分享:镍基高温合金K417G与氧化物耐火材料的界面反应
宋庆忠1,2, 潜坤1,3, 舒磊1,3, 陈波,1,3, 马颖澈1,3, 刘奎1,3
1.
2.
3.
研究了1600℃温度下Al2O3、CaO、MgO、Y2O3稳定ZrO2、CaO稳定ZrO2和Y2O3共6种材料坩埚与镍基高温合金K417G熔体的界面反应。结果表明:熔体对Al2O3坩埚以物理侵蚀为主,但坩埚易剥落导致合金中含有Al2O3夹杂物;CaO坩埚与合金界面处生成了液相Ca3Al2O6,促进熔体与CaO之间的润湿性,导致界面处粘连严重;MgO坩埚与熔体中Al反应生成MgAl2O4并进入合金生成夹杂物;Y2O3稳定ZrO2坩埚与合金界面处生成Al2O3反应层,但是Al2O3层未对坩埚发生侵蚀,可见这种坩埚具有较强的抗Al2O3渣的能力;CaO稳定ZrO2坩埚与合金界面处生成液相CaAl2O4,导致坩埚失稳,向合金内剥落溶解;Y2O3坩埚与合金界面处主要生成Al2Y4O9反应层,并且Y2O3向合金内溶解较为严重。坩埚和熔体交互作用对K417G熔体杂质O含量有显著影响,CaO、Y2O3和Y2O3稳定ZrO2坩埚熔炼合金中O含量没有增加,而CaO稳定ZrO2坩埚熔炼后O含量由0.0007% (质量分数)增加至0.0011%,MgO和Al2O3坩埚熔炼后,合金O含量增加明显,由0.0007%分别增加至0.0034%和0.0135%。
关键词:
镍基高温合金是国防工业最重要的材料之一[1],主要应用于航空发动机和燃气轮机的热端零部件,在航空发动机发展中扮演重要角色[2,3]。随着镍基高温合金的承温能力和使用寿命需求的提高,对合金质量的要求也越来越严格[4]。虽然近年来发展出了诸如超纯净熔炼等工艺[5,6],但是耐火材料对合金质量的影响仍然无法避免[7]。为此需要澄清耐火材料与合金熔体的反应机理,进一步提升合金质量。
由于镍基高温合金K417G具有强度高,塑性好和密度低等优点,因此主要被用于900℃长期工作的燃气涡轮发动机涡轮转子叶片[3]。K417G中含有5%~6% (质量分数)的Al和Ti,用来增加γ'相数量获得强化效果。由于合金内Al、Ti含量较高,所以过高含量的S、N、O会与Al、Ti反应生成Ti2SC[8]、TiN[8]和Al2O3夹杂物[9]等有害相。在高温燃气热冲击和温度循环双重作用下,涡轮叶片中的有害相和夹杂物将导致疲劳裂纹的产生和扩展[10]。
目前,真空感应熔炼是镍基高温合金母合金主要的生产方式之一[3,11],具有精确控制合金成分,活性金属不易氧化,化学成分均匀,过热度高,有利于脱氧、脱氮[12,13]和脱除易挥发杂质元素等优点[14,15]。自20世纪50年代随着真空技术的提高,真空感应熔炼被广泛应用在特殊钢、高温合金和钛合金等特种合金材料的冶炼。真空感应熔炼需要使用氧化物制成的坩埚盛装高温下的合金熔体,氧化物耐火材料虽然具有较高的熔点,但是在高温低压条件下长时间服役,耐火材料的化学稳定性和力学性能都会降低。此外,熔体对耐火材料的物理冲刷和化学侵蚀将进一步加剧耐火材料自身的分解,分解的有害物质会玷污熔炼的母合金[16],影响其产品的使用性能[17]。
耐火材料在熔炼过程中对合金的危害主要来自2方面:其一是高温下耐火材料向熔体内分解,使熔体内O含量升高;此外,在电磁搅拌作用下,合金熔体不断地冲刷坩埚内壁引入外来夹杂物进入合金。其二是熔体与耐火材料之间发生化学侵蚀。镍基高温合金成分中含有Al、Ti、Hf和Y等活性元素,这些元素会与坩埚内壁发生化学侵蚀[18~22],侵蚀生成的杂质元素随后进入合金。化学侵蚀不仅加快耐火材料的分解,还会降低耐火材料的使用寿命,增加生产成本。为了保证熔炼的高温合金纯净度满足航空航天工业的发展要求,普通的耐火材料已经不能满足高温合金熔炼的要求,亟待开发具有耐高温、抗腐蚀、高温化学和热稳定性好的特种耐火材料。
特种耐火材料是以熔点在1800℃以上的高纯氧化物、非氧化物和碳素等单一材料或各种复合型耐火材料为原料,其制品具有特殊性能和特种用途的新型耐火材料[23]。由于氧化物具有较低的生成Gibbs自由能[24],因此常被用做坩埚耐火材料熔炼镍基高温合金[9,18]。其中,ZrO2、CaO和Y2O3已经被用来熔炼TiAl合金[25~29]、TiNi合金[30~32]和TiFe合金[33]。但是,每种氧化物各有优缺点,如CaO易水化难以保存[34],MgO高温真空下易分解[35],Y2O3价格昂贵,抗热震性差[36]并且难于烧结[37],掺杂稳定剂的ZrO2随着熔炼次数的增加,易发生晶型转变导致制品开裂[38]。由此可知,耐火材料的热力学稳定性不能单独作为评判耐火材料优劣的标准[39]。因此,厘清合金熔体和坩埚之间高温作业过程,对合金生产和耐火材料的研发具有重要意义。本工作选择了Al2O3、CaO、MgO、Y2O3稳定的ZrO2、CaO稳定的ZrO2和Y2O3作为熔炼K417G镍基高温合金的耐火材料,研究不同耐火材料和K417G镍基高温合金之间的交互作用,评价它们的抗熔体侵蚀的能力,分析界面反应机理,为挑选适合熔炼高铝钛含量的镍基高温合金耐火材料提供指导。
