分享:热挤压与热处理对网状TiBw/TC18复合材料组织及性能的影响
对不同增强相含量的TiBw/TC18进行了热挤压与热处理,利用OM、SEM、TEM及电子万能试验机研究了热挤压与热处理对复合材料的组织与拉伸性能的影响。结果表明,通过β单相区挤压变形,TiBw/TC18的β晶粒由70 μm减小到40 μm左右,TiBw呈定向排列。挤压态TiBw/TC18通过三重退火与固溶时效处理后,基体组织变为不同尺寸的α相分布在β相基底上,这种多尺度的组织使TiBw/TC18获得了优异的综合性能。力学性能测试结果表明,挤压处理可明显提升烧结态TiBw/TC18复合材料的延伸率,但强度下降17%。经三重退火处理后,2.0%TiBw/TC18 (体积分数)的抗拉强度和延伸率分别达到1200 MPa和21.7%,较烧结态分别提高了5.5%和189%。而采用固溶时效处理后,2.0%TiBw/TC18复合材料的抗拉强度和延伸率分别为1389 MPa和9.9 %,较烧结态分别提高了22.2%和32%。2种热处理制度均实现了复合材料强度和塑性的协同提升。网状结构TiBw/TC18通过挤压与不同制度的热处理可以调控其性能,以满足不同服役条件的使用需求。
关键词:
在钛合金基体中引入陶瓷增强相制备的非连续增强钛基复合材料(discontinuously reinforced titanium matrix composite, DRTMC)[1,2],具有更高比强度、更高弹性模量与耐高温等优点[3]。传统的DRTMC制备方法包括熔铸法和粉末冶金法等。其中粉末冶金结合原位自生的方法既可以使原位生成的增强相与基体具有良好的界面[4,5],又可以调控增强相在基体中的分布状态[6,7]。用这种方法制备的DRTMC力学性能优异,可以做到近净成形,具有良好的应用前景。Huang等[8]基于Hashin-Shtrikman (H-S)理论[9],利用粉末冶金与原位自生的工艺方法,调控钛基复合材料中增强相呈准连续网状分布。这种独特的网状结构解决了传统粉末冶金钛基复合材料塑性差的瓶颈问题,使钛基复合材料强度提升的同时,保留良好的塑性[10~13]。但是当引入较高含量的陶瓷增强相时,DRTMC的塑韧性往往会急剧下降。因此,通过只引入少量(≤ 2.0%,体积分数,下同)的增强相有望同时提高基体合金的强度和塑韧性[14~16]。
近β钛合金是航空航天领域中广泛应用的结构性钛合金[17~20]。在前期研究[21]中,采用TC18 (Ti-5Al-5Mo-5V-1Cr-1Fe,质量分数,%)作为基体合金成功烧结制备了一系列低增强相含量(≤ 2.0%,体积分数)的TiBw/TC18复合材料,通过一步烧结制备的烧结态TiBw/TC18的强度与塑性均超越锻造态TC18合金。研究[22~24]发现热轧制、锻造、挤压等变形工艺可以提高复合材料致密度和组织均匀性等,是进一步提高钛基复合材料综合力学性能的有效手段。其中挤压加工具有变形量大与工艺流程简单等优点,因此,本工作研究了热挤压变形对网状结构TiBw/TC18复合材料组织和力学性能的影响规律。在此基础上,对挤压态复合材料分别进行了三重退火与固溶时效2种制度的热处理。研究热处理制度对挤压态复合材料组织及拉伸性能的影响,并揭示其强韧化机理。
1 实验方法
