分享:NiTi-Nb原位复合材料的准线性超弹性变形
姜江1, 郝世杰2, 姜大强2, 郭方敏2, 任洋3, 崔立山,2
1.
2.
3.
据文献报道,Nb纳米线增强NiTi记忆合金复合材料可展现超常的准线性超弹特性。为揭示该准线性超弹特性的产生和变形机制,通过真空感应熔炼、锻造、拔丝方法原位合成了NiTi-Nb复合材料丝材。TEM显微分析表明,Nb纳米线沿丝材轴向平行分布在纳米晶NiTi基体中。该材料在经历一次9%的预变形后会展现准线性超弹特性,其屈服强度达1.7 GPa,表观Young's模量约34 GPa,准线性超弹性应变接近5.5%。同步辐射高能X射线原位拉伸实验结果表明,准线性超弹性的产生与以下2点原因有关:(1) 复合材料经历预变形后,Nb纳米线和NiTi基体间会产生耦合力,再次加载时,NiTi所受的耦合拉应力可以将局部区域应力诱发马氏体相变所需的外应力降低到零附近,并且耦合力越大,加载初期的相变速率越高,经过适当的预变形后,加载初始就能够持续发生高速率相变;(2) NiTi中耦合拉应力呈梯度分布,使相变应力-应变曲线不再是常见的“平台型”,转变为“硬化型”斜线。
关键词:
长期以来,TiNi基记忆合金因具有优良的形状记忆效应和伪弹性等功能特性而受到学者们的广泛关注[1~16]。在过去的十年间,一种Nb纳米线增强NiTi记忆合金复合材料成为研究热点[17~25]。这种NiTi-Nb复合材料打破了纳米增强相在复合材料中难以展现其本征高性能的禁锢。其中,一篇发表在《Science》的研究[20]指出,若将记忆合金作为纳米线增强复合材料的基体,加载时基体的变形就会以应力诱发马氏体相变为主导,而不是像常规金属材料那样以位错滑移引起的塑性变形为主导。这样就会在一定程度上避免因界面出现位错堆积(应力集中)而对纳米线产生伤害,使复合态的纳米线展现出与自由态纳米线相当的超大弹性应变(4%~7%),获得了集高强度(1.65 GPa)、低模量(25.8 GPa)和准线性超弹性(准线性超弹性变形量6.4%)于一身的超常性能。这样的材料填补了金属、陶瓷和高分子三大类传统材料性能图表的空白区,在牙齿矫正器、心脏起搏器、人体可植入装置和柔性医疗器械等领域都有潜在的应用前景[26]。
根据以往的报道[20],NiTi-Nb复合材料的超常准线性超弹特性与应力诱发马氏体相变密切相关,但与二元NiTi合金相比,该相变具有以下3个特点:(1) NiTi-Nb复合材料需要经历一次适当的预变形之后,才能发生这种“准线性超弹”类型的相变;(2) 在展现准线性超弹特性的拉伸循环中,复合材料中的NiTi相在加载初始就会持续发生应力诱发马氏体相变,似乎此时开启相变所需的外应力降低到了零;(3) 在准线性超弹拉伸循环中,应力诱发马氏体相变并没有导致拉伸曲线出现“相变平台”,而是在加载之初,相变应变就与材料的初始弹性变形混合在一起,形成一条表观弹性模量(拉伸曲线斜率)低于30 GPa的准线性曲线。即相变曲线是“硬化型”的斜线而非通常的“平台型”的水平线。尽管这种奇特的应力诱发马氏体相变特征被归因于预变形后样品内部各复合组元间的耦合作用[20],但是该耦合作用具体如何导致准线性超弹性的产生,目前尚缺乏与之相关的实验性研究。本工作通过同步辐射高能X射线原位拉伸实验研究了不同预变形下NiTi-Nb复合材料内部复合组元间耦合状态的演变过程,并系统分析了准线性超弹特性的形成和变形机制。
