分享:汽油发动机气门弹簧断裂失效分析
胡 鹏,江仲佶,祁学军
(神龙汽车有限公司,武汉 430056)
摘 要:某汽油发动机气门弹簧在台架试验中发生了早期断裂失效.采用断口观察和分析、化学成分分析、金相检验、硬度测试等方法,对气门弹簧断裂的原因进行了分析.结果表明:气门弹簧断裂的性质为疲劳断裂,气门弹簧断裂的原因为表面存在磨损,导致弹簧的疲劳强度和疲劳寿命下降.
关键词:气门弹簧;磨损;疲劳断裂
中图分类号:TG115.2 文献标志码:B 文章编号:1001G4012(2017)07G0507G03
气门弹簧是发动机配气系统中的一个关键零件,其作用是保证气门座与气门的气密性,吸收气门在开启和关闭过程中传动零件所产生的惯性力.因此,气门弹簧的性能直接影响着发动机的运行安全及效率[1].
山东 某 公 司 生 产 的 发 动 机 气 门 弹 簧 材 料 为OTEVA75超纯净弹簧钢,经过绕簧、热处理、磨簧、喷丸等工艺处理后,装入发动机进行台架试验.试验进行到第468h时(要求进行500h耐久试验),发动机功率下降,重启后怠速抖动,停止试验拆机后发现4缸第2个弹簧断裂,其他零件无异常.故障件实物形貌如图1所示.该气门弹簧为两端变节距气门弹簧,弹簧两端并头并磨平,经过一圈均匀过渡到等节距.为了确定其断裂原 因 ,笔 者 对 其 进 行 了 断 口 形 貌 观 察 和分析、化学成分分析、金相检验和硬度测试.
1 理化检验
1.1 断口宏观观察
该气 门 弹 簧 断 裂 位 置 在 第 2~3 个 弹 簧 圈处,将断口 放 在 扫 描 电 镜 下 进 行 观 察,发 现 其 断裂源处于 磨 损 带 处,磨 损 带 上 有 一 些 小 凹 坑,如图2~5所 示,且 有 些 凹 坑 附 近 可 以 看 见 一 些 细小裂 纹 (图 5 箭 头 所 示 ),磨 损 带 在 弹 簧 的 接 触圈处.
1.2 断口微观观察
弹簧断口经超声波清洗后,在 FEIG650型扫描电子显微镜上进行观察.断口截面的整体形貌如图6所示,断裂源位于弹簧接触表面的磨损带处;B区为疲劳扩展区,该区域较为平坦,疲劳辉纹明显,如图7所示;C区为最终瞬断区,起伏较大,为韧窝形貌,如图8所示.
1.3 化学成分分析
使用SPECTRO ARCOSICP型等离子体发射光谱仪对断裂气门弹簧的化学成分进行分析,如表1所示,可见气门弹簧的化学成分符合供货双方签订的技术协议要求.
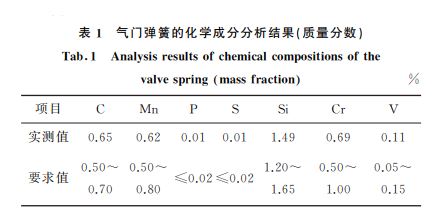
1.4 金相检验
对气门弹簧断口附近的横纵截面分别取样,镶嵌后研磨、抛光.观察纵截面试样,其夹杂物含量较低,钢材较纯净.采用4%(体积分数)硝酸酒精溶液侵蚀横 截 面 试 样,可 见 其 显 微 组 织 为 回 火 屈 氏体[2](图9),表面无脱碳或渗碳现象(图10).
1.5 硬度测试
依照 GB/T4340.1-2009中的测试方法,使用Wilson432SVD型显微维氏硬度计对该气门弹簧进行硬度测试.结果显示其基体显微硬度实测值为590,596,592HV,平均硬度为593HV,根据 DINENISO18265-2004转换成洛氏硬度为54.8HRC,符合技术协议中硬度为52~56HRC的要求.
2 分析与讨论
断裂是气门弹簧常见的损坏形式,总结气门弹计出现问题造成强度不够,裂纹源一般在弹簧的内侧.失效弹簧两端并紧磨平,该结构在第1~3圈处承受的弯曲应力及扭转应力最大,工作时在此处发生断裂的概率也最大.同时因为在1~3个弹簧圈处先承受冲击载荷,又不能迅速有效地将载荷传递给其他圈弹簧,吸收的冲击能量最多[4],因此相对于其他圈的压缩量要更大.力学性能、微观组织及化学成分的分析结果显示,该气门弹簧的硬度、化学成分均符合要求,显微组织为正常的回火屈氏体,内部夹杂物也无异常.断口的微观形貌分析发现,该气门弹簧断裂是由于在弹簧表面存在磨损带,受应力作用下在该处发生疲劳开裂.弹簧受应力集中的作用在擦伤磨损处产生微裂纹,弹簧工作时不断地周期性往复变形,裂纹在应力循环作用下逐渐扩展,形成了图6所示的疲劳扩展区 B,因此该区域较为平坦.失效气门弹簧断裂源处的磨损带呈直线分布,
说明弹簧磨损带是在断裂之前形成的,同时弹簧内表面与外表面的受力分析表明,该气门弹簧断裂属于异常疲劳断裂.在扫描电镜下观察,疲劳断裂源在弹簧表面磨损带处,显示接触面擦伤对该气门弹簧的断裂有影响.