实验采用粒径为53~108 μm的球形TC18粉末,平均粒径5 μm的TiB2粉末(纯度99.8%)作为原料。使用行星式球磨机将TC18粉末和不同质量分数的TiB2颗粒进行混合,球磨转速为220 r/min,球料比3∶1,时间5 h,球磨过程采用Ar气保护。之后将混合粉末放入真空热压烧结炉进行烧结,烧结工艺为1300℃、25 MPa、2 h,制得TiB体积分数为0.5%、1.0%和2.0%的烧结态TiBw/TC18网状复合材料。烧结态材料组织特征如图1a所示,TiBw呈网状分布。并采用相同工艺制备TC18合金作为对比。对所制备的4种材料在1100℃保温2 h后进行正向热挤压,挤压比为16∶1,挤压后空冷至室温。在挤压棒材的10、95、265和380 mm位置处切取试样进行电子背散射衍射(EBSD)分析,并将其编号为A、B、C、D,如图1b所示。将平行于挤压方向命名为ED,垂直于挤压方向命名为ND。将4种挤压态的材料分别进行固溶-时效(830和600℃)与三重退火(830、750和600℃)热处理。2种热处理制度分别见图1c和d。利用金相法测得TC18合金与0.5%TiBw/TC18的相变点在855~865℃之间,1.0%和2.0% TiBw/TC18的相变点在865~875℃之间。
图1
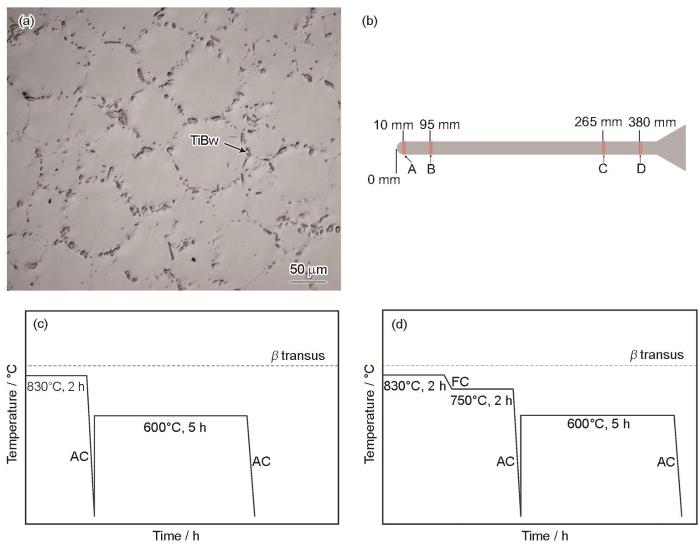
图1 烧结态复合材料OM像、挤压棒材EBSD分析取样位置及挤压态材料热处理过程示意图
Fig.1 OM image of as-sintered 2.0%TiBw/TC18 composites (a), schematic illustrating samples' locations of as-extruded 1.0%TiBw/TC18 for EBSD analysis (b), schematics of solution aging (c) and triple-annealing (d) treatments for as-extruded alloy and composites (AC—air cooling, FC—furnace cooling)
使用120、320、600、1000、1500和2000号砂纸手动打磨金相试样,利用Cr2O3溶液进行机械抛光。腐蚀液为Kroll's试剂,腐蚀时间1~2 s。金相观察采用配备了电荷藕合器件(CCD)相机的PEM-3光学显微镜(OM)。利用Merlin Compact与HELIOS NanoLab 600i扫描电镜(SEM)对材料进行组织观察。使用SUPRA55型SEM中的EBSD对材料进行晶粒尺寸分布与织构分析。EBSD试样利用电解抛光制成,电解液为体积比为1∶6∶10的高氯酸、正丁醇、甲醇混合溶液,输出直流电压为40 V,抛光时间为80 s。使用TalosF200x透射电镜(TEM)对材料进行相结构与成分分析。TEM试样经砂纸磨至40 μm厚,然后对其进行离子减薄。利用WDT-20电子万能试验机进行拉伸实验,应变速率为0.5 mm/min。拉伸采用板状试样,中部均匀段尺寸为1.5 mm × 5 mm × 15 mm。采用引伸计测量应变,引伸计标距为10 mm。
2 实验结果与讨论
2.1 挤压态与热处理态TiBw/TC18的组织变化
2.1.1 挤压态TiBw/TC18组织表征
