分享:CrMoTi中熵合金的性能及其原位合金化增材制造
1.
2.
3.
4.
以新型模具材料为应用背景,首先从多主元合金设计的角度,预测了CrMoTi中熵合金成分,并在实验中验证了其单相bcc结构。对CrMoTi中熵合金的硬度和热学性能进行了测试。结果表明,电弧熔炼样品在室温下硬度为520.6 HV0.3,在600℃时硬度为356.0 HV0.3;在室温下比热容为371 J/(kg·K),热导率为14.0 W/(m·K)。随后以金属元素粉为原材料,对比研究了直接激光沉积(DLD)和选区激光熔化(SLM) 2种增材制造技术在原位合金化成型CrMoTi中熵合金的加工适性。其中DLD样品在打印态密度最高达7.46 g/cm3,硬度达到634.6 HV0.3。SLM的原位合金化加工适性相对较差,样品密度最高为7.27 g/cm3,硬度为605.9 HV0.3,且在其内部残留有未熔Mo粉。相比较而言,在作为模具的性能方面,CrMoTi合金表现出略优于H13钢的硬度和高温热导率。在原位合金化方面,CrMoTi合金的原料包含了熔沸点差异较大的金属元素,且形成相为硬脆bcc结构相,对增材制造技术而言有较大的加工难度,而DLD技术相对SLM表现出更好的原位合金化加工适性。
关键词:
高熵合金/多组元合金的概念自提出以来[1~3],过去十余年间其研究获得了蓬勃发展。对多主元合金的研究主要集中在四元及以上的高熵合金领域[4,5]。三元中熵合金组分相对简单,可根据潜在应用需求进行合金开发,也获得了相当程度的关注。热作模具作为制造业的重要组成部分,通常要求模具材料具有高耐磨性、高硬度、耐蚀性以及高温性能等。中熵、高熵合金具有天然的高温稳定性,具有单相bcc结构的中熵合金,有望满足该类模具性能需求,尤其考虑到Cr和Mo为热作模具钢中的常见元素,可基于其进行中熵合金的设计开发进而制备成型。
近年来增材制造/3D打印技术在金属模具制造方面已经有了广泛应用,其可大幅提高小批量、定制化模具的生产效率,并可实现独特的随形水冷功能[6]。直接激光沉积(direct laser deposition,DLD)和选区激光熔化(selective laser melting,SLM)作为代表性的金属增材制造技术,已经在包括Inconel 625超合金、316L不锈钢和AlSi10Mg等合金上有优异的成型表现[7]。就多主元合金的增材制造而言,目前研究更多集中于以FeNiCrCo为基础的fcc体系[8]。bcc体系多主元合金的研究相对较少。如Li等[9]和Brif等[10]的研究表明,使用预合金粉的fcc结构FeNiCrCo高熵合金在SLM技术下具有良好的加工适性。与使用预合金粉末相比,使用元素粉体,通过原位合金化,有助于缩短加工周期与降低成本,可进一步提高增材制造的生产效率。Joseph等[11]的研究证明,采用元素粉为原料并结合DLD技术,可以实现Al x CoCrFeNi双相高熵合金的原位合金化。目前,当体系中包含高熔点元素且组元间熔沸点差异较大时,增材制造原位合金化的可行性仍需论证,相关研究尚少[12]。
本工作以多主元合金的概念及相关判据为出发点,以模具材料为应用背景,选取了热作模具钢中常见的Cr和Mo元素,并引入相对原子质量较低且原子半径较大的Ti元素,以降低合金密度并增加晶格畸变,提高相应中熵合金的力学性能。首先进行中熵合金成分预测,然后进行实验验证,最终开发出了CrMoTi中熵合金,并表征了该合金的热学及力学性能。以此为基础,对比了电弧熔炼及DLD和SLM 2种激光增材制造技术下CrMoTi中熵合金的原位合金化加工适性。本工作可以为类似包含高熔点元素的中熵合金体系的原位合金化增材制造提供参考。
