分享:Y2O3 含量对燃烧合成Fe-Y2O3 纳米复合粉末性能的影响
张德印,1,2, 郝旭1, 贾宝瑞1, 吴昊阳1, 秦明礼
,1,2,3, 曲选辉1,3
1
2
3
采用溶液燃烧合成技术制备了不同Y2O3含量(质量分数)的Fe-Y2O3纳米复合粉末,分析了Y2O3含量对制备的复合粉末的微观结构、晶粒尺寸、磁性能和烧结性能的影响。结果表明,制备的Fe-Y2O3纳米复合粉末均呈现由纳米颗粒组成的连通的网状结构,随着Y2O3含量的增加,晶粒尺寸逐渐降低。通过磁性能测试,不含Y2O3的纳米铁粉的饱和磁感应强度为1.97 T,相应的矫顽力为6.4 kA/m。随着Y2O3含量的增加,Fe-Y2O3纳米复合粉末的饱和磁感应强度逐渐降低,矫顽力逐渐增大。当Y2O3含量为2%时,Fe-Y2O3纳米复合粉末的饱和磁感应强度为1.45 T,相应的矫顽力为58.9 kA/m。对制备的纳米粉末进行常压烧结,当Y2O3含量低时,该粉末在较低的烧结温度(700℃)下可以获得较高的相对密度,当Y2O3含量增加到1%或2%时,在高的烧结温度(1300℃)下也难以实现致密化。
关键词:
金属/陶瓷纳米复合材料因其优异的电、磁、力学性能而受到越来越多的关注,在工业领域有着广泛的应用前景[1~3]。其中,因具有高的饱和磁感应强度和Curie温度,铁基金属/陶瓷磁性纳米复合材料被认为是一种在数据存储、水处理、催化和生物医药领域颇具吸引力的候选材料[4~7]。多种方法已被应用于铁基金属/陶瓷纳米复合材料制备,如Ge等[8]采用共沉淀-煅烧的方法制备了Fe@MgO磁性纳米复合材料,该复合材料对甲基橙和Pb(II)表现出优异的吸附性能;Wei等[9]采用溶胶-凝胶法制备了Fe/SiO2复合材料,其在微波波段表现出优异的复介电常数和磁导率;Torabinejad等[10]采用电沉积的方法制备了Fe-Ni-Al2O3纳米材料,并研究了其耐磨性;Raghavendra等[11]采用机械球磨的方法制备了Fe-ZrO2纳米复合粉末,研究了球磨过程中粉末颗粒的形态及氧化物和铁晶的细化等。然而,这些制备技术或多或少面临着一些挑战,比如昂贵的原材料、冗长的实验过程、复杂的实验设备等。因此迫切需要开发一种简易便捷的方法用于制备铁基金属/陶瓷磁性纳米复合材料。
氧化物弥散强化铁基合金因其优异的强度和高温蠕变性能已获得了研究者的广泛关注[12~14]。Y2O3因熔沸点高、热稳定性好、物理化学性质稳定,尤其在高温下优异的空间结构稳定性,被广泛作为弥散体添加到氧化物弥散强化铁基合金中[15]。Y2O3弥散强化铁基合金通常采用粉末冶金路线制备,其关键是首先制备高活性、均匀混合的Y2O3掺杂铁基粉末。
