分享:金属材料的组织定制
根据性能需求设计组织是金属材料的重要发展方向。本工作提出了金属材料组织定制的新学术理念,其内涵是:基于材料物理本质进行介观尺度设计,建立组织与性能的量化关系,通过逆向精准调制并制备材料组织,满足材料服役性能需求。即,根据服役性能需求,首先进行组织筛选、跨尺度计算与组织要素量化,然后基于热力学和动力学调控进行组织制备,最后进行性能考核,迭代优化,实现组织定制。组织定制的前提是保证金属材料的纯净度和均质性,只有解决了材料的纯净性问题,夹杂物、杂质元素的影响作用才能排除;只有消除了宏观偏析缺陷的影响,材料才能实现均质性,材料的本征性能才能充分体现。本工作以航空发动机轴承用M50 (G80Cr4Mo4V)钢为例,介绍了在控制钢的纯净度和宏观偏析基础上,根据疲劳性能目标要求,指出粗大的共晶碳化物是影响疲劳性能的关键组织,进而对碳化物量化设计,最后通过控制碳化物尺寸、类型、形貌及演化行为满足了疲劳性能需求。随着冶金工业的技术进步,组织定制是金属材料学科发展的必然。依托材料计算与数据科学,在组织定制基础上,未来将逐步优化合金成分设计,实现贵金属元素减量化、微量化直至素化,从而节约资源,发展绿色材料。
关键词:
在金属材料的研发和制备过程中,成分-工艺-组织-性能四面体模型一直是材料科学与工程研究的基本框架[1]。通常在已知合金成分的条件下,研究人员期望建立组织与性能的量化对应关系,根据性能的需求逆向设计组织,做到量体裁衣,使制备的组织恰好满足性能需求,我们称之为组织定制。组织定制的优点是,一方面可以量化组织和性能,做到性能可控,避免性能过剩或者不足;另一方面,通过组织定制,依托材料基因组工程的数据科学与高通量模拟计算[2],逐步有效减少合金含量,实现合金添加减量化、微量化直至素化,这有利于节约资源,贯彻双碳战略,是未来的发展方向。然而,现实情况是,研究人员通常根据材料成分,进行冶炼、铸造、锻/轧、热处理、焊接等热加工制备样品,然后测试材料的性能,反过来继续迭代优化工艺,直到达到满意的性能为止,有时性能大幅度过剩,这种做法更多依赖试错的经验,不仅成本高而且效率低。因此,组织定制是学科发展的必然。但传统上难以实现组织定制的主要原因,一是缺少大数据支撑,目标性能与组织之间难以建立有效的定量关联[3];二是以往的冶金水平难以达到组织定制的条件。组织定制的前提是材料的纯净性和均质性要高,而由于冶炼的纯净度不高,夹杂物和杂质对性能的影响很大,导致材料强韧性和疲劳性能等剧烈波动,无法有效实现组织定制。同时,如果材料中存在严重的宏观偏析等缺陷,不同区域之间成分不均匀等因素导致材料的性能大幅度波动,也不能实现组织定制。
随着冶炼和凝固技术水平的提高,人们可以对金属材料的夹杂物进行有效控制,例如在工业化生产的钢中,全氧含量能够控制到5 × 10-6以下,S含量也可以控制到2 × 10-6以下,大幅度减少了钢中的夹杂物[4]。在减少夹杂物的同时,研究人员还可以通过对硬脆夹杂物进行改性处理,逐步使之无害化。例如,在钢中采用稀土处理的方法,使钢中原有的硬脆Al2O3夹杂物、大尺寸长条状的MnS夹杂物转变为稀土氧硫化物。稀土氧硫化物硬度与钢的硬度接近,而且具有一定的塑性变形能力,显著减少了夹杂物/基体界面处的应力集中,大幅度提升了钢的疲劳性能[5]。在凝固偏析控制方面,人们通过模拟与实验,进行锭型优化、外场处理、大压下等技术手段改善偏析,有效减轻了宏观偏析的影响[6~8]。中国科学院金属研究所在对大钢锭的研究中,通过模拟计算和实物解剖,建立了可视化方法。研究[9]发现,O对钢中通道偏析具有关键影响,降低O含量可减轻直至消除通道偏析。提出了氧致偏析的新观点,发现了通道偏析形成的新机制,拓展了经典的偏析形成理论[9]。“控氧可有效控制偏析”这一观点形成行业共识。目前,通过控氧纯净化和稀土处理,GCr15轴承钢等特殊钢中C的偏析可以控制到± 0.02%以内,对材料后续组织演化和力学性能不会产生显著影响。因此,在纯净化和均质化的基础上,就可以根据材料性能要求,建立起性能与组织演化的定量关系模型,开展组织定制的研究。
