分享:冷喷涂辅助感应重熔合成AlCo x CrFeNiCu高熵合金涂层的显微组织和性能
冯力,1,2, 王贵平1, 马凯1, 杨伟杰1, 安国升1,2, 李文生1,2
1
2
通过冷喷涂辅助感应重熔技术在45钢基体成功制备AlCo x CrFeNiCu (x = 0、0.5、1.0、1.5、2.0,摩尔分数)高熵合金涂层。研究了Co元素含量对冷喷涂辅助合成高熵合金涂层物相、微观组织的影响。结果表明:通过低压冷喷涂辅助感应重熔技术合成的AlCo x CrFeNiCu高熵合金涂层由fcc + bcc双相混合结构组成,涂层组织为等轴树枝晶+晶间组织,其中枝晶为bcc结构,晶间组织为fcc结构。Co含量的变化会引起AlCo x CrFeNiCu高熵合金涂层的晶格畸变状态发生变化,当x = 1.0时,AlCo1CrFeNiCu高熵合金涂层的晶格应变最大。Co元素含量增加会促进AlCo x CrFeNiCu高熵合金涂层中的枝晶数目增加,同时涂层中的树枝晶尺寸也随着Co元素含量增加而增大。涂层中的树枝晶富集Fe、Cr、Co、Ni元素,枝晶间富集Cu元素,Al均匀地分布在整个涂层中。随着Co含量增加,AlCo x CrFeNiCu高熵合金涂层的硬度先增加后减小;当x = 1.0时,AlCo1CrFeNiCu高熵合金涂层的硬度达到562.5 HV,此时涂层的摩擦系数最小,为0.352。
关键词:
2004年初,Yeh等[1~3]提出了高熵合金的概念用来指导制备新型合金材料。高熵合金的晶体结构一般为简单的bcc结构或fcc结构,具有混合熵高、机械性能好等特点,有非常好的应用前景[4~6]。利用表面涂敷技术制备高熵合金耐磨、耐腐蚀涂层,推进了高熵合金的工业应用[7]。
目前,制备高熵合金涂层的方法有激光熔覆技术、磁控溅射技术、等离子喷涂技术、电火花沉积技术等[8~15]。郝文俊等[16]采用激光熔覆技术在45号钢表面制备CoCrFeNiSi x (x = 0、0.5、1.0、1.5、2.0,摩尔分数,下同)高熵合金涂层,Si的添加可以提高熔覆层表面成型的能力,随着Si含量的增加,涂层的组织结构由fcc向bcc转变,涂层中的组织以等轴晶和树枝晶为主,当x = 2.0时,高熵合金涂层的硬度最大为600 HV左右。张冲等[17]通过激光熔覆法制备FeCrNiCoMnB x 高熵合金涂层,研究了B含量对FeCrNiCoMnB x 高熵合金涂层的结构、硬度和耐磨性的影响,结果表明,B含量对涂层中硼化物相的生成以及组织结构有直接影响,涂层的硬度和耐磨性随着B含量的增大而增加。Liu等[18]采用等离子喷涂技术制备CoCrFeNiNb x 高熵合金涂层,研究了Nb元素对合金涂层结构和拉伸性能的影响,结果显示,Nb元素的加入使合金涂层的微观结构由fcc转变为fcc + hcp,并且随着Nb含量的增加合金涂层的屈服强度和断裂强度增加。