分享:露点对连续退火0.2%C-1.5%Si-2.5%Mn高强钢选择性氧化及脱碳的影响
1.
2.
以成分为0.2%C-1.5%Si-2.5%Mn (质量分数)的先进高强钢为研究对象,采用连续退火模拟实验研究了露点对钢板表面Si、Mn选择性氧化以及次表层脱碳的影响。使用辉光放电发射光谱(GD-OES)分析了退火试样表面元素深度分布,使用SEM、OM观察了试样截面内氧化层及脱碳层深度,使用TEM观察了FIB制备的截面试样上Si、Mn内外氧化层的微观结构。结果表明,提高连续退火加热段和均热段的气氛露点可以促使Si、Mn由外氧化转变成内氧化,但露点过高会引起钢板次表层发生明显的脱碳,形成次表层显微硬度显著降低的铁素体层。当露点提高到临界值后,继续提高露点对进一步减少外氧化的效果有限,但是内氧化层和脱碳层的厚度会继续显著增加,因此在退火时需要选择兼顾外氧化和脱碳层控制的合适的露点范围。
关键词:
轻量化是实现汽车节能减排的重要手段之一,使用先进高强钢(advanced high strength steel,AHSS)是现阶段实现汽车轻量化的重要技术方案之一。过去十多年间,各类AHSS钢种的开发与应用得到了快速发展[1~5]。利用亚稳奥氏体的相变行为实现增强增塑已成为第三代AHSS的发展方向[4,5],与传统低强度的钢种相比,AHSS中添加了更高含量的奥氏体稳定元素,如C、Si、Mn等。
AHSS中越来越高的Si、Mn等合金元素在传统退火条件下会形成表面富集,从而引起热镀锌钢板的可镀性问题[6~9]、锌层附着性问题[10,11]或者连退钢板的磷化[12]等涂装问题,因此AHSS表面选择性氧化的控制研究已成为AHSS继组织调控技术研究之外的另一重要研究方向。近年来,在合金元素、退火气氛露点、H2含量、氧分压、水压、温度、时间等工艺参数对不同成分的高强钢选择性氧化的影响方面已有大量研究[13~21],内氧化技术已经在连续热镀锌线上实现了工业应用,是目前AHSS表面控制的重要技术手段。
钢中添加的与O2亲和力强的元素先于基体Fe元素发生氧化,称为选择性氧化。根据氧化物在钢板上所处的位置,可将氧化分为外氧化和内氧化。外氧化是指扩散至表面的合金元素与O发生反应生成氧化物,内氧化是指O扩散至表面以下的次表层与基体中的金属元素反应生成氧化物。
当外氧化减少、内氧化增加时,带钢的可镀锌性问题可以得到改善。但是随着AHSS品种的不断丰富,高C、高合金成分的钢种逐渐增多,在利用提高退火气氛露点将Si、Mn外氧化转变成内氧化的同时,也带来了一些副作用。Wu等[21]及Zhang等[22]在研究水压对高强钢选择性氧化的影响时,观察到了钢板表面的脱碳,表面脱碳严重时会导致材料强度下降。Han等[23]研究发现内氧化对焊接电流区间有影响,内氧化会降低接触电阻和热输入,从而延迟熔核生长。