分享:冷速对高碳铬轴承钢液析碳化物凝固析出机制的影响
李闪闪1,2, 陈云,1, 巩桐兆1,2, 陈星秋1, 傅排先1, 李殿中1
1.
2.
为明确液析碳化物的形成与工艺的关系和产生机制,以及受添加稀土元素的影响,对添加稀土元素和未添加稀土元素的GCr15系连铸高碳铬轴承钢进行了不同冷却速率下的重熔凝固实验。试样凝固完毕后,采用OM、EPMA、SEM和XRD等表征和分析了铸态轴承钢中的液析碳化物的数量、面积、平均尺寸和化学成分等与冷却速率的关系,以及添加稀土元素的影响效果。结果表明,GCr15系轴承钢液析碳化物的类型为M3C型渗碳体,Cr含量较高,可达15% (质量分数)以上,并且随冷速增加,其数量明显增加。但是,当冷却速率较快时,初生奥氏体细化,同时因形成碳化物所需的C、Cr元素扩散时间减少,碳化物尺寸显著减小,且分布更加弥散均匀。通过对比分析添加稀土元素对凝固组织的影响,发现稀土元素有细化奥氏体进而细化液析碳化物的作用。根据不同冷速下液析碳化物的特点,提出了高碳铬轴承钢凝固过程一次碳化物形成的动力学机制。
关键词:
随着我国工业水平的不断提高,轴承作为各类机械设备的关键基础零件,得到了迅猛的发展,在重大装备领域(如高端精密机床、大型矿山机械、常用冶金设备)和新兴产业领域(如航空航天、轨道交通、风力发电)等均得到了广泛应用。各类轴承中关键的套圈和滚子所使用的材料主要是GCr15系高碳铬轴承钢。而影响高碳铬轴承钢服役寿命的主要因素是非金属夹杂物和组织均匀性[1~3]。目前采用的精炼技术将轴承钢中的O含量控制到接近极限水平后[4],钢中的非金属夹杂物也逐渐地减少、细化,甚至通过添加Ca[5]或者稀土[6~8]处理,使钢中常见的Al2O3类脆硬夹杂物变质为对轴承滚动接触疲劳寿命不敏感的其他类型夹杂物。此时,钢中的碳化物对轴承服役寿命的影响就逐渐突显出来,甚至成为决定轴承钢性能的关键因素。而碳化物中尺寸最大、危害最大、最难消除的是液析碳化物。控制液析碳化物的形貌、分布和尺寸是提升轴承服役寿命和可靠性的一个重要因素[9]。
通过对连铸坯中液析碳化物的研究,发现铸坯中心偏析程度越大,液析碳化物尺寸也越大,其尺寸变化规律一般与轴承钢的中心偏析程度呈线性关系[10]。然而,值得注意的是,在中心偏析程度相近的连铸坯中,液析碳化物的尺寸却不同,这也就意味着液析碳化物的尺寸虽然与中心偏析的程度有关,但应该还存在着其他因素影响其凝固析出[11]。研究人员[12]解剖了多种不同冶炼方式生产制备的GCr15系圆锭,并统计碳化物的分布,结果显示液析碳化物的数量均从圆锭中心至边缘逐渐减少。对连铸钢锭不同位置处的液析碳化物尺寸进行统计,发现中心区域液析碳化物尺寸最大,边缘区尺寸最小[13]。注意到圆锭凝固时各处凝固速率不同,推测液析碳化物的形成和长大应该与凝固速率有很大关系。目前尚未见到凝固冷却速率如何影响高碳铬轴承钢中液析碳化物形成过程的详细研究。本工作从GCr15系轴承钢工业连铸锭中心附近区域取出小尺寸试样,在重熔保温均匀化后,以不同的冷却速率凝固至室温,然后分析和统计不同冷速下液析碳化物的数量、尺寸、面积和化学成分,以及随冷速的变化关系,从而明确液析碳化物的形成与凝固冷却工艺的关系。同时,由于不同冷速对应着不同的凝固时间,也能揭示液析碳化物凝固析出的动力学机制。另外,研究[14]表明添加稀土氧化物能够细化奥氏体晶粒进而细化液析碳化物,为此,本工作也同时研究了不同冷速时添加高纯稀土元素对轴承钢中液析碳化物的影响规律。
1 实验方法
