分享:Ca、Mg掺杂下夹杂物对C70S6非调质钢点蚀行为的影响
通过溶液调制的方法对C70S6非调质钢及其掺Ca、Mg样品进行了动电位极化曲线测试,并对测试前后的样品进行了SEM-EDS表征,揭示了夹杂物对非调质钢点蚀行为的影响。结果表明,MnS夹杂易作为活性位点诱发点蚀,而掺杂Ca、Mg元素使得夹杂物分布更弥散,MnS含量更低,相应的点蚀抗性也更高。
关键词:
为了实现“碳达峰”、“碳中和”的目标,节能减排日益成为工业生产和生活中的重要主题,也是学术界的研究热点[1]。非调质钢是近年来发展迅速的一种铁合金材料,相较传统的调质钢,其在节能环保的同时保有优良的性能,已在汽车、高铁等多个领域得到广泛应用[2~4]。
非调质钢的服役环境对力学性能要求较高,而其内部常见的夹杂物会对力学性能产生显著影响[5]。例如质软的MnS会在轧制过程中被拉伸为长条,破坏钢材的各向同性[6~8];质硬的Al2O3夹杂物尖角处会产生应力集中和腐蚀疲劳等问题,严重影响其服役性能。目前业界多采用Mg、Ca等元素掺杂的方式对Al2O3进行改性,钝化其尖角,同时提高氧化物形核数量,使夹杂更加弥散[9~11]。同时,MnS围绕氧化物析出,降低了团聚后被轧制为长条状的概率,整体夹杂物形貌呈现蝌蚪状和眼状[12]。然而,该改性方法对非调质钢的腐蚀行为会产生何种影响尚无定论。
目前针对非调质钢腐蚀行为的研究大多采用盐雾腐蚀、溶液浸泡等方法,目的在于均匀腐蚀性能。但任何均匀腐蚀都并非完全均匀,金属表面总会同时存在着阴极区和阳极区,尤其是在初期阶段,不同的夹杂物类型、夹杂物形态都有可能对腐蚀产生显著影响。而非调质钢由于整体耐蚀性较弱,其夹杂物对腐蚀行为的影响采用均匀腐蚀的评价方法难以进行揭示。
在钝性合金体系中,夹杂物对于腐蚀行为的影响得到广泛研究[13~19]。本工作采用钝性体系中的点蚀电化学评价方法,首先以纯Fe这一简单体系为对象,通过溶液调制赋予材料钝性,在此基础上探究了点蚀的评价方法和溶液条件,随后对C70S6非调制钢以及相应的Mg、Ca调制样品进行极化曲线测试,并对测试前后样品进行扫描电镜-能谱(SEM-EDS)表征,分析夹杂物对点蚀的影响。
1 实验方法
实验用材料包括C70S6非调质钢和在此基础上掺Ca、Mg的样品(样品简记为C70S6-CaMg),其中掺杂的Ca、Mg元素含量均为10-6量级。C70S6的化学成分(质量分数,%)为:Cr 0.1,Ni 0.06,Mo 0.002,C 0.72,Mn 0.57,Si 0.21,P 0.006,S 0.062,V 0.0014,Al 0.005,W 0.036,Fe余量。除此之外,在探索pH测试条件时还用到了纯Fe和409L不锈钢,其中409L不锈钢的化学成分(质量分数,%)为:Cr 11.45,Ni 0.12,C 0.010,Mn 0.24,Si 0.42,P 0.015,S 0.008,Cu 0.02,Ti 0.2,N 0.008,Fe余量。
