分享:Al-AlN异构纳米复合材料的组织构型与热稳定性
1.
2.
采用FESEM、TEM、EBSD、拉伸实验和热暴露实验等方法研究了Al-AlN异构复合材料的微观组织、力学性能和热稳定性,分析了复合材料的热稳定性及其稳定机理。结果表明:Al-AlN复合材料的组织为由粒子富集区和粒子贫乏区交替分布形成的异质片层结构,粒子富集区的基体晶粒为超细晶结构,粒子贫乏区为粗晶结构;该复合材料在500℃长达100 h的热暴露条件下表现出优异的热稳定性,并且其热稳定性和抗拉强度的综合性能组合显著优于传统的耐热铝合金;分析认为其主要的热稳定机理是高温下晶界上的AlN纳米颗粒钉扎晶界,抑制了晶界迁移和晶粒长大,从而使该Al-AlN异构纳米复合材料在表现出优异的强度-塑性匹配的同时,还表现出良好的热稳定性。此外,在热暴露实验的初期,还发现了异常强化和硬化现象,且热暴露温度越高其强度和硬度提高的幅度越大,这主要与热处理过程中发生了晶界驰豫强化有关。
关键词:
铝基复合材料凭借其低密度、高比强度、高比模量、低膨胀、高热导、良好的耐磨性等综合性能优势在交通运输、航空航天、电子封装等高端制造领域展现出广阔的应用前景[1~3]。其中,以轻质高强、高韧、高热稳定为代表的高性能陶瓷颗粒增强铝基复合材料(particle reinforced aluminum matrix composite,PRAMC)成为助力汽车、轨道交通、航空和国防等对结构重量极其敏感领域的关键构件实现轻量化,及实现碳达峰和碳中和国家重要战略目标的重要基础材料之一,是当前材料轻量化领域的研究热点[4~6]。目前常用的陶瓷颗粒增强相主要有SiC、Al2O3、TiC、TiB2、AlN、Al3BC和Si3N4等。其中,AlN具有六方纤锌矿型的晶体结构,密度为3.26 g/cm3,弹性模量为310 GPa,热膨胀系数为4.84 × 10-6℃-1,热导率为320 W/(m·K),具有低膨胀性、高热稳定性及高硬度等优点,鉴于其优异的物理化学性能,近年来逐渐成为一种具有重要发展潜力的增强相[7,8]。然而由于在Al基体中引入了硬度较高的增强相颗粒,导致材料的塑性和断裂韧性显著下降,严重影响材料使用的安全性,即颗粒铝基复合材料低塑韧性限制了其发展和应用。
另外,在一些中/高温(300~500℃)应用场合,对铝基合金的高温强度和热稳定性提出了更高的要求,但传统耐热铝合金主要是通过合金化的方式来实现,其高温使用寿命与性能稳定性受到了其较低的高温强度与抗蠕变性能不足的巨大限制,而难以满足要求。如,汽车铝合金活塞的高温蠕变-疲劳破坏,铝合金架空输电线缆因蠕变导致的熔断等失效行为[9,10]。目前大多数高强铝合金的强度在高温下急剧下降,如7075铝合金,其200和300℃的高温抗拉强度分别约为室温抗拉强度的约30%和10%。当前交通运输领域如汽车发动机上的关键零部件(如活塞、气缸、缸盖等)需要能够适用于300~400℃温区的高强韧铝合金材料。高功率密度发动机在服役时其核心零部件(活塞)的工作环境尤为复杂苛刻,活塞顶部温度可高达400℃以上,达到纯Al熔点的75%以上,而且还要承受最大爆压15~20 MPa,如今汽车工业迫切要求发动机活塞能够在350~400℃温区内正常和安全服役[11]。但对绝大多数高强铝合金来说,在高温下基体晶粒将会长大,且由于高温下强化元素(Cu、Zn、Mg、Ag等)扩散速率加快,进而导致析出强化相的严重粗化,因此在高温下服役时基于传统细晶强化和析出相强化的强化机制难以有效发挥强化作用,导致力学性能(强度、硬度、韧性等)急剧衰退。近年来Gao等[12,13]在通过构建界面偏聚结构实现析出相的稳定化方面取得了突破性进展,通过调控Sc、Zr元素偏聚显著改善了θ′-Al2Cu的稳定性,从而显著提升了Al-Cu系合金的热稳定性和高温蠕变性能,最终突破了时效强化铝合金无法在250℃以上服役的瓶颈,并实现了300℃、30 MPa的严酷蠕变环境下小于10-9 s-1的极低蠕变速率并大于600 h的蠕变寿命。