1 实验方法
采用真空感应熔炼,将纯度为 99.95% (质量分数)的Ti、Ni 和 Nb熔炼成名义成分为Nb20Ti39Ni41 (摩尔比)的合金锭7 kg。将合金铸锭辅以热锻(热锻温度为850℃)和拔丝加工(拔丝工艺为: 先将锻造棒热拔到直径1.1 mm,再冷拔到直径0.35 mm。热拔温度为400~500℃;冷拔过程中,每当冷变形量达到70%左右就进行中间退火,中间退火温度为450~750℃,直径越小退火温度越低),最终获得直径0.35 mm的丝材作为样品。所有样品在测试前均先置于箱式炉中在350℃处理20 min,空冷。采用Tecnai F20透射电子显微镜(TEM)观察丝材样品的显微组织。采用WDT II-20型万能拉伸试验机对样品进行拉伸力学性能测试,加、卸载速率均为0.05 mm/s。为使样品展现准线性超弹特性,需先对其进行一次9%的预变形。预变形过程为将退火样品加载至9%并卸载,如图1a所示。本实验中涉及的预应变量均为预变形过程中的最大加载应变。为进行对比实验,另将一根二元NiTi丝依次进行最大加载应变为9%、5%和9%的3次拉伸循环,如图1b所示,可将其第一次加卸载循环视为预变形过程,后面的2次拉伸循环用于对比同样经历9%预变形后,二元NiTi合金与NiTi-Nb复合材料不同的应力-应变响应。采用美国阿贡实验室同步辐射高能X射线衍射(HE-XRD,11-ID-C beamline of the Advanced Photon Source,Argonne National Laboratory)设备测试样品中各复合组元的变形行为,高能X射线束斑尺寸为0.6 mm × 0.6 mm,波长0.010798 nm。采用自制原位拉伸台,在同步辐射高能X射线测试过程中对丝材样品进行原位拉伸。原位拉伸过程中,高能X射线束斑始终探测丝材的同一位置区域。
图1
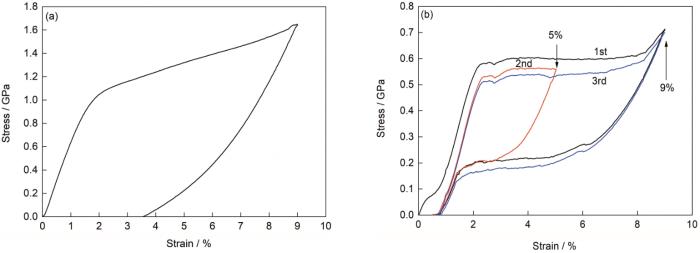
图1 NiTi-Nb复合材料的预变形过程曲线和二元NiTi合金丝的循环拉伸曲线
Fig.1 Pre-deformation process of the NiTi-Nb sample (a) and multiple-step cyclic stress-strain curves of a binary NiTi alloy (b)
2 实验结果与分析
2.1 NiTi-Nb复合材料的显微组织
