分享:Cu-2.0Fe合金等温处理过程中富Fe析出相的形态演变
陈凯旋1, 李宗烜1, 王自东,1,2, Demange Gilles3, 陈晓华2, 张佳伟1, 吴雪华1, Zapolsky Helena3
1
2
3
研究了Cu-2.0Fe (质量分数,%)合金中富Fe析出相形态的演变行为及其与等温温度和保温时间的关系。结果表明,Cu-2.0Fe合金在Fe相fcc温区内的924、964和984℃保温时,富Fe相粗化并伴随着球状(纳米级)→立方状(亚微米级)→四分支花瓣状(亚微米级)→多分支花瓣状(微米级)的形态演变。随着等温温度和保温时间的增加,多分支花瓣状颗粒的尺寸逐步增大,分支数量逐步增加。多分支花瓣状颗粒的长大需要吞噬周边的小颗粒,导致温度升高时纳米~亚微米级富Fe颗粒的数量密度下降。基于相场模拟的分析表明,界面能、弹性能和化学驱动力的综合作用诱发富Fe相的多重形态演变,其中四分支花瓣状颗粒长大过程中,在弹性应变能和化学驱动力相互角逐作用下,从一次分支上生长出二次分支,进而产生了多分支花瓣状的形态。
关键词:
合金中普遍存在着析出现象,即在凝固[1,2]和形变热处理阶段[3,4]从熔体或过饱和固溶体中分离出第二相的一种相分离现象。合金中析出的第二相粒子在变形过程中阻碍位错运动,使合金的强度提高[5]。析出相的形态、尺寸、数量、分布等特征强烈影响析出强化型合金的力学性能,因此人们往往通过成分设计、形变和热处理工艺调控合金的析出特征,改善合金的力学性能[6~18]。富Fe相强化锡青铜合金[1,19]和Cu-Fe(-Co)合金[2]是典型的析出强化型合金,通过在熔铸过程中加入微量Fe元素,在Cu基体中析出高度弥散的共格或半共格纳米富Fe颗粒,使合金强度和塑性同时成倍提高。富Fe相的特征可以通过后续固溶和时效处理进行优化调控,从而进一步改善铜合金的综合力学性能[20,21]。
Thermo-Calc热力学计算表明,Fe在Cu基体中的固溶度极低,716℃下固溶总量只有0.5% (原子分数),因此,凝固冷却过程中富Fe相可以从Cu基体中析出[2]。根据热力学计算可知,富Fe相首先以fcc结构在熔体(1097~1140℃)或高温基体(902~1073℃)中析出;温度降至877℃,由fcc结构转变为bcc结构,晶体结构的转变行为会影响富Fe相的动力学析出过程[2]。研究[2,22]发现,空冷凝固态Cu-Fe(-Co)合金中的富Fe颗粒在高温阶段长大过程中发生球状→立方状→花瓣状的形态演变。研究[23~25]表明,变形过程中具有尖锐棱角(如立方或花瓣形态)的颗粒易导致应力集中,加剧微裂纹的萌生和扩展,恶化金属材料的塑韧性,而球状形态则能够缓解该恶化作用。比如,球状和立方状富Fe相强化的Cu-Fe-Co合金在125℃慢应变速率拉伸实验中,后者相对于前者均匀延伸率下降10%[2],因而高温下富Fe颗粒的形态演变显著影响铜合金的力学性能。另外,花瓣状富Fe颗粒的异常分裂现象提示了一种潜在的强化途径,即分裂导致Cu基体中形成更多尺寸细小、均匀分布的球状强化粒子,有望产生额外的强化效应。可见,铜合金在铸造、形变和热处理等制备过程中或服役阶段必须考虑析出相的形态演变,对这一问题的深入研究可为析出相的调控提供指导,对改善合金性能及性能稳定性具有实际意义。
