分享:9%Cr合金钢在含Cl-环境中的初期腐蚀行为及局部腐蚀起源
陈润农1,2,3, 李昭东,1, 曹燕光1,4, 张启富2, 李晓刚3
1
2
3
4
通过干湿循环测试、SEM、TEM、XRD和电化学方法研究了一种9%Cr合金钢在含Cl-环境中的初期腐蚀行为,探讨了复合夹杂物(Mg, Si, Al)O-MnS和富Cr的M23C6对其局部腐蚀行为的影响。结果表明,合金钢初期耐蚀性能较09CuPCrNi提高了12倍以上,在360 h的干湿循环过程中发生局部腐蚀,锈层下的蚀坑深度符合Lognormal分布,蚀坑的最大深度(Dmax)与平均深度(Dave)随时间(t)变化规律分别符合幂函数Dmax = 8.4844 × t 0.65717和Dave = 7.3181 × t 0.53866。合金钢锈层的致密度和α / γ* (α-FeOOH / (γ-FeOOH + Fe3O4 + β-FeOOH)含量比)随腐蚀时间延长均不断增加,但高Cr的添加推迟了腐蚀进程,使得锈层未完整覆盖表面,仅提供了有限的保护能力,因而根据幂函数拟合失重数据得到的指数大于1。复合夹杂物(Mg, Si, Al)O-MnS通过MnS或单一MgO区域的局部优先溶解导致亚稳态点蚀,但其在2%NaCl溶液中浸泡300 min并未诱发周围基体溶解,而富Cr的M23C6析出导致基体的Cr消耗是优先诱发局部腐蚀的主要原因。
关键词:
海岸带经济的发展离不开基础工程设施的支撑,而海洋环境下金属材料的腐蚀问题严重制约了海洋工程技术的发展[1]。近年来我国对南海海域开发与建设愈发重视,而南海苛刻的高湿热、高盐粒和强辐射的海洋大气环境对工程结构用钢提出了更高的要求,为了满足我国海洋工程发展的需要,进一步探索更高耐蚀性能的钢种是十分必要的[2]。
国内现有的耐候钢种,如09CuPCrNi与09CuPTiRE等,无法直接应用于高湿热海洋气候,相关研究[3,4]指出,其在万宁(濒近南海)暴晒8 a后便出现了腐蚀加速的现象,原因在于耐候钢无法在海洋大气下形成保护性锈层,Cl-会通过增大锈层颗粒进而降低其保护性,且这种影响在高Cl-浓度的作用下更加显著[5,6]。日本的3Ni先进耐候钢是应用于海洋大气环境下的成熟钢种,虽然研究证实其可未经涂装直接应用于中等盐度的海洋大气环境[7],但是在高盐度南海环境下直接应用3Ni先进耐候钢仍然存在诸多难题[8,9]。相对于不锈钢而言,Cr含量为2.5%~10% (质量分数,下同)的合金钢以非常低的成本提供了腐蚀性能的边际收益[10],其具有应用于高湿热海洋大气环境下的巨大潜力。Cr元素能够有效提高低碳钢的耐蚀性能,近年来有不少研究[11,12]关注于含Cr耐候钢的腐蚀行为及其耐蚀机制。在海洋大气环境下,Cr可以在锈层的内侧富集,促进钢基体表面形成无裂纹的均匀锈层[13]。Zhang等[14,15]通过在青岛的大气暴晒实验确定了Cr对耐海洋大气腐蚀的有益作用,认为当Cr含量超过2%时,可以获得纳米级的均匀锈层颗粒,提高了锈层的防护能力;而当Cr含量超过4%时可以获得阳离子选择性的锈层,抵抗侵蚀性粒子渗透的能力进一步增强。Yamashita等[16,17]提出Cr3+可以与O2-配对,占据α-FeOOH晶体结构中FeO3(OH)3八面体网格内的双链空位(double chains of vacant sites),形成一种具有阳离子选择性的Cr代α-FeOOH,这是高Cr耐候钢表现出极佳耐Cl-能力的重要原因。在海洋大气环境下,目前关于含Cr钢的腐蚀行为研究主要集中于Cr含量在5%以下的钢种,为了获得更高的耐大气腐蚀性能,进一步提高Cr含量值得深入研究。基于此,本工作设计并研究了一种9%Cr合金钢在Cl-环境中的初期腐蚀特征,同时探究了夹杂物和M23C6与其局部腐蚀行为之间的联系,相关数据可以为发展新型海洋大气环境用耐蚀钢提供参考。
1 实验方法
1.1 实验材料