图2a为NiTi-Nb复合材料丝材的TEM明场像。其中,深色衬度的条带状区域是富Nb相,而浅色衬度区域是NiTi相。由图可见,经过拔丝后,NiTiNb合金中的富Nb相都形成了Nb纳米线(富Nb相中仅固溶少量Ti和Ni,这里简称Nb纳米线),其直径基本介于25~50 nm之间,沿丝材轴向平行排列在NiTi基体中;NiTi相中可清晰分辨出多个纳米尺度(< 100 nm)的晶粒,说明NiTi基体是纳米晶材料。故而该材料是一种纳米线增强纳米晶基体复合材料。图2b为NiTi-Nb复合材料的同步辐射高能XRD花样,图片竖直方向为丝材轴向。可见,复合材料中含有bcc-Nb相和B2-NiTi母相。因此,材料中NiTi在室温下处于母相(奥氏体)状态。Nb(220)和Nb(110)晶面在竖直方向上出现强衍射斑点,说明拔丝加工使Nb相沿丝材轴向形成强织构。
图2

图2 NiTi-Nb复合材料丝材纵截面的TEM像及其同步辐射高能XRD花样
Fig.2 TEM bright field image of the longitudinal section microstructure of the NiTi-Nb composite wire (a) and 2D high-energy XRD pattern of the wire (B2—B2-NiTi, Nb—bcc-Nb) (b)
2.2 NiTi-Nb复合材料的准线性超弹性力学响应
NiTi-Nb复合材料样品经历一次9%预变形之后,再次拉伸的应力-应变曲线如图3a所示(预变形过程如图1a所示)。可见,材料展现出高强度、低模量、准线性超弹特性,屈服强度达到1.7 GPa,表观Young's模量约34 GPa,准线性超弹性应变接近5.5%。将另一根同样经过9%预变形的复合材料样品,依次进行最大加载应变为5%和断裂应变的2次拉伸循环,结果如图3b所示。可见,在最大应变为5%的拉伸循环中,该NiTi-Nb复合材料的相变滞后环狭长,滞后曲线呈准线性。作为对比,常规二元NiTi合金的力学响应行为如图1b所示。由图可见,经过一次9%拉伸循环后,二元NiTi合金的拉伸循环曲线仍呈现出类四边形滞后环,并无线性超弹特征。
图3
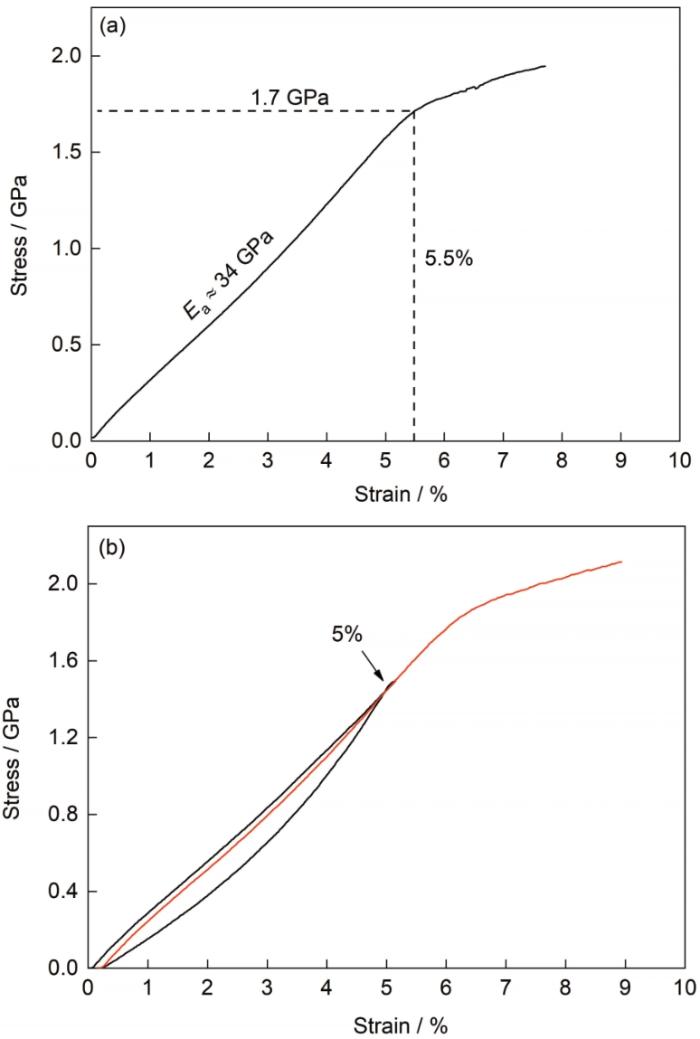
图3 NiTi-Nb复合材料的准线性超弹性应力-应变曲线
Fig.3 Quasi-linear superelasticity stress-strain curves of the NiTi-Nb composite
(a) typical macroscopic mechanical property of the NiTi-Nb composite after pre-deformation (Ea—apparent Young's modulus)
(b) cyclic tensile stress-strain curves of the NiTi-Nb composite after pre-deformation
2.3 预变形对NiTi-Nb复合材料的影响