实验样品通过线切割加工成为12 mm × 12 mm × 1 mm的片状样品,从样品的非工作面引出导线,用环氧树脂封装样品,并暴露测试面积为1 cm2。待工作电极封好之后, 用水磨砂纸逐级打磨工作面,依次用蒸馏水、乙醇、丙酮清洗,吹干。
利用CHI660E型电化学工作站对上述材料进行极化曲线测试,采用标准的三电极体系,辅助电极为Pt电极,参比电极为饱和甘汞电极(SCE),工作电极为样品。首先将工作电极浸入添加不同浓度NaOH和NaCl (控制值pH和Cl-浓度[Cl-])的0.1 mol/L浓度Na2SO4溶液中,先进行-900 mV的恒电位阴极极化120 s,而后维持在开路状态下稳定900 s,最后施加动电位从开路电位(OCP)处开始以一定的扫描速率向阳极方向扫描,直到稳态点蚀或者过钝化发生,电流上升达到一定数值,停止实验。
采用pH调制方法,考察纯Fe在不同pH值下是否如409L不锈钢一样,随着pH值的升高,改善其表面性能,出现钝化区。溶液的pH值由pH计实测得出,每次实验前均对pH计进行校准。
对C70S6和C70S6-CaMg样品进行打磨并用2.5 μm金刚石悬浊液抛光。采用上海立光4XG金相显微镜(OM)观察样品的点蚀形貌,并采用Gemini 300扫描电镜(SEM)对测试前后的C70S6系列样品夹杂物进行尺寸统计及能谱(EDS)表征。
2 实验结果与讨论
2.1 掺Ca、Mg对夹杂物尺寸的影响
C70S6和C70S6-CaMg样品均统计了面积约10 mm2中的夹杂物类型、数量及尺寸分布信息,结果如表1、表2及图1所示。随着Ca、Mg的添加,MnS的平均直径由2.36 μm减小为1.82 μm,尺寸降低22.9%;同时,夹杂物的数量密度由444 mm-2增加到567 mm-2;小尺寸夹杂物(2 μm以下)的比例由52%增加到73%;大尺寸夹杂物(2 μm以上)的比例由48%降低到27%。由此可见,Ca、Mg的添加使得钢中MnS夹杂物的等效直径减小,夹杂物更加弥散。
表1 C70S6非调质钢中夹杂物类型、数量及尺寸分布
Table 1
Inclusion type | Number | 0-2 μm | 2-5 μm | 5-10 μm | > 10 μm |
---|---|---|---|---|---|
MnS | 4750 | 2487 | 2064 | 198 | 1 |
MgO-MnS | 12 | 7 | 3 | 2 | 0 |
CaO-MnS | 18 | 10 | 8 | 0 | 0 |
Al2O3-MnS | 105 | 63 | 35 | 7 | 0 |
Spinel-MnS | 77 | 34 | 40 | 3 | 0 |
Aluminate-MnS | 157 | 68 | 76 | 13 | 0 |
Others | 23 | 11 | 8 | 4 | 0 |
Total | 5142 | 2680 | 2234 | 227 | 1 |
表2 C70S6-CaMg非调质钢中夹杂物类型、数量及尺寸分布
Table 2
Inclusion type | Number | 0-2 μm | 2-5 μm | 5-10 μm | > 10 μm |