挤压态1.0%TiBw/TC18微观组织晶粒取向图、极图、反极图与晶粒尺寸分布如图2所示。由图2a1~d1的晶粒取向分布图可以看出,在4个位置上,样品的组织均为等轴β晶粒。说明整个挤压过程是在β单相区进行的,同时说明在变形过程中样品发生了动态再结晶。如图2a2~d2中的晶粒尺寸分布图所示,A、B、C、D样品的平均晶粒尺寸分别为43.6、39.7、38.2和27.1 μm。首先,复合材料挤压后组织中β晶粒尺寸相对烧结态β晶粒平均尺寸(70 μm)显著减小。其次,随着距挤压棒材头部距离的增大,晶粒尺寸逐渐变小。这是因为:(1) 样品在挤压变形过程中靠近挤压棒材头部的区域变形程度较小,晶粒破碎程度较低,在小挤压比时甚至会保留烧结态的组织;(2) 棒材头部的变形温度高,一方面头部在变形时坯料本身的温度高,另一方面钛合金在挤压开始阶段由于剧烈塑性变形的热效应和低的热导率会导致温度的剧烈升高。但是大挤压比(16∶1)时,过了头部一段距离后变形程度趋于稳定,所以在挤压棒材的中间段会产生一个稳态变形段[25],已有研究[26]认为此挤压比下钛基复合材料从棒材前端头部100 mm之后就进入稳态阶段。本工作中样品B和样品C平均粒径只相差1.5 μm,因此可以认为挤压态材料的BC段处于均匀变形阶段。后续讨论的样品组织与拉伸性能都是在各自棒材的均匀变形段进行取样。即挤压使复合材料的晶粒尺寸由70 μm减小到40 μm左右(均匀变形段)。通过分析图2a3~d3与图2a4~d4中的极图与反极图,在A、B、C样品中没有发现明显的织构,但是在D样品中存在明显的丝织构<110>//ED。
图2
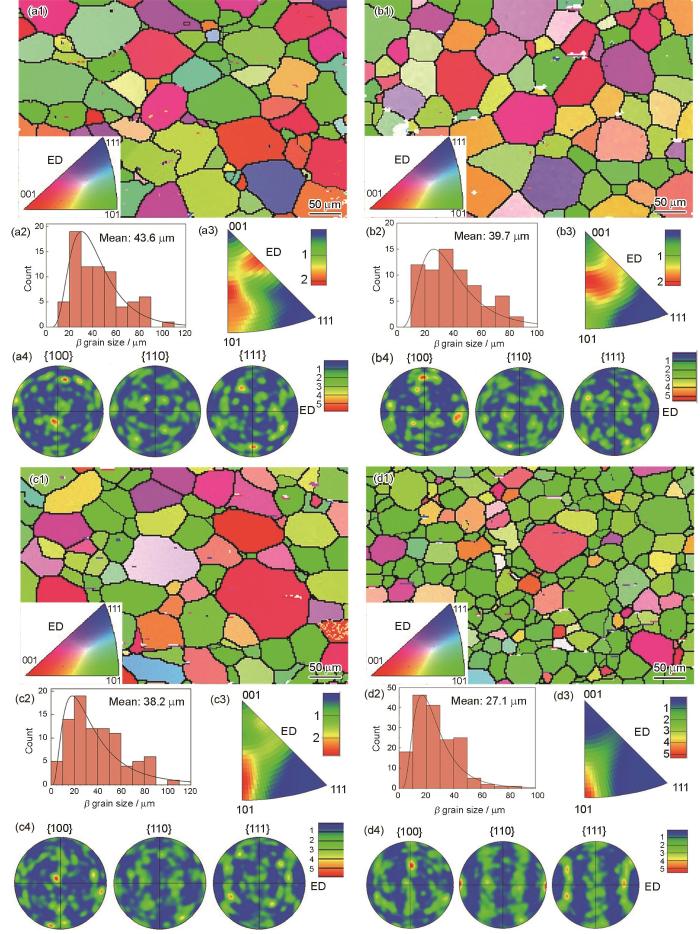
图2 挤压态1.0%TiBw/TC18不同部位的EBSD分析
Fig.2 EBSD grain orientation maps (a1-d1), frequency distributions of grain size (a2-d2), inverse pole figures (IPFs) (a3-d3), and pole figures (PFs) (a4-d4) of samples A (a1-a4), B (b1-b4), C (c1-c4), and D (d1-d4) in as-extruded 1.0%TiBw/TC18 composites (ED—extrusion direction)
图3为不同体积分数TiBw/TC18组织的OM像。由图3a与b可见,挤压态TC18合金与0.5%TiBw/TC18组织不均匀。其中灰色部分为动态再结晶后的β晶粒,黑色部分为未再结晶区域。未再结晶区域由于存在大量位错等缺陷,在冷却过程中促进了α相在这些高能量区域析出。图3c与d中则未出现未再结晶区域。这主要由2个原因引起:第一,烧结态TC18合金β晶粒粗大(平均粒径815 μm),并且热挤压前在1100℃的保温会促进晶粒进一步长大。而由于一定含量TiB的阻碍作用,复合材料的β晶粒相对细小。TC18合金较少的晶界面积导致其在挤压时变形抗力大于复合材料,在挤压力一定时,其变形速率明显低于复合材料。由于挤压过程未在等温下进行,其后期挤压温度也较低,最终导致未再结晶区域的出现。第二,TC18合金的晶粒尺寸不均匀,在高温变形时局部区域的变形不均匀,所以变形量小的区域没有充分再结晶。挤压态0.5%TiBw/TC18组织中也发现了未再结晶的区域,也是因局部变形不均匀导致。将烧结态0.5%TiBw/TC18加热至1100℃保温2 h,水淬,其组织如图3e所示。发现个别区域的β晶粒突破网状增强相的限制发生了晶粒的合并长大(图中椭圆区域)。所以判断0.5%TiBw/TC18在挤压前其局部组织并不均匀,从而导致它的局部不均匀的变形量。同样也证明了网状结构复合材料在增强相含量达到一定程度时可以限制热加工之前坯料组织的不可控变化,为后续的加工提供优良的组织准备。
