分享:基于热力学计算与机器学习的增材制造镍基高温合金裂纹敏感性预测模型
穆亚航1,2, 张雪1,2, 陈梓名3, 孙晓峰,1, 梁静静
,1, 李金国1, 周亦胄1
1
2
3
利用实验和热力学计算研究了镍基高温合金的增材制造裂纹敏感性,发现镍基高温合金增材制造裂纹以热裂纹为主,热裂纹敏感性系数(HSC)与实测裂纹面积分数相关性高。基于实验数据和热力学计算结果,建立高温合金裂纹敏感性的机器学习预测模型,该模型具有良好的预测和泛化能力,在训练集上和验证集上的相关性系数(R2)分别达到0.96和0.81,可以快速有效地计算出高温合金的热裂纹敏感性。采用SHapley Additive exPlanation (SHAP)方法对模型中的输入参数进行特征分析,获得了合金元素对裂纹敏感性的影响规律,并根据SHAP值对合金元素的裂纹敏感性影响进行了排序。结果表明,沉淀强化元素Ti、Al和微量元素C、B对镍基高温合金的裂纹敏感性的影响较大,其余合金元素对裂纹敏感性的综合影响排序为:Re > W > Cr > Mo > Ta > Co。
关键词:
发展复杂型腔结构高温合金构件已经成为提升航空发动机和燃气轮机整机性能的关键手段。然而,随着构件结构的精细化和复杂化,传统熔模精密铸造、锻造和粉末冶金等技术在制备这些构件方面面临较大挑战。为此,急需发展一种制备复杂结构高温合金构件的新型技术。增材制造技术集设计与制造于一体,在制备多孔、网格、空心等构件方面具有明显优势[1]。但目前大多数镍基高温合金的增材制造工艺性较差,在制造过程中容易产生裂纹,难以直接用于增材制造工艺,严重阻碍了高温合金在增材制造中的应用[2]。鉴于此,许多研究人员致力于寻找一种增材制造工艺性优良的高性能高温合金。
裂纹敏感性是评价合金增材制造过程中开裂倾向的关键参数之一。建立裂纹敏感性评价标准可以为寻找和设计低裂纹敏感性的高温合金提供指导。目前,研究人员已经从理论和实验2方面提出了一些裂纹敏感性的评价手段和测试方法。在理论方面,Rappaz、Drezet和Gremaud[3]基于临界变形速率这一概念指出,当超过临界变形速率时在糊状区会诱发孔洞,从而导致开裂,共同提出了RDG准则;Kou[4]根据晶粒生长速率和液体补缩的关系提出了凝固开裂指数;Yu等[5]根据γ'相析出速率的大小提出了应力时效开裂指数;Xu等[6]基于枝晶干/枝晶间的差异关系提出了增材制造镍基合金开裂准则。每种裂纹敏感性模型的提出都有其特殊的物理意义,一般可以通过热力学计算软件和Scheil-Gulliver凝固模型来获得具体裂纹敏感性数值,但是难以实现将高通量计算应用于合金的设计与筛选。在测试方法方面,一般是通过在拘束应力下利用临界裂纹数量和长度来评估合金的裂纹敏感性,该方法广泛地应用于铝合金[7]、镁合金[8],但对高温合金而言,目前除了Jain[7]提出的热裂行为测试方法外,并没有适合高通量实验的测试方法,而且高温合金的测试成本太高。因此,急需一种快速、有效的高温合金裂纹敏感性预测方法。
随着材料基因工程的快速发展,机器学习(machine learning,ML)在材料科学中的应用越来越广泛。它通过从数据中学习嵌入式知识,并从中寻找数据的内在规律(材料学知识),能够实现由特征参数(合金成分)到目标参数(合金性能)的高通量计算,为材料设计和性能预测提供一种有效的方法[9~11]。Zhu等[12]利用高通量实验和机器学习方法建立了钛合金的成分-微观结构-力学性能模型,并通过该模型准确预测了钛合金随热处理温度和时间变化的组织演变规律。Menou等[13]针对镍基单晶高温合金的高温蠕变性能,建立了蠕变断裂应力的Gauss过程回归模型,通过数据挖掘和相图计算成功筛选出多种极具应用前景的镍基单晶合金。同时,机器学习在高温合金的硬度、拉伸性能和疲劳性能的预测方面也得到了成功应用[14~17]。鉴于机器学习方法的普适性,也可将其用于增材制造过程中高温合金裂纹敏感性的预测。