---|---|---|---|---|---|
MnS | 6774 | 4949 | 1777 | 48 | 0 |
MgO-MnS | 62 | 39 | 22 | 1 | 0 |
CaO-MnS | 3 | 2 | 1 | 0 | 0 |
Al2O3-MnS | 207 | 142 | 62 | 3 | 0 |
Spinel-MnS | 230 | 161 | 67 | 2 | 0 |
Aluminate-MnS | 445 | 299 | 136 | 10 | 0 |
Others | 49 | 31 | 17 | 1 | 0 |
Total | 7770 | 5623 | 2082 | 65 | 0 |
图1
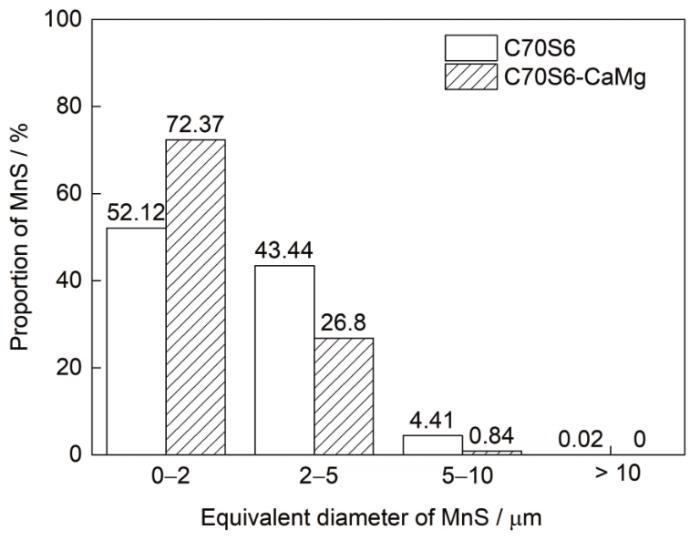
图1 C70S6及C70S6-CaMg非调质钢中MnS夹杂物等效直径分布图
Fig.1 Equivalent diameter distribution of MnS inclusions in C70S6 and C70S6-CaMg non-quenched and tempered steel
2.2 C70S6夹杂物的形貌表征
图2和3分别给出了C70S6和C70S6-CaMg样品典型夹杂物的微观形貌和元素分布。可以看到,2者的夹杂物呈现为椭球型,不同夹杂物组成大型颗粒状夹杂。EDS显示2者的整体夹杂物都呈包裹形态,不掺Ca、Mg样品夹杂物内核以MgO和Al2O3为主,外层包裹了一层MnS夹杂物,掺Ca、Mg样品夹杂物内核以包含Mg-Ca-Al-O的复合夹杂物为主,外层包裹了一层Ca-Mn-S夹杂物,整体呈椭球形,结合文献[11]可以判断,在钢冷凝的过程中,熔点较低的硫化物在氧化物夹杂周围析出,形成以MgO、CaO和Al2O3为内核,MnS和CaS为外壳的眼状夹杂物。
图2

图2 C70S6夹杂形貌夹杂物的微观形貌及EDS元素分布图
Fig.2 Inclusion morphology (a) and element distribution maps (b) of C70S6
图3
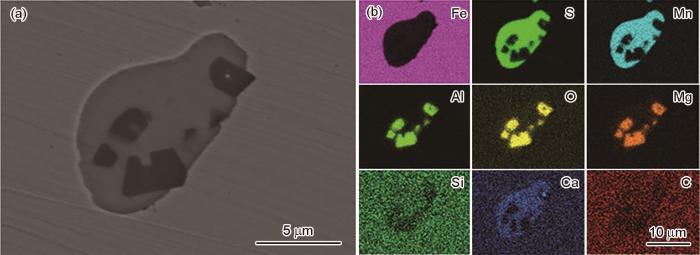
图3 C70S6-CaMg夹杂形貌及EDS元素分布图
Fig.3 Inclusion morphology (a) and element distribution maps (b) of C70S6-CaMg
2.3 C70S6系列非调质钢极化曲线测试
通常的点蚀研究多采用中性NaCl溶液,但非调质钢这类低合金钢在其中无法钝化,因此本实验考虑通过介质调制的方式来赋予材料钝性。影响钝性的溶液因素很多,包括溶液pH值、Cl-浓度、温度等。其中最重要的因素之一在于溶液的pH值,提高溶液的碱性,可以使活性铁合金在表面生成较稳定的钝化膜[20~23]。采用这种方式产生的钝化膜与不锈钢表面的钝化膜是具有一定可比性的,图4给出了不同碱性条件下409L不锈钢的极化曲线,图中不同pH的调整方法是在0.1 mol/L的Na2SO4基础溶液中,逐渐添加NaOH固体使得溶液逐步升高到指定的pH值。