Kalashami等[24]研究了内氧化对热镀锌双相(DP)钢的焊接液态金属脆性(liquid metal embrittlement,LME)的影响,发现晶界的内氧化会促使焊接时液态锌在晶界扩散。Kalashami等[25]指出,为了获得相同的熔核直径和焊点强度,存在内氧化的热镀锌钢板需要更高的焊接电流和更长的焊接时间。可见对于工业生产的热镀锌高强钢而言,内氧化并不是越厚越好,在使用内氧化技术时,需要找到能够兼顾多方面的合适的工艺窗口。
本工作以主成分为0.2%C-1.5%Si-2.5%Mn (质量分数)、目标抗拉强度为1180 MPa的热镀锌AHSS为研究对象,从实际应用出发,综合考虑了合金元素内外氧化和表面脱碳的控制,研究了连续退火气氛露点对Si、Mn选择性氧化和脱碳的影响,以期为AHSS表面微结构精确控制提供参考。
1 实验方法
实验用样板取自宝钢工业化生产的0.2%C-1.5%Si-2.5%Mn高强钢轧硬卷,试样尺寸为70 mm×120 mm,板厚为1.2 mm。使用NaOH浓度为2% (质量分数)的工业脱脂剂对轧硬板试样进行清洗处理,脱脂剂温度为40~60℃,脱脂后用流水冲洗干净,用压缩空气吹干。
模拟退火实验在Iwatani HDPS设备上进行,温度曲线如图1所示,包括升温、保温、冷却3个阶段。以5℃/s由室温加热至870℃后保温120 s,然后以-10℃/s冷却至70℃。升温和保温过程使用相同的5%H2-N2 (体积分数)退火气氛,露点(dew point)分别控制为-40、-20、0和+10℃;冷却过程使用100%N2,不控制露点。
图1
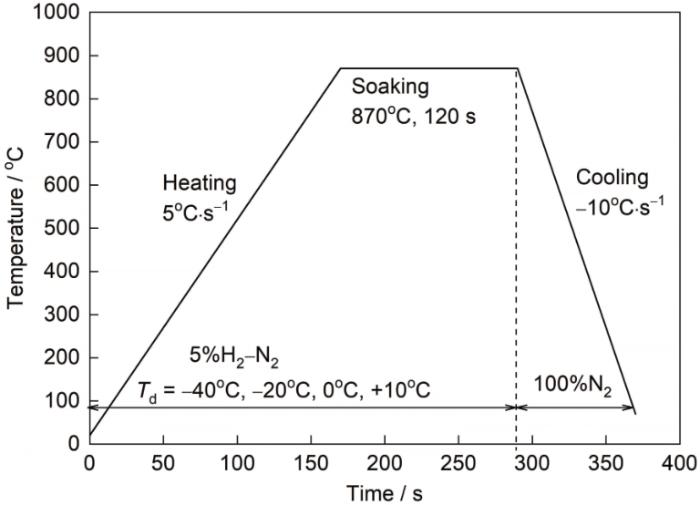
图1 模拟退火实验温度曲线
Fig.1 Thermal cycle of the annealing experiments (Td—dew point)
采用LECO 750A辉光放电发射光谱分析仪(glow discharge optical emission spectrometry,GD-OES)对退火样板和未退火的轧硬板进行表面元素深度分析,重点关注试样表层合金元素Si、Mn、C及O的深度分布。取Si、Mn元素深度分布曲线上靠近表面的峰值以及峰值一半位置的深度表征外氧化的程度;取C元素深度分布上5~6 μm位置C含量平均值表征钢板次表层的脱碳程度。
采用常规金相方法制备截面试样,使用EVO MA25扫描电镜(SEM)观察抛光状态的截面,观察钢板次表层的内氧化并测量内氧化层厚度;使用Axio Imager M2m显微镜(OM)观察4% (体积分数)硝酸酒精溶液侵蚀后的截面,观察钢板次表层的脱碳层并测量脱碳层的厚度;使用Future-Tech FM-7显微硬度计检测次表层显微硬度沿深度方向的分布。