实验用原材料取自工业生产的添加高纯稀土元素(La、Ce,其中O含量低于0.01% (质量分数))和不添加稀土元素的直径为600 mm的GCr15SiMn连铸轴承钢锭,2个圆坯的全氧含量均控制在6 × 10-6以下,其化学成分如表1所示。从钢锭边缘至中心每隔50 mm取样检测成分,结果显示C含量波动幅度在10%以内,宏观偏析并不严重,但是从圆锭边缘至中心的晶粒之间都出现了液析碳化物,其尺寸和分布与目前文献报道的结果[13,15]一致。
表1 未添加稀土元素的GCr15SiMn钢和添加稀土元素的GCr15SiMn(RE)钢的化学成分 (mass fraction / %)
Table 1
Steel | C | Cr | Si | Mn | Mo | P | S | Ni | Cu | La | Ce | Fe |
---|---|---|---|---|---|---|---|---|---|---|---|---|
GCr15SiMn | 0.99 | 1.55 | 0.48 | 0.99 | < 0.05 | 0.013 | 0.001 | 0.06 | < 0.05 | - | - | Bal. |
GCr15SiMn(RE) | 0.99 | 1.55 | 0.50 | 0.98 | < 0.05 | 0.013 | 0.001 | 0.08 | < 0.05 | 0.0005 | 0.001 | Bal. |
为了研究液析碳化物析出和长大与冷却速率的关系,明确液析碳化物的形成条件和机理以及析出动力学,分别在上述GCr15SiMn和GCr15SiMn(RE)连铸圆坯中心到1/2半径之间区域,利用线切割各切取5个直径25 mm、高30 mm的圆柱型试样,将试样表面打磨干净后,使用无水乙醇超声清洗2次,每次5 min,最后干燥。
将GCr15SiMn 和GCr15SiMn(RE)试样分别置于刚玉坩埚内,然后放置在SKL16BYL管式电阻炉中加热熔化,并通Ar气保护,保温1 h后以不同的速率冷却。本实验中共设置了5个冷却速率,分别为空冷(实验测得从1490℃冷却至1300℃时的平均冷速约为190℃/min)、炉冷(实验测得从1490℃冷却至1300℃时的平均冷速约为40℃/min)、10℃/min、1℃/min和0.1℃/min,最后凝固成直径30 mm的小圆锭,如图1所示。由于试样尺寸很小,冷却过程中整个试样可以近似地认为是等温凝固。这样,通过冷速的不断降低,明确在凝固过程逐渐趋近于相图平衡态的情况下凝固一次碳化物的析出行为。其中最慢冷速0.1℃/min,低于直径600 mm连铸钢锭中心的冷速,与正常百吨级钢锭中心冷速接近,从而实现在凝固过程中液相内的溶质元素充分扩散均匀化,以期望凝固接近平衡态。图2是利用Thermo-Calc软件计算的本实验所用GCr15SiMn钢的伪二元相图,虚线所示为1.0%C (质量分数)时从液态至固态的相变过程。相图计算结果显示,该GCr15SiMn钢的平衡液相线温度为1448℃,固相线温度为1318℃。在实验中将GCr15SiMn和GCr15SiMn(RE)试样缓慢加热到1490℃后保温1 h,确保试样完全熔化且钢液合金元素充分扩散均匀化。每次实验,电阻炉内放置2个坩埚,重熔和凝固试样分别是添加稀土和未添加稀土元素的试样,保证加热冷却历程完全一致。所有试样的加热和冷却曲线如图3所示。为避免每次从高温炉中取样操作快慢不同导致冷却速率不一致的问题,除了空冷实验,试样在凝固结束后(冷却至1300℃),关断加热随炉冷却。将5组试样冷却至室温,随后打磨抛光并使用4% (体积分数)的硝酸酒精溶液进行腐蚀,利用Lab.A1光学显微镜(OM)、JXA-8530F电子探针(EPMA)、Inspect F50扫描电镜(SEM)和D/Max-2500PC X射线衍射仪(XRD)等仪器分析试样中的液析碳化物形貌、数量、尺寸、成分和结构类型等信息。