1 实验方法
1.1 坩埚的制作
坩埚的生产工艺一般包括:原料、混料、成型、干燥和烧成5个主要步骤。特种耐火材料成型工艺主要分为[23]:注浆法、热压注法、挤压成型法、等静压法、压制法、振动法、热压法和熔铸法。本工作采用冷等静压成型方法制作坩埚,其优点是可任意改变塑性模具的形状和尺寸,工艺灵活方便,适用性强且坯体各向施压均匀[40]。坩埚原料的纯度如表1所示。首先将原料进行混料,为保证耐火材料的纯度,不添加任何助成型剂和烧结剂,然后将混合后的物料填充到模具中,放入冷等静压机中,在280 MPa下保压2 min之后进行卸压。取出成型后的样品,迅速将坩埚素坯放入真空干燥箱储存,真空下加热到100℃,烘干2 h。再将烘干后的坩埚放入马弗炉内,以2.5℃/min升温到1200℃保温2 h进行预烧结,再以2.5℃/min的速率升温到1680℃保温0.5 h,最后断电停止加热,使坩埚随炉冷却至室温,烧制完成的坩埚放入真空干燥箱内储存。烧结后的氧化物坩埚显气孔率和体积密度如表2所示。
表1 制作氧化物坩埚的原料纯度
Table 1
Raw material | Purity / (mass fraction, %) |
---|---|
Al2O3 | ≥ 99.61, MgO ≤ 0.10, SiO2 ≤ 0.13, CaO ≤ 0.16, Fe2O3 ≤ 0.002, TiO2 ≤ 0.01, Na2O ≤ 0.03 |
CaO | ≥ 96.78, MgO ≤ 0.53, Al2O3 ≤ 0.20, SiO2 ≤ 0.05, TFe ≤ 0.01, TiO2 ≤ 0.014, S ≤ 0.001, Loss ≤ 2.01 |
MgO |
≥ 98.5, Fe ≤ 0.005, Ba ≤ 0.003, Cl- ≤ 0.07, SO |
Y2O3 | ≥ 99.99, Loss ≤ 0.01 |
ZrO2 | ≥ 99.0, Fe2O3 ≤ 0.005, MgO ≤ 0.05, CaO ≤ 0.05, TiO2 ≤ 0.005, SiO2 ≤ 0.01, Loss ≤ 1 |
表2 坩埚制作工艺参数、显气孔率和体积密度
Table 2
Crucible | Composition | Pressure | Sintering temperature | Apparent porosity | Bulk density |
---|---|---|---|---|---|
(mass fraction) | MPa | ℃ | % | g·cm-3 | |
Al2O3 | 100% | 280 | 1680 | 1.26 | 3.76 |
CaO | 100% | 280 | 1680 | 1.23 | 3.00 |
MgO | 100% | 280 | 1680 | 1.23 | 3.40 |
Y-PSZ | 12%Y2O3 + 88%ZrO2 | 280 | 1680 | 15.00 | 4.94 |
CSZ | 20%CaO + 80%ZrO2 | 280 | 1680 | 28.00 | 3.50 |
Y2O3 | 100% | 280 | 1680 | 21.50 | 3.94 |
用SmartLab多功能X射线衍射仪(XRD)在45 kV和200 mA的条件下测定坩埚烧结后的物相组成(CuKα,衍射角(2θ)为10°~80°,扫描速率10°/min)。
1.2 熔炼过程
使用上述6种不同材料坩埚分别熔炼镍基高温合金K417G,母合金的化学成分(质量分数,%,下同)为:Cr 8.81,Co 9.66,Al 5.28,Ti 4.36,Mo 3.00,C 0.18,Zr 0.07,V 0.77,O 0.0007,N 0.0002,S < 0.0004,Ni 余量。将K417G母合金加工成直径14 mm、长14 mm的圆柱体,表面打磨光亮后放入丙酮中超声波清洗并烘干。
图1为实验过程使用的真空感应炉的结构示意图,其结构由气体净化系统、加热控制系统和水冷系统3部分组成。气体净化系统由干燥分子筛、脱氧Pt催化剂和气体质量流量计组成,主要用来脱除Ar气和H2中的微量水分和O2,并控制Ar气和H2的混合比例;加热控制系统为高频感应电源通过感应线圈搭配石墨发热体组成,再由坩埚底部的热电偶测温,然后利用温度控制表反馈调节加热电源功率进行控温加热;水冷系统主要用于冷却样品托和炉体。
图1
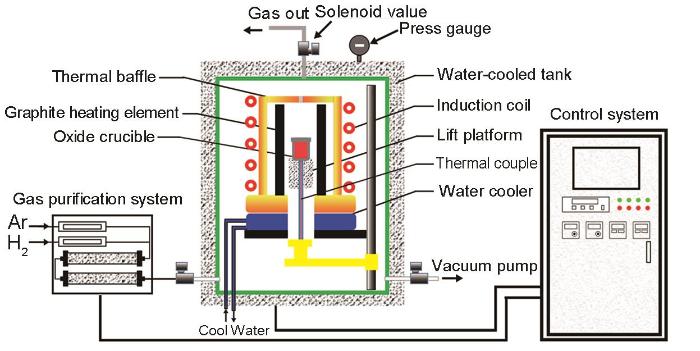
图1 实验设备示意图
Fig.1 Schematic diagram of experiment equipment
将K417G样品放入坩埚中,熔炼前先进行抽真空,将炉内压力抽至1 Pa后通入高纯Ar气(99.999%),重复抽真空和充高纯Ar气3次后,启动气体净化系统,通入Ar∶H2体积比为95∶5的混合气体,直至炉体压力为微正压后,炉体顶部阀门自动泄压。启动温度控制系统,以40℃/min的升温速率加热到1600℃,保温40 min,之后快速冷却至1400℃,防止坩埚和熔体之间进一步发生反应,再以10℃/min的降温速率降温至600℃,防止合金和坩埚之间界面破碎严重,为后续分析界面处的微观组织提供条件,随后自然冷却至室温。