选择露点为-40℃和+10℃ 2个典型试样,使用Helios Nanolab 600i双束聚焦离子束(FIB)显微镜制备截面透射电镜(TEM)样品,并在2010 F TEM下观察截面形貌。在FIB制样前,试样表面沉积Pt保护层,然后使用镓离子束轰击样品直到样品达到大约100 nm的厚度来完成TEM试样制备。使用扫描透射电子显微镜-能谱仪(STEM-EDS)进行成分分析,重点关注钢板表面的Si、Mn元素外氧化以及钢板次表层的Si、Mn元素内氧化。
2 实验结果
露点为-40℃模拟退火试样表面1000 nm深度范围内Fe、Mn、Si和O元素的深度分布曲线如图2所示,图中还标记了Mn、Si元素曲线上的峰值pMn和pSi,及Mn元素曲线上峰值一半位置的深度te (以此代表外氧化层的厚度)。在试样表层100 nm深度范围内,Mn和Si的含量均高于基体含量,而且Mn元素和O元素的曲线形状轮廓较接近,说明表面形成了较明显的Mn、Si元素外氧化。比较pMn和pSi可知,该试样Mn元素的外氧化比Si元素的外氧化更显著。图2中pMn和pSi相对应的深度分别为25.6和51.7 nm,te = 61 nm,比较上述深度和厚度位置的差异,推测外氧化层的成分可能存在沿厚度方向梯度分布的特征,靠近表面的氧化物Mn含量更高,而靠近基体的氧化物Si含量更高。
图2
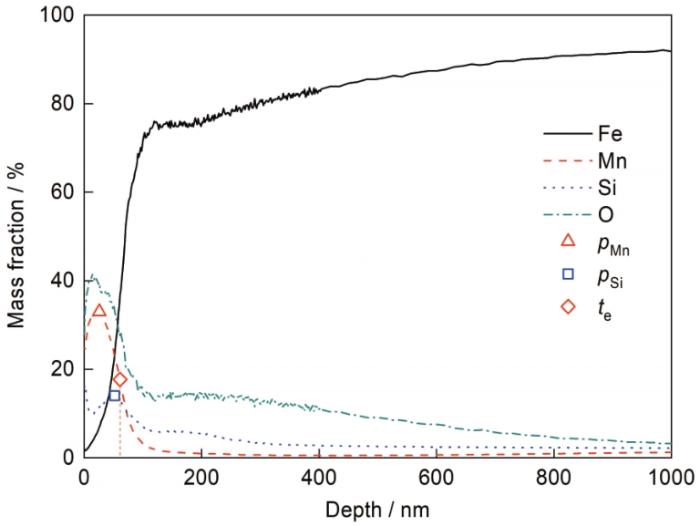
图2 露点-40℃退火试样表面Fe、Mn、Si、O元素深度分布曲线
Fig.2 Fe, Mn, Si, and O depth profiles of the sample annealed at dew point of -40oC (pMn—peak value of Mn, pSi—peak value of Si, te—thickness of external oxidation)
为便于比较退火气氛露点对同一个元素深度分布的影响,将不同露点退火试样的Mn和Si元素分别绘制在同一张图中,同时以退火前的轧硬板作为对照,结果如图3所示。与轧硬板表面的原始Mn、Si含量相比,退火试样表面均出现了Mn、Si元素的富集,且Mn的表面富集量高于Si。露点对pMn、pSi的影响如图4a所示。当露点为-40℃时,Mn、Si的外氧化最显著,pMn和pSi分别为33%和14%;当露点由-40℃提高到-20℃时,外氧化明显减少,pMn和pSi分别降至24.3%和7.7%;当露点进一步由-20℃提高到+10℃时,Mn、Si外氧化的变化不大。
图3
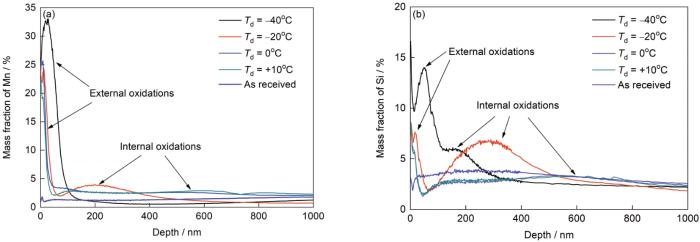
图3 不同露点退火试样Mn、Si元素深度分布
Fig.3 Mn (a) and Si (b) depth profiles of the samples annealed at different dew points
图4
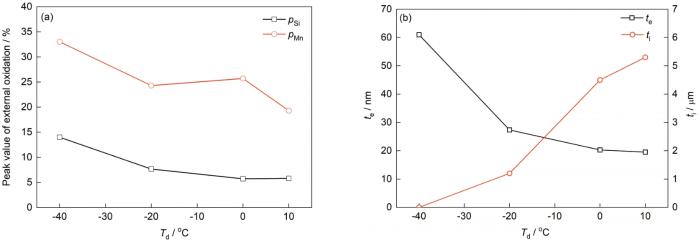