可以看出,随着pH值的升高,点蚀电位逐渐向正方向移动,钝化区持续变宽,直到pH值为13时,样品一直到发生放氧反应也未出现点蚀。这表明,溶液碱性提高使不锈钢获得的钝性,能够定性地对应于合金化程度提高带来的钝性。
图4
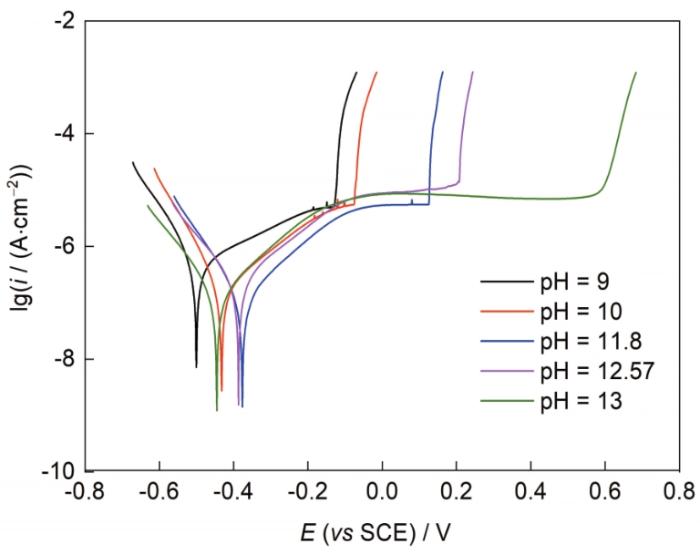
图4 不同碱性条件下409L不锈钢的极化曲线
Fig.4 Polarization curves of 409L stainless steel under different alkaline conditions
为减少材料本身的干扰因素,采用纯Fe作为条件探索样品进行测试,图5是不同pH值下纯Fe的极化曲线。可以看出,在pH = 11.2~11.8之间时出现了明显的活化钝化转变,当pH > 11.8时,非钝性的纯Fe也出现了钝化区,但样品并未发生点蚀,电流上升值集中在放氧电位0.6 V左右。在此基础上本实验于pH = 12.6时添加了不同浓度的Cl-。
图5

图5 不同pH值下纯Fe的极化曲线
Fig.5 Polarization curves of pure iron at different pH
图6是纯Fe在pH = 12.6时分别添加0.001、0.01、0.1、0.2、0.5和1 mol/L Cl-时的极化曲线结果。实验表明,在该pH值下0.01 mol/L及以下的Cl-浓度对试样仍然几乎没有影响,但在0.1 mol/L及以上的Cl-浓度溶液环境中进一步提高Cl-浓度后,发现在溶液pH = 12.6、[Cl-] ≥ 0.1 mol/L时,随着Cl-浓度的升高,电流突升点逐渐降低。实验结果表明通过调制合适的溶液环境可以使弱钝性铁合金获得与不锈钢相似的钝性。
对C70S6和C70S6-CaMg样品进行动电位极化曲线测试。在纯Fe溶液条件探索的前提下考虑到非调质钢相较于纯Fe有一定的钝性,因此实验选择pH = 12.6、[Cl-] = 1 mol/L的条件,以便能有较大的调整空间。实验结果如图7所示。图7表明,相较于纯Fe,掺杂一定量钝性元素的非调质钢显然有更好的耐点蚀性能。掺杂样品和未掺杂样品极化曲线基本重合,电流突升电位接近放氧电位,因此考虑进一步采用更加苛刻的条件进行研究。实验选取pH = 12、[Cl-] = 0~1 mol/L下C70S6-CaMg的OCP和极化曲线,如图8所示。结果表明,当[Cl-] > 0.1 mol/L时难以钝化完全,因此选取pH = 12、[Cl-] = 0.1 mol/L时的临界条件下对2者进行多次实验,结果如图9所示,其极化曲线测试后的蚀坑形貌如图10所示。
图6
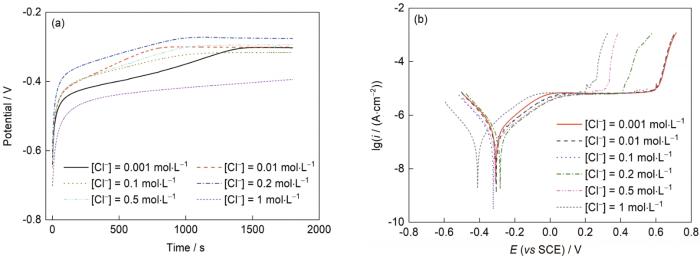
图6 pH = 12.6时不同Cl-浓度[Cl-]下纯Fe的开路电位(OCP)和极化曲线
Fig.6 Open circuit potential (OCP) (a) and polarization (b) curves of pure iron with different Cl- concentration [Cl-] at pH = 12.6