黄元盛等[19]采用磁控溅射法在玻璃和单晶Si片基体上制备了AlCoCrFeCu0.5Ni高熵合金氧化物薄膜,结果表明,氧化物薄膜的折射系数随着O含量的增加而减小;经过退火处理后,氧化物薄膜厚度减小,并且颜色加深。Hung等[20]通过电火花沉积技术制备Co x CrFeNiTi0.3 (x = 1.0、0.8、0.6)高熵合金涂层,研究了Co元素含量对合金组织和力学性能的影响,结果表明,Co x CrFeNiTi0.3高熵合金涂层由简单的fcc相和η + σ相组成,随着Co含量增加,涂层的硬度从366 HV增加到436 HV,屈服应力从522 MPa增加到667 MPa,抗压强度和断裂应变分别从1290 MPa、0.56下降到955 MPa、0.24。上述研究表明,改变高熵合金中某种元素的含量,会导致高熵合金组织结构发生变化,从而影响合金的力学性能与使用性能。研究高熵合金中的元素含量对其性能的影响规律,有助于更好地推广应用高熵合金。
本工作采用目前报道较少的冷喷涂辅助感应重熔技术[21]制备AlCo x CrFeNiCu (x = 0、0.5、1.0、1.5、2.0)高熵合金涂层,研究了Co元素含量对低压冷喷涂辅助感应重熔合成AlCo x CrFeNiCu高熵合金涂层微观组织与性能的影响规律。
1 实验方法
1.1 涂层的制备
本实验所用原料Al、Co、Cr、Fe、Ni和Cu (纯度> 99.5%)为商用金属单质粉末,将金属单质粉末机械混合4 h后作为冷喷涂预制原料,实验中的基体材料为45钢,其化学成分(质量分数,%)为:C 0.42~0.50,Si 0.17~0.37,Mn 0.50~0.80,Cr ≤ 0.25,Fe余量。在喷涂之前用丙酮超声清洗基体表面的油污等杂质,然后用喷砂粗化处理基体表面。将金属单质粉末按照AlCo x CrFeNiCu (x = 0、0.5、1.0、1.5、2.0)实验设计的摩尔比机械混合。冷喷涂过程中各种粉末的上粉率不同,造成喷涂原料中各元素含量与涂层中设计的元素含量不同。
采用GDU-3-15低压冷喷涂设备在45钢基体上预制混合金属涂层,工艺参数为温度490~510℃,大气压0.7~0.8 MPa,喷涂距离10~20 mm,喷嘴移动速率0.4~0.6 m/s。对冷喷涂预制的混合金属涂层进行感应重熔合成高熵合金涂层。感应重熔加热功率选用1.5~2.2 kW,加热时间为10~15 s,加热温度为490~510℃。表1列出了感应重熔合成高熵合金涂层各元素的含量。
表1 感应重熔合成高熵合金涂层各元素的含量 (mass fraction / %)