目前国际上尚无直接明确的组织定制的思想提出,但对于组织与性能对应关系的研究一直是材料学界的重点工作。中国科学院金属研究所卢柯课题组[10~12]提出了材料素化的思想,把组织、界面调控作为一个重要手段,通过纳米化结构设计,大幅度减少合金加入量,以此实现材料素化。在低碳钢的轧制过程中,建立了成分、工艺、组织、性能四面体模型,通过大数据积累,不断迭代优化模型,成功进行了拉伸强度、屈服强度、伸长率的预测,效果良好[13,14]。在纯净化和均质化基础上,实现金属材料性能导向的组织定制的一个重要手段就是热处理。在热处理过程中,加热、保温、冷却等过程中调控组织的方法很多,甚至需要多种组织组合才能满足一项性能的指标要求,但在实际工程中对热处理的研究和重视程度远远不够,甚至成为行业短板。热处理过程中,在微米级的介观尺度甚至微纳尺度上,根据设计的组织,进一步调控组织演化的热力学和动力学,在微米、纳米层次进行组织定制,制备出合适的组织,可以大幅度提高材料的使役性能,这也是组织定制的一个重要组成部分。
1 组织定制技术路线
图1

图1 组织定制的技术路线示意图
Fig.1 Schematical technology route of tailoring microstructures of metals
组织定制的第一步是对金属构件的应用需求进行分析,梳理其对所使用金属材料的性能需求。金属材料的常规力学性能通常包括强度、塑性、韧性以及疲劳性能等,对于一些环境工况,金属材料还需要具备耐热、耐磨、耐蚀、抗辐照等性能要求。对于静态承力结构件,其性能需求基本上可以通过这些性能指标进行反映。但对于一些复杂应用场景的零部件,其服役性能通常很难通过上述常规的理化性能进行评价。因此,构建金属零部件服役性能与可检测的理化性能之间的关系是解析性能需求的关键。
实际上,构建零部件服役性能与可检测的理化性能之间的关系也是图1中组织考核环节的重要任务。同时,通过对组织考核过程数据的采集和分析,以及考核过程中和考核后样本的系统分析,也有助于梳理出零部件服役性能与材料理化性能之间的关系。当前对零部件性能需求的分析主要还是依靠科研人员在基础理论指导下的经验积累,直接的理论指导较弱,这是因为当前无论是性能需求分析还是组织考核都面临诸多难题,最为核心的是缺少对金属构件进行近服役工况的性能考核,以及在近服役工况考核过程中进行原位分析与测量。例如,当前精密机床主轴轴承在实际使用过程中主要关注其精度寿命,随着使用时间的延长,机床主轴轴承可能因为残余应力、亚稳组织转变以及轻微磨损而导致精度降低,此时对于实际应用而言,轴承已经达到了精度寿命期限,不能再继续使用。但目前多数轴承考核台架以轴承出现疲劳剥落为判据测试轴承的疲劳寿命,导致无法对精密机床主轴轴承材料提出合理的性能要求。针对缺少近服役工况性能考核的难题,国内外已有大量研究,如我国建设了重大科技基础设施“重大工程材料服役安全研究评价设施”项目,为重大工程中关键金属构件提供近服役工况的性能考核与评价。同时世界范围内先进同步辐射光源、中子源等大科学装置的建设,也为在近服役工况下原位测量材料应力应变状态和组织演化提供了可能。例如Reid等[16]使用中子衍射测量了轴承套圈在服役状态下的应变演化,可以用于支撑相应服役状态下材料微观组织的设计。未来随着考核条件逐渐逼近实际应用,考核数据量的不断增加,以及借助人工智能、机器学习和大数据技术,将会有效助力构建零部件服役性能与可检测的理化性能之间的关系。