图7

图7 pH = 12.6、[Cl-] = 1 mol/L条件下Fe、C70S6和C70S6-CaMg的OCP和极化曲线
Fig.7 OCP (a) and polarization (b) curves of Fe, C70S6, and C70S6-CaMg at pH = 12.6 and [Cl-] = 1 mol/L
图8

图8 pH = 12、不同Cl-浓度下C70S6-CaMg的OCP和极化曲线
Fig.8 OCP (a) and polarization (b) curves of C70S6-CaMg at different [Cl-] and pH = 12
图9
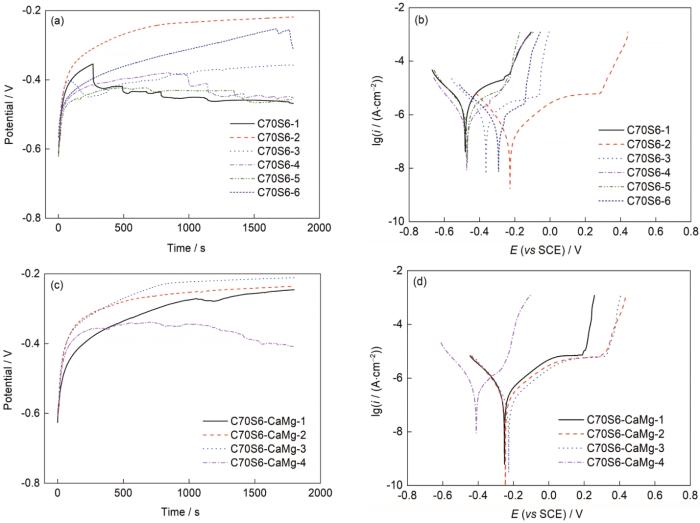
图9 pH = 12、[Cl-] = 0.1 mol/L条件下C70S6及C70S6-CaMg样品的OCP和极化曲线
Fig.9 OCP (a, c) and polarization (b, d) curves of C70S6 (a, b) and C70S6-CaMg (c, d) at pH = 12 and [Cl-] = 0.1 mol/L
图10

图10 C70S6-CaMg和C70S6极化曲线测试后的蚀坑形貌
Fig.10 Etch pit morphologies of C70S6-CaMg (a) and C70S6 (b) after polarization curve test
根据图9中数据所示,在pH = 12、[Cl-] = 0.1 mol/L条件下, C70S6-CaMg样品的稳定性和钝化性能明显高于C70S6样品,且在该条件下2者的点蚀行为均不稳定,而在表观形貌上C70S6-CaMg样品的蚀坑以较大的坑状形貌为主,C70S6样品表面观察蚀坑则是以多点弥散为主。
在此基础上,进一步改善溶液条件和测试终止条件,选择在pH = 12.3、[Cl-] = 0.1 mol/L的条件下进行C70S6、C70S6-CaMg的极化曲线测试,一方面提高溶液pH值,降低溶液的苛刻程度,另一方面限制电流密度小于1.2 × 10-4 A/cm2。2者极化曲线的结果如图11所示,蚀坑形貌如图12所示。
图11
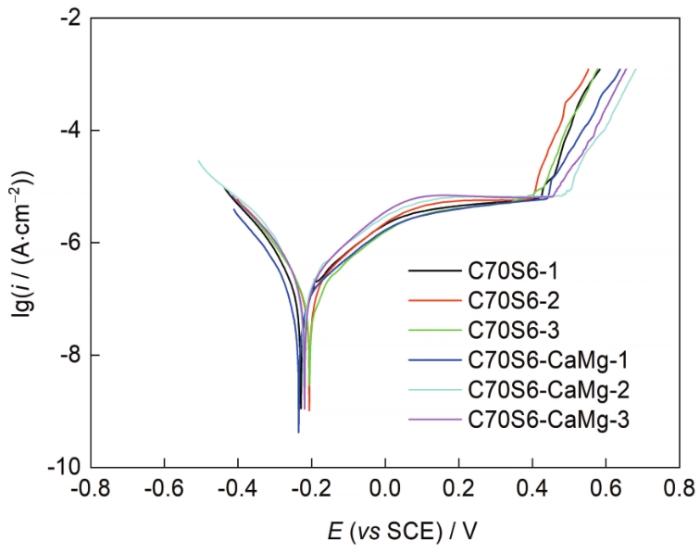
图11 pH = 12.3、[Cl-] = 0.1 mol/L条件下C70S6和C70S6-CaMg的极化曲线
Fig.11 Polarization curves of C70S6 and C70S6-CaMg at pH = 12.3 and [Cl-] = 0.1 mol/L
上述实验结果表明,在该条件下C70S6-CaMg的点蚀电位明显高于C70S6,而在蚀坑形貌上,C70S6-CaMg的蚀坑以大块单个点蚀为主,而C70S6样品在主蚀坑周围存在大量小型蚀坑。
2.4 C70S6系列非调质钢点蚀形貌表征