Table 1
Coating | Al | Co | Cr | Fe | Ni | Cu |
---|---|---|---|---|---|---|
AlCrFeNiCu | 10.9 | 0 | 14.6 | 25.3 | 20.5 | 28.7 |
AlCo0.5CrFeNiCu | 10.3 | 8.7 | 11.8 | 24.6 | 18.7 | 25.9 |
AlCo1CrFeNiCu | 9.0 | 15.8 | 9.5 | 22.3 | 18.9 | 24.5 |
AlCo1.5CrFeNiCu | 8.6 | 25.2 | 9.2 | 20.9 | 14.7 | 21.4 |
AlCo2CrFeNiCu | 6.5 | 31.7 | 10.0 | 18.2 | 13.5 | 20.1 |
1.2 涂层性能表征
采用D/MAX 2500PC型X射线衍射仪(XRD)对涂层进行物相检测,选用Cu靶(波长0.1542 nm),扫描速率10°/min,扫描范围10°~90°,加速电压40 kV,管电流30 mA。使用王水对抛光的AlCo x CrFeNiCu高熵合金涂层试样进行腐蚀,然后观察微观组织。采用Quanta FEG450场发射扫描电子显微镜(SEM)及其附带的能谱仪(EDS)对冷喷涂预制合金粉体和高熵合金涂层表面、截面微观形貌及微区成分进行观察和分析。采用Talos F200S透射电子显微镜(TEM)观察高熵合金涂层表面的微观组织结构,首先将样品制成直径3 mm、厚度50 μm的圆形薄片,然后使用精密离子减薄仪进行减薄。减薄完成后,在200 kV电压条件下,对样品进行观察分析。采用WilsonHV-1102型显微硬度计测量试样的Vickers硬度,选取载荷0.5 N,保持时间10 s,在试样表面选取5个点测量,然后求其平均值。
采用UMT-Tribolab型往复式摩擦试验仪,以直径为6 mm的Al2O3小球作为对磨件,在室温干滑动条件下测试合金涂层的摩擦性能,实验前将涂层和对磨件小球用酒精擦拭干净。摩擦方式为往复式,加载载荷为7.5 N,摩擦行程为3 mm,频率为3 Hz,摩擦时间为20 min。涂层的磨损率可以用以下公式计算[22]:
式中,V为磨损体积(mm3),σ为磨损率(mm3/(N·m)),A为磨损痕横截面积(mm2),L为磨损痕长度(mm),W为累积摩擦功(N·m),F为施加的载荷力(N),f为滑动频率(Hz),T为摩擦时间(min)。
2 实验结果与分析
2.1 微观组织
