分享:纳米金属层状材料强塑性的界面调控
1.
2.
3.
纳米金属层状材料具有优异的力学性能、抗辐照损伤性能和热稳定性,在诸多领域有着广阔的应用前景。但强度的上升往往伴随着塑性的降低,如何有效地平衡层状材料强度与塑性之间的矛盾,仍是目前层状材料界面设计的巨大挑战。当层厚减小至纳米尺度,界面所占比重大幅上升,可动位错的密度急剧降低,界面成为塑性变形的源头。因此研究界面结构与其塑性变形行为之间的关系,是理解纳米层状金属材料微观变形机制及其对力学性能影响的关键。结合目前国内外纳米金属层状材料研究的最新进展,本文以常见层状材料体系为例,系统阐述了界面强化机制、界面结构、界面主导的强度及塑性变形行为和主要界面调控方法等关键科学问题,并对层状材料界面研究发展趋势进行了展望。
关键词:
在金属材料内部,当晶粒尺寸减小到纳米级别,相邻晶界(GB)间距也随之降低到纳米尺度,材料强度显著提高[1,2],产生明显的“尺寸效应”[3~8]。因此,对于包含丰富界面的纳米材料来说,界面对材料性能的影响将由“辅助作用”变成“主导作用”[5]。然而界面在提升材料强度的同时也往往引起应力集中,诱发裂纹,导致材料失效。尤其是在极端应用条件下,界面的快速迁移、辐照缺陷在界面上的富集、界面软化或脆化都会导致材料性能急速下降[9~12]。因此,界面调控是获得性能优异的纳米材料的重要途径。
纳米金属层状材料是由层厚在纳米尺度的不同成分金属交替排列而制成的复合材料。由于这种层状结构可以引入大尺度的平坦界面,使得层状材料常作为研究界面的理想模型材料,为科研人员深入理解界面取向、界面结构和界面成分等界面特征对材料宏观性能的影响提供理论基础。此外,纳米金属层状材料还具有许多出色的性能,如优异的强度[13~16]、热稳定性[15~19]、抗冲击性能[20~22]和抗辐照损伤能力[23~27],使得其在核电、航空航天等领域具有广阔的应用前景。目前纳米金属层状材料的研究体系主要以铜基为主:如Cu/Nb[28,29]、Cu/Ag[30~32]、Cu/Ni[33~36]、Cu/Ta[37]、Cu/Zr[38~40]等。实验上一般利用近热力学平衡法或非热力学平衡法制备层状复合材料,常见如物理气相沉积(PVD)[41~43]、熔炼法[44,45]和累积叠轧(ARB)[46~52]等。高分辨透射电镜(HRTEM)等表征手段是解析界面结构的主要研究方法。但利用HRTEM只能得到原子尺度界面投影和晶体取向,不能直接观察到界面所在平面内的原子结构,因此分子动力学模拟(MD)常作为补充手段为人们提供实验无法直接得到的界面信息与变形机制。
层状材料力学性能优异,但具有强烈的尺寸效应,组元与层厚的改变会影响层内的位错形核、运动和湮灭,进而影响材料的力学性能。如图1[29,32,38,48]所示,不同组元、不同层厚的层状材料其力学性能表现可能截然不同。关于纳米金属层状材料具有优异力学性能的原因, Misra等[13]系统研究了金属层状材料层厚对力学性能的影响,合理地解释了界面主导的强化行为,并根据不同层厚范围提出了相应的位错机制。此外,目前已知的异质界面主导的强度和塑性变形行为主要有:① 阻碍位错运动;② 促进位错形核;③ 承担剪切塑性流变;④ 调控形变孪晶形核。提高界面的力学性能就可以相应提高材料的力学性能,因此通过界面工程可以设计出具有优异力学性能的金属材料。在界面设计时,具体可以利用几何调控、化学成分调控和多组元调控等手段调整界面结构以实现材料宏观力学性能的提高。
图1
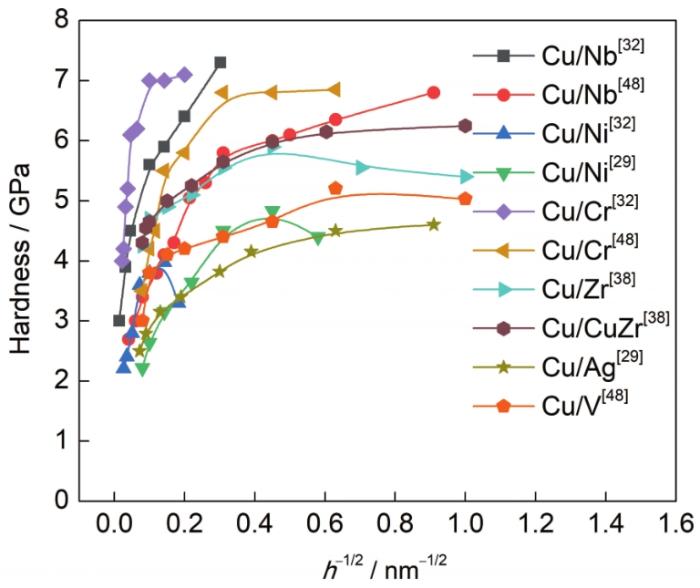
图1 不同组元层状材料硬度与单层厚度的关系[29,32,38,48]
Fig.1 Relationship between hardness and the layer thickness for different multilayer systems (h—individual layer thickness)[29,32,38,48]
本文围绕纳米金属层状材料,分别阐述层状材料强化机制、常见体系界面结构、界面主导的强度和塑性变形行为等相关结果,并概括了目前界面调控手段及其内在机制,最后针对研究现状提出展望,以期为通过界面结构设计实现材料性能调控提供研究思路。
1 层状材料强化机制
Misra等[13]系统研究了铜基纳米层状材料尺度对力学性能的影响,提出了如图2[13]所示的不同层厚下层状材料强度的位错机制。
图2

图2 不同层厚下层状材料强度的位错机制示意图[13]
Fig.2 Schematic illustration of the dislocation mechanisms in metallic multilayer strength at different length scales (σ—strength, b—Burgers vector)[13]
1.1 位错界面塞积机制
在单层厚度
1.2 位错约束层滑移(CLS)机制
随着层状材料层厚继续减小至几十纳米,层内存储的位错数目已经显著减少,导致位错塞积作用的减弱甚至不能形成塞积,此时Hall-Petch关系不再适用[55,56]。Misra等[13]提出约束层滑移机制,来解释在此尺度下的强化机制:作用在位错上的应力不足以使位错穿过界面,单根位错被界面钉扎并沿平行于界面的方向弓出滑移。此时层状材料的屈服应力σcls可以表示为[12]:
式中,
1.3 位错界面穿过机制