在低碳钢的成分基础上添加Cr、Ni、Cu等耐蚀合金元素获得一种低碳9%Cr耐蚀合金钢(后文简称9Cr钢),生产工艺流程如图1所示。9Cr钢采用真空感应炉熔炼,铸锭加热至1200℃保温1 h后锻造开坯,终锻温度大于900℃。1200℃均匀化处理1 h,1100℃开轧,经6道次轧制到2.5 mm厚,终轧温度为850℃,空冷至680~730℃后送入710℃电阻炉保温30 min以模拟卷取过程,随炉冷却至200℃后出炉空冷至室温,最后将热轧板在650℃退火4 h后出炉空冷。经测量所得9Cr钢的化学成分如表1所示(其中09CuPCrNi作为9Cr腐蚀性能的对比钢),其室温抗拉强度为591 MPa,屈服强度为443 MPa,断后延伸率为19%。
图1

图1 9Cr钢的制造工艺示意图
Fig.1 Schematic of manufacturing process of 9Cr steel
表1 9Cr和09CuPCrNi钢的化学成分 (mass fraction / %)
Table 1
Steel | C | Si | Mn | Cr | Ni | Co | Cu | Fe |
---|---|---|---|---|---|---|---|---|
9Cr | 0.02 | 0.50 | 0.90 | 8.98 | 1.50 | 0.30 | 0.015 | Bal. |
09CuPCrNi | 0.10 | 0.40 | 0.30 | 0.30 | 0.02 | - | 0.300 | Bal. |
1.2 微观组织表征
利用线切割从9Cr钢板表面切取金相样品,样品依次采用320、600和1000号砂纸粗磨,然后进行机械抛光,利用Quanta650扫描电子显微镜(SEM)和配套的Oxford X-Max50能谱仪(EDS)检测钢中夹杂物的形貌与成分。利用Tecnai G2 F20透射电子显微镜(TEM)和配套的TEAMTM EDS检测9Cr钢中M23C6的分布和成分。TEM样品由机械研磨减薄至50 μm以下,冲压成直径3 mm的圆片,然后在-20℃下利用MTP-1A减薄仪将圆片电解双喷为薄膜样品,电解溶液为10% (体积分数)高氯酸酒精,电解电流为50~80 mA。
1.3 干湿循环测试与腐蚀产物表征
利用LF-65A室内干湿循环试验箱研究9Cr钢在Cl-环境下的初期腐蚀行为,对比钢为09CuPCrNi。实验温度维持在(45 ± 2)℃,箱内空气的相对湿度为70% ± 5%,1次干湿交替的时间为(60 ± 2) min,其中湿润时间为(12 ± 2) min,溶液为pH值在6.5~7.5的2%NaCl (质量分数)。对9Cr和09CuPCrNi进行时间为72、168、264和360 h的加速腐蚀实验,每种钢在每个周期下各准备7个样品,其中3个样品(40 mm × 60 mm × 3 mm)用于腐蚀速率测定,3个样品(10 mm × 10 mm × 3 mm,一端焊接导线后用树脂镶嵌,裸露面积1 cm2)用于电化学测试,1个样品(15 mm × 20 mm × 3 mm)用于锈层形貌观察。所有样品表面均用800号砂纸磨平,用丙酮清洗表面油污后干燥待用。
样品按预定的腐蚀时间分批取出,使用配比为500 mL HCl + 500 mL蒸馏水 + 20 g六次甲基四胺的除锈液去除表面腐蚀产物,不同时间干湿循环后的腐蚀失重与腐蚀速率分别采用
式中,W为腐蚀失重,g/cm2;W0为样品腐蚀前质量,g;Wt为样品除锈后的质量,g;S为样品表面积,cm2;ρ为样品密度,取7.8 g/cm3;V为腐蚀速率,mm/a;t为腐蚀时间,h。
利用GX53光学显微镜(OM)统计除锈样品表面的蚀坑参数,蚀坑直径按照截线法测量,腐蚀坑深度测量方法为:在200倍的OM下分别对蚀坑边缘和底部进行聚焦,记录下2次聚焦完成时细准焦螺旋对应的刻度值,2次刻度值之差即为蚀坑深度。记录深度大于5 μm的蚀坑,统计区域为挂片的上下2个表面,测量时舍弃靠近样品边缘的蚀坑。