尽管关于空冷凝固态Cu-Fe-Co合金中富Fe颗粒析出行为的探索阐述了形态演变的现象,但温度、保温时间、成分等因素对颗粒形态的影响规律尚不明确。首先,空冷和炉冷凝固实验反映的是连续冷却条件下富Fe相的形态演变,富Fe相发生形态转变的温度区间并未确定。其次,前期综合考虑界面能、弹性能和化学驱动力作用的相场模拟结果[22]指出,富Fe相形态演变强烈依赖于等温温度和保温时间,然而温度和时间因素对富Fe相粗化过程中形态演变行为的影响目前尚不清楚。此外,目前空冷凝固态Cu-Fe(-Co)合金中发现了富Fe颗粒球状→立方状→花瓣状的形态演变,但花瓣状颗粒随着保温时间进一步延长时的粗化行为及形态演变规律亦不明确。因此,亟需开展等温实验研究,明确富Fe析出相的形态演变行为及其与等温温度和保温时间的关系,进而为铜合金中富Fe相形态的宏观调控(如铸造冷却速率、热处理温度和时间等参数的设计)及其性能改善提供依据。本工作通过对Cu-2.0Fe (质量分数,%,下同)合金进行不同温度和保温时间的等温实验,观察分析富Fe析出相在高温Cu基体中的多重形态演变,明确形态转变的温度区间以及温度和时间对富Fe相形态演变的影响,并结合等温实验和相场模拟对富Fe相形态演变的机理进行讨论。
1 实验方法
1.1 样品制备
本实验以纯度分别为99.99%和99.98%的Cu和Fe为原材料,采用中频感应熔炼和真空重力铸造工艺制备Cu-2.0Fe合金铸锭,铸锭的实测成分为Cu-2.05Fe,尺寸为50 mm × 70 mm × 260 mm。熔炼时将原材料放入石墨坩埚中,在真空下加热到1300℃保温20 min,保温结束后将温度降低到1150~1200℃,将合金熔体浇铸到石墨铸型内获得空冷凝固态的铜合金铸锭。
采用电火花切割机从Cu-2.0Fe合金铸锭上切取直径10 mm、长度120 mm的圆柱样品,并将其密封在石英玻璃管中。对封管后的样品进行高温熔融+水淬处理,即将石英管中的圆柱样品加热至1200℃保温30 min,保温结束后降温到Cu-2.0Fe的熔点(1084℃)时水淬,此时石英管内Cu-Fe熔体从高于熔点的温度快速冷却,获得水冷凝固态Cu-2.0Fe合金样品。
在水冷凝固态Cu-2.0Fe合金样品上取样,试样为直径12 mm、厚5 mm的圆柱样品。将水冷凝固态圆柱样品进行真空封管,随后将其放入硅碳棒电阻炉中进行不同温度和保温时间的等温处理。前期相场模拟结果[22]显示富Fe相在902~1073℃之间的fcc温区发生形态转变,故本工作选用924、964和984℃为等温温度分别进行6 h的保温后水淬,获得3种等温处理态Cu-2.0Fe合金样品,开展不同温度下富Fe相形态演变的研究,实验过程中的水淬处理是为了保留特定温度和保温时间下富Fe相的形态特征;另外,将水冷凝固态样品在964℃进行1、6和12 h的保温后水淬,获得3种等温处理态样品,进行不同保温时间下富Fe相形态演变的研究。