当
2 常见体系界面结构
首先根据界面两侧原子的排布吻合程度可以将界面分为共格界面、半共格界面以及非共格界面。定义晶格错配度
式中,
2.1 物理气相沉积法制备的界面
物理气相沉积法能精确控制各个层的厚度,还可以实现结构和成分的精确控制,但是此方法只能制备微米级厚度的层状材料,不能批量生产块状材料。根据界面组元的晶体结构可以分为fcc/bcc、fcc/fcc、fcc/hcp和hcp/bcc等几类界面。
2.1.1 fcc/bcc界面
Li等[57]通过物理气相沉积法,制备了Cu/Nb纳米层状材料。通过HRTEM表征后发现组成界面的两晶体学面均为能量最低的密排面,即Cu{111}//{110}Nb。图3a[57]给出了该界面的HRTEM像。可以看到物理气相沉积法制备的Cu/Nb纳米层状材料中的界面可以同时存在2种取向关系:① Kurdjumov-Sachs (K-S)取向关系,此时两晶体的密排方向相互平行,即Cu<110>//<111>Nb,结合界面取向后可以标记为Cu{111}<110>//{110}<111>Nb,如图3b[57]所示;② Nishiyama-Wasserman (N-W)取向关系,即Cu<110>//<100>Nb,结合界面取向后可以标记为Cu{111}<110>//{110}<100>Nb,如图3c[57]所示。
图3
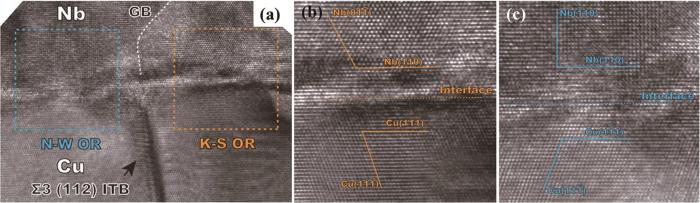
图3 物理气相沉积(PVD)法制备的Cu{111}//{110}Nb界面HRTEM像[57]
Fig.3 Cross-sectional HRTEM images of PVD Cu{111}//{110}Nb interface (PVD—physical vapor deposition, GB—grain boundary, ITB—incoherent twin boundary, OR—orientation relationship)[57]
(a) microstructure of Cu/Nb interface (b) K-S orientation relationship (c) N-W orientation relationship
通过HRTEM只能得到界面截面方向的原子排布,却不能直接观察到二维界面的原子信息,利用MD模拟可以得到实验手段无法得到的界面结构信息。Beyerlein等[61]通过MD模拟并结合Frank-Bilby理论[62],得到了K-S及N-W 2种取向的Cu{111}//{110}Nb界面原子结构并分析了其错配位错组态,如图4[61]所示,图中实线代表错配位错线。由图4a[61]可知,K-S界面内存在2组错配位错,一组位错线平行于y轴方向,位错线间距约为1.25 nm,实际Burgers矢量为(-0.25, -0.16, 0.00) nm;另一组位错线与x轴方向呈约28°角,位错线间隔约为2.13 nm,实际Burgers矢量为(0.00, 0.27, 0.00) nm。对于N-W界面(图4b[61]),其错配位错组态十分复杂,共存在7组错配位错,在此不作具体展开。通过对界面的结构分析可知,2种取向的界面角度仅仅相差约5.26°,即将其中某一取向晶体绕垂直于界面的z轴旋转5.26°即可实现2种界面结构的转变。
图4
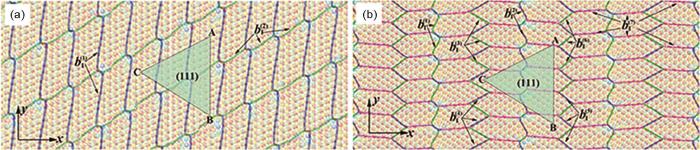
图4 Cu{111}//{110}Nb界面弛豫后的错配位错结构[61]
Fig.4 Relaxed misfit dislocation structures of Cu{111}//{110}Nb interface[61] ( b1—Burgers vector)
(a) K-S orientation (b) N-W orientation
2.1.2 fcc/fcc界面
Misra等[33]通过物理气相沉积法制备了Cu/Ni纳米多层膜,其所含界面的晶体学特征与上述Cu/Nb界面存在较大差异。组成界面的晶体学面为各自非密排{100}面,且其晶体取向为立方-立方(cube-on-cube)关系,即上下两晶体中相同的晶向是平行的,如Cu[110]//[110]Ni。且Misra等[33]观察到错配位错的存在,其为刃型全位错,Burgers矢量为
此外Cu/Ni纳米多层膜中还存在另外一种更为常见的界面特征,Zhu等[34]利用物理气相沉积法制备了Cu/Ni纳米层状材料,如图5[34]所示。Cu/Ni层状材料界面的晶体学面同样为各自密排面{111},即Cu{111}//{111}Ni;且其晶体取向关系既可以是立方-立方,如Cu[
图5
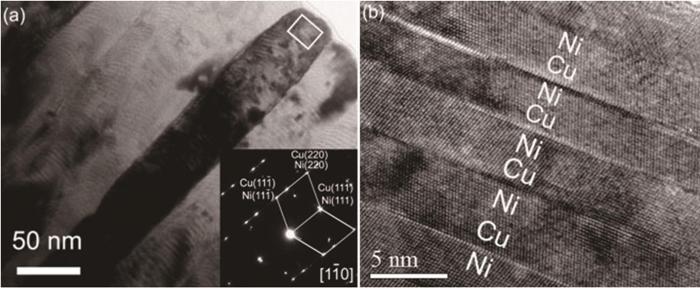
图5 Cu{111}//{111}Ni界面特征[34]
Fig.5 Schematics of Cu{111}//{111}Ni interface characteristics[34]
(a) TEM image of interface and SAED pattern (inset) (b) cross-sectional HRTEM image
