分享:基体表面喷丸处理对纳米晶涂层循环氧化行为的影响
黄鼎1, 乔岩欣,1, 杨兰兰1, 王金龙2, 陈明辉2, 朱圣龙3, 王福会2
1
2
3
采用磁控溅射技术分别在抛光和喷丸处理后的镍基单晶高温合金基体上制备纳米晶涂层,并研究了2种涂层在1100℃下的循环氧化行为。采用XRD、SEM和EDS表征涂层的物相组成和微观形貌。结果表明,1100℃下2种纳米晶涂层的循环氧化增重趋势基本一致,均能在表面形成致密的氧化膜,展现出优异的抗氧化性能。2种纳米晶涂层与基体的界面及界面附近区域的微观形貌演变有所差异,随着氧化实验的进行,在抛光基体/涂层界面处涂层一侧观察到γ'相的持续形成;在喷丸基体/涂层界面处涂层一侧未发现此现象,而在基体一侧观察到γ'相不断长大。
关键词:
镍基单晶高温合金由于其优异的高温力学性能[1,2],成为航空燃气涡轮叶片的首选材料。为了保障叶片在高温下的力学性能,镍基单晶高温合金往往具有较高含量的难熔元素(Ta、W、Mo和Re等),和相对较少的抗高温氧化有益元素(Al和Cr)[3,4],因此,其抗氧化性能和抗热腐蚀性能往往难以同时达到最优化。为了解决上述矛盾,常常在合金上施加高温防护涂层,如铝化物涂层[5,6]、MCrAlY包覆涂层[7,8]等。而无论合金还是涂层,都可以使用各种表面处理技术,以使合金(或涂层)表层改性,达到提高合金(或涂层)抗氧化性能的目的[9,10]。
研究[10~12]表明,通过适当的表面处理技术改性合金(或涂层)表层,引入大量的位错和晶界,增加合金(或涂层)内部的扩散通路,有助于Al或Cr元素向外扩散,促进合金(或涂层)表面连续外氧化层的形成。而喷丸、喷砂处理作为简单、高效的表面处理工艺,常常被用于改善合金(或涂层)的抗高温氧化性能[10,13,14]。Tan等[15]研究了喷丸处理对850℃下800H合金循环氧化行为的影响,结果表明,经过喷丸处理后的合金表面的晶粒得到细化,从而加强了Cr的扩散,有利于合金表面Cr和富Cr氧化物的形成,有效提高了800H合金的抗氧化性能。Ni等[16]研究了1050℃下喷砂、喷丸表面处理工艺对超音速火焰喷涂NiCrAlY涂层等温氧化行为的影响,结果表明,2种表面处理工艺都促进了涂层表面连续Al2O3的生成,改善了涂层的抗高温氧化性能。
表面处理工艺除了改性合金(或涂层)表面,也会改变合金(或涂层)的表面粗糙度,表面粗糙度也是影响合金(或涂层)高温氧化行为的一个重要因素[17,18]。Wang等[19]的研究表明,表面改性区能够促进DD3单晶合金表面连续Al2O3膜的形成,表面粗糙度越大,形成Al2O3层的速率越快,但也会加速氧化膜的剥落。Gil等[20]研究发现,粗糙表面的NiCoCrAlY涂层中,表面波峰与波谷处呈现出不同的氧化行为,波谷处Y从涂层内部到涂层表面的扩散路径比波峰处更短,较小的Y-Al氧化物钉扎倾向于在粗糙表面的波谷处优先形成,而Al2O3膜中Y-Al氧化物含量的提高会加速氧化膜的生长速率,所以波谷处Al2O3膜的厚度比波峰处的更厚。因此,在采取喷丸或喷砂处理改善合金(或涂层)的高温氧化性能之前,需要考虑表层改性区和表面粗糙度的综合影响。
