分享:TiAl合金板材轧制研究现状
1.
2.
在航空航天和汽车工业领域,轻质高强耐高温的TiAl合金板材是重要的战略结构材料。然而,TiAl合金板材成形难度大,尤其是大尺寸高性能TiAl合金轧板的制备更是困难。本文从TiAl合金轧板制备方法研究现状出发,综述了近年来铸锭冶金轧制、粉末冶金轧制、铸锭直接热轧和叠轧法制备TiAl合金板材的工艺、尺寸、组织和力学性能,论述了上述制备方法的特点及存在的不足,提出了关于制备大尺寸高性能TiAl合金轧板的建议以及未来发展方向。
关键词:
TiAl合金是航空航天和汽车工业领域未来发展的重要工程材料,具有低密度(3.9~4.2 g/cm3)、高弹性模量(室温弹性模量达170 GPa,750℃时约150 GPa,与GH4169相当)、高比强度、高比刚度、低膨胀系数、高导热系数、抗氧化性、抗蠕变性和疲劳性能优异等特点[1, 2]。轻质耐高温的TiAl合金板材应用在飞行器蒙皮、整体壁板类构件和翼舵等结构上具有巨大的应用潜力,将有效提高飞行器的综合性能。图1[3]为TiAl合金薄板和箔制作的蜂窝夹层板,该结构应用于飞行器热保护系统,具有重量轻、强度高、耐用、耐高温等优点。但TiAl合金塑性低、热变形抗力大、热加工窗口窄,导致轧板制备难度大。为降低轧板的制备难度,已研制出诸多体系TiAl合金,目前主流变形TiAl合金主要为β凝固型合金,其包括Ti-43Al-9V系合金[4]、TNB合金(高Nb-TiAl合金)[5]、TNM合金(Ti-43Al-4Nb-1Mo-0.1B合金)[1]等。在高温下,它们的相组成中含有一定量易变形的无序β相,所以具有相对较好的高温变形能力。目前,普通尺寸TiAl合金轧板制备问题已解决。然而,大尺寸TiAl合金轧制板材存在协调变形不均匀、平面应变大、平面应力和残余应力高等问题,导致其易起皱、开裂。迄今为止,国内研究机构尚未能制备出大尺寸高性能TiAl合金板材,从而限制了其工程化应用。本文总结了TiAl合金轧板制备方法及国内外TiAl合金板材轧制研究现状,分析各轧制方法的优势,指出当前存在的问题,并对未来发展趋势进行探讨。
图1
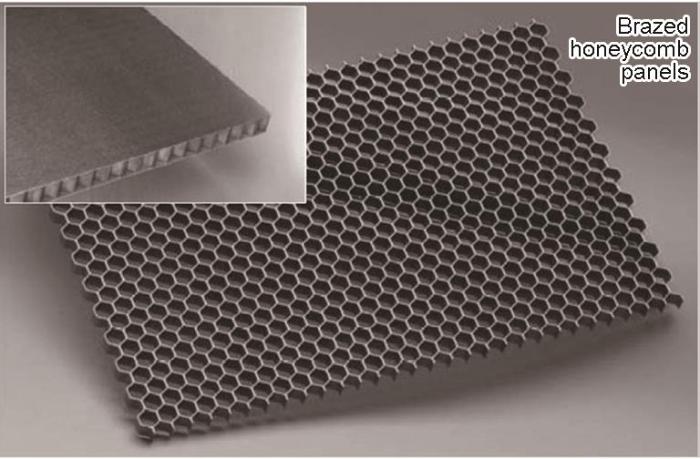
图1 TiAl合金蜂窝芯和夹芯板[3]
Fig.1 An all TiAl honeycomb core and sandwich panel[3]
1 TiAl合金轧板制备方法
轧制是制备高性能TiAl合金板材的主要方法之一。轧板组织均匀,晶粒细小,力学性能良好。根据TiAl合金轧制坯料获得路径不同,TiAl合金板材轧制方法主要分为铸锭冶金轧制、粉末冶金轧制、铸锭直接热轧和叠轧法。目前,为避免轧制过程中TiAl合金温降过快和氧化行为发生,通常将轧坯进行包套处理,然后采用近等温包套轧制坯料获得TiAl合金轧板。其他TiAl合金板材制备方法主要包括物理气相沉积法[6]、元素箔反应法[7]、等离子喷涂成形法[8]、3D打印成形法[9~12]和注射成形法[13]等。
1.1 铸锭冶金轧制
铸锭冶金轧制是传统TiAl合金板材制备方法,图2为铸锭冶金轧制流程示意图。首先通过多次熔炼,制备出成分均匀的TiAl合金铸锭;随后,将合金铸锭进行热等静压处理,减少合金的偏析、微孔、疏松、微裂纹等缺陷,同时实现组织均匀化,并减少铸锭中的残余应力;然后,采用近等温包套锻造(或挤压)对合金铸锭进行多道次锻造(或挤压),使铸造合金中粗大组织破碎、细化,为后续轧制做准备;接下来,采用近等温包套轧制法对锻坯进行多道次高温轧制获得板材;最后,将轧板随炉保温退火,获得组织均匀细小的高性能TiAl合金板材。铸锭冶金轧制研究开始较早,针对该轧制工艺的研究已相对系统,大变形量下轧板组织中粗大晶粒和残余片层得到有效细化,合金室温和高温强度较高,未来有望制备出大尺寸高性能TiAl合金轧板。
图2
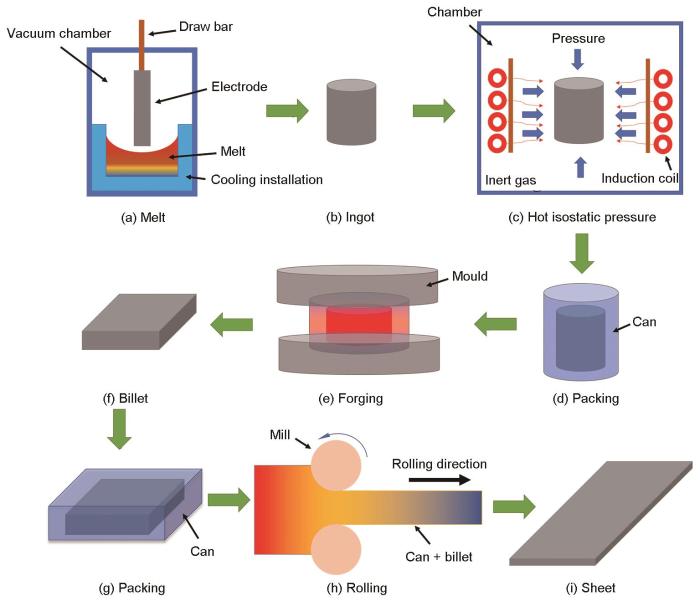
图2 铸锭冶金轧制加工路线
Fig.2 Schematics of ingot metallurgy (IM) rolling route (a-i)