近年来,溶液燃烧合成在制备纳米复合粉末方面已取得了重大进展,其中包括简单的二元、三元以及复杂的多元纳米复合粉末[16~18]。该方法具有以下显著优点[19~21]:燃烧反应放出的热量可以使反应自维持,无需外部提供热源,能耗低;燃烧过程释放大量气体,可防止粉体团聚,形成高比表面积的纳米粉体;溶液中所有原料实现在分子水平上的均匀混合,从而导致获得产物中各生成组分均匀分布;燃烧反应速率快,工艺简单、便捷、成本低,适合规模生产。溶液燃烧合成本质上是燃料和氧化剂之间放热的氧化还原反应,氧化剂(一般为金属硝酸盐)与还原剂(有机燃料)的配比是影响产物粉末结构和燃烧反应的重要因素[22]。由于在不同配比条件下,反应的起始点火温度、燃烧温度、燃烧速率、反应过程中产生气体的量以及放出热量的大小均不相同,从而影响燃烧产物的成分、形貌和颗粒尺寸。
因此,本工作采用Fe(NO3)3·9H2O、Y(NO3)3·6H2O和C2H5NO2为原料,基于溶液燃烧路线制备不同Y2O3含量的Fe-Y2O3纳米复合粉末,通过保持Fe(NO3)3·9H2O和C2H5NO2摩尔比例不变,调整Y(NO3)3·6H2O的添加量,探究Y2O3含量对制备的纳米复合粉末的微观结构、晶粒尺寸和磁性能的影响,通过对制备的纳米复合粉末常压烧结致密化研究Y2O3含量对纳米复合粉末烧结性能的影响。以期为制备其他高性能金属/陶瓷纳米复合材料提供思路和理论借鉴。
1 实验方法
采用溶液燃烧合成和后续氢还原制备了不同Y2O3含量的Fe-Y2O3纳米复合粉末。所用实验原料为Fe(NO3)3·9H2O (氧化剂和Fe源)、Y(NO3)3·6H2O (氧化剂和Y源)和C2H5NO2 (燃料)。以上原料纯度均为分析纯,Fe-Y2O3纳米复合粉末前驱体制备时,Fe(NO3)3·9H2O的用量为80.8 g,C2H5NO2的用量为15.0 g,调整Y(NO3)3·6H2O的用量,以获得纳米复合粉末中Y2O3含量(质量分数)分别为0、0.2%、0.5%、1.0%、2.0%为目标。为了便于表达,不同原料配比体系分别标记为F、FY0.2、FY0.5、FY、FY2。
Fe-Y2O3纳米复合粉末的具体制备工艺如下:将上述原料分别按照不同配比称量置入玻璃烧杯中,加入适量的去离子水,通过不断搅拌使各原料充分溶解于去离子水中形成澄清溶液。将盛有上述溶液的烧杯置于DK-98-11型电子调温万用炉上,在空气中加热,随着加热进行,溶液中的水分不断蒸发,逐渐浓缩并形成暗褐色的凝胶,继续加热,凝胶起燃并不断膨胀,伴随着大量的气体放出,燃烧产物充满整个烧杯,生成红棕色的多孔泡沫状前驱体。接着,将得到的燃烧前驱体铺放在石英烧舟中,并放入OTF-1200X型管式炉内,在400℃ H2气氛下还原2 h (其中,加热速率控制为5℃/min,H2流速控制为1 L/min),制得还原产物。将制备的不同Y2O3含量的Fe-Y2O3纳米复合粉末装入不锈钢磨具,用YDK-100T四柱液压机在300 MPa压力下进行压制成形,得到生坯。然后将生坯放入GSF-1600X型管式炉中,在600~1300℃ H2气氛下烧结2 h,随炉冷却至室温获得烧结样品,不同Y2O3含量的Fe-Y2O3纳米复合粉末烧结后的样品分别标记为pF、pFY0.2、pFY0.5、pFY、pFY2。
