分享:不同Si3N4 相涂层坩埚中全熔多晶硅锭的制备及表征
李永乐1,黄金亮1,2,李飞龙3,李 谦1,李丽华1
(1.河南科技大学材料科学与工程学院,洛阳 471003;2.有色金属共性技术河南省协同创新中心,
洛阳 471023;3.阿特斯光伏电力(洛阳)有限公司,洛阳 471023)
摘 要:以αGSi3N4 和βGSi3N4 粉为原料,采用免烧结工艺在坩埚内壁上分别制备了αGSi3N4 涂层、βGSi3N4 涂层以及二者质量比为1∶1的复合涂层,然后在这些涂层坩埚中制备得到了多晶硅铸锭,观察了涂层和硅锭的表面形貌,测试了硅锭的表面粗糙度、晶粒大小以及红区长度.结果表明:αGSi3N4 涂层表面粗糙不平、起伏不均匀,对应硅锭的表面粗糙度和晶粒尺寸最大,红区最长;βGSi3N4 涂层表面较平整且起伏均匀,对应硅锭的表面粗糙度最小,晶粒尺寸较小,红区最短;复合涂层的表面粗糙度介于上述二者之间,对应硅锭的晶粒尺寸最小,红区长度介于二者之间.
关键词:表面粗糙度;Si3N4 涂层;红区长度;晶粒尺寸
中图分类号:TM615 文献标志码:A 文章编号:1000G3738(2017)05G0059G04
0 引 言
目前半熔籽晶铸造法是多晶硅生产工艺中的主流技术,此法生产的硅锭因具有晶粒细小均匀、转化效率高 等 特 点 而 被 广 泛 用 于 制 造 硅 基 太 阳 能 电池[1].其中,以 αGSi3N4 相为主的 Si3N4 涂层因具有良好的杂质阻隔性和脱模性而被用作制备多晶硅铸锭的主要隔离层[2G3].但是半熔籽晶铸造法的主要缺点是底部红区长、产率低,这极大地降低了产品的性价比.全熔引晶技术是将熔融硅直接在涂层上形核长晶的一种高效的多晶硅铸锭制备工艺,它可以显著缩短底部红区长度、提高成品率.自 LI等[4]通过改变坩埚底部的槽角大小而实现选晶的目的后,全世界掀起了全熔引晶技术研究的热潮.全熔引晶技术包括全熔同质形核引晶法[5G6]、全熔异质形核引晶法[7G8]、全熔孔洞形核引晶法[9]等,
这些方法或多或少都存在着硅颗粒因高温熔化而失去形核作用,石英颗粒因氧污染而使硅锭少子寿命缩短,形核孔洞的均匀性难以控制等不足.因此,寻求简单高效的新型形核引晶涂层材料成为了研究热点.BRYNJULFSE等[10]研究了熔融硅在 αGSi3N4涂层上的形核,结果表明,αGSi3N4 涂层对熔融硅显惰性.βGSi3N4 相的性能与αGSi3N4 相的相当,且其高温结构更稳定.NAKAJIMA 等[11G12]在研究坩埚非接触法制备铸锭时发现,βGSi3N4 相具有促进晶体形核、细化晶粒的作用,但鲜有利用βGSi3N4 涂层作为引晶涂层制备全熔高效多晶硅的文献报道.为了对比不同涂层的形核引晶效果,作者分别在坩埚内壁上制备了αGSi3N4 涂层、βGSi3N4 涂层以及αGSi3N4 和βGSi3N4 质量比为1∶1的复合涂层,采用全熔引晶技术和免烧结工艺在这3种坩埚中制备出多晶硅锭,研究了不同涂层的表面形貌及不同涂层对应硅锭的表面形貌和表面粗糙度,分析了垂直于长晶方向横截面上硅锭晶粒的大小,测试了硅锭的底部红区长度.粉(粒径小于5μm 的占90%,中位径为2μm,纯度为99.99%)和 超 能 新 材 料 公 司 生 产 的 βGSi3N4 粉(粒径小于5μm 的占90%,中位径为2μm,纯度为99.99%)作为制备氮化硅涂层的原料,以山东百特新材料公司生产的硅溶胶作为黏结剂.
分别以αGSi3N4、βGSi3N4 粉,以及质量比为1∶1的αGSi3N4 和βGSi3N4 混合粉为原料制备αGSi3N4 涂层、βGSi3N4 涂层和复合涂层.共称取550gSi3N4粉、200mL硅溶胶、1450 mL 去离子水混合在一起,在25MPa压力下热喷涂在石英坩埚内壁上,确保涂层厚度一致、喷涂均匀、不起泡和不脱落;同时称取270kg块状硅、70kg颗粒硅、20kg碎硅片、160kg提纯硅,装入坩埚中,通过免烧结工艺在 GT铸锭炉中铸造出质量为520kg的硅锭.利用照像机观察不同Si3N4 涂层以及该涂层对应硅锭的表面形貌;利用奥林巴斯 LEXT OLS40003D型共聚焦显微镜分析硅锭的表面粗糙度.在硅锭中央、距底面 5 mm 处,垂直于长晶方向截取试样,用照 像 机 观 察 其 截 面 上 的 晶 粒 大 小,同 时 用SemilabTW2000型少子寿命测试仪测其红区长度.