图1
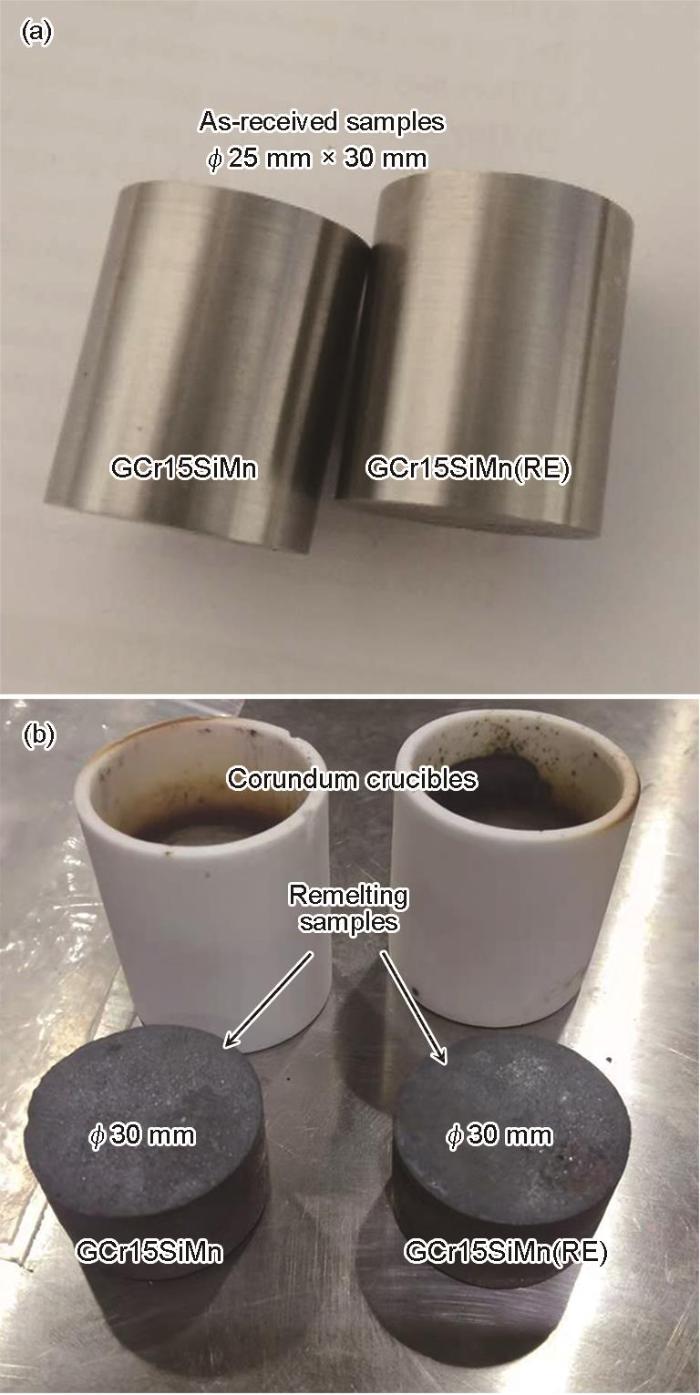
图1 重熔凝固前后GCr15SiMn和GCr15SiMn(RE)钢的圆柱试样,以及所使用的刚玉坩埚
Fig.1 As-received cylindrical samples of GCr15SiMn and GCr15SiM(RE) steels before remelting (a) and the samples after remelting and solidification and corundum crucibles (b)
图2
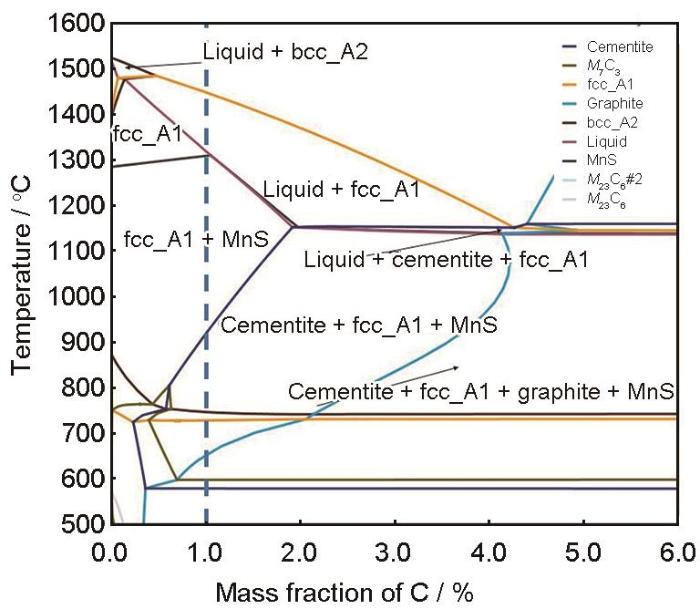
图2 采用Thermo-Calc软件计算的GCr15SiMn钢的伪二元相图
Fig.2 Pseudo-binary phase diagram of GCr15SiMn steel calculated by Thermo-Calc software (The dashed line represents the phase change sequence from liquid to solid at 1.0%C (mass fraction))
图3
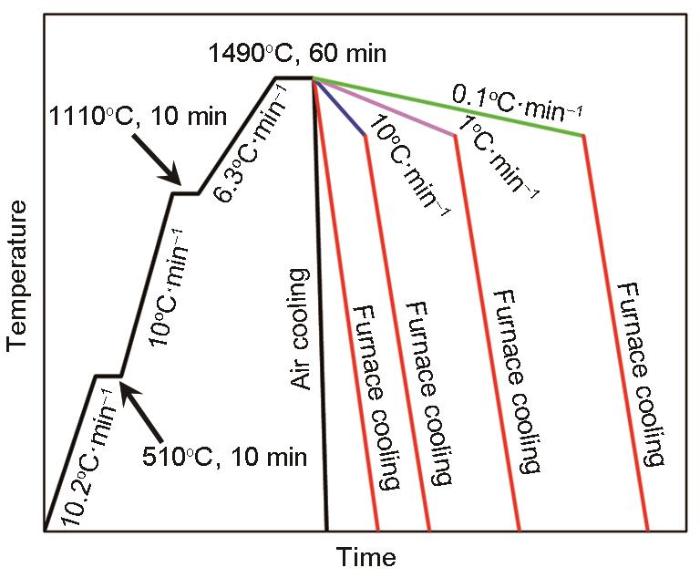
图3 试样熔化和凝固实验过程中的加热和冷却曲线
Fig.3 Heating and cooling curves of the sample in the remelting and solidification experiments
2 实验结果与讨论
2.1 冷速对液析碳化物析出的影响
直径为600 mm的GCr15SiMn连铸圆坯中心区域原始铸态组织中出现了液析碳化物,其典型OM像如图4所示。GCr15SiMn(RE)连铸圆坯同样出现了这种典型液析碳化物,从形貌上大致可分为2种:一种是大块孤立的液析碳化物;另一种是片层状的共晶碳化物。重熔凝固后,试样尺寸虽然很小,但是在铸态组织中同样也出现了这2种典型形貌的液析碳化物,表明所采用的实验工艺能够复现连铸钢锭中一次碳化物凝固析出现象。图 5和 6是相应试样凝固后的基体组织和块状孤立液析碳化物(箭头所示)。可以看出,不同冷速下的GCr15SiMn和GCr15SiMn(RE)试样基体中均没有出现明显发达的树枝晶组织,但无论是比较快速的空冷,还是接近相图平衡态的非常缓慢的冷却过程,都出现了明显的液析碳化物。各冷速下,液析碳化物主要形成于晶粒之间,但受冷速影响,尺寸和数量各不相同。总体上,冷速越慢,液析碳化物的尺寸越大,数量越少。随着冷却速率的不断增加,液析碳化物的数量也显著增加,趋向于弥散均匀分布于晶粒之间。对比添加稀土元素和未添加稀土元素试样的组织可以看出,在低冷速下2者差别较大,不添加稀土元素的试样出现了大块的孤立液析碳化物,在炉冷和空冷的试样中,2者差别不明显,碳化物都非常小,且数量较多。
图4

图4 直径为600 mm的GCr15SiMn连铸轴承钢锭中心区域出现的典型液析碳化物形貌的OM像
Fig.4 Low (a) and locally high (b) magnified OM images of primary carbides found in the center zone of a continuous cast GCr15SiMn bearing steel ingot with a diameter of 600 mm
图5
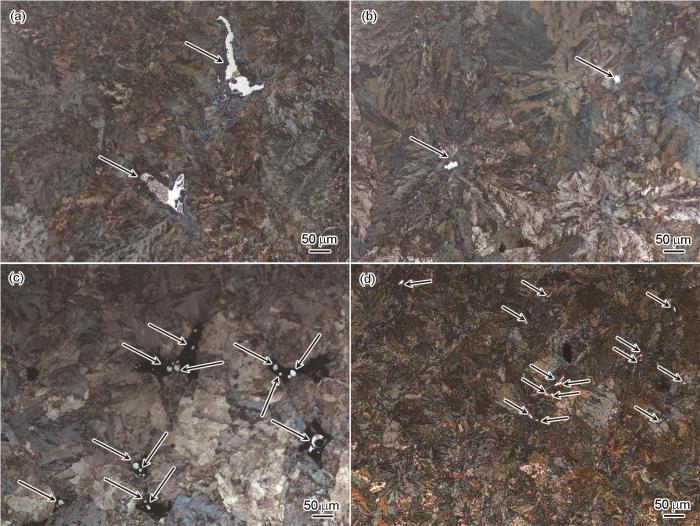
图5 不同冷速下GCr15SiMn钢铸态显微组织的OM像