同样,可以利用MD模拟观察到Cu/Ni界面的原子结构信息。Shao等[63,64]通过MD计算得到了弛豫后Cu{111}//{111}Ni界面的原子势能分布与位错组态,如图6[63]所示。其弛豫后的界面结构如图6a[63]所示,界面大致可以分为近fcc区、近hcp区、位错节点区和位错线区4个区域。节点位于位错线交点处,具有最高的势能,漩涡状的位错线把近fcc区和近hcp区分隔开。Shao等[63]通过错合度分析得到,Cu/Ni界面上存在着3组错配位错,它们的Burgers矢量分别为
图6
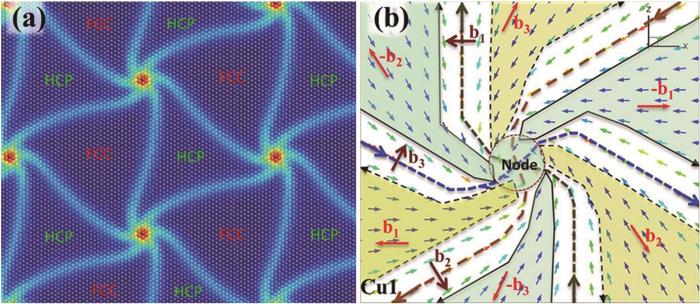
图6 弛豫后的Cu{111}//{111}Ni界面[63]
Fig.6 Relaxed Cu{111}//{111}Ni interface[63]
(a) atomistic structure (b) misfit dislocation structure ( bi —Burgers vector)
2.1.3 fcc/hcp界面
Zhang等[65]在室温下利用磁控溅射制备了Cu/Zr纳米层状材料,如图7a[65]所示。对于fcc/hcp的界面结构,通过电子衍射图谱和TEM表征得到了界面晶体取向仍为各自密排面,即Cu{111}//{0001}Zr;其常见晶体取向为Cu<110>//<1120>Zr。Xiao等[66]利用MD模拟得到了弛豫后Cu{111}//{0001}Zr界面的原子位错组态信息,如图7b[66]所示,界面同样可以分为近fcc区、近hcp区、位错节点区和位错线区4个区域。其界面错配位错也存在着3组错配位错,它们的实际Burgers矢量分别为
图7
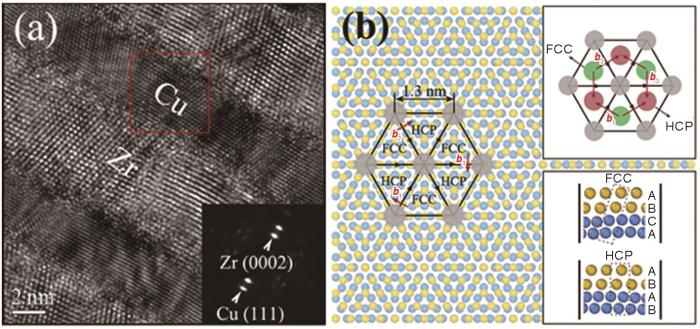
图7 Cu{111}//{0001}Zr界面特征[65,66]
Fig.7 Schematics of Cu{111}//{0001}Zr interface characteristics
(a) bright-field cross-sectional TEM micrograph[65]
(b) top views of atomistic structure of the Cu/Zr interface[66]
2.1.4 hcp/bcc界面
Chen等[67]利用磁控溅射沉积了层厚为50 nm的hcp-Mg/Nb层状复合材料。利用TEM分析得到了其界面晶体取向为Mg(0001)//{110}Nb,并采用选区衍射分析得到了Mg/Nb界面存在2种晶体取向关系,分别为Mg[
图8
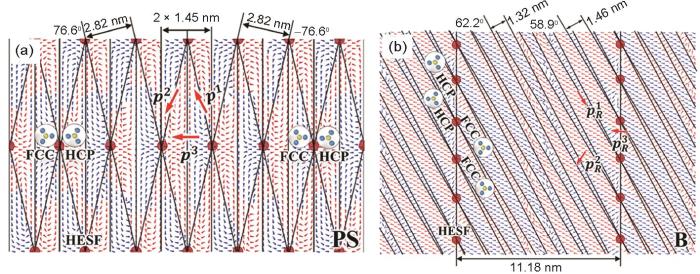
图8 Mg{0001}//{110}Nb界面PS和B取向界面位错组态[68]
Fig.8 The interface dislocation patterns of the Mg{0001}//{110}Nb of PS (a) and B (b) interfaces[68] ( pi,
2.2 熔炼法制备的界面
Zheng等[44,45]通过熔炼法制备了Cu/Ag共晶纳米层状复合材料,同样获得了原子尺度平坦界面,截面形貌如图9a[44]所示。由于同样是近热力学平衡条件下所制备的层状材料,其界面晶体学特征与Cu/Ni界面类似,均为各自密排面,即Cu{111}//{111}Ag,材料中同样可以存在2种取向关系:立方-立方取向关系,如Cu[
图9

图9 Cu{111}//{111}Ag界面[44]
Fig.9 Cross-sectional view of Cu{111}//{111}Ag interface[44]
(a) bright-field TEM micrograph
(b) HRTEM image of cube-on-cube interface
(c) HRTEM image of hetero-twin interface
由上文可知,对于利用近热力学平衡技术制备层状材料来说,产生的界面结构往往产生对应着低界面形成能的界面特征。表1对上述常见界面结构的晶体学平面和取向进行了汇总。
表1 不同体系层状材料界面结构对比
Table 1
System | Crystal structure | Lattice mismatch / % | Orientation relationship | Dislocation type | |
---|---|---|---|---|---|
Cu/Nb | fcc/bcc | 11.1 | Cu{111}//{110}Nb | Cu〈110〉//〈111〉Nb | 2 |
Cu{111}//{110}Nb | Cu〈110〉//〈100〉Nb | 7 | |||
Cu/Ni | fcc/fcc | 2.7 | Cu{001}//{001}Ni |
Cu |
1 |
Cu{111}//{111}Ni |
Cu |
3 | |||
Cu{111}//{111}Ni |
Cu |
3 | |||
Cu/Ag | fcc/fcc | 12.3 | Cu{111}//{111}Ag |
Cu |
3 |
Cu{111}//{111}Ag |
Cu |
3 | |||
Cu/Zr | fcc/hcp | 20.7 | Cu{111}//{0001}Zr |
Cu |
3 |
Mg/Nb | hcp/bcc | 11.1 | Mg{0001}//{110}Nb |
Mg |
3 |
Mg{0001}//{110}Nb |
Mg |
3 |
2.3 累积叠轧法制备的界面