本工作分析了镍基高温合金的裂纹敏感性,设计了397组单一元素变化合金和999组随机成分合金,利用热力学计算获取了大量合金的裂纹敏感性系数,并通过机器学习方法构建了一个高温合金增材制造过程中裂纹敏感性的预测模型。基于该模型,探讨了不同合金元素对高温合金增材制造过程中裂纹敏感性的影响规律,并给出了不同合金元素对裂纹敏感性的影响顺序,以期为增材制造高温合金成分优化提供参考。
1 研究方法
本工作的研究思路和工作流程包括以下几个部分:增材制造实验、热力学计算、数据库建立、机器学习模型训练、模型评估以及合金裂纹敏感性预测,如图1所示。
图1

图1 镍基合金裂纹敏感性预测模型建立流程
Fig.1 Workflow for crack susceptibility prediction of Ni-based superalloy (FR—freezing range, CSC—crack susceptibility criterion, HSC—hot-tearing susceptibility criterion, SCI—solidification cracking index, SAC—strain age cracking index, MSAC—index of strain age cracking by mass-percentage, ABR—AdaBoost regression, BR—Bagging regression, GBR—gradient boosting regression, RFR—random forest regression, KNN—K-nearest neighbors, SVR—support vector regression, LR—linear regression, R2—correlation coefficient, RMSE—root mean squared error, MAE—mean absolute error)
1.1 增材制造镍基高温合金成分设计
本工作采用的基础合金是一种Ni-Co-Cr-W-Mo-Ta-Al-Ti多元合金,合金名义成分(质量分数,%)为:Co 8,Cr 8,W + Mo 10,Al 4.5,Ti 1,Ta 5,C 0.08,B 0.015,Ni余量。在此合金基础上,设计42种不同成分的高温合金进行增材制造实验,且该42种合金成分均在表1的成分范围内。此外,按照表1所示的范围和步长设计了397种单一元素含量变化的镍基高温合金及999种随机取样的镍基高温合金,作为热力学计算以及后续机器学习模型训练的原始数据库。
表1 增材制造镍基合金的成分设计范围 (mass fraction / %)
Table 1
Range | Co | Cr | W | Mo | Al | Ti | Ta | C | B | Ni |
---|---|---|---|---|---|---|---|---|---|---|
Max. | 14 | 14 | 14 | 6 | 12 | 4 | 7 | 0.3 | 0.2 | Bal. |
Min. | 2 | 2 | 2 | 0 | 2 | 0 | 0 | 0 | 0 | Bal. |
Step | 0.2 | 0.2 | 0.2 | 0.2 | 0.2 | 0.2 | 0.2 | 0.02 | 0.005 | - |
1.2 热力学计算
由于增材制造过程中镍基高温合金会出现不同类型的裂纹且具有不同的开裂机制,为了定量评价合金的裂纹敏感性,使用6种裂纹敏感性系数来综合评估合金的裂纹敏感性,如表2[4,5,18~21]所示。