近年来,磁控溅射纳米晶涂层因其较好的抗高温氧化性能以及抗剥落性能得到广泛关注[21~23]。不同于传统的高温防护涂层,纳米晶涂层本身具有纳米级的晶粒尺寸和众多的晶界扩散通路[24~26]。因此通过表面处理来改性涂层表层,提高其抗高温氧化性的做法是不适用的,而考虑涂层表面粗糙度对抗高温氧化性能的影响更有意义。Yang等[27]的研究表明,纳米晶涂层的表面粗糙度与高温合金基体的表面粗糙度有关,基体表面粗糙度越大,沉积态涂层的表面粗糙度也越大。因此,可以通过不同的基体表面预处理工艺来获得表面粗糙度不同的纳米晶涂层。然而,对基体进行表面处理时往往会使其表层改性。Chen等[28]研究发现,基体合金的喷砂预处理可以使基体表面纳米晶化,从而促进搪瓷与基体之间Al2O3中间层的形成,提高搪瓷涂层的抗氧化性和抗剥落性,即表层改性区可能会影响涂层的抗高温氧化性能。因此,在经过不同表面处理的高温合金基体上沉积纳米晶涂层时,既需要考虑基体表面粗糙度对纳米晶涂层高温氧化行为的影响,也不能忽略表层改性区的作用。目前有关基体表层改性区对纳米晶涂层氧化行为影响的研究鲜有报道。
为了尽量减小粗糙度对纳米晶涂层氧化行为的影响,选择对基体表面破坏性较小的喷丸处理工艺对基体表面进行处理。因此,本工作采用磁控溅射技术分别在抛光和喷丸处理后的镍基单晶高温合金基体上制备纳米晶涂层,并研究2种涂层在1100℃下的循环氧化行为,通过对比分析其微观形貌和物相组成,探究基体表面抛光、喷丸处理分别对纳米晶涂层氧化行为以及基体/涂层界面微观组织演变的影响。
1 实验方法
实验基体材料采用第二代镍基单晶高温合金N5,合金的名义成分(质量分数,%)为[24]:Cr 7,Co 7.5,Al 6.2,Ta 6.5,Mo 1.5,W 5,Re 3,其他元素 0.24,Ni余量。样品尺寸为直径18 mm、厚2.0 mm。制备涂层前将基体分为2组,一组经过240、400、1000和2000号SiC砂纸打磨后用粒径为1.5 μm的Al2O3抛光膏抛光,另一组经过240和400号SiC砂纸打磨后进行表面喷丸处理(玻璃珠的标准粒径为0.178 mm,压力0.4 MPa,处理时间1 min)。表面处理好后用酒精丙酮(体积比3∶1)混合溶液超声清洗20 min以去除表面油污。然后利用JP-500BY型磁控溅射仪制备Y元素改性的纳米晶涂层[29],靶材中Y的质量分数为0.5%,无Re元素,其他成分与基体一致,溅射前需对腔室进行抽气,直至本底真空度小于5 × 10-3 Pa,然后通入Ar气,并打开加热装置使基体温度稳定在200℃,通过调节进气流量和光栅阀使腔室真空度稳定在0.15 Pa,随后开始溅射,溅射功率为2 kW,溅射时间10 h,涂层厚度37~40 μm。
将制备好的样品置于1100℃的立式循环氧化炉中进行氧化实验。实验中以炉内60 min、炉外空冷10 min计为1 cyc,分别在5、20、40、60、80、100 cyc后进行称重。每组试样的氧化增重为3个平行试样氧化增重的平均值。