20世纪80年代,Semiatin等[14,15]采用铸锭冶金轧制,制备出尺寸为700 mm × 400 mm的TiAl合金板材,这是TiAl合金板材轧制的开创性成果。1995年,Semiatin和Seetharaman[14]使用等温包套轧制在α + γ两相区制备出Ti-45.5A1-2Cr-2Nb合金板材,轧板总厚度为3~4 mm (含包套)。日本神户制钢所使用坯料尺寸为200 mm × 60 mm × (3~4) mm的Ti-46Al合金,在1100℃等温轧制出厚度为0.93 mm的TiAl合金薄板[16]。俄罗斯采用低温轧制技术(轧制温度低于共析温度Te)制备出Ti-45.2Al-3.5(Nb, Cr, B)板材,最大尺寸可达400 mm × 200 mm × 1.7 mm[17]。德国GKSS研究中心Clemens研究组制备出1000 mm × 450 mm × 1 mm的Ti-45Al-(5~10)Nb-X(B, C)合金板材[3]。目前,奥地利Plansee AG公司在大尺寸TiAl合金板材轧制方面处于世界领先地位,他们提出了先进板材轧制技术(ASRP),可常规生产800 mm × 400 mm × 1.0 mm的γ-TiAl合金薄板,最大可轧制1800 mm × 500 mm × 1.0 mm的大尺寸薄板[15]。该板材轧制是在α + γ两相区完成,板材组织为双态组织,由γ晶粒和层片晶团组成。图3[18]为Plansee AG公司采用ASRP (近等温轧制)和非等温轧制TiAl合金板材宏观形貌及显微组织。
图3
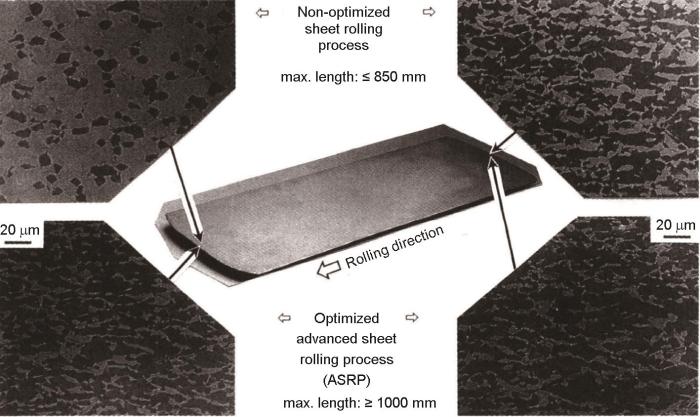
图3 近等温轧制和非等温轧制TiAl合金板材宏观形貌及显微组织[18]
Fig.3 Phase distribution within TiAl sheet after processing under quasi-isothermal rolling conditions and non-isothermal rolling conditions[18]
国内哈尔滨工业大学针对铸锭冶金轧制TiAl合金板材进行了大量研究。2017年,Zhou等[19,20]采用铸锭冶金轧制路线,在1250℃ (α + γ两相区)近等温包套轧制出Ti-44Al-8Nb-0.2W-0.2B-Y合金板材(如图4a[19]),轧制总变形量为85%。该板材组织为细小均匀双态组织,平均晶粒尺寸为5.3 μm,如图5[19]所示。然而,经过大变形量轧制后,TiAl合金中依然存在少量小尺寸残余片层,如图5b[19]所示。轧板室温屈服强度和抗拉强度分别达到962和1174 MPa,塑性为1.0% (此文中塑性指标为伸长率去掉弹性部分,后文不再赘述);800℃高温屈服强度和抗拉强度分别达到681和777 MPa,塑性为37%[19]。其制备的轧板最大尺寸为410 mm × 70 mm × 2.1 mm。该板材是目前国内已知较高室温与高温强度TiAl合金轧板。其强度较高的重要原因之一是轧制变形量高达85%,板材组织中粗大残余片层几乎完全破碎,晶粒和层片晶团细小均匀。
图4
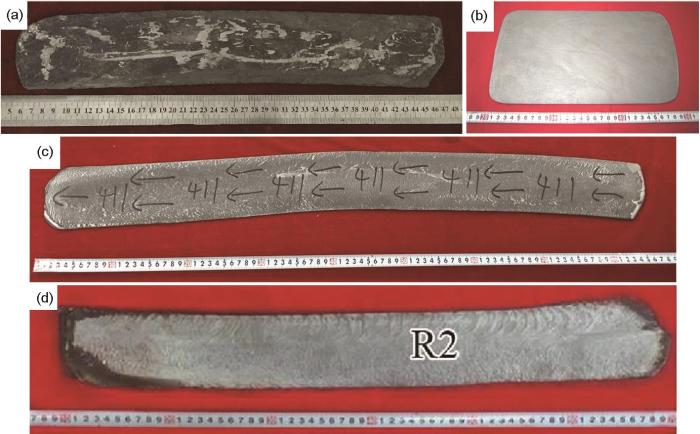
图4 铸锭冶金轧制TiAl合金板材宏观形貌[19,21,22,24]
Fig.4 Appearances of IM rolling TiAl alloy sheets
(a) Ti-44Al-8Nb-0.2W-0.2B-Y alloy[19] (b) Ti-44Al-5V-1Cr alloy[21]
(c) Ti-43Al-9V-0.2Y alloy[22] (d) Ti-45Al-8.5Nb-(W, B, Y)[24]
图5
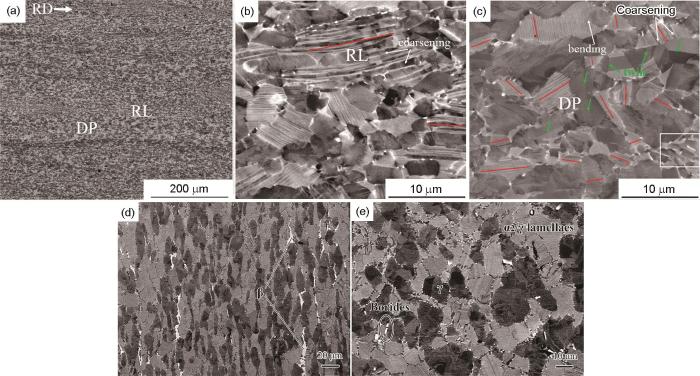
图5 Ti-44Al-8Nb-0.2W-0.2B-Y合金板材及轧制Ti-45Al-8.5Nb-(W, B, Y)合金显微组织[19,24]
Fig.5 Microstructures of Ti-44Al-8Nb-0.2W-0.2B-Y alloy sheet (a-c)[19] and Ti-45Al-8.5Nb-(W, B, Y) alloy sheet (d, e)[24] (RD—rolling direction)
(a) low magnification (b) residual lamellar region (c) duplex microstructure region
(d) normal direction section (e) RD section
2017年,燕山大学刘宏武[21]采用铸锭冶金轧制,在1200~1240℃ (α + β + γ三相区)制备出尺寸为300 mm × 200 mm × 2.7 mm的Ti-44Al-5V-1Cr合金板材,如图4b[21]所示。板材组织主要由等轴γ晶粒、短条状或块状B2相、少量的块状α相组成,平均晶粒尺寸为3.5 μm,如图6[21]所示。室温拉伸速率为5 × 10-4 s-1时,板材抗拉强度为725 MPa,伸长率为2.0%。该轧板组织为等轴组织,晶粒比较细小。通常为保证板材良好的成形能力和力学性能,一般选择在温度适中的α + γ两相区轧制,而该实验轧制温度选择在偏低的α + β + γ三相区。轧制过程中,组织发生β、α→γ相变和γ动态再结晶,当轧制温降过快时,会发生不完全相变,导致大量的β相分布于γ晶粒晶界处,由此形成了等轴组织。通常认为在α + β + γ三相区轧制温度偏低,不利于大尺寸薄板的成形,这项研究对在α + β + γ三相区轧制大尺寸高性能TiAl合金板材具有一定的指导作用。
