DRX晶粒的取向分布较为随机,从而弱化基面织构。从图2b3和b4可以看出,合金在变形初期形成了大量的小角度晶界(< 15°),大部分小角度晶界位于孪晶内部。与原始晶粒相比,孪晶内部的位错滑移程较短,位错更容易塞积、重排,从而产生小角度晶界,这种小角度晶界随着应变的增加逐渐转变为大角度晶界,从而形成由大角度晶界和孪晶界包围的DRX晶粒[18~20]。这种孪晶内形核的晶粒是典型的孪生动态再结晶(twin dynamic recrystallization,TDRX)晶粒。从图2c1可以发现,发生TDRX的孪晶以56°的(10
图2
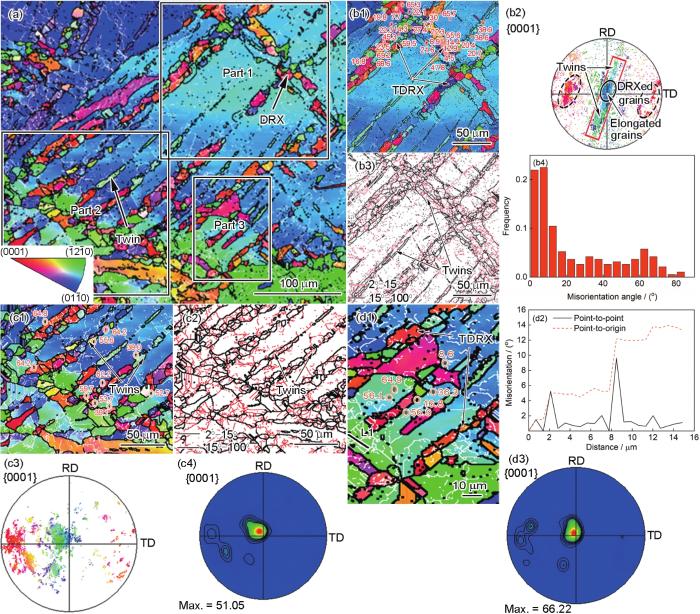
图2 变形量为25%时轧制态Mg-2.0Zn-0.5Er合金轧向-法向(RD-ND)面的EBSD分析
Fig.2 EBSD analyses of Mg-2.0Zn-0.5Er alloy on the RD-normal direction (ND) plane with thickness reduction of 25%
(a) inverse pole figure (IPF)
(b1-b4) EBSD analyses of part 1 in Fig.2a for IPF (b1), {0001} pole figure (b2), and misorientation angle distributions (b3, b4) (TDRX—twin dynamic recrystallization)
(c1-c4) EBSD analyses of part 2 in Fig.2a for IPF (c1), misorientation angle distribution (c2), and {0001} pole figures (c3, c4)
(d1-d3) EBSD analyses of part 3 in Fig.2a for IPF (d1), distribution of misorientation along line L1 in Fig.2d1 (d2), and {0001} pole figure (d3)
图3为变形量44%时Mg-2.0Zn-0.5Er合金RD-ND面的EBSD分析。从图3a可以看出,合金的显微组织主要由DRX晶粒和变形晶粒组成,与图2a对比发现,随着变形量的增加,合金中DRX晶粒数量明显增多并且有长大的趋势。