1 CrMoTi合金的相形成理论计算
选取Cr、Mo、Ti 3种元素来形成中熵合金,其物理性质列于表1[13]。根据Yang等[14]总结多主元合金研究时提出的Ω-δ (Ω为合金相稳定的判定参数,δ为组元原子半径差的均方差)判据,对其形成单一固溶体相的能力进行理论计算。其中Ω参数综合了合金的熔点(Tm)、混合熵(ΔSmix)与混合焓(ΔHmix)。其表达式如下:
表1 Cr、Mo和Ti元素的物理性质[13]
Table 1
Element | Ar | Tm / K | Tb / K | r / nm | VEC | κ / (W·m-1·K-1) |
---|---|---|---|---|---|---|
Cr | 51.99 | 2180 | 2945 | 0.128 | 6 | 93.9 |
Mo | 95.95 | 2896 | 4912 | 0.139 | 6 | 138.0 |
Ti | 47.87 | 1941 | 3560 | 0.147 | 4 | 21.9 |
式中,Tm根据混合规则(the rule of mixtures)[15],通过下式获得:
式中,ci 为对应组元i在体系中的原子浓度。在等原子比条件下,ΔSmix的表达式为:
式中,R为摩尔气体常数,R = 8.3144 J/(mol?K);N为合金中的主元素数。基于双相体系的混合焓,多主元合金中的ΔHmix由下式获得:
式中,cj 为对应组元j在体系中的原子浓度,
式中,ri 和rj 分别为组元i和j的原子半径。当Ω ≥ 1.1且δ ≤ 6.6%时,合金体系偏向于形成单相固溶体。根据表1[13]给出的物理性质,由
当7.5 < VEC < 9.5时,倾向于形成单相fcc结构;当4.3 < VEC < 5.7时,倾向于形成单相bcc结构[19]。由
2 实验方法
以商业纯度≥ 99.9% (质量分数)的Cr、Mo和Ti元素颗粒为电弧熔炼原材料。通过WK-II型真空电弧炉熔炼中熵合金,熔炼锭经过6次重熔以促进元素均匀化。增材制造用近球形Cr、Mo和Ti元素粉体的C、N、O和H含量及粒径分布如表2所示。原始粉体经过Retsch AS 200 Basic 振动筛分仪进行筛分后,粗粉与细粉分别用于DLD和SLM增材制造技术。其中Cr与Ti粉体由75 μm筛网进行筛分,Mo粉体由53 μm筛网进行筛分。元素粉以等原子比配置后,使用Turbula三维混合机以49 r/min转速混合30 min进行均匀化。在开始打印前,粉体在真空干燥箱中60℃下烘干24 h去除水分。
表2 增材制造原料粉体的C、N、O、H含量和粒径分布
Table 2
Powder | Mass fraction of element / % | d / µm | |||
---|---|---|---|---|---|
C | N | O | H | ||
Cr | 0.0027 | 0.0912 | 0.0366 | - | 40-150 |
Mo | 0.0027 | 0.0200 | 0.1390 | - | 30-100 |
Ti | 0.0050 | 0.0080 | 0.0687 | 0.0031 | 40-150 |
研究所使用的自搭建DLD设备配备光斑直径为2 mm的3000 W大功率光纤激光器,同时配备保护气体输送管道。打印于室温下进行,基板为经过喷砂处理的钛板。保护气体为Ar气,与粉体同时输出。激光功率范围850~1550 W,扫描速率3 mm/s,送粉率8 g/min,气流量6 L/min,Z轴层厚0.5 mm。