实验结束后,将凝固的合金与坩埚整体冷镶嵌,然后采用无水的金刚石线切割机沿样品的中心处进行切割,切下的样品制成金相样品,使用S-3400N扫描电子显微镜(SEM)及能谱仪(EDS)分析坩埚和合金的界面反应层及元素分布情况;使用OPTIMA 8300DV电感耦合等离子体原子发射光谱仪(ICP-AES)定量分析合金内金属元素含量;使用LECO-ONH836氧氮氢分析仪定量分析合金内O元素。
2 实验结果和讨论
2.1 坩埚物相表征
图2为原始氧化物坩埚的XRD谱。纯组元坩埚Al2O3、MgO、CaO和Y2O3材料坩埚未发现其他物相。ZrO2坩埚具有单斜(m)、四方(t)以及立方(c) 3种晶型,不同温度下晶型转变伴随着体积变化,易产生裂纹导致开裂。为了使ZrO2在各种温度下晶型稳定,需向ZrO2内加入稳定剂,如CaO[41]、MgO[18]和Y2O3[42]等。本实验中分别向ZrO2中掺杂了Y2O3和CaO,其中掺杂12%的Y2O3的ZrO2坩埚物相为四方相、立方相以及少量的单斜相,并未发现Y2O3的物相存在。这是由于ZrO2和Y2O3形成固溶体,Y2O3将常温下稳定存在的单斜ZrO2高温处理后稳定为四方相和立方相[42]。但是,因为Y2O3的掺杂量有限,并未完全将单斜相全部稳定为四方相和立方相,所以掺杂12%Y2O3的ZrO2坩埚被称为Y2O3部分稳定的ZrO2坩埚(Y-PSZ)。掺杂20%CaO的ZrO2坩埚中物相为四方相、立方相和CaZrO3物相,未发现单斜ZrO2物相。可知一部分CaO将单斜相ZrO2完全稳定为四方相和立方相,另一部分CaO与ZrO2生成复合氧化物CaZrO3物相,因此掺杂20%CaO的ZrO2坩埚被称为CaO完全稳定的ZrO2 (CSZ)坩埚。
图2
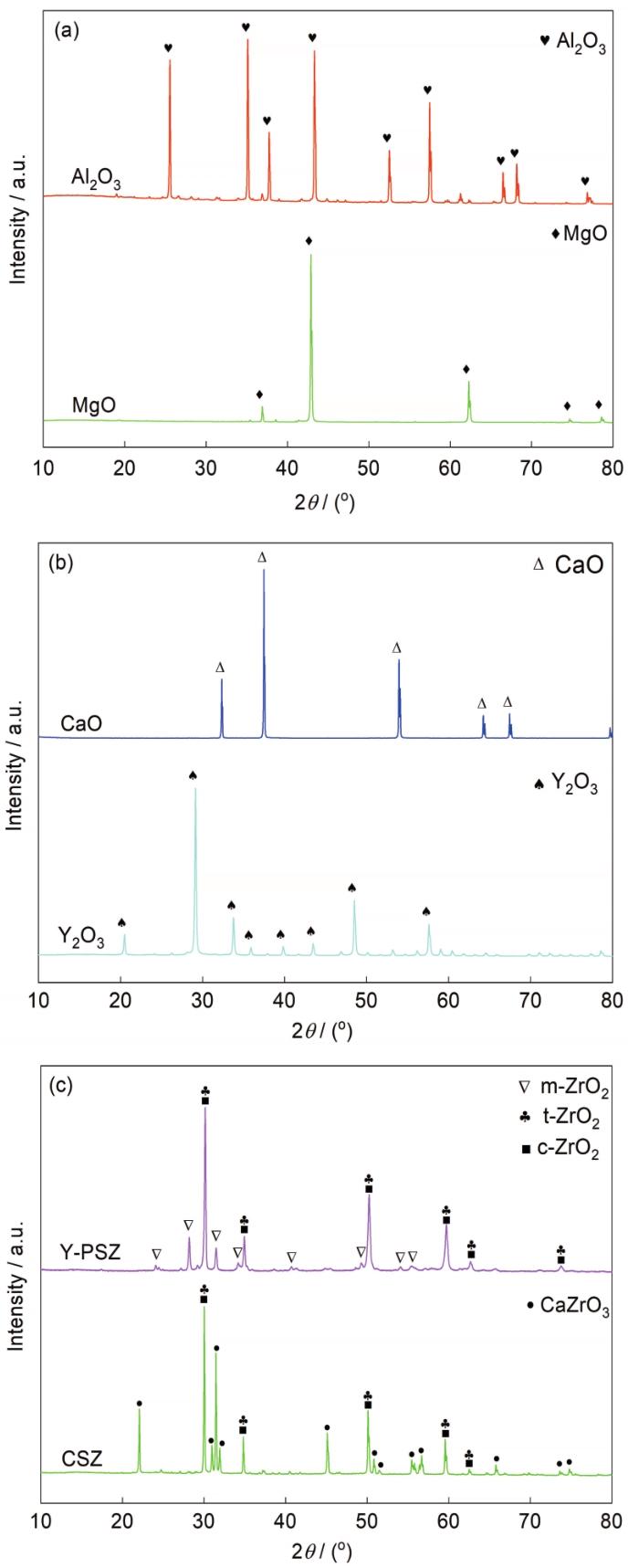
图2 不同氧化物坩埚的XRD谱
Fig.2 XRD spectra of various oxide crucibles after sintering
(a) Al2O3 and MgO
(b) CaO and Y2O3
(c) Y-PSZ and CSZ (m—monoclinic, t—tetragonal, c—cubic)
2.2 界面反应研究
2.2.1 Al2O3坩埚
Al2O3耐火材料具有价格便宜,化学性质稳定和力学性能优异等优点,是目前使用最为广泛的耐火材料之一。可见,Al2O3坩埚与镍基高温合金的界面反应研究具有重要的实践意义。图3为熔炼后的Al2O3坩埚和K417G合金。可以看出,Al2O3坩埚和熔体接触的界面较为光滑,其颜色为黑灰色,不存在Al2O3和合金的黏结,这说明合金与坩埚之间润湿性较差,熔体没有渗透进入Al2O3坩埚内部。Al2O3属于中性耐火材料,兼具酸性和碱性2种性质,具有优异的抗酸性和碱性熔体侵蚀性质。镍基高温合金内Al元素虽然具有极高的化学活性,但是Al2O3坩埚对K417G展现了优异的抗侵蚀性能。此外,在接近熔体/坩埚界面的熔体内发现了Al2O3夹杂物,推测Al2O3坩埚颗粒之间的结合力较差,并且在熔体的冲刷下颗粒向合金内剥落。图4为合金内部发现的Al2O3夹杂物,同样证明了K417G合金与Al2O3坩埚之间的交互作用以物理侵蚀为主。
图3
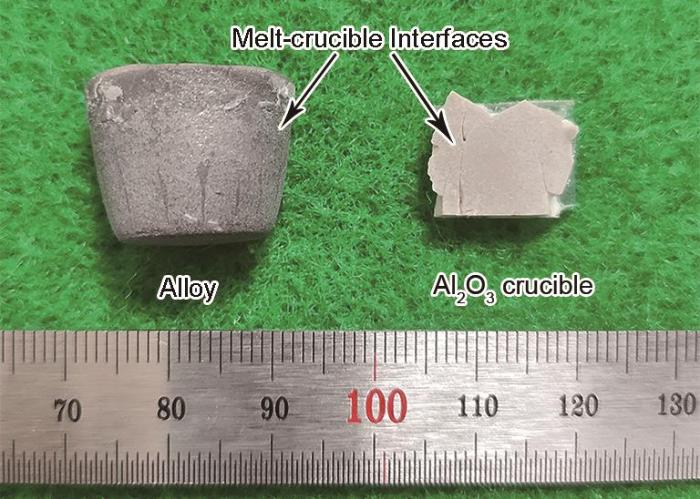
图3 Al2O3熔炼后K417G合金宏观形貌
Fig.3 Macromorphology of nickel-based superalloy K417G smelted by Al2O3 crucible
图4
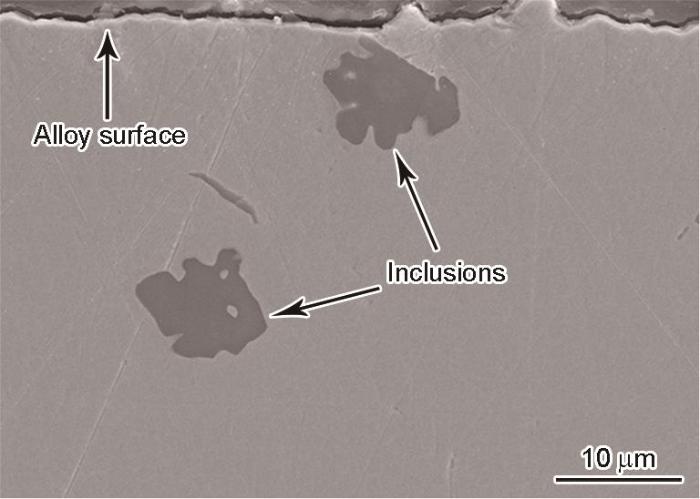
图4 Al2O3坩埚熔炼后合金液面处的Al2O3夹杂物
Fig.4 Al2O3 inclusions flowed at the liquid surface
图5为Al2O3坩埚和K417G合金界面的SEM像和EDS元素分布图。从图5a可以看出,临近界面的坩埚形貌变为疏松多孔,出现大量黑灰色孔隙,在熔体渗透和流动冲刷作用下,坩埚中的Al2O3颗粒剥落进入熔体。这也可以解释图4中熔体出现的Al2O3夹杂是熔体与Al2O3之间发生物理侵蚀,促使Al2O3向熔体中剥落。如图5c和f所示,熔体中Ni和Ti并未穿过熔体/坩埚界面进入坩埚内部。此外,在界面处熔体一侧发现了坩埚向熔体伸出的针状物,并分别对合金一侧发现的针状物(A点)和坩埚基体(B点)进行EDS分析。如表3结果所示,坩埚基体的B点仅含有Al和O元素,基本符合Al2O3的原子比例。而合金一侧发现的针状物(A点)成分除了Al和O元素外,还含有3.31%的Ca元素,而Al2O3坩埚基体并未检测出Ca元素,推断Ca元素来自合金液。实验用K417G母合金是由CaO坩埚真空感应熔炼,母合金中含有0.0008%的Ca,熔炼过程中合金液中微量的Ca元素与Al2O3坩埚之间置换反应生成CaO,而CaO与Al2O3可以生产多种化合物,导致坩埚一侧出现Ca元素富集,但总体来说,生成的量很少。