图4 露点对Mn、Si内外氧化的影响
Fig.4 Effects of dew point on the external and internal oxidations of Mn and Si (ti—thickness of internal oxidation)
(a) pMn and pSi (b) te and ti
图4b显示了露点对te和内氧化层厚度ti的影响,ti由退火试样截面SEM照片(图5)上测量得到。随着露点升高,总体呈现te减小ti增大的趋势,但2者变化的幅度有较大差异。当露点由-40℃提到高-20℃时,te由61 nm显著降至27 nm,而此时ti仅增加至1.2 μm左右。当露点进一步由-20℃提高至+10℃时,te的下降幅度明显减缓,仅由27 nm降至19.5 nm;而ti则持续增加,由1.2 μm增加至5.2 μm。
图5
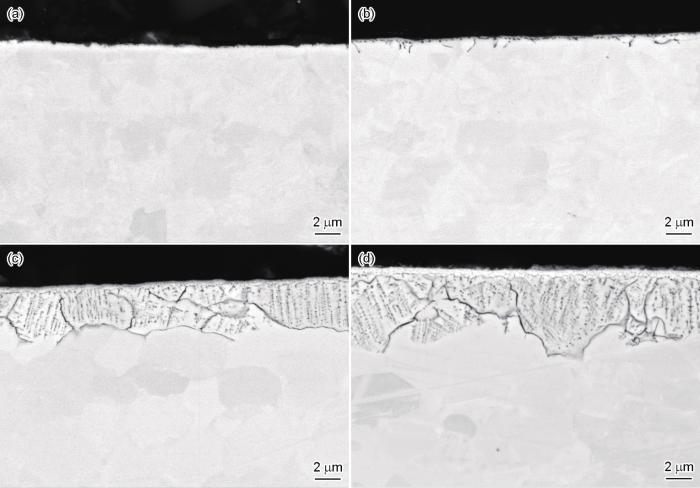
图5 不同露点退火试样截面组织SEM像
Fig.5 Cross-sectional SEM images of the samples annealed at different dew points
(a) -40oC (b) -20oC (c) 0oC (d) +10oC
FIB制备的-40℃露点退火试样截面组织TEM像如图6所示,其中图6a为较低倍数的整体形貌,图6b~d为局部区域放大形貌。当露点为-40℃时,钢板表面有一层连续的外氧化层,微观上厚度并不均匀。若不考虑局部深入基体的位置,外氧化层的平均厚度为40~50 nm;若适当考虑局部深入基体的氧化,则外氧化层的平均厚度会略有增加,该结果与图4b显示的由GD-OES检测的外氧化厚度基本相当。除连续的外氧化外,在钢板次表层约300 nm的深度范围内,还观察到少量内氧化颗粒,如图6b和d中箭头所示。对照图3b中同一个试样相同深度内(100~300 nm)的Si元素含量,发现该位置的Si含量明显高于更深位置基体的Si含量,而相应位置的Mn含量仅为0.5%左右,明显低于基体Mn含量。局部元素面分布结果如图7所示,外氧化物中同时含有Mn和Si,其中Mn含量更高,而内氧化颗粒主要是Si的氧化物,仅在颗粒边缘检测到少量的Mn。由此可见,在露点为-40℃时,Si、Mn同时形成了连续致密的外氧化物,少量Si形成了内氧化颗粒。
图6
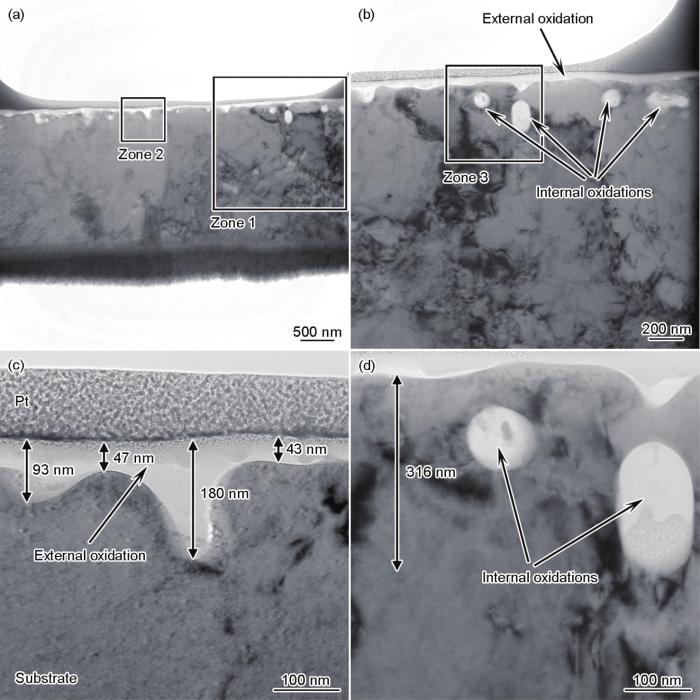
图6 聚焦离子束(FIB)制备的露点为-40℃退火试样截面组织TEM像
Fig.6 TEM image of the focused ion beam (FIB) prepared cross-sectional sample annealed at dew point of -40oC (a) and enlarged images of zone 1 (b), zone 2 (c), and zone 3 (d)