图3
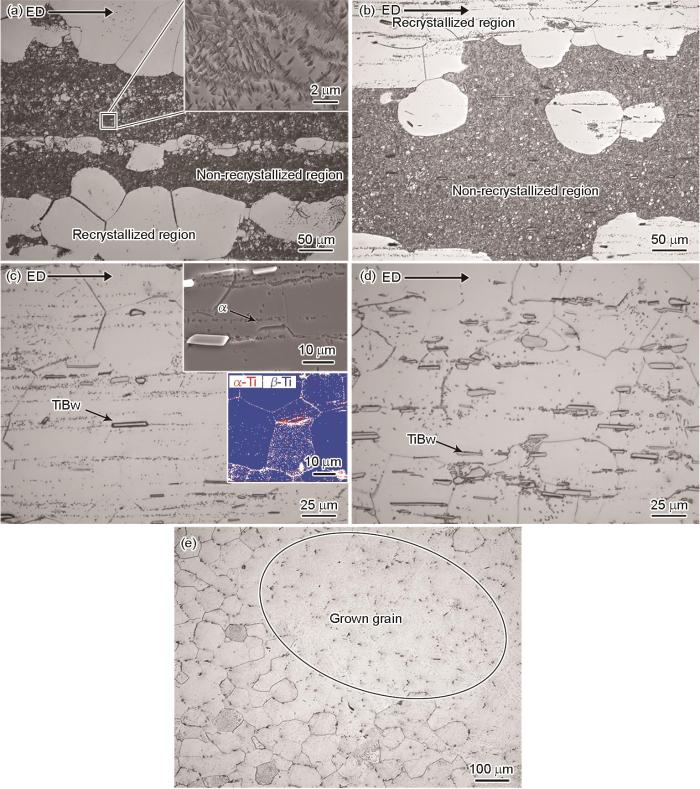
图3 不同体积分数TiBw/TC18的OM像
Fig.3 OM images of TiBw/TC18 composites with different reinforcement volume fractions
(a) as-extruded TC18 and enlarged SEM image of the marked area (inset)
(b) as-extruded 0.5%TiBw/TC18
(c) as-extruded 1.0%TiBw/TC18, and SEM image and phase map (insets)
(d) as-extruded 2.0%TiBw/TC18
(e) as-sintered 0.5%TiBw/TC18 solution at 1100oC followed by water quench, and the area circled by the line is the area where the grains grow
1.0%和2.0%TiBw/TC18的组织中几乎全为β相,但有极少数α相在晶界或者亚晶界等高能量区域处析出,对应图3c和d中的晶界α和晶内细小黑色斑点,亚晶界的形成是因为挤压变形时动态再结晶的晶粒还会继续变形从而形成高能量区域。TiBw晶须由烧结态的网状分布变为定向排列,这是由于挤压变形过程中TiBw随基体合金的流动变形发生转动造成的。此外,并未出现TiBw折断、脱黏等现象,说明了低含量的TiBw (增强相之间间距较大)在挤压过程中未相互挤压碰撞,也说明塑性较好的β基体组织未使TiBw在挤压时受到很大的作用力。
2.1.2 热处理态TiBw/TC18的组织变化
不同体积分数TiBw/TC18经热处理后的组织如图4所示。其中图4a~d为TC18合金与0.5%TiBw/TC18经三重退火与固溶时效之后的组织,热挤压过程中未发生动态再结晶的区域并未在热处理过程中进一步再结晶。这是因为挤压后的降温过程中α相在高能量区析出,消耗了静态再结晶所需的驱动力。图4e为2.0%TiBw/TC18经三重退火后的组织。β晶粒为均匀的等轴状,并且其尺寸未发生明显变化。组织中包含尺寸粗大的晶界α (GBα)、晶内片层状α相与晶内细小的针状α相。粗大的片层状α相(coarse α,αc)为第一阶段830℃退火和随后炉冷至750℃保温2 h时析出,细小的针状α相(fine α,αf)为600℃保温5 h阶段析出。这里将αf与其周围的β相基底称为β + αf组织,简称βf,这一组织的形成与三重退火制度有关。第一段退火稳定组织并析出一部分αc (最终其拥有更大的尺寸);第二段退火继续析出另一部分αc并控制组织中αc的比例;第三段退火控制αf的含量与尺寸。多尺度的α相构成了基体的多尺度组织,有助于提高材料的综合性能。在图4e中,还可以观察到αc与GBα中具有十分细小的颗粒状析出物。