分享:铁基粉末冶金零件常见生产缺陷的金相分析
杨 洁
(赫格纳斯(中国)有限公司,上海 201799)
摘 要:介绍了铁基粉末冶金零件金相试样的制备工艺及侵蚀液的选用,并利用金相手段分析了几种铁基粉末冶金零件中的缺陷.结果表明:在粉末冶金的混粉、压制、烧结、热处理等过程中,存储及生产工艺不当均会造成零件产生缺陷,通过金相分析的方法检验缺陷件并与正常件进行对比,可找到引起缺陷的根本原因,从而指导生产、提高质量.
关键词:铁基粉末冶金;金相分析;缺陷
中图分类号:TG115.2 文献标志码:B 文章编号:1001G4012(2017)05G0337G05
作为一种绿色环保、近净成型技术,粉末冶金近年来得到迅速发展,在家电、汽车、电动工具等领域都有广泛应用[1].在零件的实际生产和使用过程中,由于生产工艺、材料、设计、装配、使用环境等原因会造成零件失效,而粉末冶金零件特有的孔隙结构使得其设计和生产与钢铁材料的有很大区别,因此对其的检测分析也具有独特的地方.
粉末冶金零件的生产过程包括混粉、压制、烧结、热处理、机加工及其他表面处理工序,某一环节出现问题都会导致零件在生产和使用过程中出现失效.比如混粉工艺不当造成合金元素偏析,压制参数不当造成裂纹、密度分布不均、拉模或毛边,烧结不当造成脱碳渗碳、氧化或冷却速率异常,热处理渗碳过度导致硬度过高,热处理温度不够导致硬度偏
低等.金相分析可以通过对显微组织的评估,快速找到失效原因,从而改善生产工艺,是一种非常直观有效的检测手段.笔者在一些实际工作中利用金相分析手段,分析了铁基粉末冶金零件的生产缺陷案例,以期为工厂提高生产质量提供参考.
1 金相分析过程
金相分析过程就是对显微组织进行观察,通过基本的材料学知识推断出零件生产过程中可能会造成缺陷的异常参数.金相分析通常分为3个步骤:
金相试样制备,试样侵蚀,显微组织评估,现代金相分析还包括结合扫描电镜进行分析[2].
在金相试样的制备过程中需要注意以下几点.
(1)试样在切割时不能过热,否则会造成表面组织改变[3].
(2)磨抛时确保去除切割变形层,且不能引入额外的变形[4].
(3)对粉末冶金钢的金相试样制备需要特别注意选择合适的镶嵌树脂、镶样方法、抛光力度、抛光时间、抛光布和抛光液,以显示真实的孔隙度.铁基粉末冶金零件的金相试样磨抛过程如下.
(1)水磨:依次用180,320,500,800,1200 号水磨砂纸各磨1 min.手动磨样时要注意,每换一道砂纸,试样需旋转90°以确保去除上一道砂纸带来的划痕,半自动精磨时可用树脂复合盘配合9μm金刚石悬浮液[4]代替320~1200号砂纸手磨.