SLM设备为SLM Solution 125HL 打印机。该设备配备了光斑直径约为64 μm的400 W光纤激光器。钛基板在打印仓中预热温度为200℃。腔体在打印开始前充Ar气洗气至O2含量低于0.1% (质量分数)。原位合金化实验中激光功率(P)为240~320 W,扫描速率(v)为400~800 mm/s,搭接间距(h)为0.08~0.1 mm,层厚(t)固定为0.04 mm。
块体试样的密度(ρ)通过Archimedes排水法测得。打印样品的微观缺陷通过Diondo D2 CT系统进行分析。组织分析样品在金相砂纸打磨至800号后,分别用3和1 μm金刚石抛光液进行抛光。采用SmartLab 9kW X射线衍射仪(XRD,CuKα,波长λ = 0.154 nm)对块体样品的物相进行分析。使用配备了能谱仪(EDS)与电子背散射衍射(EBSD)探头的Merlin Gemini2扫描电子显微镜(SEM)对样品的元素分布以及微观组织进行分析和观察。采用Archimedes HTV-PHS30高温硬度计在抛光的样品表面上进行25℃至高温区间((600 ± 10)℃) Vickers硬度测量,加载压力为2.942 N,加载时间为15 s。采用TA DLF1600激光闪光导热仪测量样品的热学性能,温度测试区间28~709℃。
3 实验结果
3.1 混合元素粉体的表征
图1为DLD实验中使用的混合元素粉末的SEM-EDS像。可见,粉末主要呈球形且卫星粉极少出现,有利于在加工过程中保持良好的流动性。元素分布结果显示经过混粉后3种元素粉实现了初步的均匀化。图2为混合粉体的XRD谱。Cr、Mo和Ti 3种元素的峰均在图谱中呈现。
图1
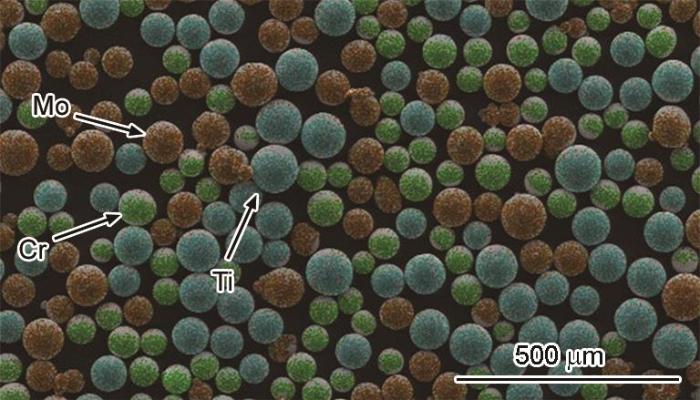
图1 直接激光沉积(DLD)使用的混合元素粉末的SEM-EDS像
Fig.1 SEM-EDS image of the blended elemental powder used for direct laser deposition (DLD)
图2
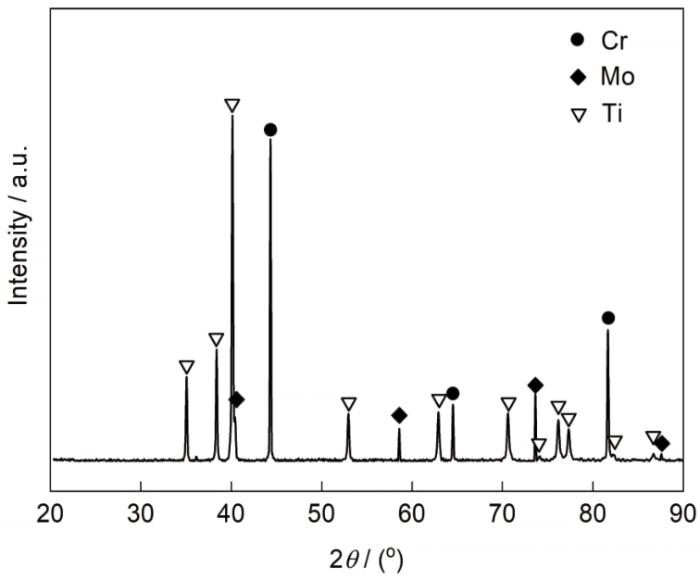
图2 DLD混合粉末的XRD谱
Fig.2 XRD spectrum of the blended powder used for DLD
3.2 电弧熔炼CrMoTi中熵合金的微观组织与性能
图3给出了电弧熔炼、DLD和SLM 3种制备工艺制得CrMoTi中熵合金的XRD谱。结果显示全部样品均为单相bcc结构。图4为电弧熔炼样品的EBSD像,其平均晶粒尺寸约为192 μm。
图3
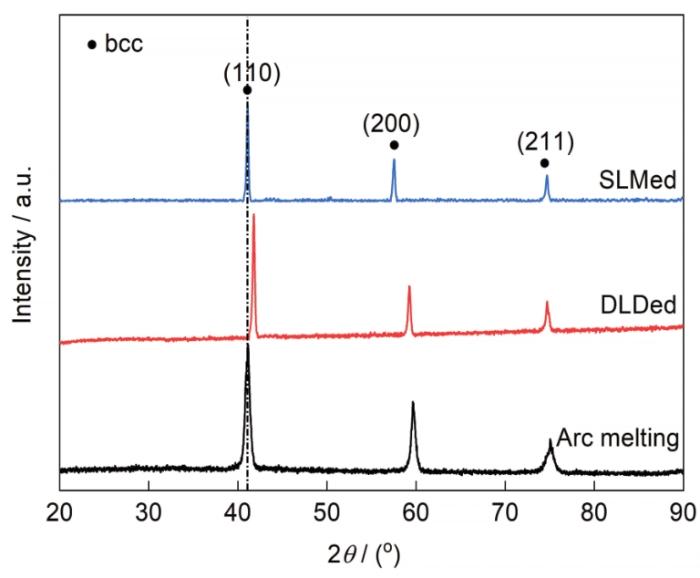
图3 通过电弧熔炼、DLD和选区激光熔化(SLM)成型的CrMoTi中熵合金XRD谱
Fig.3 XRD spectra of CrMoTi medium-entropy alloys (MEA) fabricated by arc melting, DLD, and selective laser melting (SLM) techniques
图4
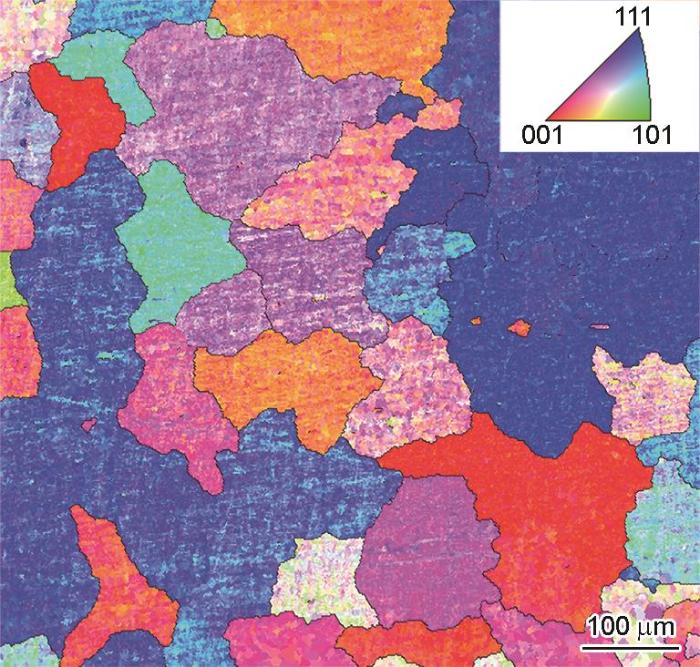
图4 电弧熔炼制备CrMoTi中熵合金的EBSD像
Fig.4 EBSD image of CrMoTi MEA fabricated by arc melting