1.2 样品表征
以空冷凝固态、水冷凝固态和等温处理态Cu-2.0Fe合金样品为对象,利用配备X射线能谱仪(EDS)的LEO 1450扫描电子显微镜(SEM)对样品中亚微米和微米级析出相的形态、尺寸、数量、分布和成分等特征进行观察和分析。在SEM表征之前对样品进行机械抛光和室温腐蚀,腐蚀液为1 g FeCl3 + 20 mL C2H5OH溶液。使用Tecnai G2 F20型场发射透射电子显微镜(TEM)对纳米级析出相进行观察,采用选区电子衍射(SAED)以及Digital Micrograph 3.5软件对高分辨TEM (HRTEM)照片进行快速Fourier变换(FFT)和FFT斑点分析,明确析出相的晶体结构,结合高角环形暗场像(HAADF-STEM)和EDS对析出相进行化学成分分析。TEM薄片样品通过电解双喷和离子减薄制备,电解双喷采用50~60 mA电流和8~10 V电压,在液氮保护下的25%HNO3 + 75%CH3OH (体积分数)溶液中进行。
2 实验结果与讨论
2.1 连续冷却态Cu-2.0Fe合金中富Fe相特征
图1
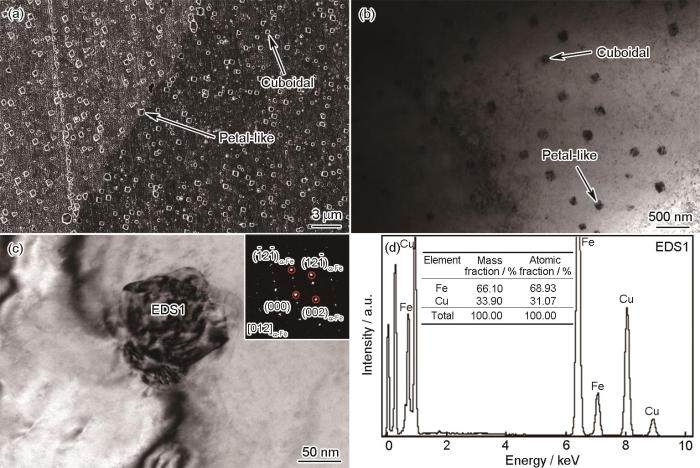
图1 空冷凝固态Cu-2.0Fe合金中富Fe析出相显微组织及EDS分析
Fig.1 Characterization of Fe-rich precipitates in the air-cooled Cu-2.0Fe alloy (a, b) SEM (a) and TEM (b) images showing the cuboidal and petal-like precipitates (c) HRTEM image showing a petal-like precipitate (Inset shows the SAED pattern of the precipitate) (d) TEM-EDS result of the petal-like precipitate in Fig.1c
图2
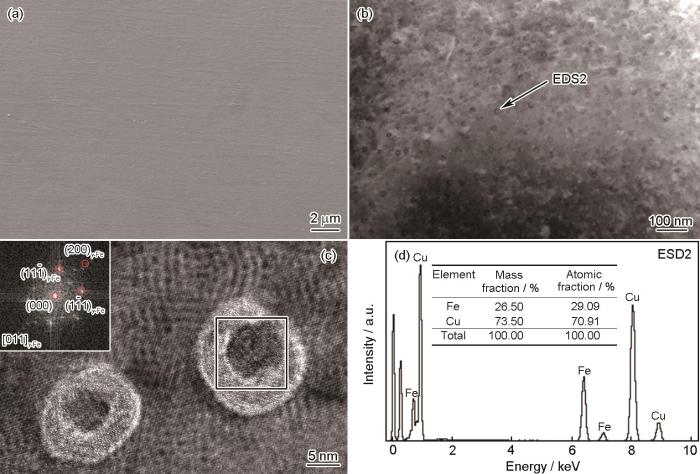
图2 水冷凝固态Cu-2.0Fe合金中富Fe析出相表征
Fig.2 Characterization of Fe-rich precipitates in the water-cooled Cu-2.0Fe alloy
(a) SEM image showing no precipitate
(b) HAADF-STEM image showing the nano-sized spherical precipitates