这是由于α稳定元素在最先析出的GBα与αc中含量较高,导致形成α2相,即Ti3Al。Ti3Al的析出可以使αc得到一定程度的强化[27]。图4f为经过固溶时效处理后2.0%TiBw/TC18的组织,与三重退火后的组织相似。对比图4e与f可以看出,固溶时效处理后αc与GBα的含量与尺寸相对三重退火后的组织有所降低,这是因为缺少了750℃退火所致。同时还可以看出,固溶时效后组织中αf的比例更高,但是尺寸与三重退火后的尺寸没有明显差异。1.0%TiBw/TC18与2.0%TiBw/TC18组织类似。
图4

图4 不同体积分数TiBw/TC18经不同热处理后的OM与SEM像
Fig.4 OM (a-d) and SEM (e, f) images of the TC18 alloy (a, b), 0.5%TiBw/TC18 (c, d), and 2.0%TiBw/TC18 (e, f) composites after triple-annealing (a, c, e) and solution aging (b, d, f) heat treatments (Insets show the high magnified images. GBα—grain boungry α, αc—coarse α, αf—fine α, α2—Ti3Al)
图5为三重退火态2.0%TiBw/TC18的TEM明场像、HRTEM像及快速Fourier变换(FFT)。由图5a与b明场像可见,组织中存在粗大的αc与细小的αf。αf普遍相互垂直分布,因为这种析出方式一方面满足Burgers位向关系,另一方面可以降低αf析出时的弹性应变能[28]。图5c为图5b中标记区域的HRTEM像,其中α、β相界面清晰。图5d为αc的HRTEM像,未在图中发现明显的析出物。图5e为图5c的FFT,可看出αc与β相满足位向关系[
图5
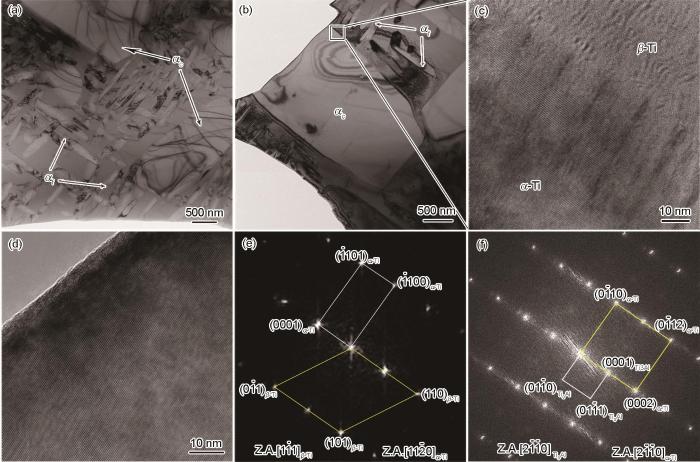
图5 三重退火态2.0%TiBw/TC18的TEM、HRTEM像及快速Fourier变换
Fig.5 Bright field TEM (a, b) and HRTEM (c, d) images of 2.0%TiBw/TC18 composites after triple-annealing, and fast Fourier transformation (FFT) patterns taken from Figs.5c (e) and d (f)
2.2 挤压态与热处理态TiBw/TC18的拉伸性能
图6为不同状态不同增强相含量复合材料的拉伸应力-应变曲线。结合表1给出的拉伸性能数据可知,随着增强相含量的增加挤压态材料的屈服强度与抗拉强度先降低后升高。TC18合金的屈服强度为804 MPa,略高于0.5%TiBw/TC18 (786 MPa)。这是由于TC18合金组织中未再结晶区域的比例大于0.5%TiBw/TC18,这些未再结晶区域中细小片层状α相所提供的第二相强化效果大于0.5%TiBw所提供的纤维强化效果。但是当增强相含量继续增加时,TiBw的增强效果逐渐显现。可以看出,1.0%和2.0%TiBw/TC18的屈服强度(853和876 MPa)相较于TC18合金分别提高了49和72 MPa。