分享:Cr2AlC涂层相结构演变对力学性能的影响
袁江淮1,2, 王振玉2, 马冠水2, 周广学2, 程晓英1, 汪爱英,2
1
2
采用电弧复合磁控溅射技术在镍基高温合金基底表面沉积了Cr-Al-C涂层,通过后续热处理获得了高纯Cr2AlC MAX相涂层,研究了Cr2AlC涂层在1073、1123、1173和1223 K退火2 h后的微观结构演变及其对力学性能的影响。利用XRD、SEM和EDS表征了涂层的相结构、表面/截面形貌和元素分布,利用Vickers压痕仪和纳米压痕仪分析了涂层的硬度和韧性等力学性能。结果表明,随着退火温度的升高,Cr2AlC相逐步分解转变为Cr2Al、Cr7C3和Cr23C6相,元素间扩散作用逐渐增强,但相结构演变没有导致涂层/基底界面的失配,且涂层依然能够保持较高的硬度(超过11 GPa)和弹性模量(超过280 GPa)。由于脆性CrC x 相的形成和Al元素的扩散,高温退火后涂层的韧性有轻微下降。
关键词:
GH4169是一类含Nb和Mo等元素的沉淀硬化镍基高温合金,具有强度高、密度低以及优异的可加工性能、耐腐蚀和辐照性能,因而在航空发动机和燃气轮机(“两机”)领域拥有广泛的应用前景[1,2]。随着对大推力、高推重比性能要求的提高,“两机”的服役温度越来越高,并且叶片表面温度不均匀[3,4],单一的镍基高温合金已经不能满足“两机”的使用需求,所以通常需要在其表面涂覆铝化物涂层、MCrAlY涂层、热障涂层(如Y2O3稳定ZrO2涂层,YSZ)和Mn + 1AXn 相(其中,M为前过渡族元素,A为第Ⅲ或Ⅳ主族元素,X为C或者N元素,n = 1~3,简称MAX相,其空间群为P63/mmc)涂层等来提高其高温下的使用性能。其中,MAX相是一类具有热力学稳定性和hcp结构的层状高性能材料,其特殊的强M—X共价键/离子键和弱M—A金属键结构使其兼具有陶瓷优异的耐氧化、腐蚀和热稳定性能,又具有金属优异的电导率、热导率和可加工性能[5~7]。
Cr2AlC作为一种典型的三元MAX相层状材料,具有与镍基高温合金、YSZ、Al2O3等相匹配的热膨胀系数(Cr2AlC的热膨胀系数为12 × 10-6~13 × 10-6 K-1,镍基高温合金为15 × 10-6~16 × 10-6 K-1,YSZ为10 × 10-6~11 × 10-6 K-1,Al2O3为8.5 × 10-6 K-1)[8~10],可以作为黏结层来起到降低热应力、避免涂层开裂和剥落的作用,并且具有质轻、高温稳定性好、耐腐蚀和抗氧化等特性而在高温防护涂层领域拥有广泛的应用前景。Wang等[11]研究表明,Cr2AlC涂层在1173~1373 K高温环境下氧化40 h依然能够表现出优异的性能,这主要是因为表面Al2O3和(Cr, Al)2O3致密氧化物的生成。Shamsipoor等[12]通过放电等离子烧结的方法制备了高纯的Cr2AlC样品,研究了其在1223 K熔盐环境下的热腐蚀行为,结果表明,表面形成的致密且均匀富Cr的Al2O3层可以显著提升材料的抗热腐蚀能力。Li等[13]在1073~1573 K范围内研究了Cr2AlC在水、油和熔盐介质下的热冲击行为,由于Cr2AlC在高温下具有优异的自愈合性能,材料表现出优异的抗热震性能。由于Cr和Al元素的存在,Cr2AlC涂层具有优异的抗氧化性能,但根据Cr-Al-C体系的等温相图[14],在Cr2AlC成相区附近极易形成Cr7C3、Cr5Al8等二元相,相关系复杂,高温长时间保温会导致Cr2AlC相分解。据报道[15,16],MAX相块体材料在真空/Ar气环境下均拥有优异的热稳定性能。但Zhang等[17]在真空状态下将Cr-Al-C涂层在973 K退火3 h就探测到了Cr7C3相。Li等[9]采用电弧离子镀沉积Cr-Al-C涂层并在883~1273 K Ar气环境下退火1~20 h,结果表明,当温度超过973 K时涂层中Cr7C3相含量高于Cr2AlC相。这是因为MAX相涂层具有纳米级晶粒尺寸,晶界等元素快速扩散通道多,会显现出与块体材料不同的热学和力学性能[18],但关于MAX相涂层材料在高温下的相结构演变、热稳定性和力学性能的研究较为罕见。
