分享:Fe13Cr5Al4Mo合金在高温高压水环境中的腐蚀行为
林晓冬1, 马海滨,2, 任啟森2, 孙蓉蓉1, 张文怀1, 胡丽娟1, 梁雪3, 李毅丰1, 姚美意
,1
1.
2.
3.
利用XRD、SEM和TEM等测试技术研究了Fe13Cr5Al4Mo合金在360℃、18.6 MPa去离子水和360℃、18.6 MPa、3.5 mg/L Li + 1000 mg/L B水溶液中的腐蚀行为。结果表明,Fe13Cr5Al4Mo合金的腐蚀增重远低于参比锆合金,且腐蚀增重速率较慢,表明Fe13Cr5Al4Mo合金的耐腐蚀性能优于参比锆合金。在2种水环境下,Fe13Cr5Al4Mo合金表面均形成了一层Fe(Cr, Al)2O4纳米尖晶石结构的氧化膜,在去离子水中还产生了Fe3O4外层氧化颗粒。Fe(Cr, Al)2O4尖晶石氧化膜整体上较为致密,可以阻碍氧离子和金属阳离子在氧化膜内的扩散,提高合金的耐腐蚀性能。此外,高温高压水中添加Li + B导致Fe13Cr5Al4Mo合金的腐蚀增重和氧化膜厚度发生变化,且抑制了外层氧化颗粒的产生,这与Li + B水溶液较高的pH值和Li+、B3+的相互作用有关。
关键词:
自2011年福岛核事故后,锆合金包壳-UO2燃料元件的安全性引发了广泛关注,由此人们提出了事故容错燃料(ATF)的概念。其中,ATF包壳材料作为重要发展方向之一,主要包括涂层锆合金、难熔合金、FeCrAl合金和SiC复合材料等[1,2]。FeCrAl合金因具有良好的高温力学性能、抗辐照肿胀能力和耐高温蒸汽氧化性能,被视为重要的ATF包壳候选材料之一[3~6]。
FeCrAl合金在失水事故工况下的抗氧化性能直接决定了其耐事故能力,因此国内外针对FeCrAl合金的高温(900~1200℃)蒸汽氧化行为已开展了大量工作[7~11]。研究表明,Cr的第三组元作用和Al的选择性氧化可使FeCrAl合金在高温(≥ 1000℃)下快速形成致密、具有保护性的Al2O3膜,从而有效抑制FeCrAl合金的进一步氧化[12,13]。
相比于锆合金,虽然FeCrAl合金具备良好的抗高温蒸汽氧化性能,但若完全替代锆合金包壳实现商用,还需确保其在常规腐蚀环境下表现出优良的耐腐蚀性能。根据ASTM G2/G2M-19标准,评价锆合金耐腐蚀性能的常规水化学条件主要包括360℃高温高压水和400或500℃过热蒸汽,其中前者主要用于研究锆合金的均匀腐蚀行为,而后者主要用作锆合金耐疖状腐蚀性能评价或锆合金包壳出厂评估。目前关于FeCrAl合金在常规水化学条件下的腐蚀研究较少,且多为高温高压水腐蚀[9,14~16]。例如,Park等[9]研究了FeCrAl合金在360℃除氧水中的腐蚀行为,发现合金表面生成了FeO、Fe3O4和α-Fe2O3等氧化物,且氧化膜/基体(O/M)界面处存在大量孔隙。Rebak等[15]发现在330℃含氧水中FeCrAl合金表面生成了外层富Fe、内层富Cr的双层氧化膜,而在加氢水中只形成一层富Cr氧化膜。然而,Ning等[16]近期研究了FeCrAl合金在360℃、含2.3 mg/L Li + 1200 mg/L B、除氧水溶液中的腐蚀行为,发现在内层氧化膜和基体之间还存在一层含有Cr/Al氧化物的过渡层。因此,目前关于FeCrAl合金在高温高压水中的腐蚀行为尚不能形成统一定论,亟需进一步研究。
压水堆核电站一回路水中常添加一定浓度的H3BO3作为可溶性中子吸收剂,为调节冷却剂pH值,同时加入LiOH使冷却剂呈弱碱性[17]。研究[17~19]表明,Li + B的添加对核电关键材料(如不锈钢、镍基合金和锆合金等)的腐蚀或应力腐蚀行为具有重要影响。例如,Molander等[20]研究了Li + B对600镍基合金应力腐蚀裂纹萌生和扩展行为的影响,结果表明,Li浓度在3~5 mg/L范围时合金的裂纹萌生时间最短,而裂纹扩展速率随B浓度减小而降低。Vankeerberghen等[21]通过研究316不锈钢在模拟一回路水中的裂纹扩展行为,发现随Li浓度增加,不锈钢裂纹扩展速率降低。关于Li + B对锆合金腐蚀行为的影响,Liu等[22]和Wei等[19]均发现随Li浓度增加,锆合金的腐蚀速率增加;而Billot等[23]和赵永福等[24]发现B浓度增加提高了锆合金的耐腐蚀性能。然而,目前关于Li + B对FeCrAl合金腐蚀行为的影响鲜有报道,FeCrAl合金在Li + B水化学条件下的腐蚀机理尚不清晰。