利用X' Pert PRO型X射线衍射仪(XRD)测定磁控溅射纳米晶涂层的物相结构;使用Inspect F50型扫描电子显微镜(SEM)观察涂层的表面和截面微观形貌,并结合其配备的X-Max型能谱仪(EDS)分析氧化膜、涂层、基体合金中元素的含量及其分布,综合分析涂层的氧化行为。
2 实验结果
2.1 纳米晶涂层沉积态微观形貌
图1是利用磁控溅射技术在经过不同表面处理的N5单晶高温合金上沉积的N5纳米晶涂层的截面和表面形貌。由图可知,相对于沉积在喷丸高温合金表面的纳米晶涂层,沉积在抛光高温合金表面的纳米晶涂层与基体的界面更加平滑,表面更加平坦。
图1

图1 沉积在抛光和喷丸N5单晶高温合金表面上的纳米晶涂层的截面和表面形貌
Fig.1 Cross-sectional (a, c) and surface (b, d) morphologies of the as-sputtered nanocrystalline coatings deposited on the polished (a, b) and shot peened (c, d) N5 single crystal superalloys
2.2 纳米晶涂层循环氧化动力学
图2a是2种纳米晶涂层在1100℃下循环氧化的动力学曲线。在100 cyc中,2种纳米晶涂层均未发生明显的失重,氧化膜具有一定的抗剥落性能。2种纳米晶涂层的循环氧化增重趋势大致相同,在前20 cyc中,氧化增重较快,20 cyc后,沉积在抛光、喷丸高温合金表面的纳米晶涂层的氧化增重分别为0.259和0.282 mg/cm2,2者氧化增重差为0.023 mg/cm2。在20~100 cyc之间,2者进入缓慢增重过程,同时,2种涂层的氧化增重差也在不断减小,100 cyc后,沉积在抛光、喷丸高温合金表面的纳米晶涂层的氧化增重分别为0.385和0.390 mg/cm2,2者氧化增重差仅为0.005 mg/cm2。
图2
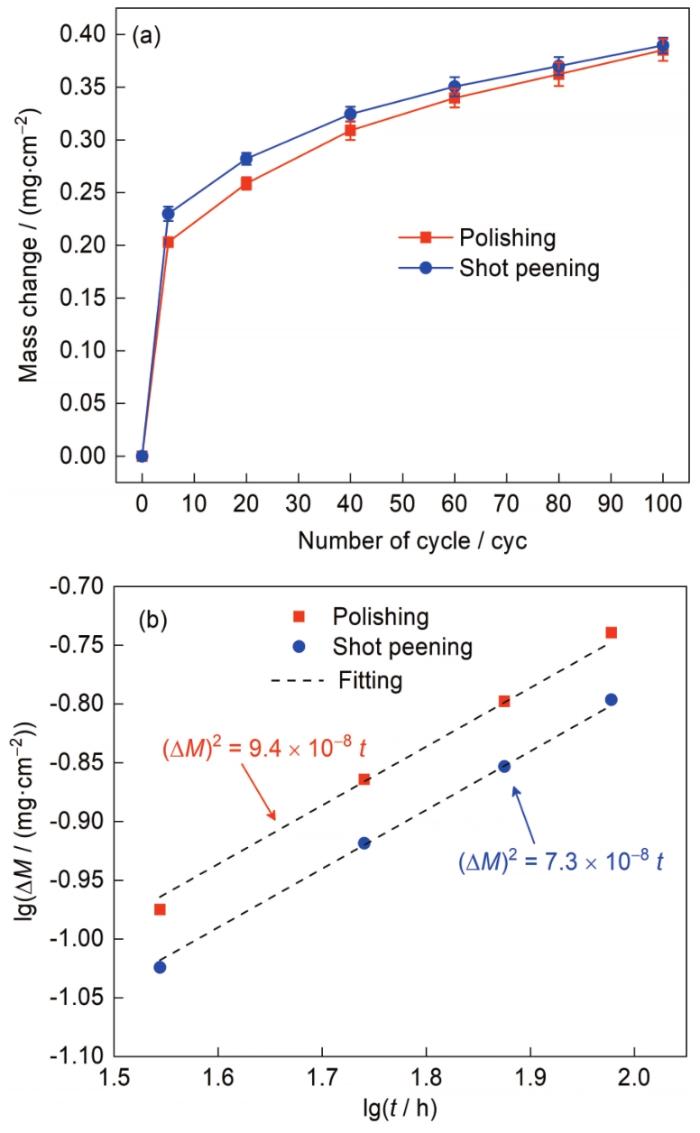
图2 纳米晶涂层1100℃循环氧化动力学曲线和单位面积的质量增重(ΔM)与氧化时间(t)的拟合曲线
Fig.2 Cyclic oxidation kinetics of nanocrystalline coatings at 1100oC (a) and lg(ΔM)-lgt fitting cu-rves (b) (ΔM—mass gain per unit area, t—oxidation time)
为了更好地了解各组样品的氧化规律,2种纳米晶涂层的单位面积的质量增重(ΔM)与氧化时间(t)的拟合曲线(lg(ΔM)-lgt)如图2b所示,为了避免初期氧化中的不稳定因素对拟合结果干扰,20 cyc前的氧化增重数据在曲线拟合处理时并没有录入。进一步研究发现,在20 cyc后的缓慢增重阶段,2种纳米晶涂层的循环氧化增重数据符合大多数高温合金所遵守的抛物线规律:
式中,k为氧化速率常数,在本工作中,沉积在抛光、喷丸高温合金表面的纳米晶涂层的k分别为9.4 × 10-8和7.3 × 10-8 mg2/(cm4·s),即沉积在抛光高温合金表面的纳米晶涂层的k大于沉积在喷丸高温合金表面的纳米晶涂层,这表明基体喷丸处理会影响纳米晶涂层在缓慢氧化阶段的氧化规律,需要进一步探索。