使用MXP21VAHF X射线衍射仪(XRD)对燃烧前驱体和还原产物的物相成分进行测定(CuKα,波长为0.154 nm)。采用NETZSCH-Ger?tebau GmbH Netzsch 409PC型热分析仪和QMS403C质谱仪对燃烧反应过程中形成的凝胶样品进行差热分析(DSC)、热重分析(TG)和质谱分析(MS),测试温度范围从室温至600℃,升温速率为10℃/min,测试气氛为空气,气体流速控制为20 mL/min。采用ESCALAB 250 X射线光电子谱仪(XPS)对还原产物进行分析。分别利用ULTRA 55型场发射扫描电镜(FE-SEM)和Tecnai G2 F30型透射电子显微镜(TEM)分析燃烧前驱体和还原产物的微观形貌和颗粒尺寸。采用QUADRASORB SI-MP型比表面积分析仪分析燃烧前驱体以及还原产物的比表面积。使用Lake Shore 7307 magnetometer振动样品磁强计(VSM)测量还原产物的磁性能。
燃烧前驱体和还原产物的平均晶粒尺寸(D)根据Scherrer公式进行计算[23]:
式中,K为Scherrer常数(通常为0.9),λ为X射线波长(本文取0.154 nm),β为实测样品衍射峰半高宽度,θ为衍射角。
烧结样品密度(ρ1)根据Archimedes排水法原理[23]进行测量,液体介质为去离子水,实验选用精度为0.01 mg的分析天平,测量样品在空气中的质量记为m1,然后将样品置于去离子水中,称得质量m2,ρ1可通过以下公式计算:
式中,ρ'为去离子水的密度。每个样品至少测定5次,去除最大、最小值,随后取平均值。
Fe-Y2O3合金的密度(ρ0)根据复合材料的理论密度公式计算[4]:
式中,M和V分别为复合材料的总质量和总体积,下角标i为复合材料中的组分,mi 为材料各组分的质量,vi 为各组分的体积,ρi 为各组分的理论密度(其中Fe和Y2O3的理论密度分别为7.87和5.01 g/cm3),ωi 为各组分的质量分数。Fe-Y2O3合金的相对密度(w)计算公式为:
2 实验结果与讨论
2.1 不同原料配比所得燃烧产物的表征及机理分析
图1为不同原料配比的凝胶样品在加热条件下的TG-DSC曲线和相应的MS曲线。从图1a中的TG曲线可以看出,在室温到165℃温度区间内,F凝胶样品的质量损失分数约为25%,相应的DSC曲线上出现一个“V”型吸热峰,这主要是由于凝胶中残余水分的蒸发以及化学束缚水的去除。随着加热继续进行,在DSC曲线上165℃左右出现一个明显的放热峰,相应地样品出现约50%的质量损失(TG曲线)。并且在相应的质谱中检测到CO2、H2O、N2、O2、NO和NO2等存在(图1b)。该放热峰的出现是来自实验中所观察到的发生剧烈燃烧并放出大量气体的现象。Varma等[22]研究表明,在加热过程中,当凝胶中的水分被持续蒸发去除后,凝胶表现出高的反应活性并随之发生燃烧。