图1是低压冷喷涂AlCo x CrFeNiCu预制混合金属涂层横截面微观形貌的SEM像。可以看出,冷喷涂涂层与基体存在不平整的结合面。涂层组织比较致密,孔隙小且分散,通过Image-Pro-Plus 6.0软件测得5种涂层的孔隙率分别为0.42%、0.15%、0.072%、0.31%和0.35%。从横截面的形貌可以看出,基体与涂层之间通过机械咬合的方式结合在一起,并且结合的界面存在明显不平整。在冷喷涂涂层中,涂层的孔隙率、各粒子之间的结合强度等共同影响着涂层的性能。
图1
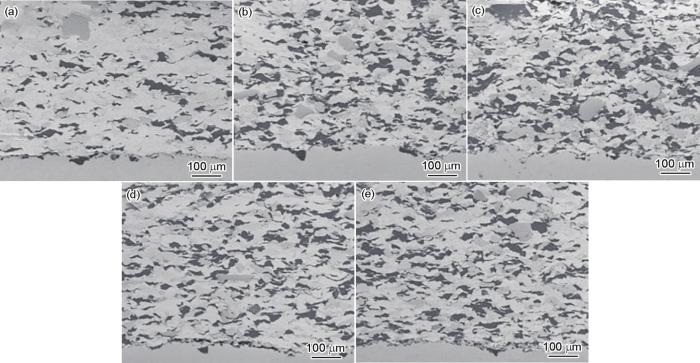
图1 冷喷涂AlCo x CrFeNiCu预制合金粉体涂层横截面形貌的SEM像
Fig.1 Cross sectional SEM images of cold spray AlCo x CrFeNiCu prefabricated alloy powder coatings
(a) x = 0 (b) x = 0.5 (c) x = 1.0 (d) x = 1.5 (e) x = 2.0
图2是感应重熔合成AlCo x CrFeNiCu高熵合金涂层的XRD谱。可以看出,涂层由简单的fcc和bcc双相混合结构组成,并没有出现复杂的物相。这是因为高熵合金的高熵效应增强了各组元的相容性,并显著降低了系统的自由能,元素的偏析趋势降低。当系统的混合熵大于形成金属间化合物的熵变时,可抑制金属间化合物的出现,从而促进元素间混合形成简单的固溶体结构。当x = 0时,AlCrFeNiCu高熵合金涂层中fcc相的衍射峰很强,bcc相衍射峰很弱。随着Co含量的增加,在x = 0.5时,bcc相的衍射峰开始增强。当x = 1.0时,bcc相和fcc相的衍射峰达到相同的高度。随着Co含量的增加,bcc相的衍射峰强度持续增强,fcc相的衍射峰强度在持续减弱。bcc相的衍射峰强度开始高于fcc相衍射峰的强度。这说明,随着Co元素含量增加,涂层组织中的bcc结构组织也在增加。表2中列出了不同Co含量涂层中fcc结构和bcc结构的晶格常数,表明Co含量的变化会引起高熵合金涂层晶格畸变状态的变化。
图2
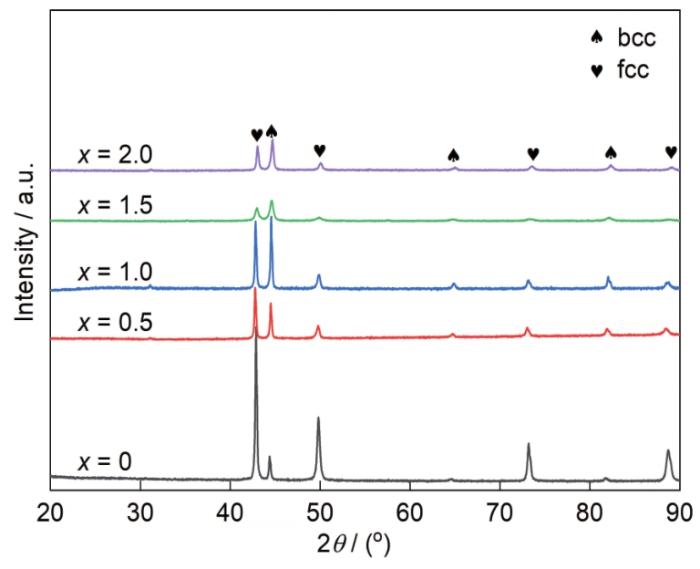
图2 感应重熔AlCo x CrFeNiCu高熵合金涂层的XRD谱
Fig.2 XRD spectra of induction remelting of AlCo x -CrFeNiCu high-entropy alloy coatings
表2 AlCo x CrFeNiCu高熵合金涂层各相的晶格常数 (nm)
Table 2
Coating | fcc phase | bcc phase |
---|---|---|
AlCrFeNiCu | 0.3654 | 0.2873 |