将退火状态的样品进行连续6次加、卸载循环拉伸测试,各循环的最大加载应变依次为5.5%、6.5%、7.5%、9.0%、9.8%和断裂应变,拉伸曲线如图4所示。在这些循环中,若将其中任意一次拉伸循环视为其后一次循环的预变形过程(预应变量为预变形过程中的最大加载应变),则该曲线具有如下特点:(1) 随预应变量的增加,卸载后的残余应变量逐渐增加(塑性变形量逐渐增加);(2) 第1次加载样品仅发生一次屈服,而第2~5次加载样品发生两次屈服。通常认为第一次屈服与应力诱发马氏体相变有关,而第二次屈服则对应上次拉伸循环的最大加载应变位置(应变记忆效应[29,30]);(3) 到了第5次循环(经历9%预变形后),“第一次屈服”变得非常不明显,近乎消失,而“第二次屈服”成为该循环真正的屈服,此时材料展现出近乎完美的准线性超弹的变形特性。可见,“第一次屈服”的消失导致了准线性超弹性的产生;(4) 第6次加载曲线虽然也接近线性,但超弹性应变不到5%,超弹特性较第5次循环差。
图4
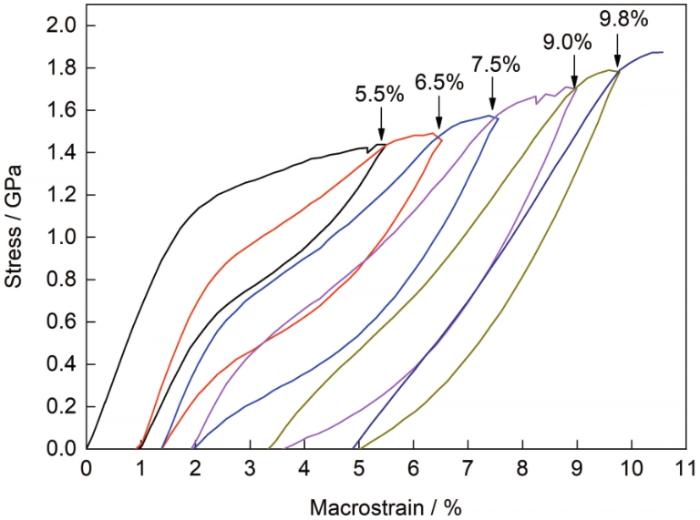
图4 NiTi-Nb复合材料不同拉伸循环的应力-应变曲线
Fig.4 Multiple-step cyclic stress-strain curves of the NiTi-Nb composite sample, where the max strains of each cycle are 5.5%, 6.5%, 7.5%, 9.0%, 9.8%, and fracture strain in sequence
图5为以上6次拉伸循环对应的同步辐射高能X射线原位拉伸测试谱线。该谱线显示了样品中垂直于丝轴向的Nb(220)、B2-NiTi(211)以及B19'-NiTi(001)晶面的衍射峰在6次拉伸循环中的演变。可见,各衍射峰的峰位均随加载而右移(面间距增加),并随卸载而左移(面间距减小)。同时,B2(211)母相峰的强度随着加载而衰减,直至消失(正相变),并随着卸载而浮现并增强(逆相变)。对应母相峰的衰减和增强,B19'(001)马氏体峰随着加载而逐渐浮现、增强,并随着卸载而逐渐消失。这说明在加、卸载过程中,复合材料中的NiTi分别发生了B2-B19'应力诱发马氏体相变和B19'-B2逆相变。
图5
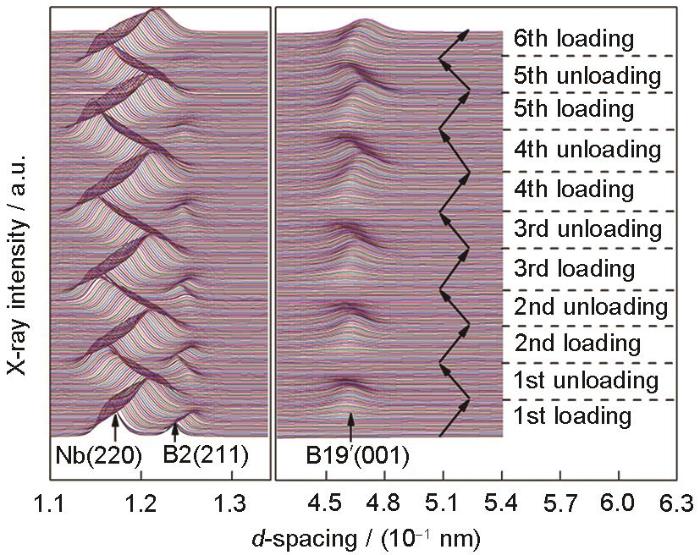
图5 NiTi-Nb复合材料6次拉伸循环对应的的同步辐射高能X射线原位拉伸衍射谱线
Fig.5 Evolutions of the diffraction peaks of Nb(220), B2-NiTi(211), and B19'-NiTi(001) planes in NiTi-Nb composite perpendicular to the loading direction during the multiple-step cyclic tensile test