累计叠轧法是先将经表面处理后2种金属片层堆叠起来,然后经过轧制、截断、再堆叠、再轧制,中间有时会进行热处理以消除内应力,如此往复[70]。累积叠轧法制备层状材料工艺简单且效率很高,可以批量制备块状材料。由于此种方法会引入严重塑性变形,是一种非热力学平衡的方法,因此会产生一系列织构以及高能界面。Zheng等[71]发现,通过改变轧制的方向可以得到不同的界面结构:① 保持轧制方向不变的定向轧制(LR-ARB),最终界面结构如图10a[71]所示。界面存在许多规则排列的小刻面,可以将其界面形状称为锯齿状,锯齿高度约为5~6个原子,界面取向为Cu{112}<111>//{112}<110>Nb;② 每次轧制过后旋转90°再进行轧制的交叉轧制(CR-ARB),最终界面结构如图10b[71]所示。界面为平直状,界面取向为Cu{110}<111>//{001}<110>Nb。
图10
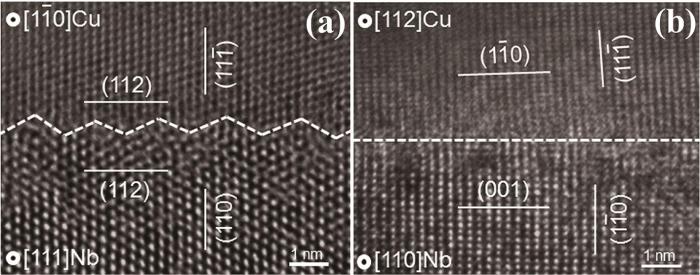
图10 累积叠轧(ARB)法制备的Cu/Nb界面[71]
Fig.10 Schematic diagrams of Cu/Nb interface by accumulative roll bonding (ARB) process[71]
(a) LR-ARB (LR—longitudinally rolled) (b) CR-ARB (CR—cross-rolled)
3 界面主导的强度和塑性变形行为
纳米金属层状材料最重要的结构特征是存在着大量的异质界面,这些界面主导材料的强度和塑性变形行为,并决定着层状材料的力学性能。结构材料在受到应变后可以通过多种塑性变形行为来协调变形,如位错运动、界面滑移、孪生、相变[72]等行为释放材料内部应力。因此,本节将从位错、孪晶和界面的交互作用角度来阐述界面所主导的变形机理。
3.1 阻碍位错运动
已知金属中的晶界和相界在决定材料特性方面发挥着重要作用,例如强度、塑性和加工硬化。在外加应力下,晶粒中产生的位错将不断穿过晶格直到遇到晶界,随着越来越多位错传播到晶界,由于位错无法移动穿过晶界而产生位错塞积[73~75]。而对于界面具体阻碍位错运动作用的原因,主要有以下几个方面:① 晶界两侧金属固有属性不同,如组元晶体类型、晶体取向以及滑移系统不同,位错穿过需要更多的能量;② 晶界比晶粒内部原子结构或缺陷结构更无序,这阻止了位错在连续滑移平面中移动;③ 晶内滑动位错与界面错配位错应力场之间的弹性交互作用,从而对滑动位错产生排斥效果;④ 晶内滑动位错与界面交互后的位错核心在界面处扩展,从而无法穿过界面。
由于界面位错交互的复杂性,实验中很难直接观察到界面与位错交互时的位错反应,因此一般采用MD模拟的方法进行研究。Wang[76]通过MD模拟研究了Al内Σ11非对称倾转晶界与晶内滑动位错的交互作用,提出了界面与位错反应可能发生的几种动力学交互模式(图11[76]):位错穿过、位错滑移、位错反射、位错攀移。这些过程可能单独发生或耦合发生,导致产生许多不同的变形模式。并且Wang[76]指出,这些交互过程在很大程度上取决于跨越晶界的2个晶粒中滑移系统的连续性、晶界的原子结构、应力状态、温度等。
图11
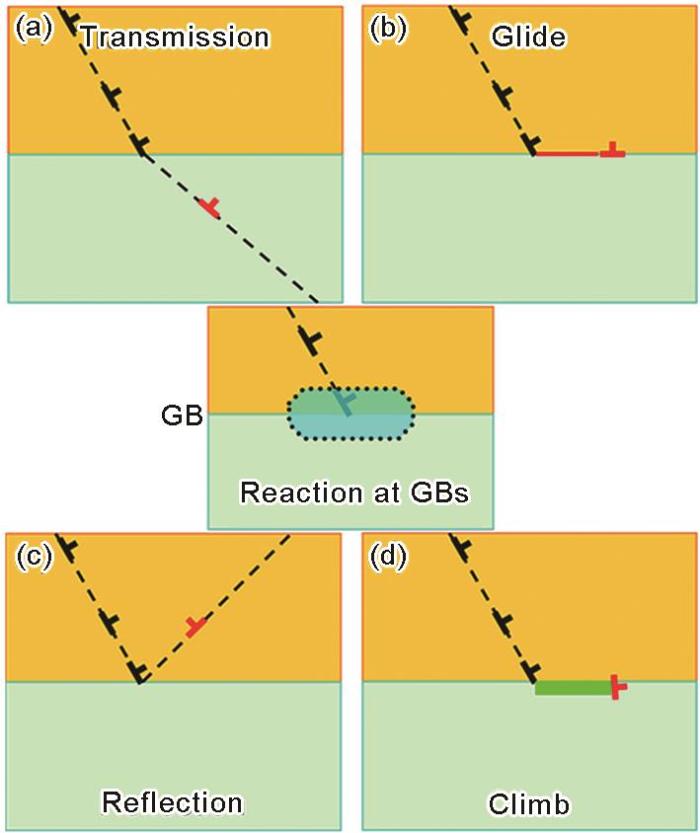
图11 位错-晶界交互作用的4种交互模式[76]
Fig.11 Four reaction modes of dislocation-GB interactions[76]
(a) transmission (b) glide
(c) reflection (d) climb
3.2 位错从界面形核
众所周知,晶界、表面和异质界面是位错的潜在来源。对于粗晶材料,晶粒内部包含充足的位错来源。然而,对于纳米材料,由于晶内位错源受到抑制,界面可能是位错的主要来源[77,78]。最近,MD模拟被广泛用于研究异质界面的位错形核,并建立了位错形核与异质界面结构尤其是错配位错结构之间的联系。
Zhang等[79,80]对Cu{111}//{110}Nb的K-S界面沿不同方向施加正应变加载,以促使点阵位错形核。结果表明,点阵位错形核的位置并非随机的,而是与界面错配位错结构密切相关,如图12a和b[79]所示。通过对界面原子的相对位移矢量(图12c[79])研究表明,界面沿着错配位错线两侧均存在着密集的相对剪切,从而诱导位错沿着位错线形核。随后Beyerlein等[81]对Cu{111}//{110}Nb的N-W界面的研究同样证实了界面错配位错结构与位错形核的相关性,但其产生位错的滑移系统与K-S界面有所不同。位错只在K-S界面的一个滑移系统上形核,而在N-W界面上有2个滑移系统均可形核。对于2种界面位错形核的不同表现,Beyerlein等[81]认为这与错配位错的几何形貌相关,预示着界面结构的轻微变化也必然会影响后续的力学性能。更进一步说明可以通过调制界面形态来调制点阵位错的类型、形核的数目甚至变形的方式,从而实现对层状材料塑性变形行为的调控。为了进一步研究界面结构如何影响滑移系的激活过程,Mara和Beyerlein[82]通过Cu/Nb系列界面的形核特征进行归纳拓展,并提出以下结论:① 错配位错的存在导致了界面错配位错处的局部剪切,是位错的优先形核位置;但是只有当晶体的滑移面与界面的交线(迹线)平行于错配位错线时,形核才容易发生并在滑移面上向晶体内部滑移;② 若2者偏离角度在一定范围内(通常小于10°),形核也能发生,但需要更大的驱动力;③ 当2者偏离角度较大时,相邻错配位错可能会反应产生一段新的位错平行于迹线,点阵位错沿着新位错形核,当位错反应不能发生时,点阵位错于错配位错的交点处形核,并扩展至准共格区,并向晶体内部滑移,此时位错形核最为困难。这解释了为什么K-S和N-W界面在相同加载条件下激活的滑动系统不同。K-S界面只有一个错配位错与最大Schmid因子滑移系统对齐,而N-W界面有2个错配位错与2个最大Schmid因子滑动系统对齐。