AlCo0.5CrFeNiCu | 0.3661 | 0.2878 |
AlCo1CrFeNiCu | 0.3668 | 0.2884 |
AlCo1.5CrFeNiCu | 0.3650 | 0.2873 |
AlCo2CrFeNiCu | 0.3641 | 0.2866 |
图3是冷喷涂辅助感应重熔合成AlCo x CrFeNiCu高熵合金涂层组织形貌的SEM像。可以看出,高熵合金组织由枝晶(DR)和枝晶间(ID)组成。随着Co含量的增加,灰色的枝晶数目明显增加。当x = 0时,如图3a1和a2所示,形成的枝晶数目较少且晶粒尺寸较小,枝晶的平均尺寸为0.27 μm,枝晶组织面积分数为41%。当x = 0.5时,如图3b1和b2所示,晶粒数目明显增多,晶粒粗化,枝晶的平均尺寸为0.83 μm,枝晶组织面积分数为48%。当x = 1.0时,如图3c1和c2所示,枝晶数目较多,晶界清晰,并且晶粒明显粗化,枝晶的平均尺寸为1.89 μm,枝晶组织面积分数为63%。当x = 1.5时,如图3d1和d2所示,组织分布较均匀,晶界较清晰,晶粒尺寸变得更大,枝晶的平均尺寸为2.21 μm,枝晶组织面积分数为72%。当x = 2.0时,如图3e1和e2所示,组织结构致密,晶粒尺寸进一步增大,枝晶的平均尺寸为2.69 μm,枝晶组织面积分数为84%。从图3可以看出,随着Co含量的增加,涂层组织中枝晶组织面积占比明显增加,晶粒尺寸越来越大。采用TEM对AlCo1CrFeNiCu高熵合金涂层进行显微组织观察,如图4所示。从图4a和b中可以看出,涂层结构由DR和ID结构组成。图4c和d分别为DR和ID的选区电子衍射(SAED)花样。结果表明,AlCo1CrFeNiCu高熵合金涂层组织中DR选区为bcc结构,ID选区为fcc结构。
图3
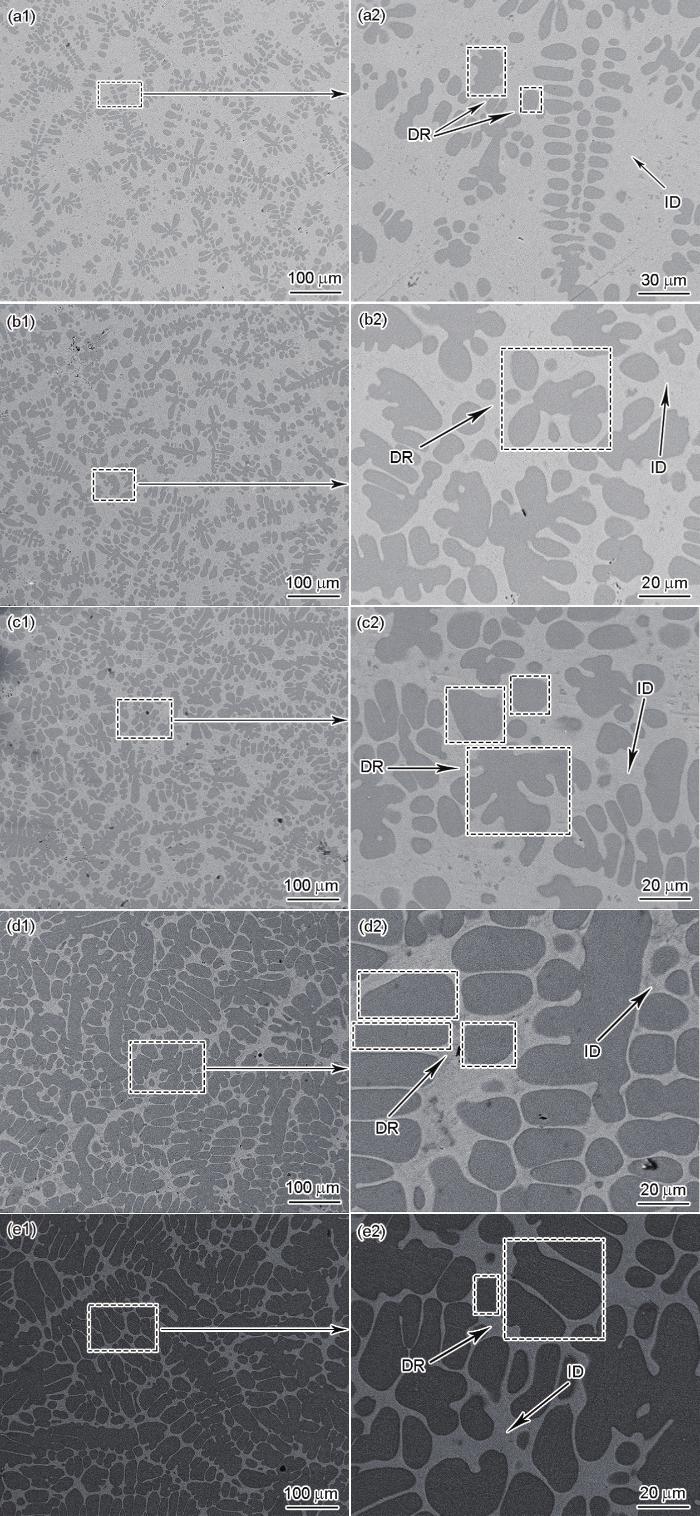
图3 感应重熔AlCo x CrFeNiCu高熵合金表面形貌的SEM像
Fig.3 Low (a1-e1) and locally high (a2-e2) magnified SEM images of surface morphologies of induction remelting AlCo x CrFeNiCu high-entropy alloy (DR—dendrite, ID—interdendritic structure) (a1, a2) x = 0 (b1, b2) x = 0.5 (c1, c2) x = 1.0 (d1, d2) x = 1.5 (e1, e2) x = 2.0
图4
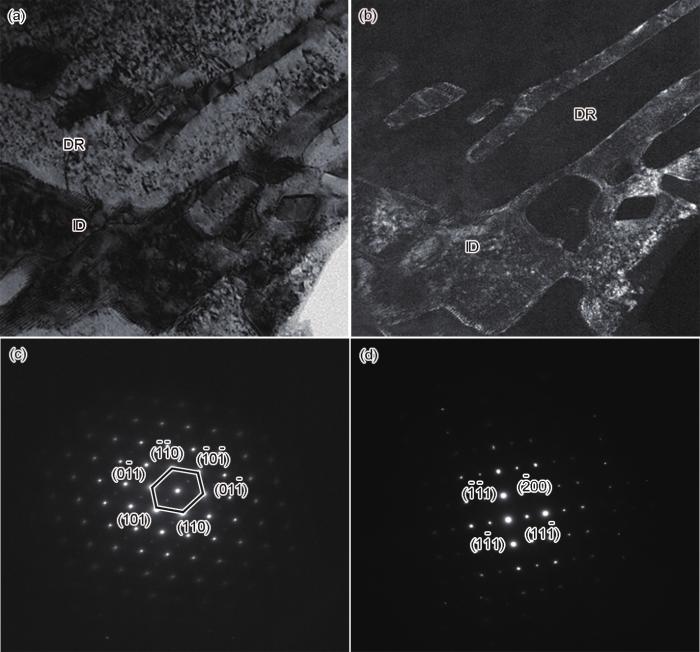