由于陶瓷颗粒具有较高的熔点与模量,陶瓷颗粒增强铝基复合材料可以有效发挥增强相与Al基体的互补优势,因此能够表现出优异的室温和高温力学性能[14]。当前高性能颗粒增强耐热铝基复合材料已经成为突破铝基材料高温服役最具前景和可行性的策略之一。Tang等[15]采用低温球磨-固结工艺制备具有纳米结构的10%SiCp/5083 (体积分数)复合材料,经过500℃退火后依然能很好地保持复合材料的强度和基体晶粒尺寸的稳定,具有很高的热稳定性。Ma等[7]在高耐热铝基复合材料的研究方面,利用液-固反应法制备了AlN纳米颗粒增强铝基复合材料,原位合成的AlN纳米颗粒通过孪晶键合链接在一起形成三维网络骨架,其中含有16.4%AlN (体积分数)纳米颗粒的复合材料在350℃时的抗拉强度可达到190 MPa。但由于其中AlN颗粒体积分数较高,使得材料的塑性较低,均匀延伸率只有1%左右。因此,探究改善铝基复合材料的热稳定性与强塑性匹配的协同提升方法和机制,对于推动铝基复合材料发展和应用具有重要的现实意义和价值。
近年来,研究学者们不断探索新的强韧化机理,基于新的微观结构设计思想,提出了一种新型金属材料——异构金属材料(也称为非均质结构材料,heterostructured materials)[16~18],能够同时获得高强度和良好的塑性,其综合性能超过了混合法则的理论预测值,异构材料表现出传统的均质材料所无法达到的优异综合性能。目前异构材料组织类型主要有异质片层结构、叠层结构、梯度结构和核壳结构,其共同特征是,其组织中存在跨尺度的微观组织结构(主要是指基体晶粒尺寸),即同时存在粗大的晶粒和细小的晶粒,并且粗大的晶粒被细小的晶粒所包围,根据经典的Hall-Petch关系可知,晶粒越细小,强度越高,因此细小晶粒可以认为是“硬相区”,而粗大晶粒可以认为是“软相区”。 由于异构金属材料中结构单元的微观结构(晶粒尺寸、片层厚度等)和力学性能(强度、塑性、韧性等)存在显著差异,具有显著的非均匀特征,因此其力学行为和变形过程均表现出许多与均质结构材料不同的特征,如强度不遵循混合法则、出现加工硬化率的反转现象等。这些特性使得异构金属材料的强度和塑韧性匹配远远优胜于传统材料,当前金属材料的异构化设计已成为一种极具潜力的新型强韧化策略。例如,Wu等[16]利用异步轧制技术和退火,制备出纳米异质片层结构的纯Ti,实际上可以认为是一种“软-硬”复合的层片状微结构,其中高强度的超细晶“硬”层片为基体,弥散分布着体积分数约为25%、大塑性的再结晶晶粒的“软”片层。该结构表现出很大的加工硬化能力,甚至超过了粗晶结构。Geng等[19]利用累积叠轧的方法制备出层状异构的TiC/Al-Mg-Si纳米复合材料,实现了强度和塑性的协同提升,获得了屈服强度443 MPa和均匀延伸率6.4%的良好拉伸力学性能。
在前期的研究工作[4]中,利用异构组织设计策略提高了Al3BC/6061铝基复合材料的强塑性和刚度匹配,其抗拉强度和均匀延伸率分别为495 MPa和4.3%,且弹性模量达到105 GPa的优异力学性能组合。目前异构材料的研究重点是在室温下的强度和塑韧性匹配,但对于其热稳定性方面的研究和报道较少。因此,本工作以Al-AlN异构纳米复合材料为研究对象,探究高温下热暴露对其异构组织稳定性和力学性能的影响,并对其微观组织、热稳定性机制展开深入的分析,以期为制备高强塑、高热稳定铝基复合材料提供依据。
1 实验方法
以原位自生Al-8.2AlN (质量分数,%)复合材料作为研究对象,将Al-8.2AlN复合材料棒材在580~600℃进行热挤压,挤压比约为9∶1,最终得到直径30 mm的圆棒。为研究Al-8.2AlN复合材料的高温下长时热稳定性,对其进行了一系列不同温度和时间的热暴露实验。实验对象选取直径为30 mm的Al-8.2AlN圆棒为原材料,沿材料轴向切取一系列长度为40 mm的圆柱体,然后将一系列的圆柱体分别放入温度为350 和500℃的马弗炉进行热暴露处理,保温时间分别为1、2、4、5、10、20、50 和100 h,并在达到相应的处理时间后,取出样品空冷。