图5
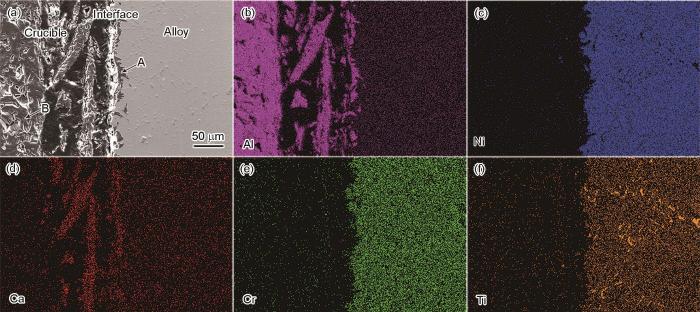
图5 Al2O3坩埚与镍基高温合金K417G界面的SEM像及EDS元素分布图
Fig.5 SEM image (a) and EDS mappings (b-f) of the interface between Al2O3 crucible and nickel-based superalloy K417G
表3 图5a中Al2O3坩埚与K417G合金界面处EDS分析结果 (atomic fraction / %)
Table 3
Location | O | Al | Ca | Mg | Ti | Ni |
---|---|---|---|---|---|---|
A | 54.27 | 41.12 | 3.31 | 0.45 | 0.30 | 0.55 |
B | 55.79 | 44.21 | 0.00 | 0.00 | 0.00 | 0.00 |
2.2.2 CaO坩埚
图6是CaO坩埚与K417G合金界面的SEM像和EDS元素分布图。图6a中左侧为CaO坩埚,右侧为K417G合金,从图中可以看出熔炼后坩埚和合金的界面清晰并且粘连在一起。界面处元素EDS线扫描结果表明,坩埚元素Ca和O在界面处并没有向合金内溶解和扩散的现象,同时,K417G熔体中多数组元未向CaO坩埚内部渗透和扩散,仅观察到熔体中Al元素穿过界面向CaO坩埚一侧扩散,并出现局部富集现象,如图6d所示。
图6
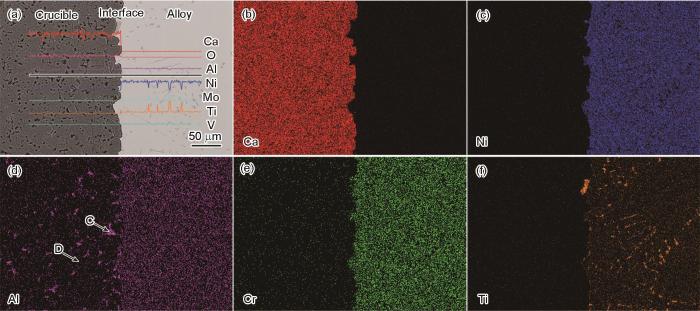
图6 CaO坩埚与镍基高温合金K417G界面的SEM像及EDS元素分布图
Fig.6 SEM image (a) and EDS mappings (b-f) of the interface between CaO crucible and nickel-based superalloy K417G
为了确定图6d中Al元素扩散富集区的成分,对图6d中C和D 2点进行EDS分析。表4结果显示D点坩埚基体成分与原始坩埚成分基本相同,而Al富集区的C点主要含有Ca、Al、O元素,并且Ca∶Al原子比为3∶2。根据CaO-Al2O3系相图[43],推测C点富Al区为Ca3Al2O6。因为Ca3Al2O6的熔点仅为1539℃,低于实验温度1600℃,故Ca3Al2O6为液相,可以沿坩埚孔隙渗透进入坩埚内部。Xie等[8]在使用CaO坩埚熔炼镍基高温合金时,同样发现了坩埚内壁存在Ca3Al2O6的渣,这种碱性渣有利于镍基高温合金熔体脱硫[44]。
表4 图6d中CaO坩埚与K417G合金界面处EDS分析结果 (atomic fraction / %)
Table 4
Location | O | Al | Ca | Ti | V | Co | Ni |
---|---|---|---|---|---|---|---|
C | 49.39 | 20.04 | 30.15 | 0.04 | 0.07 | 0.07 | 0.24 |
D | 64.92 | 0.00 | 34.97 | 0.08 | 0.00 | 0.00 | 0.03 |
为了进一步观察熔炼后界面处情况,将熔炼后的镍基高温合金从坩埚中取出。图7是CaO坩埚熔炼后的K417G镍基高温合金界面宏观形貌。可见,合金外表面处存在CaO的黏结层,并且CaO黏结层和K417G合金粘连紧实。熔炼结束后高温降至室温的过程,由于坩埚和合金的收缩速率不同,导致Al2O3、MgO、Y-PSZ、CSZ和Y2O3这几种坩埚和合金界面处发生分离,但是使用CaO熔炼后的K417G镍基高温合金界面处并未发生分离。熔体/坩埚界面处的黏结程度用下式表示[35,45,46]:
式中,
图7

图7 CaO熔炼的镍基高温合金K417G宏观形貌
Fig.7 Macromorphology of nickel-based superalloy K417G smelted by CaO crucible
因此,使用CaO坩埚熔炼含Al的K417G镍基高温合金,坩埚与熔体界面清晰,没有明显的物理侵蚀和化学反应,坩埚元素Ca和O没有向合金内溶解和扩散,熔体中组元除Al之外,其他组元没有进入坩埚。熔体中组元Al会首先生成Al2O3并且附着在坩埚内壁,高温下Al2O3与CaO进一步生成Ca3Al2O6液相,具有促进熔体脱硫的有益作用,但界面Ca3Al2O6相降低了CaO坩埚和合金熔体的润湿角,导致坩埚与合金粘连严重[35]。
2.2.3 MgO坩埚