凝固温度区间(freezing range,FR)通过衡量液相线与固相线的温度差来评判合金的热裂倾向,凝固温度区间越大,合金的热裂倾向越大;热裂纹敏感性系数(crack susceptibility criterion,CSC)和(hot-tearing susceptibility criterion,HSC)通过衡量合金凝固过程中应力集中时间(温度区间)与应力松弛时间(温度区间)的比值来评判合金的热裂倾向,一般认为2者的比值越大则合金的热裂倾向越大;凝固开裂因子(solidification cracking index,SCI)则是通过凝固末期温度随固相含量的平方根的导数来评判合金的热裂倾向,数值越大则合金的热裂倾向越大;应变时效裂纹因子(index of strain age cracking by mass-percentage,MSAC)是通过比较合金中的Al、Ti、Nb、Ta 4种沉淀强化元素(γ'相形成元素)的含量来评价合金的固态开裂倾向,沉淀强化元素含量越高γ'相含量越高,则固态开裂倾向越大;而另一种应变时效裂纹指数(strain age cracking index,SAC)是通过γ相的变化速率间接获得γ'相的析出速率,从而评判合金的应力时效开裂倾向,其数值越大则合金的开裂倾向越大。
表2 增材制造镍基高温合金的裂纹敏感性系数[4,5,18~21]
Table 2
Type of crack | Crack susceptibility criteria | Formula | Ref. |
---|---|---|---|
Hot-tearing crack | FR |
|
[18] |
CSC |
|
[19] | |
HSC |
|
[20] | |
SCI |
|
[4] | |
Solid-state crack | SAC |
|
[5] |
MSAC |
|
[21] |
基于上述6种裂纹敏感性系数,本工作使用Thermo-Calc热力学软件与镍基高温合金TCNI10数据库分别计算合金相组成随温度的变化曲线、固相含量随温度的变化曲线和合金的CSC。随后,通过基于TC-python的python脚本对获得的热力学数据进行计算,以获得FR、HSC、SCI和SAC,而MSAC则直接由合金成分计算可得。
1.3 机器学习
1.3.1 数据筛选
由于热力学数据库中数据有限,有些成分在热力学计算中无法获得收敛结果,因此没有得到相应的裂纹敏感性值,这些成分未被输入到机器学习的数据库中。数据归一化有利于提高机器学习模型的准确性,所以本工作采用最大值-最小值归一化方法[22]对裂纹敏感性系数进行归一化,如
式中,a为某一数据点的值,a'为数据点a对应的归一化值,amin和amax分别为原始数据的最小值和最大值,
1.3.2 模型训练
本工作采用GridSearchCV (一个用于搜索机器学习模型超参数值的python函数)与多种机器学习算法,以找到预测性能最优的机器学习模型及其对应的最优超参数。本工作共采用7种回归算法用于筛选和训练机器学习预测模型,包括线性回归(linear regression,LR)、支持向量回归(support vector regression,SVR)、AdaBoost回归(AdaBoost regression,ABR)、K-近邻回归(K-nearest neighbors,KNN)、随机森林回归(random forest regression,RFR)、梯度提升回归(gradient boosting regression,GBR)和Bagging回归(Bagging regression,BR)算法。
1.3.3 模型验证与评价
采用五折交叉验证法对模型进行验证,即将每个数据集随机分为五折,其中,四折作为训练集,一折作为验证集,共测试5次,5次测试的平均预测能力代表了模型的性能。利用相关性系数(correlation coefficient,R2 )、均方根误差(root mean squared error,RMSE)和平均绝对误差(mean absolute error,MAE)来评估机器学习预测模型:
式中,i为数据点序号,n为数据点总个数,
1.4 实验方法
1.4.1 高温合金母合金冶炼与Ar气雾化制粉
根据1.1节中的设计原则筛选出42组合金进行母合金制备,采用25 kg真空感应炉进行母合金熔炼,然后进行Ar气雾化制粉,筛选出粒径为53~150 μm的粉末进行下一步增材制造实验。
1.4.2 增材制造试样制备