Fig.5 OM images of as-cast GCr15SiMn steel under different cooling rates (Arrows indicate the isolated primary carbides)
(a) 0.1oC/min (b) 1oC /min (c) furnace cooling (d) air cooling
图6
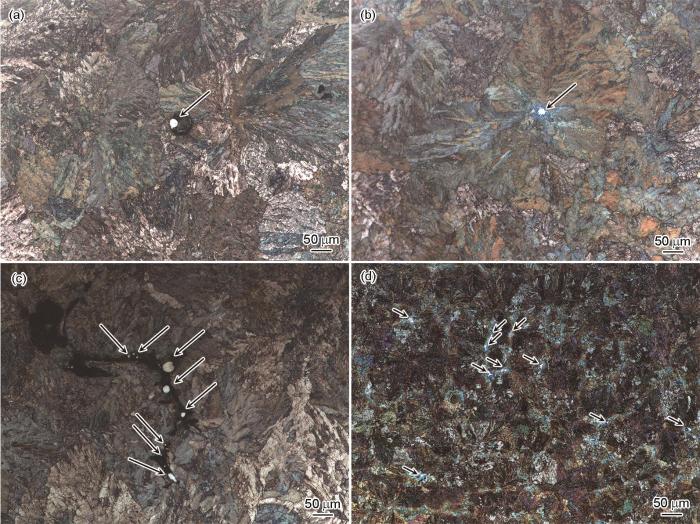
图6 不同冷速下GCr15SiMn(RE)钢铸态显微组织的OM像
Fig.6 OM images of as-cast GCr15SiMn(RE) steel under different cooling rates (Arrows indicate the isolated primary carbides)
(a) 0.1oC/min (b) 1oC/min (c) furnace cooling (d) air cooling
为进一步明确不同冷速下孤立液析碳化物的定量差别,统计分析了孤立液析碳化物的数量、面积和平均尺寸。由于试样尺寸较小,凝固过程基本可以认为是等温凝固,因此在试样的整个横截面上均随机选取了8个200倍视野,然后利用Image Pro Plus软件对金相照片进行统计分析。图7a是孤立液析碳化物的数量随冷速的变化关系。可以看出,2种试样中孤立液析碳化物数量均随冷速的提高不断增加。当冷速为0.1℃/min时,2种试样的所有视场中碳化物数量均只有几个,而空冷时碳化物数量可达上百个。添加稀土元素后,孤立液析碳化物的数量略有减少。图7b是孤立液析碳化物面积随冷却速率的变化关系。不添加稀土元素的试样中孤立液析碳化物的总面积随冷速增加呈下降趋势,而添加稀土元素的试样中碳化物总面积则随冷速的变化呈现波动变化。图7c是孤立液析碳化物的平均直径受冷速的影响关系。不添加稀土元素的试样中孤立碳化物的平均直径随冷速增加不断减小,由冷速为0.1℃/min的51.15 μm逐渐减小为空冷时的5.06 μm;而添加稀土元素的试样中孤立液析碳化物的平均直径随冷速增加出现了波动,且规律性也不是很明显,但总体上呈下降趋势。与不添加稀土元素的结果对比看出,添加稀土元素后液析碳化物平均直径减小,尤其是在低冷速的情况。比如,当冷速为0.1℃/min时,添加稀土元素的钢中液析碳化物平均直径为21.27 μm,比未添加稀土元素的试样小很多,显著细化;而空冷时,液析碳化物的平均尺寸减小至约5 μm,与未添加稀土元素的结果很相近,都已经细化和小颗粒化,且分布更加弥散均匀。
图7
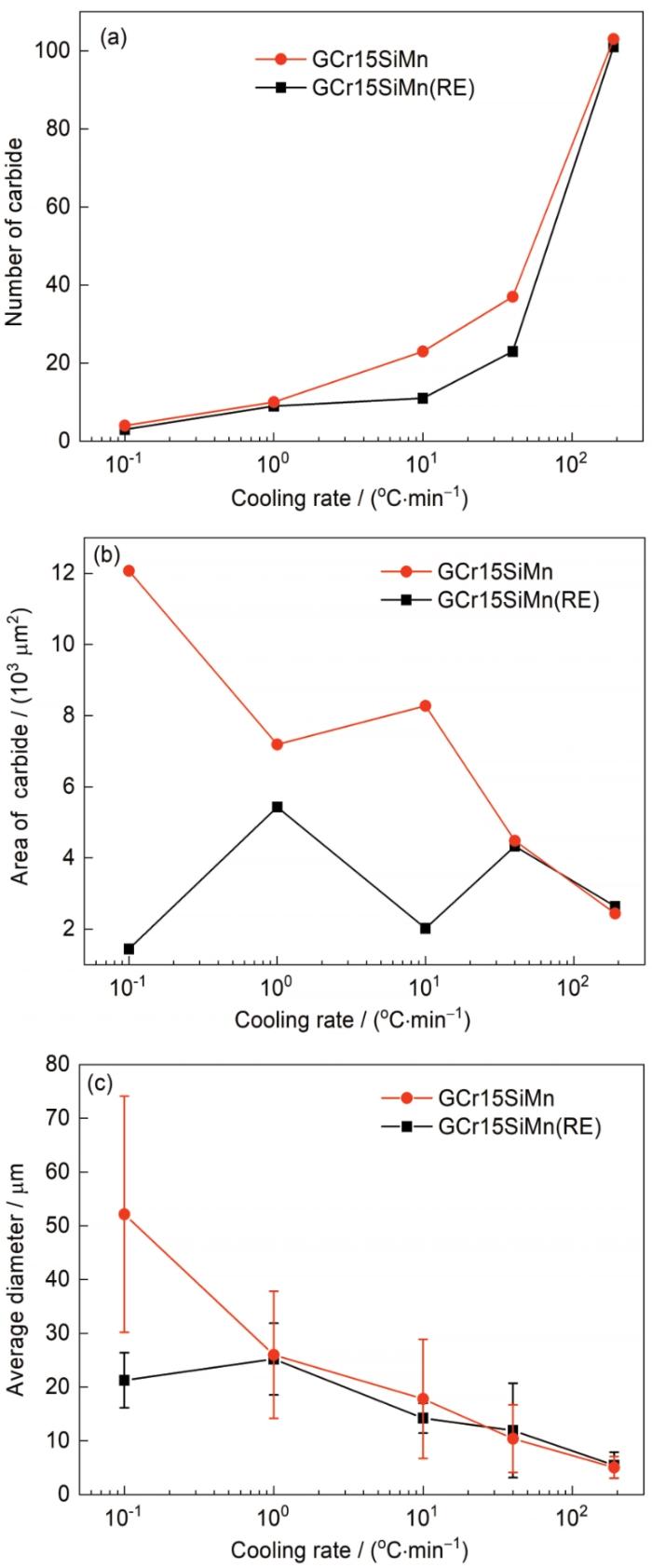
图7 冷速对块状孤立液析碳化物的影响
Fig.7 Effects of cooling rate on isolated primary carbides
(a) number of primary carbides
(b) total area
(c) average diameter
不同冷速下孤立液析碳化物的平均直径分布如表2所示。冷却速率越快,尺寸小于10 μm的碳化物数量百分比越大,尺寸在20 μm以上的碳化物数量百分比则越少。另外,不添加稀土元素的试样中,在冷速不超过10℃/min时,就已经存在直径超过40 μm的大尺寸块状碳化物,而在添加稀土元素的试样中碳化物直径都小于40 μm,且尺寸分布较为集中。这些结果表明,添加稀土元素有细化液析碳化物的作用。Kim和Bae[14]通过向轴承钢中添加稀土Ce的氧化物作为奥氏体的孕育剂,促进形核,提高等轴晶数量,从而细化晶粒,扩大等轴晶区,减轻中心偏析,最终减少和细化了液析碳化物。