(2)抛光:使用3μm 金刚石悬浮液配合粗制羊毛抛光布抛光5~15min.材料越软抛光时间应越长,以显示真实孔隙.若材料很软,例如纯铁,孔隙不易打开,可以在抛光布上加少量清洁剂,或者轻微侵蚀后再抛光.
(3)终抛:使用1μm 金刚石悬浮液配合细软绒布抛光30~60s.试样侵蚀时应针对不同的材料选择不同的侵蚀剂,以显示真实的显微组织.在侵蚀冲洗后需要迅速吹干试样,以避免试样表面残留水渍影响真实显微组织的判断.常见的铁基粉末冶金材料的侵蚀剂[5]如表1所示
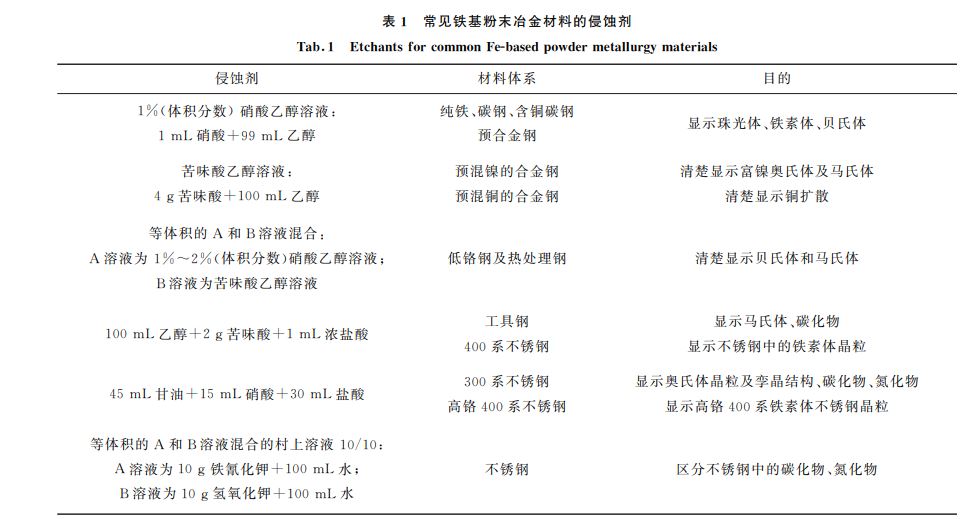
2 粉末冶金零件缺陷分析
2.1 压制过程中的缺陷
(1)分层
使用铁G铜G碳粉生产某零件时发现多件生坯内外表面出现黑色分层现象,问题零件烧结后的强度较低.为调查产生分层的原因,取合格(OK)件和不合格 (NG)件 生 坯 在 网 带 炉 中,在 1120 ℃ 下,N2+H2(体积比为9∶1)气氛中烧结30min,随后取烧结 NG 件分层处和 OK 件进行扫描电镜观察和显微组织对比分析,结果见图1.扫描电镜和金相分析都显示 NG 件分层处留下大量孔隙,并探测到大量游离石墨和铜.金相分析显示 OK 件的碳含量正常,显微组织为珠光体和铁素体,从珠光体含量判断其碳含量约为0.5%(质量分数).而 NG 件的碳含量偏高,未分层区出现了全珠光体,表明碳含量达到
了0.8%(质量分数),而分层区出现了晶界渗碳体,碳含量已经远超过了0.8%(质量分数).从金相分析结果可知,零件分层现象为石墨、铜偏析.细粉产生偏析有可能是混粉不均或者压制时粉末填充问题造成的.然后检查生产现场发现,所
有的问题生坯件都是集中在某一次压制换粉时产生的,此次换粉不及时导致送粉管中粉末位置过低,使粉末在下落时做自由落体运动,导致石墨、铜粉等细粉产生偏析,从而压制时产生分层.因此该零件的分层偏析是由于粉末传送不当造成的.由于产生了大量孔隙和异常组织,分层零件将会出现烧结后性能(例如尺寸)变化、力学性能不稳定.
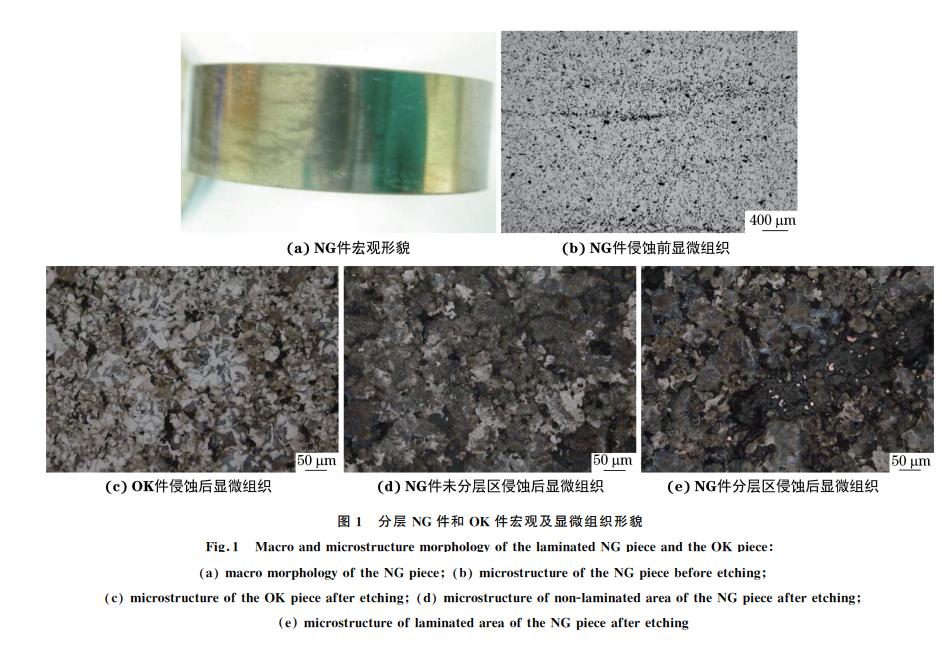
(2)裂纹与断裂
在某次测试过程中发现,某零件出现裂纹导致强度偏低,易断裂.为找出裂纹产生的阶段以便消除裂纹,将零件沿裂纹处打开,在扫描电镜(SEM)下观察断面形貌.裂纹区及无裂纹区的断面形貌如图2(a),(b)所示,对比可知裂纹区颗粒表面无韧窝
或解理面等烧结后断裂特征,表明裂纹区无烧结颈产生,说明裂纹产生于生坯阶段.随后沿压制方向取易断裂部位制备金相试样,显微组织形貌见图2(c),裂纹如箭头所示,可以看出裂纹靠近拐角处并向零件内部延伸,呈直线型,裂纹两边存在严重密度差,表明粉末填充非常不均匀.