图7
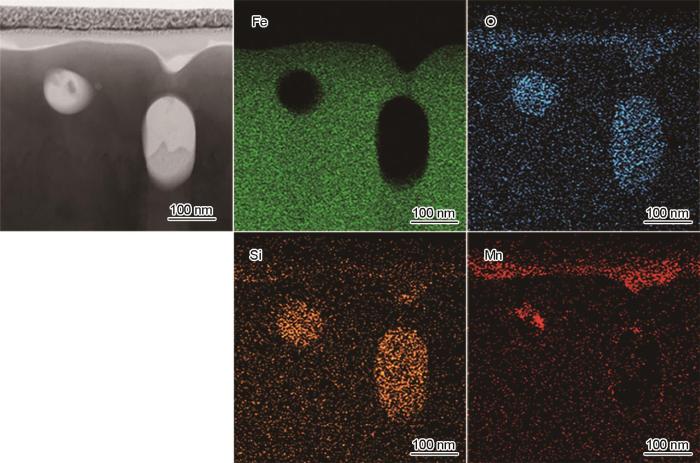
图7 露点为-40℃退火试样TEM元素面分布结果
Fig.7 EDS elemental mapping of the TEM sample annealed at dew point of -40oC
露点为+10℃退火试样截面TEM像如图8所示,其中图8a为低倍整体形貌,图8b~d分别为区域1~3的局部放大形貌。当露点为+10℃时,钢板表面未观察到连续的外氧化膜,仅局部位置存在分散的、尺寸较小的外氧化颗粒,如图8c中箭头所示。取代外氧化的是钢板次表层形成了大量的内氧化,包括晶粒内部的内氧化颗粒及晶界位置的网状内氧化物。
图8
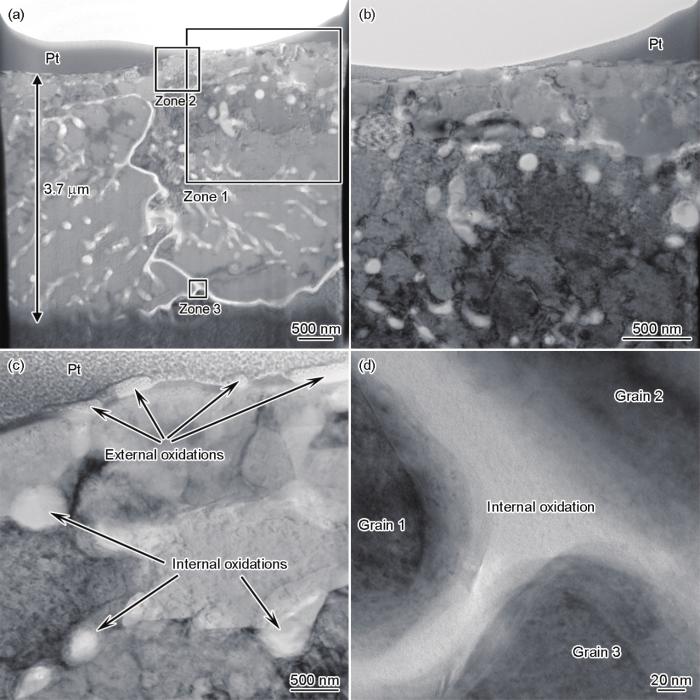
图8 FIB制备的露点为+10℃退火试样截面组织TEM像
Fig.8 TEM image of the FIB prepared cross-sectional sample annealed at dew point of +10oC (a) and enlarged images of zone 1 (b), zone 2 (c), and zone 3 (d)
露点为+10℃退火试样深度方向上3个不同区域(见图8a)的元素面分布结果如图9所示,确认图8中观察到的晶内、晶界的白色相是Si和Mn的氧化物。比较图9a和图7a同为靠近表面位置的面分布结果,当露点由-40℃提高到+10℃后,试样表面O、Si、Mn的含量显著减少,而下方的Si、Mn内氧化明显增加。图9b为深度居中的晶粒内部位置的元素面分布结果,发现该位置的内氧化颗粒芯部Si含量较高、基本不含Mn,而氧化物颗粒外层Mn含量较高。图9c为更深的晶界位置,同样也观察到了氧化物芯部Si含量高、外层Mn含量高的特征。
图9
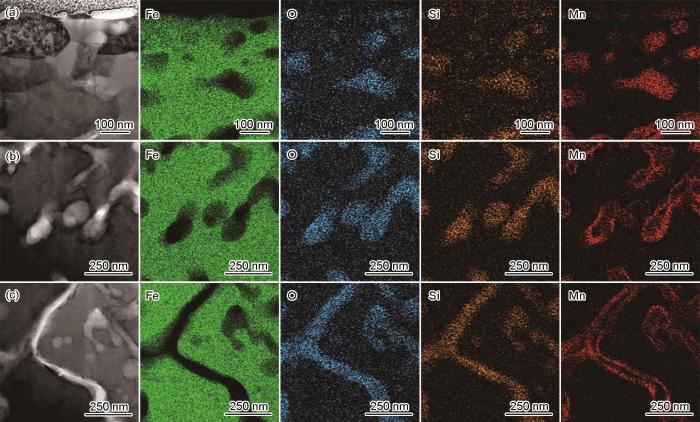
图9 露点为+10℃退火试样上3个不同区域(见图8a)元素面分布
Fig.9 EDS elemental mapping of three different areas (in Fig.8a) on the sample annealed at dew point of +10oC
(a) upper zone (b) middle zone (c) bottom zone
不同露点退火试样表层6 μm深度范围内C元素的深度分布曲线如图10所示,露点对次表层C含量以及脱碳层厚度的影响如图11所示。由于GD-OES检测时受试样表面残碳的影响,近表面(0~1 μm范围内)检测到的C误差较大,但2 μm之后的C含量比较准确,因此取5~6 μm位置的C含量的平均值代表次表层的C含量。当露点为-40℃时,次表层C含量和轧硬板相同位置的C含量基本相同,当露点升高至-20℃,次表层C含量由0.18%降至0.08%,当露点进一步升高至0和+10℃时,次表层C含量降至约0.01%,可见露点升高后钢板次表层发生了明显的脱碳。
