分享:新型钴基高温合金中W元素对蠕变组织和性能的影响
以γ?相强化的Co-Al-W高温合金(Co-9Al-xW,x = 8、9、10,原子分数,%)为研究对象,耦合CALPHAD和晶体塑性本构关系,建立了高温加载时微观组织演化的三元弹塑性相场模型,考察了W含量对蠕变过程中γ?相演化行为和蠕变性能的影响。结果表明,随W含量增加,γ'相体积分数增加,γ基体塑性变形降低,筏化形成并提前,导致蠕变性能提高。不变矩分析表明,9W和10W合金中筏组织形成是出现稳态蠕变阶段的主要原因。应力/应变分析表明,高W合金γ基体中较大的错配应力减小了塑性变形。
关键词:
以高温稳定的γ'-Co3(Al, W)沉淀相强化的新型钴基高温合金[1],具有高熔点、优异的抗热腐蚀和热疲劳性能以及良好的焊接性能,合金主要由无序fcc结构的γ基体和有序L12结构的γ'强化相组成。在高温应力条件下,立方状γ'会发生定向粗化形成筏排组织,进而对高温蠕变性能产生重要影响。已有研究[2,3]表明,对于正错配度的钴基高温合金,拉伸蠕变条件下形成平行于应力轴的P型筏组织,压缩蠕变条件下形成垂直于应力轴的N型筏组织。Xue等[4]认为N型筏可作为一种有效的强化机制,促使蠕变速率持续降低。Lu等[5]发现Co-Al-W-Ta-Ti合金在1273 K、137 MPa蠕变过程出现2个稳态阶段,其中第一稳态阶段与P型筏组织形成有关,而第二稳态阶段则与γ/γ'拓扑反转结构有关。有研究[6,7]发现,提高γ'相的体积分数有利于提高蠕变性能。W是形成γ'相的必需元素,其含量变化显著影响γ?相体积分数[8~10]。蠕变测试表明[9],高W合金具有更优的蠕变性能。然而,W含量变化也会影响γ/γ'两相错配度、层错能、扩散系数等,使合金在蠕变过程中表现出独特的组织演化和变形行为。
相场法作为微观组织模拟的强有力手段,可通过耦合温度场、溶质场及其他外场实现宏微观尺度的结合,现已广泛用于凝固、晶粒长大、固态相变等领域[11]。近年来,塑性理论被引入到描述固态相变的弹性相场模型中,用以模拟外力作用下合金微观组织演变。Gaubert等[12]和Cottura等[13]将唯象的晶体塑性本构关系耦合进相场模型,得到了与实验结果相似的γ?筏化模拟结果。Wang[14,15]将该模型用于钴基合金,从应力/应变和扩散势的角度分析了ERBOCo-2Ta合金在拉伸和压缩蠕变条件下的筏化行为。通过改变应力大小和方向,Yang等[16]和Ali等[17]探索了介于N型和P型筏之间的45°筏形成机制,认为是局域非均匀变形带来的应变集中导致的γ?形成元素沿对角线方向定向扩散。Zhou等[18]通过分析筏结构长宽比研究了错配度对筏化行为的影响。Nguyen等[19]采用不变矩算法对筏化行为进行了定量表征。Yang等[20,21]进一步在模型中引入蠕变损伤机制,将组织演化模拟从初期的筏化阶段扩展至整个蠕变过程,首次实现了Ni-Al二元合金微观组织、蠕变性能及断裂寿命的同步预测;而Chen等[22]基于该模型,揭示了Co-Al-W-Ta合金950℃、150 MPa条件下的双极小蠕变行为。