(c) HRTEM image of two nano-sized spherical precipitates (Inset shows the FFT pattern of the square zone)
(d) TEM-EDS result of the spherical precipitate marked by the arrow in Fig.2b
对比空冷凝固态和水冷凝固态Cu-2.0Fe合金中富Fe相特征可知,富Fe析出相可以在铜合金熔体中呈球状析出,如图2所示,在高温时Fe在Cu中的固溶度较高,而低温时基本不溶[26],说明将空冷凝固态合金在1200℃进行重熔保温时,由于温度较高,大部分的Fe重新溶入到合金熔体中;从1200℃降温至1084℃的熔融态阶段,富Fe颗粒形核析出但是没有充分长大;温度为1084℃时将高温熔体直接水淬,由于合金熔体从高温迅速冷却,Fe来不及扩散,富Fe颗粒不能长大从而保持为尺寸较小的球状纳米颗粒。而在空冷凝固态Cu-2.0Fe合金中,富Fe析出相在慢速冷却过程中扩散长大,并在长大过程中发生形态转变,产生了立方状和花瓣状的形态,如图1所示,说明1084~1200℃的高温熔融阶段Cu-2.0Fe合金中的富Fe颗粒不会发生球状→立方状→花瓣状的演变,该形态演变必然发生在凝固后的固相Cu基体中。
2.2 等温过程中富Fe相形态演变
图3
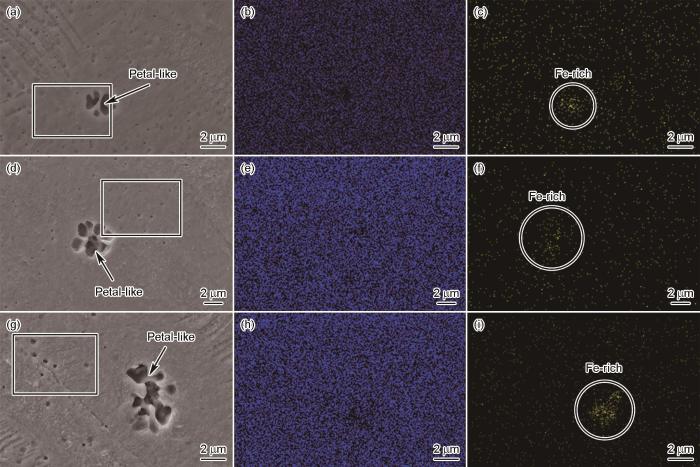
图3 水冷凝固态Cu-2.0Fe合金等温处理后富Fe析出相的SEM像和EDS面扫图
Fig.3 SEM images (a, d, g) and corresponding EDS mappings of Cu (b, e, h) and Fe (c, f, i) elements showing Fe-rich precipitates in the isothermal-treated Cu-2.0Fe alloy (a-c) 924oC, 6 h (d-f) 964oC, 6 h (g-i) 984oC, 6 h
图4
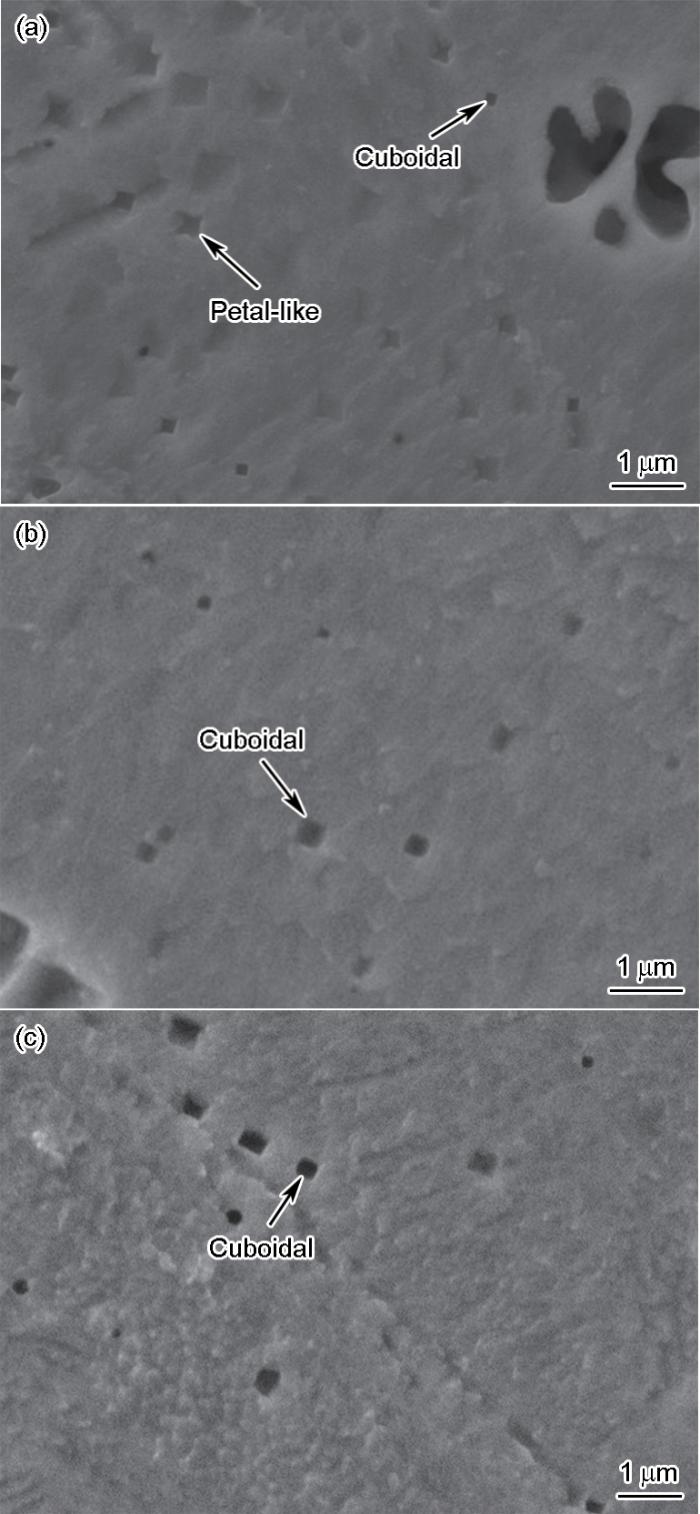
图4 图3中水冷凝固态Cu-2.0Fe合金等温处理后SEM像局部放大图
Fig.4 Magnified SEM images of the square zones in Fig.3 of the isothermal-treated Cu-2.0Fe alloys
(a) 924oC, 6 h (b) 964oC, 6 h (c) 984oC, 6 h
图5
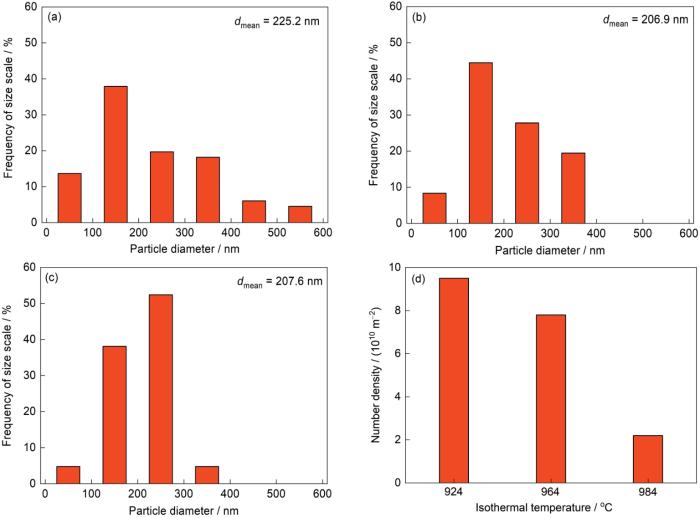
图5 等温处理6 h后微米级花瓣状颗粒周边的富Fe小颗粒的尺寸分布和数量密度