事实上,当凝胶中的残余水分和化学束缚水去除后,持续加热进行到某一临界温度时,氧化剂和燃料之间发生剧烈的氧化还原反应,致使相应的金属硝酸盐转变为金属氧化物,并伴随着大量的气体放出。随着加热温度继续上升,TG曲线几乎保持不变,DSC曲线上也无明显的吸放热峰出现,标志着整个燃烧反应过程结束。FY0.2、FY0.5、FY和FY2凝胶样品均呈现了相似的热力学行为,在相应的DSC曲线上只观察到一个明显的吸热峰和放热峰的存在,MS也检测到相同的气体成分(图1c~j)。综上可知,为了控制燃烧反应的程度,更好地获得颗粒细小的燃烧产物,根据推进剂化学理论[22],C2H5NO2与Fe(NO3)3·9H2O的理论比为5/3,该反应体系处于贫燃料体系,Y(NO3)3·6H2O含量的增加,对整个反应体系的氧化剂和燃料的配比所表现的热力学行为没有产生明显的影响,这主要是由于目标Y2O3添加量低的原因。整个反应过程中,在所有原材料溶于水后,Y源、Fe源和C2H5NO2分别以Y3+、Fe3+离子态和分子态的形式存在于所形成的混合溶液中,这有助于各成分在离子、原子或分子水平上的均匀分散和混合。随着加热的进行,溶液中的
图1

图1 不同原料配比凝胶试样的TG-DSC曲线及相应的质谱曲线
Fig.1 TG-DSC curves (a, c, e, g, i) and corresponding mass spectrometry (MS) curves (b, d, f, h, j) of gels samples F (a, b), FY0.2 (c, d), FY0.5 (e, f), FY (g, h), and FY2 (i, j) (T—temperature)
图2为不同原料配比样品燃烧产物的XRD谱。从图中可知,不同原料配比所得燃烧产物中均存在γ-Fe2O3和α-Fe2O3衍射峰。该结果表明,通过燃烧反应过程金属硝酸盐转变为相应的金属氧化物。此外,也注意到所获得前驱体的相组成基本不变,但随着Y2O3含量的增加,燃烧产物衍射峰的最大半宽峰的宽度逐渐变大。由于Y2O3含量相对低的缘故,XRD谱中未观察到Y2O3衍射峰的存在。通过计算,F、FY0.2、FY0.5、FY和FY2所获得燃烧产物的晶粒尺寸分别为40、38、35、32和30 nm,相应地测得比表面积分别为20.2、22.7、25.1、27.9和31.7 m2/g。这说明Y2O3的加入能有效抑制燃烧产物粉末晶粒的长大,并且随着Y2O3含量的增加抑制效果愈加显著。这主要是由于产物中Y2O3含量增加,原料配比中Y(NO3)3·6H2O的添加量增加,因此溶液中所含氧化剂的量增加,过多的氧化剂分解需要吸收燃烧反应的热量并伴随着更多的气体放出,放出气体也会相应带走一部分燃烧反应的热量,进而防止燃烧能量过高而使晶粒长大,另外Y2O3含量的增加也能有效阻碍燃烧产物中Fe2O3的结合聚集,进而有助于燃烧产物前驱体晶粒尺寸的降低。