图12
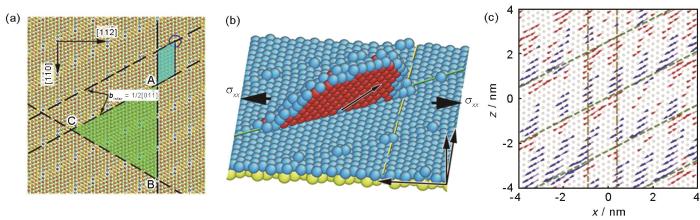
图12 K-S取向Cu{111}//{110}Nb界面对应的位错形核特征[79]
Fig.12 Dislocation nucleation characteristics of Cu{111}//{110}Nb K-S interface[79]
(a) structure of interface misfit dislocation ( binter—interface Burgers vector)
(b) a dislocation loop is nucleated into Cu from the interface (σxx —strain tensor in xx-direction)
(c) relative displacement vector of interface atoms
3.3 承担剪切滑动的塑性流变
已知对于抗剪切能力比较弱的界面,界面内滑动位错的核心很容易在界面上扩展,意味着位错被界面吸收从而无法穿过界面。这表明位错滑移穿越界面的能垒取决于界面平面中位错核心的扩展程度,而后者又取决于界面的剪切阻力[83],并且对于剪切加载,界面承担着剪切滑动塑性流变的关键角色。目前通过近热力学平衡方法所制得的纳米金属层状材料中,构成异质界面的2种金属的晶体学面倾向于是密排面,即晶体的滑移面,一般具有较低的剪切强度。由于存在晶格错配,界面内会形成若干错配位错,在外加切应力作用下,错配位错可以直接滑移也可以通过界面产生相对滑动而承担塑性变形[84]。对于非热力学平衡方法所制备的异质界面,其组成界面通常为非密排面,部分错配位错具有指向面外的Burgers矢量。在切应力作用下,错配位错会直接向晶体内部滑移。以上情况虽然有利于材料的塑性变形,但均不利于层状材料强度的提高。
目前针对剪切研究的主要目的是建立界面剪切强度与界面原子结构的对应关系。Wang等[84]运用MD模拟,对2种具有不同Cu原子面密度的K-S Cu{111}//{110}Nb界面的剪切强度及滑移机理进行了系统的研究。发现:① Cu/Nb界面的剪切强度远低于完美单晶的理论剪切强度;② 其界面剪切强度有着强烈的各向异性;③ 空间上的不均匀性;④ 强烈依赖于界面的原子结构。随后Demkowicz和Thilly[85]对ARB方法制备的Cu{112}//{112}Nb界面的剪切强度进行了研究。与Cu{111}//{110}Nb界面类似,{112}界面也显示出剪切的各向异性。但由于此界面具有锯齿状的小刻面,因此具有极高的抗剪切强度,沿着特定方向剪切,即使切应力达到4500 MPa界面滑移也不会发生。而在剪切过程中,具有指向面外Burgers矢量的错配位错会向Cu晶体内部滑移。在另一些方向剪切,界面在大约1200 MPa下发生滑移,其过程也显示出明显的空间不均匀性,薄弱的错配位错节点附近首先发生滑动。除Cu/Nb界面外,Chen等[69]对具有立方-立方取向关系的Cu{111}//{111}Ni和Cu{111}//{111}Ag界面进行剪切加载后发现,在切应力下界面内的错配位错会直接进行滑移,从而承担塑性变形。图13[69]展示了Cu/Ni界面沿
图13
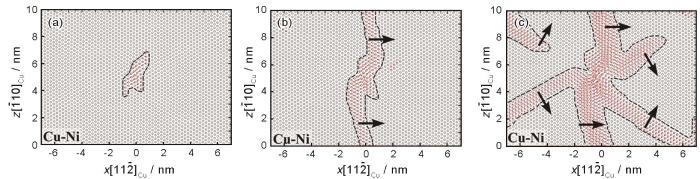
图13 Cu{111}//{111}Ni界面在剪切下的错合度分析图[69]
Fig.13 Disregistry vector plots of the Cu{111}//{111}Ni interface under shearing[69]
(a) initial stage (b) middle stage (c) expand stage
3.4 孪生承载应变
除了滑移外,fcc金属还可以通过孪生来承载应变。孪晶界作为典型的共格界面在调控材料性能方面发挥了重要作用,孪晶界不但具有界面能低、电阻率低的优点,还能在一定程度上阻碍位错运动,并与位错反应促发位错增殖,且塑性变形可逆,从而实现高强度、高塑性、高热稳定性、耐疲劳[86~88]。
与纯fcc金属的孪生相比,虽然关于双金属界面结构对材料孪生的影响还没有系统的研究,但也取得了可喜的进展。当利用ARB方法制备的Cu/Nb层状材料被轧制成层厚低于60 nm时,Cu层开始产生孪晶[89]。而用PVD方法制备的层厚75 nm的Cu/Nb层状材料直至被轧制到40 nm时仍没有观察到孪晶[90]。除轧制外,在其他应变状态下,如拉伸[91~93]、压缩[94]和剪切[95]后,同样没有观察到孪晶。在纳米材料中,孪晶主要源自晶界或双金属界面。ARB方法制备的材料界面主要是Cu{112}<111>//{112}<110>Nb锯齿状界面;而PVD方法制备的材料界面主要是Cu{111}<110>//{110}<111>Nb平界面。因此,2种不同制备方法制备的层状材料中产生孪晶的差异主要是由于它们界面结构不同。