图10
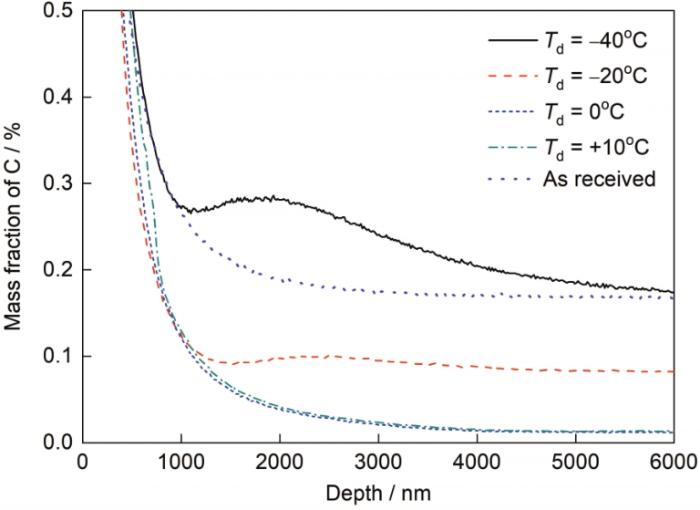
图10 不同露点退火试样C元素深度分布
Fig.10 C depth profiles of the samples annealed at different dew points
图11

图11 露点对钢板次表层C含量及脱碳层厚度的影响
Fig.11 Effects of dew point on C content (a) and decar-burization thickness (b) in the subsurface area (td1—thickness of total decarburization, td2—thickness of full decarburization)
硝酸酒精腐蚀后试样截面显微组织的OM像如图12所示。基体组织主要是马氏体和少量铁素体,露点升高后的试样表面出现了明显的铁素体组织,表层脱碳层厚度检测结果如图11b所示。由于表层脱碳层在深度方向有一定的渐变趋势,因此以表面至铁素体和少量马氏体组织混合层的深度作为总脱碳层厚度(td1),以表面至纯铁素体层的深度作为完全脱碳层厚度(td2)。当露点为-40℃时,次表层无脱碳层;当露点升高至-20℃时,次表层出现部分脱碳层,厚度接近21 μm,此时未出现完全脱碳层;当露点继续升高至0和+10℃时,次表层出现了明显的完全脱碳层,厚度达到22 μm,同时总脱碳层的厚度达到了45 μm。
图12
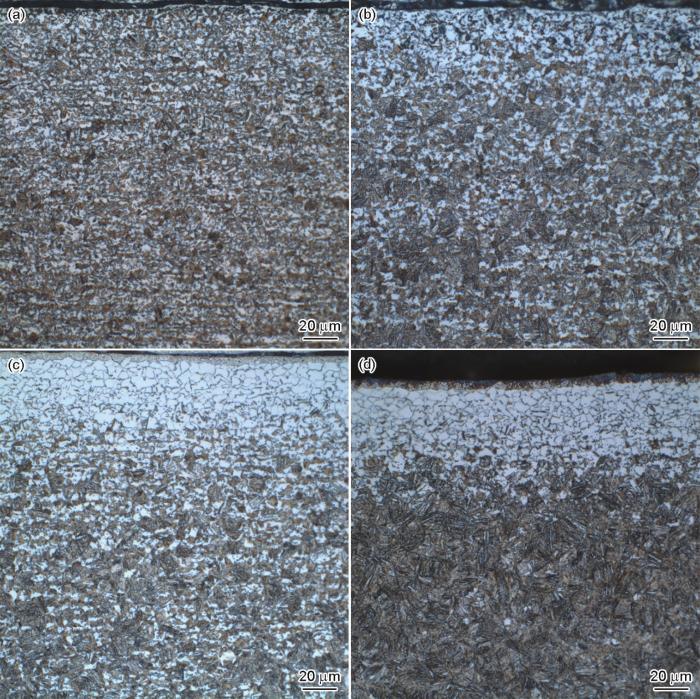
图12 不同露点退火试样截面显微组织的OM像
Fig.12 Cross-sectional OM images of the samples annealed at different dew points
(a) -40oC (b) -20oC (c) 0oC (d) +10oC
试样截面次表层显微硬度沿深度方向的变化如图13所示,因提高露点后钢板次表层出现了脱碳,因此次表层的显微硬度均降低。深度100 μm后基体的显微硬度超过了400 HV,当露点为-40℃时,仅最表层的显微硬度降至350 HV左右,其余位置和基体显微硬度差别不大。当露点为-20℃时,次表层显微硬度最低降至290 HV左右;当露点为0和+10℃时,次表层显微硬度最低降至200 HV左右。
图13
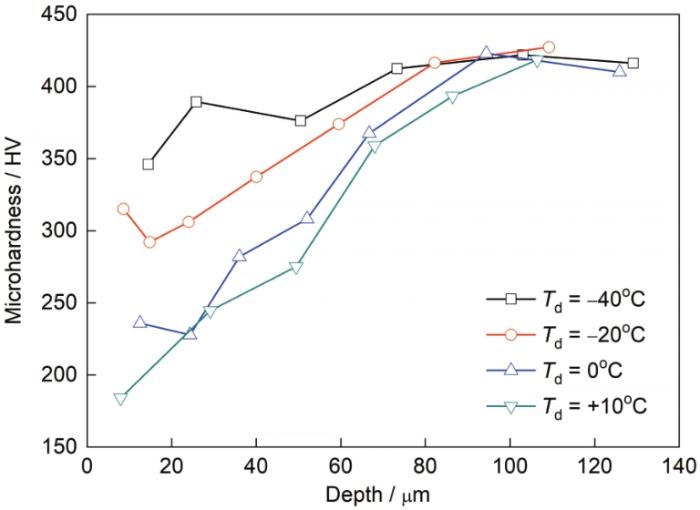
图13 露点对钢板次表层深度方向显微硬度的影响