Fig.5 Size distributions of the precipitates after 924oC, 6 h (a), 964oC, 6 h (b), and 984oC, 6 h (c) isothermal treatments, and number density of the small precipitates after isothermal treatments for 6 h (d) (dmean—mean diameter)
图6
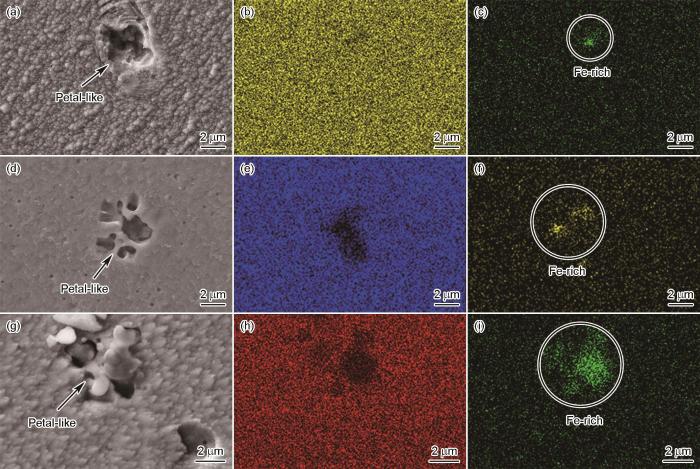
图6 水冷凝固态Cu-2.0Fe合金在964℃等温处理不同时间后富Fe析出相的SEM像和EDS面扫图
Fig.6 SEM (a, d, g) images and corresponding EDS mappings of Cu (b, e, h) and Fe (c, f, i) elements showing Fe-rich precipitates in the isothermal-treated Cu-2.0Fe alloys at 964oC for 1 h (a-c), 6 h (d-f), and 12 h (g-i)
2.2.1 等温温度对富Fe相形态演变的影响
对水冷凝固态Cu-2.0Fe合金在924、964和984℃进行6 h的等温处理,SEM表征发现每个温度下都出现微米级尺寸且具有多个分支的花瓣状颗粒,如图3a、d和g所示。将图3a、d和g中的矩形框区域放大后,发现在微米级多分支花瓣状颗粒的周围弥散分布着亚微米级的立方状和花瓣状颗粒,如图4所示,其形态和尺寸特征与图1a~c中空冷凝固态Cu-2.0Fe合金的富Fe析出相类似。对图3a、d和g进行EDS面扫分析,可以看出,花瓣状颗粒对应的区域存在Fe元素富集,如图3b、c、e、f、h和i所示,说明这些花瓣状颗粒是富Fe析出相。需要指出的是,由于SEM样品事先进行了侵蚀处理,花瓣状富Fe颗粒发生局部脱落,所以在EDS面扫图中颗粒的Fe元素成分比较微弱。
将水冷凝固态与等温处理态的富Fe相形态、尺寸对比分析可知,相对于水冷凝固态,924、964和984℃等温处理6 h的Cu-2.0Fe合金中富Fe析出相发生了明显的粗化,且粗化过程中伴随着球状(纳米级,图2)→立方状(亚微米级,图4)→四分支花瓣状(亚微米级,图4)→多分支花瓣状(微米级,图3)的形态演变。924、964和984℃均处于富Fe相的fcc温度区间,相场模拟研究[22]表明,fcc富Fe颗粒在界面能、弹性能和化学驱动力的综合作用下经历球状→立方状→四分支花瓣状的多重形态演变。首先,生长初期(颗粒尺寸< 100 nm),弹性能和界面能的交互作用促使颗粒沿着弹性“软”取向生长,颗粒由球状转变为具有平坦界面的立方状,其中平坦界面为{001}γ-Fe晶面;接着,化学驱动力使立方状颗粒拐角沿<111>γ-Fe晶向快速生长,立方颗粒失去稳定性并转变为具有凹陷界面的花瓣状。立方形态的不稳定性取决于富Fe颗粒周边Fe元素的过饱和度。水冷凝固态Cu-2.0Fe合金等温处理过程中球状→立方状→四分支花瓣状形态演变的实验结果与前期相场模拟结果[22]十分吻合,可以明确富Fe相的形态演变发生在高温固相Cu基体中,而发生形态演变的温度区间是Fe相的fcc温区。