C70S6和C70S6-CaMg样品通过在600 mV下恒电位5 s,激发点蚀活性位点,结果如图13所示。经统计,在C70S6中,点蚀密度为185 mm-2,点蚀坑的平均尺寸约为23.1 μm,最大尺寸约为64 μm;C70S6-CaMg中,点蚀密度为406 mm-2,点蚀坑的平均尺寸约为4.7 μm,最大尺寸约为23.0 μm。整体来看,添加Ca、Mg后,点蚀密度提高2.2倍,点蚀坑更加弥散分布,但点蚀坑的平均尺寸和最大尺寸大幅度减小。
通过对2者蚀坑的EDS表征发现,样品萌生的较大点蚀坑直径在100 μm左右,而周围分布的小型蚀坑直径在5~10 μm范围。整个蚀坑周围以主蚀坑为中心出现圆形氧化物覆盖区域,且MnS夹杂导致的大小蚀坑均在此范围内出现,推测为主蚀坑发生点蚀时,内部酸性溶液不断扩散,致使周围溶液酸化,酸化后的溶液接触到的基体在夹杂物处萌生了小型蚀坑。
图12

图12 pH = 12.3、[Cl-] = 0.1 mol/L时,C70S6-CaMg及C70S6的蚀坑形貌
Fig.12 Pit morphologies of C70S6-CaMg (a) and C70S6 (b) at pH = 12.3 and [Cl-] = 0.1 mol/L
图13
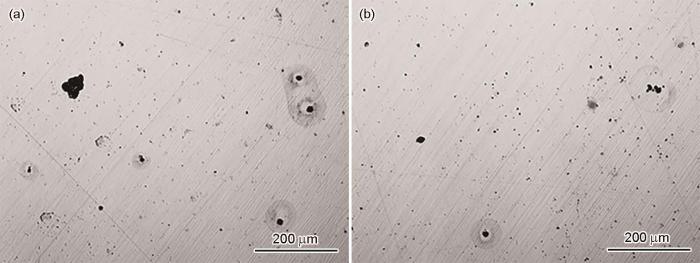
图13 C70S6和C70S6-CaMg样品经恒电位极化后的OM像
Fig.13 OM images of C70S6 (a) and C70S6-CaMg (b) samples after potentiostatic polarization
图14

图14 C70S6主蚀坑形貌及EDS元素分布图
Fig.14 Main pit morphology (a) and element distribution maps (b) of C70S6
如图14所示,中央主蚀坑的主要成分以铁氧化合物为主,由于其尺寸远大于夹杂物尺寸,因此难以直接分析夹杂物对点蚀的影响,而C70S6样品主蚀坑(图16a)周围的小型蚀坑中,发现了大量的MnS存在(见图15)。对其放大进行进一步分析(图16b)发现,整体蚀坑呈椭球形,椭球边缘受腐蚀影响严重,内部存留小块MnS的内核,图15a中左上角蚀坑甚至存在内核脱落的现象。
图15

图15 C70S6夹杂蚀坑形貌及EDS元素分布图
Fig.15 Pit morphology (a) and element distribution maps (b) of C70S6
图16
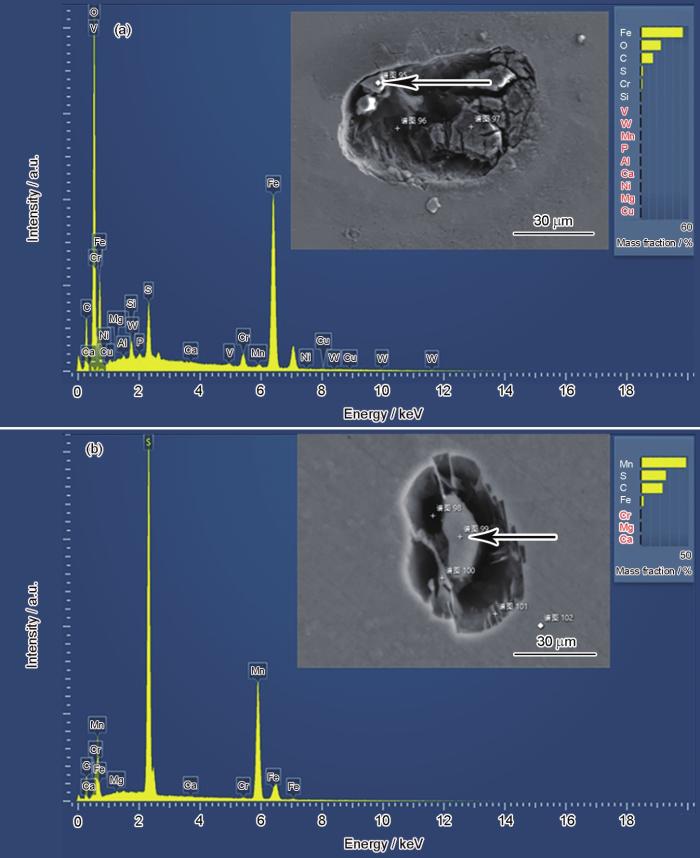
图16 C70S6主蚀坑成分及夹杂蚀坑成分
Fig.16 Main pit (a) and inclusion pit (b) (insets) compositions of C70S6