目前关于高温合金的相场模拟大多数采用伪二元相场模型。考虑到Co、Al、W是新型钴基高温合金中形成γ'强化相的必需元素,本工作基于相图计算(CALPHAD)建立了耦合蠕变损伤的三元弹塑性相场模型。利用该模型考察了Co-9Al-xW (x = 8、9、10,原子分数,%)合金在900℃、275 MPa蠕变过程中的组织演化,分析了W元素含量对蠕变组织和筏化行为的影响规律,并从应力/应变角度探索了W含量对蠕变性能的影响。
1 模型及方法
1.1 相场模型
Co-Al-W三元合金蠕变过程中γ/γ'两相组织采用浓度序参量cAl( r, t)、cW( r, t)和结构序参量φp ( r, t)描述,根据质量守恒,Co浓度序参量为(1 - cAl( r, t) - cW( r, t))。序参量随空间( r )和时间(t)的演化过程通过相场模型中Cahn-Hilliard方程和Ginzburg-Landau方程控制[23]:
式中,Mij 和L分别为化学迁移率和界面迁移率。当(φ1, φ2, φ3, φ4) = (1, 0, 0, 0)、(0, 1, 0, 0)、(0, 0, 1, 0)、(0, 0, 0, 1)时表示γ'相的4种反相畴,(φ1, φ2, φ3, φ4) = (0, 0, 0, 0)时表示无序γ基体。假定γ和γ'两相摩尔体积Vm为常数且相等,取值为6.8 × 10-6 m3/mol[24]。F为系统自由能,包括体自由能fbl、梯度能fgra和弹性应变能fel 3部分:
体自由能fbl根据KKS理论[25]表示为γ'析出相和γ基体相自由能之和:
式中,
式中,i, j和k代表Al和W元素;
为避免同一时空下出现2种γ'畴,引入γ'不同畴之间的能垒,即
KKS模型中,假定界面处共存的γ相和γ'相具有相同的化学势[25]:
梯度能fgra包括成分和结构序参量梯度能2部分,以表征成分和结构不均匀对界面能的贡献[12]:
式中,梯度项系数α和β与界面能和界面宽度有关,取值为α = 1 × 10-8 J/m,β = 2 × 10-10 J/m。
根据Khachaturyan等[30]建立的非均匀弹性理论,fel可表示为[30]:
式中, λouvw ( r )为局域弹性模量张量,
根据二元相场模型计算弹性非均匀系统中弹性模量的方法[31],这里将 λouvw ( r )扩展为Al和W浓度的函数:
式中,
式中,
表1 γ、γ'两相弹性常数
Table 1