在完成对性能需求的分析之后,即可开展对金属材料的组织筛选。与材料基因组计划[17]目标为研发新材料不同,面向工程的金属材料组织定制的组织筛选是基于已有的专业知识,结合性能需求分析,在材料成分基本确定的情况下,开展关键组织筛选。工程应用的金属结构材料一般都具有一定的应用基础,从而可以根据上述性能需求分析和前期应用基础确定影响其服役性能的关键组织,进而在后续的组织定制中聚焦到关键组织的设计和定量调控上。
在确定影响服役性能的关键组织之后,明确组织与性能的定量关联是组织定制的核心研究内容之一。开展材料组织与性能之间关系的研究也是材料科学与工程研究的核心工作。传统的研究方法是通过试错法来改变结构进而测试性能,通过不断地实验,最终推演出组织-性能关系,但这种研究范式不仅研发周期长、成本高,而且很难将金属材料多个组织中某一个组织(或相)的影响剥离出来进行单一变量的研究。为了研究关键组织对材料性能的影响,一方面需要了解关键组织的本征性能,另一方面需要了解关键组织与其他组织之间的交互作用(包括界面的作用),即处于某种具体环境下关键组织的性能响应。随着研究手段的不断进步,目前人们可以使用纳米压痕[18]、微米柱压缩/弯曲[19,20]、透射电镜(TEM)下的原位加载实验[21]等方法测得材料中某一组织的力学性能。还可以使用扫描电镜(SEM)原位加载实验(包括原位电子背散射衍射(EBSD)、原位微观数字图像相关(μ-DIC)法等)[22~24]、同步辐射X射线衍射(XRD)或中子衍射等方法对多相材料中各组成相在与其他相间存在交互作用时的力学性能进行测试[25~27],也有学者将上述研究手段结合在一起,构建起多尺度的组织-性能关系研究方法[28]。通过这些实验手段可以精确了解关键组织的本征性能以及其对金属材料宏观性能的影响,为揭示关键组织对性能的影响奠定了基础。此外,快速发展的计算材料学为高效探索组织与性能的定量关系提供了巨大的帮助,这其中,有效衔接宏观有限元同时充分考虑材料显微组织变形机制的晶体塑性有限元方法对于理解材料组织和性能之间的关系具有重要意义[29]。科研人员通过晶体塑性有限元与原位实验相结合的方式探究了金属材料组织与性能的关系[30~33]。2008年美国提出集成材料计算工程(Integrated Computational Materials Engineering,ICME)的概念[34],并进一步发展成为著名的材料基因组计划[17]。材料基因组计划通过实验-计算-理论的集成创新,加速材料大数据技术的发展,培养具有材料基因组新思想和新理念的材料工作者,变革材料研发文化,加速新材料和高端制造业的发展[2,35],我国也部署了相关研究计划[2]。在材料基因组计划的影响下,国内外学者开展了大量的材料组织与性能之间关系的研究[36,37],相关研究思路、方法和成果也为本文提出的金属材料的组织定制提供了支撑和帮助。
在确定关键组织与性能的定量关联之后,即可根据性能需求设计金属材料中的关键组织,但如何准确制备出满足设计要求的关键组织是实现组织定制的另一核心工作。在材料成分体系基本确定的情况下,其关键组织的演化由材料热力学和动力学控制。因此厘清凝固、锻轧、焊接、热处理等热加工工艺中宏观工艺参数与材料微观组织演化之间的关系,进而通过宏观工艺参数调控组织演化过程是面向应用的金属材料组织定制的主要工作。研究金属材料在凝固、锻轧、焊接、热处理等热加工以及冷加工过程中的组织演变是材料加工领域最基础的工作,针对不同类型的材料都存在大量的加工工艺参数与组织演化之间关系的实验数据[40~44],可以为组织定制中的显微组织调控提供关键信息。但是以往的研究通常把金属构件的冷、热加工,甚至热加工过程的各个环节分割来考虑,而对于金属构件来说,其显微组织演化是具有典型遗传效应的,这种分割显然不利于从全流程角度调控金属材料中的关键组织。