图2
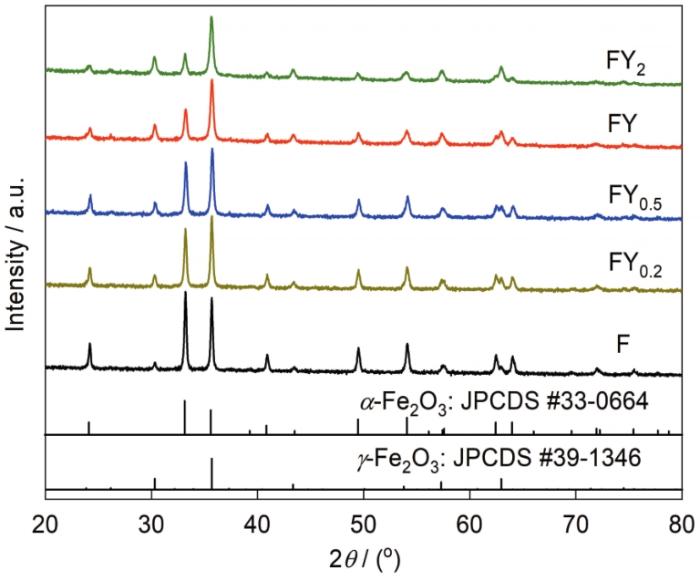
图2 不同原料配比所得燃烧产物的XRD谱
Fig.2 XRD spectra of the combustion product with different raw material ratios
图3为不同原料配比所得燃烧产物的SEM像。由图可见,不同原料配比所得燃烧产物的微观结构均呈现薄片状。随着Y2O3含量的增加,燃烧产物的微观结构发生轻微的变化。F样品燃烧产物有少量的孔隙结构,其是由一定颗粒组成的连通的网状结构(图3a)。随着Y2O3含量的增加,所得燃烧产物中的孔隙逐渐增加,片状产物上的颗粒越来越不清晰(图3b~e)。其原因是Y2O3含量的增加相应增加了燃烧体系中氧化剂的含量,促使燃烧反应放出更多的气体,气体的分散作用增强,导致产物中有更多的孔隙存在。此外,Y2O3含量的增加也能在一定程度上抑制燃烧产物颗粒的聚集和长大。由以上分析可知,燃烧产物的形貌变化与相应的比表面积结果相一致。
图3
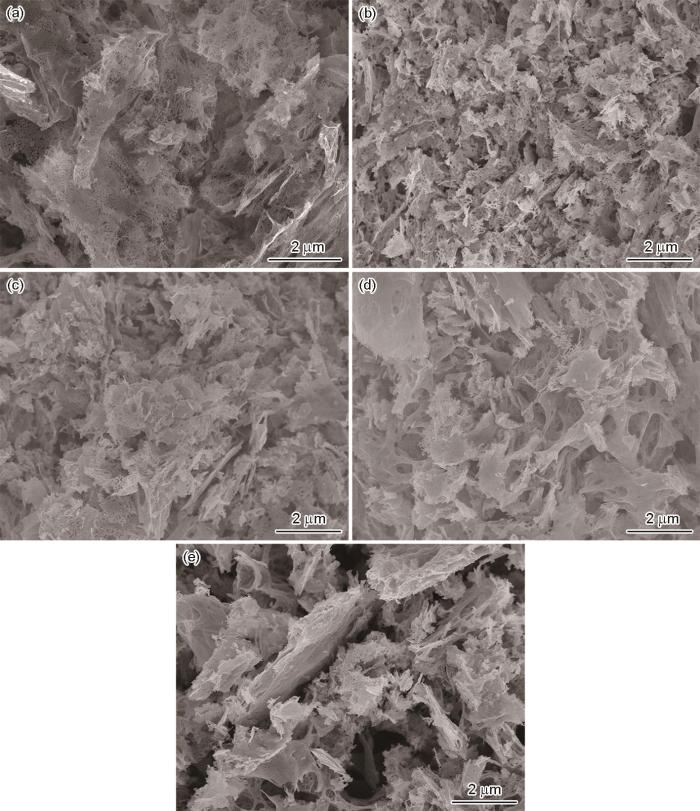
图3 不同原料配比所得燃烧产物的SEM像
(a) F (b) FY0.2 (c) FY0.5 (d) FY (e) FY2
Fig.3 SEM images of the combustion product with different raw material ratios
2.2 不同Y2O3 含量纳米复合粉末的表征
图4为不同原料配比所得燃烧产物在400℃ H2气氛下还原2 h得到产物的XRD谱。由图可见,还原产物中只出现了Fe的衍射峰,这表明在该还原温度下燃烧产物已全部被还原。此外,随着Y2O3含量的增加,所得还原产物的衍射峰变宽。通过计算,得到还原产物的晶粒尺寸和比表面积如表1所示。从表1中可知,随着Y2O3含量的升高,所得还原产物的晶粒尺寸逐渐降低,比表面积逐渐增加。进一步说明了Y2O3的加入有效抑制了还原产物中Fe颗粒的聚集和长大,从而导致还原产物晶粒尺寸的降低,且Y2O3含量越高,抑制作用越明显。此外,在所得还原产物中未探测到Y2O3衍射峰的存在,这主要是由于Y2O3的含量相对偏低不足以被XRD检测出来。
图4

图4 不同原料配比所得还原产物的XRD谱
Fig.4 XRD spectra of the reduction products with different raw material ratios
表1 不同Y2O3含量的Fe-Y2O3纳米复合粉末的晶粒尺寸、比表面积和室温下的磁性能
Table 1
Sample | Crystallite | SSA | Bs | Hc |
---|---|---|---|---|
size / nm | m2·g-1 | T | kA·m-1 | |
Fe | 43 ± 0.2 | 9.7 ± 0.2 | 1.97 | 6.4 ± 0.7 |