图6
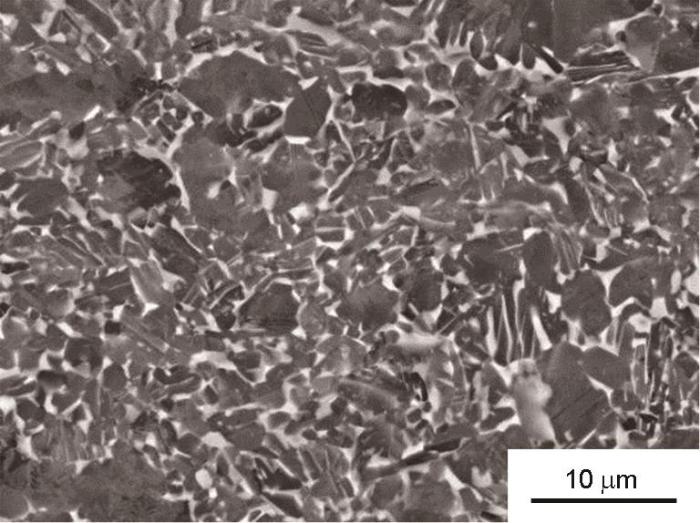
图6 Ti-44Al-5V-1Cr合金板材显微组织[21]
Fig.6 Microstructure of Ti-44Al-5V-1Cr alloy sheet[21]
2018年,哈尔滨工业大学Zhang等[22,23]采用铸锭冶金轧制,在1260℃ (α + γ两相区)近等温包套轧制,制备出尺寸为875 mm × 70 mm × 2.6 mm的Ti-43Al-9V-0.2Y合金板材,如图4c[22]所示。该板材是目前国内已知较大尺寸的TiAl合金轧板,其长度较长,但宽度不足。Ti-43Al-9V系合金在高温下β相含量较高,相对更容易变形,其显著降低了大尺寸板材轧制难度,进一步推动了国内大尺寸TiAl合金轧板制备进程。该板材显微组织包括γ再结晶晶粒(尺寸3~20 μm)、不规则粗大的β/γ层片和规则细小的α2/γ层片,轧制后新形成的层片晶团平均尺寸约为30 μm,如图7[23]所示。该轧板室温屈服强度和抗拉强度分别为684和826 MPa,室温塑性为1.4%;700℃时抗拉强度为671 MPa,塑性为27%;800℃高温时抗拉强度为391 MPa,塑性为67.5%。该合金板材室温和高温力学性能良好,但室温组织中存在一定量的脆性B2相,导致合金板材力学性能降低,可通过进一步优化热处理工艺,调控组织,降低乃至消除组织中的B2相,以释放该合金体系板材的力学性能潜力,制备出大尺寸高性能TiAl合金板材。
图7
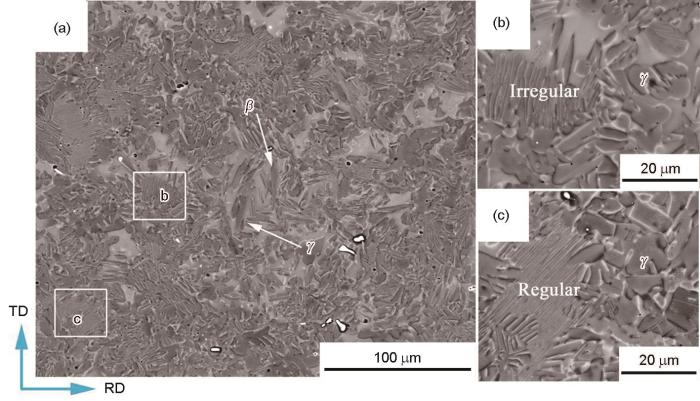
图7 Ti-43Al-9V-0.2Y合金板材显微组织[23]
Fig.7 Microstructures of Ti-43Al-9V-0.2Y alloy sheet[23] (TD—transverse direction)
(a) low magnification (b) irregular lamellar structures (c) regular lamellar structures
2018年,北京科技大学Gao等[24]采用铸锭冶金轧制,在1270℃制备出最大尺寸为600 mm × 75 mm × 3 mm的Ti-45Al-8.5Nb-0.2W-0.2B-0.03Y合金板材(如图4d[24]),轧制总变形量为86.6%。该轧板组织为双态组织,平均晶粒尺寸为6.0 μm,如图5d和e[24]所示。该合金板材室温屈服强度和抗拉强度分别达到911和1053 MPa,伸长率为1.8%;800℃高温屈服强度和抗拉强度达到556 和745 MPa,伸长率为42.5%;900℃高温屈服强度和抗拉强度达到369 和414 MPa,伸长率为93.6%。该板材是目前国内尺寸较大的高Nb-TiAl合金轧板,并且力学性能较好。同时,他们通过控制轧制温度实现了板材组织的原位控制,经热轧可直接获得细化均匀的DP、NL和FL组织,无需后续热处理工艺。与Zhou等[19]的研究结果相比,该轧板尺寸更大,室温塑性达到了1.8%,仅强度略低于Zhou等[19]制备的板材,该轧板对高Nb-TiAl合金轧板具有重要意义。
近年哈尔滨工业大学陈玉勇等采用铸锭冶金轧制,在1300℃ (α + γ两相区)制备出尺寸为500 mm × 400 mm × (2~3) mm的大尺寸高性能Ti-43Al-9V-0.2Y合金板材,轧制完成后对轧板采用普通板材退火工艺,去除包套过程中板材横向与纵向均开裂。分析其开裂的主要原因之一是热处理工艺不当,大尺寸轧板中平面应变较大、平面应力和残余应力过高所致,所以大尺寸TiAl合金板材的退火热处理工艺也是突破大尺寸TiAl合金板材制备的关键。
目前国外铸锭冶金轧制板材已实现常规化生产,已知可生产最大尺寸为1800 mm × 500 mm × 1 mm的薄板。而国内仍受限于实验室之内,已知的制备板材最大尺寸为875 mm × 70 mm × 2.6 mm,厚度在2~3 mm之间,其尺寸距离工程化应用尚有差距。国外轧板力学性能相关信息较少。目前,国内高Nb-TiAl合金轧板的室温和高温强度较高,如北京科技大学梁永峰等[24]制备的Ti-45Al-8.5Nb-0.2W-0.2B-0.03Y合金轧板及哈尔滨工业大学Zhou等[19]制备的Ti-44Al-8Nb-0.2W-0.2B-Y合金轧板室温与高温强度优良,其力学性能如上述。