例如,以轴承领域应用最为广泛的GCr15轴承钢为例,其在特殊钢厂完成冶炼、凝固和锻轧加工,通常在完成热轧并空冷(或控制冷却)至室温后将轧材移交给下游轴承企业,此时轴承钢材料的显微组织为片层珠光体组织;轴承企业将热轧棒材(快速)加热奥氏体化后进行轴承套圈或滚动体的锻造(以下以轴承套圈为例介绍),锻后再次空冷至室温,重新获得片层珠光体组织;之后轴承企业将对锻造套圈毛坯进行球化退火处理,使片层珠光体组织转变成为粒状珠光体;再进行冷变形或粗加工;完成套圈的粗加工后,再进行淬火和回火热处理(一些产品还会有深冷处理),将材料的显微组织调整为基体马氏体+颗粒状渗碳体+少量残余奥氏体(也可能无残余奥氏体),最后进行轴承套圈的磨加工。因为GCr15钢是过共析钢,在钢厂锻轧后的片层珠光体中可能有一部分碳化物在随后复杂的热、冷加工过程中没有完全回溶至基体中,这些碳化物不仅C、Cr等含量与基体存在显著差异,而且硬度也明显高于基体,因此在后续的加工流程中会诱发微区能量/成分的不均匀分布,从而影响材料的组织演化,最终影响轴承的服役性能。因此,在组织定制中需建立全流程组织调控的思路,以获取各环节的关键信息,以及各环节间关键要素的传递规律,进而有针对性地设计目标技术方案,实现组织制备。除了利用传统的冷、热加工手段进行组织制备,近年快速发展的增材制造技术依靠温度梯度大、冷速快以及成分调控灵活等技术优点,为组织优化制备提供了更加灵活的手段,使用增材制造技术可制备出传统冷、热加工工艺下难以制备出的高性能金属材料[45,46]。除直接的物理实验之外,材料冷、热加工过程中多尺度全流程的模拟仿真对于获得更多加工过程的组织演化信息,揭示组织演化机理,提升组织制备的精准度也具有重要的意义。
在通过热、冷加工全流程调控实现组织制备后,对制备出的材料进行合理的考核是评价组织定制效果的必要环节,同时考核评价过程中获得的近服役工况材料响应数据对于优化组织定制同样具有极为重要的意义。因此,除了前文介绍的金属构件亟需加强近服役工况考核评价之外,使用当前快速发展的大数据、机器学习、人工智能等手段对考核评价过程中关键数据进行分析和再利用,将会大大提升组织定制的应用效果和实施效率。进一步来讲,如果能够获取从设计、生产、服役到失效的金属构件全生命周期关键数据,并对这些数据进行积累、分析、挖掘,将会大大促进金属材料组织定制的设计水平及研发效率,并可以进一步建立构件寿命相关的预测模型,以实现对金属零部件服役寿命的准确预测。
2 组织定制应用案例
M50轴承钢是高温轴承钢的代表性钢种,主要用于航空发动机主轴承等关键零部件上。发动机寿命和安全性的不断提升对航发轴承钢的寿命和可靠性提出越来越严苛的要求。然而,M50钢合金体系和显微组织演化复杂,且生产制造流程长,在实际应用中仍然存在诸多技术难题。本文以某应用场景下M50钢的性能需求为例,介绍根据疲劳性能要求,在控制钢的纯净度和宏观偏析基础上,通过研究碳化物的尺寸、类型、形貌及演化行为对疲劳性能的影响,实现对其组织要素的量化定制。
某应用场景对M50钢在± 900 MPa拉压疲劳载荷下的平均寿命L50要求为不低于1 × 108 cyc。根据上述应用的目标需求,基于图1所提出的组织定制的技术路线,首先根据国内外的研究成果分析了影响M50钢疲劳性能的关键因素。在通过双真空(真空感应+真空自耗)熔炼技术制备出O含量低于7 × 10-6的工业用超纯净M50轴承钢,且通过稀土处理进一步优化变质夹杂物的情况下,M50轴承钢中夹杂物尺寸和数量大幅降低,统计数据如图2所示。大量的实验数据显示此时夹杂物不再是疲劳失效的主要因素(最大夹杂物尺寸小于10 μm)。而对于M50高温轴承钢,其C、Cr、Mo、V含量高,在凝固时不可避免地产生大量沿晶界析出的一次碳化物。这些碳化物硬度显著高于基体,经过锻轧处理后呈带状分布在M50钢内部,如图3所示。