在耐久试验过程中,气门弹簧第2圈与第3圈不断接触,表面产生磨损带.工作中气门弹簧不停地往复运动,伴随着应力的不断循环,磨损带处形成疲劳断裂源,受力的同时裂纹不断扩展.当弹簧所剩有效截面不能承受外界载荷时,就会造成该气门弹簧早期断裂失效[5].
3 结论及建议
该气门弹簧断裂属于早期疲劳断裂,断裂失效的主要原因是由于在弹簧第2~3圈处有较严重的磨损带,导致弹簧疲劳强度和疲劳寿命下降.建议生产厂家优化喷丸工艺,提高气门弹簧表面的疲劳强度,同时在满足装配的情况下,增加第2~3圈弹簧 间 距,尽 量 避 免 或 减 少 弹 簧 第 2 圈 与第3圈接触.簧断裂失效的原因主要有以下几个方面:①气门弹簧表面有缺陷,即使用或装配过程中操作不规范,损坏了弹簧表面;②过载断裂,即弹簧工作时受力超过材料本身所能承受的强度;③材料内部微观组织异常或含超标非金属夹杂物.该断裂失效的气门弹簧属圆柱压缩螺旋弹簧,两端并紧磨平.该类型弹簧在轴向应力的作用下,任意横截面所受到的切应力在弹簧的内径受力最大,外径受力最小[3].如果选择材料不合适或者设计出现问题造成强度不够,裂纹源一般在弹簧的内侧.失效弹簧两端并紧磨平,该结构在第1~3圈处承受的弯曲应力及扭转应力最大,工作时在此处发生断裂的概率也最大.同时因为在1~3个弹簧圈处先承受冲击载荷,又不能迅速有效地将载荷传递给其他圈弹簧,吸收的冲击能量最多[4],因此相对于其他圈的压缩量要更大.
力学性能、微观组织及化学成分的分析结果显示,该气门弹簧的硬度、化学成分均符合要求,显微组织为正常的回火屈氏体,内部夹杂物也无异常.断口的微观形貌分析发现,该气门弹簧断裂是由于在弹簧表面存在磨损带,受应力作用下在该处
发生疲劳开裂.弹簧受应力集中的作用在擦伤磨损处产生微裂纹,弹簧工作时不断地周期性往复变形,裂纹在应力循环作用下逐渐扩展,形成了图6所示的疲劳扩展区 B,因此该区域较为平坦.
失效气门弹簧断裂源处的磨损带呈直线分布,说明弹簧磨损带是在断裂之前形成的,同时弹簧内表面与外表面的受力分析表明,该气门弹簧断裂属于异常疲劳断裂.在扫描电镜下观察,疲劳断裂源在弹簧表面磨损带处,显示接触面擦伤对该气门弹簧的断裂有影响.
在耐久试验过程中,气门弹簧第2圈与第3圈不断接触,表面产生磨损带.工作中气门弹簧不停地往复运动,伴随着应力的不断循环,磨损带处形成疲劳断裂源,受力的同时裂纹不断扩展.当弹簧所剩有效截面不能承受外界载荷时,就会造成该气门弹簧早期断裂失效[5].
3 结论及建议
该气门弹簧断裂属于早期疲劳断裂,断裂失效的主要原因是由于在弹簧第2~3圈处有较严重的磨损带,导致弹簧疲劳强度和疲劳寿命下降.建议生产厂家优化喷丸工艺,提高气门弹簧表面的疲劳强度,同时在满足装配的情况下,增加第2~3圈弹簧 间 距,尽 量 避 免 或 减 少 弹 簧 第 2 圈 与第3圈接触.
1.3 支架受力与结构分析
支架除了受到装配和连接总管的弯扭应力外,主要承受发动机工作时的振动应力,销轴与支架采用点焊方式连接,易产生应力集中.从多起销轴脱落和焊接区出现的裂纹特征来看,焊接点是支架中承力最薄弱的区域.
2 分析与讨论
销轴与支架连接的焊点在发动机工作的振动应力作用下产生疲劳裂纹,进而断裂引起销轴脱落.该支架作为发动机总管的支架,在飞机飞行时承受振动应力,除飞机起飞和降落时,飞机正常飞行时振动应力很小.但出现了多起销轴脱落和连接焊点疲劳裂纹,其原因应有支架的结构形式、焊接的连接方式、焊接强度等因素.在支架组件中,销轴起到固定杆的作用,与支架采用开口管状连接和点焊接方式,其支架与销轴间的间隙很难保证,销轴和支架焊缝结合线处存在尖锐夹角,在工艺上也难以彻底消除.因此,改进支架整体结构和连接方式,消除振动的局部集中点,是解决该故障的根本措施.故障件中焊接的熔化深度和有效焊接厚度都很小,这也是造成零件强度低,产生疲劳开裂的主要原因之一[8].对该故障件进行了焊接工艺改进研究,改进了焊接工艺参数和方法,使焊接的熔化深度、有效焊接厚度有了很大提高,改进后样件焊点的微观形貌见图9.
通过以上分析,可以得出该型发动机发生多起销轴脱落和销轴与支架开裂的主要原因是支架组件的设计结构、连接工艺不合理和焊接强度低.
3 结论
(1)该销轴脱落是由于销轴与支架连接点焊缝在发动机工作时产生疲劳开裂所引起的.
(2)销轴脱落和销轴与支架产生裂纹的主要原因是支架组件的设计结构、连接工艺不合理和焊接
强度低.
文章来源:材料与测试网