对电弧熔炼样品显微硬度及热学性能进行了测试。图5为不同温度下显微硬度测试结果。其中25℃时CrMoTi合金的Vickers硬度为520.6 HV0.3,随温度升高,Vickers硬度逐渐减小,600℃时Vickers硬度为356.0 HV0.3。不同温度下比热容(cp )与热导率(κ)测试结果绘制于图6中。其中100、300和500℃对应的热学性能为拟合数据,用以参考对比。28℃时,CrMoTi合金的cp 为371 J/(kg·K),κ为14.0 W/(m·K)。随温度升高,cp 和κ增大。709℃时cp 和κ分别为446 J/(kg·K)和28.4 W/(m·K)。
图5
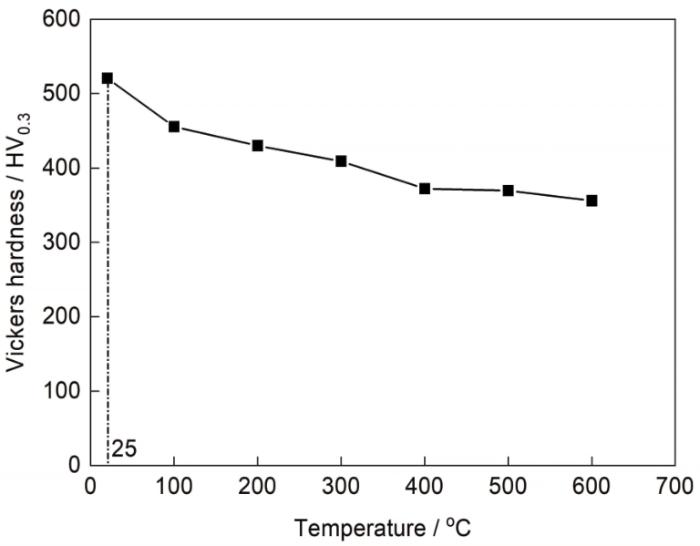
图5 不同温度下电弧熔炼CrMoTi中熵合金的Vickers硬度
Fig.5 Vickers hardnesses of CrMoTi MEA fabricated by arc melting, tested from 25oC to 600oC
图6
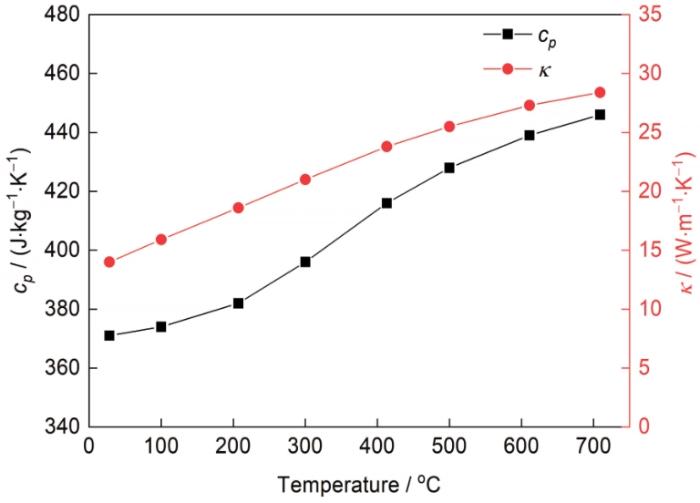
图6 不同温度下CrMoTi中熵合金的比热容(cp )与热导率(κ)
Fig.6 Thermal capacity (cp ) and κ results of CrMoTi MEA tested from 28oC to 709oC (Data at 100, 300, and 500oC were obtained from regression treatment)
3.3 增材制造CrMoTi中熵合金
3.3.1 打印态样品致密度及成型适性
图3表明,2种增材制造原位合金化样品中没有明显来自元素粉末的峰出现,打印态样品为bcc结构单相,表明在DLD及SLM增材制造过程中,可以实现近等原子比中熵合金的原位合金化,且没有明显的单质元素粉末残留。
图7a1和a2分别为DLD加工成型的CrMoTi薄壁样品的俯视图和侧视图。其无明显裂纹且与钛基板紧密结合,同时其表面具有金属光泽无明显氧化现象。图7b1和b2分别为SLM打印的圆片样品的俯视图和侧视图。与DLD样品相对比,在所选用的打印工艺参数范围内,出现较多的边缘翘曲导致打印大部分无法完成,且打印完成试样的侧面可观察到不同程度的宏观裂纹。通过SEM观察SLM打印样品的截面,有大量的毫米级别裂纹,如图8所示。部分裂纹由表面深入基体。初步分析,该中熵合金粉体的SLM原位合金化加工适性较差,难以成型致密块体。
图7
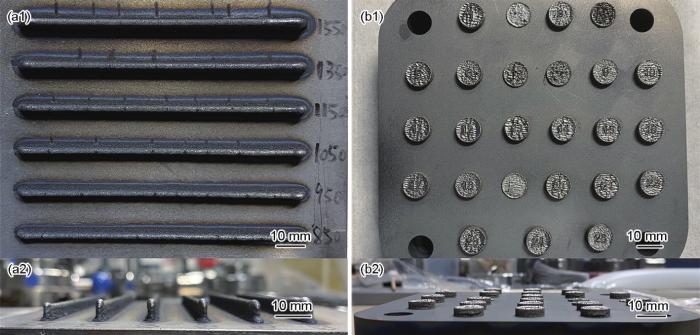
图7 增材制造原位合金化CrMoTi中熵合金成型效果
Fig.7 Top-views (a1, b1) and side-views (a2, b2) of CrMoTi MEA fabricated by DLD (a1, a2) and SLM (b1, b2) in situ alloying
图8

图8 SLM加工CrMoTi中熵合金试样截面形貌的SEM像
Fig.8 Cross-section SEM image of SLMed CrMoTi MEA