图8是MgO坩埚与K417G合金界面的SEM像和EDS元素分布图。图8a给出了MgO坩埚与合金熔炼后界面形貌和界面元素线扫描曲线。相比于CaO与合金界面,MgO坩埚与合金在界面处发生了分离,冷镶样过程中镶料进入界面处缝隙。元素线扫描曲线表明Mg、Al和O在界面处同时出现了富集区。根据图8d的EDS元素面扫结果,发现界面处出现了连续的Al富集层,由此可推断合金中的元素Al与MgO坩埚发生了交互作用。为了确定界面处的产物,分别对图8a中的E和F点进行了EDS元素分析,结果如表5所示。其中E点存在Mg、Al和O 3种元素,Mg∶Al原子比为1∶2;F点主要为Mg和O 2种元素,Mg∶O原子比为1∶1。由于Al2O3和MgO在1600℃会生成镁铝尖晶石MgAl2O4[43],据此推断界面产物为MgAl2O4,反应过程为:合金熔体中Al元素与MgO发生置换反应,随后Al2O3与MgO生成MgAl2O4[49]。
图8
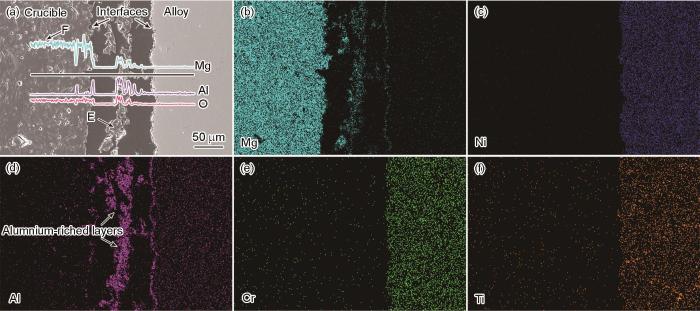
图8 MgO坩埚与镍基高温合金K417G界面SEM像及EDS元素分布图
Fig.8 SEM image (a) and EDS mappings (b-f) of the interface between MgO crucible and nickel-based superalloy K417G
式中,[Al]Ni为合金熔体中的Al元素。熔体/坩埚界面处出现的反应层为MgAl2O4,由于MgAl2O4熔点较高,实验温度下为固态产物,所以并未促进MgO坩埚与镍基高温合金的润湿。
表5 图8a中MgO坩埚与K417G合金界面处EDS分析结果 (atomic fraction / %)
Table 5
Location | O | Al | Mg | Cr | Ni |
---|---|---|---|---|---|
E | 50.91 | 32.73 | 16.12 | 0.09 | 0.15 |
F | 43.41 | 0.17 | 56.21 | 0.08 | 0.13 |
此外,在合金液面处还发现了MgAl2O4夹杂物。由于坩埚内壁MgO反应生成MgAl2O4后体积发生膨胀,使MgO坩埚内壁组织变得疏松。随着熔体冲刷作用,反应产物将裹进合金液内部并上浮在合金液面,如图9所示。
图9
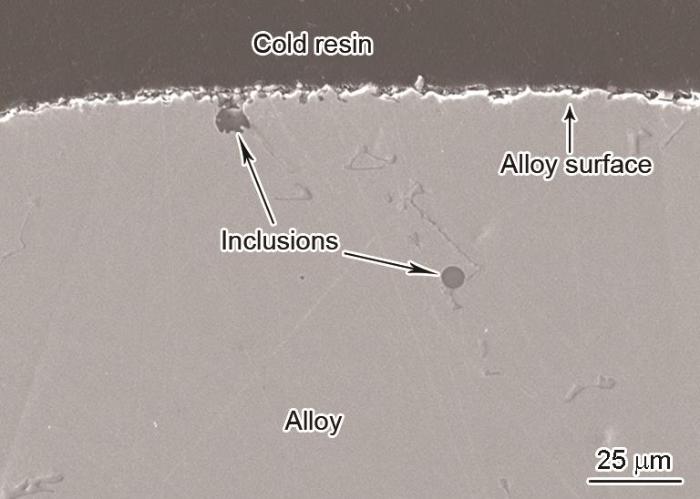
图9 MgO坩埚熔体上表面液面处镁铝尖晶石夹杂物
Fig.9 MgAl2O4 inclusions flowed at the liquid surface
2.2.4 Y2O3部分稳定的ZrO2坩埚
实验后K417G合金与Y-PSZ坩埚之间界面清晰完整且坩埚无破裂,但是凝固的熔体和坩埚之间出现分离,如图10a显示,导致冷镶料进入缝隙。图10b、d、e显示了Y-PSZ坩埚与K417G合金界面处Zr、Al和Y的元素分布,其中Zr和Y未出现在合金一侧,但Al却富集在坩埚壁,其厚度为22 μm,与CaO界面处情况不同的是熔体中Al并未渗入坩埚内部,也未出现合金熔体向坩埚内渗透的情况。结合表6中G和H 2点EDS分析结果(分析位置如图10a所示),可以确定界面处的富Al层为Al2O3。由于ZrO2高温下与活性金属接触易失去O原子生成贫氧ZrO2 - x[50],所以ZrO2坩埚熔炼镍基高温合金时熔体中组元Al会争夺ZrO2中的O原子生成Al2O3[18],据此推断反应过程为:
图10
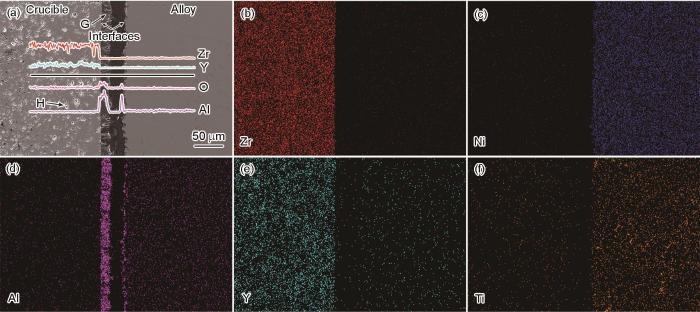
图10 Y2O3部分稳定的ZrO2 (Y-PSZ)坩埚与镍基高温合金K417G界面的SEM像及EDS元素分布图
Fig.10 SEM image (a) and EDS mappings (b-f) of the interface between Y-PSZ crucible and nickel-based superalloy K417G
表6 图10a中Y-PSZ坩埚与K417G合金界面处EDS分析结果 (atomic fraction / %)
Table 6
Location | O | Al | Zr | Y | Ti | Cr | Co | Ni |
---|---|---|---|---|---|---|---|---|
G | 57.99 | 41.78 | 0.00 | 0.00 | 0.11 | 0.00 | 0.00 | 0.12 |
H | 62.33 | 0.47 | 31.26 | 5.15 | 0.10 | 0.24 | 0.11 | 0.34 |
相比于CaO坩埚,Al2O3与ZrO2不形成固溶体,Y-PSZ坩埚有着很好的抗铝渣性能,所以并未出现Al2O3向坩埚内部发生侵蚀。
图11是Y-PSZ坩埚熔炼后的合金液面,同样发现了夹杂物的存在,经成分分析确认为Al2O3夹杂物,这是由熔体冲刷后将界面处的反应产物卷入合金内部并上浮到上表面造成的。
图11
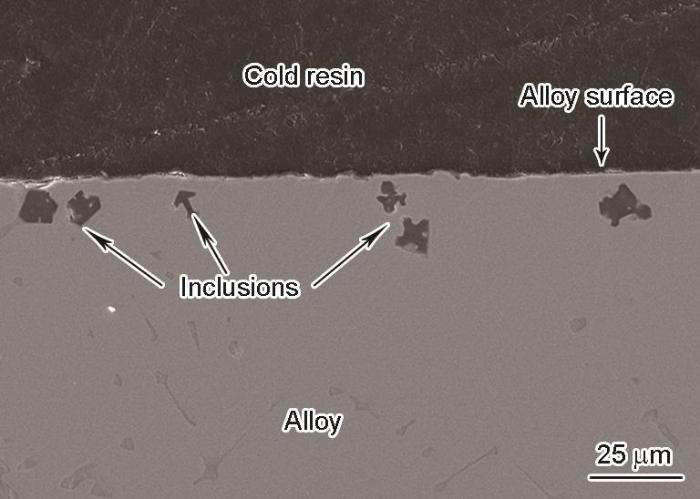
图11 Y-PSZ坩埚熔炼后合金液面处的Al2O3夹杂物
Fig.11 Al2O3 inclusions flowed at the liquid surface smelted by Y-PSZ crucible