稀土金属加入钢液中会形成多种不同类型的含稀土元素的夹杂物,如稀土氧化物、稀土硫化物和稀土氧硫化物,这些化合物的熔点都高于钢液的温度[16,17],成分结构也有很大不同,且与Al2O3类夹杂物不同的是,这类夹杂物的密度接近钢液,不会发生明显的漂浮聚集,具备成为钢中形核剂的基本条件。而作为优质形核剂的一个必要条件就是与奥氏体的晶格错配度越低越好。有研究[14,18]显示,奥氏体与CeO2和CeS的错配度分别为6.7%和6.6%,而CeAlO3与奥氏体的错配度在1500 K以上更低,甚至不到4%。这表明这些化合物都是奥氏体的有效形核剂。与Kim等[14]研究不同的是,本工作中稀土是在连铸过程中以高纯稀土金属的方式加入,通过变质钢液中的氧化物和硫化物,形成细小且形状规则的稀土氧化物或者稀土硫化物,或者稀土氧硫化物[19,20],进而可以产生有效的形核剂。为验证这种稀土元素添加方式对晶粒尺寸的影响,分析了不同冷速下的凝固奥氏体晶粒尺寸。在采用苦味酸进行晶界腐蚀时,发现只有冷速为1℃/min试样中的晶界腐蚀效果最好,奥氏体晶界轮廓清晰,统计误差较小,而其他冷速下奥氏体晶界不明显,统计误差较大。
表2 不同冷速下孤立液析碳化物平均直径分布 (quantity percentage / %)
Table 2
Steel | Cooling rate / (oC·min-1) | ? 40 μm | 30-40 μm | 20-30 μm | 10-20 μm | ? 10 μm |
---|---|---|---|---|---|---|
GCr15SiMn | 0.1 | 75 | 0 | 0 | 25 | 0 |
1 | 10 | 30 | 30 | 20 | 10 | |
10 | 4.35 | 13.04 | 21.74 | 34.78 | 26.09 | |
40 | 0 | 0 | 10.81 | 32.43 | 56.76 | |
190 | 0 | 0 | 0 | 1.94 | 98.06 | |
GCr15SiMn(RE) | 0.1 | 0 | 0 | 66.37 | 33.33 | 0 |
1 | 0 | 22.22 | 44.45 | 33.33 | 0 | |
10 | 0 | 0 | 8.33 | 83.34 | 8.33 | |
40 | 0 | 4.35 | 17.39 | 21.74 | 56.52 | |
190 | 0 | 0 | 0 | 6.93 | 93.07 |
表3是GCr15SiMn和GCr15SiMn(RE)试样重熔后以1℃/min冷却凝固得到的晶粒尺寸分布。可以看出,未添加稀土元素试样的晶粒尺寸分布在20~60 μm的占75.5%,添加稀土元素后晶粒尺寸分布在10~30 μm的占84.7%,并且平均晶粒尺寸由39 μm减小至20 μm。这些结果表明添加高纯稀土金属也能够细化奥氏体组织。奥氏体晶粒细化后,缩小了晶粒间距,阻碍了溶质长距离扩散,进而细化液析碳化物。而在高冷速下,液体过冷度增加,相变的驱动力变大,形核率提高[21],此时无论是否添加稀土元素,奥氏体晶粒都会得以显著细化,致使添加稀土元素形成的变质夹杂物对奥氏体细化作用变得不明显。因此在高冷速下,添加稀土元素对液析碳化物的影响也就不明显。
表3 冷速为1℃/min的GCr15SiMn和GCr15SiMn(RE)试样凝固的奥氏体晶粒尺寸分布(数量)
Table 3
Steel | 0-10 μm | 10-20 μm | 20-30 μm | 30-40 μm | 40-50 μm | 50-60 μm | 60-70 μm | 70-80 μm | ? 80 μm |