从图3b可以看出,小角度晶界接近闭环状分布在原始晶粒内,这是由于位错通过动态回复重新排列和湮灭,在初始晶粒内形成了亚晶,随着应变不断增加,这些亚晶将会逐渐转变为新的晶粒,该过程在整个晶粒内部均匀发生,为典型的连续动态再结晶(continuous dynamic recrystallization,CDRX)[21];图3a中极图表明此时合金仍具有强烈的基面织构,但与小变形量(25%)相比,其织构强度明显下降,表明DRX可以显著弱化基面织构。合金不同变形量的EBSD分析表明,随着变形量的增加,DRX机制也会发生相应变化。变形初期合金中主要发生TDRX伴随少量的DDRX,随着变形量增加,TDRX逐渐向CDRX转变。较大变形量后,合金中主要发生 CDRX。
图3
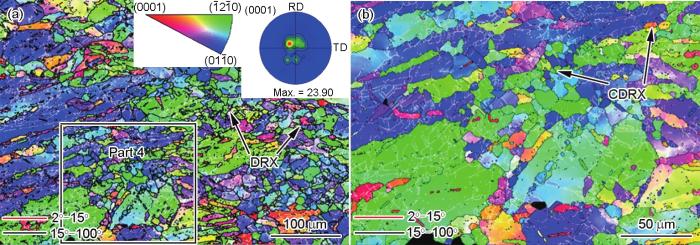
图3 变形量为44%时轧制态Mg-2.0Zn-0.5Er合金RD-ND面的EBSD分析
Fig.3 EBSD analyses of Mg-2.0Zn-0.5Er alloy on the RD-ND plane with thickness reduction of 44%
(a) IPF and {0001} pole figure (inset)
(b) local enlarged IPF of the part 4 in Fig.3a (CDRX—continuous dynamic recrystallization)
2.3 终态板材显微组织分析
图4所示为变形量78%时轧制态Mg-xZn-0.5Er合金板材RD-TD面微观组织的OM像。与图1对比可以发现,轧制过程中发生的DRX可以显著细化晶粒,Mg-0.5Zn-0.5Er、Mg-2.0Zn-0.5Er、Mg-3.0Zn-0.5Er和Mg-4.0Zn-0.5Er合金的平均晶粒尺寸分别约为8.9、15.6、14.4和20.3 μm。合金化元素Zn可降低Mg的层错能,导致扩展位错难以束集,激发DRX提前发生[22],DRX晶粒在以后道次轧制过程中会显著长大;而且提高Zn的含量会明显提高第二相(主要是I相和W相)的含量和尺寸[23],粗大的第二相也会加速DRX发生,最终合金的DRX程度随Zn含量的升高而升高,所以Mg-4Zn-0.5Er合金平均晶粒尺寸较大[13,24]。
图4
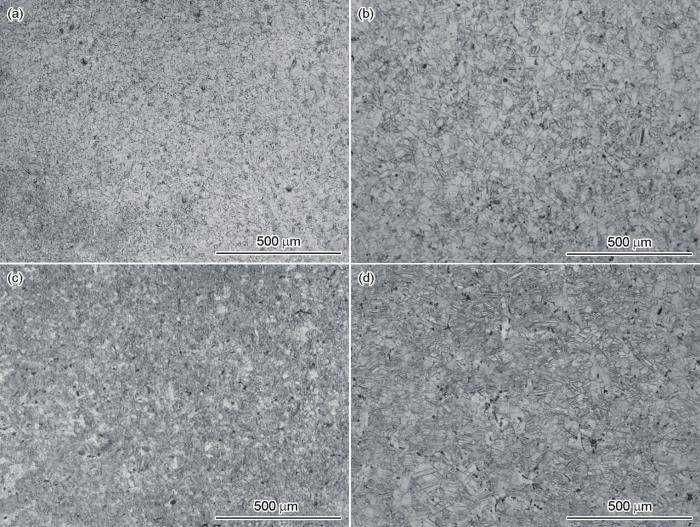
图4 变形量为78%时轧制态Mg-xZn-0.5Er合金RD-TD面微观组织的OM像
Fig.4 OM images of as-rolled Mg-0.5Zn-0.5Er (a), Mg-2.0Zn-0.5Er (b), Mg-3.0Zn-0.5Er (c), and Mg-4.0Zn-0.5Er (d) alloys on the RD-TD plane with thickness reduction of 78%