Alloy | Elastic constant of γ / GPa | Elastic constant of γ' / GPa | ||||
---|---|---|---|---|---|---|
|
|
|
|
|
|
|
Co-9Al-8W (8W) | 315 | 209 | 160 | 361 | 190 | 212 |
Co-9Al-9W (9W) | 316 | 363 | ||||
Co-9Al-10W (10W) | 317 | 364 |
控制方程(1)中,Mij 与原子迁移率Ml (l = Al、Co、W)有关:
式中,δil 和δjl 为Kronecker δ函数,Ml 从动力学数据库获取[32]。
1.2 晶体塑性模型
对于施加外力发生塑性变形的系统,弹性应变
式中,
对于γ→γ'相变,
塑性应变
式中,
式中,θ控制滑移系开动阈值在γ/γ'界面处的演化,取值为-5;μ为剪切模量,对于单晶高温合金来说,μ =
表2 γ和γ'中滑移系开动阈值
Table 2
Alloy |
|
|
---|---|---|
8W | 18 | 210 |
9W | 26 | 235 |
10W | 30 | 260 |
钴基合金γ基体中位错运动以{111}<110>八面体滑移为主,而γ'相中以{111}<112>十二面体滑移为主。由于塑性变形主要发生在γ基体中,本工作γ、γ'两相中的位错运动均采用{111}<110>八面体滑移系描述,如图1所示。12个八面体滑移系可分为(B2, D1, A2, C1)、(B4, D4, A3, C3)和(B5, D6, A6, C5) 3组,每组中的4个滑移系运动行为相同[39]。
图1
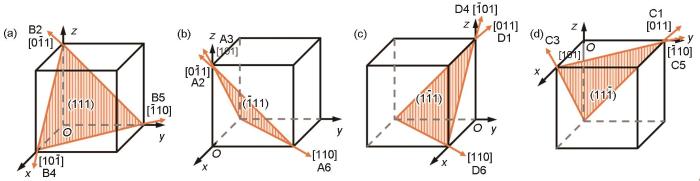
图1 八面体滑移系
Fig.1 Octahedral slip systems of fcc structure
(a) (111) plane (b) (
对于扩散控制的蠕变过程,由于建立力学平衡所需时间远比元素扩散所需时间短得多,因此,在任何状态下,系统总是满足力学平衡条件:
1.3 模型验证
图2是基于以上模型及参数预测的Co-9Al-xW (Co-9Al-8W、Co-9Al-9W、Co-9Al-10W,下文分别简记为8W、9W、10W)合金在900℃、275 MPa压缩条件下的蠕变应变和蠕变速率曲线,其中实线代表模拟结果,散点代表实验结果[9]。对比相同蠕变时间下模拟预测和实验测量的塑性变形,发现9W合金的预测结果与实验值偏离小于7%,8W合金的偏离小于17%,说明建立的三元弹塑性相场模型能较好地预测Co-Al-W三元合金的蠕变性能。
图2
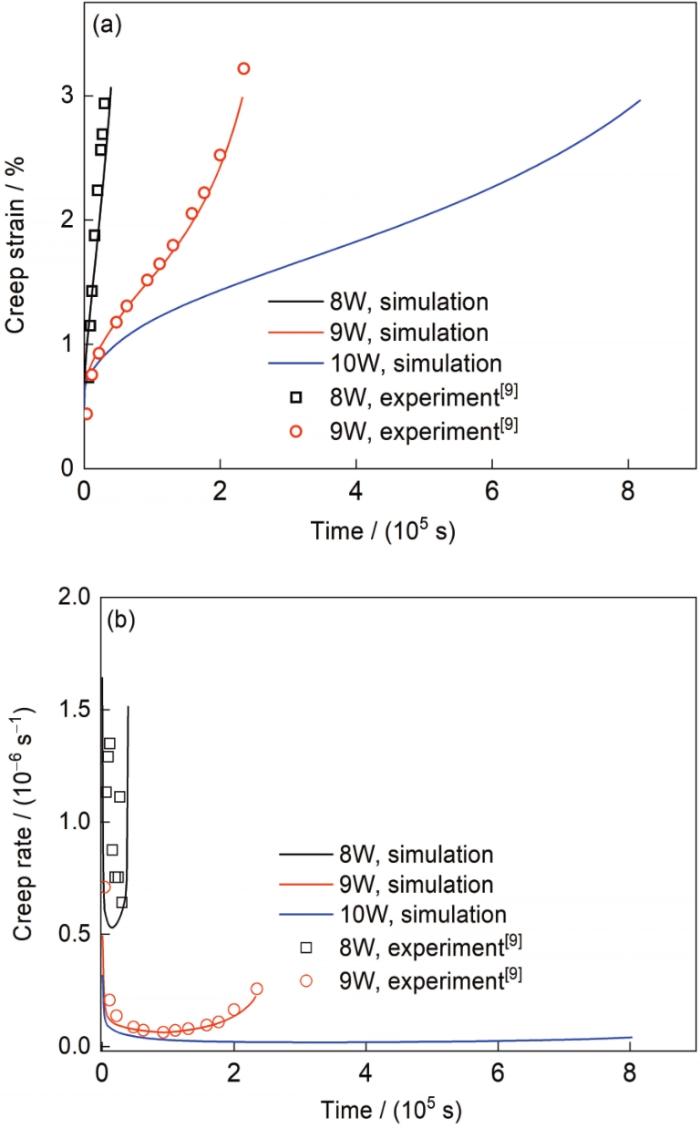
图2 蠕变应变和蠕变速率曲线