采用配备能量色散X射线谱仪(EDS)的Quanta 250F场发射扫描电子显微镜(FESEM),对热暴露前后的样品进行微观组织分析,并利用Tecnai G2 20透射电子显微镜(TEM)观察组织中AlN粒子的微观形貌、尺寸分布及基体内的位错形态等。为了进一步分析热暴露实验中Al基体晶粒的变化,使用Auriga FIB/SEM双束系统对不同状态下的铝基复合材料进行电子背散射衍射(EBSD)分析。扫描区域尺寸设置原则上保证样品采集区域所采集的晶粒个数超过100即可,加速电压为15 kV,束流强度20 nA,样品倾斜角度70°。TEM样品的制备方法如下:首先使用线切割从样品上切取厚度为0.5 mm的薄片,采用粗细砂纸依次对样品进行粗磨,直至样品被磨至厚度60 μm左右,随后使用TEM冲孔器将样品冲裁为直径3 mm的圆片,接着使用凹坑仪对试样进行进一步的减薄,将样品中心凹薄至15~20 μm,上述步骤完成后,使用Gatan PIPS695离子减薄仪获得具有较大薄区的TEM样品。
使用Walter + bai LFM20KN拉伸试验机对不同热暴露时间的复合材料样品进行拉伸性能测试,拉伸速率为2 × 10-4 s-1,所用板状试样的标距为15 mm、宽度2.5 mm、厚度2 mm。热暴露前后的拉伸试样均沿着挤压方向切取,并将样品采用砂纸打磨至平滑,防止线切割产生的割痕对拉伸实验的影响。每个样品至少选取3个测试样品,并取平均值。
2 实验结果
2.1 Al-AlN复合材料的微观组织
图1a和b所示分别为原始挤压态Al-AlN异构纳米复合材料纵截面和横截面(插图所示)的SEM像。从图1a可以看出,热挤压变形后,在复合材料内部形成了沿挤压方向的非均匀的类异质片层结构,而在横截面上(图1b)形成了波浪状结构。其中粒子富集区和粒子贫乏区交替分布,粒子富集带宽度为2~7 μm,粒子贫乏的Al条带宽度为1~3 μm。在更高的放大倍数下(图1c),可以看到AlN纳米粒子相互连接形成微米尺度的粒子链,并且这些粒子链在三维空间构建形成三维网络结构(3D network structure),该结构在前期的研究工作[7,8]中已经被证实。如图1d所示,对颗粒(图1c中的A点)进行的EDS分析进一步证实,颗粒含有Al和N元素,这证明Al基体中分布的颗粒均为AlN相。图1d中插图显示了AlN颗粒尺寸的统计信息,结果表明粒子的平均尺寸约为95 nm。
图1
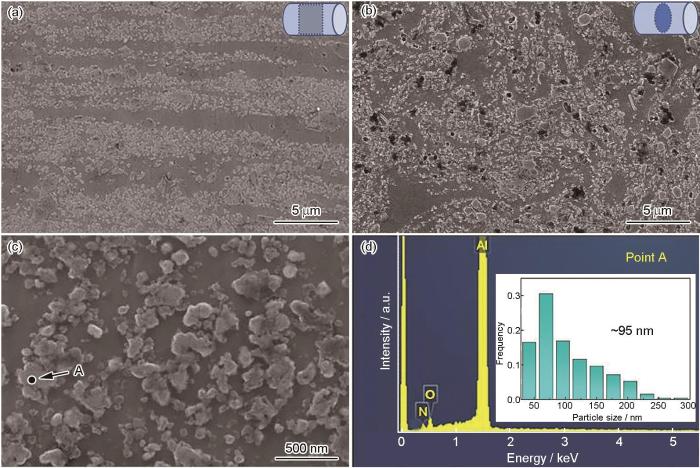
图1 挤压态Al-8.2AlN异构纳米复合材料微观组织的SEM像和EDS分析,以及AlN粒子的尺寸分布
Fig.1 SEM images of Al-8.2AlN heterostructured nanocomposites on the longitudinal section (a) and cross section (b); SEM image of AlN particles at a higher magnification (c); EDS analysis for point A in Fig.1c (d) (Insets in Figs.1a and b schematically showing the selected positions for observation, inset in Fig.1d showing the statistics of the AlN particle size)