通过自主研发的激光定向能量沉积(laser direct energy deposition,L-DED)系统制备了42种成分的高温合金试样。采用尺寸为17 mm × 17 mm × 17 mm 的镍基高温合金基板,使用400号SiC砂纸对其表面进行打磨,并使用C3H6O和C2H5OH清洗后进行L-DED实验。L-DED工艺参数为:激光功率1700 W (CO2激光器),扫描速率1100 mm/min,送粉速率12 g/min,光斑直径2 mm,Ar气流速为40 L/min,采用往复交叉光栅式扫描策略,层间旋转90°,搭接率40%。最终所制备样品尺寸为16 mm × 16 mm × 60 mm。
1.4.3 组织分析与裂纹统计
用电火花线切割距增材制造样品表面2 mm处切割出矩形试样,试样经打磨和抛光后进行裂纹统计,每个样品取相同位置的一个截面进行统计。利用DM4 M金相显微镜(OM)的铺展扫描功能对金相试样在10 mm × 30 mm视野范围内的裂纹宏观形貌进行表征,再使用Image Pro Plus软件对裂纹进行定量统计,得到裂纹面积分数,用于衡量合金的裂纹敏感性。随后用50 g CuCl2 + 100 mL HCl + 100 mL C2H5OH溶液对金相试样进行腐蚀。使用MIRA4扫描电子显微镜(SEM)观察样品的组织和裂纹的微观结构。使用附带能谱仪(EDS)的Talos F200X型透射电子显微镜(TEM)对样品的析出相进行鉴定和观察。
2 结果及讨论
2.1 沉积态试样裂纹统计与热力学计算结果
图a2和b4#合金(Ni-8Co-10Cr-8W-4.5Al-1Ti-5Ta)增材制造试样中裂纹的微观结构SEM像。在较低放大倍数下能够观察到裂纹沿晶界开裂的特征,同时还伴随有少量液膜(图2a),在较高放大倍数下可观察到裂纹处有明显的枝晶结构(图2b),据此可以判断出该合金主要以热裂纹为主。随后在OM下对裂纹进行观察,42种合金的裂纹面积分数和热力学计算的裂纹敏感性值如图3所示。由图3a可知,42种合金中均出现了不同程度的裂纹,由于所有合金均采用相同的工艺参数,能够根据裂纹面积分数对不同合金裂纹敏感性进行比较。由图3b可知,合金的凝固区间FR高则SCI也较高,而MSAC变化不大。除了42#合金(Ni-8Co-10Cr-10W-5Mo-6Re-4.5Al-1Ti-5Ta)的SAC异常高外,其他试样的SAC无明显变化,这是由于42#合金与其他合金的相变过程不同,高固溶元素含量导致针状拓扑密排 (topologically close-packed,TCP)相析出(图2c),由EDS分析发现该相为富W、Mo和Re的TCP相(图2d),这一相变过程消耗了大量固溶强化元素,严重影响了γ相的含量,而SAC是根据γ相析出速率来间接判断γ'相析出速率的,因此42#合金的SAC达到了5.57 × 10-3 K-1,而其他合金的SAC在0~2.5 × 10-3 K-1范围内。据此可初步判断42种合金的开裂主要是由于高的热裂纹敏感性导致的,但仍无法准确判断几种热裂纹敏感性系数与裂纹面积分数之间的定量关系。
图2
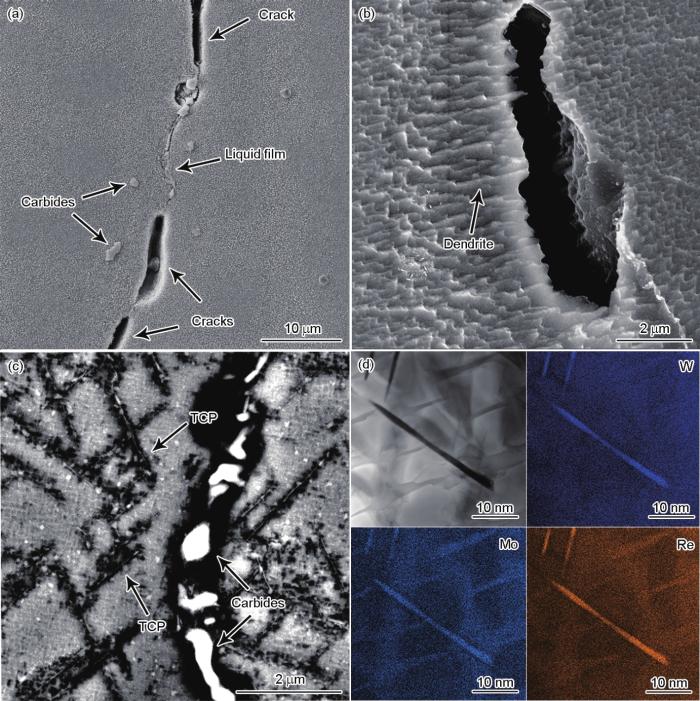
图2 沉积态下4#合金(Ni-8Co-10Cr-8W-4.5Al-1Ti-5Ta)试样中的微观组织SEM像,TCP相的BSE像、TEM像及EDS元素面分布图
Fig.2 Low (a) and high (b) magnified SEM images of cracks in as-built 4# (Ni-8Co-10Cr-8W-4.5Al-1Ti-5Ta) sample, corresponding BSE image of TCP phase (c), bright field TEM image and EDS elemental maps of TCP phase (d) (TCP—topologically close-packed)
图3