Fig.2 Simulated and experimental[9] creep property curves of Co-9Al-xW alloys
(a) creep strain (b) creep rate
1.4 筏组织分析方法
采用图像识别领域的矩技术对蠕变过程中的γ?相演化进行表征。Nguyen等[19]的研究表明,二阶不变矩谱(second order moment invariant map,SOMIM)可以较好地区分筏化和未筏化组织。立方状γ?具有高的不变矩(moment invariant,MI)值,位于SOMIM谱的右上角,而筏状γ'具有低的MI值,位于SOMIM谱的左下角。二阶矩
式中,A为物体的面积,
2 模拟结果与分析
2.1 W含量对蠕变组织的影响
图3所示为8W、9W、10W合金蠕变过程中的组织演化,图中γ/γ'两相组织通过序参量场(φ1 + φ2 + φ3 + φ4)用灰度图表示,箭头代表应力施加方向。从模拟结果可看出,压缩蠕变条件下,3种合金中γ'相均发生垂直于应力轴的定向粗化,但其形貌和粗化程度明显不同。采用二阶不变矩对蠕变过程中的微观组织形貌进行分析。图4为达到不同应变时γ'相的SOMIM谱,其中散点代表单个γ'的不变矩(
图3
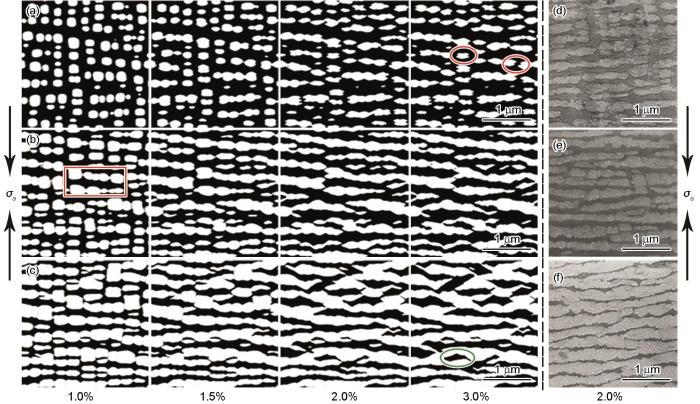
图3 不同W含量合金在900℃、275 MPa压缩蠕变过程中γ/γ?两相组织演化
Fig.3 Simulated (a-c) and experimental[9] (d-f) results of γ/γ' micrstructures at different plastic strains (1.0%, 1.5%, 2.0%, 3.0%) during 900oC, 275 MPa compressive creep for alloys with different W contents (The arrows represent the applied compressive stress σa; the red elliptical regions imply the corners of γ' precipitate protruding outward; the red rectangular region and the green elliptical region implies the formation of continuous rafts and “small island” γ matrix embedded in the rafted γ', respectively) (a, d) 8W (b, e) 9W (c) 10W (f) 11W (Co-9Al-11W)
图4