图2所示为Al-8.2AlN异构纳米复合材料中基体晶粒组织和AlN颗粒分布的TEM像。如图2a和b所示,在纵截面上可以看到沿挤压方向被拉长的Al基体晶粒带(红色箭头所指)和由AlN纳米颗粒团簇组成的富颗粒带(黄色箭头所指)。其中大部分为被拉长的Al晶粒,其宽度为1~2 μm,长度为2~10 μm,呈现出挤压变形后的典型组织。此外,值得注意的是,富颗粒带基体区域的Al晶粒明显细化,呈现出超细晶结构的特征,如图2c所示。这是因为在热变形过程中,在AlN纳米颗粒的钉扎和切割作用下,基体Al晶粒得到显著细化,而且AlN颗粒还能够抑制晶界迁移和促进基体晶粒发生动态再结晶,从而促进了超细晶组织的形成[20]。同时可以看到,晶内的AlN纳米颗粒可以有效地钉扎位错,从而限制位错在Al晶粒中的滑移,提高了位错储存能力[21],如图2d中蓝色箭头所示。分析认为,超细晶结构的Al晶粒与AlN纳米颗粒以及基体中塞积的大量位错可以协同提高材料的强度。
图2

图2 Al-AlN异构纳米复合材料纵截面的TEM像
Fig.2 TEM images of Al-AlN heterostructured nanocomposites on longitudinal section
(a-c) Al matrix grains (red arrows) and the distribution of AlN nanoparticles (yellow arrows)
(d) interaction of AlN particles with dislocations (blue arrow) in the matrix
为了进一步分析复合材料中AlN纳米颗粒与Al基体的界面结合情况,采用高分辨透射电镜(HRTEM)对AlN纳米颗粒及Al基体的相界面结构进行表征,如图3所示。从图3a可以看到,2个相邻的AlN颗粒分布在Al基体中,尺寸分别约为35和20 nm。进一步放大如图3b所示,基体中的这2个AlN纳米颗粒并没有紧密连接在一起,颗粒之间还存在大约几纳米的间隙。此外,根据界面区的晶格图像(图3c)可知,AlN和Al基体之间的界面洁净、结合良好,没有其他界面化合物的形成。另外,AlN与Al晶粒之间保持一定的取向关系即(111)Al//(
图3
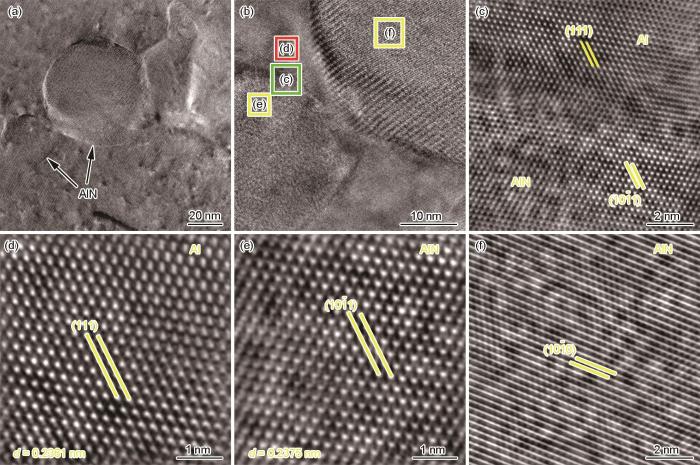
图3 AlN及AlN/Al基体界面结构的HRTEM表征
Fig.3 HRTEM characterizations of AlN and the AlN/Al matrix interface structure
(a, b) HRTEM images of AlN particles
(c) HRTEM image of the green square in Fig.3b showing the metallurgical atomic bonding and matching between AlN and Al matrix (d-f) HRTEM images of the red square and yellow squares in Fig.3b showing the atomic plane spacing of the Al matrix and the AlN nanoparticles (d—interplanar spacing)
2.2 热暴露处理对Al-AlN复合材料微观组织的影响
为了探究热暴露处理对Al-AlN纳米复合材料Al基体晶粒尺寸和结构的影响,对在500℃热暴露100 h前后的复合材料试样进行了EBSD表征分析,结果如图4所示。通常认为,在高于再结晶温度以上的温度进行长时间的热暴露会导致Al基体晶粒及其析出相的长大或粗化。图4a所示为原始态热挤压Al-AlN纳米异构复合材料基体晶粒组织图(反极图IPF)。可以看到,大多数Al晶粒沿着挤压方向被拉长,并且在拉长晶粒之间还存在着晶粒尺寸小于1 μm的超细晶组织,图4c所示为其晶粒尺寸分布图,基体晶粒的平均尺寸约为1.41 μm。值得注意的是,与热暴露处理前的挤压态样品相比,热暴露处理以后Al基体晶粒的形貌(图4b)和平均晶粒尺寸(图4d)变化不大。且从图4b可以看到大量的拉长晶粒以及分布其间的少量超细晶晶粒,并且这些超细晶晶粒在高温长时的保温过程中没有进一步长大,统计结果(图4d)显示基体平均晶粒尺寸约为1.42 μm,与热暴露之前晶粒尺寸相当。上述实验结果表明,Al-AlN异构纳米复合材料在500℃的高温下表现出优异的晶粒尺寸稳定性。