图5为变形量78%时Mg-xZn-0.5Er合金的EBSD像。可以看出,轧制态Mg-0.5Zn-0.5Er合金的显微组织比较均匀,其织构强度最低。随着Zn含量的增加,合金的织构强度逐渐增大。这是因为Mg-2.0Zn-0.5Er、Mg-3.0Zn-0.5Er和Mg-4.0Zn-0.5Er合金提前发生了完全动态再结晶(图1),在后续轧制过程中细小的动态再结晶晶粒长大并在应力的作用下被拉长,其显微组织由细小的等轴晶和粗大的变形晶粒组成。DDRX机制有助于形成具有随机取向的DRX晶粒,CDRX机制有助于形成与母晶取向相似的DRX晶粒[25]。由动态再结晶机制分析可知,Mg-xZn-0.5Er合金在轧制过程中主要发生了TDRX和CDRX,因此,虽然Mg-0.5Zn-0.5Er合金发生了完全动态再结晶,但其仍具有较强的织构。
图5
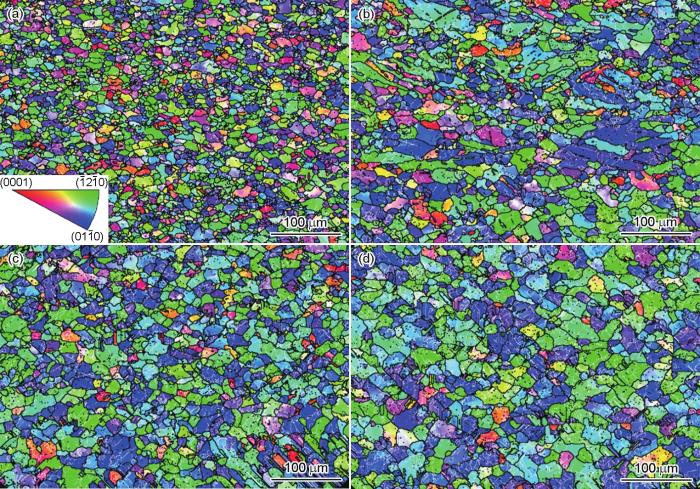
图5 变形量为78%时轧制态Mg-xZn-0.5Er合金RD-ND面的EBSD像
Fig.5 EBSD images of Mg-0.5Zn-0.5Er (a), Mg-2.0Zn-0.5Er (b), Mg-3.0Zn-0.5Er (c), and Mg-4.0Zn-0.5Er (d) alloys on RD-ND plane with thickness reduction of 78%
2.4 Mg-Zn-Er合金板材的室温成形性能
图6是变形量为78%时轧制态Mg-xZn-0.5Er合金室温杯突胀破样品。可以看出,Mg-0.5Zn-0.5Er合金具有最好的成形性能,其IE值为5.67 mm;随着Zn含量的增加合金的IE值逐渐降低,Mg-2.0Zn-0.5Er、Mg-3.0Zn-0.5Er和Mg-4.0Zn-0.5Er合金的IE值分别为4.73、2.92和2.20 mm,即Zn含量的增加导致合金的室温成形性能降低。
图6
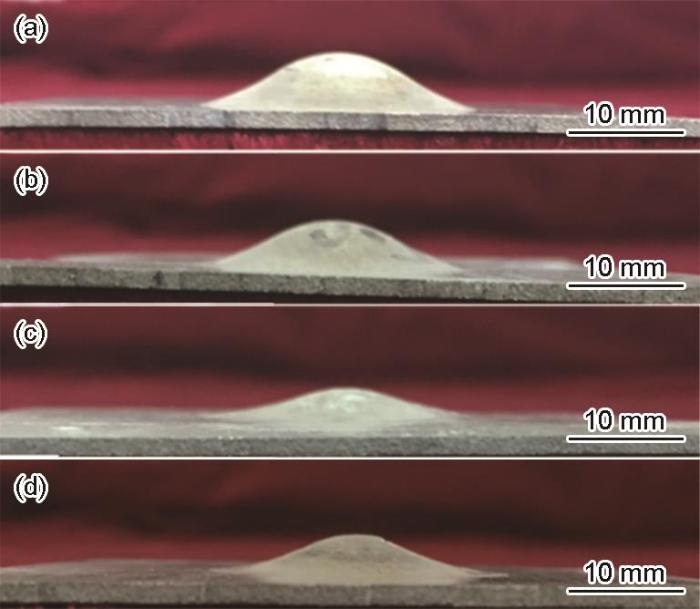
图6 室温条件下变形量为78%时轧制态Mg-xZn-0.5Er合金的杯突成形性能
Fig.6 Cupping formabilities of as-rolled Mg-0.5Zn-0.5Er (a), Mg-2.0Zn-0.5Er (b), Mg-3.0Zn-0.5Er (c), and Mg-4.0Zn-0.5Er (d) alloys with thickness reduction of 78% at room temperature
图7
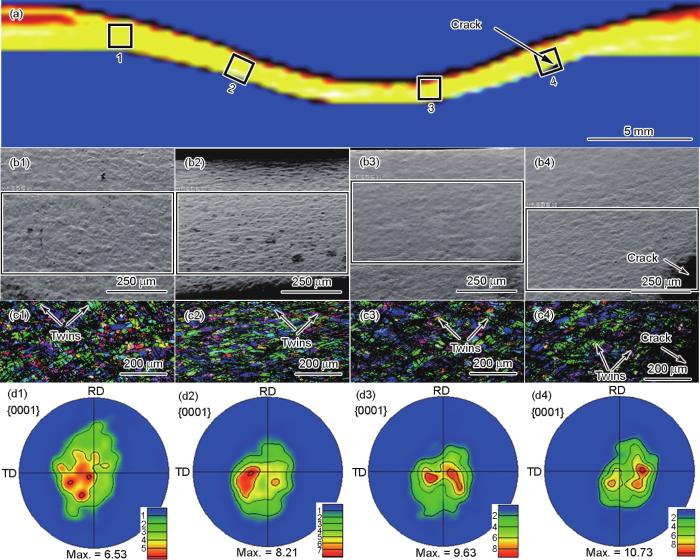