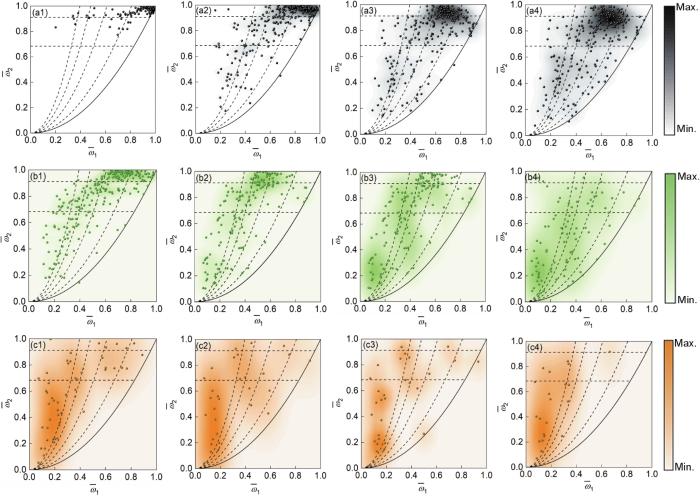
图4 不同应变下的二阶不变矩密度谱(SOMIM)
Fig.4 Second order moment invariant maps (SOMIM) for 8W (a1-a4), 9W (b1-b4), and 10W (c1-c4) at strains of 1.0% (a1-c1), 1.5% (a2-c2), 2.0% (a3-c3), and 3.0% (a4-c4) (
蠕变前期(变形为1.0%),8W合金中γ'相保持立方状,而9W合金中γ'相已出现沿水平方向的轻微延伸,且竖直通道距离短的一些γ'相在延伸过程中已发生合并形成连续筏,如图3b中红色方框所示,该合并现象在10W合金中更加明显。由于该阶段8W和9W合金中γ'相近立方状,其SOMIM谱的最大分布均位于上部,
进一步统计蠕变过程中SOMIM谱在0 <
图5
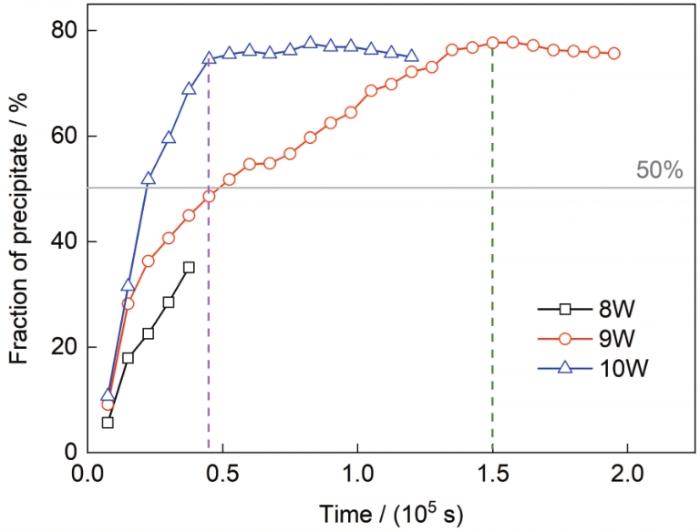
图5 SOMIM中0 <
Fig.5 Fraction of γ? precipitates in the SOMIM for which 0 <
二阶不变矩具有旋转、平移和缩放不变的特征,故无法定量表征γ'相的体积分数、长度和宽度等组织特征。图6为统计的蠕变过程中的组织特征演化。从图6a可以看出,整个蠕变过程中8W、9W、10W合金的γ'相体积分数基本为常数,分别为31%、44%、56%,接近实验报道值34% (8W)和41% (9W)[9]。从图6b~d可以看出,9W和10W合金的筏长度、筏厚度和通道宽度均在蠕变初期快速变化,之后趋于稳定,而8W合金的筏特征在整个蠕变过程中均呈现较为快速的变化。筏厚度快速下降以及筏长度和γ通道宽度快速增加的现象说明,压缩蠕变过程垂直于外力方向的γ'相边缘元素溶解向平行于外力方向的γ通道扩散发生定向粗化。对比3种合金的筏组织,发现在整个蠕变过程中,10W合金的筏最宽最长且通道宽度小,9W合金次之,8W合金的筏最窄最短同时通道宽度最大,该趋势遗传了蠕变初始时的组织差异。
图6
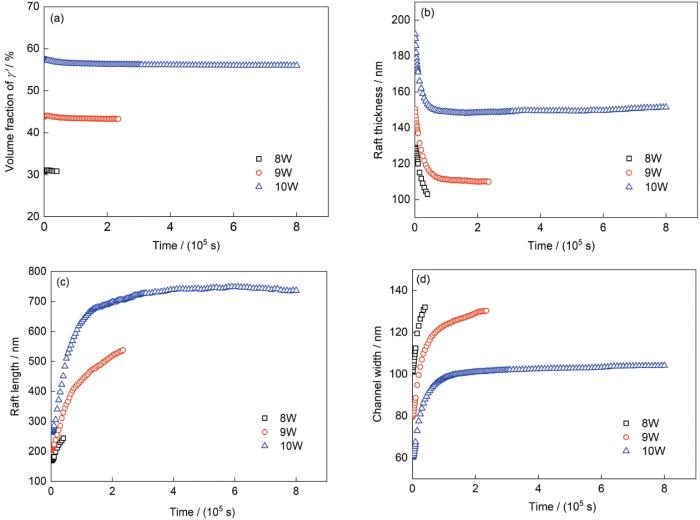
图6 蠕变过程中筏组织特征演化
Fig.6 Raft structure characteristics variations during 900oC, 275 MPa creep for 8W, 9W, and 10W alloys
(a) γ' volume fraction (b) raft thickness (c) raft length (d) γ channel width
2.2 W含量对蠕变性能的影响