图4
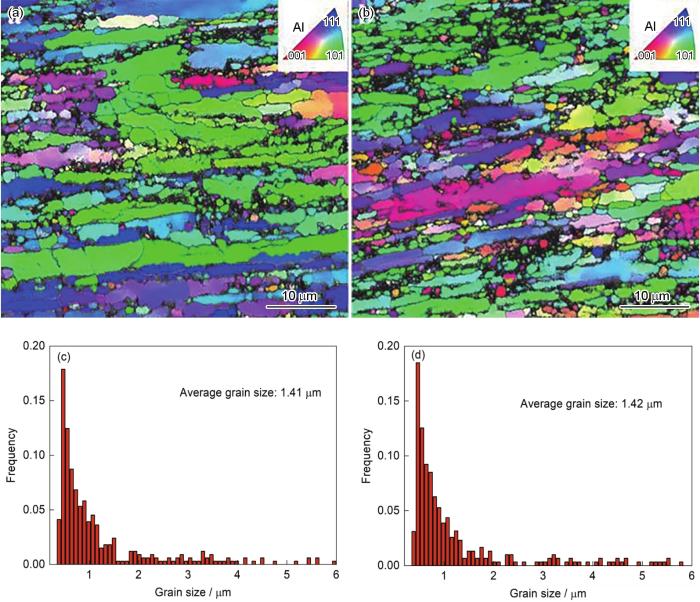
图4 Al-AlN异构纳米复合材料500℃热暴露处理100 h前后基体晶粒尺寸的EBSD分析
Fig.4 Inverse pole figures (a, b) and grain size distributions (c, d) for the heterostructured Al-AlN nanocomposites before (a, c) and after (b, d) thermal exposure treatment at 500oC for 100 h
为了进一步揭示热暴露过程中Al-AlN异构纳米复合材料基体晶粒的回复和再结晶情况,对图4所示Al-AlN异构纳米复合材料热暴露前后的EBSD数据进行处理分析,结果如图5所示。在热暴露之前的原始样品中,晶粒主要是以变形态的结构(红色区域)和亚结构(黄色区域)为主,再结晶晶粒(蓝色区域)的体积分数约为12.5%。经过热暴露处理以后,晶粒结构各组分的体积分数与原始样品中各组分的体积分数基本一致,如图5b和c所示。分析认为,分布在基体晶粒晶界上的AlN纳米颗粒阻碍了高温热暴露过程中晶界的迁移,从而阻碍晶粒的长大,同时基体晶粒内部的AlN纳米颗粒也能够在一定程度上抑制亚晶界的旋转。根据图5d的晶界取向差的体积分数统计分析可知,热暴露后纳米复合材料的小角晶界(晶界取向差为2°~15°)的体积分数略有降低,从15.2%下降到8.9%,这主要是由于小角晶界在高温下会向大角晶界转化,进而导致大角度晶界(晶界取向差大于15°)的体积分数从51.5%相应增加到60.1%。上述实验结果表明,基体中AlN纳米颗粒显著提高了铝基复合材料的热稳定性。
图5
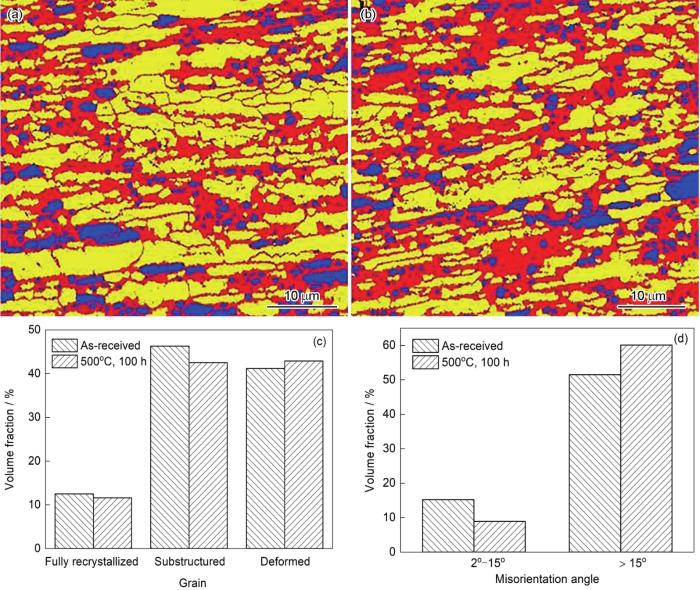
图5 Al-AlN异构纳米复合材料500℃热暴露处理100 h前后再结晶分析图
Fig.5 Recrystallization proportions (a, b) and their volume fraction variations (c) and misorientation angle variations (d) for the heterostructured Al-AlN nanocomposites before (a) and after (b) thermal exposure treatment at 500oC for 100 h (Fully recrystallized grains are shown in blue, substructured grains in yellow, and severely deformed grains in red)
2.3 热暴露处理对Al-AlN复合材料力学性能的影响
对不同条件下热暴露处理前后的样品进行了显微硬度和拉伸力学性能测试,结果如图6所示。图6a为Al-AlN纳米复合材料在350℃热暴露不同时间的显微硬度变化曲线。值得注意的是,Al-AlN纳米复合材料的平均Vickers硬度在350℃热暴露2 h后从79.5 HV增加到90 HV;随着保温时间延长,其显微硬度略有降低,然后保持在86.5 HV左右。对传统的耐热铝合金,350℃以上的高温热暴露后材料会出现明显的软化,其反映在显微硬度上会有明显的降低趋势,但在本工作中的Al-AlN异构纳米复合材料的显微硬度并没有发生明显的降低现象,表明该复合材料在350℃长时保温条件下保持了良好的力学性能稳定性。