研究[47]表明,M50钢中一次碳化物主要由富V具有fcc结构的MC型碳化物和富Mo具有hcp结构的M2C型碳化物组成,其中MC型碳化物的硬度显著高于M2C型碳化物。因此,对于M50钢,在其O含量和夹杂物得到控制之后,内部大尺寸碳化物就成为疲劳失效的主要因素[48,49],传统工艺制备的M50钢疲劳断裂绝大部分起源于粗大的一次碳化物,如图4所示。改善航发轴承钢碳化物粗大和分布不均匀的问题,根据M50钢服役寿命的目标要求,定制碳化物的尺寸、形貌和数量,是稳定提高M50轴承钢服役寿命的关键。
图2

图2 低氧稀土处理的双真空M50钢中夹杂物统计
Fig.2 Inclusions in the M50 steel manufactured by vacuum induction melting (VIM) + vacuum arc remelting (VAR) and low-oxygen RE treatment
图3

图3 M50钢中一次碳化物典型形貌
Fig.3 Typical morphology of primary carbides in M50 steel
图4
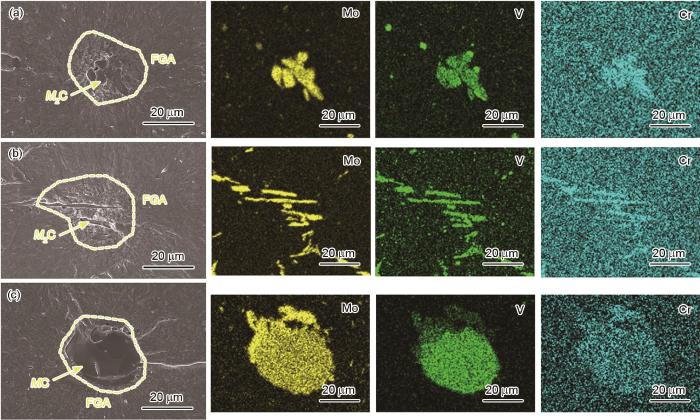
图4 M50钢疲劳试样中的裂纹萌生区域形貌及EDS
Fig.4 Morphology and EDS element mappings of crack initiation region in tension-compression fatigue specimens of M50 steel (a-c) (FGA—fine grain area)
进一步,瞄准M50钢疲劳寿命L50应达到1 × 108 cyc循环周次的技术指标,首先研究M50钢中一次碳化物的演化规律,发现凝固过程中C及其他合金元素在残余液相中的偏聚富集导致了一次碳化物形成。M50钢中一次碳化物主要有富Mo的M2C和富V的MC 2种类型,与尺寸小、呈椭球形态的MC碳化物相比,尺寸大、形态不规则的M2C碳化物与基体的协调变形能力更差,易引起应集中进而发生开裂,同时M2C碳化物在高温下不稳定,会发生向MC的转变。基于上述分析,确定了需要从真空感应、真空自耗、锻轧和热处理全流程对一次碳化物的演化进行调控的组织定制思路。
基于晶体塑性有限元模拟,将位错密度演化纳入裂纹形核判据,初步建立了基于位错演化的裂纹形核和扩展判据。通常,不可逆的位错滑移是造成疲劳裂纹形核和扩展的原因。位错结构(胞状位错、位错墙)随着循环载荷变得更加精细和尖锐,直到引起足够的硬化导致材料的局部裂纹形核。之后,裂纹尖端释放的位错在力的作用下处于平衡位置,而卸载时这些位错试图返回裂纹尖端。这个过程中难以复位的位错产生的残余Burgers矢量进一步导致了裂纹的扩展。基于此,将单个滑移系α上总的位错密度
式中,
式中,A和B代表相邻的2个晶粒, m 和 s 分别为滑移面的单位法向量和滑移方向。
式中,
临界储存能量密度
在确定关键组织的定制目标之后,通过锭型的合理控制和自耗凝固工艺优化,可有效改善宏观偏析缺陷,切头去尾后,控制钢锭的宏观偏析。具体地,为了提高铸坯冷速,在铜模和凝固壳之间的气隙中充入冷He气,通过优化流量和压力控制,实现了基于充氦处理的碳化物细化。在锭型设计方面,发现随着自耗坯直径的增加,二次枝晶臂间距和宏观偏析呈现倒置关系,导致碳化物尺寸先减小后增大。通过优化设计,发现当把自耗坯直径控制在约300 mm时,碳化物尺寸最小,从而明确了铸坯最佳尺寸范围。同时,利用稀土元素与钢液中的S、O结合形成细小稀土氧硫化物可以作为MC碳化物的形核基底,促进MC形核,起到细化的作用,并起到固溶稀土抑制枝晶生长,增加碳化物形核位置的作用,降低了凝固后一次碳化物的尺寸。