根据模拟结果,比较W含量对蠕变性能的影响。从图2可以看到应变达到3.0%时,8W、9W、10W合金所需时间分别为39.38、232.5和817.5 ks,蠕变过程中的最小蠕变速率分别为5.30 × 10-7、6.30 × 10-8和1.92 × 10-8 s-1。该结果说明,Co-Al-W三元合金中增加W含量可提高其蠕变性能。从蠕变速率曲线可以看出(图2b),3种合金的蠕变行为存在差异:随W含量增加,蠕变第二阶段由瞬态阶段转变为稳态阶段,且10W合金在模拟结束时仍处于稳态蠕变阶段。由于筏组织在钴基合金蠕变过程中阻碍位错运动,起强化作用[4]。结合组织图和筏化过程分析可知,未形成筏组织是8W合金呈现瞬态蠕变的主要原因,而连续筏组织的形成使得9W和10W合金呈现稳态蠕变阶段。
蠕变应变是局域塑性变形的宏观表现,图7为不同蠕变应变下的塑性变形场。可以看出,蠕变过程中3种合金的变形趋势基本一致。蠕变初期,塑性变形主要发生在水平γ通道且变形较均匀;随蠕变进行,局域塑性变形增加,其中γ通道中沿<011>方向的塑性变形增加较为显著,这是由于在[001]方向的单轴加载条件下<011>方向的Schmid因子最大导致其分切应力最大的结果,同时,γ'相中也逐渐发生变形;蠕变后期,在<011>和<0
图7
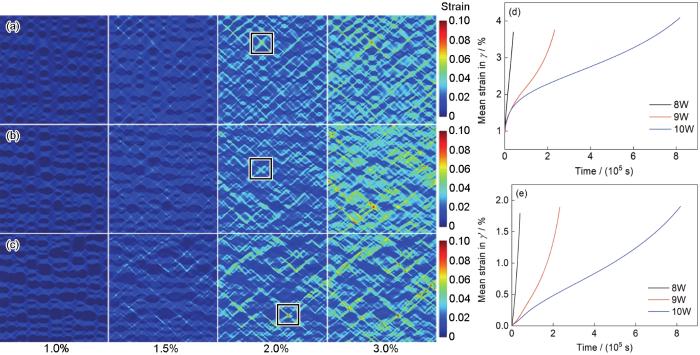
图7 蠕变过程中塑性变形演化
Fig.7 Evolution of plastic strain during creep for alloys 8W (a), 9W (b) and 10W (c), and mean strain in γ (d) and γ' (e) phases (The box areas show the large plastic deformations)
局域塑性变形是所有滑移系变形之和,而滑移系运动的驱动力由分切应力τ和位错运动阻力r以及合金自身抗力r0共同决定。这里以(
图8为A2滑移系蠕变过程中分切应力的演化。可以看出,随蠕变进行,3种合金在γ基体中的分切应力逐渐降低,而在γ'相中的分切应力逐渐升高。这是由于γ基体中位错开动,部分应力被释放,与此同时,位错在γ/γ'界面塞积使得γ'相中应力增加。比较3种合金γ基体的分切应力,相同蠕变应变内,8W合金的分切应力最高,9W合金次之,10W合金最低。根据γ、γ'两相中平均分切应力<τ>演化(图8d和e)可知,γ和γ'两相中的分切应力随W含量增加均降低。具体来说,整个模拟过程中,8W、9W、10 W合金γ基体中<τ>的变化范围分别为176~186、150~165和115~131 MPa,γ'析出相中<τ>的变化范围分别为324~338、308~326、302~328 MPa。
图8
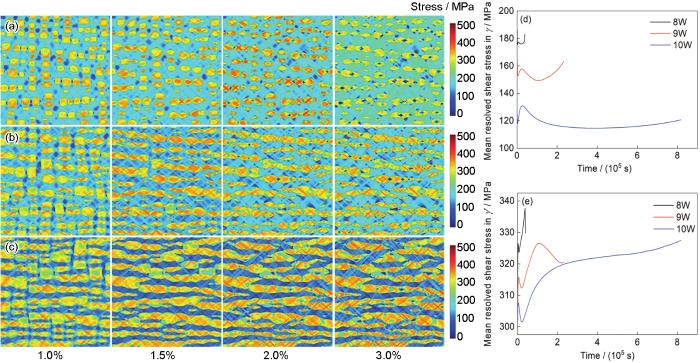
图8 蠕变过程中分切应力演化