图4 AlCo1CrFeNiCu高熵合金涂层的TEM分析
Fig.4 TEM analyses of AlCo1CrFeNiCu high-entropy alloy coating (a, b) bright field TEM images of coating (c) SAED pattern of DR (d) SAED pattern of ID
图5a为感应重熔合成AlCo1CrFeNiCu高熵合金涂层截面的SEM像。可以看出,涂层与基体结合较好,涂层与基体间有一条亮白色的冶金结合带。图5b为涂层表面组织形貌SEM像及其面扫描EDS。可以看出,AlCo1CrFeNiCu高熵合金涂层的枝晶间区域主要富集Cu元素,枝晶区域富集Fe、Co、Cr和Ni元素,而Al元素均匀分布在整个涂层当中。这是因为Cu元素与Fe、Co、Cr、Ni元素之间的混合熵较大,为正值,不易与这些元素形成稳定的固溶体。凝固过程中Fe、Co、Cr、Ni和Al元素因混合熵较小而容易形成稳定固溶体,因此先形成以Fe、Co、Cr、Ni和Al元素为主的枝晶状组织。低熔点的Cu与Al在枝晶间形成固溶体组织。当x = 0、0.5、1.5、2.0时,涂层表面的面扫描EDS与x = 1.0时的特征类似,在文中不做赘述。
图5
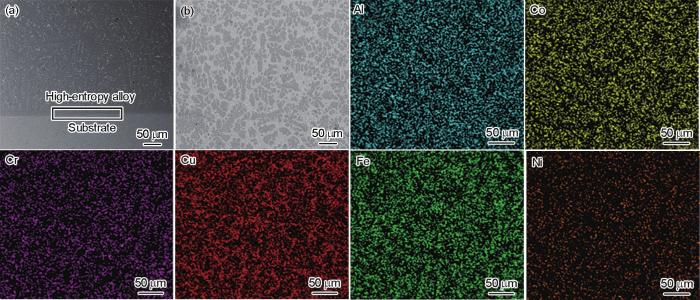
图5 感应重熔AlCo1CrFeNiCu高熵合金涂层截面SEM像、表面SEM像和EDS
Fig.5 Cross sectional SEM image (a), surface SEM image and corresponding EDS (b) of induction remelting AlCo1CrFeNiCu high-entropy alloy coating
Color online
根据Hume-Rothery准则[23],通过表2中AlCo x CrFeNiCu高熵合金涂层中的晶格常数计算涂层组织的晶格应变(ε)。
式中,a和a0分别为实际晶格点阵和理想晶格点阵的点阵常数。计算结果如图6所示。当x = 1.0时,原子尺寸差异(δ)最大,AlCo1CrFeNiCu高熵合金涂层的晶格应变最大。从晶体学角度讲,fcc结构属于最密堆积,原子排列紧密,致密度为74%,而bcc结构则相对较为松散,致密度为68%[24],bcc结构更容易发生变形以释放晶格畸变能[25]。这导致了AlCo x CrFeNiCu高熵合金涂层中,bcc结构的晶格应变总体小于fcc结构。
图6
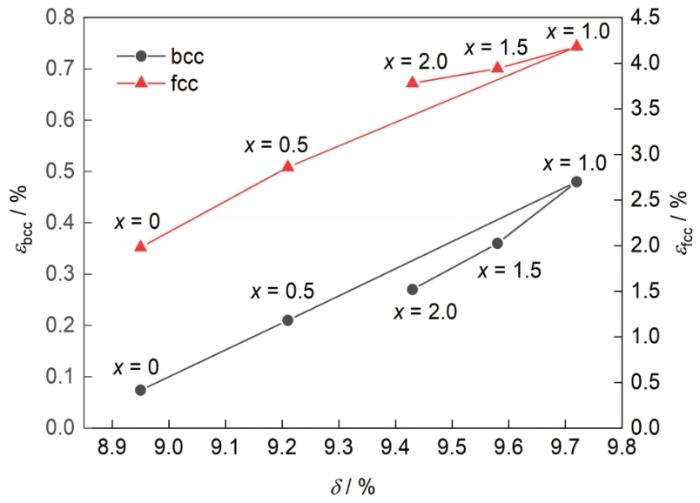