2.3 纳米晶涂层物相组成
图3为1100℃ 2种纳米晶涂层在不同循环次数后的XRD谱。可见,氧化前2种涂层均由单一γ相组成,γ相为镍基奥氏体,其他多种元素以固溶的形式存在于γ相中[24]。在1100℃下100 cyc后2种纳米晶涂层的相组成也基本相同,均为涂层基体相γ/γ'和氧化产物Al2O3,其中,γ'相主要为Ni3Al。
图3

图3 1100℃下纳米晶涂层在不同循环次数后的XRD谱
Fig.3 XRD spectra of the nanocrystalline coatings after cycle oxidation with different cycles at 1100oC
2.4 纳米晶涂层循环氧化后微观形貌
图4为1100℃下2种纳米晶涂层100 cyc后的截面和表面形貌。可以看出,2种纳米晶涂层的氧化膜与涂层之间结合较好,氧化膜内部没有明显裂纹(图4a和c),EDS分析表明,深色氧化膜主要含Al和O元素,结合XRD推测氧化物为α-Al2O3。由图4b和d可见,2种纳米晶涂层的氧化膜表面均分布着大量颗粒氧化物,XRD结果显示表面颗粒氧化物主要含Al和O元素,可以判断氧化物为α-Al2O3,与截面结果相对应。
图4

图4 沉积在抛光和喷丸高温合金表面上的纳米晶涂层在1100℃下100 cyc后的截面和表面形貌
Fig.4 Cross-sectional (a, c) and surface (b, d) morphologies of nanocrystalline coatings deposited on polished (a, b) and shot peened (c, d) superalloys after 100 cyc at 1100oC
2.5 高温合金基体/纳米晶涂层界面微观组织演变
1100℃下不同循环次数后的抛光高温合金基体/纳米晶涂层界面微观组织如图5所示,沿着左图中虚线的EDS线扫描结果见右图。在开始循环氧化实验之前,界面左侧的单晶合金基体中γ'相以立方体形有序分散于具有fcc结构的γ相中[30,31],而右侧纳米晶涂层与基体之间几乎不存在任何的色差,EDS线扫描结果表明涂层内部成分均匀(图5a)。5 cyc之后,涂层主要由深色基体相以及均匀分布于深色相中的浅色颗粒相构成,而在靠近界面的区域,浅色颗粒相有向基体一侧运动的趋势,EDS结果表明,在依次经过浅色颗粒相和深色基体相时,Al元素强度呈现先升高后降低的趋势,而Cr元素强度呈现相反的变化趋势(图5b)。在20 cyc之后,涂层内部浅色颗粒相长大,且界面处涂层一侧浅色相聚集区域持续扩大,这种变化趋势更加明显(图5c)。而在100 cyc后,界面附近浅色相聚集区域宽度已达到6 μm左右,而涂层内部浅色颗粒相尺寸可以达到3 μm左右,且呈现出向界面运动的趋势。同时,随着循环氧化时间的延长,在界面处靠近基体一侧,浅色颗粒相也不断形成、长大,并向基体一侧运动,最终取代以立方体形γ'相有序分散于γ相中的初始组织(图5d)。伴随着界面靠近涂层区域浅色相聚集、并向基体区域一侧运动整个过程,纳米晶涂层与基体之间的原始界面也在不断弥合,图5d中,涂层/基体界面已基本消失。