图6给出了6次加载过程中B19'(001)马氏体峰的面积积分曲线,并对第2~6次加载曲线在横坐标轴上进行了适当的平移以便区分。由于B19'(001)峰面积的变化反映了材料中马氏体含量的改变,故而可用来定性分析不同加载阶段应力诱发马氏体相变的转变情况。B19'(001)峰面积曲线的斜率越高,则马氏体相变的转变速率越高。图6中也给出了这6次加载所对应的宏观拉伸应力-应变曲线,用于对比相变与材料力学响应之间的关系。由图可见,前4次拉伸过程中,每次加载,B19'(001)峰面积曲线先以较低的斜率缓慢升高(相变速率低),到达一个“转折点”后,又突然以较高的斜率接近线性升高(相变速率高)。这些标志着相变速率突然增加的“转折点”恰与宏观拉伸曲线的“第一次屈服”位置相对应,如图中竖直虚线标明。上述现象说明在这些循环中,样品在“第一次屈服”之前就发生了应力诱发马氏体相变,只是相变速率较低,相变并不明显;而在“第一次屈服”后的加载过程中,相变转而以更高的速率持续进行。由于相变应变(非弹性因素)的引入会使样品的表观弹性模量(应力-应变曲线斜率)降低,并且相变速率越高,表观模量越低,因此,正是相变速率的突然升高大幅降低了表观模量,使拉伸曲线出现“第一次屈服”。在第5、6次循环中,B19'(001)峰面积曲线在加载初期几乎就以最高的斜率线性升高,即加载初始就发生了高速且持续的应力诱发马氏体相变,导致整个加载前中期相变速率的差别不大。表现在拉伸曲线上,则是“第一次屈服”之前、之后2个阶段的表观模量非常接近,“第一次屈服”变得难以辨认,拉伸曲线更接近线性。图7总结了这6次循环中,加载初期和“第一次屈服”后2个阶段B19'(001)峰面积-宏观应变曲线的斜率(表征相变速率)。可以看出,随着预变形量的增加,加载初期的相变速率逐渐升高,而“第一次屈服”后的相变速率略有降低,2者逐渐接近,最终达到一致。由此可见,准线性超弹性的产生源于“第一次屈服”的消失,而“第一次屈服”的消除源于加载初期和“第一次屈服”后2个阶段的相变速率趋于一致。
图6
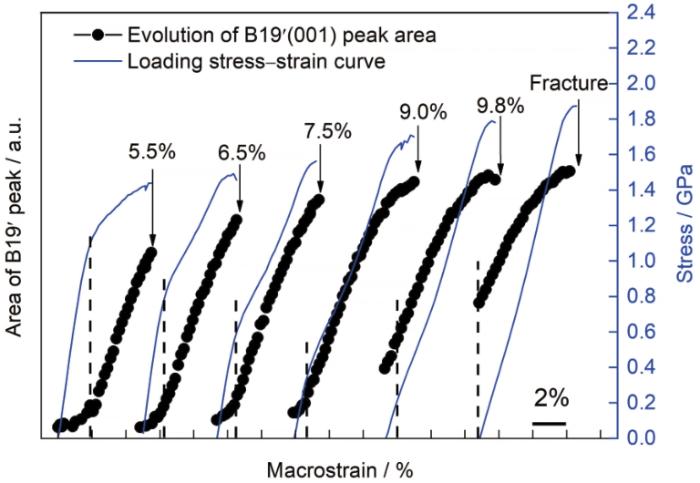
图6 NiTi-Nb复合材料在6次加载过程中的应力-应变曲线,以及在加载过程中NiTi马氏体峰面积随宏观应变的演变曲线
Fig.6 Stress-strain curves of the as-annealed NiTi-Nb composite, and the corresponding B19'-NiTi(001) peak area curves in the 6 loading processes (In each loading process, the “first yield point” on the stress-strain curve just corresponds to the “turning point” on the evolution curve of B19' peak areas, as marked by each dash line)
图7
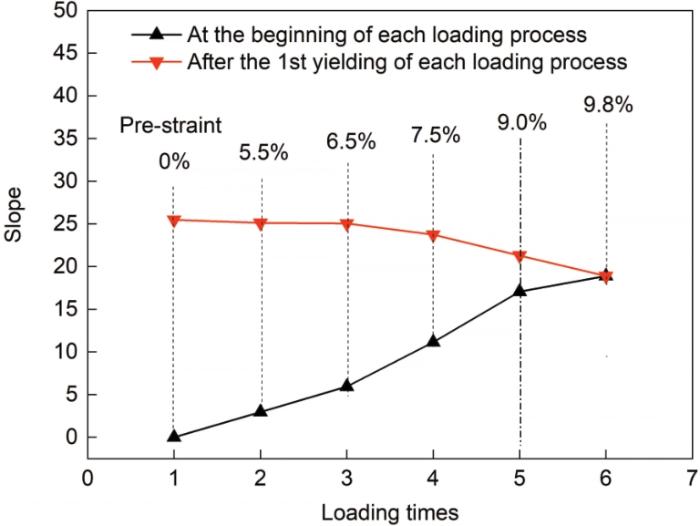
图7 实验涉及的6次循环中,每次加载的初期和“第一次屈服”后2个阶段B19'(001)峰面积-宏观应变曲线斜率的演变
Fig.7 Slopes of B19'-NiTi(001) peak area curves at the beginning and after the 1st yielding of each loading process, which can be seen as a measurement of the transformation velocity