图9为DLD加工CrMoTi合金样品的密度与功率曲线。可见,随着激光功率的上升,沉积样品的密度由功率850 W时的6.95 g/cm3增加至1150 W时的7.41 g/cm3,并在功率1350 W时达到最高的7.47 g/cm3并随后趋于稳定。最高密度样品记为DLD1350W。图10为SLM打印件密度与体能量密度曲线。其中体能量密度(VED)由VED = P / (vht)计算[20]。可见,样品的密度总体呈现出随体能量密度的增加而提高的趋势。其中最高密度为7.27 g/cm3,对应的体能量密度为166.67 J/mm3 (P = 320 W,v = 800 mm/s,h = 0.06 mm)。该样品记为SLM167J。从图9还可以看出,采用DLD原位合金化的CrMoTi样品密度在激光功率大于1150 W时超过了电弧熔炼样品。由于Cr、Mo、Ti 3种元素熔沸点差异较大且原料为单质元素,在加工中随热输入增大将伴随不同程度的元素烧损,从而影响完成试样的真实密度。关于原位合金化烧损带来的影响将在后文讨论。
图9
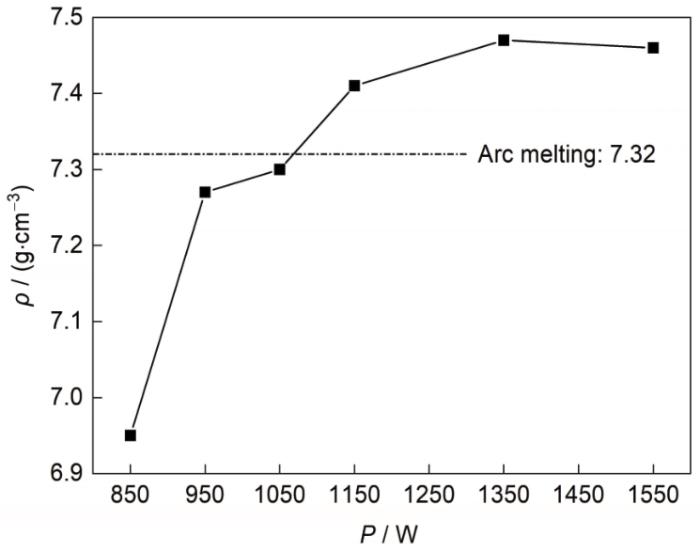
图9 DLD原位合金化CrMoTi中熵合金的密度-激光功率(ρ-P)曲线
Fig.9 Density-laser power (ρ-P) curve of CrMoTi MEA fabricated by DLD in situ alloying
图10
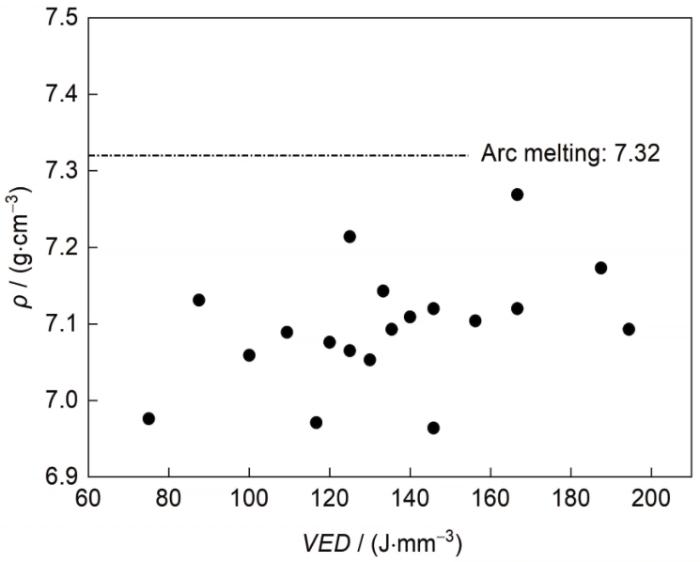
图10 SLM原位合金化CrMoTi中熵合金的密度-体能量密度(ρ-VED)曲线
Fig.10 Density-volumetric energy density (ρ-VED) curve of CrMoTi MEA fabricated by SLM in situ alloying
3.3.2 打印态样品的微观组织
从图3可见,2种增材制造技术下所成型CrMoTi样品的主体结构为单相bcc结构固溶体。图11为增材制造原位合金化DLD1350W和SLM167J样品的SEM像和EDS分析,表明2种技术下均可发生不同程度的组分元素富集。其中DLD样品中可发现残留Ti元素,示于图11a。在图11b所示的SLM样品中存在明亮半球形区域,EDS面扫结果表明此区域为Mo元素的富集,结合形貌像可知其为部分熔化的Mo粉颗粒。类似的不完全熔化或未熔Mo粉在SLM样品中有较多残留。表3为CrMoTi中熵合金的名义成分和由EDS测得电弧熔炼和2种增材制造技术成型样品中的成分。分析表明,电弧熔炼制备的样品最接近等原子比。DLD原位合金化样品中的Cr含量低于名义含量。而在SLM成型的样品中,由于Mo粉固溶程度较差,导致EDS测试结果中基体的Mo含量明显偏低。相比较而言,DLD技术打印的样品中,元素溶解及均匀化程度优于SLM技术制备的样品。在后文将结合元素性质与2种增材工艺的特点综合讨论。
图11

图11 增材制造原位合金化DLD1350W和SLM167J样品的SEM像和EDS分析
Fig.11 SEM image and corresponding EDS results of samples DLD1350W (a) and SLM167J (b) (DLD1350W denotes the DLDed sample fabricated using P = 1350 W; SLM167J denotes the SLMed sample fabricated with VED = 167 J/mm3)
表3 CrMoTi中熵合金的名义成分和电弧熔炼及增材制造成型CrMoTi中熵合金的主元素含量 (atomic fraction / %)
Table 3
Sample | Cr | Mo | Ti |
---|---|---|---|