本工作开展了Fe13Cr5Al4Mo合金管在360℃、18.6 MPa去离子水和360℃、18.6 MPa、3.5 mg/L Li + 1000 mg/L B水溶液中的长期腐蚀浸泡实验,研究了FeCrAl合金的腐蚀动力学;利用X射线衍射仪(XRD)、扫描电子显微镜(SEM)和透射电子显微镜(TEM)等测试技术表征和分析了氧化膜的结构、形貌与化学成分,研究了FeCrAl合金在高温高压水环境中的腐蚀机制;通过对比分析去离子水和Li + B水溶液中的腐蚀行为,讨论了Li + B对FeCrAl合金高温高压水腐蚀行为的影响。
1 实验方法
1.1 实验材料
实验材料为Fe13Cr5Al4Mo合金管,外径为9.5 mm,壁厚约0.3 mm。利用PerkinElmer 7300DV电感耦合等离子体原子发射光谱所测Fe13Cr5Al4Mo合金的化学成分列于表1中,为方便比较,将合金名义成分也列在表内。可以看出,Fe13Cr5Al4Mo合金的实测成分与名义成分基本一致。
表1 Fe13Cr5Al4Mo合金的名义和实测成分 (mass fraction / %)
Table 1
Alloy | Cr | Al | Mo | Y | Fe |
---|---|---|---|---|---|
Nominal | 13 | 5 | 4 | 0.02 | Bal. |
Measured | 12.99 | 5.03 | 4.02 | 0.015 | Bal. |
1.2 腐蚀实验
腐蚀实验前,先利用线切割将Fe13Cr5Al4Mo合金管切成长度约20 mm的试样,然后利用2000号SiC砂纸磨掉端面线切割痕迹,依次使用丙酮和去离子水清洗、烘干,再利用游标卡尺测量合金管的尺寸,最后使用精度为0.01 mg的XS105DU电子天平称重。
腐蚀实验根据ASTM G2/G2M—19标准开展。使用316材质、容积为5 L的静态高压釜,分别在360℃、18.6 MPa去离子水和360℃、18.6 MPa、3.5 mg/L Li + 1000 mg/L B水溶液中进行腐蚀实验,腐蚀时间为3、14、28、42、70、100、130、160、190、220和250 d。根据上述ASTM标准,当高压釜温度升至150℃时打开阀门排放一定量的水蒸气,以此排出釜内的空气。此除氧操作可使水中的溶解氧含量降至40 μg/L以下,但不能完全去除水中的溶解氧。在每个腐蚀时间节点处,均更换水溶液并进行以上除氧操作。为了评价Fe13Cr5Al4Mo合金在上述水环境中的耐腐蚀性能,采用Zr-4合金(Zr-1.5Sn-0.2Fe-0.1Cr,质量分数,%)作为参比合金。在每个腐蚀时间节点处取样、称重,获得腐蚀动力学曲线。为提高实验结果的可靠性,每次至少取5个试样的增重平均值作为该节点处的腐蚀增重。
1.3 显微组织表征
利用DM2700M光学显微镜(OM)分别观察合金管表面和截面的晶粒形貌,统计晶粒尺寸;利用JSM-7500型SEM观察合金管的表面形貌;利用D/MAX2500V + /PC型XRD结合JEM-2100F型TEM (加速电压200 kV)分析合金基体的物相组成。
腐蚀后,Fe13Cr5Al4Mo合金表面会生成一层氧化膜。为观察和分析氧化膜的微观特征,先利用SEM分别观察氧化膜表面和截面形貌,测量氧化膜厚度,然后利用配备有INCA能谱仪(EDS)的TEM分析氧化膜截面的结构和成分。在TEM观察过程中,首先在扫描透射电子显微(STEM)模式下获得氧化膜截面的明场(STEM-BF)像或高角环形暗场(STEM-HAADF)像和EDS数据,得到氧化膜的化学成分和元素分布,然后在TEM模式下获得氧化膜截面的明场(TEM-BF)形貌、高分辨透射电子显微(HRTEM)像、选区电子衍射(SAED)花样或快速Fourier变换(FFT)花样,并结合EDS结果确定氧化膜的晶体结构和物相组成。氧化膜截面的TEM试样使用Helios 600i双束型聚焦离子束(FIB)制备。为减小镓离子导致的辐照损伤,采用2 keV低能量离子束进行最后阶段的减薄处理,具体制备流程详见文献[25]。考虑到TEM观察区域有限,为验证TEM分析结果,还利用XRD分析了腐蚀样品的物相组成,2θ角在20°~120°范围内,扫描速率为5°/min。