2.2 烧结过程中的缺陷
(1)表面熔化
某零件烧结后表面产生局部熔化,为找到造成表面熔化的原因,沿熔化区域取样制备金相试样,其显微组织形貌如图3所示.图3(a)为侵蚀前显微组织形貌,可见熔化区域材料致密,存在少量圆孔.图3(b)为侵蚀后显微组织形貌,可见熔化区域存
在大量晶界渗碳体,表明该处石墨含量很高.此缺陷应该是由于大量石墨团聚,在高温下(高于液相开始形成温度)烧结形成液相造成的.由于零件内部也发现了熔化的团聚区域,说明该混粉内已存在石墨团聚,应该检查压制前所有步骤,比如粉末混合是否有团聚,是否有过筛,筛网是否干净,料斗和送粉管是否未定期清洁导致细粉团聚.如果此类缺陷仅出现在表面而且位置比较固定,应该是压制模具某一个位置异常导致的.
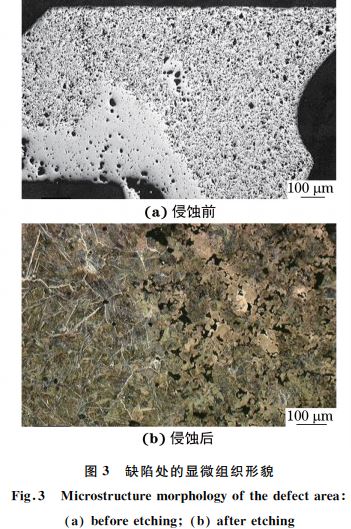
(2)硬度异常
生产某纯铁粉末冶金零件时发现某些零件烧结后硬度偏高,OK 件硬度为24 HRB,NG 件硬度为51HRB.为了分析造成异常的原因,取 OK 件和NG 件侵蚀后进行金相分析,分析结果如图4所示.
OK 件的显微组织为正常的纯铁素体,而 NG 件的显微组织中除了铁素体外还发现了细针状的铁的氮化物以及极少量的马氏体.由于零件在分解氨气氛中烧结,如果氨分解不彻底,残余氨在高温下会促使零件渗氮,从而形成铁的氮化物,甚至出现马氏体,使表面硬度增高[6].
图4 OK 件及硬度异常 NG件的显微组织形貌
Fig敭4 MicrostructuremorphologyoftheOKpieceand
theNGpiecewithabnormalhardness
a OKpiece b NGpiece
2.3 热处理过程中的缺陷
(1)硬度异常
使用 Dis.AB赫格纳斯扩散合金黏结粉(FeGNiGCuGMo)加 0.15%碳(质量分数)生产某零件,需要进行热处理提高硬度,热处理工艺为渗碳淬火后回火,热处理后发现零件硬度偏低.侵蚀后分析零件的显微组织时发现,在低碳马氏体基体上出现了大量硬度低的显微组织,即黑色细珠光体和白色铁素体(侵蚀后可见铁素体晶界),如图5所示.白色岛状富镍奥氏体是该材料的正常组织.检查热处理参数发现热处理温度为820 ℃,碳势为0.6%,对于原材料0.15%(质量分数)的碳含量来说渗碳温度太低,导致零件在奥氏体化温度时未能完全奥氏体化,仅在奥氏体和铁素体两相区加热,零件冷却后残留铁素体.而细珠光体是由于碳含量低,在此冷却速率下未能避开珠光体形成区域产生的.使用铁铜碳粉生产的零件在进行表面渗碳处理后硬度异常升高,观察侵蚀后的显微组织发现大量粗大的片状高碳马氏体及残余奥氏体,在表面还出现了很多白色碳化物,如图6所示.这是由于零件表面渗碳过度,碳含量过高导致形成了渗碳体.一般而言,如果在热处理后发现有碳化物存在,除了渗碳热处理过程中碳势过高或者时间过长导致之外,烧结过程中如果渗碳,也会造成表面形成碳化物,最好有烧结件进行确认.