采用SEM和EDS观察表面和截面的腐蚀形貌、分析化学成分,使用JXA8230电子探针(EPMA)表征截面锈层中元素分布特征。收集不同腐蚀时间下的腐蚀产物粉末颗粒,利用Bruker D8X X射线衍射仪(XRD)对锈层的物相组成进行定性与半定量(RIR法)分析[18],使用Co靶,X射线波长为0.1789 nm,参数为40 kV、300 mA,扫描范围(2θ角)为10°~105°,扫描速率为0.02°/s,测试完成后利用HighScore Plus软件解析XRD谱。
1.4 连续浸泡实验与形貌表征
利用连续浸泡实验研究9Cr钢在Cl-环境下局部腐蚀的萌生与扩展。首先用FM300硬度计在抛光后的金相样品表面打点标记夹杂物,然后使用SEM和EDS检测标记夹杂物的形貌和成分。将金相样品放置在45℃的2%NaCl溶液中浸泡,分别在浸泡5、50和300 min时取出金相样品晾干,采用SEM观察标记夹杂物以及样品整体表面的腐蚀形貌。
1.5 电化学测试
使用Princeton 273A电化学工作站进行电化学测试,采用三电极体系,9Cr钢为工作电极,Pt片为辅助电极,饱和甘汞(SCE)为参比电极,电解质为2%NaCl溶液。动电位极化曲线在0.332 mV/s的扫描速率下获得。电化学阻抗谱(EIS)测试频率范围为10 mHz~100 kHz,正弦波扰动电压幅值为±10 mV。所有电化学测试均在(25 ± 1)℃进行,测试开始前需将样品浸泡30 min以使开路电位稳定。
2 实验结果与分析
2.1 腐蚀动力学与锈层形貌
图2为9Cr和09CuPCrNi钢的腐蚀速率以及失重随时间的变化趋势。不同于09CuPCrNi随时间延长腐蚀速率逐渐降低的趋势,9Cr钢的腐蚀速率先降低后增加,在360 h的初期腐蚀过程中,9Cr钢的腐蚀速率在0.16~0.22 mm/a,这较09CuPCrNi的耐蚀性能提高了12倍以上(图2a),表明其具有优异的耐Cl-腐蚀性能。2种钢在含Cl-环境中的腐蚀失重与时间均呈幂函数变化规律(图2b),值的注意的是,9Cr钢的幂指数高于09CuPCrNi且大于1,表明其初期腐蚀速率呈增大趋势。耐候钢的腐蚀速率会经历增加、下降而后趋于稳定的过程[19],Morcillo等[20]指出耐候钢需要一定时间的暴晒才能使锈层稳定,从而使腐蚀速率降低并趋于稳定,不同钢种达到腐蚀速率稳定的周期是不同的。9Cr钢由于耐蚀性能远高于09CuPCrNi钢,相比于09CuPCrNi钢,其腐蚀进程被显著推迟,这是导致其幂指数高于1的主要原因。
图2

图2 9Cr和09CuPCrNi钢的腐蚀速率和失重随时间的变化趋势
Fig.2 Corrosion rates (a) and weight losses (b) of 9Cr and 09CuPCrNi steels as a function of time (W—weight loss, t—corrosion time)
9Cr钢腐蚀不同时间后的表面腐蚀形貌与EDS结果分别如图3和表2所示。由宏观腐蚀形貌可知,样品表面均呈现典型的局部腐蚀特征(图3a1~a4)。腐蚀72 h后,局部区域优先溶解,表面有盐颗粒沉积(图3b1),EDS结果表明O含量仅为3.96%,化学成分与基体相近,表明此时局部腐蚀区域尚未形成致密锈层。腐蚀168 h后,已腐蚀区域面积向周围扩展,局部腐蚀区域的边缘可见疏松的锈层颗粒(图3b2),而中心区域锈层明显致密但存在裂纹,对图3b2中方框区域放大可见棉球状腐蚀产物(图3c2),这与文献[21]报道的α-FeOOH形态相吻合,EDS结果表明此时锈层主要成分为Fe与Cr的氧化物。当腐蚀时间进一步延长至264和360 h,表面锈层平整度增加,仍存在一定数量的微裂纹(图3c3和c4)。对比腐蚀不同时间后锈层的EDS结果可知,表面锈层中的Cr含量随腐蚀时间延长逐渐降低(表2)。耐候钢锈层为双层结构,外锈层的主要物相为Fe的氧化物与氢氧化物,而Cr倾向于在内锈层富集[22],随腐蚀时间延长,锈层厚度不断增加,这可能也是表面锈层Cr含量逐渐降低的原因。
图3