Han等[96]在实验中提供了界面结构影响孪生的另一有力证据。Han等[96]利用PVD方法制备了Cu/Nb样品,并对其进行了冲击加载,图14a[96]展示了冲击加载后的Cu/Nb样品界面TEM像。可以明显看出,中心的界面区域形成了孪晶(图14c[96]),而左侧的界面没有产生孪晶。与孪晶区域对应的界面是Cu{112}<111>//{112}<110>Nb界面(图14d[96]),而未产生孪晶的界面是Cu{111}<110>//{110}<111>Nb界面(图14b[96])。Mara和Beyerlein[82]根据这一线索概括了抑制/促进孪生的界面特性,提出了2种与界面结构相关的位错发射机制:① 位错从一个相穿越到另一个相(T机制);② 在外加载荷作用下界面发射位错(D机制)。通过位错理论以及MD模拟,Han等[96]研究了这2种机制与界面结构之间的关系。结果表明,对于Cu{112}//{112}Nb界面,机制T和机制D都是可能发生的。具有许多小刻面的Cu{112}//{112}Nb界面存在许多可以分解成孪生位错的位错组态,一方面孪生位错可以直接从此界面发射出去,另一方面该界面对位错穿越的阻碍较小,位错可以从Nb侧进入界面并传递到Cu内。而对于平直的Cu{111}<110>//{110}<111>Nb界面,2种机制都很难发生。
图14
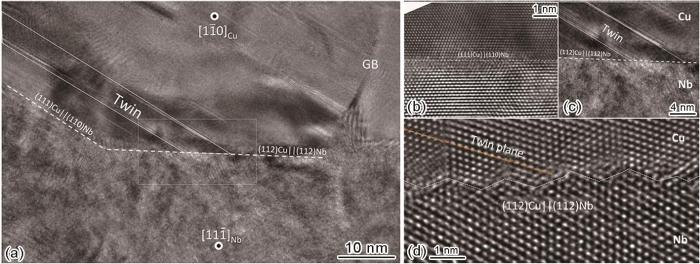
图14 冲击加载后的PVD Cu/Nb界面HRTEM像[96]
Fig.14 HRTEM images of PVD Cu/Nb interface after shock loading[96]
(a) cross-sectional micrograph
(b) Cu{111}<110>//{110}<111>Nb interface
(c) higher magnification of a typical twin
(d) Cu{112}<111>//{112}<110>Nb interface
4 界面调控方法
界面对纳米复合材料的塑性变形和力学行为起着极其重要的作用。目前针对界面结构对孪生影响的研究还不够深入,界面研究主要集中在界面主导的界面位错形核和剪切下的界面滑动2种塑性变形机理研究,而强化行为主要由界面对位错运动的阻碍来实现。并且这些塑性机制都与界面上的各种缺陷特征密切相关。在拉伸/压缩加载下,这些界面缺陷可以作为位错的形核源,且这种界面上位错的形核和发射通常决定了纳米层状材料的主要塑性机制[81]。而在剪切加载下,界面相对滑动将对塑性变形起主导作用,并且由于界面缺陷的存在,界面剪切阻力存在显著的各向异性[84]。根据上述强度和塑性机制可知,提高强度的主要途径有:① 提高界面处位错形核的阻力,即提高位错形核能垒;② 提高界面发生剪切滑移的阻力,即提高剪切强度;③ 提高界面对位错穿越的阻碍作用,即提高位错穿越能垒。为实现界面强化,目前界面调控手段主要分为几何调控、化学成分调控和多组元调控3种。
4.1 几何调控
目前研究已经证明了位错可以从平坦的K-S Cu{111}//{110}Nb界面形核,但必须克服相对较高形核能垒,因为所有界面错配位错都具有面内的Burgers矢量[79,80]。相比之下,锯齿状的Cu{112}//{112}Nb界面由于存在面外的Burgers矢量,位错形核的能垒要低很多[81]。由3.3节可知,Cu{112}//{112}Nb界面比Cu{111}//{110}Nb界面有更高的剪切阻力。不同的界面几何形态可以对材料性能产生显著影响,由此可知,界面几何调控具有强化材料性能的可行性。但一般界面难以做到“位错形核”和“剪切滑动”之间的塑性平衡,因此可以通过几何调控对界面进行设计以期待同时提高形核能垒和剪切阻力。
Zhang等[97]在低能、平坦的K-S Cu{111}//{110}Nb界面引入了适当的原子台阶,在不降低形核能垒的前提下,实现了剪切阻力的提高。Zhang等[97]在Cu/Nb纳米层状材料中观察到存在这种原子台阶的界面并由此受到启发,设计了多种类型的阶梯状K-S Cu/Nb界面,如图15[97]所示。相较于平直的K-S Cu{111}//{110}Nb界面,添加原子台阶只会略微增加界面能(8.1%)。这种阶梯状界面同样具有密排且阶段平直的Cu/Nb界面,同时在“台阶”拐角处存在的较大空间可以缓解局部应变,所以“台阶”的存在并未导致位错形核能垒的降低,与平坦的Cu{111}//{110}Nb界面具有相当的位错形核垒。此外,由于原子台阶引起的界面不连续性,在剪切应力作用下在界面处发射位错或形成孪晶,应力得以释放,因此阶梯状的结构对界面滑动具有更大的抵抗力,这与锯齿状Cu{112}//{112}Nb界面类似。通过把平坦界面高位错形核能垒和锯齿界面高滑动阻力的优势结合起来,实现了材料性能的提高。
图15
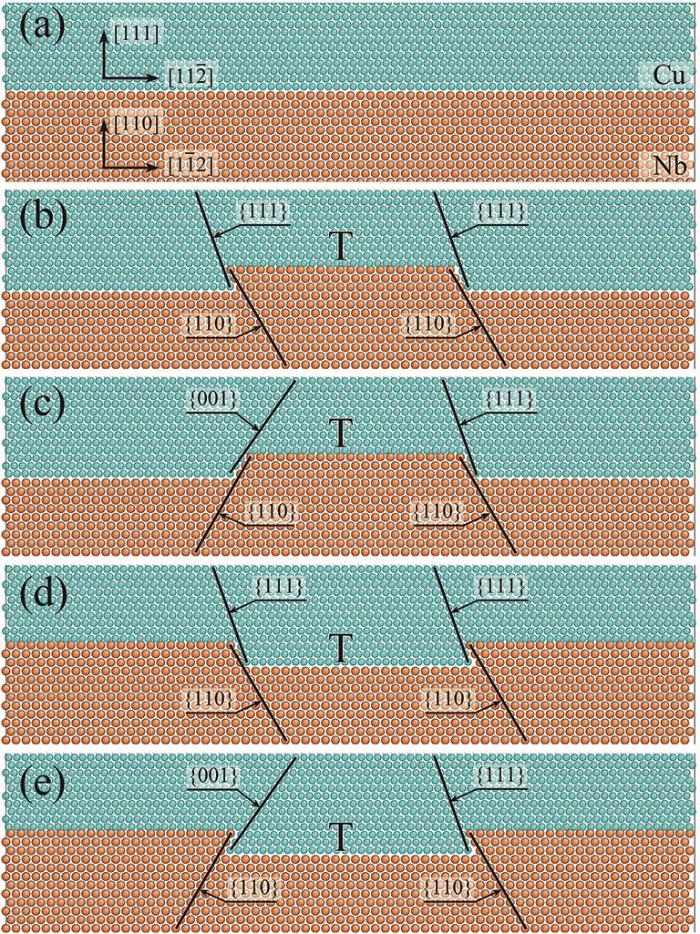
图15 包含原子台阶的K-S Cu{111}//{110}Nb界面模型[97]
Fig.15 Side views of K-S Cu{111}//{110}Nb interface models with the atomic steps[97]
(a) flat interface