图6 AlCo x CrFeNiCu高熵合金涂层中fcc和bcc相晶格应变(εfcc和εbcc)随原子尺寸差异(δ)的变化
Fig.6 Lattice strains of fcc and bcc phases (εfcc and εbcc) in AlCo x CrFeNiCu high-entropy alloy coating varies with atomic size difference (δ)
2.2 涂层性能分析
图7a为感应重熔合成AlCo x CrFeNiCu高熵合金涂层的显微硬度。随着Co含量的增加,AlCo x -CrFeNiCu高熵合金涂层的硬度先增大后减小,当x = 1.0时,涂层的硬度达到562.5 HV,约为基体45钢的3倍。结合图2和3,AlCo x CrFeNiCu高熵合金涂层的微观组织是由fcc结构和bcc结构的固溶体结构组成。当x = 1.0时,涂层中fcc结构和bcc结构的晶格应变最大,此时晶格畸变能最高,导致此时涂层硬度最高。一般而言,硬度与耐磨性呈正相关,硬度越高耐磨性就越好[26]。图7b为冷喷涂辅助感应重熔AlCo x CrFeNiCu高熵合金涂层和45钢基体的摩擦系数曲线。根据图中的曲线计算,AlCo x CrFeNiCu涂层与对磨件Al2O3小球的摩擦系数在0.352~0.540之间,而45钢与对磨件Al2O3小球的摩擦系数为0.690,当x = 1.0时,感应重熔合成AlCo1CrFeNiCu高熵合金涂层的摩擦系数最小,为0.352。
图7

图7 AlCo x CrFeNiCu高熵合金涂层和45钢基体的硬度和摩擦系数
Fig.7 Hardnesses (a) and friction coefficients (b) of AlCo x CrFeNiCu high-entropy alloy coatings and 45 steel substrate
Color online
图8为AlCo x CrFeNiCu高熵合金涂层平均磨损率和摩擦系数。可以看出,涂层的摩擦系数和磨损率有着相同的变化规律。随着Co含量的增加,涂层的摩擦系数和磨损率先下降后上升。当x = 1.0时,AlCo1CrFeNiCu高熵合金涂层的磨损率为4.19 × 10-5 mm3/(N·m),与其他4种AlCo x CrFeNiCu (x = 0、0.5、1.5、2.0)高熵合金涂层相比,磨损率分别降低52%、44%、31%和33%。AlCo1CrFeNiCu高熵合金涂层表现出良好的耐磨性。
图8
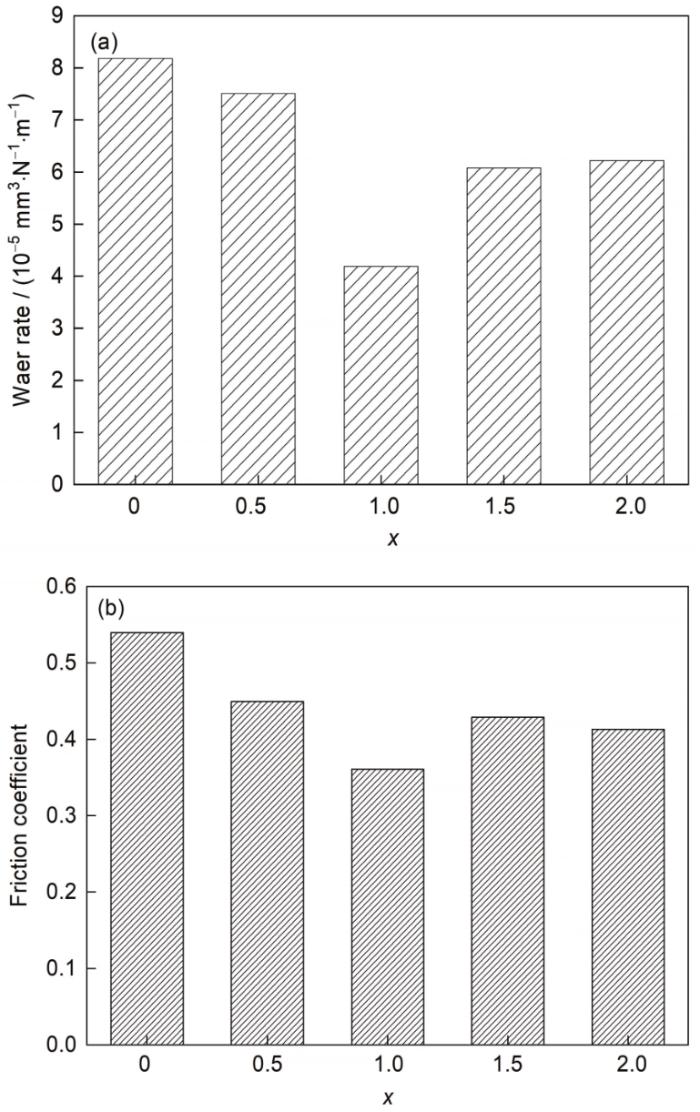
图8 AlCo x CrFeNiCu高熵合金涂层的平均磨损率和摩擦系数