图3 9Cr钢腐蚀不同时间后的表面宏观和微观腐蚀形貌
Fig.3 Macro (a1-a4) and micro (b1-b4) surface corrosion morphologies of 9Cr steels corroded for different time and the high-resolution SEM images (c1-c4) corresponding to the square areas in Figs.3b1-b4
(a1-c1) 72 h (a2-c2) 168 h (a3-c3) 264 h (a4-c4) 360 h
表2 图3c1~c4中方形区域对应的EDS结果 (mass fraction / %)
Table 2
Position | O | Cr | Mn | Fe | Co | Ni | Cl | C |
---|---|---|---|---|---|---|---|---|
1 | 3.96 | 8.65 | 1.18 | 83.86 | 0.35 | 2.00 | - | - |
2 | 42.28 | 7.20 | - | 46.31 | - | - | 3.43 | 0.78 |
3 | 46.00 | 6.08 | - | 45.72 | - | - | 2.20 | - |
4 | 41.90 | 3.67 | - | 49.21 | - | - | 5.22 | - |
9Cr钢腐蚀不同时间后局部腐蚀区域的截面锈层形貌及主要元素分布特征如图4所示。腐蚀不同时间后,截面锈层均呈半圆状,且朝着钢基体一侧生长,从O的分布可辨别锈层边界,锈层内Ni均匀分布而Cr明显富集(图4e~h)。腐蚀72 h后,锈层较薄且疏松多孔(图4a),为Cl-的渗透提供了通道[23],从而进一步诱发锈层下基体溶解。腐蚀168 h后,锈层厚度增加,但锈层中间区域仍疏松多孔,而且锈层与基体界面处也存在裂纹(图4b),阻碍Cl-渗透的能力较差。腐蚀264 h后,锈层内部缺陷进一步减少,虽然锈层中间区域仍然存在孔隙和疏松结构,但在基体上方已形成一层致密的半圆环状锈层(图4c),阻碍Cl-渗透的能力得到增强。腐蚀360 h后,锈层为致密性良好的完整半圆状(图4d),具有更强阻碍Cl-渗透的能力。受EDS分辨率限制,锈层中含量较低的Ni和Co无法被精准表征,因而采用EPMA分析腐蚀360 h后锈层的主要元素分布特征,结果如图5所示。在锈层中,Fe含量低于基体,Cr含量显著高于基体,而Ni和Co的含量则与基体相近。锈层最外侧存在Fe富集,锈层内侧则以Cr层与Fe层交替分布。Ni于锈层中为层状分布,而Co在锈层中分布较为均匀。
图4

图4 9Cr钢腐蚀不同时间后的锈层截面形貌和相应的主要元素分布
Fig.4 Cross-sectional morphologies of rust layer (a-d) and corresponding main element distributions (e-h) of 9Cr steels after corrosion for 72 h (a, e), 168 h (b, f), 264 h (c, g), and 360 h (d, h)
图5

图5 9Cr钢腐蚀360 h后锈层截面的EPMA面扫描图
Fig.5 Cross-sectional morphology (a) and EPMA elemental mappings (b-e) of the cross-sectional rust layer of 9Cr steel after corrosion for 360 h
2.2 电化学性能及腐蚀产物