Fe-0.2%Y2O3 | 40 ± 0.5 | 13.7 ± 0.5 | 1.83 | 28.7 ± 0.5 |
Fe-0.5%Y2O3 | 37 ± 0.3 | 15.6 ± 0.3 | 1.75 | 47.8 ± 0.6 |
Fe-1%Y2O3 | 34 ± 0.4 | 19.8 ± 0.5 | 1.71 | 51.0 ± 0.4 |
Fe-2%Y2O3 | 33 ± 0.2 | 22.6 ± 0.4 | 1.45 | 58.9 ± 0.7 |
图5为不同原料配比所得还原产物的XPS全谱图和相应的Y3d窄扫图。从图5a可知,不同试样中均探测到Fe2p和O1s的特征峰。Fe2p特征峰的存在说明,所得还原产物中,由于生成高活性纳米Fe颗粒,其表面不可避免地发生氧化反应,从而生成一层Fe的氧化物薄膜。O1s仅有一个特征峰,表明还原产物中存在金属氧化物。此外,随着Y2O3含量的增加,在全谱图中也探测到了微弱的Y3d的特征峰,从Y3d窄扫图(图5b)中可以观察到,随着Y2O3含量的增加,所得还原产物中Y3d特征峰变得愈加明显,从而证明了Y2O3存在。综上可知,由于Y2O3具有高的还原稳定性,因此在还原过程中,燃烧产物粉末中只有Fe2O3被还原为纳米金属Fe颗粒,从而获得Fe-Y2O3纳米复合粉末。
图5
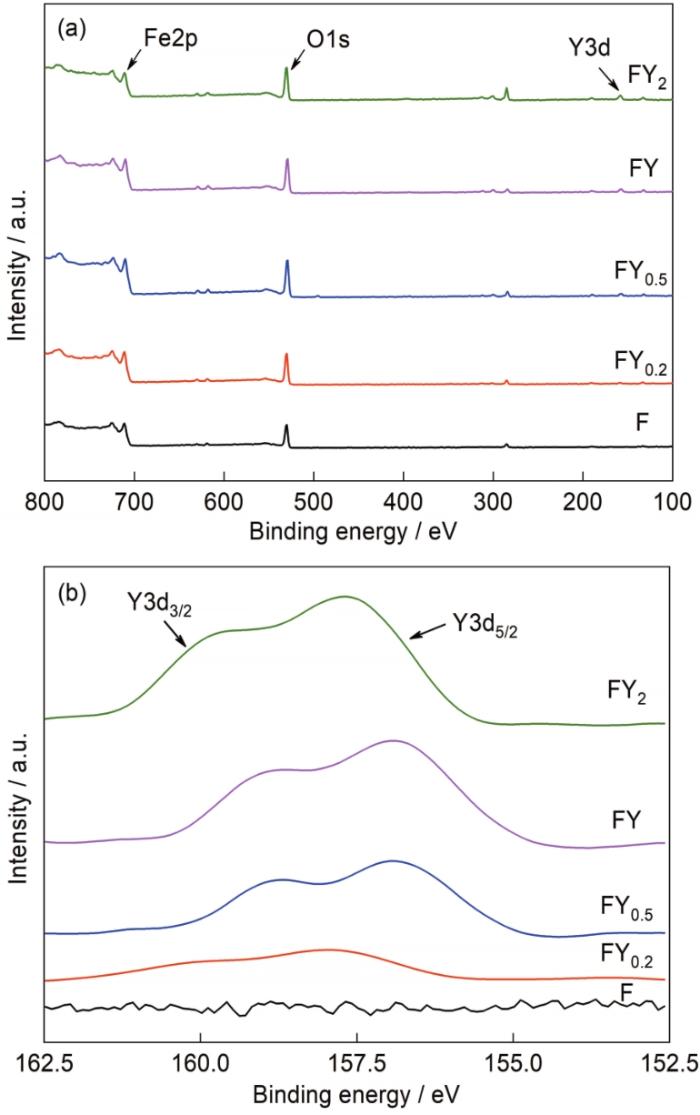
图5 不同原料配比所得还原产物的XPS全谱图和相应的Y3d窄扫图
Fig.5 XPS spectra (a) and Y3d spectra (b) of the reduction products with different raw material ratios
图6为不同原料配比所得还原产物的FE-SEM像。从图中可以看出,不同原料配比所得还原产物的微观结构形貌均呈现由纳米颗粒组成的连通的网络结构。这种微观结构特征主要来源于还原过程中片状前驱体的断裂和获得的高活性Fe纳米颗粒的结合。随着Y2O3含量的增加,所得还原产物的颗粒尺寸逐渐减小,进一步验证了Y2O3的加入能够阻碍还原产物颗粒的长大,且Y2O3的含量越高,其阻碍作用越明显。该分析结果与XRD结果和Scherrer公式计算结果相一致。
图6

图6 不同原料配比所得还原产物的FE-SEM像
Fig.6 Low (a, c, e, g, i) and high (b, d, f, h, j) magnified FE-SEM images of the reduction products with different raw material ratios (a, b) F (c, d) FY0.2 (e, f) FY0.5 (g, h) FY (i, j) FY2
2.3 不同Y2O3 含量纳米复合粉末的磁性能