---|---|---|---|---|---|---|---|---|---|
GCr15SiMn | 6 | 24 | 95 | 62 | 49 | 31 | 19 | 18 | 10 |
GCr15SiMn(RE) | 15 | 170 | 123 | 33 | 4 | 1 | - | - | - |
与工业生产的连铸钢锭类似,在重熔凝固的实验室小尺寸试样中同样出现了片层状的共晶碳化物,形貌与图4非常一致。共晶碳化物的两相片层间距差别很大,部分片层间距达到微米级别,且在一个共晶团内,片层间距也是不均匀的。图8是添加稀土元素和不添加稀土元素试样中共晶碳化物面积随冷速的变化情况。与孤立碳化物不同的是,共晶碳化物面积受冷速影响的变化规律不明显。随着冷速的提高,不添加稀土元素的试样中共晶碳化物的总面积呈现较大的波动,而添加稀土元素的试样中共晶碳化物总面积呈先增加后减小的趋势。
图8
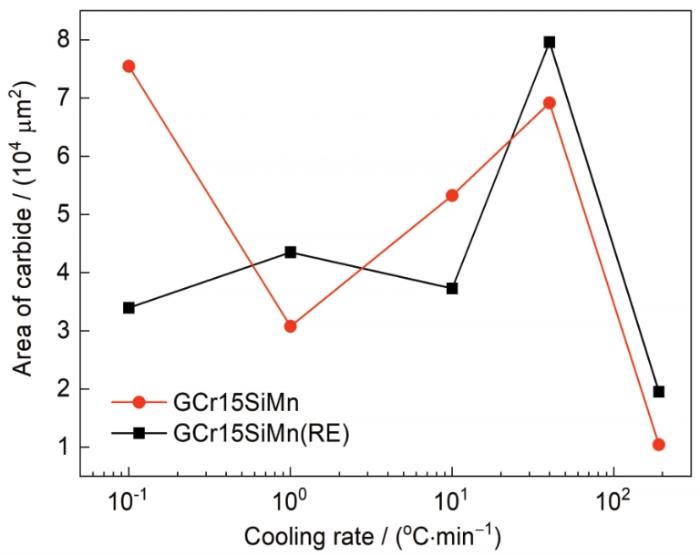
图8 冷速对共晶碳化物面积的影响
Fig.8 Effects of cooling rate on the area of eutectic carbide
2.2 冷速对液析碳化物成分的影响
液析碳化物的成分和类型至今仍存在一些争议。一些研究[22~24]认为凝固过程中由于偏析的存在,凝固末期的液相分解为奥氏体和渗碳体的共晶组织,也就是室温下观察到的莱氏体,但也有研究[22,25]认为液相应该分解为奥氏体、渗碳体和M7C3型碳化物。为确定液析碳化物的类型,在连铸钢锭中心区域取样分析,通过低温电解的方法萃取出连铸锭中的碳化物,随后利用XRD分析物相结构。之所以选择连铸锭而不是实验室试样是因为连铸锭试样足够大,碳化物足够多,尺寸相对较大,可以萃取出所需要量的液析碳化物进行分析。图9a和b是萃取出的添加稀土元素和未添加稀土元素的2种连铸锭中块状孤立液析碳化物的SEM像,也能明显看出连铸钢锭中的液析碳化物都很粗大。图9c和d是2种钢中萃取出的液析碳化物的XRD谱。可见,无论是否添加稀土元素,液析碳化物的类型都只有M3C渗碳体,添加稀土元素不影响液析碳化物的类型。由此,可以确定GCr15SiMn轴承钢中凝固析出的块状孤立碳化物类型是M3C渗碳体而不是M7C3型碳化物。鉴于M3C是多元复合的碳化物,进一步利用EPMA分析了液析碳化物的合金元素组成,结果如图10所示。考虑到重熔凝固前后的液析碳化物类型不会发生改变,并且为了进一步对比不同冷速及添加稀土元素对液析碳化物化学组成元素的影响,使用EPMA分别对5组不同冷速下试样中的块状孤立液析碳化物进行了成分分析。由于共晶碳化物的成分测定受另外一相的影响,测出的结果波动范围非常大,不能准确反映碳化物相的成分,因此本工作没有给出共晶状碳化物的成分测定结果。从图10可以看出,不同冷速下重熔凝固后的试样中液析碳化物的各组成元素含量波动不大,较为集中,说明冷速对液析碳化物的成分影响较小,且化学计量比接近M3C型碳化物,与XRD谱结果一致。不同冷速试样中多个孤立液析碳化物成分分析显示,液析碳化物中的Cr含量(质量分数,下同)多在15%~20%之间,Mn含量在2.5%~3.5%之间,C含量在4%~7%之间,说明液析碳化物是C、Cr元素严重富集的析出相。这也就意味着,虽然不同冷速下C、Cr、Mn在液相中的扩散时间差别较大,但是组成复合碳化物中的Fe、Cr、Mn等金属元素含量相对固定,受冷速影响不明显。此外,不同冷速添加稀土元素和未添加稀土元素结果对比也进一步确认碳化物各组成元素含量几乎不受稀土元素的影响。
图9
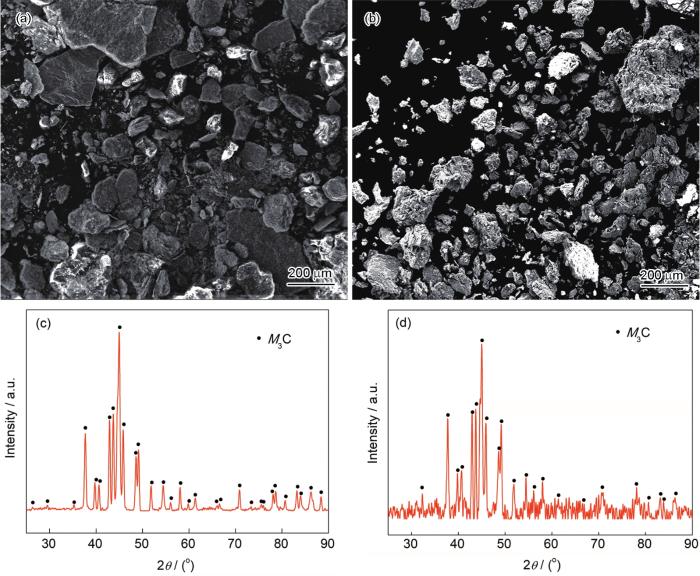