2.2.5 CaO完全稳定的ZrO2坩埚
图12为CSZ坩埚和K417G合金界面的SEM像和EDS元素分布图。从图12a可看出,界面处合金与坩埚发生分离,界面为曲线状,并且坩埚一侧破碎严重。图12b、d、e分别为Zr、Al和Ca元素的分布图,其中虚线为合金与坩埚的界面分割线。首先,从元素Zr的分布可以看出除了坩埚一侧存在元素Zr,分割线的右侧(合金内部)同样发现了元素Zr。对I和J 2点进行成分分析,如表7结果所示,I和J 2点主要是Zr和O元素,原子比为1∶2,可知进入合金内的夹杂为纯ZrO2。值得注意的是,ZrO2夹杂成分中的Ca元素消失不见。此外,熔体中Al在坩埚一侧呈零星状分布,从含Al处(K点)的成分分析来看,未发现合金中其他元素大量存在。
图12
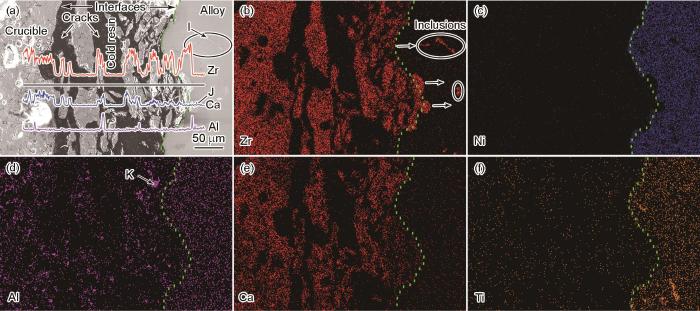
图12 CaO完全稳定的ZrO2 (CSZ)坩埚与镍基高温合金K417G界面SEM像及EDS元素分布图
Fig.12 SEM images (a) and EDS mappings (b-f) of the interface between CSZ crucible and nickel-based superalloy K417G
表7 CSZ坩埚与K417G合金界面处EDS分析结果(见图12~14各点) (atomic fraction / %)
Table 7
Location | O | Al | Ca | Zr | Ti | Cr | Co | Ni |
---|---|---|---|---|---|---|---|---|
I | 56.33 | 0.27 | 0.20 | 39.75 | 0.08 | 0.42 | 0.45 | 2.50 |
J | 60.28 | 0.10 | 0.22 | 38.39 | 0.07 | 0.00 | 0.00 | 0.95 |
K | 50.61 | 27.25 | 16.95 | 4.54 | 0.14 | 0.01 | 0.17 | 0.34 |
L | 70.04 | 0.00 | 5.23 | 24.74 | 0.00 | 0.00 | 0.00 | 0.00 |
M | 63.43 | 23.77 | 11.51 | 1.29 | 0.00 | 0.00 | 0.00 | 0.00 |
N | 60.07 | 0.00 | 17.93 | 21.32 | 0.27 | 0.00 | 0.00 | 0.00 |
O | 61.94 | 0.00 | 6.65 | 31.41 | 0.00 | 0.00 | 0.00 | 0.00 |
如图13a~d所示,对坩埚一侧含Al处进行微观区域分析,L点为ZrO2晶粒,M点为晶粒间隙。M点间隙处主要为Al、O和少量的Ca元素,Ca∶Al原子比为1∶2,可知在晶粒间隙生成了CaAl2O4液相。图14为CSZ坩埚原始形貌的背散射电子(BSE)像,其中N点的Zr和Ca元素原子比为1∶1,即N点为CaZrO3,O点为1∶6,即O点为Ca0.15Zr0.85O1.85,其结果与XRD物相分析结果一致。
图13
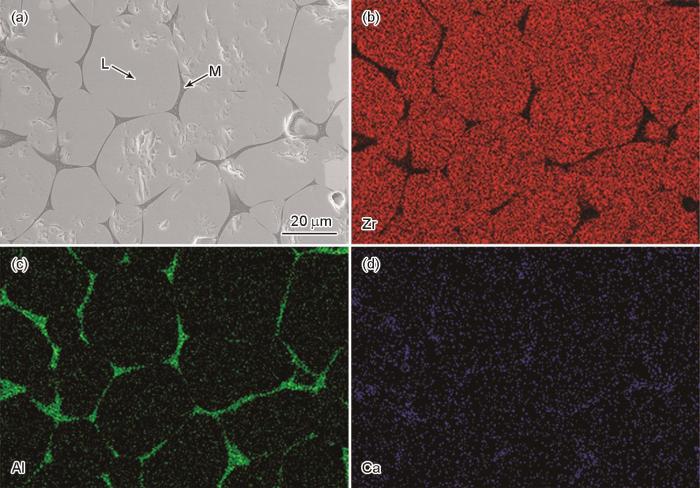
图13 熔炼K417G合金后的CSZ坩埚背散射电子(BSE)像及EDS元素分布图
Fig.13 Backscattered electron (BSE) image (a) and EDS mappings (b-d) of CSZ crucible after smelting nickel-based superalloy K417G
图14
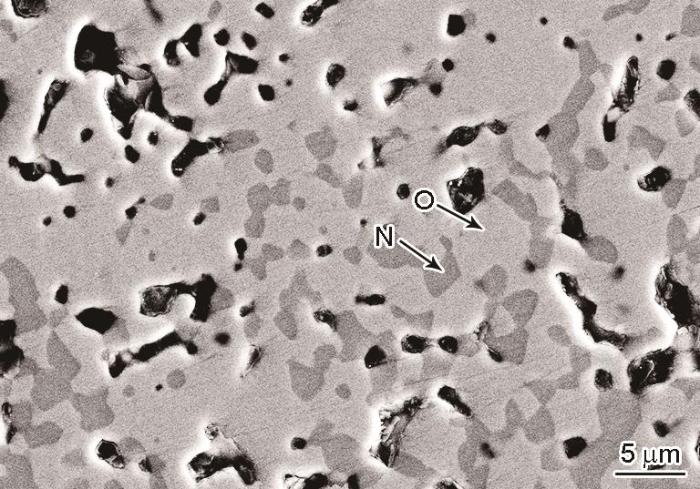
图14 CSZ坩埚原始形貌BSE像
Fig.14 BSE image of original micromorphology of CSZ crucible
根据图12e中Ca元素的分布情况和图12a中Ca元素的线扫描强度,在接近K417G合金界面时Ca元素强度降低。Ca和Zr元素线扫描强度在远离界面时其强度同步增加或降低,但在接近合金时,Zr元素强度未变,Ca元素强度却出现了降低的情况。此外,将CSZ坩埚熔炼后的合金取出后,从图15中可观察到界面凹凸不平,说明坩埚和熔体之间的反应较为强烈。
图15
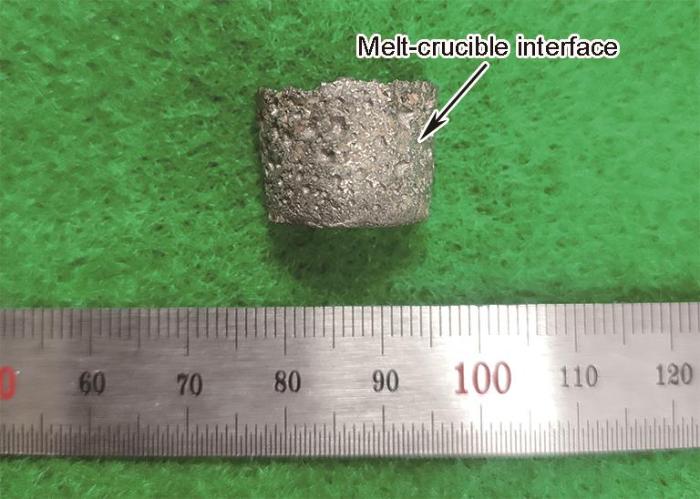
图15 CSZ坩埚熔炼的K417G镍基高温合金宏观形貌
Fig.15 Macromorphology of nickel-based superalloy K417G smelted by CSZ crucible
对比CSZ坩埚熔炼前(图14)和熔炼后(图13a)的BSE像可以得出,熔炼过程中CSZ坩埚与K417G的交互作用主要为合金熔体中Al2O3渣沿着ZrO2晶粒间隙渗透和CSZ坩埚中稳定剂CaO的流失。由于CSZ和Y-PSZ坩埚皆是以ZrO2为基体的二元耐火材料,所以K417G熔体与CSZ、Y-PSZ坩埚开始接触时具有相同的反应过程,即熔体中的Al与ZrO2坩埚接触生成了Al2O3渣,即反应式(4)。