图7为不同Y2O3含量纳米复合粉末的室温磁滞回线,具体的饱和磁感应强度(Bs)和矫顽力(Hc)列于表1中。由图可见,不同Y2O3含量的纳米复合粉末均呈现出明显的铁磁性特征。由表1可知,不含Y2O3的纳米Fe粉Bs达到1.97 T,相应的矫顽力为6.4 kA/m。随着Y2O3含量的增加,所得Fe-Y2O3纳米复合粉末的Bs逐渐降低,Hc逐渐增大。当Y2O3含量为2%时,所得Fe-Y2O3纳米复合粉末的Bs为1.45 T,相应的Hc为58.9 kA/m。据研究报道[18,24],纳米磁性材料Bs的变化取决于材料的结晶性、杂质含量以及化学成分。在同一还原工艺制备的条件下,随着Y2O3含量的增加,所得纳米复合粉末的晶粒尺寸越小,粉末表面越容易被氧化,引起杂质含量升高,且Fe纳米颗粒的磁性能明显优于Y2O3,因此所得Fe-Y2O3纳米复合粉末的Bs逐渐降低。纳米磁性材料的Hc随晶粒尺寸的变化发生显著改变,当晶粒尺寸从极小值逐渐增大时,Hc表现出先增大后减小的趋势,并在某一临界晶粒尺寸处取得最大值,这一临界尺寸被认为是该材料的单畴晶粒临界尺寸[24~26]。多晶纳米Fe晶粒的临界尺寸约为15 nm[18,25]。当磁性材料的晶粒尺寸等于临界尺寸时,晶粒表现为单磁畴状态,由于此状态下晶粒中不存在畴壁,磁化反转只能依靠材料中各晶粒磁畴协调一致的转动来完成,结果导致磁性材料表现出高的Hc。当晶粒尺寸小于临界尺寸时,随着晶粒尺寸减小,材料中的晶粒更易保持单磁畴状态,热振动对磁畴的影响更加明显,使磁畴逐渐转变为超顺磁状态,材料Hc逐渐减小为零。当晶粒尺寸大于临界尺寸时,畴壁逐渐形成,此时材料中的晶粒表现为多磁畴状态,磁化反转不再依靠磁畴的转动来完成,而是依靠畴壁的形核和运动来完成,结果导致材料Hc降低。由表1可知,所得纳米复合材料的晶粒尺寸均大于临界晶粒尺寸,随着Y2O3含量的增加,晶粒尺寸逐渐降低,因此复合粉末的Hc逐渐增大。
图7
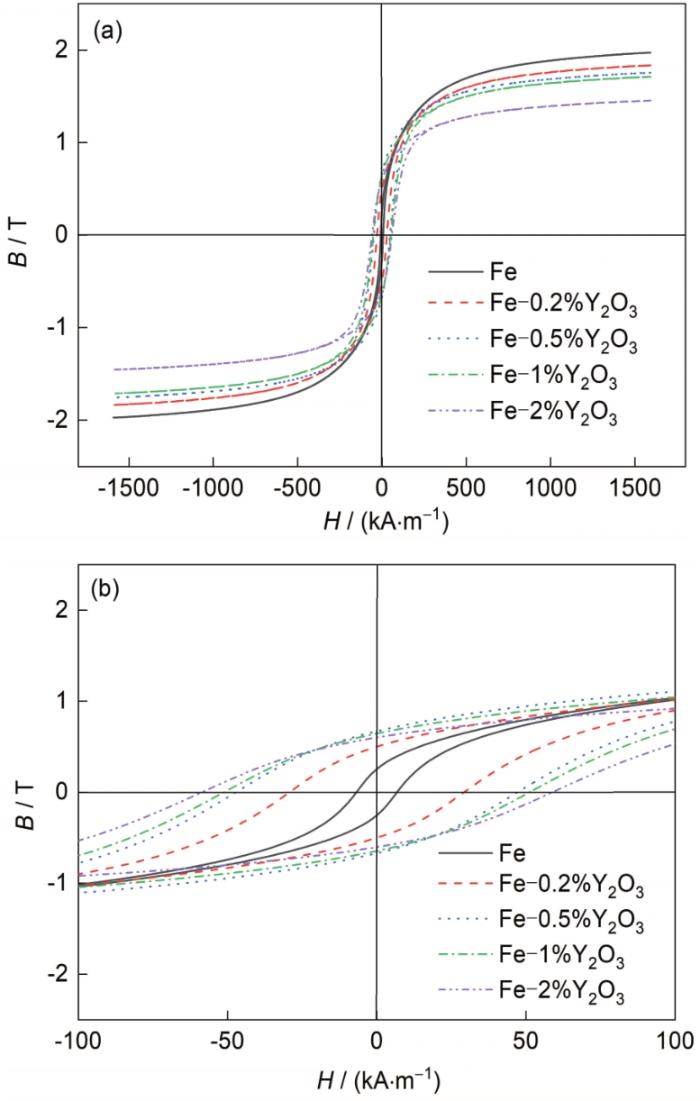
图7 不同Y2O3含量纳米复合粉末的室温磁滞回线
Fig.7 Room-temperature magnetic hysteresis loops (a) and local enlargement (b) of the reduction products with different Y2O3 content (B—saturation induction, H—magnetic field)
2.4 不同Y2O3 含量纳米复合粉末的烧结性能
图8为烧结不同Y2O3含量纳米复合粉末的相对密度与烧结温度的关系曲线。从图中可知,随着温度提升,烧结样品的相对密度均逐渐增大,当达到一定的烧结温度后,温度的进一步升高对相对密度的提升影响减小,相对密度逐渐趋于稳定。同一烧结温度下,随着Y2O3含量的升高,相对密度逐渐降低。当烧结温度为600℃时,烧结样品的相对密度均未达到90%,说明此时的烧结温度过低,粉末的烧结驱动力不足以克服阻碍粉末致密化的活化能。