Fig.8 Average wear rates (a) and friction coefficients (b) of AlCo x CrFeNiCu high-entropy alloy coatings
图9为AlCo x CrFeNiCu高熵合金涂层表面磨损形貌的SEM像。如图9a1和b1所示,x = 0和x = 0.5时涂层的磨损表面非常粗糙,沿着磨损滑动方向清楚地看到一些长而窄的犁沟,图中明显存在着具有白色边缘的脱黏坑。从图9a2和b2可以看出,涂层的磨损表面存在大量片状分层,这表明当x = 0和x = 0.5时,涂层在磨损过程中经历了分层断裂。涂层的磨损机制主要为黏着磨损、分层磨损和磨粒磨损。如图9c1所示,当x = 1.0时,涂层的磨损表面变得光滑,黏着层和脱黏坑变少,犁沟也逐渐变浅,磨粒磨损与分层磨损逐渐减少。当Co含量继续增加时,如图9d1和e1所示,涂层表面黏着坑增多,并且分层严重,犁沟也明显加深。从图9d2和e2可以清楚地看到上述现象,说明涂层磨损加剧。
图9

图9 AlCo x CrFeNiCu高熵合金涂层磨损形貌的SEM像
Fig.9 Low (a1-e1) and high (a2-e2) magmfied SEM images showing wear morphologies of AlCo x CrFeNiCu high-entropy alloy coatings (a1, a2) x = 0 (b1, b2) x = 0.5 (c1, c2) x = 1.0 (d1, d2) x = 1.5 (e1, e2) x = 2.0
3 结论
(1) 冷喷涂辅助感应重熔AlCo x CrFeNiCu高熵合金涂层显微结构为等轴树枝晶+晶间组织,其中枝晶为bcc结构,晶间组织为fcc结构。Co元素含量增加会促进AlCo x CrFeNiCu高熵合金涂层中的枝晶数目增加,同时涂层中的树枝晶尺寸也随着Co元素含量增加而增加。涂层中枝晶间组织富集Cu元素,枝晶组织内富集Fe、Cr、Co和Ni元素,Al元素均匀分布在整个涂层中。
(2) Co元素含量的变化会引起AlCo x CrFeNiCu高熵合金涂层的晶格畸变状态发生变化,随Co含量增加,涂层显微硬度先增加后减小,当x = 1.0时,AlCo1CrFeNiCu高熵合金涂层的晶格应变最大,涂层硬度达到562.5 HV。
(3) 随着Co元素含量的增加,AlCo x CrFeNiCu高熵合金涂层与Al2O3小球对磨件的摩擦系数范围在0.352~0.540之间;当x = 1.0时,合金涂层与Al2O3小球对磨件的摩擦系数最小,为0.352,涂层磨损率为4.19 × 10-5 mm3/(N·m),此时涂层的耐磨性能最好。
来源---金属学报