Nominal | 33.3 | 33.3 | 33.3 |
Arc melting | 31.2 | 32.8 | 36.0 |
DLD1350W | 25.5 | 38.6 | 35.9 |
SLM167J | 36.9 | 23.4 | 39.7 |
4 分析讨论
4.1 CrMoTi与热作模具钢的性能对比
在高熵合金/多主元合金概念兴起前,Kubo等[21]研究过包含CrMoTi在内的bcc结构合金体系及其作为储氢材料的可能性。但总体而言,之前对于CrMoTi中熵合金的性能了解有限。本工作针对热作模具材料中重要的硬度和热学性能,对该合金进行了更深入的研究。常用的H13热作模具钢的硬度通常在458~613 HV区间[22],在600℃时H13钢硬度降低至200~300 HV区间[23]。电弧熔炼制备CrMoTi中熵合金不同温度下硬度列于表4。可见,室温下其硬度与H13模具钢相近,而在600℃下硬度优于H13模具钢。研究[24]表明,因为高熵/中熵合金的独特单相组织结构在高温下较为稳定,bcc结构的高熵合金在600~1000℃高温下仍然可以保持优异的力学性能。本工作CrMoTi合金的硬度有利于在高温下作为模具应用。
表4 电弧熔炼CrMoTi中熵合金的硬度和热学性能
Table 4
T | Hardness | κ | cp | a |
---|---|---|---|---|
oC | HV0.3 | (W·m-1·K-1) | (J·kg-1·K-1) | (10-6 m2·s-1) |
RT* | 520.6 | 14.0 | 371 | 5.26 |
100 | 455.6 | 15.9 | 374 | 5.91 |
207 | 430.0 | 18.5 | 382 | 6.78 |
300 | 409.2 | 21.0 | 396 | 7.37 |
413 | 372.3 | 23.8 | 416 | 7.93 |
500 | 369.6 | 25.5 | 428 | 8.28 |
611 | 356.0 | 27.3 | 439 | 8.63 |
709 | - | 28.4 | 446 | 8.84 |
电弧熔炼CrMoTi中熵合金热学性能也列于表4,表中κ、cp 与热扩散系数(a)间的换算关系为a = κ / (ρcp )。其中100、300和500℃对应数据为拟合数据,用以参考对比。可见,一方面,合金室温下热导率均低于其3种纯金属组成元素(表1)。另一方面,合金的热导率呈现出随温度升高而增加的趋势,在700℃时达到28.3 W/(m·K)。相比较而言,在28~700℃范围内,H13钢的热导率基本稳定在25 W/(m·K)[25]。实际生产时,高热导率材料有利于提高模具整体的散热性,减少模具成型产品的加工周期。尽管CrMoTi中熵合金在较低温度下热导率较低,但随使用温度的升高,其热导率可达到甚至高于H13钢的热导率,有利于作为高温模具材料的应用。在纯金属中,热导率通常呈现为随温度升高而降低的趋势。而在多主元合金中,由于晶格畸变效应会对声子浓度产生影响,使得合金的热学性质更接近为准金属范畴[26]。
对CrMoTi合金的初步探究显示出其具备一定的模具应用潜力,然而作为实验材料体系其成本尚无法与成熟模具钢种相提并论,不过基于三元中熵合金,可在未来进一步的合金开发中引入更多组元(如Al),以期实现性能优化和成本调控的多重目标。
4.2 2种增材制造技术对于CrMoTi中熵合金的加工适性