从延伸率数据可知挤压态材料的延伸率随着TiBw含量的升高而下降。2.0%TiBw/TC18的延伸率为26%,相较于1.0%TiBw/TC18 (29.7%)降低了12.5%。而TC18与0.5%TiBw/TC18的延伸率较低(分别为6.5%和19.4%)是因为其不均匀的组织导致应力在局部的集中,从而造成过早断裂。将挤压态材料的性能与烧结态材料[21]的性能进行对比,可以看出挤压态材料的强度明显低于烧结态材料。虽然挤压过程带来的β晶粒细化与TiBw晶须的定向排列可提高强度[29],但挤压态材料缺少α相的第二相强化作用。而高强度钛合金的主要强化手段就是细小α相的析出强化。对比挤压态材料与烧结态材料的延伸率,可以看出挤压态材料的延伸率显著高于烧结态。组织均匀的挤压态1.0%与2.0%TiBw/TC18的延伸率(29.7%和26%)相较于烧结态的(13.5%和7.5%)都提高了100%以上。这一方面因为挤压态材料β晶粒的细化;另一方面因为其组织基本都为拥有良好塑性变形能力的bcc结构β-Ti。
图6

图6 不同状态TiBw/TC18复合材料拉伸应力-应变曲线
Fig.6 Tensile stress-strain curves of TiBw/TC18 composites with different states
表1 不同状态下TiBw/TC18复合材料的拉伸性能
Table 1
State | V / % | σ0.2 / MPa | σb / MPa | δ / % |
---|---|---|---|---|
As-sintered[21] | 0 | 1082 ± 17.6 | 1151 ± 10 | 0.6 ± 0.5 |
0.5 | 1052 ± 4.4 | 1171 ± 6.2 | 15.6 ± 0.5 | |
1.0 | 1023 ± 9.8 | 1140 ± 3.2 | 13.5 ± 1.0 | |
2.0 | 1041 ± 7.3 | 1137 ± 2.5 | 7.5 ± 1.1 | |
As-extruded | 0 | 804 ± 19 | 890 ± 18.5 | 6.5 ± 3.5 |
0.5 | 786 ± 8 | 881 ± 9.5 | 19.4 ± 3.4 | |
1.0 | 853 ± 7 | 925 ± 1 | 29.7 ± 0.3 | |
2.0 | 876 ± 4 | 946 ± 3.5 | 26 ± 0.1 | |
Triple-annealing state | 0 | 1040 ± 13 | 1139 ± 13.5 | 22.6 ± 0.7 |
0.5 | 1073 ± 1 | 1175 ± 3 | 19.7 ± 0.5 | |
1.0 | 1093 ± 3.5 | 1191 ± 4 | 24.5 ± 0.9 | |
2.0 | 1097 ± 2.5 | 1200 ± 7.5 | 21.7 ± 1.9 | |
Solution aging state | 0 | 1208 ± 3 | 1310 ± 14.5 | 9 ± 0.1 |
0.5 | 1263 ± 19 | 1337 ± 7 | 6.4 ± 0.5 | |
1.0 | 1280 ± 8 | 1374 ± 10 | 12 ± 0.1 | |
2.0 | 1296 ± 18 | 1389 ± 7 | 9.9 ± 0.6 |