富Fe析出相在等温处理过程中的粗化与Fe元素在Cu基体中的扩散有关,其中扩散系数D是描述元素扩散能力的参数,D强烈地依赖于温度,其中关系由Arrhenius方程表示[27]:
式中,D0为扩散常数;Q为扩散激活能;R为理想气体常数;T为绝对温度。由此可知,等温温度越高,Fe在Cu基体中的扩散能力越强,球状富Fe析出相粗化程度越高,导致微米级花瓣状富Fe颗粒的尺寸随着等温温度的升高而增大。此外,随着颗粒尺寸的逐步增大,花瓣状富Fe颗粒的分支数量逐步增加,后面2.3节将结合相场模拟对多分支的现象进一步分析讨论。
对微米级花瓣状富Fe颗粒周边的小颗粒进行了尺寸分布和数量密度统计,结果如图5所示。假设在区域面积为A μm2的范围内有N个富Fe颗粒,数量密度Ns 即为每平方米区域内的颗粒个数,其计算公式为:
根据
2.2.2 等温时间对富Fe相形态演变的影响
图6为水冷凝固态Cu-2.0Fe合金在964℃分别进行1、6和12 h等温处理后富Fe颗粒的形态特征。可以看出,964℃等温处理1 h后,Cu基体中出现四分支花瓣状富Fe颗粒,颗粒尺寸约3.5 μm,如图6a所示。当等温时间延长到6 h时,颗粒由四分支花瓣状演变为多分支且分支明显的花瓣状,颗粒尺寸约4.3 μm,如图6d所示。当等温时间达到12 h时,等温时间的延长进一步促进了花瓣状颗粒分支的延伸和新分支的萌生,颗粒尺寸达到5.6 μm,如图6g所示。结合Cu、Fe元素EDS面扫分析可知图6a、d和g中的花瓣状颗粒均为富Fe成分。综上分析表明,随着等温时间的延长,Cu-2.0Fe合金中的富Fe颗粒不断长大,形态由图2中水冷凝固态的球状转变为图6a中四分支花瓣状,以及图6d和g中分支明显的多分支花瓣状,分支的数量随着等温时间的延长而增多。
2.3 等温过程中富Fe相形态演变的相场模拟
式中,r* = r / l0,其中,r为空间长度,l0为网格步长;t*为无量纲时间;k* = kl0, k*和 k 为取向矢量;
为研究Cu-Fe合金中富Fe相的析出动力学,利用Spectral-Eyre方法求解非线性方程(3)得到数值解[29]。前期在5123的三维模拟盒子中进行的相场模拟结果[22]显示,随着颗粒尺寸的增大,在弹性能各向异性的主导下其形态逐渐趋近立方状;随着模拟时间的进一步延长,立方颗粒出现凹陷形态,随之沿着立方颗粒的<111>取向快速生长,颗粒形态从立方状演化为花瓣状,接着颗粒的8个分支进一步发展形成稳定的花瓣状形态,以上模拟结果与图2和4中等温实验观察到的结果一致。