图5

图5 1100℃下氧化0、5、20和100 cyc后抛光高温合金基体/纳米晶涂层界面微观组织及沿虚线的EDS线扫描结果
Fig.5 Microstructures (left) and EDS line scanning results along the dash lines (right) of the interface between the polished substrate and nanocrystalline coating after 0 (a), 5 (b), 20 (c), and 100 (d) cyc oxidation at 1100oC
图6是1100℃下不同循环次数后的喷丸高温合金基体/纳米晶涂层界面微观组织及EDS线扫描结果,沿着左图中虚线的EDS线扫描结果见右图。在循环氧化开始之前,界面两侧的微观形貌与抛光基体/涂层界面附近区域的微观形貌特征基本一致,EDS线扫描结果表明涂层内部成分均匀,不同点在于,喷丸基体/涂层界面不像抛光基体/涂层界面那么平滑,基体与纳米晶涂层之间的间隙更加明显(图6a)。5 cyc之后,在涂层内部,浅色的颗粒相均匀分布(图6b)。随着循环氧化实验的不断进行,浅色颗粒相也在不断长大(图6c和d)。图6b~d线扫描结果显示,经过涂层内部浅色颗粒相和深色基体相时,Al元素强度亦呈现先升高后降低的趋势,而Cr元素强度则呈现先降低后升高的趋势,这种趋势伴随着浅色颗粒相的长大更加明显。值得注意的是,在界面处靠近涂层一侧,并未出现浅色相聚集的区域,而在界面处靠近基体一侧,大范围的浅色相出现,这些浅色相形状不一,尺寸则远大于左侧涂层内部的浅色颗粒相,且这些浅色相也在不断长大。伴随着界面两侧浅色相的不断长大,喷丸基体与纳米晶涂层界面处部分区域的间隙发生弥合。
图6
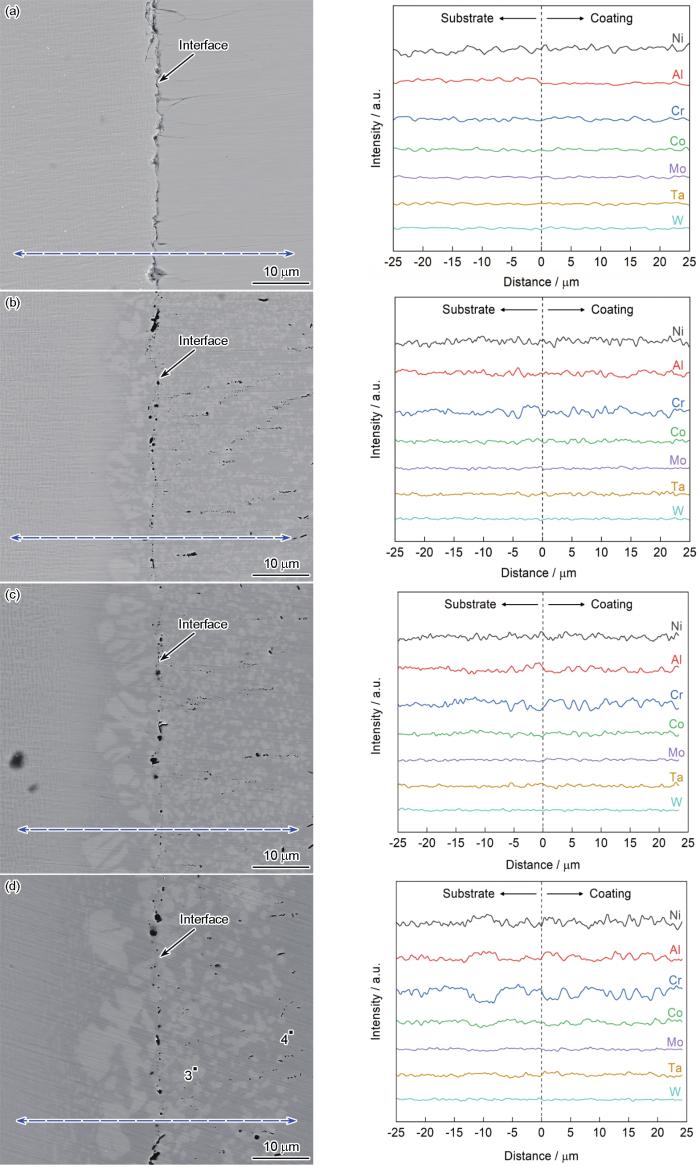
图6 1100℃下氧化0、5、20和100 cyc后喷丸高温合金基体/纳米晶涂层界面微观组织及沿虚线的EDS线扫描结果
Fig.6 Microstructures (left) and EDS line scanning results along the dash lines (right) of the interface between the shot peened substrate and nanocrystalline coating after 0 (a), 5 (b), 20 (c), and 100 (d) cyc oxidation at 1100oC
表1列出了图5d和6d中点1~4的EDS成分分析结果。与图5和6中EDS线扫描结果一致,浅色相中Al的含量高、Cr的含量低,深色相中Al的含量低、Cr的含量高,且浅色相中Ta的含量大概是是深色相中的3倍。
表1 图5d和6d中点1~4的EDS结果 (mass fraction / %)