图17则是C70S6-CaMg在极化曲线测试后的蚀坑形貌和元素分布。其夹杂物形貌从图3的基础上从边缘开始溶解(左侧和上侧),其组分和分布与图3一致,中心为MgO和Al2O3,外层为MnS和CaS,夹杂物整体在电化学测试后边缘溶解产生了如图17a中红色箭头所指出的凹槽,除了在基体和MnS之间出现的溶解凹槽,硫化物和氧化物中间也出现了溶解形貌,如17a中黄色箭头所示。
图17

图17 C70S6-CaMg夹杂蚀坑形貌及EDS元素分布图
Fig.17 Pit morphology (a) and element distribution maps (b) of C70S6-CaMg (Red arrows point to the dissolved grooves between the matrix and the MnS;yellow arrows point to the dissolved grooves between sulfides and oxides)
图15中MnS夹杂物导致的小型蚀坑表明,在动电位极化曲线测试中,夹杂物和基体之间的部分发生溶解,不能确定究竟是基体溶解还是MnS溶解,结合图17a中红黄箭头指出的双溶解,考虑到氧化物的不溶性和外加电位显著高于MnS和纯Fe的自腐蚀电位,认为在外加电位下MnS和基体均发生了溶解。
而实验中观察到的掺Ca、Mg样品耐点蚀性能优于不掺Ca、Mg样品的现象,结合文献[9,10,24~28]可知,随着Ca和Mg的加入,由于其与O、S等元素组成的化合物利于成核,使得非调质钢内常见的MnS以MgO和Al2O3为核组成夹杂物,一方面使得夹杂物数量更多,另一方面使得夹杂物总体变小,整体分布更弥散,又由于其形核内部存在不反应的MgO和Al2O3,因此总体上与不掺Ca、Mg样品相比,夹杂物中MnS含量更低,因此更难被侵蚀,而MnS夹杂更大、含量更高的不掺Ca、Mg样品夹杂物更容易发生点蚀产生蚀坑,因此点蚀破裂电位更低,抗点蚀性能更差。而图12中C70S6样品点蚀坑周围的圆环,在图14中显示应该是Fe的氧化物,结合主蚀坑周围大量暴露的MnS夹杂坑,推测应该是主蚀坑点蚀过程中溶液浓差扩散时导致周围溶液酸化,使得蚀坑周围的MnS夹杂物与周围基体纷纷溶解。而掺Ca、Mg样品夹杂物总体反应难度大于未掺Ca、Mg样品,一方面夹杂物更难反应,另一方面也更难提供足够的酸化溶液诱使主蚀坑周围夹杂发生反应。
3 结论
(1) C70S6系列非调质钢内部夹杂主要为MnS,Mg、Al等元素主要以氧化物的状态作为夹杂物内核,Ca、Mn主要以硫化物的形式包裹在外层。
(2) 在合适的溶液条件下(pH = 12.3,[Cl-] = 0.1 mol/L),极化曲线测试反映出C70S6掺Ca、Mg后比C70S6耐点蚀性能更强,结合OM和SEM观察,推测与夹杂有关。
(3) C70S6和C70S6-CaMg样品夹杂物均为包裹结构。C70S6夹杂物中心主要成分为Al2O3,外层为MnS;C70S6-CaMg样品夹杂物中心主要成分为MgO和Al2O3,外层为MnS和CaS。
(4) 由于C70S6-CaMg样品相较于C70S6样品夹杂物中易溶解的MnS含量更少,因此耐点蚀性能更强,更难发生点蚀。
来源--金属学报