但是,由于CSZ显气孔率较高,其界面形貌不会像Y-PSZ与K417G合金的界面一样,Al2O3黏结在CSZ坩埚内壁,而是会向坩埚基体一侧渗透(图12a所示)。然后,在Al2O3渣的渗透作用下,CSZ坩埚中的稳定剂CaO由晶粒内部向晶粒间隙的Al2O3渣中溶解,导致坩埚基体中的CaZrO3转变为Ca0.15Zr0.85O1.85,即图13a中L处含有5%CaO (原子分数)的ZrO2晶粒,同时,流失的CaO与晶粒间隙的Al2O3渣化合生成CaAl2O4液相,即图13a中晶粒间隙物质。反应过程如下:
由于稳定剂CaO的流失,CaZrO3会完全转化为Ca0.15Zr0.85O1.85,并且越接近合金界面处的坩埚,其所受熔体中Al的化学侵蚀时间越长,CaO的流失也越严重,这也说明了接近界面处的Ca元素分布强度降低的原因,最终CaO的完全流失导致Ca0.15Zr0.85O1.85完全失稳,界面处的Ca0.15Zr0.85O1.85相最终转化为ZrO2 (图12a中I和J点的ZrO2),随之进入合金内部形成夹杂物。反应过程如下:
2.2.6 Y2O3坩埚
Y2O3是6种材料中热力学上最稳定的,从图16a中坩埚与凝固合金的界面处微观形貌可以看出,合金与坩埚之间的少部分黏结,坩埚一侧未出现破碎以及剥落现象。从界面元素分布来看,熔体/坩埚界面两侧元素区分明显,未出现合金向坩埚内的渗透以及坩埚向合金内的剥落情况,仅在界面处出现了10 μm的Al元素富集层,如图16d所示。
图16
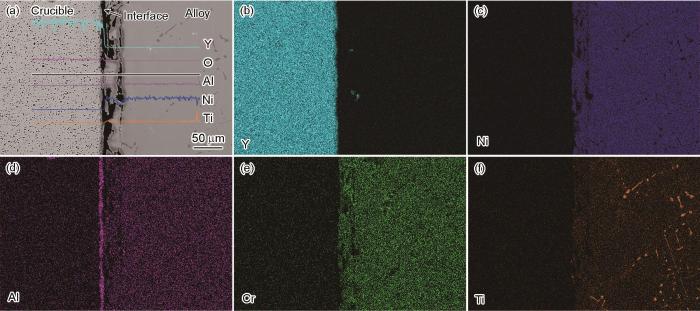
图16 Y2O3坩埚与镍基高温合金K417G界面SEM像及EDS元素分布图
Fig.16 SEM image (a) and EDS mappings (b-f) of the interface between Y2O3 crucible and nickel-based superalloy K417G
图17a为Y2O3坩埚与镍基高温合金K417G界面组织的BSE像,对图17a界面处富Al层(P点)和坩埚基体(Q点)进行化学成分分析,结果如表8所示。可见,界面的富Al层(P点)包含Al、Y和O元素,且Al和Y原子比为1∶2,初步确定在界面处生成Y4Al2O9[51]。分析合金γ + γ'共晶前沿[52],即图17b中框内元素分布,发现框内白色相有Y元素的富集,其成分Ni∶Y∶Al∶Co∶Cr∶O原子比为67.67∶13.19∶7.01∶5.90∶2.77∶2.96,其中O和Y的原子比为1∶4,可知不是Y2O3颗粒剥落进入合金液内,而是坩埚向合金内发生溶解。因γ + γ'共晶前沿是合金最后凝固的区域,随着凝固的进行,正偏析Y元素逐渐向该区域富集,最终形成富Y元素区域。此外,表9结果显示熔炼后的合金内Y含量达到0.0150%,熔体中Y元素的增加也间接证明了Y2O3分解成Y和O元素。据此判断高温熔炼过程中Y2O3首先分解成Y和O元素,其中O元素与熔体中的Al在界面处生成了Al2O3,随后与Y2O3发生反应生成Y4Al2O9,分解的Y则溶解进入熔体中,反应过程如下:
图17
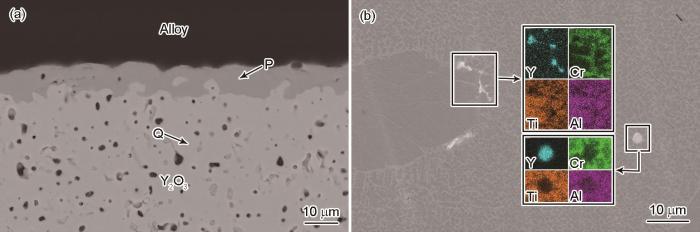
图17 Y2O3坩埚与K417G合金界面组织及Y2O3坩埚熔炼后的K417G合金的BSE像
Fig.17 BSE images of interface between Y2O3 crucible and K417G alloy (a) and K417G alloy (b) smelted by Y2O3 crucible (Insets are EDS mappings of segregation regions of Y inside K417G alloy)
式中,[Y]Ni为溶解在合金熔体中的元素Y,[O]Ni为溶解在合金熔体中的元素O。
表8 图17a中Y2O3坩埚与K417G合金界面处EDS分析结果 (atomic fraction / %)
Table 8
Location | O | Al | Y | Ti | Cr | Co | Ni |
---|---|---|---|---|---|---|---|
P | 57.23 | 13.45 | 28.70 | 0.15 | 0.04 | 0.06 | 0.37 |
Q | 56.05 | 0.00 | 43.82 | 0.00 | 0.03 | 0.05 | 0.05 |
表9 熔炼后K417G合金内杂质元素含量 (atomic fraction / %)
Table 9
Crucible | O | Al | Ca | Mg | Zr | Y |
---|---|---|---|---|---|---|
Al2O3 | 0.0135 | 5.25 | - | - | - | - |