图6b所示为Al-AlN纳米复合材料在500℃热暴露处理不同时间前后的拉伸性能曲线,根据不同热暴露时间的拉伸曲线计算出不同状态下复合材料的平均抗拉强度、屈服强度和延伸率见表1。原始挤压态Al-AlN异构纳米复合材料的平均屈服强度和抗拉强度分别为(232 ± 13) MPa和(299 ± 20) MPa,伸长率为12.9% ± 1.71%。根据文献[10,12]报道,经过高温热暴露或热处理后,纳米材料的强度会发生下降。然而,当在500℃热暴露条件下保温5、10 h时,Al-AlN异构纳米复合材料的抗拉强度略有增加(表1),保温时间延长到10 h时,其平均抗拉强度达到(390 ± 10) MPa,与原始样品相比提高了30.4%,然而延伸率急剧下降到2.2%。随着保温时间继续延长到20 h以上,试样的抗拉强度又发生降低。在随后100 h的保温时间内,复合材料的抗拉强度和屈服强度仅在一个较小的范围内波动,并与原始样品的强度保持同一水平,如图6c所示。同时经过较长时间的热处理后样品的延伸率也有所提高,达到7%左右。上述实验结果表明, Al-AlN异构纳米复合材料经过500℃长达100 h的热暴露处理后,仍表现出优异的力学性能稳定性。
图6
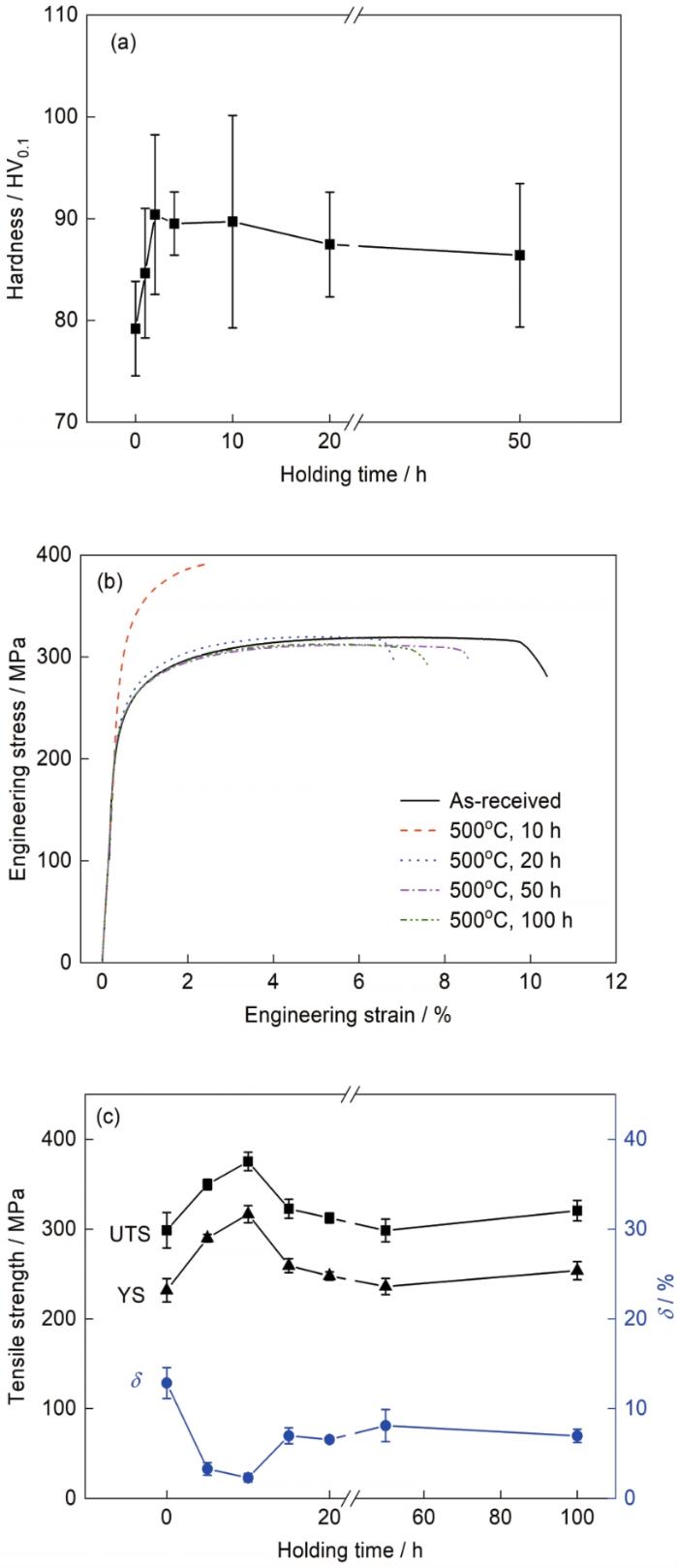
图6 Al-AlN异构纳米复合材料热暴露前后的力学性能
Fig.6 Mechanical properties of heterostructured Al-AlN nanocomposite before and after thermal exposure
(a) variation of microhardness versus the thermal exposure time at 350oC
(b) engineering stress-strain curves after exposure at 500oC for different holding time
(c) ultimate tensile strength (UTS), yield strength (YS), and elongation (δ) variation curves of the composites with the exposure time
表1 Al-AlN纳米复合材料500℃热暴露处理不同时间的拉伸力学性能
Table 1
State | YS / MPa | UTS / MPa | δ / % |
---|---|---|---|
As-received | 232 ± 13 | 299 ± 20 | 12.9 ± 1.71 |
500oC, 5 h | 290 ± 4 | 350 ± 6 | 3.3 ± 0.70 |
500oC, 10 h | 315 ± 10 | 390 ± 10 | 2.2 ± 0.46 |
500oC, 15 h | 259 ± 8 | 323 ± 11 | 6.9 ± 0.88 |
500oC, 20 h | 248 ± 5 | 312 ± 6 | 6.6 ± 0.17 |
500oC, 50 h | 236 ± 9 | 298 ± 13 | 8.1 ± 1.79 |
500oC, 100 h | 251 ± 10 | 321 ± 11 | 6.9 ± 0.75 |
3 分析讨论
以上实验结果表明,AlN颗粒增强铝基异构纳米复合材料在500℃的高温以及保温时间长达100 h的条件下,仍表现出良好的热稳定性,且具有良好的强度和塑性匹配。下面将从3个方面分析讨论Al-AlN异构纳米复合材料具有高强度和延展性以及良好热稳定性的内在机理。
3.1 Al-AlN异构纳米复合材料中异质片层结构的形成