本工作另一目的是探究当成分中包含较高含量(如33%,原子分数)难熔元素(如Mo)时的激光原位合金化增材制造的可行性。原位合金化增材制造技术有助于节约生产预合金粉体需要的时间和降低成本,进一步提高其在制备小批量、定制化产品中的生产效率、灵活性和竞争力。
上述研究表明,在激光功率大于1150 W时,DLD原位合金化的CrMoTi合金样品密度超过了电弧熔炼样品。由于Cr、Mo和Ti 3种元素熔沸点差异较大且原料为单质元素粉末,其中Cr的沸点仅略高于Mo的熔点,在加工中随热输入增大出现不同程度的元素烧损。同时Cr原子量较小,且在DLD样品中含量较低,因此制备试样的真实密度也受到成分变化的影响而偏大。因此采用了CT技术进一步表征增材制造样品的致密化。
图12展示了2种增材制造产品的CT扫描结果以直观地反映样品中的缺陷形貌及分布。图12a所示DLD产品的孔隙率为1.01%,相对致密度为98.99%,缺陷主要体现为密集分布的近球形孔隙。在高能激光增材制造样品中,部分金属元素的气化以及制粉过程中粉体内部残留的气体,均会导致类似球形的小尺寸气孔形成。在图12b所示的SLM样品CT结果中,孔隙率为1.05%,与DLD样品接近,但其形貌呈现为层片状裂隙。此结果与打印态下所能观察到的大量宏观开裂行为相符合。SLM技术所采用的激光光斑远小于DLD,因此其在加工过程中所形成的熔池更小、冷却速率更高,更容易造成热应力及热变形。可见,采用混合元素粉为原料的激光原位合金化过程中,SLM可成型性低于DLD技术。这与硬脆bcc结构高熵合金AlCrCoFeNi研究结果[27]类似。
图12
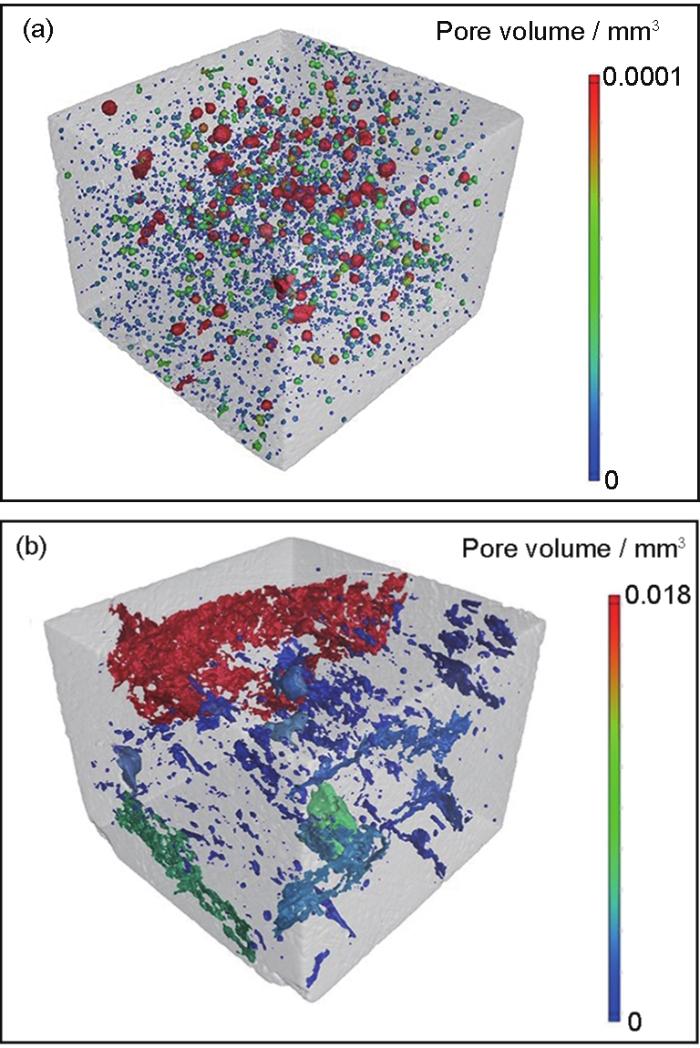
图12 增材制造块体的CT分析结果
Fig.12 CT results of samples DLD1350W (a) and SLM167J (b)
DLD和SLM已经被证实可以实现包括bcc结构的AlFeNiCrCo、fcc结构的CrCoFeMnNi等高熵合金的原位合金化,且合金元素在激光熔池中也可以被充分混合[11,28]。本工作结果进一步证明,尽管增材制造技术可实现CrMoTi中熵合金由元素粉体到块体的原位合金化成型,在打印态材料中的元素分布以及成分均匀性尚难以达到特别理想的均匀化和等原子比。在2种工艺中所观察到的组织特征与工艺自身的特质和合金元素性质都有关系。
在DLD试样中,Mo作为3种合金元素中熔点最高的元素,没有明显的未熔粉末残留。说明DLD加工过程实现了高熔点Mo粉的充分熔化,但相应的高激光能量输入也会导致最终打印态试样内低沸点的Cr元素出现损耗,其含量低于设计成分。由于元素间原子半径相差较大,不同工艺间样品的XRD谱也出现偏移(图3)。在DLD试样中还观察到了未固溶Ti (图11a)。图13a中的DLD样品微观组织的SEM像显示,未固溶Ti主要存在于枝晶间区域。EDS线扫结果(图13b)表明了枝晶偏析现象的存在。熔点最高的Mo元素主要分布于枝晶内部,而熔点较低的Cr与Ti则倾向于聚集至枝晶间,且在合金固溶体互溶反应中,相较于Cr-Mo体系,Ti-Mo与Ti-Cr的互溶较弱[29],因此凝固结束后Ti易在枝晶间析出。另一方面,SLM样品中的EDS成分结果与DLD样品存在明显差异,体现为基体中Mo含量偏低,但Cr与Ti的比例相对稳定。样品中的Mo颗粒(图11b)说明SLM过程中,所输入能量形成的熔池难以在极短的存活时间内充分熔化高熔点的Mo粉。部分Mo粉作为单质残留在产品中,而通过合金化进入中熵合金基体中的Mo含量则低于其他元素。
图13

图13 DLD加工CrMoTi中熵合金中的枝晶结构与元素分布图