图7 轧制态Mg-2.0Zn-0.5Er合金板材的杯突失效分析
Fig.7 Failure analyses of cup test of as-rolled Mg-2.0Zn-0.5Er alloys
(a) cross-section image
(b1-b4) SEM images of areas 1-4 in Fig.7a, respectively
(c1-c4) IPFs of box areas in Figs.7b1-b4, respectively
(d1-d4) pole figures of Figs.7c1-c4, respectively
3 分析与讨论
3.1 织构、第二相对合金室温成形性的影响
织构是影响镁合金室温成形性的一个重要因素。通过有限元模拟,Suh等[26]揭示了Mg-Zn-Ca合金板材在拉深成形初期,合金的上半部分受沿TD方向的拉应力,合金的下半部分受沿着TD方向的压应力。在本工作中,在拉深成形初期合金板材上半部分所受到的应力主要是沿着TD方向的拉应力,下半部分所受到的应力主要是沿着TD方向的压应力。当镁合金基面平行于应力方向时,基面和柱面的<a>滑移不能有效地适应厚度方向的应变,并且由于<10
3.2 合金室温杯突失效分析
室温条件下,镁合金主要的变形机制以基面滑移和孪生为主,基面位错滑移并不会引起晶粒取向的改变,因此断裂失效样品不同位置的织构强度变化主要是由孪生引起的。随着变形量的提高,基面滑移转变为硬取向,孪晶也从拉伸孪晶转变为压缩孪晶与双孪晶。从图7可以看出,在杯突实验过程中,有大量孪晶产生,并且越靠近断裂失效位置织构强度越大,因此孪晶在断裂失效位置处聚集。文献[29,30]中报道第二相粒子尺寸增大,不利于合金力学性能和成形性能提高,因为这些微米级的第二相是产生应力集中和形成裂纹的主要位置。在应力的作用下,孪晶、第二相相互作用,导致裂纹产生并扩展。因此,进行杯突实验时,孪晶、第二相是引起合金板材破裂失效的主要原因。
4 结论
(1) 随着Zn含量的增加,Mg-xZn-0.5Er合金提前发生了完全动态再结晶,在后续轧制过程中细小的动态再结晶晶粒长大并在应力的作用下被拉长,其显微组织由细小的等轴晶粒和粗大的变形晶粒组成,织构强度增加。
(2) 合金中第二相的尺寸较小时,板材成形性能的优劣主要由基面织构决定;合金中第二相的尺寸较大时,板材成形性能的优劣由基面织构和第二相共同决定,且第二相对成形性能的恶化作用会大于织构弱化所带来的积极作用。
(3) 在应力的作用下,孪晶、第二相相互作用,导致裂纹产生并扩展。因此,进行杯突实验时,孪晶、第二相是引起合金板材破裂失效的主要原因。