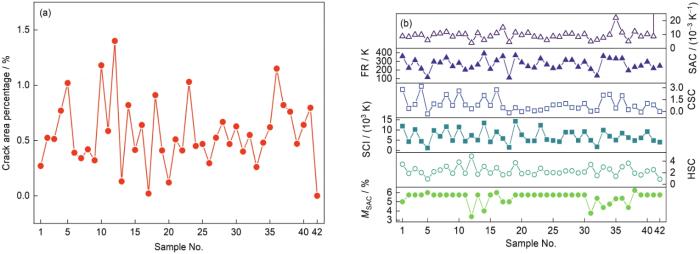
图3 不同合金的裂纹面积分数及裂纹敏感性系数
Fig.3 Crack area percentages (a) and calculated crack susceptibility criteria (b) of different superalloys
2.2 裂纹敏感性系数优选
为了得到裂纹敏感性系数和裂纹面积分数之间的定量关系,将实验获得的裂纹面积分数(crack area percentage,CAP)和热力学计算获得的裂纹敏感性系数进行Pearson相关性分析,如图4所示。图4对角线为各变量的频率分布直方图,从图中可以看出,42种合金的裂纹面积分数和裂纹敏感性系数分布较为集中,合金元素的变化会引起数值少量波动。
图4
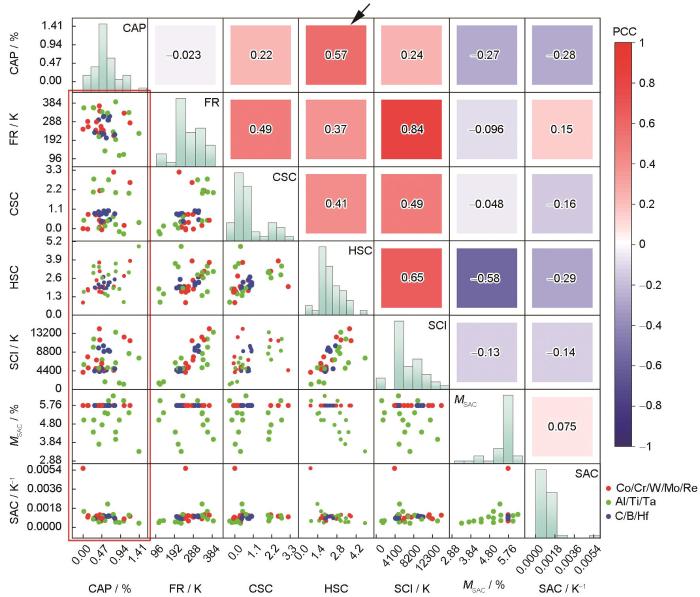
图4 各裂纹敏感性系数与裂纹面积分数的关系图
Fig.4 Sactterplot matrix and Pearson correlation map of crack area percentage and crack susceptibility criteria (The lower triangular matrix is scatterplot matrix between each pair of variables, the diagonal is the frequency distribution histogram of each variable, and the upper triangular matrix is Pearson correlation map. The red frame line part represents the scatter plot of CAP and crack sensitivity, and the arrow refers to the crack susceptibility criterion with the highest correlation with CAP. Red, green, and blue dots represent the alloys that only change the solid solution elements, the γ′ forming elements, and trace elements, respectively. CAP—crack area percentage, PCC—Pearson correlation coefficient)
图4左侧红色框线部分为6种裂纹敏感性系数与裂纹面积分数的散点图。由图可知,HSC与CAP呈较强的正相关性,通过改变微量元素含量获得的数据点相对集中,其原因是元素添加量较少,对裂纹敏感性系数和裂纹面积分数的影响幅度较小,而沉淀强化元素影响较大。2种固态裂纹敏感性系数MSAC和SAC与裂纹面积分数的相关性不大。由于MSAC只考虑了Al、Ti、Nb和Ta这4种元素,对于只改变固溶强化元素和微量元素的合金来说,其具有相同的Al、Ti和Ta含量,因此这些合金的MSAC没有区别,如图4中CAP与MSAC散点图中的红色和蓝色数据点所示。沉淀强化元素对SAC的影响较大,其他元素对SAC的影响较小。
裂纹面积分数和不同裂纹敏感性系数的Pearson相关性系数如图4右上部分所示。由图可知,对于CAP而言,FR没有明显的相关性,SAC和MSAC显示出弱的负相关性,CSC和SCI显示出弱的正相关性,而HSC显示出较强的正相关性,说明HSC可以更好地评价镍基高温合金的裂纹敏感性。因此,裂纹面积分数与热裂纹敏感性系数均有较强的正相关性,表明本工作所研究的增材制造镍基高温合金的裂纹以热裂纹为主,这与图2中裂纹SEM像的分析结果一致。有趣的是,FR与SCI显示出强正相关性。从计算的裂纹敏感性系数值和实测的裂纹统计结果之间的比较来看,单一裂纹敏感性系数在对裂纹敏感性进行预测时,偏差较大,因此,本工作中采用了FR、CSC、HSC和SCI 4种热裂纹敏感性系数来评价高温合金的裂纹敏感性,作为后续机器学习预测模型的目标变量。