在实验涉及的6次拉伸循环过程中,垂直于丝轴向的Nb(220)晶面的晶格应变随宏观应变的演变曲线如图8a所示。考虑到弹性应变与应力成正比关系,故而图8a亦反映了复合态Nb纳米线分担的轴向应力在不同拉伸阶段的演变情况。由图8a可以看出,第一次卸载后,Nb纳米线产生了0.65%的残余晶格压应变(粗略取Nb的模量93 GPa[31],换算成压应力约0.6 GPa)。在随后的拉伸循环中,每次卸载后,Nb纳米线的残余压应变随着预变形量的增加而呈现先增加后减小趋势。其中,在第3次卸载后Nb纳米线的残余压应变最大(晶格压应变1.59%,换算成压应力约1.48 GPa)。与图8a类似,图8b为B2-NiTi母相(211)晶面的弹性晶格应变-宏观应变曲线,表征了不同宏观加载阶段母相的轴向受力状态。由于母相在加载过程中逐渐消失,而在卸载过程中逐渐浮现,同时给出加、卸载曲线会非常混乱,故而图中只给出各拉伸循环的加载曲线。由图可见,从第二次加载开始,每次加载初始NiTi母相都处于受拉状态,并且该残余拉应变随着预应变量的增加而逐渐增加。
图8
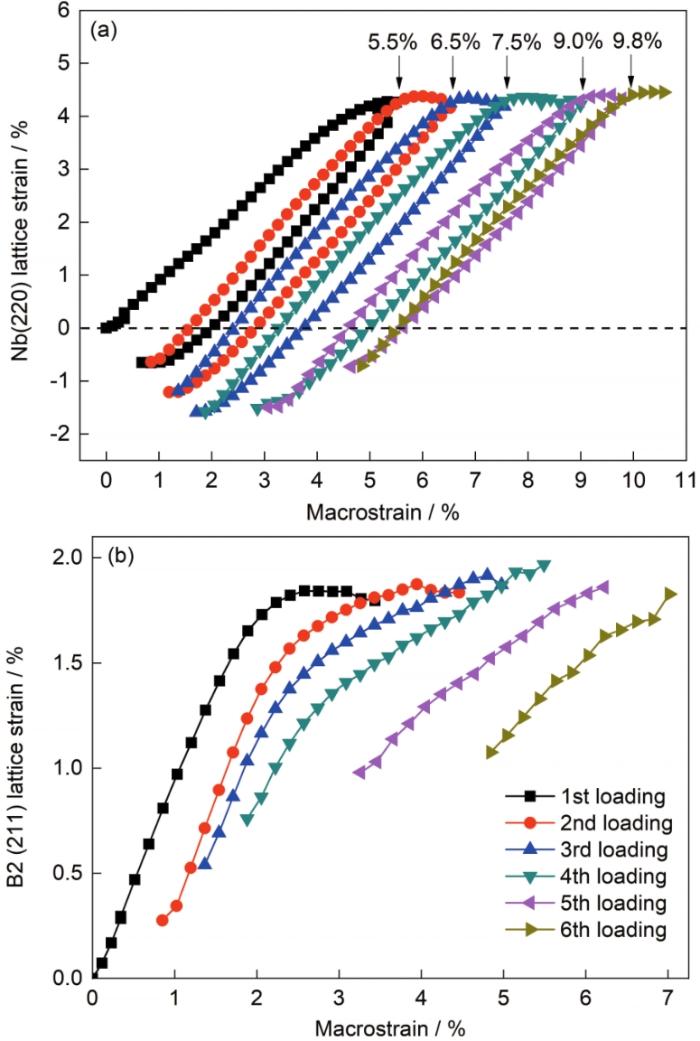
图8 Nb纳米线的弹性晶格应变-宏观应变曲线,及6次加载过程中B2-NiTi母相的弹性晶格应变-宏观应变曲线
Fig.8 Evolutions of the lattice strain for Nb(220) plane (a) and B2-NiTi(211) plane (b) perpendicular to the loading direction during the tensile process, which can be regarded as elastic strain vs total strain (elastic + plastic strain) relation of the embedded Nb nanowire and NiTi phase
2.4 准线性超弹特性的形成原因与变形机制
综合图8a和b可以看出,预变形使Nb纳米线受压而使NiTi母相受拉。这“一压一拉”的耦合关系及其耦合过程可通过图9a和b示意:当材料经历预拉伸并卸载后,Nb纳米线发生了塑性变形,并阻挡了NiTi的相变超弹性回复(图9a),因此2者间产生了耦合力,NiTi受到Nb纳米线的耦合拉应力,而Nb纳米线受到NiTi的耦合压应力(图9b)。考虑到2者间耦合力是通过界面传递的,此时NiTi内部应力分布必然会变得不均匀(NiTi母相峰半高宽升高,图9c),界面附近受到Nb纳米线的耦合拉应力最大,而NiTi芯部区域耦合拉应力最小,从界面到芯部会形成梯度应力场(图9b)。在随后的加载过程中,NiTi所受的耦合拉应力能够为应力诱发马氏体相变提供驱动力,而驱动力越大的区域诱发相变所需的外应力越低,那么相变必然从驱动力最大的界面附近开始,沿着梯度应力场向NiTi芯部推进,如图9d所示意。在梯度应力场中,越靠近芯部耦合拉应力越低,因而加载过程中诱发相变从界面向芯部推进所需的外应力逐渐升高,使相变(应力-应变)曲线呈“硬化型”的斜线而非通常的“平台型”的水平线。