为了进一步细化共晶碳化物的尺寸,系统研究了热-力作用下的碳化物转化和细化行为。在锻轧工艺方面,基于M2C碳化物高温不稳定特性,研究了高温扩散工艺对一次碳化物演化的影响。发现其转变存在2种模式:碳化物与基体界面形核生长及碳化物内部缺陷原位转变。为了充分发挥扩散界面在碳化物转化细化方面的重要作用,借助位错工程概念,提出在锻轧过程中添加预变形高温扩散工艺,配合合理的锻轧变形工艺,不仅碎化M2C碳化物,同时增加相界面和位错密度,促进扩散相变,细化MC碳化物。此外,基于2种一次碳化物在高温下溶解和粗化行为不同的热力学和动力学特点,设计了一种新型热-力联合处理思路,有效促进了M2C向MC碳化物的转变,且进一步大幅降低了M50钢中一次碳化物的尺寸,获得一次碳化物尺寸≤ 20 μm的显微组织,如图5所示,材料的疲劳性能测试结果如图6所示。其拉压疲劳寿命达到了1 × 108 cyc,而且疲劳寿命测试结果的稳定性也显著提升,即很好地实现了组织定制。
图5
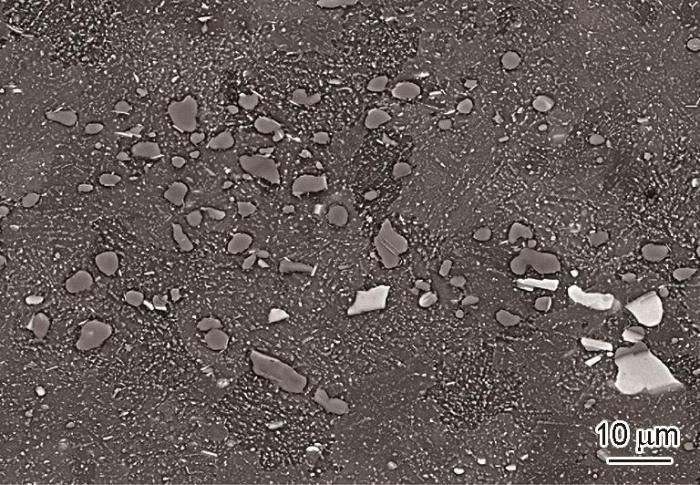
图5 根据组织设计制备出的一次碳化物尺寸≤ 20μm的M50钢显微组织
Fig.5 SEM image of the tailored microstructure of M50 steel (The size of primary carbide ≤ 20 μm)
图6

图6 不同工艺制备的M50钢± 900 MPa拉压疲劳寿命Weibull分布曲线(S1为组织定制控制一次碳化物尺寸≤ 20 μm材料曲线,S2为常规生产工艺不控制一次碳化物材料曲线)
Fig.6 Weibull distribution curves of ± 900 MPa tension-compression fatigue life of M50 steel prepared by different processes (S1 and S2 curves are the fatigue life of M50 steel manufactured by microstructure tailoring technology and normal technology, respectively)
未来将继续完善上述基于位错密度储能计算疲劳寿命的模型,推动不同碳化物类型、尺寸和分布对疲劳性能的定量影响研究,即在锁定了碳化物是疲劳裂纹萌生的源头后,根据寿命要求,发展位错密度储能算法,开展介观和微观尺度基于位错密度的预测模型计算,从而定制碳化物的尺寸、形貌等相关要素,为实验提供依据,减少实验量,提高制备效率和精度。同时,由于轴承钢在拉压疲劳和接触疲劳下的失效机制有显著差异,未来还将根据轴承的滚动接触疲劳性能要求,开展相关组织定制工作。
3 总结与展望
展望金属材料学科的发展方向,本文提出了组织定制的新学术理念,强调以目标性能需求为导向,开展组织设计、模拟计算、制备和评价等研究工作,进而构建组织与性能的定量化关系。组织定制理念的提出将研究方法从以往的正向设计转化为逆向设计,不但降低成本和时间,也有利于精准控制材料性能,为金属材料的绿色制备提供新思路。并以M50航发轴承钢为例,以共晶碳化物控制为核心,借助于晶体塑性有限元计算,基于临界位错密度储能模型,对一次碳化物的尺寸进行了定制,满足了疲劳寿命的要求。
为实现组织定制,一方面需要建立金属材料全生命周期研发测试平台,系统研究材料热加工、冷加工以及服役工况中材料组织的演化规律及其对性能的影响,以及各环节之间的要素传递规律,为精确设计、制备和评价组织提供基础支撑;另一方面,发展数据科学与模拟计算也十分重要且必不可少。未来随着研究工作的深入、数据积累和模型建立,组织定制将会越来越精准,在科学研究和工程应用中将会发挥更大的作用,也是学科发展的必然。
来源--金属学报