Fig.13 Effects of dew point on microhardness along the depth in the subsurface area
3 分析与讨论
以上实验结果表明,当0.2%C-1.5%Si-2.5%Mn钢板在退火温度为870℃、保温时间为120 s、退火气氛为5%H2-N2的条件下进行连续退火时,退火气氛露点对Si、Mn内外氧化及表层脱碳的影响显著。低露点(-40℃)和高露点(+10℃)退火后的钢板表层示意图如图14所示。
图14
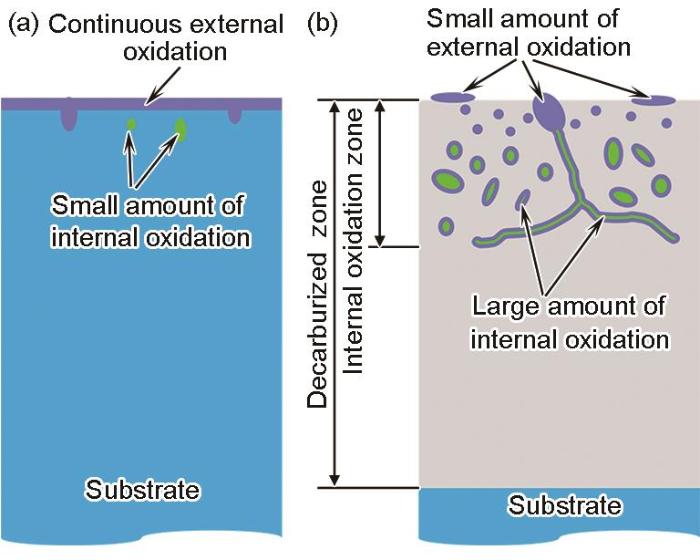
图14 露点对连续退火0.2C-1.5Si-2.5Mn钢选择性氧化及次表层脱碳的影响示意图
Fig.14 Schematic diagram showing the effect of dew point on selective oxidation and decarburization of 0.2C-1.5Si-2.5Mn high strength steel sheet during continuous annealing at the dew points of -40oC (a) and +10oC (b)
当露点为-40℃时,钢板表面会形成连续覆盖的Si-Mn外氧化膜,次表层形成少量Si的内氧化颗粒,钢板次表层未形成脱碳。当露点为+10℃时,钢板表面形成少量不连续的Si-Mn外氧化颗粒,在次表层约5 μm深度范围形成显著的内氧化层,在次表层约40 μm深度范围内形成脱碳。内氧化层中的氧化物可分成3类:第一类是靠近表面(深度为0~0.5 μm)的内氧化颗粒,其颗粒尺寸相对较小,主要是Si-Mn复合氧化物;第二类是位于深度大于0.5 μm的晶粒内部的内氧化颗粒,这些颗粒芯部是SiO2,外层为Si-Mn复合氧化物;第三类是位于晶界的网状内氧化物,同样是芯部为SiO2,外层为Si-Mn复合氧化物。
内氧化形成过程可以分为2步,第一步是O2和O原子溶于合金中,第二步是溶解的O原子和钢中的合金元素发生反应生成氧化物,内氧化深度(ξ)的表达式为[26]:
式中,
在本实验条件下,变化的参数只有退火气氛露点,根据式(
式中,
表1 根据露点计算的氧分压
Table 1
Td / oC | T / oC |
|
|
|
---|---|---|---|---|
-40 | 870 | 0.05 | 1.27 × 10-4 | 8.08 × 10-23 |
-20 | 870 | 0.05 | 1.02 × 10-3 | 5.20 × 10-21 |
0 | 870 | 0.05 | 6.03 × 10-3 | 1.82 × 10-19 |
+10 | 870 | 0.05 | 1.21 × 10-2 | 7.37 × 10-19 |
Note:T—temperature,