本工作在镍基高温合金表面采用电弧复合磁控溅射镀膜装置结合后续真空退火热处理制备了高纯Cr2AlC涂层,研究了涂层在不同温度下长时间真空退火的相结构和力学性能的演变规律,并探究了涂层的表、截面形貌和退火过程中元素的扩散行为。通过研究Cr2AlC涂层的相结构演变和热稳定性可以分析其失效机理,对优化涂层的使用条件和寿命,拓宽其在高温下的应用具有重要的指导意义。
1 实验方法
沉积涂层前,将抛光后的GH4169基底(金刚石砂纸粗磨,抛光剂通过将0.25 μm的Cr2O3粉末与水混合制得)在CH3COCH3和C2H5OH中分别超声清洗0.5 h,并用导电胶将其粘在能够自转/公转的基架上。基底尺寸为直径11.9 mm、厚1.5 mm的圆片,其化学成分(质量分数,%)为:Cr 18.06,Fe 18.90,Nb 5.34,Mo 2.96,Al 0.58,Ti 0.94,Ni余量。
然后采用电弧复合磁控溅射镀膜设备(图1)在GH4169基底表面沉积Cr-Al-C涂层。靶材为纯度为99.9%的Cr靶和Al靶,为有效避免低熔点Al靶电弧放电产生大颗粒缺陷,获得结构均匀致密的涂层,此处电弧源为Cr靶,磁控源为Al靶。抽真空时将腔体加热至423 K以挥发腔体内的水蒸气,待腔体真空度低于4 × 10-3 Pa,通入5.5 × 10-10 m3/s的Ar气体并对基体施加-200 V的偏压,用离子束对基体刻蚀0.5 h以去除基体表面的杂质,提高膜基结合力;之后调整Ar气体和CH4气体流量为5.0 × 10-10和8.3 × 10-10 m3/s,Ti靶电流为70 A,偏压为-80 V,沉积TiC x 过渡层,时间为0.25 h。然后调整Ar气体和CH4气体流量为3.3 × 10-9和2.5 × 10-10 m3/s,Cr靶电流为60 A,Al靶功率为3.1 kW,偏压为-150 V,沉积Cr-Al-C涂层,时间为2.5 h。最后将沉积态的样品放置在OTF-1200X-80SL型管式炉中,抽真空至室温真空度为2.0 × 10-3 Pa,加热至973 K保温1.5 h得到Cr2AlC涂层,加热速率为600 K/h,随炉冷却,将制备样品标记为S0。
图1

图1 电弧复合磁控溅射设备示意图
Fig.1 Schematic of hybrid cathodic arc/magnetron device
为了探究涂层在高温下的相结构演变,将制备的Cr2AlC涂层样品在管式炉中(室温真空度为2.0 × 10-3 Pa)退火2 h,退火温度分别为1073、1123、1173和1223 K,将退火后的样品分别标记为S1~S4,加热速率为600 K/h,随炉冷却。
采用D8-Advance X射线衍射仪(XRD)测试高温退火后样品的相组成,使用CuKα 谱线(波长λ = 0.15406 nm),管电压和电流分别为40 kV和40 mA,步长0.02°,每步停留时间为0.2 s。之后借助配备有能谱仪(EDS)的Quanta 250 FEG扫描电子显微镜(SEM)观察样品的表面形貌、截面形貌和成分,工作电压为15 kV。采用MTS G200纳米压痕设备对S1~S4样品进行连续压入测试,压入深度为1000 nm,为减小测试误差,每个样品进行6次重复测试取平均值。借助MVS-1000 D1型Vickers压痕仪以2 N的力对涂层进行压痕测试以表征涂层的韧性,保载时间为10 s。进行力学测试前,用金刚石抛光剂对各个样品表面进行抛光以去除涂层表面的杂质和大颗粒,获得清晰的压痕,并可以减少压头与涂层之间的摩擦[19]。