挤压态材料经三重退火处理后,材料的强度随着增强相含量的增加而提高。由表1可知,0.5%TiBw/TC18相较于TC18合金,屈服强度和抗拉强度分别提高了33和36 MPa。而TiBw体积分数由0.5%逐渐提高到2.0%时强度指标提升幅度不大,说明此时复合材料的强度主要取决于钛合金基体固有的强度。从表1可知,2.0%TiBw/TC18的延伸率(21.7%)相较于1.0%TiBw/TC18 (24.5%)降低了11.4%,说明TiBw对三重退火后复合材料的延伸率有不利影响。将三重退火态材料的拉伸性能与烧结态TiBw/TC18[21]进行对比,可以看到三重退火态TC18合金的强度略微下降,而0.5%、1.0%、2.0%TiBw/TC18的抗拉强度(1175、1191和1200 MPa)相较于烧结态材料的(1171、1140和1137 MPa)都有小幅度的提高,可以认为材料的强度在同一水平。但材料的延伸率得到了大幅度的提高,1.0%和2.0%TiBw/TC18的延伸率从13.5%和7.5%分别提高到24.5%和21.7%。强度基本保持不变但是延伸率成倍增长的原因如下:(1) 热挤压对原始β晶粒的细化;(2) 三重退火热处理使材料的组织多级化,既有大尺度的αc提供塑性变形能力,又有βf保证高强度;(3) TiBw定向排列可以更好地承担载荷与传递应力。
挤压态材料经固溶时效处理后的性能变化规律与经过三重退火后的规律相似。结合表1可以看出,固溶时效后材料的抗拉强度相较于烧结态材料提高了200 MPa左右,并且1.0%与2.0%TiBw/TC18的延伸率(12%、9.9%)与烧结态相当。其中1.0%TiBw/TC18抗拉强度为1374 MPa,并保持了12%的延伸率,获得了优异的综合性能,说明经过挤压与固溶时效热处理后烧结态材料的性能得到显著改善。对比固溶时效与三重退火后材料的性能可看出,固溶时效后材料强度更高但塑性降低,其原因为固溶时效后可塑性变形的GBα与αc的含量降低并且尺寸减小,强度高但几乎不可塑性变形的βf比例增多。
综上,通过挤压与热处理后,烧结态材料的综合性能得到大幅度提高,并可以通过选择不同的热处理制度来调控材料的组织,以使材料的性能满足不同应用的要求。
2.3 挤压态与三重退火后TiBw/TC18的断裂分析
图7和8分别为挤压态和三重退火后1.0%TiBw/TC18断口与侧断面SEM像。由图7a低倍断口像可以观察到大量韧窝与撕裂棱,其为微孔聚集型断裂,这也对应了挤压态材料的高延伸率。图7b中观察到TiBw被拉断或拔出的痕迹,说明TiBw在断裂过程中发挥了增强作用。由图7c低倍侧断面像中观察到曲折扩展的主裂纹,并且在主裂纹旁伴随有二次裂纹产生,证明断裂要消耗更多的能量。相比烧结态侧断面,挤压态侧断面组织有更明显的塑性变形痕迹,表面粗糙不平,在距离断口较远处也是同样现象,说明挤压态β相在缺少α片层析出强化的情况下拥有更好的塑性变形能力。图7d中观察到断裂为多段的TiBw,说明TiBw充分发挥了增强效果,还可以观察到挤压态材料裂纹的萌生也发生在TiBw处。同时图中密集且均匀分布在一个β晶粒内部的滑移带,也说明了挤压态材料具有优异的塑性变形能力。
图7

图7 挤压态1.0%TiBw/TC18断口与侧断面SEM像