2 实验结果
2.1 Fe13Cr5Al4Mo合金基体显微组织
图1为Fe13Cr5Al4Mo合金管的尺寸和取样位置示意图及基体显微组织。由OM像(图1b、c、e和f)可知,合金管表面和截面均为等轴晶组织,表明合金发生了完全再结晶。经测量,表面晶粒的平均尺寸为(41.5 ± 12.7) μm,略大于截面晶粒尺寸((36.0 ± 6.2) μm)。从二次电子(SE)像(图1g)可以看出,合金管表面较为粗糙,局部存在很多犁沟或深坑。FeCrAl合金管显微组织的TEM明场像如图1h所示,根据晶粒的SAED花样(图1h插图)可以确定,FeCrAl合金基体主要由bcc结构的铁素体(PDF卡片06-0696)组成。
图1
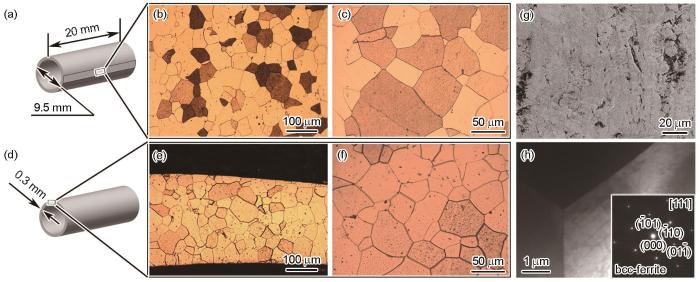
图1 Fe13Cr5Al4Mo合金管的基体显微组织
Fig.1 Microstructures of Fe13Cr5Al4Mo alloy tube
(a) tube dimension and surface sampling position (b, c) surface metallographic images with small and large magnifications, respectively (d) tube dimension and cross-sectional sampling position (e, f) cross-sectional metallographic images with small and large magnifications, respectively (g) secondary electron (SE) image of surface morphology (h) TEM bright field (TEM-BF) image and selected aera electron diffraction (SAED) pattern (inset) of matrix
Fe13Cr5Al4Mo合金基体中存在不同类型的第二相(SPP),对SPP的分析结果如图2所示。根据TEM-BF形貌(图2a~c),SPP的尺寸在几百纳米到几微米范围内。结合EDS结果和SAED花样(图2d~f)可以得出,基体中的SPP主要包含fcc结构的Fe3Mo3C (PDF卡片47-1191)、体心四方(bct)结构的YC2 (PDF卡片11-0602)和fcc结构的Cr23C6 (PDF卡片35-0783)。需要说明的是,由于C原子质量较小,EDS探头难以准确获取C元素的EDS信号,因此EDS结果中C的含量均低于化学计量值。
图2

图2 Fe13Cr5Al4Mo合金中的第二相形貌、成分和SAED花样
Fig.2 TEM-BF images of second phase particles (SPPs) 1-3 in Fe13Cr5Al4Mo alloy (a-c) and SAED patterns of SPPs 1-3 (d-f) (The chemical compositions of SPPs with an atomic fraction are listed in the corresponding TEM-BF images)
2.2 腐蚀增重曲线
图3为Fe13Cr5Al4Mo合金和参比Zr-4合金在360℃、18.6 MPa去离子水和360℃、18.6 MPa、3.5 mg/L Li + 1000 mg/L B水溶液中的腐蚀增重随时间的变化曲线。可以看出,Fe13Cr5Al4Mo合金在去离子水中的腐蚀增重随时间变化不大,均低于20 mg/dm2,且在160 d后略有下降;在Li + B水溶液中,Fe13Cr5Al4Mo合金的腐蚀增重在250 d内缓慢增加,但不超过15 mg/dm2,仅在220 d后略高于去离子水环境。此外,Fe13Cr5Al4Mo合金在2种水环境中的腐蚀增重均显著低于参比锆合金,表明Fe13Cr5Al4Mo合金的耐腐蚀性能优于参比锆合金。
图3

图3 Fe13Cr5Al4Mo和Zr-4合金在去离子水和Li + B水溶液中的腐蚀增重曲线