2.3 单一元素对热裂敏感性的影响
确定单一元素对合金裂纹敏感性的影响在常规的合金设计过程中起着至关重要的作用。本工作按照表1所示的范围和步长改变单一合金元素含量设计了397种合金,并利用这些合金分析了合金元素对裂纹敏感性的影响。由图4相关性分析结果可知,HSC与CAP相关性最高,文献[23]中也将HSC作为镍基合金热裂纹的主要判据,因此,本工作通过分析合金元素变化对HSC的影响来间接判断元素对裂纹敏感性的影响。
图5给出了不同元素对HSC的影响规律。可见,当其他元素保持不变(与基础合金相同)时,HSC随着单一元素含量的变化呈现出一定趋势的变化。HSC随着Co含量的增加而缓慢升高,随着Cr、W和Mo含量的增加而降低。HSC随其他元素的变化则更为复杂。在图5所示的范围内,随着Al含量的增加,HSC先升后降,之后又上升,Al的最佳添加量约为7.5% (质量分数,下同),应避免在4.2%~5.0%的范围内。随着Ti含量的增加,HSC首先增加,当Ti = 1.2%时达到最大值,然后下降。与Ti一样,Ta也存在类似的规律。对于微量元素C和B,在较低的水平上,HSC随着C和B含量的增加而明显增加;当元素添加量较多时,C含量对HSC影响不大,但HSC随着B含量的继续增加而减少。然而,由于析出相的形成,C和B的添加量不会太多,通常C的添加量为0~0.6%,B的添加量为0~0.1%,甚至有些高温合金并不添加B,因为硼化物的产生会降低合金的初熔温度,硼化物是液态薄膜的形成源,而且硼化物影响了合金元素的再分配,极易促进热裂纹的产生[24]。研究[25]表明,添加少量的B有利于提高高温合金的蠕变性能,所以为了均衡裂纹敏感性和合金力学性能,结合图5的计算结果,B含量应控制在0.005%以内。
图5
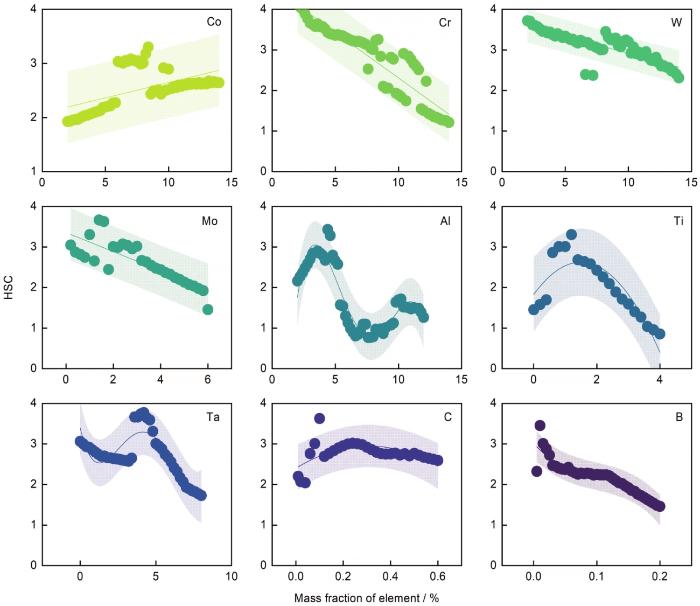
图5 热裂纹敏感性(HSC)随单一元素含量的变化趋势
Fig.5 Trend of HSC variation with single element content
值得注意的是,虽然能够通过HSC随单一元素含量的变化获得不同元素对热裂倾向的影响规律,但结果与其他研究的结果不太相符,尤其是Al和Ti等沉淀强化元素的最优添加范围,一般认为Al、Ti含量较低时合金的抗裂能力强,例如文献[21]报道的增材制造用镍基高温合金ABD-900AM中的Al和Ti含量分别为2.11%和2.39%。由于各元素之间存在相互作用,而且在增材制造过程中元素存在显著的微观偏析现象,当Al、Ti含量过高时,容易在枝晶间产生γ/γ′共晶[26],非平衡凝固无法模拟出增材制造的微观偏析现象,故热力学计算的裂纹敏感性结果与传统的材料学知识不太相符。因此,为了准确评判合金的增材制造裂纹敏感性,需要进一步对元素影响进行探讨,具体结果将在后续研究中给出。
2.4 机器学习模型的建立与验证
2.4.1 建立原始数据库
在第2.3节中,仅通过改变单一元素含量来设计的397种合金,可以获得各单一元素变化对裂纹敏感性的影响趋势,及各合金元素最佳的添加范围。但是该方法没有考虑元素之间的相互作用,由此类数据训练出的机器学习模型不足以获得良好的预测精度。为了获得足够的数据来训练高温合金裂纹敏感性的机器学习预测模型,本工作按照表1所示的成分设计范围通过python中sample函数随机选择999种合金,用于建立机器学习模型数据库。本工作所建立的数据库包含10种合金元素和5种裂纹敏感性系数共15个特征参数。图6显示了数据库中所有合金的4种裂纹敏感性数值的分布状态,呈现出了一定的规律:MSAC高的合金大多分布在左下角,而它们的HSC和SCI的数值较低,高FR点的分布较为随机。这说明FR并不能准确评价合金的裂纹敏感性,这与相关性分析结果相一致。高MSAC并不一定引起合金的高热裂纹敏感性,这一点与实验得到的普遍结果不一致,其原因为Al、Ti等沉淀强化元素极易发生微观偏析[6],在凝固前沿形成γ/γ'共晶,在热循环和内应力的作用下优先开裂。