腐蚀不同时间后9Cr钢的EIS及拟合等效电路图如图6所示。经不同时间腐蚀后,Nyquist图均为半圆形电容弧(图6a),表明电化学反应过程均受电荷转移控制[24]。随腐蚀时间延长,电容弧的直径先增加后减小,其中在168 h获得最大值,表明耐蚀性能先增强后降低。由图6b可看出,经不同时间腐蚀后的最大相位角均位于1~10 Hz的中间频率区域,这是典型的电容响应特征[25]。同时,最大相位角低于90°,说明电极偏离理想电容特性,因而进行EIS拟合时需要用常相位元件来代替纯电容C[26]。低频0.01 Hz对应的模抗值可看成是溶液电阻与极化电阻之和,高频105 Hz对应的模抗值为溶液电阻[27],结合图6c可知,腐蚀不同时间后,溶液电阻均小于10 Ω·cm2,而极化电阻则先增大后降低。
图6

图6 9Cr钢腐蚀样品在2%NaCl溶液中的EIS及拟合等效电路图
Fig.6 Nyquist plots (a), phase angle plots (b), modulus plots (c), and equivalent circuit (d) of corroded 9Cr steels in 2%NaCl solution (Zim-imaginary part of impedance, Zre-real part of impedance, |Z|-impedance modulus, Rs-resistance of electrolyte, Qdl-constant phase element of double layer, Rp-polarization resistance)
基于以上分析,同时考虑到9Cr钢在腐蚀360 h后锈层尚未完整覆盖表面(图3a1~a4),锈层对基体保护能力有限,所以采用如图6d所示的等效电路拟合EIS,其中Rs为溶液电阻,Qdl为电极表面双电层的常相位元件,Rp为极化电阻(可看作电荷转移电阻与锈层电阻之和),相应的曲线拟合结果见图6a~c,拟合数据如表3所示。可见,Rp为先增加后减小的规律,这与图2a中腐蚀速率的变化规律相吻合。
表3 9Cr钢腐蚀样品在2%NaCl溶液中的EIS拟合数据
Table 3
Time / h | Rs / (Ω·cm2) | Y0 / (10-3 s-n ·Ω-1·cm-2) | n | Rp / (Ω·cm2) | χ2 / 10-3 |
---|---|---|---|---|---|
72 | 1.127 | 6.154 | 0.6797 | 778.1 | 3.877 |
168 | 1.727 | 3.841 | 0.6068 | 1694.0 | 1.999 |
264 | 2.774 | 3.662 | 0.6414 | 860.2 | 1.549 |
360 | 4.012 | 9.520 | 0.5094 | 704.8 | 2.809 |
图7为9Cr钢腐蚀不同时间后的腐蚀产物粉末XRD谱及半定量结果。可见,不同腐蚀时间后的锈层主要物相种类相同,均包含α-FeOOH、γ-FeOOH与Fe3O4/γ-Fe2O3,但3种产物的含量存在明显差异。随腐蚀时间延长,Fe3O4/γ-Fe2O3的含量逐渐降低而α-FeOOH与γ-FeOOH的含量均不断增加,除腐蚀72 h以外,α-FeOOH含量均高于γ-FeOOH。锈层保护能力主要依赖α-FeOOH,α-FeOOH具有相对致密的结构且稳定性高于γ-FeOOH。γ-FeOOH具有氧化性,可作为阴极去极化剂参与电化学反应,加速腐蚀进程。Fe3O4是良导体,可作为有效的电子通道,同样促进电化学反应[23,28]。锈层的保护能力由多种腐蚀产物共同决定,一般可通过计算α / γ* (α-FeOOH / (γ-FeOOH + Fe3O4 + β-FeOOH)含量比)[29]的数值来评价保护能力强弱,相关结果见图7b。可以看出,9Cr钢的锈层保护能力随腐蚀时间延长不断提高。
图7

图7 9Cr钢腐蚀不同时间后表面腐蚀产物的XRD谱和半定量结果