Fig.3 Weight gain curves of Fe13Cr5Al4Mo and Zr-4 alloys exposed to deionized water and Li + B aqueous solution
2.3 氧化膜形貌
Fe13Cr5Al4Mo合金在去离子水和Li + B水溶液中腐蚀不同时间后的氧化膜表面形貌如图4所示。在去离子水中腐蚀42 d后,合金表面出现了少量氧化物颗粒(图4a),尺寸在1~5 μm范围内。随腐蚀时间增加至100 d,氧化物颗粒数量增加,但尺寸无明显变化(图4b)。然而,当腐蚀时间增加到250 d时,合金表面氧化物颗粒明显减少,并出现很多腐蚀坑(图4c),说明在腐蚀过程中氧化物颗粒可能发生了溶解。与去离子水不同,Fe13Cr5Al4Mo合金表面在Li + B水溶液中腐蚀后未出现氧化物颗粒,仍保留有原始表面的起伏形貌,如图4d~f所示。
图4

图4 Fe13Cr5Al4Mo合金在去离子水和Li + B水溶液中腐蚀不同时间后的氧化膜表面形貌
Fig.4 Surface morphologies of the oxide films formed on the Fe13Cr5Al4Mo alloy after exposure to deionized water (a-c) and Li + B aqueous solution (d-f) for 42 d (a, d), 100 d (b, e), and 250 d (c, f)
图5为Fe13Cr5Al4Mo合金氧化膜截面形貌的背散射电子像。根据氧化膜和基体原子序数不同导致的衬度差异可清晰标示出氧化膜区域,从而可以测量氧化膜厚度,测量结果列于表2中。可知,Fe13Cr5Al4Mo合金在去离子水中腐蚀42 d后,氧化膜厚度仅为(0.52 ± 0.08) μm,且O/M界面起伏不平,如图5a所示。在腐蚀250 d后,氧化膜厚度增加至(1.46 ± 0.20) μm,O/M界面起伏程度降低,如图5c所示。在Li + B水溶液中,随腐蚀时间由42 d增加至250 d,氧化膜厚度由(0.36 ± 0.12) μm增加至(1.55 ± 0.75) μm,但O/M界面起伏较大,如图5d~f所示。
图5
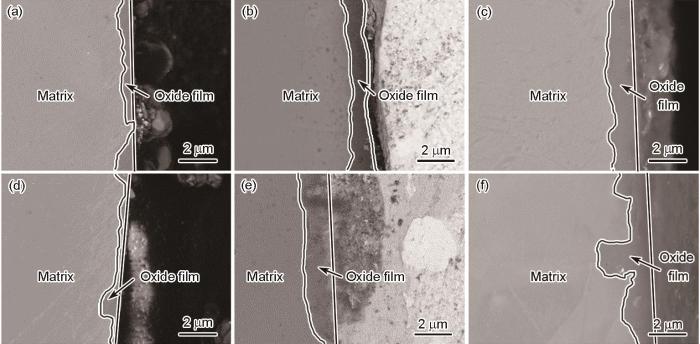
图5 Fe13Cr5Al4Mo合金在去离子水和Li + B水溶液中腐蚀不同时间后的氧化膜截面形貌
Fig.5 Cross-sectional morphologies of the oxide films formed on the Fe13Cr5Al4Mo alloy after exposure to deionized water (a-c) and Li + B aqueous solution (d-f) for 42 d (a, d), 100 d (b, e), and 250 d (c, f)
表2 Fe13Cr5Al4Mo合金在360℃、18.6 MPa去离子水和360℃、18.6 MPa、3.5 mg/L Li + 1000 mg/L B水溶液中腐蚀不同时间的氧化膜厚度 (μm)
Table 2
Water environment | 42 d | 100 d | 250 d |
---|---|---|---|
Deionized water | 0.52 ± 0.08 | 1.42 ± 0.80 | 1.46 ± 0.20 |
Li + B solution | 0.36 ± 0.12 | 1.11 ± 0.23 | 1.55 ± 0.75 |
2.4 XRD分析
对Fe13Cr5Al4Mo合金未腐蚀样品以及在去离子水和Li + B水溶液中腐蚀不同时间后的样品进行XRD分析,结果如图6所示。其中,未腐蚀样品的XRD谱中只出现了α-Fe衍射峰(PDF卡片06-0696),说明合金基体主要由铁素体组成,这与前述TEM表征结果(图1f)相符。然而,Fe13Cr5Al4Mo合金在2种水环境中腐蚀14 d后,XRD谱中开始出现Fe3O4峰(PDF卡片26-1136)或Fe(Cr, Al)2O4尖晶石峰(PDF卡片03-0873)。随腐蚀时间增至250 d,这2种氧化物对应的衍射峰强度无明显变化。事实上,XRD谱中的Fe3O4峰和Fe(Cr, Al)2O4尖晶石峰难以区分,因此这里的谱峰标注结合了后续TEM的分析结果(见2.5节)。此外,所有腐蚀样品的XRD谱中均以基体α-Fe衍射峰为主,而氧化物衍射峰较弱,说明腐蚀250 d后氧化膜厚度仍然较小,这与氧化膜截面观察结果(图5)一致。