根据实验数据可知,AlN纳米颗粒的加入可以显著提高Al-AlN异构纳米复合材料的强度,同时保持良好的延性(> 10%)。实际上,复合材料良好的综合力学性能是由其独特的微观结构决定的,因此首先分析其微观组织特征及其形成机理。根据文献[20~23]报道,弥散分布的AlN纳米颗粒在铝基复合材料中具有良好的强化效果。而在本工作中,AlN纳米颗粒在Al基体中通过液-固原位反应形成,颗粒尺寸保持在纳米尺度范围内(如图1所示)。然而,由于纳米颗粒具有较高的表面能,粒子的聚集现象是不可避免的,进而形成了一些纳米颗粒网络结构,这在前期的工作[7]也报道过。但经过热挤压塑性变形处理,进一步调控了基体中AlN颗粒的空间分布,在Al基体上形成了交替分布的粒子富集区(PRDs)和粒子贫乏区(PLDs)的异质片层结构,如图7a所示。经过塑性变形后,粒子贫乏区中比较粗大的Al晶粒被拉长,形成了层状结构;而在粒子富集区中,由于大量AlN纳米颗粒的钉扎效应,使得Al基体晶粒得到了显著细化,从而形成了超细晶结构,并且与纳米粒子一同沿挤压方向形成条带状分布。因此,最终在Al基体中形成了由PLDs和PRDs组成的异质片层结构。同时,在热挤压过程中,粒子富集区域内的纳米粒子三维网状结构会随着Al基体的流变变形发生整体的变形,并且大部分三维网状结构不会发生变化 [8]。根据文献[23,24]报道,这种粗晶区(软区)和细晶区(硬区)交替分布的异质片层结构,有利于发挥“硬区”的强度并具有“软区”的良好塑性,且大量的异质界面能够进一步产生异质变形诱导强化(HDI)和硬化作用,进一步提高材料的加工硬化率,从而使得材料表现出优越的强度和塑性匹配。因此,这种异质片层结构有助于提高Al-AlN异构纳米复合材料的综合力学性能。
图7

图7 Al-AlN异构纳米复合材料层状异质结构示意图及其热稳定温度和抗拉强度与其他铝合金[27~40]的对比图
Fig.7 Schematic of lamellar heterostructure of the heterostructured Al-AlN nanocomposites (UFG—ultrafine grain, ECG—elongated coarse grain, PRD—particle rich domains, PLD—particle lean domains) (a) and thermal stable temperature versus tensile strength for current Al-AlN nanocomposite and the comparison with other aluminum alloys[27-40] (b)
3.2 Al-AlN异构纳米复合材料的热稳定性
Al-AlN异构纳米复合材料在500℃的高温热暴露条件下表现出良好的力学性能稳定性,这主要归因于其独特且稳定的异构组织特征。如2.2节中所阐述的,Al-AlN纳米复合材料优良的力学性能热稳定性与其微观结构的稳定性相一致,基体晶粒在500℃、保温达100 h的条件下仍然没有显著的变化,这主要是由于AlN纳米粒子的钉扎作用。在高温下,AlN纳米粒子及其原位构筑的三维网状结构能够钉扎并稳定基体α-Al晶界,从而抑制晶界的迁移和晶粒的粗化,从而使得材料即使经历了高温(500℃)长时(100 h)的热暴露处理后仍能够保持良好的组织稳定性和力学性能稳定性[25,26]。根据文献[16~19]报道,目前大多数研究重点揭示了异构材料具有优异的强度和塑性匹配这一特性,而本工作首次揭示了异构铝基复合材料还具有优异的热稳定性,这也是典型非均质结构复合材料的重要特性之一。
另外,将Al-AlN异构纳米复合材料的耐热温度与其他铝合金及复合材料[27~40]进行了比较,并绘制了材料所能承受的热稳定温度与其抗拉强度的关系图,如图7b所示。可以看出,Al-AlN异构纳米复合材料表现出优异的耐热极限和抗拉强度协同效应,且显著优于目前报道的大多数铝合金和复合材料。目前该材料的热稳定温度比传统的Al-Cu-X[28,30,34,35,37]和Al-Ce-X[29]合金高出200℃左右,其热稳定性和强度的综合性能也明显优于Al2O3/Al和GNPs/Al复合材料的性能[38,40]。Al-AlN异构纳米复合材料优异的热稳定性和强度协同效应是其典型的非均质组织所特有的,因此,本工作设计的具有热稳定性良好的纳米颗粒增强铝基复合材料可作为新一代耐热铝基材料。