Table 1
Point | Al | Cr | Co | Mo | Ta | W | Ni |
---|---|---|---|---|---|---|---|
1 | 6.7 | 3.6 | 5.3 | 1.0 | 12.2 | 6.0 | Bal. |
2 | 4.0 | 10.4 | 9.7 | 2.7 | 3.9 | 7.0 | Bal. |
3 | 7.0 | 3.0 | 5.0 | 0.7 | 12.9 | 5.7 | Bal. |
4 | 4.0 | 10.3 | 10.0 | 2.2 | 4.2 | 6.9 | Bal. |
3 分析讨论
3.1 循环氧化动力学
根据2种纳米晶涂层在1100℃下的循环氧化动力学曲线(图2a)可知,前20 cyc中,喷丸高温合金表面的纳米晶涂层的氧化增重比抛光高温合金表面的纳米晶涂层的更大,20 cyc时2者循环氧化增重差可达到0.023 mg/cm2。根据Wagner[32]理论,影响氧化进程由内氧化形式向外氧化形式转换的临界溶解浓度(NB)为:
式中,g* 为氧化物体积分数,NO为合金表面O的摩尔分数,DO为O在合金中的扩散系数,DB为溶质元素的扩散系数,VM和VOX分别为金属及其氧化物的体积。由于磁控溅射纳米晶涂层具有纳米级的晶粒尺寸和众多的晶界扩散通路[24,27],显著降低了形成外Al2O3膜所需要的临界Al含量,因此氧化初期纳米晶涂层表面很快形成一层Al2O3膜。而相对于沉积在抛光合金表面的纳米晶涂层,沉积在喷丸合金表面的纳米晶涂层初始态表面较为粗糙,氧化物的形核位点更多[19,20],相同时间内,生成的氧化物总量会更多。因此,喷丸表面纳米晶涂层的氧化增重要大于抛光表面纳米晶涂层(图2a)。但随着循环次数的增多,2种涂层的氧化增重差在不断减小,100 cyc后,沉积在抛光、喷丸高温合金表面的纳米晶涂层的氧化增重分别为0.385和0.390 mg/cm2,2者氧化增重差仅为0.005 mg/cm2。图2b中的拟合结果也显示,基体喷丸处理对纳米晶涂层在后续稳定阶段的氧化规律存在影响。
3.2 高温合金基体/纳米晶涂层界面微观组织演变
图5和6显示,氧化后纳米晶涂层内部出现了深色基体相以及分布于其中的浅色相,结合图3、表1结果以及Ni-Cr-Al三元相图[33]可知,深色相为γ相,浅色相为γ'-Ni3Al,即纳米晶涂层在氧化过程会发生以下转变[26,34]:
一般情况下,Al、Ta元素主要存在于γ'沉淀相中,Cr、Co、Re、W和Mo元素主要存在于γ基体相中[4,30,35]。随着氧化过程的持续进行,涂层中富Al的γ'相消耗,因此氧化膜下方观察不到γ'相的存在(图4a和c),同时,γ'相耗尽区不断向涂层内部推进(图5和6)。然而图5b~d中,在界面附近涂层一侧,出现γ'相聚集区域,并随着氧化过程的进行持续扩大,从微观形貌看,似乎涂层中的γ'相在朝着基体/涂层界面方向移动。这与涂层中γ'相消耗的事实相悖,即纳米晶涂层底部的γ'相聚集区域是由于其他原因形成的。前面提到,伴随氧化过程的发生,涂层中的γ'相逐渐被消耗,纳米晶涂层中的Al含量逐渐降低。