图6
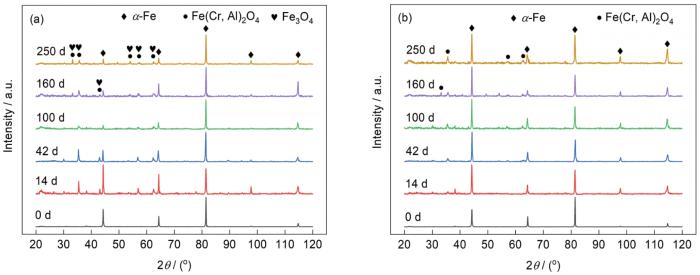
图6 Fe13Cr5Al4Mo合金在去离子水和Li + B水溶液中腐蚀不同时间后的XRD谱
Fig.6 XRD spectra of Fe13Cr5Al4Mo alloy after exposure to deionized water (a) and Li + B aqueous solution (b) for different durations
2.5 氧化膜截面显微组织
为研究氧化膜的晶体结构和化学成分,利用TEM分别观察了Fe13Cr5Al4Mo合金在2种水环境中腐蚀100和250 d后的氧化膜截面显微组织。图7为Fe13Cr5Al4Mo合金在去离子水中腐蚀100 d后氧化膜的TEM表征结果。从HAADF像(图7a)和元素面分布(图7b)可以看出,氧化膜的厚度不均匀,主要含Fe、Cr、Al、O等元素。此外,氧化膜内还存在富Cr、Mo的团簇,根据基体显微组织表征结果(图2),可判定这些团簇为Cr23C6第二相,且由O分布可知这些第二相滞后于基体发生氧化。在O/M界面附近的氧化膜一侧存在大量的微孔隙和微裂纹缺陷,且互相连接、平行于O/M界面成带状分布。对氧化膜进行SAED分析,结果如图7d所示,可见SAED花样呈现明显的多晶环特征,经标定可以得出,氧化膜主要由fcc-Fe(Cr, Al)2O4纳米尖晶石(PDF卡片03-0873)组成。O/M界面处的HRTEM像如图7e所示,对氧化物区域进行FFT变换(图7f),也可标定出fcc-Fe(Cr, Al)2O4结构,与SAED结果一致。
图7
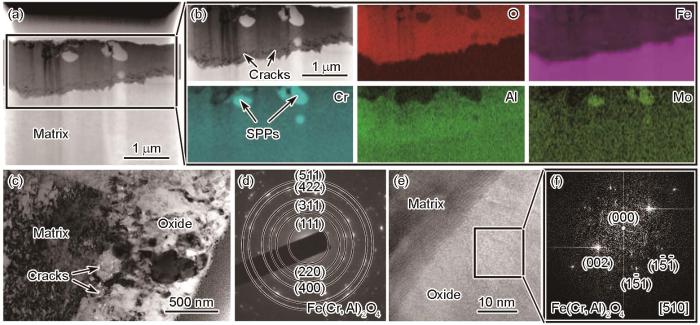
图7 Fe13Cr5Al4Mo合金在去离子水中腐蚀100 d后氧化膜的截面显微组织、元素分布、SAED花样及快速Fourier变换(FFT)结果
Fig.7 Cross-sectional microstructure, element mapping, SAED pattern, and fast Fourier transformation (FFT) result of the oxide film formed on the Fe13Cr5Al4Mo alloy following exposure to deionized water for 100 d
(a) high angle annular dark field image under scanning transmission electron microscopy mode (STEM-HAADF image)
(b) STEM-HAADF image and element mapping of the selected region in Fig.7a
(c) TEM-BF image (d) SAED pattern
(e) high resolution transmission electron microscopy (HRTEM) image of the oxide/matrix (O/M) interface
(f) FFT pattern of the oxide corresponding to the rectangle region in Fig.7e
图8为Fe13Cr5Al4Mo合金在去离子水中腐蚀250 d后氧化膜的TEM表征结果。可以看出,氧化膜同样含有Fe、Cr、Al、O等元素,但其厚度较100 d有所增加且更加均匀,未发现氧化膜内存在富Cr、Mo的团簇。值得注意的是,在氧化膜外表面还出现了不连续分布的富Fe氧化物。经过SAED或FFT分析可知,氧化膜主要为fcc-Fe(Cr, Al)2O4纳米尖晶石,而外表面富Fe氧化物为fcc-Fe3O4 (PDF卡片24-0511)。