对于金属材料,其良好的热稳定性主要取决于组织中基体晶粒和增强相的稳定性。对于Al-AlN异构纳米复合材料,一方面,增强相AlN纳米颗粒具有较高的熔点(> 3000℃)[41],在当前的热暴露温度下不会发生粗化和长大,其在Al基体中具有良好的热稳定性;另一方面,由于大量的AlN纳米颗粒及其构成的纳米颗粒网络沿晶界和在晶粒内部分布,这些颗粒能够抑制高温下晶界的迁移和晶内位错的重排[42]。根据Smith-Zener钉扎原理[43]可以计算出钉扎压力:
式中,PZ为Zener钉扎压力,γAB为晶界张力,fp为颗粒的体积分数,dp为颗粒的直径。晶界的迁移主要取决于3个方面:曲率力、位错驱动力和Zener钉扎力。在高温下,抑制晶界迁移的关键因素取决于Smith-Zener钉扎力所决定的晶界迁移活化能的增加[43]。根据
3.3 Al-AlN异构纳米复合材料热暴露处理过程中的异常强化现象
另外,本工作还发现,Al-AlN异构纳米复合材料经500℃的热暴露处理过程中出现了异常硬化现象,即屈服强度和拉伸强度在保温初期(10 h内)呈现增加的趋势,其平均值分别由232和299 MPa增加到315和390 MPa,分别提高了约35.8%和30.4%。为了理解这一异常的强化或者硬化现象,通过其微观组织的TEM和EBSD数据分析,并没有观察到基体晶粒尺寸和AlN纳米颗粒的明显变化。结合材料的制备过程[7],分析认为,经过高能球磨和剧烈挤压工艺制备的AlN纳米颗粒增强铝基复合材料,其组织中往往含有大量的非平衡晶界,即存在过量的位错、错配区域或过量的自由体积[44~46]。这些非平衡晶界在退火过程中会发生演变,多余的缺陷在晶界弛豫过程中湮灭,这些现象可以在没有任何可测量的晶粒尺寸变化的情况下发生。相关的研究[47]发现,热暴露过程中的晶界弛豫具有显著的强化作用,可以显著提高金属的强度或硬度。并且进一步的研究[48]表明,晶界弛豫产生的强化效果与退火温度密切相关,退火温度越高其产生的强化效果越强。因此,分析认为,在本实验的热暴露过程中发生了晶界弛豫现象并诱导产生了驰豫强化,这应是导致Al-AlN异构纳米复合材料在热暴露实验初期发生强度异常升高的主要原因。进一步通过对不同温度下的热暴露处理强化效果进行比较发现,经500℃热暴露后,Al-AlN异构纳米复合材料的最大抗拉强度提高了约30.4%,而在350℃热暴露处理时,最大显微硬度仅增加了13.2%,进一步证明了热暴露温度越高,其强化效果越显著,这也符合晶界弛豫强化效果与温度有关的特性,这表明晶界弛豫是导致其强度升高的主导因素。但随着保温时间的延长,材料的抗拉强度又发生一定程度的下降,分析认为,这可能是因为在热暴露过程中还存在其他微观结构的演变,如小角晶界向大角晶界的转变等,从而使晶界强化效率略微下降,在一定程度上抵消了晶界弛豫强化的效果,最终导致材料强度略有降低。
4 结论
(1) Al-AlN异构纳米复合材料经过500℃长达100 h的热暴露实验后,其非均匀组织没有显著变化,Al基体中的大部分超细晶粒保持不变,晶粒尺寸与原始样品相近,没有发生再结晶,基体晶粒结构没有显著变化,表现出优异的异构组织稳定性。
(2) Al-AlN异构纳米复合材料经热暴露处理后,其显微硬度和抗拉强度没有明显的降低,主要原因是由于AlN纳米颗粒对晶界的钉扎作用,显著抑制了高温下的晶界迁移和晶粒长大,从而使该复合材料不仅表现出优异的强度-塑性匹配,还具有优异的热稳定性。
(3) Al-AlN异构纳米复合材料在热暴露实验初期表现出异常强化和硬化现象,并且在一定范围内热暴露温度越高其强化和硬化现象越显著,这主要与热暴露过程中发生的晶界弛豫强化有关。
来源--金属学报