Fig.7 XRD spectra (a) and semi-quantitative results (b) of the scraped rust formed on 9Cr steel surface after corrosion for different time (α / γ*-ratio of the content of α-FeOOH to the content of γ-FeOOH and Fe3O4)
腐蚀失重和EIS均表明9Cr钢的初期腐蚀速率先降低后增加,这与XRD测试所得的锈层保护能力随腐蚀时间延长而增强的结论相矛盾。实际上,9Cr钢的初期腐蚀进程较09CuPCrNi被显著推迟(图2),360 h腐蚀后锈层未完全覆盖表面(图3a1~a4)。此外,Nyquist图的低频区不存在与离子扩散相关的电容弧(图6a),电化学过程受电荷转移控制[24],这说明锈层所提供的保护能力对腐蚀速率的影响有限。综上,在腐蚀时间为360 h的初期腐蚀进程内,尽管锈层的α / γ*随时间延长不断增加,但由于锈层未完全覆盖样品表面,对整体耐蚀性能贡献很小,所以整体腐蚀速率仍呈上升趋势。
2.3 局部腐蚀坑几何特征及其起源
9Cr钢在腐蚀初期为局部腐蚀特征,由经典失重法计算的平均腐蚀速率无法真实反映其腐蚀发展规律,因而有必要对除锈后样品表面的腐蚀坑参数进行统计。图8给出腐蚀不同时间后的表面蚀坑深度分布特征及变化规律。可见,腐蚀不同时间后的蚀坑深度均符合对数正态分布,蚀坑的最大深度(Dmax)与平均深度(Dave)随时间(t)变化规律分别符合幂函数Dmax = 8.4844 × t 0.65717和Dave = 7.3181 × t 0.53866。图9为9Cr钢在腐蚀不同时间后的蚀坑直径与深度的比值(径深比)。可见,腐蚀不同时间后的蚀坑径深比主要分布于1~10之间,蚀坑的纵向生长趋势随时间延长愈发明显,表明锈层覆盖下的钢基体存在强烈的局部阳极溶解行为。局部腐蚀通常发生于极小区域内,不易察觉但危害很大,严重的局部腐蚀甚至会引发应力腐蚀开裂,进而导致钢材提前失效[30]。明确何种微观因素诱发9Cr钢的局部腐蚀是进一步提高其耐蚀性能的先决条件。
图8
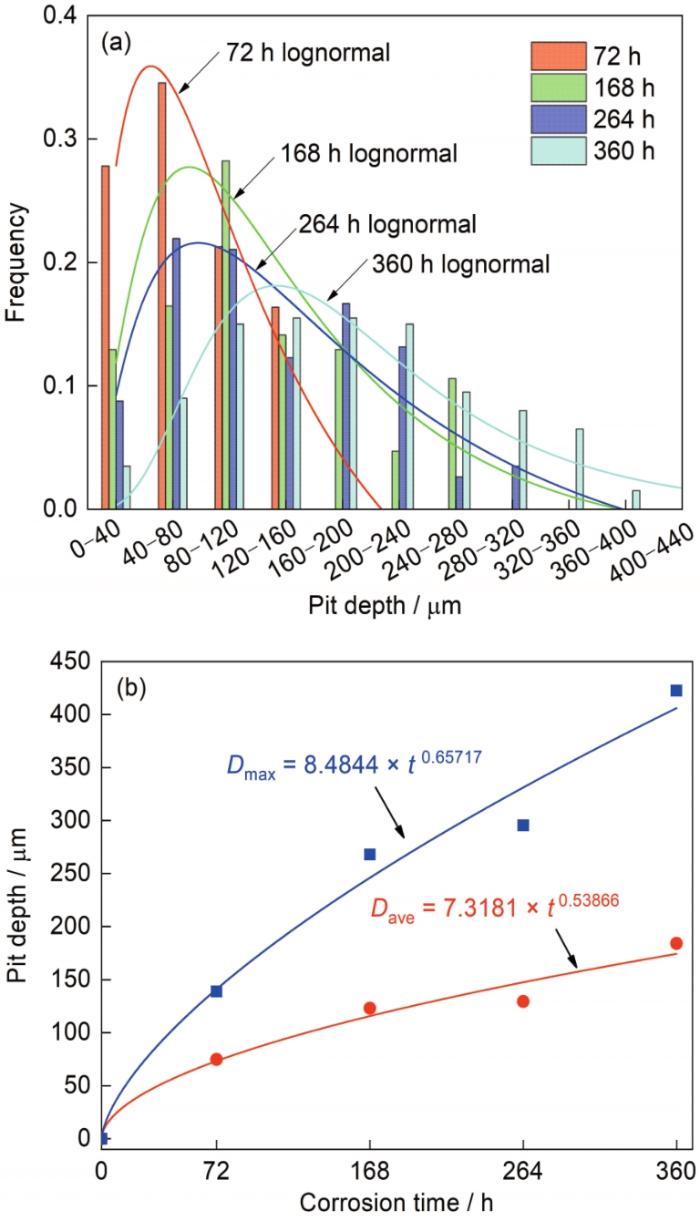
图8 9Cr钢腐蚀不同时间后的表面蚀坑深度分布图和蚀坑深度变化规律
Fig.8 Distributions of pit depth (a) and variation law of pit depth (b) of 9Cr steel surface after corrosion for different time (Dmax-maximum value of the measured pit depth, Dave-average value of the measured pit depth)
图9
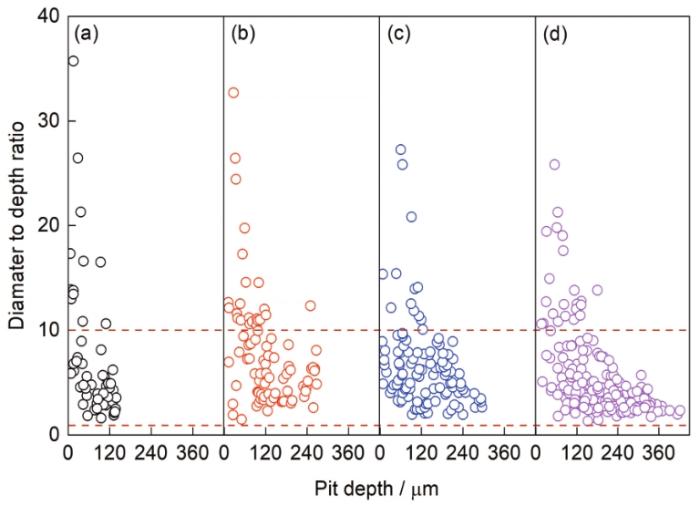
图9 9Cr钢腐蚀不同时间后表面蚀坑的径深比分布图
Fig.9 Distributions of diameter-depth ratio of pits on 9Cr steel surface after corrosion for 72 h (a), 168 h (b), 264 h (c), and 360 h (d)
局部腐蚀与钢基体早期的亚稳态点蚀行为密切相关[31],阳极极化曲线可以反映亚稳态点蚀对应的电流瞬态,结合SEM观察极化测试后9Cr钢的表面形貌可以将亚稳态点蚀与基体微观结构相互联系。图10为9Cr钢在2%NaCl溶液中的极化曲线。可见,阴极为吸氧反应,阳极曲线出现了一段小范围的钝化区间,当外加电位超过点蚀电位(约0.05 V)后电流突增(图10a)。对图10a中方形区域放大观察,钝化区间内的极化曲线明显起伏,存在电流瞬态峰(图10b),这对应典型的亚稳态点蚀行为[32]。电极表面无肉眼可见的腐蚀(图10b插图),表明亚稳态点蚀发生在微观尺度。图11给出了9Cr钢的代表性亚稳态点蚀形貌。可见夹杂物自身的部分区域发生腐蚀,而且夹杂物与基体界面处也有明显的腐蚀。
图10

图10 9Cr钢在2%NaCl溶液中的极化曲线