图8
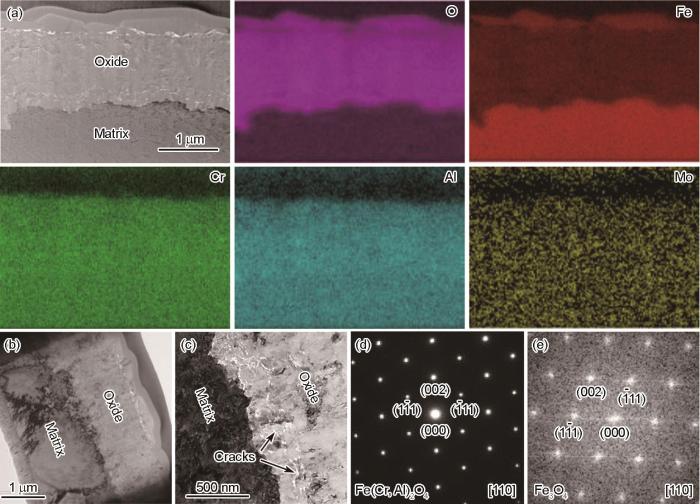
图8 Fe13Cr5Al4Mo合金在去离子水中腐蚀250 d后氧化膜的截面显微组织、元素分布、SAED花样及FFT结果
Fig.8 Cross-sectional microstructure, element mapping, SAED pattern, and FFT result of the oxide film formed on the Fe13Cr5Al4Mo alloy following exposure to deionized water for 250 d
(a) bright field image under scanning transmission electron microscopy mode (STEM-BF image) and the corresponding element mapping
(b) TEM-BF image of oxide film (c) TEM-BF image of the O/M interface
(d) SAED pattern of oxide film (e) FFT pattern of outer oxide particle
图9为Fe13Cr5Al4Mo合金在Li + B水溶液中腐蚀100 d后氧化膜的截面显微组织。与去离子水中的腐蚀结果相似,合金在Li + B水溶液中形成的氧化膜主要含有Fe、Cr、Al、O等元素,且在O/M界面处存在很多微孔隙。此外,对SAED和FFT花样进行标定可以得出,氧化膜同样主要由fcc-Fe(Cr, Al)2O4纳米尖晶石组成。值得注意的是,根据此TEM试样可以测得氧化膜厚度为(0.46 ± 0.09) μm,远小于SEM测量结果((1.11 ± 0.23) μm),这是因为氧化膜厚度不均匀,而TEM试样尺寸较小,仅能体现局部信息。
图9
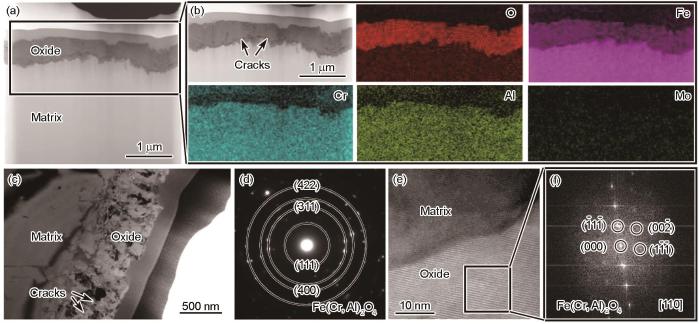
图9 Fe13Cr5Al4Mo合金在Li + B水溶液中腐蚀100 d后氧化膜的截面显微组织、元素分布、SAED花样及FFT结果
Fig.9 Cross-sectional microstructure, element mapping, SAED pattern, and FFT result of the oxide film formed on the Fe13Cr5Al4Mo alloy following exposure to Li + B aqueous solution for 100 d
(a) STEM-HAADF image
(b) STEM-HAADF image and element mapping of the selected region in Fig.9a
(c) TEM-BF image
(d) SAED pattern
(e) HRTEM image of the O/M interface
(f) FFT pattern of the oxide corresponding to the rectangle region in Fig.9e
Fe13Cr5Al4Mo合金在Li + B水溶液中腐蚀250 d后,氧化膜的截面显微组织如图10所示。与腐蚀100 d相比,氧化膜厚度增加,O/M界面起伏不平。结合元素面分布和SAED结果,同样可确定氧化膜为fcc-Fe(Cr, Al)2O4纳米尖晶石结构。然而,与去离子水中250 d的腐蚀结果不同,Li + B水溶液中形成的氧化膜外表面未发现富Fe的氧化物。
图10

图10 Fe13Cr5Al4Mo合金在Li + B水溶液中腐蚀250 d后氧化膜的截面显微组织、元素分布和SAED花样
Fig.10 Cross-sectional microstructure, element mapping, and SAED pattern of the oxide film formed on the Fe13Cr5Al4Mo alloy following exposure to Li + B aqueous solution for 250 d