在α + γ两相区采用铸锭冶金法轧制,板材组织多由层片晶团和γ晶粒组成,平均晶粒尺寸较小可达3.5 μm,较大可到30 μm[19,21,23]。通常,TiAl合金板材平均晶粒尺寸越细小,板材力学性能越好。目前,国内铸锭冶金轧制存在的主要问题是受限于传统轧制装置无法实现等温条件下的连续轧制。轧制过程中温降过快,会导致塑性急剧下降,增加了大尺寸TiAl合金板材的轧制难度,同时严重降低了板材力学性能。国内传统铸锭冶金轧制板材的塑性相对不足,较少超过2.0%,与工程应用仍有一定差距。另外,铸锭冶金轧制材料利用率低,加工周期长,成本高。但与其他TiAl合金轧板制备方法相比,铸锭冶金轧制的加工工艺相对成熟,并且轧板的室温与高温强度表现突出,未来实现工业化生产与应用前景巨大。
1.2 粉末冶金轧制
粉末冶金轧制可分为元素粉末法和预合金粉末法。元素粉末法是将Ti、Al元素粉和其他元素粉经过混粉、压实和轧制等加工形成元素粉板坯,然后在高温下反应形成TiAl合金板坯,最后经热等静压或热压烧结制备TiAl合金板材的方法。由于此方法制备板材中O元素与其他杂质元素含量偏高,存在严重孔洞问题,致密度差,导致板材力学性能差[25,26]。预合金粉末法是将制备好的TiAl预合金粉末经过热等静压或热压烧结成板坯,再通过近等温包套轧制为板材的方法,如图8所示。相比于元素粉末法,预合金粉末法所制得的合金板材O元素与其他杂质元素含量相对较低,成分均匀,致密度高,力学性能更胜一筹。因此,目前TiAl合金粉末冶金轧制典型常用方法主要为预合金粉末法,后文提到的粉末冶金轧制也属于预合金粉末法。粉末冶金轧制板材组织均匀,晶粒细小,塑性较好,具有生产大尺寸箔材的优势,未来商业化生产前景广阔。
图8
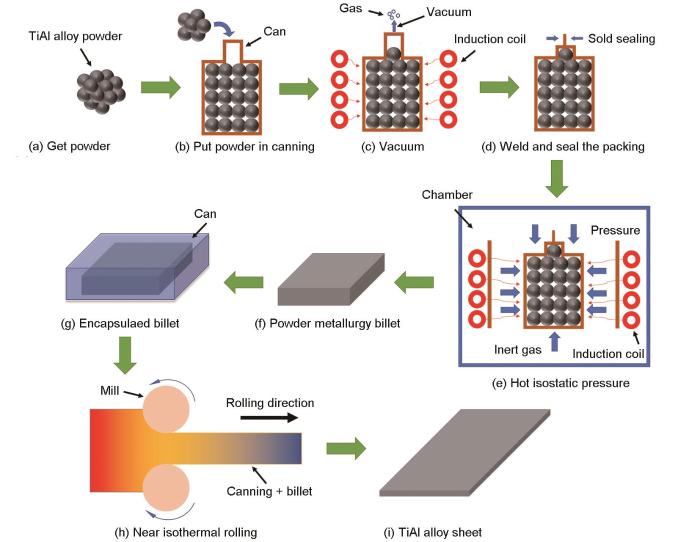
图8 粉末冶金轧制加工路线
Fig.8 Schematics of powder metallurgy (PM) rolling route (a-i)
20世纪,美国BF Goodrich航空结构集团采用粉末冶金轧制,制备出厚度为0.635 mm的Ti-46.5Al-4(Cr, Nb, Ta, B)合金箔材[15]。奥地利Plansee AG公司与德国GKSS研究中心的Clemens团队针对粉末冶金轧制进行了研究,成功生产出大尺寸TiAl合金箔材。20世纪90年代,Clemens团队已轧制出厚度为150 μm的TiAl合金箔材[15]。德国GKSS研究中心已知可制备出尺寸为750 mm × 350 mm × 0.25 mm的Ti-45Al-(5~10)Nb-X(B, C)合金箔材。Clemens团队可制备厚度为75 μm的TiAl合金箔材,这是国际上公开发表的已知最薄TiAl合金箔材,但其具体制备工艺、组织和力学性能等信息未知[5]。
2011年,中国科学院金属研究所采用粉末冶金路线,轧制出尺寸为370 mm × 220 mm × 2 mm的TiAl合金板材(内部编号TLA γ-TiAl)[27],图9[27]为该轧板显微组织和宏观形貌。该轧板室温屈服强度和抗拉强度分别为608和668 MPa,伸长率为2.56%;1000℃高温屈服强度和抗拉强度分别为163和330 MPa,伸长率为32.0%[27]。这是国内较早通过粉末冶金轧制的较宽尺寸TiAl合金板材,其具有良好的焊接成形性,焊缝无缺陷及二次裂纹,焊接区组织与基体差别小,但该合金成分及主要服役温度区间(600~900℃)力学性能信息尚未透露[27]。
图9

图9 粉末冶金轧制γ-TiAl合金板材[27]
Fig.9 γ-TiAl alloy sheet of PM rolling[27]
(a) microstructure (b) appearance
2014年,中南大学Liu等[28]采用粉末冶金轧制,在1280℃轧制出Ti-45Al-7Nb-0.3W合金板材,总变形量最高达到73%,板材组织为双态组织,平均晶粒尺寸为15 μm,如图10[28]所示。该轧板室温抗拉强度为870 MPa (轧制总变形量为63%),这是目前国内通过粉末冶金轧制板材中具有较高室温强度的代表之一。
图10
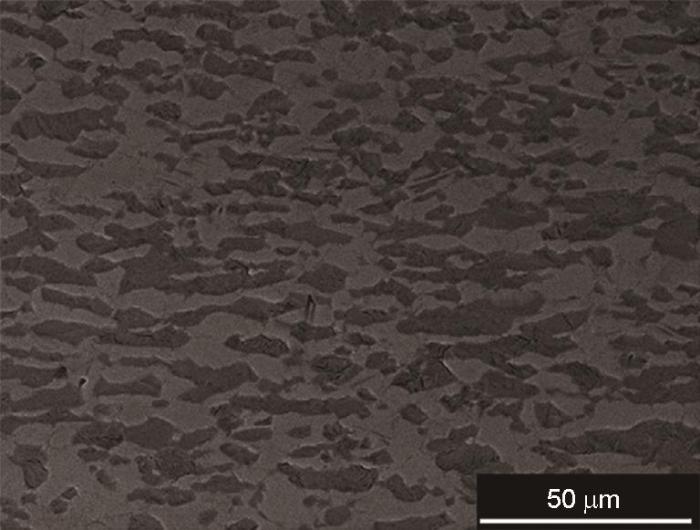
图10 Ti-45Al-7Nb-0.3W合金板材(变形量73%)显微组织[28]
Fig.10 Microstructure of Ti-45Al-7Nb-0.3W alloy sheet (reduction 73%)[28]
2016年,中南大学Li等[29]使用粉末冶金轧制路线,在1270℃轧制出Ti-45Al-7Nb-0.3W合金板材。轧制总变形量为50%,每道次变形量为10%,最终轧板厚度为4 mm。板材组织为双态组织,平均晶粒尺寸为8 μm,如图11[29]所示。该轧板室温屈服强度和抗拉强度分别为582和621 MPa,塑性为2.0%;800℃高温时,板材的屈服强度和抗拉强度分别约为460和650 MPa,塑性为7.2%。该合金室温与高温力学性能良好,但轧板具体尺寸未知。