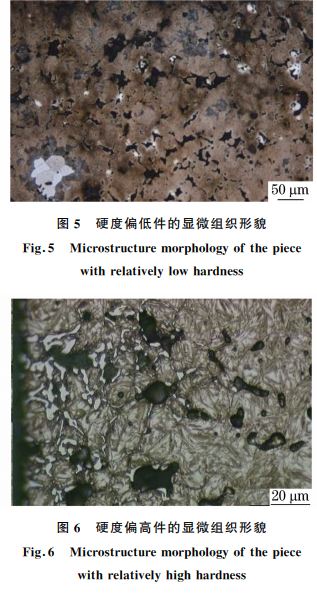
(2)尺寸异常
使用铁铜碳材料生产某环形零件,渗碳热处理后发现硬度偏高,尺寸偏大.为分析造成异常的原因,取 OK 件和 NG 件侵蚀后进行金相分析,如图7所示.对比显微组织可知 OK 件和 NG 件都为马氏体,但 NG 件的马氏体更粗大而且出现了少量残余
奥氏体,说明 NG 件的碳含量较高导致高碳马氏体和残余奥氏体出现.碳含量越高,马氏体硬度越高,测 试 马 氏 体 硬 度,OK 件 马 氏 体 显 微 硬 度 为764HV0.1,NG 件马氏体显微硬度为819HV0.1.高碳马氏体中,由于碳含量高,产生的体积膨胀更大.造成碳含量偏高的原因可能是渗碳热处理过程中碳势过高或者时间过长,另外如果烧结过程存在渗碳也会导致后续热处理硬度偏高.粉末冶金零件相比钢件来说,残留的孔隙使得其渗碳过程更加快速,应适当调整工艺以得到合适
的组织及渗碳层深度.
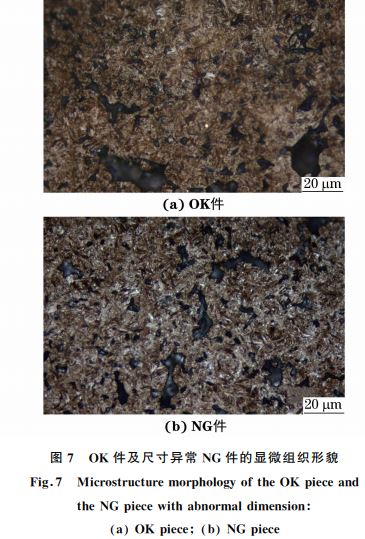
3 结论
在进行粉末冶金铁基零件的失效分析时,可以使用光学显微镜以及电子显微镜分析等手段,观察裂纹及孔隙分布,要注意试样的制备过程以显示真实的孔隙率.
通过对比正常件和异常件的孔隙及显微组织的差异,可以推断粉末冶金零件失效的原因,一般有以下规律.
(1)粉末偏析会导致零件烧结后化学成分、尺寸、力学性能等出现大范围波动,或者表面出现层状细孔聚集,偏析处的孔隙及显微组织都会出现异常.粉末偏析可能来源于粉末混合、运输、传送、压制等过程中的不当操作.
(2)细粉团聚将导致零件局部出现孔洞或者熔
化的现象,造成缺陷周边组织异常.细粉团聚可能来源于粉末储存时吸潮,或料斗、送粉管及压制基台残留细粉未及时清理产生结块.
(3)压制脱模不当将导致零件出现密度分布不均以及裂纹,从而导致烧结后尺寸变化及力学性能异常.选择合适的压制脱模过程以及粉末性能较好的材料,定期维护模具都可以减少此类失效.
(4)烧结不当会导致零件出现孔隙和显微组织含量,例如可以采取吸湿性液体吸收、用活性固体干燥剂吸收、用压缩或冷却方法冷凝等方法来减少二氧化碳气体中的水含量.
4.2 钢瓶制造质量控制措施钢瓶制造材料、工艺等都可能导致钢瓶材质存在问题,不仅会影响钢瓶的力学性能,同时也会影响钢瓶的应力腐蚀敏感性.无缝钢瓶的制造过程可能会导致瓶体存在残余应力,并可能导致钢瓶发生应力腐蚀,可采取热处理措施,减小钢瓶瓶体的残余应力.在钢瓶制造完成后,应对钢瓶内部进行清洗和干燥,减少钢瓶内部水分和其他杂质的残留.在进行水压或气密性试验后,应采取内表面干燥处理,并予以密封.
4.3 钢瓶使用管理措施
钢瓶充装和使用单位应做好钢瓶的管理工作,并按照相关规定对钢瓶进行定期检验,及时发现钢瓶缺陷.应控制水压试验使用水中氯离子的含量,减少氯离子在气瓶内的残留.在水压或气密性试验后,应对内表面进行干燥处理,并予以密封[6G7].钢瓶储存和运输过程应避免碰撞和跌落,并按要求做好定期检验工作.
5 结论及建议
综合分析认为,该失效钢瓶具备应力腐蚀开裂的特征和条件,瓶体内壁发生了应力腐蚀开裂.在内部压力和搬运过程的碰撞及振动作用下,钢瓶承压能力不足,最终导致钢瓶发生了物理破裂爆炸.
建议加强对二氧化碳钢瓶的生产、储存运输、充装和使用的监管,确保各环节的规范管理,减少类似事故的发生.
文章来源:材料与测试网