与此同时,γ'相的消耗也会导致Ni、Ta元素溶入涂层中的γ基体相中,暂时提高γ基体相中Ni、Ta元素的含量。因此,高温下,基体中的Al元素有扩散到涂层中的趋势,而涂层中的Ni、Ta元素有扩散到基体中的趋势。1100℃下Ni、Al和Ta在Ni中的实际扩散系数分别为:2.72 × 10-15、2.37 × 10-14和6.18 × 10-15 m2/s[36]。可以看出,1100℃下Al元素在Ni中的扩散要快于其他元素,即Al从基体扩散到涂层一侧要快于Ni、Ta从涂层扩散到基体一侧。因此,高温下界面附近基体一侧的Al先向涂层中扩散,γ'相聚集区域优先在界面附近涂层一侧形成,后续氧化过程中,γ'相消耗导致Ni、Ta元素不断溶入到γ基体相中,为γ'相的持续形成提供了有利条件,所以图5b~d中γ'相聚集区域向涂层内扩展。
而在喷丸基体/纳米晶涂层界面附近涂层一侧并未观察到γ'相聚集区域,即喷丸处理会影响γ'相在高温合金基体/纳米晶涂层界面附近的形成。喷丸处理使得高温合金表面下方形成残余压应力区,其中存在充足的位错和晶界,为涂层与基体之间的元素互扩散提供大量的扩散通道[10,15,37]。因此,可以将喷丸处理后形成的残余压应力区视为纳米晶涂层在基体中的延伸部分。结合前面的分析,高温下基体中的Al会进入到此延伸部分中,形成新的γ'相。同时,残余压应力的存在会诱发合金表面下方的再结晶[13,38],随着氧化过程的进行,再结晶晶粒不断长大,γ'相也不断长大并向基体内部延伸,见图6b~d。
3.3 涂层内部微观组织演变
图7是20和100 cyc后2种纳米晶涂层整个涂层的截面微观组织。依据上述讨论可以将2种纳米晶涂层划分为不同的区域,其中在不同区域内γ相的EDS成分分析结果见表2,为方便比较,只给出Al元素的质量分数和原子分数。其结果表明,γ相中的Al不会随着氧化过程的持续进行而被完全消耗掉。前面提到,氧化初期纳米晶涂层中Al向外扩散的速率很快,因此氧化膜下方很快形成贫Al区,即氧化膜下面的γ相区域。随着Al2O3膜的持续形成,γ相区域持续扩大,因此合金中Al的扩散较于氧化过程相对缓慢[39]。Durham等[39]的研究指出,两相合金的相溶解情况与其中富含更活泼的溶质元素的沉淀相在基体相中的分布、溶解度、尺寸等因素有关。对于抛光基体表面的纳米晶涂层,除了涂层中的Al向外扩散形成Al2O3外,基体中的Al也会向涂层中扩散,在涂层内部靠近基体/涂层界面处形成γ'相聚集区域(图7a和c)。而对于喷丸基体表面的纳米晶涂层,若将喷丸处理后形成的残余压应力区视为纳米晶涂层在基体中的延伸部分,即γ'相聚集区域存在于应力影响区中,由于涂层中Al不断被消耗,而基体中的Al无法直接补充到涂层内部,γ'相聚集区域不会在涂层内部靠近基体/涂层界面处形成(图7b和d)。因此,相较于喷丸基体表面的纳米晶涂层,抛光基体表面的纳米晶涂层内部γ + γ'区域中的Al相对于γ相有更高的质量浓度差,浓度梯度更大。根据表2中的结果可知,在纳米晶涂层/氧化膜界面附近,抛光基体表面的纳米晶涂层的γ相中的Al含量更高,也表明γ'聚集区的存在加速了氧化过程中γ + γ'中γ'相的溶解。