2 实验结果与分析
2.1 涂层的相结构演变
图2和表1分别为制备的Cr2AlC (样品S0)涂层及其在不同温度下退火2 h后的XRD谱和相组成。由图2可知,制备的Cr2AlC涂层纯度较高,前期工作[11]借助Rietveld精修计算得到Cr2AlC相的质量分数为91%,只有少量的基底峰和中间相存在。将涂层在1073 K退火后(样品S1),此时Cr2AlC相(P63/mmc)仍为主相,但Cr2AlC在2θ为13.8°衍射峰的半高宽从0.135°减小至0.105°,42.1°衍射峰的半高宽从0.144°减小至0.117°。半高宽可以反映材料的结晶性,半高宽越小表明材料的结晶性越好[20],所以经1073 K处理后涂层结晶性有所提升。此时涂层中出现了Cr2Al (P4/mmm)和Cr7C3 (Pnma)相,说明在1073 K退火过程中,有少量Cr2AlC相发生分解。当温度上升到1123 K时(样品S2),Cr2AlC相的衍射峰消失,完全分解为Cr7C3相和Cr2Al相,其中Cr7C3相为主相。同时可以发现,涂层中出现了少量的NiAl相(Pm3m),这与之前的研究[8,21]一致,其原因是:来源于基底Ni元素的向上扩散与涂层中的Al元素发生反应。继续升高退火温度到1173 K (样品S3),发现立方结构的Cr23C6相(Fm3m)取代Cr7C3相成为主相,但Cr7C3也并未完全转化为Cr23C6;在此温度下Cr2Al相的衍射峰已经完全消失,涂层呈现出Cr23C6、Cr7C3和NiAl三相混合结构。进一步将退火温度提升到1223 K (样品S4),Cr7C3相完全转化为Cr23C6相,由于真空退火氛围中还含有少量的氧,退火后检测到涂层中含有少量Al2O3的衍射峰。加热温度在1123~1223 K之间时,NiAl相始终存在,温度的升高没有导致其晶体取向的变化。
图2
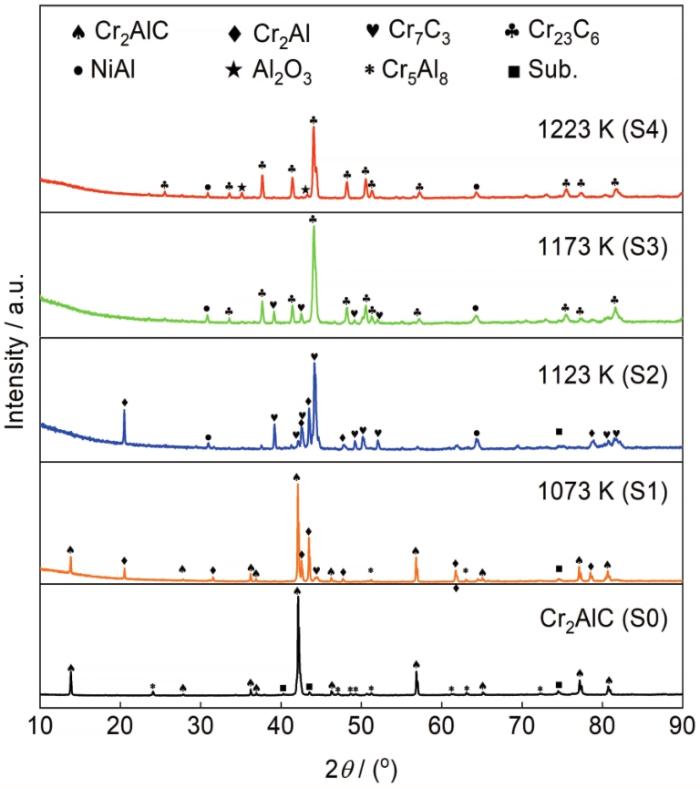
图2 Cr2AlC涂层及其在不同温度下退火2 h后的XRD谱
Fig.2 XRD spectra of the Cr2AlC coatings before and after annealing at different temperatures for 2 h
表1 Cr2AlC涂层及其在不同温度下退火后的相组成
Table 1
Sample | Annealing | Phase |
---|---|---|
temperature / K | ||
S0 | - | Cr2AlC |
S1 | 1073 | Cr2AlC, Cr2Al, Cr7C3 |
S2 | 1123 | Cr7C3, Cr2Al, NiAl |
S3 | 1173 | Cr23C6, Cr7C3, NiAl |
S4 | 1223 | Cr23C6, Al2O3, NiAl |
Debye温度源于原子热振动理论,是反映原子间结合力和评估相稳定性的一个重要物理量,Debye温度越高,晶体的化学键越强,材料的稳定性越高[22]。从表2[23~27]中Cr7C3与Cr23C6相的Debye温度计算结果可以看出,相较于Cr7C3,Cr23C6拥有较高的Debye温度,这也能够解释在高温下Cr7C3相向Cr23C6相的转变。Cr2O3和Al2O3的在1173 K的Gibbs形成能分别是-827.99和-1303.57 kJ/mol[11],并且Al元素的扩散系数更高,所以在涂层表面会优先生成Al2O3化合物。基于此,Cr2AlC涂层在高温下的相结构演变可以表示为:
表2 Cr7C3与Cr23C6的Debye温度和硬度对比[23~27]
Table 2
Phase | Debye temperature / K | Hardness / GPa | ||||
---|---|---|---|---|---|---|
Ref. | Ref. | Ref. | Ref. | Ref. | Ref. | |
[23] | [24] | [25] | [23] | [26] | [27] | |
Cr7C3 | 731 | 562 | 646 | 13.5 | 18.3 | 18.0 |
Cr23C6 | 744 | 674 | 691 | 10.1 | 13.2 | 16.5 |
2.2 涂层的表面形貌分析
图3为涂层在不同温度下退火后的表面形貌和元素分布图。如图3a所示,S1样品表面结构致密,可以观察到细小的锥状颗粒和少量大颗粒,无孔洞、裂纹等缺陷存在。与S1样品相比,S2样品的细小晶粒显著增大,并且可以观察到少量长条状的晶粒(图3b),这是典型的氧化物形貌[28]。S3样品中出现大量的长条状和较为细小的晶粒,并且大颗粒的边缘变得比较光滑(图3c),这与高温下熔化的Al向外扩散和氧化有关。对S2和S3样品而言,虽有氧化物存在,但氧化物的含量较少,这也是在XRD中未观察到氧化物峰的原因。S4样品表面也能观察到明显的氧化物晶粒,但值得注意的是表面出现大量的裂纹(图3d),这是因为在1223 K下涂层发生了较为严重的相结构转变,氧化和相结构转变引起涂层体积变化,脆性陶瓷相的生成造成了应力集中,但涂层在高温下由于Al元素的向外扩散,具有良好的自愈合效果,可以填充产生的裂纹。对S4样品进行EDS面扫描的结果(图3e~h)显示,涂层表面有Al和O元素的富集,其化学成分(原子分数,%)为:O 50.22,Al 35.52,Cr 5.54,C 8.72,其中Al/O原子分数比约为2∶3,涂层表面只检测到少量的Cr和C元素,可以证明在高温下表面有Al2O3生成,与XRD结果(图2)一致。涂层表面生成的致密Al2O3层,与Cr2AlC和CrC x 具有相匹配的热膨胀系数,可以提高涂层的耐腐蚀和高温氧化能力[10]。
图3

图3 S1~S4样品的表面形貌和S4样品的EDS元素面分布
Fig.3 SEM surface images of samples S1 (a), S2 (b), S3 (c), and S4 (d); and EDS elemental maps of Cr (e), Al (f), C (g), and O (h) in sample S4
2.3 涂层的截面形貌
图4为涂层在不同温度下退火后的截面形貌和EDS元素面分布图。可以看出,涂层的厚度约为7 μm,所有退火后的样品与基底依旧保持良好的结合力,无显微裂纹等缺陷的存在。过渡层两侧有Al和Ni元素的集聚,并且随着退火温度的升高,这种元素的集聚越来越明显,这主要是因为在高温下元素的扩散作用增强,涂层中的Al与基底的Ni元素能够发生反应,生成NiAl相,这与之前的研究[8,29]一致。除界面附近区域外,S1样品中Cr和Al元素均匀分布在整个涂层中,没有元素的偏析,过渡层基本上保持直线状态(图4a)。而S2和S3样品(图4b和c)中过渡层呈现为曲线,这是由于元素扩散不均匀引起的,并且可以发现Al元素在涂层界面处富集严重,这主要与Al元素具有较高的活度和热扩散系数有关,这与XRD (图2)中检测到NiAl相的结果一致。