图6
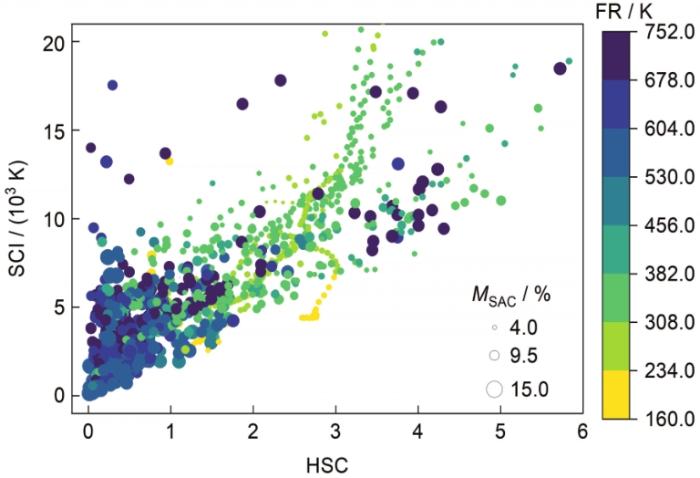
图6 镍基高温合金增材制造裂纹敏感性数据库数据散点图
Fig.6 Scatter plot of the Ni-based superalloys in the dataset, demonstrating the crack susceptibility pattern of different alloys by four criteria
2.4.2 模型建立
为了筛选出一种适用于增材制造高温合金裂纹敏感性评估的机器学习算法,本工作采用了SVR、BR、GBR、RFR、LR、KNN和ABR共7种回归算法对训练集数据进行训练。图7显示了这7种回归算法在训练集上得到的机器学习模型的R2、RMSE和MAE。RFR算法在训练集上的平均R2、RMSE和MAE分别为0.985、0.022和0.012,表明该算法在训练集上具有良好的预测结果。因此,RFR回归算法被选为本工作的机器学习预测模型的核心算法。为了提高机器学习预测模型的准确性,通过梯度寻参函数GridSearchCV搜索得到基于RFR算法的机器学习模型的最优超参数,为min_samples_leaf = 1、max_depth = 50、n_estimators = 121和max_features = log。
图7
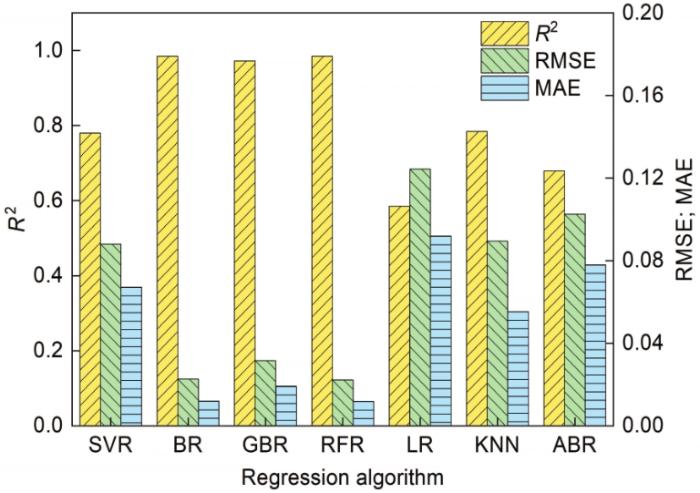
图7 不同算法在训练集的拟合效果
Fig.7 R2, RMSE,and MAE of machine learning models on training sets
2.4.3 模型评价
通过上述部分建立了基于RFR算法和最优超参数的机器学习模型。为了评价机器学习模型对4种不同裂纹敏感性系数的预测能力,将模型预测值与热力学计算值绘制为散点图,如图8所示。图中数据点越靠近45°对角线(图8中的虚线所示),表示预测值与热力学计算值越一致,进而证明该模型拟合效果良好。通过
图8
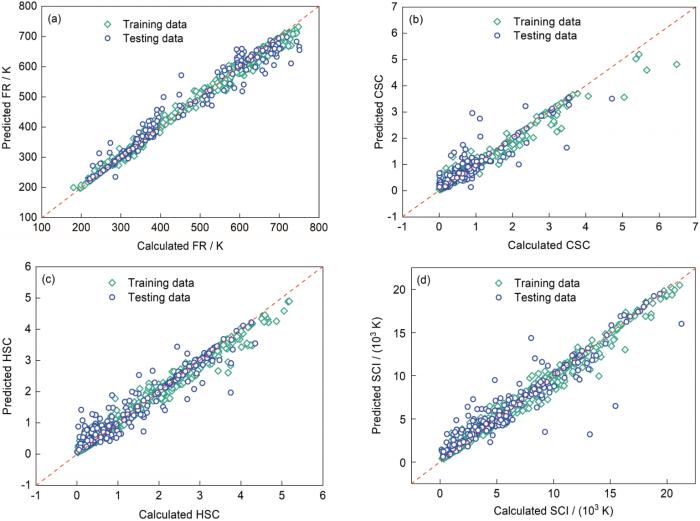
图8 机器学习(ML)模型对不同裂纹敏感性系数在训练集中的拟合效果
Fig.8 Performance of machine learning (ML) models on training and test sets for different crack susceptibility criteria
(a) FR (b) CSC (c) HSC (d) SCI
2.4.4 模型验证
为了进一步验证所得裂纹敏感性机器学习预测模型的准确性与普适性,将本工作中实验所得合金和已报道合金的成分代入模型中,对模型给出的预测值与实际值(热力学计算值)进行比较,如图9所示。由图可知,该模型在验证集上的预测效果良好,CSC、SCI、HSC和FR的R2分别为0.80387、0.7406、0.86993和0.82579,机器学习模型在验证集的综合R2为0.81。因此,本工作建立的机器学习预测模型具有良好的泛化能力,在更大范围内也能有效地预测镍基高温合金的裂纹敏感性。
图9
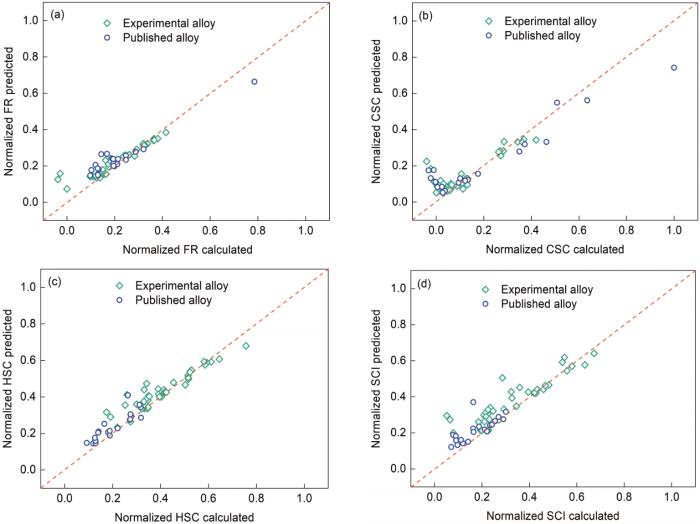
图9 机器学习模型对不同裂纹敏感性系数在验证集中的预测效果
Fig.9 Performance of ML models on validation sets for different crack susceptibility criteria
(a) FR (b) CSC (c) HSC (d) SCI
2.5 裂纹敏感性元素影响规律
机器学习模型能够对大量数据的内在规律进行学习探索,但难以对模型所得的内在规律进行解释,而SHAP (SHapley Additive exPlanation)方法能够对机器学习模型特征参数进行重要性评价,因此可以根据SHAP值对特征参数加以排序,进而分析各特征参数对预测结果的影响[16,27]。