(a) STEM-BF image and the corresponding element mapping (b) TEM-BF image (c) SAED pattern
3 分析讨论
3.1 Fe13Cr5Al4Mo合金在高温高压水环境中的腐蚀过程
根据Fe13Cr5Al4Mo合金氧化膜的显微组织表征结果(图5~10),在360℃、18.6 MPa去离子水和360℃、18.6 MPa、3.5 mg/L Li + 1000 mg/L B水溶液中形成的氧化膜均主要由Fe(Cr, Al)2O4纳米尖晶石组成,在去离子水中Fe13Cr5Al4Mo合金外表面还形成了Fe3O4颗粒,这与FeCrNi不锈钢在高温高压水环境中的腐蚀行为相似[26~29]。现有不锈钢的高温腐蚀理论和模型表明[30~34],不锈钢的腐蚀主要包括O在合金表面的吸附和电离、金属阳离子在O/M界面的产生以及离子通过氧化膜的扩散等分步骤,其中O2-和金属阳离子在氧化膜内的扩散为氧化速率控制步骤。因此,根据上述理论并结合本工作腐蚀结果,可以提出Fe13Cr5Al4Mo合金在高温高压水环境中的腐蚀模型,如图11所示。
图11
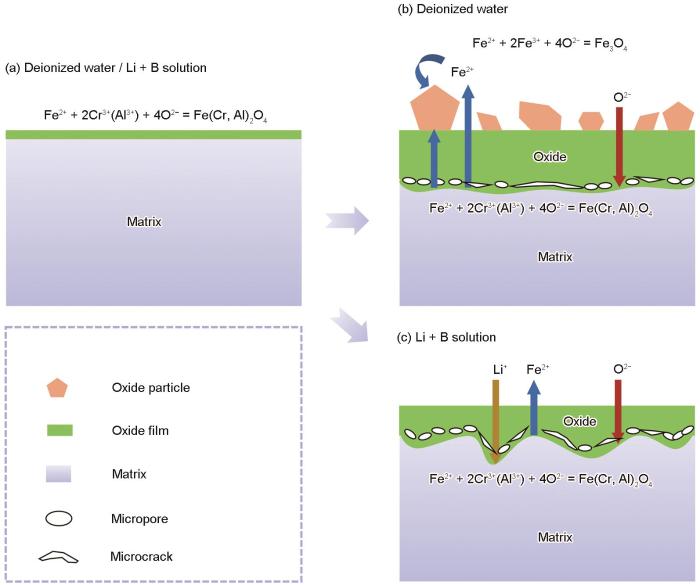
图11 Fe13Cr5Al4Mo合金在高温高压水环境中的腐蚀过程示意图
Fig.11 Schematics of corrosion process of the Fe13Cr5Al4Mo alloy in high-temperature high-pressure water environments
(a) initial corrosion stage
(b) stable corrosion stage in deionized water
(c) stable corrosion stage in Li + B aqueous solution
在腐蚀初期,合金基体与水介质直接接触,由于2者界面处氧含量较高,基体中的Fe、Cr、Al元素均发生氧化,形成Fe(Cr, Al)2O4尖晶石氧化物,如图11a所示。随腐蚀进行,合金表面生成一层尖晶石氧化膜,将合金基体与水介质隔离开。此时,腐蚀过程主要依靠O2-和金属阳离子通过氧化膜的扩散进行,氧化膜厚度随时间延长而逐渐增加。在去离子水中腐蚀时,Fe13Cr5Al4Mo合金外表面还形成了Fe3O4颗粒(图4),这是因为铁离子在氧化膜内的扩散速率较快,部分铁离子扩散至合金表面,通过固态传输机制[32,35]或溶解-再沉积机制[30]在外表面形成Fe3O4颗粒,如图11b所示。
值得注意的是,2种水环境中,在O/M界面附近的氧化膜内均形成了大量微孔隙或微裂纹等缺陷,这可能与氧化膜内应力有关。由于Fe、Cr和Al氧化为Fe(Cr, Al)2O4尖晶石的Pilling-Bedworth (P.B.)比为2[36],使氧化膜内部尤其是O/M界面处产生较大内应力,从而导致孔隙和裂纹等缺陷形成。此外,腐蚀过程中由于铁离子向外扩散速率较快,容易在O/M界面处产生大量空位[9],这些空位通过扩散和聚集形成空位团簇和微孔隙等缺陷,在氧化膜内应力作用下也可扩展成为微裂纹,如图11b和c所示。虽然这些缺陷的存在一定程度上可以增加O2-和金属阳离子的扩散速率,但由于氧化膜整体上较为致密,且Fe(Cr, Al)2O4尖晶石能够阻碍金属阳离子的扩散[35],具有较好的保护作用,因此Fe13Cr5Al4Mo合金的腐蚀速率明显小于参比Zr-4合金。
Ning等[16]在研究Fe13Cr5Al4Mo合金在360℃、19 MPa、2.3 mg/L Li + 1200 mg/L B除氧(溶解氧含量< 5 μg/L)水溶液中的腐蚀行为时,发现腐蚀100 d后在内层氧化膜和基体之间存在一层由Cr/Al氧化物和Fe单质组成的“过渡层”,即合金发生了内氧化。然而,本工作中相似成分的FeCrAl合金在360℃、18.6 MPa、3.5 mg/L Li + 1000 mg/L B水溶液中腐蚀相同时间后未出现内氧化现象,如图7所示。分析认为,造成这种差异的原因可能与水溶液中的氧含量有关。在完全除氧条件(溶解氧含量< 5 μg/L)下,O/M界面处的氧含量很低,由于Cr、Al元素发生氧化的平衡氧分压远小于Fe[37],因此O/M界面处只有Cr、Al发生氧化,形成Cr/Al氧化物和Fe单质的“过渡层”。然而,本工作中由于未完全除氧,水溶液中仍存在一定量的溶解氧(含量< 40 μg/L),较多的O2-可通过氧化膜扩散至O/M界面处,使Fe、Cr和Al元素均被氧化,从而形成Fe(Cr, Al)2O4尖晶石氧化膜,而无“过渡层”产生。