图11
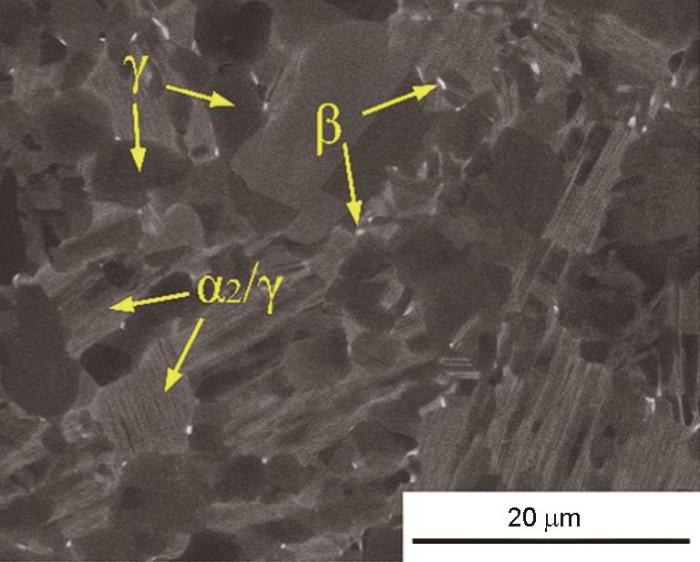
图11 Ti-45Al-7Nb-0.3W合金板材(变形量50%)显微组织[29]
Fig.11 Microstructure of Ti-45Al-7Nb-0.3W alloy sheet (reduction 50%)[29]
2020年,哈尔滨工业大学张冬冬[30]使用Ti-43Al-9V-0.3Y预合金粉末,通过粉末冶金路径,在1200℃轧制出TiAl合金板材,其组织为双态组织,平均晶粒尺寸为12.5 μm,室温屈服强度和抗拉强度分别为541和650 MPa,塑性高达3.0%;800℃高温时,屈服强度和抗拉强度分别为366和371 MPa,塑性为58%。目前国内制备的TiAl合金轧板室温塑性达到3.0%的非常少见。其室温塑性达到3.0%的主要原因之一可能是由于加入Y元素,其与O元素反应形成Y2O3,降低了合金中O含量,同时细化晶粒,从而使室温塑性得到大幅提升。
公开资料表明,欧洲在粉末冶金法轧制工艺方面已处于世界领先地位,可生产最薄厚度为75 μm的大尺寸TiAl合金箔材[5]。国内粉末冶金轧制TiAl合金板材中,力学性能相对较好的轧板为中国科学院金属研究所的γ-TiAl合金板材,其室温和高温拉伸性能如上述[27]。粉末冶金轧制板材组织均匀,晶粒细小,塑性相对较好,更容易轧制薄板或箔材。但是相比于铸锭冶金轧制板材,其强度略低,而且粉末冶金板材O含量容易升高,且预合金粉末制备成本高。然而,铸锭冶金轧制在熔炼TiAl合金时,由于Al元素烧损、偏析等,Al含量不易控制,从而导致后续板材的力学性能不稳定。而通过粉末冶金法制备的TiAl合金中,Al含量易控制,故力学性能稳定。同时,铸锭冶金轧制过程中会切去部分坯料,而粉末冶金由于近净成形,材料利用率远高于铸锭冶金轧制。并且,粉末冶金轧制路线中热等静压理论上可制备无尺寸限制的板材坯料,所以粉末冶金轧制路线使生产超大尺寸TiAl合金薄板成为可能[18]。
1.3 铸锭直接轧制
铸锭直接热轧技术是将多次熔炼的TiAl合金铸锭直接轧制获得板材的方法。相较于铸锭冶金轧制,省去了中间的热等静压和锻造(或挤压)工序。铸锭直接热轧由于加工周期较短,成本较低,引起了科研工作者的广泛关注,但该方法成形难度较大,室温塑性和组织均匀性等有待进一步提高。
1991年,日本Matsuo[31]首次提出铸轧法制备TiAl合金板材。1998年,Hanamura和Hashimeto[32]采用铸轧法制备出TiAl-1%TiB2 (原子分数)板材,轧板组织为双态组织,平均晶粒尺寸为10 μm,室温塑性为2.1%,1100℃高温拉伸强度保持在200 MPa水平。该轧板是国际上首次采用铸轧制备TiAl合金轧板,并且该轧板晶粒细小,力学性能良好。
国内北京科技大学针对铸锭直接热轧TiAl合金板材进行大量研究。2016年,沈正章[33]采用铸锭直接包套热轧技术,制备出尺寸为1000 mm × 70 mm × 2 mm的Ti-45Al-8.5Nb-(Nb, W, B)合金板材,如图12a[33]所示。该板材室温屈服强度和抗拉强度分别为646和691 MPa,塑性为0.5%;800℃屈服强度与抗拉强度分别为529和539 MPa,塑性为0.7%;850℃屈服强度与抗拉强度分别为500和530 MPa,塑性为2.1%。该板材室温与高温强度表现良好,但是室温与高温塑性偏低,与工程应用尚有一定距离。2016年,曾尚武[34]采用铸锭直接包套热轧技术,制备出尺寸为510 mm × 105 mm × 1.40 mm的TNM合金板材(如图12b[34]),实际成分为Ti-44.45Al-3.80Nb-1.01Mo-0.29Si-0.14B。该板材室温屈服强度和抗拉强度分别为348和571 MPa,伸长率为1.78%;800℃高温屈服强度和抗拉强度分别为411和460 MPa,伸长率为16.76%。该合金板材厚度为1.40 mm,是国内轧制TiAl合金板材中较薄的代表,但其室温与高温力学性能偏低。
图12
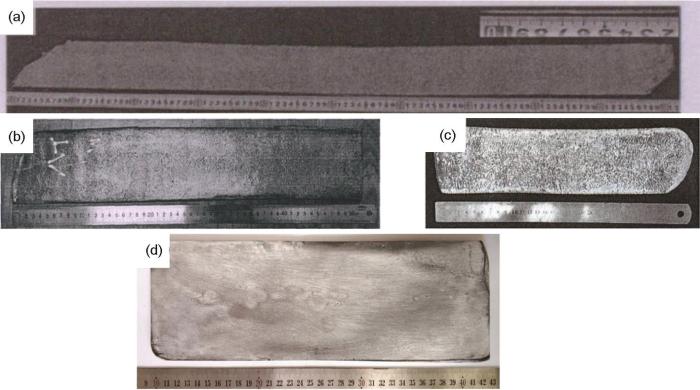
Fig.12 Appearance of direct-rolling TiAl alloy sheets
(a) Ti-45Al-8.5Nb-(Nb, W, B) alloy[33]
(b) Ti-44.45Al-3.80Nb-1.01Mo-0.29Si-0.14B alloy[34]