图7的结果也显示,抛光基体表面的纳米晶涂层的γ相区域扩大的程度更大。同时,根据循环氧化动力学结果,在缓慢增重阶段,沉积在抛光高温合金表面的纳米晶涂层的氧化速率常数大于沉积在喷丸高温合金表面的纳米晶涂层,即抛光高温合金表面上纳米晶涂层内部的组织变化加速了Al2O3膜在缓慢增重阶段的形成,然而这种变化对于纳米晶涂层的氧化行为的影响在目前看来仍不够明显,还需要进一步的研究。
图7
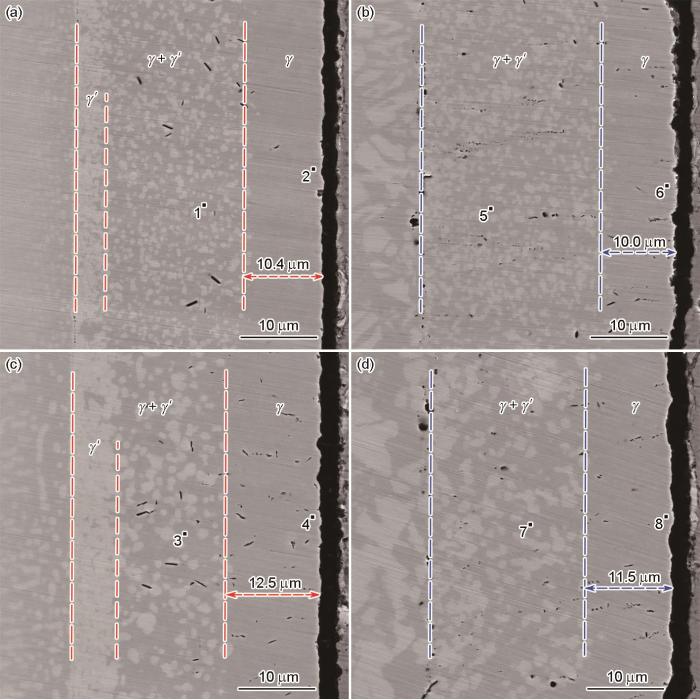
图7 沉积在抛光和喷丸高温合金表面上的纳米晶涂层在1100℃下20和100 cyc后的截面微观组织
Fig.7 Cross-sectional microstructures of nanocrystalline coatings deposited on polished (a, c) and shot peened (b, d) superalloys after 20 (a, b) and 100 (c, d) cyc at 1100oC
表2 图7点1~8处Al元素的EDS结果
Table 2
Superalloy | Cycle number / cyc | Zone | Point | Content | |
---|---|---|---|---|---|
Atomic fraction / % | Mass fraction / % | ||||
Polishing | 20 | γ + γ' | 1 | 9.0 | 4.1 |
γ | 2 | 9.6 | 4.3 | ||
100 | γ + γ' | 3 | 9.0 | 4.0 | |
γ | 4 | 9.8 | 4.4 | ||
Shot peening | 20 | γ + γ' | 5 | 8.9 | 4.0 |
γ | 6 | 9.0 | 4.0 | ||
100 | γ + γ' | 7 | 8.9 | 4.0 | |
γ | 8 | 9.0 | 4.0 |
4 结论
(1) 利用磁控溅射技术分别在抛光和喷丸处理后的N5高温合金表面上制备纳米晶涂层,2种涂层均由单一的γ/γ'固溶体组成,且在1100℃下展现出优异的抗氧化性能。
(2) 1100℃下2种纳米晶涂层循环氧化增重趋势基本一致,在前20 cyc中,氧化增重较快,20 cyc后,沉积在抛光、喷丸高温合金表面的纳米晶涂层的氧化增重分别为0.259和0.282 mg/cm2,2者氧化增重差为0.023 mg/cm2。在20~100 cyc之间,2者进入缓慢增重过程,同时,2种涂层的氧化增重差也在不断减小,100 cyc后,沉积在抛光、喷丸高温合金表面的纳米晶涂层的氧化增重分别为0.385和0.390 mg/cm2,2者氧化增重差仅为0.005 mg/cm2。
(3) 2种纳米晶涂层与基体的界面及界面附近区域的微观形貌演变有所差异,随着氧化实验的进行,在抛光基体/涂层界面处涂层一侧γ'相出现并向涂层内部推进,而在喷丸基体/涂层界面处基体一侧γ'相不断长大并向基体内部延伸。
来源--金属学报