Fig.7 Low (a, c) and high (b, d) magnified SEM images of tensile fracture (a, b) and fracture side surface (c, d) of as-extruded 1.0%TiBw/TC18 (Inset in Fig.7d shows the enlarged view)
图8
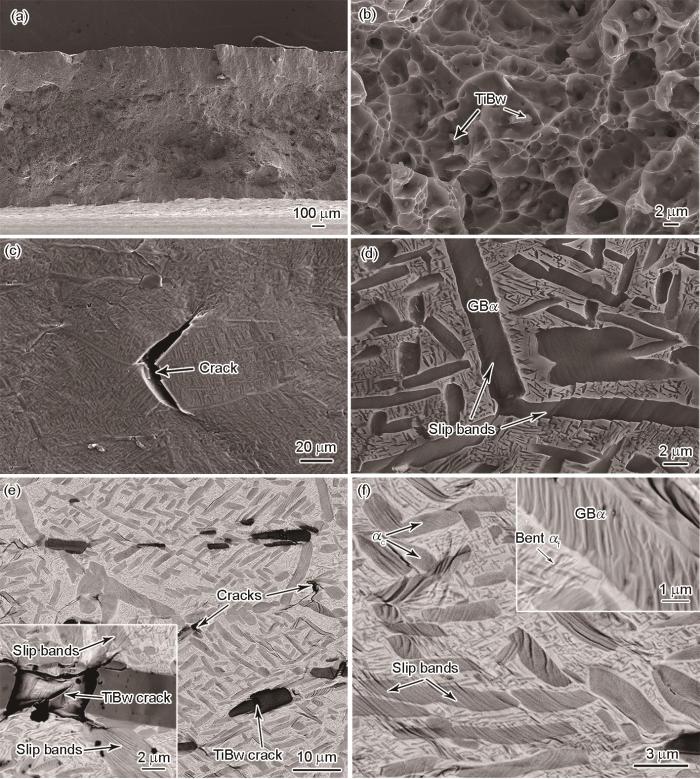
图8 三重退火态1.0%TiBw/TC18断口与侧断面SEM像
Fig.8 Low (a, c) and high (b, d-f) magnified SEM images of tensile fracture (a, b) and fracture side surface (c-f) of as-extruded 1.0%TiBw/TC18 after triple-annealing (Insets in Figs.8e and f show the enlarged views)
从图8a可以观察三重退火后1.0%TiBw/TC18断口为杯锥状断口,只有纤维区与剪切唇,说明材料塑性较好,断裂为韧性断裂。从图8b可观察到大量韧窝,韧窝尺寸不同,大尺寸韧窝中一般可以观察到断裂或脱黏的TiBw。相较于烧结态材料,此断口韧窝中心的TiBw基本都垂直于断口方向,所以其断裂或者脱黏时形成的韧窝为较小的等轴状韧窝。其余不含TiBw的韧窝对应αc或者αf,由于α取向尺寸不同所以韧窝大小不一。这也证明了该状态下材料断裂时裂纹穿过了原始β晶粒,发生了穿晶断裂。如图8c与d所示,大尺寸GBα在拉伸过程中发生大量塑性变形,最终应力在三叉晶界处集中,若晶界边缘是强度很高的αf,则裂纹就会在三叉晶界处萌生。如图8e所示,除了在三叉晶界处萌生裂纹之外,TiBw的断裂也会萌生裂纹,同时裂纹还可以在αc与βf的界面处萌生。同时还可观察到TiBw断裂后萌生的裂纹尖端被基体钝化并引起基体的塑性变形,裂纹的进一步扩展必然要伴随塑性断裂,这对材料的韧性是有利的。图8f中可以观察到αc中存在大量的滑移带,说明粗大的αc对材料的塑性是有利的。βf中没有观察到明显的滑移带,但于邻近αc和GBα的βf上形成了小范围的滑移带,此范围内的αf发生了变形弯曲,说明αc与βf界面处的应力集中可以使很小范围内的βf产生塑性变形。
3 结论
(1) 热挤压使复合材料的β晶粒尺寸从70 μm降至40 μm左右。挤压态复合材料由于缺少α析出相的增强而强度明显低于烧结态材料,但是塑性最多提高了3倍有余。其中挤压态2.0%TiBw/TC18的抗拉强度为946 MPa,延伸率为26%。挤压态复合材料的断裂属于微孔聚集型韧性断裂。
(2) 挤压态复合材料三重退火热处理后,得到多级组织,包括粗大的GBα、棒状αc和细小的针状αf;三重退火热处理使材料强度相对烧结态略有提高,并同时使延伸率提高了2~3倍。其中1.0%TiBw/TC18经过三重退火热处理后强度达到1191 MPa,同时保持了24.5%的延伸率。三重退火热处理后材料的裂纹在三叉晶界点、GBα和αc与周围组织的界面处以及TiBw断裂处萌生。
(3) 经固溶时效,材料的组织与三重退火后的组织类似,只是GBα和αc的含量与尺寸明显降低。其强度相对烧结态材料提高了约200 MPa,塑性基本与烧结态同一水平。其中1.0%TiBw/TC18经过固溶时效热处理后强度达到1374 MPa,同时保持了12%的延伸率,具有良好的强度塑性匹配。
来源--金属学报