(c) Ti-45Al-8.5Nb-0.2W-0.2B-0.2Y alloy[35]
(d) Ti-44Al-5Nb-1Mo-2V-0.2B alloy[36]
2021年,陈林[35]采用铸锭软包套直接热轧技术,在1350℃ (α相区)轧制出尺寸为300 mm × 80 mm × 3 mm的Ti-45Al-8.5Nb-0.2W-0.2B-0.2Y合金板材(如图12c[35]所示),其室温抗拉强度达到858 MPa,伸长率为0.26%,800℃高温屈服强度为573 MPa,抗拉强度为744 MPa,伸长率为6.0%。该板材室温与高温强度较高,但室温塑性差。为避免TiAl合金高温轧制过程氧化和温降等问题发生,常采用不锈钢或钛合金作为包套材料,但该实验首次使用石棉(含Zr陶瓷纤维毯,可耐1400℃)作为包套材料,其宏观形貌如图13[35]所示。使用软包套不仅可减少繁琐的传统合金包套工艺,而且避免了轧制时包套合金中的元素扩散到TiAl合金内。该方法拓展了TiAl合金包套材料的选择范围,但软包套散热比合金包套快,且软包套轧制对板材成形能力和表面质量的影响有待进一步研究。
图13
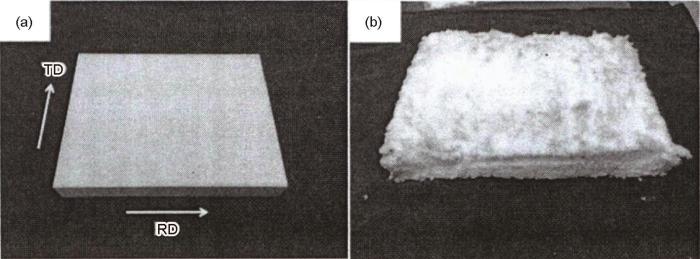
图13 铸锭直接热轧坯料宏观形貌[35]
Fig.13 Appearance of direct-rolling billet[35]
(a) Ti-45Al-8.5Nb-0.2W-0.2B-0.2Y alloy billet (b) billet + soft can
2019年,国内东北大学Li等[36]采用铸锭直接热轧技术,在1200℃ (α + γ两相区)轧制出尺寸为330 mm × 115 mm × 3 mm的Ti-44Al-5Nb-1Mo-2V-0.2B合金板材(如图12d[36]),轧制总变形量为78.8%,轧板组织为双态组织,平均晶粒尺寸为15~20 μm,如图14[36]所示。800℃时合金的抗拉强度为523 MPa,塑性为32%。该板材轧制变形量较大,平均晶粒尺寸细小,但组织均匀性不足,仍存在一定量的粗大残余片层组织,力学性能一般。
图14
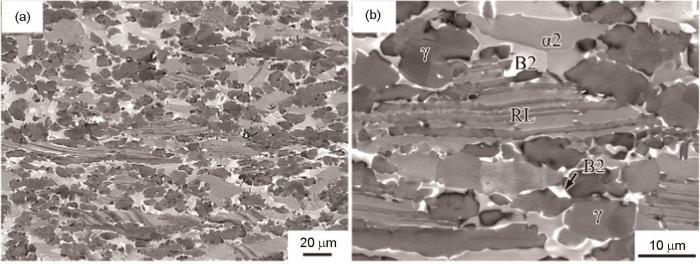
图14 Ti-44Al-5Nb-1Mo-2V-0.2B合金板材显微组织[36]
Fig.14 Microstructures of Ti-44Al-5Nb-1Mo-2V-0.2B alloy sheet with different magnifications (a, b)[36]
国内TiAl合金轧板名义成分、轧制方法、尺寸及力学性能汇总于表1[19,21,23,24,27,29,30,33~36]。目前,国外铸锭直接热轧TiAl合金板材相关信息较少,国内铸锭直接热轧技术制备的TiAl合金板材中,力学性能相对较好的轧板为北京科技大学林均品课题组制备的Ti-45Al-8.5Nb-(Nb, W, B)合金板材,其室温和高温拉伸性能如上述[33]。相对于传统TiAl合金板材轧制方法,目前国内铸锭直接热轧技术制备TiAl合金板材的组织均匀性较差,晶粒尺寸偏大,力学性能偏低,尤其塑性较差。但由于铸锭直接热轧技术省去了中间锻造(或挤压)工序,大幅降低了轧板制备的经济成本和时间成本,经估算铸锭直接热轧技术成本相较于传统的铸锭冶金轧制和粉末冶金轧制降低约35%[5]。因此,如何在保证成本优势的同时制备出力学性能优异的TiAl合金板材将是铸锭直接热轧未来发展的重要方向。
表1 国内TiAl合金轧板名义成分、轧制方法、尺寸及力学性能[19,21,23,24,27,29,30,33~36]
Table 1
Composition | Method | Size / mm3 | Room temperature | 800oC | Institution | ||||
---|---|---|---|---|---|---|---|---|---|
σ0.2 | σb | δ | σ0.2 | σb | δ | ||||
MPa | MPa | % | MPa | MPa | % | ||||
Ti-44Al-8Nb-0.2W-0.2B-Y[19] | IM rolling | 410 × 70 × 2.1 | 962 | 1174 | 1.01 | 681 | 777 | - | HIT |
Ti-43Al-9V-0.2Y[23] | IM rolling | 875 × 70 × 2.6 | 684 | 826 | 1.4 | - | 391 | 67.5 | HIT |
Ti-44Al-5V-1Cr[21] | IM rolling | 300 × 200 × 2.7 | - | 725 | 2.0 | - | - | - | YSU |