4种裂纹敏感性系数的机器学习预测模型的SHAP值如图10a~d所示。由图可知,高温合金中的合金元素对裂纹敏感性系数均有所影响,并且根据SHAP值排序结果得知,合金元素对4种裂纹敏感性的影响规律并不一致。为了评估元素对裂纹敏感性的综合影响,根据平均SHAP值对元素的重要性进行排序,如图10e所示。由图可知,4种关键元素Ti、Al、C、B对热裂纹敏感性表现出显著的促进作用,其中Al和Ti是沉淀强化元素,C和B是微量元素,均对合金的凝固过程有明显影响,故这4种元素对热裂纹的影响比其他元素更大。因此,需要严格控制这4种元素的添加量。Re在合适的计量范围内是抑制热裂纹的有利元素,在图10a和c中,Re的SHAP值相对较低,从图10d可以看出,Re的红色散点位于y轴的左侧,这说明Re的增加可以显著降低CSC值,即Re表现出较大的绝对SHAP值,且在合适的范围内对热裂纹可以起到抑制作用,但需要严格控制W、Mo和Re的添加量,3者含量过高容易引起合金内产生TCP相(图2c和d)。因此,除Ti、Al、C和B外,其余6种合金元素对裂纹敏感性的综合影响排序为:Re > W > Cr > Mo > Ta > Co。
图10
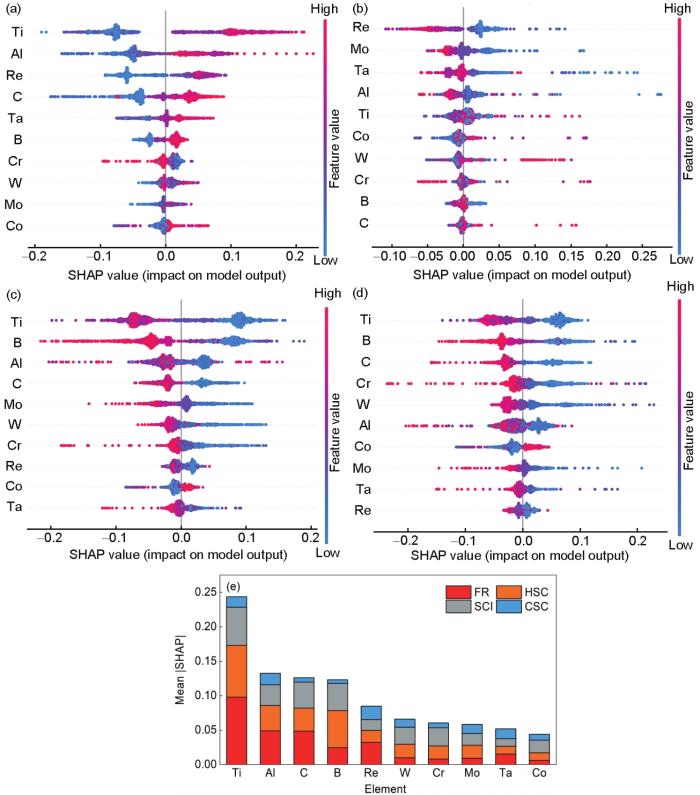
图10 机器学习裂纹敏感性预测模型特征参数的重要性评估
Fig.10 SHAP values of ten elements for FR (a), CSC (b), HSC (c), and SCI (d) for each data; ranked mean absolute value of SHAP values of ten selected features for crack susceptibility (e) (SHAP—SHapley Additive exPlanation)
一般来说,高温合金中的合金元素通常分为3类:固溶强化元素、沉淀强化元素和微量元素(晶界强化元素)[28]。这3类合金元素在多晶和定向凝固的高温合金中对合金的强度有不同程度的贡献。为了简化合金设计过程,可以从这3类元素的选择与添加量来进行设计。从图10e可以看出,对于固溶强化元素,Co、Re、Cr是首选,W和Mo对裂纹敏感性的影响较大,这与元素的偏析程度有关。研究[29~31]发现,在固溶强化元素中W和Mo的偏析程度较大,易在晶界或晶内产生富(W, Mo)元素的碳化物,而这种碳化物与(Ti, Ta)C相比,对合金的抗裂性能是不利的。根据图10e可知,对于沉淀强化元素,选择顺序是Ta、Al、Ti。对于微量元素的选择,C和B对合金的裂纹敏感性均有较大影响,因此应严格控制C和B的含量在较低水平。除C和B外,还可以考虑添加Zr、Hf、V等元素以强化晶界、增强合金的抗裂性[32],但在本工作中并未涉及这些元素,需要对微量元素的选择和添加量进行进一步研究。目前,已有学者[21,33,34]通过调整合金元素开发了一系列增材制造专用高温合金,但是镍基高温合金的强度与可打印性之间的权衡还需要进一研究,目前来看,明晰合金元素对增材制造裂纹敏感性的影响规律还需要开展大量相关工作。
3 结论
(1) 制造了42种实验合金的增材试样,通过实测裂纹面积分数和热力学计算裂纹敏感性系数,表明热裂纹是增材制造镍基高温合金的主要开裂形式。
(2) 建立了基于热力学数据的机器学习预测模型。该模型能够准确地给出镍基高温合金的增材制造裂纹敏感性系数值,具有较强的预测能力和泛化能力,在训练集和验证集上的准确性分别达到0.96和0.81。
(3) 分析了元素对镍基合金增材制造裂纹敏感性的影响。机器学习模型SHAP分析的结果显示,针对镍基合金增材制造裂纹敏感性,沉淀强化元素Ti、Al和微量元素C、B对镍基高温合金的裂纹敏感性的影响较大,其余合金元素对裂纹敏感性的综合影响排序为:Re > W > Cr > Mo > Ta > Co。
来源--金属学报