(b) interface with terrace inside Cu consisting of two Cu{111}//{110}Nb facets on each side
(c) interface with terrace inside Cu consisting of one Cu{001}//{110}Nb facet (left) and one Cu{111}//{110}Nb facet (right)
(d) interface with terrace inside Nb consisting of two Cu{111}//{110}Nb facets on each side
(e) interface with terrace inside Nb consisting of one Cu{001}//{110}Nb facet (left) and one Cu{111}//{110}Nb facet (right)
对于相对高能态的非密排界面,如Cu{112}//{112}Nb界面,其位错形核能垒较低,在较小的外加应力下便会形核,但其错配位错不容易在界面内滑移,剪切强度较高。Kong等[98]研究发现,在某些高能、非密排界面制备加工过程中,呈现出与其理论上的初始基态不同的锯齿型变体。例如Han等[99]通过累积叠轧法制备了Cu/Nb纳米复合材料,发现当变形量较小时,Cu{112}//{112}Nb界面以其初始基态出现,呈现2~3个原子高度的小锯齿状,而当变形量较大时锯齿的高度相应增高至4~5个原子,但晶面匹配关系保持不变。为了探究这种能够稳定存在的锯齿型变体是否能给界面带来强化效应,Kong等[98]以Cu{110}//{110}Ag及Cu{112}//{112}Nb界面为例,建立了多种锯齿型变体界面,研究了锯齿形貌对界面能和力学行为的影响,并据此提出了锯齿的设计原则:① 构成锯齿的小刻面均为晶体的密排面以降低界面能,增大位错形核能垒;② 锯齿的引入都遵循着原错配位错的周期布局以减轻错配位错引起的应力应变集中;③ 锯齿的尺寸要相对适中,以提供足够的界面滑动抗力的同时不减小位错形核能垒。完全符合上述规则的变体界面,除了同样具有普通锯齿形界面的高剪切阻力外,还具有很高的位错形核能垒。这主要源于上述锯齿的存在不但改变了位错滑移系统的开动情况,还减轻了界面应变局域化程度。
对于几何调控来改变界面形态的方式,非平直的界面一般会提高界面的剪切强度,但通常会以降低位错形核能垒为代价。但这并不是绝对的,可以通过改变引入几何体的密度、大小、形状和位置等变量来合理设计界面结构,使整体具有更高的力学性能。
4.2 化学成分调控
对于化学成分调控,主要方法是引入溶质原子。溶质原子可以显著改善纳米复合材料的整体性能,这主要归因于其对位错运动的钉扎效应[100]。此外溶质的存在可以改变体系的晶格常数和层错能[101,102]。同时在双金属界面处,溶质会在界面处产生偏聚并改变2个体系之间的晶格错配和界面错配位错的分布,从而改变界面处的缺陷结构和应变特征[103,104]。界面缺陷结构和应变特征的改变会影响位错的界面形核能垒,界面滑动阻力以及位错穿越界面的难易程度,最终对材料的性能产生重要影响[105~107]。
Gola等[108]通过将Ag原子掺杂到Cu层内,研究了Ag含量对Cu{111}//{111}Ni界面错配位错密度的影响。研究发现随着Ag含量的增加,界面位错密度会更加密集,层状材料的强度会随之上升,并根据计算结果提出了3种强化机制:① Ag团簇可以钉扎界面位错网络,增加界面抗剪切能力;② 随着Ag的加入,界面错配位错密度的上升会增强位错穿越界面的阻力;③ 位错在节点处形核并反应生成压杆位错,压杆位错又可以充当阻碍位错运动并强化材料的障碍物。Wang等[101]利用MD模拟和Monte Carlo (MC)模拟研究了随机分布的溶质原子对Cu{111}//{111}Ag界面位错形核和界面滑动的影响,通过改变掺杂原子的含量及位置,建立了多个Cu1 - x Ag x //Ag、Cu//Ag1 - x Cu x 界面模型(图16a[101]),结果发现:① 溶质的引入总会改变体系的晶格常数(图16b[101]),同时降低晶体的不稳定堆垛层错能(SFE) (图16c[101]),溶质原子容易在界面处产生偏聚造成界面产生多个局部剪切区,导致位错形核的能垒的降低;② 溶质引入后可以通过形成溶质团簇对界面错配位错产生强烈的钉扎效应,并且改变界面的相对滑动路径,导致界面滑动阻力的上升。
图16
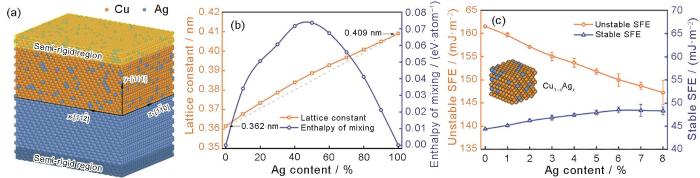
图16 Cu1 - x Ag x//Ag界面模型[101]
Fig.16 Cu1 - x Ag x //Ag bilayer mode[101]
(a) atomic structure
(b) lattice constant and mixing enthalpy corresponding to Ag content
(c) stable and unstable SFE corresponding to Ag content (SFE—stacking fault energy)
对于化学成分调控,溶质原子的存在虽然可以钉扎界面位错,增加界面抗剪切能力,但往往会降低位错形核能垒。因此如何在不降低位错形核能垒的前提下,通过调整掺杂原子的种类、数量、位置及分布状态来提高材料的强度,仍值得深入探索。