3.2 Li + B对Fe13Cr5Al4Mo合金腐蚀行为的影响
根据腐蚀增重曲线(图3)和氧化膜厚度测量结果(表2),当腐蚀时间不超过100 d时,Fe13Cr5Al4Mo合金在Li + B水溶液中的腐蚀增重和氧化膜厚度均小于去离子水,表明Li + B的添加一定程度上降低了Fe13Cr5Al4Mo合金的氧化速率。然而,当Fe13Cr5Al4Mo合金在Li + B水溶液中腐蚀250 d后,由于合金基体局部腐蚀严重,导致O/M界面起伏较大,使氧化膜厚度平均值增加。此外,根据氧化膜表面形貌(图4),在Li + B水溶液中腐蚀250 d后,Fe13Cr5Al4Mo合金表面仍无氧化物颗粒形成。通过对比分析去离子水和Li + B水溶液中的腐蚀结果可以推测,造成上述差异的原因可能与Li + B水溶液较高的pH值和Li+、B3+的相互作用有关。
去离子水的pH值随温度升高而变化,当温度由室温升至300℃时,pH值由7降至5.6,但去离子水仍保持中性[38]。若在去离子水中添加一定量的LiOH和H3BO3,可使水溶液的pH值增加。例如,含有2.2 mg/L Li + 1200 mg/L B的水溶液在300℃时的pH值为6.9[39,40],高于相同温度下去离子水的pH值(5.6)。由于本实验中的Li + B浓度(3.5 mg/L Li + 1000 mg/L B)与核燃料运行初期一回路水中的Li + B浓度相近,根据文献[17]可推测Li + B水溶液的pH值在7.0~7.4范围内,呈弱碱性。根据热力学计算[41,42],铁离子在300℃高温高压水中的溶解度先随pH值升高而减小,在pH值7.0~7.4时降至最小,之后随pH值升高而增加。因此,Fe13Cr5Al4Mo合金在Li + B水溶液中腐蚀时,碱性水环境能减缓氧化物的溶解,进而抑制铁离子通过溶解-再沉积方式形成氧化物颗粒,导致合金表面无氧化物颗粒形成。
研究[18,19,23]表明,Li+的存在能加速690镍基合金和Zr-4、HANA-4及ZIRLO等锆合金的腐蚀,而B3+的添加可以减弱Li+的加速腐蚀作用。尽管Li+、B3+对合金腐蚀的作用机理尚未完全明确,但已有研究发现,690合金腐蚀过程中Li+可以增加氧离子空位通过氧化膜的扩散速率,而B3+的存在一定程度上抑制了Li+的扩散[18]。此外,Cox等[43]提出锆合金氧化膜内四方或立方结构的ZrO2先于单斜ZrO2溶解于LiOH溶液中,导致内层氧化膜疏松多孔,从而加速锆合金腐蚀;加入H3BO3可以形成可溶性的复杂Zr-Li-B盐并堵塞孔洞,从而抑制LiOH对锆合金耐腐蚀性能的不利影响。基于上述文献研究可以推测,Li+和B3+的相互作用是导致本工作中Fe13Cr5Al4Mo合金在Li + B水溶液和去离子水中氧化速率不同的重要原因。然而,由于Li、B原子序数较小且含量很低,TEM配备的EDS探头难以检测到2者的EDS信号,不能给出Li、B元素在氧化膜内的准确分布,因此,Li + B对Fe13Cr5Al4Mo合金腐蚀行为的影响机制仍需深入研究。
4 结论
(1) Fe13Cr5Al4Mo合金在360℃、18.6 MPa去离子水和360℃、18.6 MPa、3.5 mg/L Li + 1000 mg/L B水溶液中的腐蚀增重及其增长速率明显小于参比Zr-4合金,其耐腐蚀性能优于锆合金。
(2) 2种水环境下Fe13Cr5Al4Mo合金表面均形成一层由Fe(Cr, Al)2O4纳米尖晶石组成的氧化膜,在去离子水中合金外表面还生成了Fe3O4颗粒。
(3) 靠近O/M界面处的氧化膜内存在带状分布的微孔隙或微裂纹缺陷,可能与氧化膜内应力和铁离子的快速向外扩散有关。
(4) 高温高压水中添加Li + B使Fe13Cr5Al4Mo合金的腐蚀增重和氧化膜厚度发生改变,且抑制了外层氧化颗粒的形成,推测与Li+和B3+等离子的相互作用以及水溶液较高的pH值有关。
来源-金属学报