Fig.10 Polarization curve of 9Cr steel in 2%NaCl solu-tion (a) and the magnified plot corresponding to the square region in Fig.10a (Inset shows the surface morphology of 9Cr sample after polariz-ation test) (b)
图11
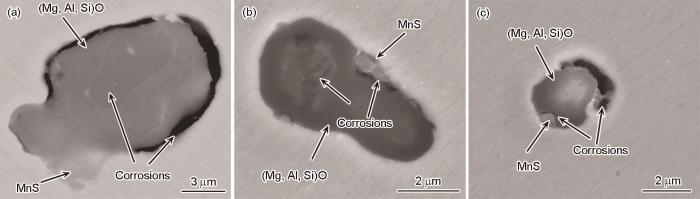
图11 9Cr钢表面代表性亚稳态点蚀形貌
Fig.11 Representative metastable pitting morphologies (a-c) on the surface of 9Cr steel after polarization test
9Cr钢中夹杂物主要为复合型 (Mg, Si, Al)O-MnS,尺寸分布在3~15 μm,其中多数夹杂物尺寸小于6 μm。图12给出钢中2种典型夹杂物的形貌和元素分布,一种含较多MnS (图12a),另一种含少量MnS (图12b)。图13为2种夹杂物在不同浸泡时间后的腐蚀形貌。对于图12a所示夹杂物,浸泡5 min后,MnS发生轻微腐蚀,夹杂物中间的贫Si区域也发生了优先溶解,而样品剩余区域无明显腐蚀发生(图13a1);浸泡50 min后,MnS的腐蚀未加重,而贫Si区域生成较多的腐蚀产物,样品剩余区域仍未发生明显腐蚀(图13a2);浸泡300 min后,夹杂物表面沉积一层腐蚀产物和盐颗粒,但仍可看出由夹杂物诱发的腐蚀未扩展至周围的基体(图13a3)。对于图12b所示夹杂物,当浸泡5 min后,单一MgO区域优先溶解,而掺杂了SiO2或Al2O3的区域未见明显腐蚀(图13b1);当浸泡时间逐渐延长至50和300 min,尽管单一MgO区域的腐蚀进一步加重,但夹杂物没有诱发周围基体腐蚀(图13b2和b3)。
图12

图12 2种典型复合夹杂物的形貌及EDS元素分布图
Fig.12 SEM images and corresponding EDS element maps of MnS-rich (a) and MnS-poor (b) composite inclusions
图13

图13 2种典型复合夹杂物在2%NaCl溶液中浸泡不同时间后的腐蚀形貌
Fig.13 Corrosion morphologies of MnS-rich (a1-a3) and MnS-poor (b1-b3) composite inclusions immersed in 2%NaCl solution for 5 min (a1, b1), 50 min (a2, b2), and 300 min (a3, b3)
值得注意的是,浸泡300 min后,基体的其余区域发生严重局部腐蚀,相应形貌和蚀坑EDS线扫描结果如图14所示。由图14c和d可知,蚀坑内不存在夹杂物,蚀坑区域O与Cr含量显著高于周围区域,其主要为富Cr贫Fe的腐蚀产物。此外,蚀坑区域的C明显富集,推测此种局部腐蚀行为与钢中的碳化物相关。图15为9Cr钢中碳化物的TEM像及成分分析。可见,碳化物呈椭圆形在基体中均匀分布,其中大多数粒子尺寸较小,存在少量大尺寸粒子(图15a),EDS与选区电子衍射(SAED)花样表明这些碳化物为富Cr的M23C6 (图15b和c)。由图15d可知,M23C6附近区域(图15d位置2~4)较无碳化物析出区域(图15d位置5)的Cr含量降低了约0.5%,证明M23C6附近存在贫Cr区。
图14

图14 9Cr钢在2%NaCl溶液中浸泡300 min后的典型局部腐蚀形貌及元素分布