4.3 多组元调控
通过引入其他组元,如界面非晶层等,来形成特殊的界面结构,也是调控材料性能的重要途径[109~111]。因此第三组元的引入有可能对位错运动产生额外阻碍效果并产生与二元体系不同的变形行为,从而有效地调控材料性能。Bellou等[112]通过连续磁控溅射在Cu/Nb层状材料之间引入了金属Ni,并通过实验测量了应变硬化行为,结果表明具有相同层厚度的Cu/Ni/Nb三层材料比Cu/Nb的双层材料具有更大的应变硬化能力。Bellou等[112]利用三维位错动力学(DD)进行模拟,并提出了一种交滑移机制来解释这一现象:Ni的引入可以加强材料对位错的存储能力,增加fcc金属层中的位错密度。
近期,Chen等[113]通过线性调制靶材的溅射功率,在Cu层和Nb层之间共溅射CuNb,制备了一种约5 nm厚且存在化学/结构梯度的三维(3D)界面,如图17a和b[113]所示,并利用微柱压缩来研究3D界面的力学性能及变形行为。结果表明,与相同厚度的二维界面的层状材料相比,3D界面分别使屈服强度和流变强度提高了50%和22%。在14%的压缩应变后,开始产生的剪切带导致3D界面变薄,并最终将其转变为锯齿状形态。因此Chen等[113]认为3D界面可以在不损害塑性变形能力的前提下,为设计具有更高强度的材料提供了新机会。随后,Yang等[114]利用PVD法制备了包含极薄(0.5 nm)的CuNb非晶层的Cu/Nb多层材料,如图17c和d[114]所示,发现非晶层的引入可以提高材料硬度。认为这是由于非晶层的存在可以产生大量的自由体积,有助于吸收晶内的可动位错,从而对位错穿越界面产生显著的阻碍作用[114]。此外,Yang等[114]通过MD模拟对这种晶体/非晶的无序界面组态进行了剪切加载,发现非晶的存在还可以极大地提高材料的剪切强度。这是由于无序界面可以有效地分解位错Burgers矢量,这不利于界面位错的滑移。但Xiao等[66]发现晶体/非晶的无序界面由于自由体积的存在很容易在加载后引起位错形核,故此种界面位错形核能垒很低,并导致材料屈服强度的降低。因此,如何在引入非晶层后不降低或少降低位错的形核能垒,值得深入探讨。例如,可以通过调整非晶层的厚度、非晶层的原子组成等方法改善位错形核能垒。
图17
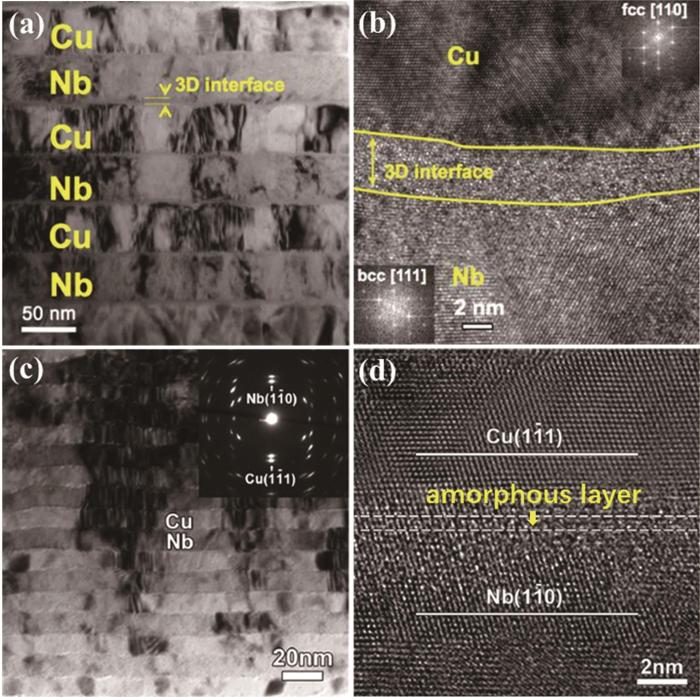
图17 包含3D界面和CuNb非晶层的Cu/Nb层状材料TEM像[113,114]
Fig.17 TEM images (a, c) and HRTEM images showing 3D interface (b) and amorphous layer (d) of Cu/Nb multilayer containning 3D interface[113] (a, b) and CuNb amorphous layer[114] (c, d)
对于多组元调控,其界面结构的可设计性更强,具有很好的研究前景,也是目前的研究热点之一。所引入的界面层可以是金属晶体、非晶或极薄的溶质层,甚至是非金属。人们可以通过改变所引入组元的元素、成分、厚度和分布状态,合理调控界面结构,进一步优化材料性能。
5 总结与展望
本文综述了界面强化机制、常见界面结构、界面主导的强度和塑性变形行为和界面调控方法等相关结果,为合理通过界面工程设计高性能金属材料提供了理论基础,总结如下。
(1) 单层厚度大于100 nm时,材料强度与层厚符合Hall-Petch关系;而单层厚度小于100 nm时,位错运动被限制在层内进行;当单层厚度降至几个纳米时,位错可以穿越界面。
(2) 接近热力学平衡的方法,倾向于产生密排、低能界面;偏离热力学平衡的方法,可以产生非密排、高能界面。特定的制备方法对应着特定的界面结构,而界面特征与力学性能存在紧密关系。
(3) 界面主导的主要强化机制为界面阻碍位错运动。界面主导的主要塑性变形机制为:作为位错源释放位错;界面发生相对滑动而变形;通过界面孪生承载应变。
(4) 实现界面强化的主要途径有:提高位错形核能垒;提高剪切强度;提高界面对位错穿越的阻碍作用。据此提出界面调控手段主要分为几何调控、化学成分调控和多组元调控3种。
界面在纳米金属层状材料的力学性能和塑性变形行为中具有主导作用,因此通过界面工程来优化界面结构是提升纳米金属层状材料性能的重要途径。虽然目前针对金属层状材料界面结构与性能已经做了大量的研究,但是金属层状材料的发展仍存在许多问题。例如,目前调控研究大多局限于层厚作用方面,原子尺度界面结构和成分的精确控制很难实现。而且原子尺度界面结构、成分与界面特征尚缺乏对应关系,界面特征与材料性能之间也未建立系统关联。此外,层状材料虽然具有优异的强度,但塑性不足的问题仍然突出,同时实验上原位观察材料变形时微观结构的演化行为仍存在很大难度。
目前研究的关注热点主要有:① 继续提高层状材料强度与塑性;② 精确调控原子尺度界面结构与成分;③ 不断发展原位技术以便于观察位错及晶界运动;④ 丰富研究体系,建立界面结构与微观变形机制系统关联。在今后的研究工作中通过定向合成、原位实验表征和原子模拟等技术手段,将微观结构表征与机理研究相结合,深入揭示微观界面结构、成分与材料宏观性能之间的关系,探究界面结构和成分主导的界面特征的动态演化过程,建立材料组分与界面结构设计准则,最终实现利用界面工程在原子尺度精确调控界面结构来优化其使役性能,仍是未来研究的主要内容。
来源--金属学报