Fig.13 SEM image of DLDed CrMoTi MEA (a) and EDS line scanning result of the dendrite structure (b)
基于上述讨论可知,在选择DLD与SLM等能量束增材制造技术作为原位合金化手段时,合金元素应该尽量选择在近似的熔沸点区间。当熔池熔化熔沸点差异过大的元素时,过高的能量输入会导致低沸点元素的挥发。而能量输入不足则会导致高熔点元素无法充分熔化。增材制造技术由于其加工过程中热应力积累的特点,能量输入还会受到成型工艺窗口的限制[30]。尤其是在利用SLM成型许多材料时(如采用高能量输入),可能会导致严重的组织开裂。相对而言,DLD技术对于原位合金化的成分选择更具有多样性。
图14为DLD1350W原位合金化CrMoTi合金样品的EBSD像。在样品中没有观察到明显的沿沉积方向(BD)生长的柱状晶,这可能与样品制备时使用的低扫描速率(3 mm/s)有关。激光光斑更长的作用时间延长了熔池的存在时间,同时也减小了熔池中的温度梯度的各向异性。与此同时,相对于电弧熔炼产品的粗大晶粒(图4),DLD样品中的晶粒尺寸较小,这是由于DLD熔池中的冷却速率(103~106 K/s)通常比电弧熔炼的冷却速率(10~100 K/s)高[11];其平均晶粒尺寸约为50 μm,对应硬度为634.6 HV0.3,高于电弧熔炼样品的硬度(520.6 HV0.3)。由Hall-Petch公式可知,较小的晶粒尺寸通常对应较高的硬度。而在SLM167J样品中,尽管SLM技术有着更高的冷却速率(106~108 K/s)[31],但Mo元素的低固溶率弱化了晶格畸变效应;以及大量裂纹导致的应力释放,样品硬度为605.9 HV0.3,反而略低于DLD样品,也反映了在增材制造技术中较差的加工适性会对产品性能带来负面影响。
图14
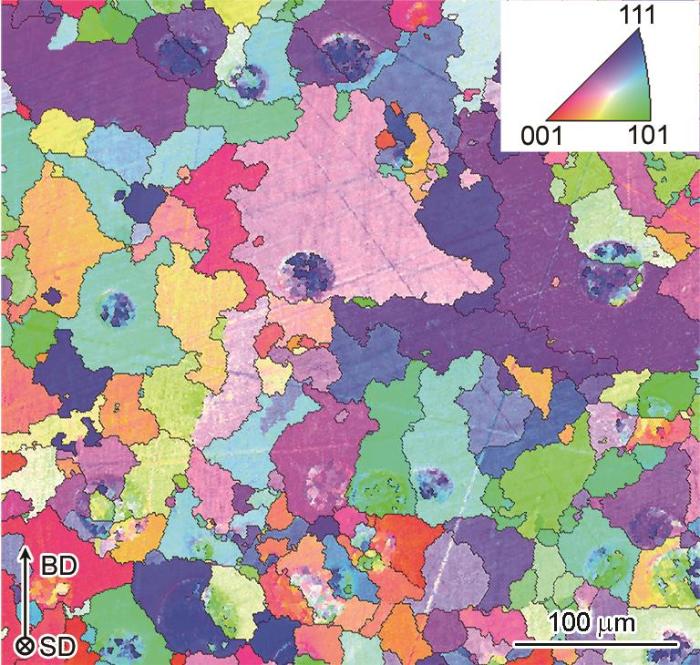
图14 DLD加工CrMoTi中熵合金的EBSD像
Fig.14 EBSD image of CrMoTi MEA fabricated by DLD (SD—scanning direction, BD—building direction along z-axis)
由于CrMoTi合金包含熔沸点差异较大元素,在其合金化过程中难以避免元素挥发,这在增材制造样品中体现尤为明显。其中低沸点元素的挥发带来成分差异,最终导致产物的晶格常数以及硬度均有差异。因此在采用增材制造技术进行原位合金化时,需考虑各元素性质的差异。
5 结论
(1) 理论预测及实验验证均表明CrMoTi中熵合金为bcc结构的单相固溶体,且DLD与SLM 2种增材制造技术均可以以单质元素粉末为原料,通过激光原位合金化该固溶体。其中DLD技术制备块体成型性较好,在激光功率1350 W、扫描速率3 mm/s的参数下打印件密度为7.47 g/cm3,CT结果显示相对致密度达到98.99%。SLM技术则因为其产生的较大热应力,较难以实现无裂纹块体的原位合金化。
(2) 电弧熔炼CrMoTi合金室温下硬度为520.6 HV0.3,600℃下为356.0 HV0.3。DLD原位合金化CrMoTi室温硬度可达634.6 HV0.3。电弧熔炼CrMoTi合金的室温热导率为13.8 W/(m·K),比热容为371 J/(kg·K)。其热导率在测试条件下随温度升高而增加,与纯金属材料的变化趋势相反,体现出准金属的热学性能。从硬度和热导率的角度,该合金略优于常见的H13热作模具钢。
来源-金属学报