当退火温度为1173 K时(图4c),涂层中的Al开始在表面富集,说明高温下Al元素向外扩散作用增强;随着退火温度的升高,涂层表面Al元素越来越多,在退火温度为1223 K时(图4d),表面Al的厚度显著增加,这与XRD (图2)和SEM (图3)中探测到Al2O3相的结果一致。Cr2AlC涂层在高温下发生了复杂的相结构转变,相结构逐步从六方结构转变为四方结构、正交结构和立方结构,但Cr2AlC涂层中Cr7C3相的少量生成对其热膨胀系数基本上没有影响[30],所以在涂层/基底界面并未观察到裂纹的萌生和扩展,界面处仍能保持较好的匹配度,表明涂层在此温度段能够起到良好的保护作用,不会产生涂层剥落失效。
图4

图4 S1~S4样品的截面形貌和EDS元素面分布
Fig.4 Cross-sectional SEM images and corresponding EDS elemental maps of samples S1 (a), S2 (b), S3 (c), and S4 (d)
2.4 涂层的力学性能演变
Cr2AlC涂层高温下长时间退火后相结构的演变会引起其力学性能的变化,图5为不同温度下退火后涂层的载荷-位移曲线,表3为S1~S4样品硬度(H)、弹性模量(E)、H / E和H 3 / E 2的统计结果。硬度是表征材料抵抗塑性变形能力的物理量,而大的弹性模量则表示材料具有较大的刚度和抵抗弹性变形的能力[31]。从图5中可以看出,载荷-位移曲线均连续,没有出现明显的断开和突变,说明在压痕测试过程中涂层表面均能够保持平整,没有出现裂纹[32]。在相同压入深度下,S4样品具有最大的压入载荷(载荷最大为223 mN),并且S4样品的残余压入深度较小,说明其具有较强的抵抗外载荷的能力。从表3中可以明显地看出,不同退火温度下涂层的硬度和弹性模量都有先增加再减小然后再增加的趋势,S4样品的硬度和弹性模量取得最大值,分别为14.46和345.17 GPa。相较于S1样品(硬度为12.39 GPa,弹性模量为313.43 GPa),Cr2AlC相完全分解为Cr7C3和Cr2Al,Cr7C3为硬质相,所以S2样品(硬度为13.53 GPa,弹性模量为330.74 GPa)的硬度有所提升。S3样品(硬度为11.12 GPa,弹性模量为286.40 GPa)中主相由Cr7C3转化为C23C6,根据表2[23~27]中Cr7C3与Cr23C6的硬度数据可知,Cr7C3拥有更高的硬度,所以Cr7C3向Cr23C6的转变使试样硬度有所下降。此外,由于退火温度的升高,Cr7C3晶粒长大也是导致其硬度降低的一个因素[33]。通过XRD谱(图2)和表面形貌(图3d)的结果可以看出,S4样品中存在Al2O3相(其理论硬度超过20 GPa[34]),大于Cr7C3与Cr23C6的理论硬度,所以相较于S3样品硬度有显著提升。H / E可以定量评价材料的韧性,H 3 / E 2也可以表征材料抵抗塑性变形的能力[35,36],表3中不同温度退火处理涂层的H / E和H 3 / E 2与硬度变化具有相同趋势。S4样品具有最高的H / E (0.042)和H 3 / E 2 (0.026),前者表明涂层表面受到的载荷能够分散到更大的区域,涂层具有最好的抵抗弹性变形的能力;后者则表明涂层具有良好的抵抗裂纹形成和扩展的能力,及良好的耐磨性。Cr2AlC涂层在1073~1223 K范围内退火后,依然具有超过11 GPa的硬度和超过280 GPa的弹性模量,硬度远高于基底材料(4 GPa)和Gd2Zr2O7涂层(6.5 GPa[37]),表明涂层在较高温度下能够起到很好的抗冲蚀和抵抗变形的能力。