Fig.14 Local corrosion morphologies (a, b) of 9Cr steel immersed in 2%NaCl solution for 300 min and main element distributions (c, d) around a corrosion pit in Fig.14b (Inset in Fig.14a shows the corresponding high magnified image)
图15

图15 9Cr钢中M23C6的分布特征和成分分析
Fig.15 Distribution characteristics and composition analysis of M23C6 in 9Cr steel (Inset in Fig.15b shows the SAED pattern of zone 1)
(a) low magnified TEM image (b) high magnified TEM image
(c) EDS of zone 1 in Fig.15b (d) Cr poor phenomenon near M23C6
局部腐蚀萌生于金属表面的化学或物理非均质区域,如夹杂物、第二相粒子以及内部缺陷等[33~35],对于9Cr钢而言,复合夹杂物中的MnS以及无SiO2或Al2O3掺杂的MgO区域会发生优先溶解而诱发亚稳态点蚀(图10~13),但基体发生的快速局部腐蚀却是由钢中富Cr的M23C6引起的(图14和15)。MnS为活性夹杂,腐蚀电位低于钢基体,可以和钢基体形成微电偶而诱发自身溶解[33,34]。Li等[35]通过研究X100管线钢中夹杂物的腐蚀行为发现,相比于无SiO2的钙镁铝酸盐类夹杂物,硅酸盐类夹杂物更难诱发基体腐蚀,这与图13中复合夹杂物的腐蚀行为相吻合。Tyurin等[36]总结了几种非金属夹杂物发生腐蚀的热力学倾向,Al2O3与SiO2在H2O溶液中发生溶解反应的Gibbs自由能变化ΔG > 0,因而均为稳定相。由此可知,(Mg, Si, Al)O中掺杂了Al2O3与SiO2的部分必然具有更高的热力学稳定性,反之单一MgO区域的热力学稳定性更低,因而容易发生优先溶解。富Cr的M23C6诱发基体的局部腐蚀行为可以从贫Cr的角度来理解,不锈钢经验耐点蚀当量PREN = wCr + 3.3wMo + 16wN (其中,w为元素的质量分数,%)[37]。9Cr未添加Mo元素,同时可认为基体中N含量均匀分布,因而PREN的区别主要由Cr含量决定。由图15d可知,贫Cr区域(位置2~4)的PREN必然低于未析出铬碳化物区域(位置5),从而降低相应区域的耐Cl-侵蚀性能[38]。此外,M23C6周围还伴随一定量的位错塞积(图15b),这些线缺陷属于热力学不稳定位置,因而提供了更高的腐蚀驱动力[39,40],一旦M23C6周围的贫Cr区萌生腐蚀后,位错塞积的高活性区域会促进基体的阳极活化溶解反应,进而加速局部腐蚀进程。
3 结论
(1) 9%Cr合金钢在含Cl-环境中的初期耐蚀性能较09CuPCrNi提高了12倍以上,在360 h的干湿循环过程中表现为典型的局部腐蚀特征。锈层覆盖下的蚀坑深度符合对数正态分布,蚀坑的最大与平均深度随时间变化规律分别符合幂函数Dmax = 8.4844 × t 0.65717和Dave = 7.3181 × t 0.53866。
(2) Cr元素富集在9%Cr合金钢的局部腐蚀锈层中,随腐蚀时间延长,锈层的物理致密度和α / γ*比值均不断增加。高Cr含量推迟了腐蚀进程,在360 h的干湿循环过程中锈层没有完全覆盖表面。电化学反应过程受电荷转移控制,锈层提供的保护能力有限,因而腐蚀速率呈上升趋势,这使得幂函数拟合失重得到的指数值大于1。
(3) 相比于(Mg, Si, Al)O-MnS,富Cr的M23C6对9%Cr合金钢局部耐蚀性能的危害更大。复合夹杂可以通过MnS或单一MgO区域的局部优先溶解而导致亚稳态点蚀,但其在2%NaCl溶液中浸泡300 min并未诱发周围基体溶解,而钢中富Cr的M23C6析出导致周围基体的Cr消耗是诱发局部腐蚀的主要原因。
来源--金属学报