Fig.8 Evolution of resolved shear stress during creep for alloy 8W (a), 9W (b) and 10W (c), and mean resolved shear stress in γ phase (d) and γ' phase (e)
图9为A2滑移系蠕变过程中受到的位错交互作用阻力的演化。显然,3种合金中由于位错交互作用产生的阻力在蠕变过程中的变化趋势是一致的。蠕变初期,由于水平γ通道位错先开动,该区域的位错交互阻力要高于竖直γ通道和γ'相内的阻力;随蠕变过程进行,水平通道阻力基本保持不变,而通道交接处以及竖直通道由于位错开动阻力逐渐升高,与此同时,γ'相由于剪切带来的位错交滑作用使其内部阻力也逐渐升高,但分布不均匀;蠕变后期,γ'相内大部分区域和γ基体的阻力值基本一致。在γ基体中的位错运动阻力随蠕变时间快速增加,之后趋于稳定,3种合金的稳态值均接近19 MPa (图9d)。在γ'相中的位错运动阻力随蠕变时间的变化与γ基体类似,但初期的增长速度要比后者慢(图9e),这是W含量高的合金中层错能较高导致的。相同蠕变时间下,8W合金中γ'相的位错运动阻力最大,9W合金次之,10W合金最小,但差别不大,其稳态值均在15~18 MPa范围内。
图9
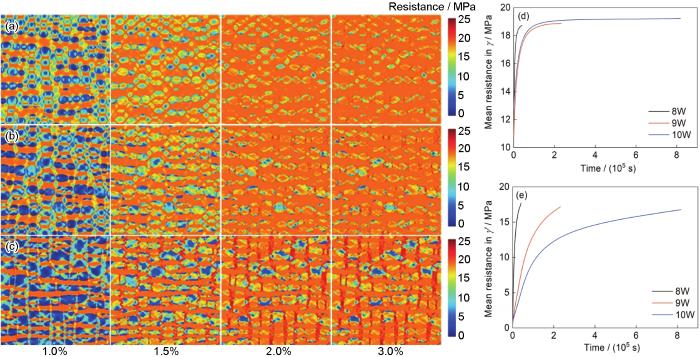
图9 蠕变过程中位错交互作用阻力演化
Fig.9 Evolution of resistance results from dislocation interaction for alloy 8W (a), 9W (b) and 10W (c), and mean resistance in γ phase (d) and γ' phase (e)
除了位错交互作用阻力,合金自身抗力r0即Orowan强化和析出相强化产生的位错运动阻力在该模型中通过γ和γ'两相中滑移系开动阈值体现,见表2。结合分切应力(图8)和位错交互作用阻力(图9),计算了γ和γ'两相中位错运动的平均驱动力,如图10。显然,随W含量增加,两相中位错运动的驱动力均降低。由于3种合金中开动的滑移系相同,故高W合金低的驱动力是造成其γ基体和γ'相中平均塑性变形小(图7)的主要原因。进一步发现,驱动力随W含量的变化(图10)与分切应力(图8d和e)随W含量的变化趋势基本一致,说明Co-Al-W三元合金中,W含量变化带来的分切应力变化是造成γ基体和γ'相中塑性变形不同的主要原因。
图10
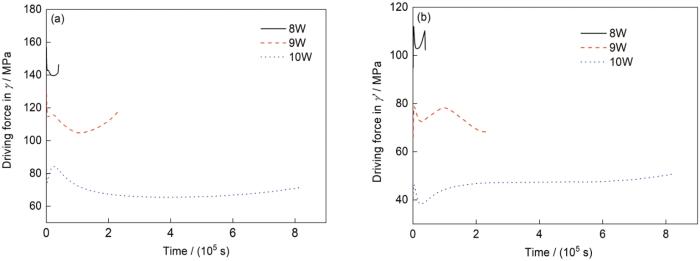
图10 γ基体和γ'相中位错运动的平均驱动力
Fig.10 Mean driving forces of dislocation activity in γ phase (a) and γ' phase (b)