Ti-45Al-8.5Nb-0.2W-0.2B- | IM rolling | 600 × 75 × 3 | 911 | 1053 | 1.8 | 556 | 745 | 93.6 | USTB |
0.03Y[24] | |||||||||
TLA γ-TiAl[27] | PM rolling | 370 × 220 × 2 | 608 | 668 | 2.56 | - | - | - | IMR |
Ti-45Al-7Nb-0.3W[29] | PM rolling | Thickness 4 mm | 582 | 621 | 2.0 | 460 | 650 | 7.2 | CSU |
Ti-43Al-9V-0.3Y[30] | PM rolling | - | 541 | 650 | 3.0 | 371 | 366 | 58 | HIT |
Ti-45Al-8.5Nb-(Nb, W, B)[33] | Direct-rolling | 350 × 90 × 3.5 | 646 | 691 | 0.5 | 529 | 539 | 0.7 | USTB |
Ti-44.45Al-3.80Nb-1.01Mo- | Direct-rolling | 510 × 105 × 1.4 | 348 | 571 | 1.78 | 411 | 460 | 16.76 | USTB |
0.29Si-0.14B[34] | |||||||||
Ti-45Al-8.5Nb-0.2W-0.2B- | Direct-rolling | 300 × 80 × 3 | - | 858 | 0.26 | 573 | 744 | 6.0 | USTB |
0.2Y[35] | |||||||||
Ti-44Al-5Nb-1Mo-2V-0.2B[36] | Direct-rolling | 330 × 115 × 3 | - | - | - | - | 553 | 32 | NEU |
1.4 叠轧法
叠轧法是将板材或箔材叠放为多层状结构,通过热压烧结、轧制和热处理等部分或全部工序制备TiAl合金板材的方法,主要包括元素箔叠轧法、预合金箔叠轧法。元素箔叠轧法是以纯Ti箔和Al箔为原材料,交替叠放为多层状结构,再通过上述热压烧结、轧制和热处理等部分或全部工序制备TiAl合金板材的方法。与粉末冶金法相比,元素箔叠轧法避免了O元素和其他杂质元素的混入。预合金箔叠轧法则是将TiAl合金箔材与其他合金箔材叠放为多层状结构,再通过热压烧结成板坯,最后轧制出TiAl基复合材料板材的方法。图15为叠轧法制备γ-TiAl合金板材工艺流程。该方法绕开了对塑性低、热变形抗力大的TiAl合金板坯直接轧制,有望成功解决TiAl合金箔材和薄板的成形问题,但目前阶段该方法制备轧板多存在Kirkendall孔洞问题,力学性能不佳。
图15
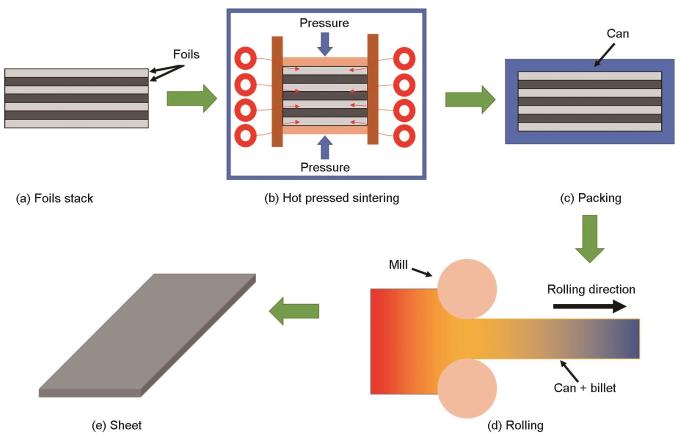
图15 叠轧法加工路线
Fig.15 Schematics of roll bonding route (a-e)
美国Alabama大学Luo等[37]和Zhang等[38]对叠轧法制备TiAl板材进行大量研究。2010年,Chaudhari和Acoff[39]以厚度为82 μm的Ti箔和77 μm的Al箔为原料,首先经累积叠轧焊法制备板坯,再将板坯进行热处理,反应生成TiAl基合金,最后将尺寸为40 mm × 30 mm的板坯进行包套热轧(包套材料为纯Ti),轧制温度为1300℃,轧制总变形量为45%。该轧板组织为近全片层组织,板材中存在较多孔洞,室温抗拉强度不到325 MPa,塑性为0.9%;600℃高温时抗拉强度不到300 MPa,塑性为1.3%。与其他制备方法相比,该轧板省去了昂贵的热等静压工艺,但力学性能较差。
国内哈尔滨工业大学针对叠轧法制备TiAl基复合材料进行了大量研究。2009年,孔凡涛和陈玉勇[40]将Ti-43Al-9V-0.3Y合金板材与Ti-6Al-4V合金板材叠放后进行包套,然后高温轧制出厚度为3 mm的Ti-43Al-9V-0.3Y/Ti-6Al-4V复合板材,轧制温度为1150℃,轧制总变形量为80%,轧板宏观形貌如图16[40]所示。其中Ti-6Al-4V侧为魏氏组织,Ti-43Al-9V-0.3Y侧相组成包括α、γ和B2相,界面处结合良好,界面层厚度约为40 μm。复合轧板室温强度和延伸率分别超过800 MPa和4%。
图16
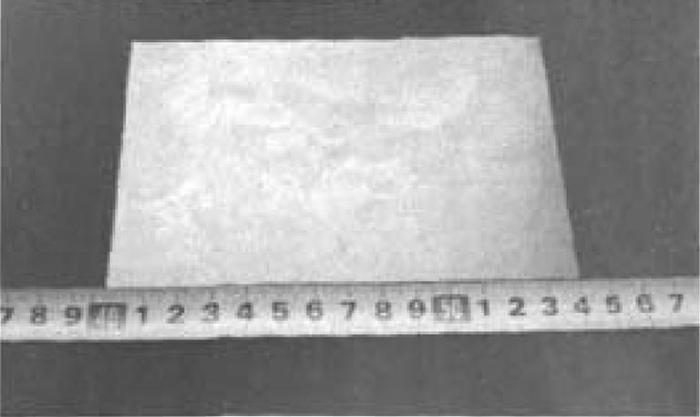
图16 Ti-43Al-9V-0.3Y/Ti-6Al-4V复合板材宏观形貌[40]
Fig.16 Appearance of Ti-43Al-9V-0.3Y/Ti-6Al-4V composite sheet[40]