图9 电解萃取GCr15SiMn和GCr15SiMn(RE)连铸轴承钢锭液析碳化物颗粒的SEM像和XRD谱
Fig.9 SEM images (a, b) and XRD spectra (c, d) of primary carbides obtained by electrolytic extraction in GCr15SiMn (a, c) and GCr15SiMn(RE) (b, d) steels
图10
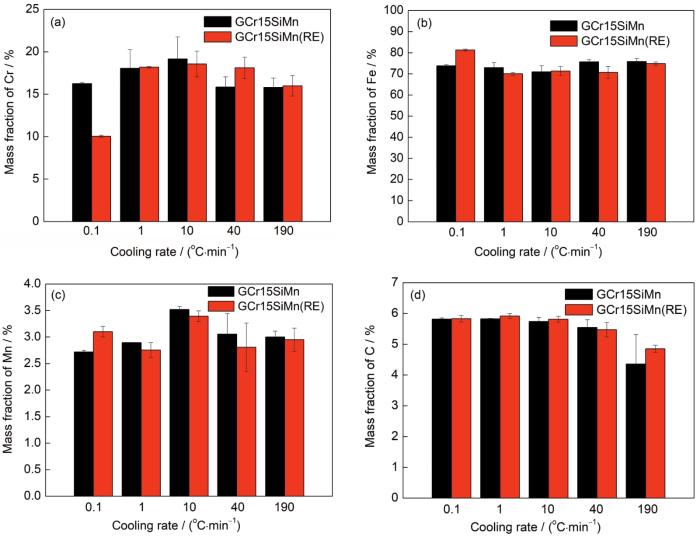
图10 冷速对液析碳化物化学组成的影响
Fig.10 Effects of cooling rate on the chemical composition of primary carbide
(a) Cr content (b) Fe content (c) Mn content (d) C content
2.3 碳化物的动力学析出机制
通过以上实验结果可以看出,无论是直径较大的工业钢锭还是尺寸较小的实验室试样,都出现了明显的液析碳化物,而且液析碳化物往往出现在晶粒之间,尺寸都比初生奥氏体的尺寸小。更为重要的是,无论是在试样边缘还是中心都有液析碳化物的产生。但需要注意的是,并不是在大部分晶粒之间的界面处都有液析碳化物的产生,有很大的随机性。基于这些现象,以及液析碳化物的溶质含量较高的特点,可以推断,在凝固中后期,当因微观偏析导致排出的溶质在液相中达到一定浓度后,一次碳化物才能够从过冷液体中形核析出,而形核后的长大过程主要受元素扩散控制,这是因为不论是工业钢锭还是实验室试样,冷速对块状孤立液析碳化物和片层状共晶碳化物的尺寸影响都非常明显。
基于以上实验表征分析,液析碳化物的形核和长大过程可以概括如下:首先奥氏体在过冷熔体中形核长大,奥氏体生长时不断将C、Cr等溶质元素排至液相中,这样熔体中的C、Cr含量随凝固的进行逐渐增加。凝固中后期,熔体中C、Cr含量较高,同时由于溶质抑制效应,奥氏体生长进入软碰撞生长阶段,生长速率降低,凝固缓慢,这些都为一次碳化物的析出提供了有利条件。原子尺度的计算[26]表明,Fe等金属元素与C原子间的吸引力要大于各自同种原子间的作用力,在液相中易形成团簇。而在凝固中后期,由于在晶粒间的剩余液相中富集了较高浓度的合金和C元素,团簇数量也将增加,同时随温度的降低,团簇和富集的C、Cr元素碰撞在一起形成晶胚的概率也显著增加。在偶然的局部成分和温度起伏作用下,一次碳化物晶坯达到临界尺寸,在枝晶间形核析出,并开始生长,或者依附于初生奥氏体形核析出并长大。碳化物的生长需要熔体中其他区域的C、Cr等溶质元素扩散过来才能满足成分要求,因此受C、Cr元素在剩余液相中的扩散控制。而碳化物的生长也将吸收奥氏体排出的C、Cr元素,促进奥氏体的生长。冷速越高,过冷度越大,相变驱动力就越大,奥氏体和一次碳化物的形核率也都将大大提高[21],因此,高冷速下液析碳化物的数量就越多。由于碳化物的生长需要远程扩散过来的C、Cr等原子,但随着冷却速率增加,碳化物生长时间减少,远程的原子无法及时扩散过来,扩散不充分,从而无法满足碳化物继续长大的成分需求。因此,冷却速率的提高增加了碳化物数量的同时,尺寸也在减少。