分切应力由内应力和Schmid因子控制。由于3种合金蠕变过程中开动滑移系相同,故Schmid因子相同,因此内应力大小决定了分切应力值。图11a和b绘制了γ和γ'两相中平均内应力随蠕变时间的演化。显然,相同蠕变时间下,W含量高的合金γ和γ'两相中的平均内应力相对较高。而内应力是错配应力和外加应力共同作用的结果。对于[001]方向的外加应力,其施加后主要改变的是σ33应力,故进一步分析了3种合金施加-275 MPa压缩应力前后γ和γ'两相中平均σ33值,如图11c和d,图中正值代表拉应力,负值代表压应力。施加应力前,8W、9W、10W合金γ基体受拉应力,σ33随W含量增加而升高,其值分别为120、166和222 MPa,γ'相受压应力,σ33随W含量增加而降低,其值分别为-410、-355和-268 MPa。施加应力后,γ'相仍受压应力,其σ33分别为-850、-790和-740 MPa,而γ基体中的应力状态由拉应力变为压应力,其σ33分别为-410、-360和-270 MPa。显然,随W含量增加,施加应力后γ基体和γ'相中σ33的绝对值均降低。
图11
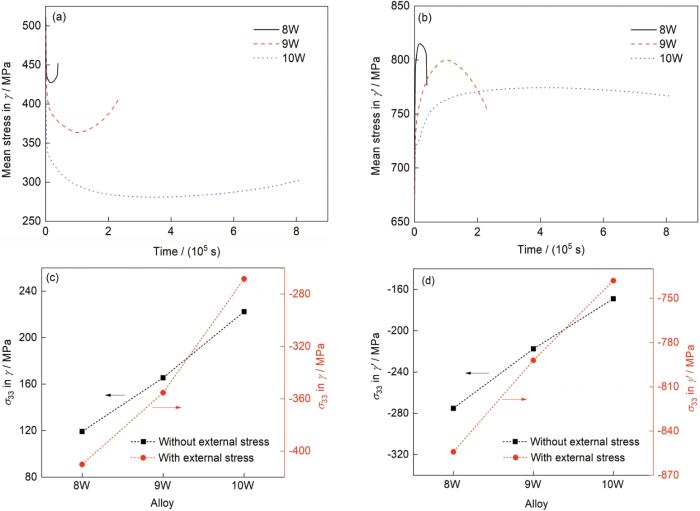
图11 γ和γ'两相中内应力和σ33的平均值演化
Fig.11 Evolution of mean internal stresses (a, b) and mean σ33 (c, d) in γ phase (a, c) and γ' phase (b, d)
由于γ相和γ'相均为fcc结构,故施加应力前的σ33值与合金的错配应力值相等。考虑到8W、9W、10W合金的弹性模量差别很小(表2),因此错配应力由错配应变决定。错配应变在一定程度上可通过γ和γ'相平衡成分与体系成分的差值Δci 反映。计算得到8W、9W、10W合金γ基体中成分差值Δ
3 结论
(1) 耦合CALPHAD和晶体塑性本构关系建立了用于蠕变过程模拟的Co-Al-W三元弹塑性相场模型,并考虑了蠕变损伤和γ'相剪切的影响,蠕变性能预测结果与实验结果偏差不大于17%。
(2) 蠕变应变达到3.0%时,8W合金未形成筏组织;9W和10W合金的筏化开始时间分别为37.5和22.5 ks,结束时间分别为150和45 ks。W含量升高致使筏化提前且加快。筏组织形成是9W和10W合金出现稳态蠕变阶段的主要原因。
(3) 8W、9W、10W合金蠕变应变达到3.0%时的时间分别为39.38、232.5、817.5 ks。8W、9W、10W的γ'相体积分数分别为31%、44%、56%,γ基体错配应力分别为120、166、222 MPa,这是高W合金具有更优蠕变性能的主要原因。
来源--金属学报