图5

图5 S1~S4样品的载荷-位移曲线
Fig.5 Load-displacement curves of samples S1-S4
表3 S1~S4样品硬度(H)、模量(E)、H / E和H 3 / E 2
Table 3
Sample | H / GPa | E / GPa | H / E | (H 3 / E 2) / GPa |
---|---|---|---|---|
S1 | 12.39 | 313.43 | 0.040 | 0.020 |
S2 | 13.53 | 330.74 | 0.042 | 0.024 |
S3 | 11.12 | 286.40 | 0.039 | 0.017 |
S4 | 14.46 | 345.17 | 0.042 | 0.026 |
为表征涂层的韧性,采用2 N的力对涂层进行Vickers压痕测试,压痕形貌如图6所示。由图可见,S1样品主相仍为Cr2AlC相,为典型的MAX相层状结构,韧性较好,压痕边缘为直线且无明显的裂纹(图6a)。S2~S4样品因为有脆性的CrC x 的生成,压痕外部出现明显的裂纹(图6b~d),表明其韧性有所下降。并且可以发现,S3和S4样品表面有大量的Kirkendall孔洞,这与Cr2AlC和DD5合金扩散偶在高温下的结构[21]一致,这是因为Al元素的向外扩散和生成C x O气体所致。涂层内部生成的Kirkendall孔洞,在高温下可能会成为腐蚀的通道,从而导致其耐腐蚀性能的下降。
图6

图6 S1~S4样品的Vickers压痕形貌
Fig.6 Vickers indentation morphologies of samples S1 (a), S2 (b), S3 (c), and S4 (d)
2.5 涂层相变机理
图7为涂层在不同温度下退火的结构演变过程示意图。对制备的Cr2AlC涂层进行高温退火,当退火温度增加到1073 K时,涂层先是转化为四方结构的Cr2Al相以及微量的Cr7C3相。随着退火温度继续升高,Cr2Al中间相转化为正交的Cr7C3相并伴随着硬度的提升和韧性的下降。继续升高温度,由于Cr23C6拥有更高的Debye温度和更低的形成能,所以其相较于Cr7C3相在高温下更能够稳定存在。当温度升高到1223 K,由于Al元素的扩散作用,在表层与退火炉中微量的O元素发生反应,生成了少量硬质的Al2O3相,使得涂层的硬度得到提升。
图7

图7 Cr2AlC涂层高温相结构演变对力学性能影响的示意图
Fig.7 Schematic of the effect of the phase-structure evolution on mechanical properties of Cr2AlC coating
3 结论
(1) Cr2AlC涂层在高温下发生从Cr2AlC相到Cr2Al相,再到Cr7C3相,最后到Cr23C6相的结构转变,但相结构的转变并没有导致涂层/基底界面的失配,在高温下依然能够保持优异的保护作用。
(2) 当加热温度超过1123 K时,由于基底Ni元素和涂层Al元素的扩散,在涂层/基底界面有NiAl相生成,并且随着加热温度的升高,Al元素的向外扩散作用愈发强烈,表层生成的致密Al2O3可以填充裂纹,提升涂层的耐氧化和高温腐蚀能力。
(3) Cr2AlC涂层经过高温长时间退火后的硬度和弹性模量依旧保持在较高的水平,但由于脆性CrC x 相的生成和Al元素的扩散,韧性相较于高纯Cr2AlC有轻微的下降,1223 K退火2 h后的样品由于表面生成的Al2O3保护层,涂层获得最高的硬度和弹性模量。
来源--金属学报