此外,碳化物的生长与局部奥氏体的生长快慢也有很大的关系,2者生长速率的匹配关系将影响碳化物以块状孤立或者片层共晶形貌析出。当碳化物的生长快于临近奥氏体生长时,主要形成块状孤立碳化物,而当2者的生长速率相近时,或者液析碳化物生长速率慢于奥氏体时,将倾向于形成片层共晶碳化物。这样的生长速率匹配关系导致碳化物在低冷速下更容易形成块状孤立碳化物,但在冷速提高后,块状孤立碳化物减少,而片层共晶碳化物增加。随着冷速继续提高,溶质元素扩散时间不足,以及奥氏体晶粒大量形核细化等因素都阻碍了合金元素的长程扩散,2种形貌的液析碳化物也都减少。这也是共晶碳化物面积随着冷速的变化出现了明显波动的原因。而加入稀土元素之所以能改变液析碳化物的尺寸和形貌,很可能与以下2个因素有关:① 稀土元素提高C扩散激活能,这已在固态相变中被证实[27],这样就可以延缓碳化物的生长,在缓慢冷却条件下,添加稀土元素的钢中共晶碳化物会比不添加稀土元素时更多,而孤立碳化物减少;② 添加稀土元素细化奥氏体晶粒已有报道[14],本实验中晶粒尺寸的统计结果也已经证实。奥氏体细化后,晶粒间距缩小,阻碍溶质长距离扩散,进而细化碳化物。根据以上提出的液析碳化物析出机制,给出了高碳铬轴承钢凝固液析碳化物形成机制和过程的示意图,如图11所示。当然这种析出过程未来还需相场模拟等介观尺度组织演化的计算方法进行验证。
图11
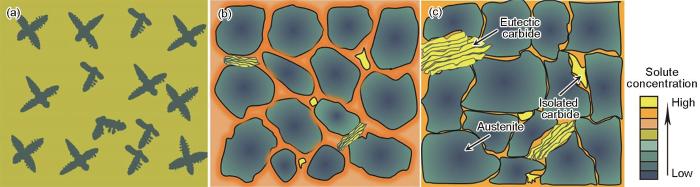
图11 液析碳化物的形成过程示意图
Fig.11 Schematic of the formation mechanism of primary carbide
(a) nucleation and growth of primary austenite at the early solidification
(b) primary carbides precipitate randomly among the austenite grains after solidification for a while and then grow in size via solute diffusion
(c) austenite grains stop growing and two typical morphologies of carbides form eventually at the end of solidification
综上可以看出,工业钢锭中液析碳化物的形成是一个多尺度的凝固问题。一次碳化物的形成除了与熔融液体中C与Cr、Fe金属元素原子间的吸引力较大、易形成团簇有关外,而且与介观尺度的奥氏体晶粒尺寸和局部的C、Cr元素分布有关。而局部的C、Cr成分又受宏观的传热传质过程影响,比如液体流动引起的宏观偏析。在严重的正偏析区域,C、Cr含量相对较高,为一次碳化物的形核析出和后续长大提供了充分的成分条件。此外,正偏析区域一般也对应着凝固缓慢的区域,甚至是最终凝固区域,奥氏体生长也相对缓慢,这也为液析碳化物的长大提供了充足的溶质扩散时间。基于这些影响机理,细化晶粒、加速凝固和减轻宏观偏析都是减少液析碳化物数量、减小液析碳化物尺寸甚至抑制液析碳化物形成的重要方法。
3 结论
(1) 液析碳化物主要有孤立块状和共晶片层状2种形貌,多随机分布于晶粒间;孤立碳化物尺寸在十至几十微米不等,在工业连铸锭中还会更大;液析碳化物的类型为M3C型渗碳体,Cr含量一般在15%以上,各元素含量不受冷速影响。
(2) 液析碳化物的形成过程受C、Cr元素扩散控制,冷速提高,凝固时间缩短,奥氏体晶粒生长快但尺寸小,导致液析碳化物细化,但数量增加,分布更加弥散均匀。
(3) 添加稀土元素对液析碳化物的成分无明显影响,但是在低冷速下可以有效细化奥氏体,进而在细化液析碳化物的同时还可以减少其数量。
(4) 趋近于平衡凝固的缓慢冷却条件下的试样中液析碳化物更加明显,表明液析碳化物的形成不是非平衡凝固的产物,而当前无论是伪二元还是三元平衡热力学相图尚不能预测GCr15系轴承钢凝固一次碳化物的形成。
来源--金属学报