2010年边卓伟[41]以TiB2颗粒增强铝基复合材料(B4C/Al)板材和纯Ti板材为原料,板材交替叠放,先采用热压烧结反应制备出板坯,再通过轧制成形工艺制备出Ti-B4Cp/Al复合材料板材。2011年,王银[42]将TiB2/Al与Ti箔交替叠放,采用与文献[41]同样工艺制备出TiAl基复合材料板材。该合金板材在700和800℃高温时抗拉强度分别为248和223 MPa。2012年,崔喜平[17]使用与文献[42]同样原材料和工艺制备出微叠层TiB2-TiAl复合材料板材,其显微组织为全片层组织和等轴状α2-Ti3Al组织,α2/γ层片晶团尺寸为300~600 μm,片层间距为0.9~3 μm,等轴α2晶粒尺寸为50~150 μm。其中,2.6%TiB2 (体积分数)-TiAl复合材料的室温屈服强度和抗拉强度分别为179和251 MPa,塑性为2.27%。该合金板材组织粗大,室温强度较低。这些通过元素箔叠轧法制备的TiAl基复合板材组织粗大,力学性能差。
叠轧法制备板材由于在界面处存在原子扩散效应,会形成大量Kirkendall孔洞,导致力学性能不足。而2018年,Sun等[43]使用尺寸为100? mm × 65? mm × 2.2? mm高Nb-TiAl合金板材与同样尺寸的Ti-6Al-4V合金板材为原料,通过叠层热压轧制,制备出尺寸为195 mm × 75 mm × 2.6 mm的钛合金-TiAl合金叠层复合材料板材,轧制总变形量为85%,在界面处未发现孔洞,如图17[43]所示。该材料界面层厚度约为260 μm (如图17b[43]所示)。界面由4种组织区组成,从Ti-6Al-4V侧向高Nb-TiAl侧组织区分别为针状α2、O-Ti2AlNb和β/B2相区;片状α2相区;针状α2和β/B2相区;针状γ相、等轴α2相和β/B2相区,如图17c和d[43]所示。在高Nb-TiAl合金与Ti-6Al-4V合金的界面处没有孔洞或裂纹,避免了Kirkendall孔洞在界面层中出现,如图17b和c[43]所示。该叠轧板材无孔洞主要是由于轧制时的高温和大变形使Kirkendall孔洞闭合所致。
图17
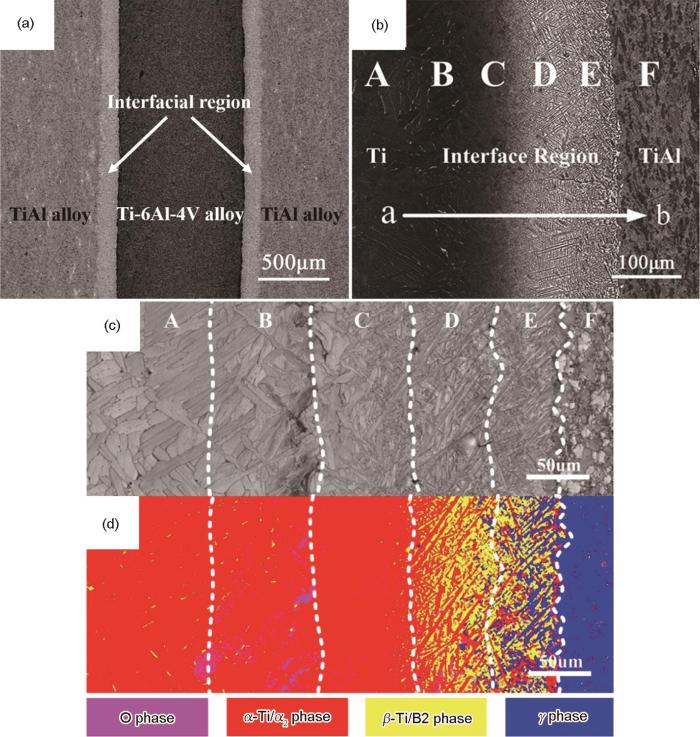
图17 Ti-6Al-4V/高Nb-TiAl叠层复合材料轧板显微组织[43]
Fig.17 Microstructures of Ti-6Al-4V/high Nb-TiAl laminate composite material[43]
(a) low magnification (b) low magnification micrograph of interface region
(c) high magnification micrograph of interfacial region
(d) schematic of phase distribution in interfacial region
由于Ti箔与Al箔塑性变形相对容易,所以叠轧法使TiAl合金板材制备难度降低。与铸锭冶金轧制和粉末冶金轧制相比,叠轧法可选择不使用成本高的热等静压。但叠轧法工艺难度较大,TiAl合金轧板致密度不足,力学性能有待提升,离实际应用尚有一段距离。
另外,宝钛集团发明了一种钢板包覆叠轧制备钛合金薄板的方法。此方法是将多层较薄钛合金板材喷涂上隔离剂,然后交替叠放,采用近等温包套轧制,以此制备出钛合金箔材的方法[44]。未来可尝试利用该方法制备TiAl合金薄板,突破国内大尺寸TiAl合金薄板的制备瓶颈。
2 总结和展望
大尺寸高性能TiAl合金板材或箔材是航空航天领域重要的轻质高温结构材料。目前,国内TiAl合金板材轧制研究发展迅猛,板材力学性能表现良好,在室温和高温下,屈服强度与抗拉强度表现突出,但室温塑性仍有待提高。国内高性能TiAl合金板材的尺寸和厚度与国外相比仍有较大差距,与工程化应用尚有一定距离。对此,提出几点关于轧制大尺寸TiAl合金板材的建议:(1) 降低TiAl合金中N、O含量,提高合金的室温塑性;(2) 对现有近等温轧制装置进行改造,实现轧制工艺参数的精准控制,保证近等温轧制条件,避免合金的起皱、开裂及力学性能降低等问题;(3) 优化轧制温度、变形量、速率等工艺参数,使合金处于合适的热加工区间,获得组织均匀、晶粒细小、力学性能优异的轧板,同时保证其协调变形,避免轧制过程中起皱、开裂;(4) 优化大尺寸高性能TiAl合金板材的退火热处理工艺,避免因残余应力过高导致弯曲、开裂等问题。
同时针对未来TiAl合金板材的服役环境,可通过建立和完善TiAl合金板材力学性能数据库,完善TiAl合金焊接方法及接头组织性能调控,以此加快TiAl合金板材商业化应用的步伐。
来源--金属学报