值得注意的是,当烧结温度为700℃时,pF相对密度可达97.3%,随着烧结温度的升高,烧结样品的相对密度逐渐升高,在1300℃烧结温度下pF的相对密度达到99.6%。随着Y2O3的加入,在700℃烧结温度下,pFY0.2、pFY0.5、pFY和pFY2试样的相对密度分别为95.6%、92.8%、77.5%和73.5%,明显低于pF试样的相对密度,且随着Y2O3含量的增加,其相对密度逐渐降低,说明Y2O3的加入明显增加了烧结难度。在700和900℃烧结温度下,pFY0.2和pFY0.5的相对密度超过95%,分别达到95.6%和95.3%。此外,在1300℃烧结温度下,pFY和pFY2试样的相对密度均未超过95%,分别为89.3%和85.1%,表明当Y2O3增加到一定含量时,Y2O3对纳米复合粉末烧结致密化和晶界迁移的阻碍作用增加,复合粉末的烧结活化能增加,粉末在该温度下不足以获得使晶界发生迁移所需要的能量,因此增加了纳米复合粉末的烧结难度。
图8
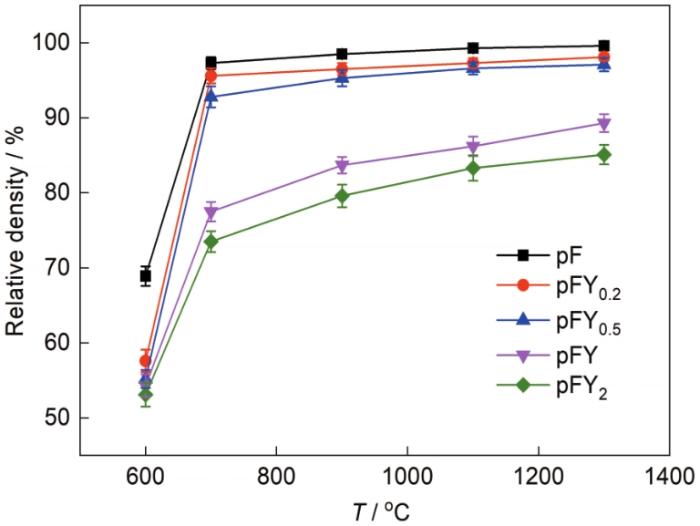
图8 常压烧结不同Y2O3含量的Fe-Y2O3纳米复合粉末的相对密度与烧结温度的关系曲线
Fig.8 Curves of the relative densities of Fe-Y2O3 nanocomposites with different Y2O3 contents varying with sintering temperature by pressureless sintering
3 结论
(1) 采用溶液燃烧合成路线制备了不同Y2O3含量的Fe-Y2O3纳米复合粉末,制备的Fe-Y2O3纳米复合粉末均呈现由纳米颗粒组成的连通的网状结构,但随着Y2O3含量的增加,纳米复合粉末的晶粒尺寸逐渐减小,比表面积逐渐增大。该结果表明,Y2O3的加入能够阻碍纳米复合粉末晶粒的长大,且Y2O3的含量越高,其阻碍作用越明显。
(2) 制备的不含Y2O3的纳米Fe粉通过磁性能测试,饱和磁感应强度达到1.97 T,相应的矫顽力为6.4 kA/m。随着Y2O3含量的增加,所得Fe-Y2O3纳米复合粉末的饱和磁感应强度逐渐降低,矫顽力逐渐增大。当Y2O3含量为2%时,所得Fe-Y2O3纳米复合粉末的饱和磁感应强度为1.45 T,相应的矫顽力为58.9 kA/m。
(3) Y2O3含量为0和0.2%时,Fe-Y2O3纳米复合粉末在700℃烧结温度下,所得烧结样品的相对密度分别达到97.3%和95.6%;当Y2O3含量为0.5%时,在900℃烧结温度下得到的样品的相对密度才达到95.3%。而当Y2O3含量为1%和2%时,即使在1300℃烧结温度下,其烧结样品的相对密度均未超过95%。Y2O3的加入明显增加了烧结难度且Y2O3含量越高其烧结后样品的相对密度越低,当Y2O3含量增加到一定程度时,烧结温度的升高难以使复合粉末实现烧结致密化。
来源--金属学报