图9
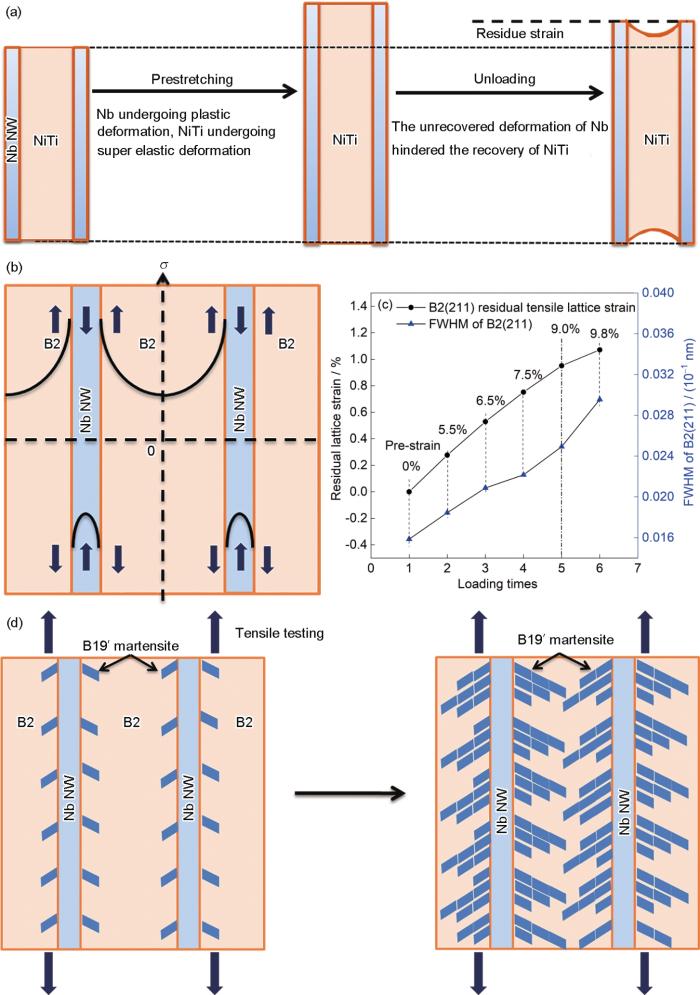
图9 样品预变形示意图,预变形后样品内部应力分布示意图,B2-NiTi母相在每次加载前的衍射峰半高宽值和残余应变,及预变形后再次加载过程中马氏体相变从界面向NiTi芯部推进示意图
Fig.9 State evolution diagrams of samples during the tensile loading after a pre-deformation
(a) schematic of the pre-deformation process (NW—nanowire)
(b) schematic of stress distribution inside the specimen after pre-deformation (σ—stress)
(c) full width half maximum (FWHM) values and residual tensile lattice strains of B2-NiTi at the beginning of each loading process, where the increase of FWHM indicates that the stress distribution in B2-NiTi becomes more unequal, and the increase of residual tensile lattice strain indicates the increasing of coupling tensile stress in B2-NiTi
(d) schematic of martensitic transformation process which starts near the NiTi/Nb interface and then gradually moves to the core of B2-NiTi when loading a pre-deformed specimen
则在实验涉及的各拉伸循环的加载起始点,样品的状态演变情况及其对相变的影响如下:随着预变形量的增加,NiTi母相所受耦合拉应力的平均值逐渐升高(母相的残余晶格拉应变逐渐升高,图8b和9c)。当NiTi界面附近某些区域的耦合拉应力接近甚至达到应力诱发马氏体相变所需临界应力(通常是NiTi应力诱发马氏体相变的“上平台”力)时,分布于这些区域的NiTi母相便可在下次加载初始就直接发生马氏体相变,出现开启相变所需的外应力几乎降低到零的现象。继续加载,相变就会沿着梯度应力场从界面向NiTi芯部推移(如图9d所示),展现“硬化型”相变曲线。