然而,由于前期相场模拟盒子的空间限制,更大尺寸(如微米级尺寸)花瓣状颗粒的演变并未进行模拟分析[22]。本工作在10242模拟盒子中进行二维相场模拟,分析了花瓣状富Fe颗粒在更大尺寸下的形态演变行为,如图7所示。相场模拟所需的无量纲建模参数参照前期实验检测和热力学计算结果评估得到,参见文献[22]中的参数值。模拟结果显示,富Fe颗粒在984℃等温状态下不断长大,其形态由图7a中球状转变为图7b中棱边凹陷的立方状,接着产生<111>取向的一次分支形成图7c中四分支花瓣状,与前期三维模拟结果[22]以及本工作图2和4所示的等温实验结果一致;随着等温时间的延长,四分支花瓣状颗粒进一步长大,一次分支继续延伸,同时在一次分支上生长出二次分支,产生了多分支的花瓣状,如图7d~f所示,该模拟结果与图3、图6d和g中等温处理态Cu-2.0Fe合金微米级尺度的多分支花瓣状富Fe颗粒的形态特征相吻合。分析表明,弹性应变能和化学驱动力相互角逐控制亚微米和微米尺度富Fe颗粒的形态,富Fe颗粒一次和二次分支的萌生和生长过程由化学驱动力(即颗粒周边Fe元素的过饱和度不同)主导产生。综合比较可知,等温实验结果与相场模拟结果一致,进一步证明了所采用相场模型[22]的可靠性。
图7
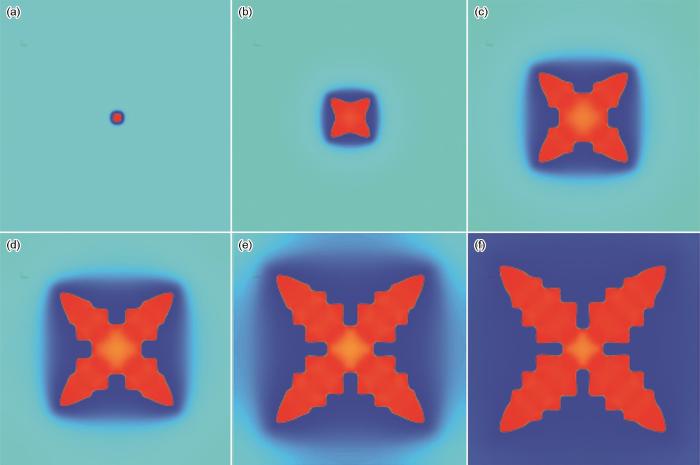
图7 相场模拟结果显示Cu-Fe体系(平均Fe浓度
Fig.7 Morphological evolutions of the Fe-rich single precipitate in Cu-Fe system with an average Fe concentration
(a) t* = 1000 (b) t* = 20000 (c) t* = 70000 (d) t* = 100000 (e) t* = 150000 (f) t* = 200000
3 结论
(1) 水冷凝固态Cu-2.0Fe合金中仅存在尺寸为10 nm左右的球状富Fe相,而在空冷凝固态富Fe相出现了亚微米尺度的立方状和花瓣状形态。水冷凝固态Cu-2.0Fe合金在富Fe相的fcc温区(即924~984℃)保温过程中,富Fe相发生球状(纳米级)→立方状(亚微米级)→四分支花瓣状(亚微米级)→多分支花瓣状(微米级)的演变,表明富Fe相的形态演变发生在高温固相Cu基体中。
(2) 随着等温温度和保温时间的增加,多分支花瓣状富Fe颗粒的尺寸逐渐增大,分支数量逐步增加。此外,随着等温温度的升高,多分支花瓣状颗粒周边小颗粒的数量密度下降,说明多分支花瓣状颗粒的长大需吞并周边纳米~亚微米尺度的小颗粒。
(3) 等温实验中富Fe相的形态演变行为与相场模拟结果相吻合。其中,弹性应变能和化学驱动力相互角逐控制亚微米和微米尺度富Fe相的形态,且在四分支花瓣状进一步长大过程中诱发二次分支在一次分支上的萌生和生长,产生多分支的花瓣状形态。