CaO | 0.0006 | - | 0.0010 | - | - | - |
MgO | 0.0034 | - | - | 0.0090 | - | - |
Y-PSZ | 0.0008 | - | - | - | 0.068 | < 0.0010 |
CSZ | 0.0011 | - | 0.0008 | - | 1.760 | - |
Y2O3 | 0.0007 | - | - | - | - | 0.0150 |
2.2.7 熔体O含量变化及坩埚热力学稳定性分析
表9为不同坩埚熔炼K417G合金的杂质含量。通过对比原始母合金与CaO、Y2O3和Y-PSZ坩埚熔炼后的合金O含量,结果发现,这3种坩埚熔炼后的合金O含量在0.0006%~0.0008%之间,这与母合金内原有的O含量0.0007%相符,可见这3种耐火材料热力学稳定性较高。而CSZ、MgO和Al2O3坩埚熔炼后合金的O含量分别为0.0011%、0.0034%和0.0135%,其中MgO和Al2O3稳定性最低,在熔炼过程中易分解成O原子进入合金。从耐火材料分解的金属元素来看,Y-PSZ坩埚分解的Y元素含量低于0.0010%,Zr含量为0.068%等于合金内的原有Zr含量。CSZ熔炼后的合金中Zr含量增至1.760%,这与界面处的分析情况相同,由于ZrO2稳定剂失稳导致ZrO2坩埚向合金内溶解和剥落。MgO分解进入合金的Mg元素达到0.0090%,相比之下,CaO和CSZ熔炼后的合金内Ca元素分别为0.0010%和0.0008%,其Ca含量相近,可见CaO的稳定性高于MgO的稳定性,熔炼过程不易分解。Y2O3虽然是最稳定的耐火材料,但是合金内的Y含量达到0.0150%,Y-PSZ熔炼后的合金的Y含量低于0.0010%,由此可知合金内Y含量的升高是由Y2O3坩埚分解导致。Y2O3用于熔炼钛合金时[53],界面处同样存在Y2O3分解现象。虽然镍基高温合金活性远低于钛合金,但是从合金内的杂质元素来看,Y2O3分解的现象依然存在[54]。
图18为不同氧化物的标准生成Gibbs自由能(ΔGθ )随温度的变化趋势[55]。在1600℃时氧化物的稳定性顺序为:Y2O3 > CaO > TiO > ZrO2 > Al2O3 > MgO。氧化物的稳定性代表其金属元素与O亲和能力的强弱。从图中初步判断,Al2O3的ΔGθ 与MgO和ZrO2接近,和CaO和Y2O3的距离较远,理论上仅MgO可以与熔体中Al元素发生置换反应。由于元素Al溶解于活性较低的镍液中,Al元素的活性势必会降低[56],因此Al2O3的ΔGθ 随温度变化的直线将向上移动,这导致熔体中Al更难以与这几种氧化物发生反应。
图18
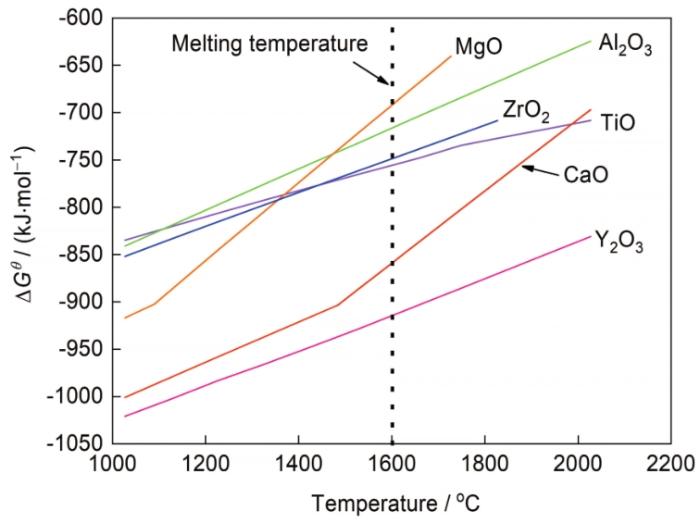
图18 氧化物耐火材料的标准生成Gibbs自由能(ΔGθ )与温度的关系
Fig.18 Relationships between the formation Gibbs free energy (ΔGθ ) of various oxide materials and temperatures
但是,实际熔体和几种坩埚均存在不同程度的交互作用,分析可能是如下原因导致:高温下坩埚材料发生分解反应,即使热力学最稳定的Y2O3坩埚熔炼K417G合金,熔体中也发现高达0.0150%Y含量,坩埚分解反应的O进入熔体,与熔体中Al元素反应生成Al2O3,而Al2O3则易与CaO、MgO、ZrO2以及Y2O3发生化合反应,化合反应的难易程度不同,导致坩埚/熔体界面反应层厚度不同,反应产物的体积变化以及与熔体润湿性不同则会导致出现不同界面反应层形貌。
3 结论
(1) K417G合金中的活性元素Al是导致熔体/坩埚界面反应发生的主要原因。
(2) Al2O3坩埚与K417G合金之间交互作用主要为物理侵蚀,合金中的微量Ca元素降低了Al2O3坩埚的耐侵蚀性,导致Al2O3夹杂卷入熔体中。
(3) CaO坩埚与合金界面清晰完整,熔体中元素Al容易与CaO耐火材料形成低熔点物质Ca3Al2O6,熔体中O含量没有增加,且熔体未发现氧化物夹杂,可见CaO耐火材料有很强的吸附Al2O3夹杂的能力,更适于熔炼高铝钛含量的镍基高温合金。
(4) MgO坩埚界面处生成了MgAl2O4,这与熔体中Al与MgO发生置换反应相关,熔炼后的合金杂质O含量高达0.0135%,且在熔体内部发现夹杂物。
(5) CaO完全稳定的ZrO2坩埚不适合熔炼Al含量较高的镍基高温合金,主要由于CaZrO3的生成伴随着体积膨胀导致熔体Al渗透进入坩埚较为严重,使稳定剂CaO向晶粒间移动与元素Al形成CaAl2O4液相,导致CSZ失稳并促使坩埚材料加速向合金内分解和剥落,引起合金内Zr元素含量增加。相比之下,Y-PSZ具有较强的抗铝渣性能且熔炼后的合金内O杂质含量为0.0008%,并未出现明显的增氧。
(6) Y2O3坩埚与K417G熔体界面清晰,仅存在薄的Al2Y4O9反应层,但在合金内部发现Y元素存在,其含量达到0.0150%,并在局部富集,推测与Y2O3分解相关。
来源--金属学报