2 试验结果与讨论
2.1 表面形貌
由图1可 以 看 出 :αGSi3N4 涂 层 的 表 面 粗 糙 不平,用该涂层坩埚铸造的硅锭表面也凹凸不平,且存在大小不一的坑洞;βGSi3N4 涂层的表面较平整光滑,铸造得到的硅锭表面也较平整;而复合涂层表面及其铸造硅锭表面的形貌介于上述二者之间.这种形貌差异与不同 Si3N4 相的结构有关.一般而言,αGSi3N4 相呈针刺状而βGSi3N4 相呈粒状,针刺状的αGSi3N4 相使得αGSi3N4 涂层的表面粗糙不平,铸造得到的硅锭表面也不平整;粒状的βGSi3N4 相使得βGSi3N4 涂层表面平整,进而也使得相应的硅锭表面平整;复合涂层因具有针刺状和粒状两种相,故而对应硅锭表面的形貌介于上述二者之间.由图2可知:在 αGSi3N4 涂层坩埚中铸造硅锭的表面粗糙度大,表面起伏不均匀,上下波动较大;在βGSi3N4 涂层坩埚中铸造硅锭的表面粗糙度小,表面起伏比较均匀,上下波动平缓;在复合涂层坩埚中铸造硅锭的表面粗糙度适中且起伏均匀.硅锭表面粗糙度和起伏的变化与图1中硅锭的表面形貌变化一致,且从另一角度反映了不同涂层的表面粗糙度和起伏.
2.2 晶粒尺寸
由图3可知:在不同涂层坩埚中铸造硅锭截面上的晶粒尺寸由大到小按涂层排序为 αGSi3N4 涂层、βGSi3N4 涂层和复合涂层.显然,在全熔铸锭工艺熔融硅形核和长晶的初期,硅晶粒尺寸不仅与涂层的表面形貌有关,还与涂层基体相颗粒的形核功密切相关.通常而言,涂层的表面越粗糙、起伏越不均匀并且基体相颗粒的形核功越小,越易形成细小的多晶硅晶粒.用αGSi3N4 涂层坩埚铸造硅锭的晶粒尺寸最大(约20mm),晶粒呈片状且分布不均匀.虽然αGSi3N4 涂层较粗糙的表面有利于增加熔融硅的形核位置,但由于该涂层表面起伏不均匀,且αGSi3N4相颗粒对熔融硅过冷度的惰性高,该相的熔融硅形核功大[9],故有效的形核位置较少且分布不均匀,导致硅锭的晶粒粗大.βGSi3N4 涂层坩埚铸造硅锭的晶粒尺寸(约5mm)比αGSi3N4 涂层硅锭的细小,晶粒呈片状.虽然βGSi3N4 涂层的表面较平整光滑,不利于熔融硅形核位置的生成,但该涂层表面起伏均匀,且βGSi3N4 相颗粒具有促进晶体形核、细化晶粒的作用,熔融硅形核功小[11],故有效形核位置较多且分布均匀,使得硅锭的晶粒细化.复合涂层中不仅含有针刺状αGSi3N4 相,同时存在低形核功的粒状βGSi3N4 相,在这两种相的协同作用下,复合涂层表面的粗糙程度适中、起伏均匀且含有大量低形核功的形核位置,故硅锭的晶粒最细,尺寸约2mm,呈零星状均匀分布.
2.3 红区长度
由图4可知,在 αGSi3N4 涂层坩埚中铸造硅锭的底部红区最长,在βGSi3N4 涂层坩埚中铸造的最短,在复合涂层坩埚中铸造的介于以上二者之间.众所周知,红区是短少子寿命区域.在多晶硅铸造工艺中引起少子寿命短的重要原因是因为坩埚和氮化硅涂层内的铁杂质向晶体中发生了扩散.由于涂层中的αGSi3N4 相颗粒呈针刺状,颗粒细小且竖直堆垛排列于坩埚表面,平行于杂质扩散的方向,故阻碍杂质扩散能力差,使得硅锭内扩散的铁杂质多,而βGSi3N4 相颗粒呈粒状,颗粒粗大且平行叠加排列于坩埚表面,垂直于杂质扩散的方向,阻挡了杂质向硅锭内的扩散,因此βGSi3N4 涂层坩埚铸造硅锭的红区长度比αGSi3N4 涂层坩埚铸造的明显减小.在复合涂层坩埚中铸造硅锭的红区长度介于二者之间,
这是由于复合涂层中针刺状的 αGSi3N4 相颗粒较多,使得阻碍杂质扩散的βGSi3N4 相颗粒的平行叠加结构不完整,杂质容易扩散进入硅锭而导致的.
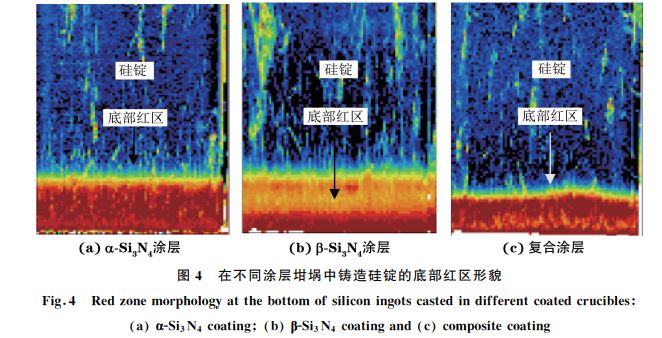
3 结 论
(1)αGSi3N4 涂层的表面粗糙不平,导致在该涂层坩埚中铸造得到的硅锭表面也凹凸不平,且存在大小不一的坑洞;βGSi3N4 涂层的表面则较平整光滑,铸造得到硅锭的表面也较平整;而复合涂层及其铸造硅锭的表面形貌介于以上二者之间;αGSi3N4 和βGSi3N4 相形貌的差异是导致涂层以及硅锭表面形貌不同的主要原因.
(2)在αGSi3N4 涂层坩埚中铸造硅锭的晶粒尺寸最大,红区最长;在βGSi3N4 涂层坩埚中铸造硅锭的晶粒较为细小,红区最短;而在复合涂层坩埚中铸造硅锭的晶粒最细小,红区长度介于以上二者之间.
文章来源:材料与测试