结合有关图6和7的分析,当预变形量较低时(如前4次拉伸循环),虽然也会出现加载初始就相变的现象,但由于加载初期由耦合拉应力提供的相变驱动力较低(预变形量较小,NiTi母相所受耦合拉应力的平均值较低),导致加载初始的相变速率很低,远低于“第一次屈服”后的相变速率,因而没有出现准线性超弹性变形。随着预变形量的继续增加,NiTi母相所受耦合拉应力的平均值随之升高,加载初期由耦合拉应力提供的相变驱动力逐渐增大,使初始相变速率逐渐升高。当加载初期相变速率增长至接近“第一次屈服”后的相变速率时(如第5次拉伸循环),“第一次屈服”就会变得难以辨认,从而使应力-应变加载曲线更接近线性,展现出完美的准线性超弹特征。但是,再进一步增加预变形量(如第6次拉伸循环),由于相变已接近尾声,该加载循环所涉及的相变转变量大幅减少(图6中第6次加载过程的相变转变量最少。每次加载过程中涉及的相变转变量可通过B19'马氏体峰面积在该加载过程的增量度量),由相变产生的超弹性变形量随之降低。因而,第6次加载曲线虽然也接近线性,但准线性超弹性应变不到5%,超弹特性较第5次循环差。
3 结论
(1) 通过真空感应熔炼、锻造、拔丝加工获得原位自生的Nb纳米线增强NiTi记忆合金复合材料丝材。NiTi基体为纳米晶基体,Nb纳米线沿丝材轴向平行排列在NiTi基体中。
(2) 该NiTi-Nb复合材料在经历一次9%的预变形后会展现高强度、低模量、准线性超弹特性。其屈服强度达到1.7 GPa,表观Young's模量约34 GPa,准线性超弹性应变接近5.5%。
(3) 复合材料经过较低的预变形后,再次加载会出现2次屈服。其中“第一次屈服”与应力诱发马氏体相变有关。“第一次屈服”之前相变就已经发生,只是相变速率很低;“第一次屈服”之后相变速率大幅提高,使拉伸应力-应变曲线斜率陡然降低,从而产生了“第一次屈服”。
(4) 随着预变形量的增加,“第一次屈服”前、后2个阶段的相变速率逐渐接近。当这2个阶段的相变速率非常接近时,“第一次屈服”基本消失,材料展现出准线性超弹特性。故准线性超弹性的产生源于“第一次屈服”的消失,而“第一次屈服”的消除源于加载初期和“第一次屈服”后2个阶段的相变速率趋于一致。
(5) 同步辐射高能X射线原位拉伸测试表明,预变形使NiTi基体和Nb纳米线间产生耦合力,Nb纳米线受耦合压应力,而NiTi母相受耦合拉应力。并且,随着预变形量的增加,NiTi母相所受耦合拉应力逐渐增加。
(6) 分析了预变形后再次加载过程中NiTi-Nb复合材料的变形机制。加载之前NiTi界面耦合力最大,而芯部耦合力最小,从界面到芯部存在梯度应力场。加载过程中应力诱发马氏体相变从界面向NiTi芯部推进,并且诱发相变从界面向芯部推进所需的外应力逐渐升高,使相变应力-应变曲线呈“硬化型”斜线。
(7) 当界面附近耦合力达到诱发马氏体相变所需的临界应力时,便可以在下次加载初始就发生应力诱发马氏体相变。随着预变形量的增加,母相所受耦合拉应力的增加导致加载初期相变驱动力的增加,有助于促进加载初期相变速率的提高,当预变形量(耦合拉应力)足够高时,加载初期的相变速率便可以接近甚至达到“第一次屈服”之后的相变速率,使拉伸曲线展现准线性超弹特征。