根据式(
表2 O、Mn、Si、C在钢中的扩散系数
Table 2
Element | Temperature | Diffusion coefficient |
---|---|---|
oC | μm2·s-1 | |
O | 870 | 1.507 × 101 |
Mn | 870 | 4.227 × 10-3 |
Si | 870 | 6.615 × 10-3 |
C | 870 | 2.551 × 101 |
式中,
当退火气氛氧分压提高后,O向内扩散占主导地位,且由于O的扩散系数远大于Mn和Si,内氧化的深度主要受O扩散深度控制。而C的扩散系数略高于O,通常认为脱碳行为的控速环节为固相中C元素扩散[29],退火气氛露点提高之后,气氛的氧化性增强,降低了界面平衡C浓度[29],进而促进了脱碳层的形成。另外,-40℃露点退火时,钢板表面形成的连续致密的Si-Mn外氧化层,也一定程度上影响了氧化性气氛的渗透,降低了表层脱碳的倾向。
根据金属氧化物标准Gibbs自由能变化和温度关系图[30]可知,形成SiO2的Gibbs自由能变化低于MnO,在相同的退火温度下,形成SiO2所需的平衡氧分压低于MnO。当O向深度方向扩散时,某些位置的氧分压先达到了生成SiO2所需的平衡氧分压,此时Si先被氧化;随着时间的延长,相同的位置氧分压进一步升高,此时Si、Mn同时被氧化,从而形成了芯部为SiO2、外层为Si-Mn复合氧化物的结构,相似的结构在Gong等[31]和Zhang等[14]的研究中也曾被观察到。
从露点对te、ti、td1以及wC的影响趋势来看,存在一个可以兼顾外氧化少且脱碳程度轻的区间。如图15所示,各曲线的交点区域可认为是兼顾外氧化和脱碳的区域,此时退火气氛露点位于-20~-10℃之间。
图15
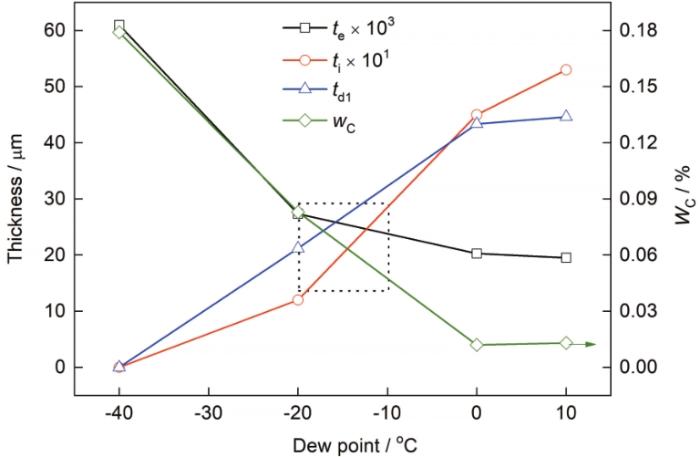
图15 露点对te、ti、td1和wC的影响
Fig.15 Effect of dew point on te,ti, td1, and wC (wC—C content of surface area)
4 结论
(1) 提高连续退火加热段和均热段的气氛露点,可以促使0.2%C-1.5%Si-2.5%先进高强钢中的Si、Mn外氧化转变成内氧化,同时会引起钢板次表层发生明显的脱碳,形成次表层铁素体层,导致钢板表层硬度降低。
(2) 当露点提高到临界值后,继续提高露点对进一步减少外氧化的作用有限,但是内氧化层的厚度和脱碳层的厚度会继续显著增加,因此需要选择合适的露点范围,兼顾外氧化和脱碳层控制。
(3) 在退火温度为870℃、保温120 s、退火气氛为5%H2-N2的工艺条件下,为获得Si、Mn外氧化显著降低,同时内氧化层厚度< 1 μm、次表层仅出现部分脱碳的表面状态,合适的露点为-20~-10℃。
来源--金属学报