分享:奥氏体化温度对Si-Mn钢热轧板淬火-配分处理后显微组织和力学性能的影响
程远遥1,2, 赵刚1,2, 许德明,1,2, 毛新平3, 李光强1,2
通过分析不同奥氏体化温度下热轧板制备的淬火-配分(Q&P)钢的显微组织和力学性能,探讨了奥氏体化温度对其显微组织与力学性能的影响。结果表明,热轧板制备Q&P Si-Mn钢中的铁素体呈带状和块状2种形貌,铁素体形貌会影响相邻区域残余奥氏体形貌,其中带状铁素体相邻区域残余奥氏体以薄带状为主,块状铁素体相邻区域残余奥氏体以块状为主。随着奥氏体化温度的升高,铁素体和残余奥氏体体积分数下降,对应的Q&P Si-Mn钢屈服强度、抗拉强度逐渐升高,延伸率及强塑积均逐渐下降。在810℃奥氏体化后,热轧板制备的Q&P Si-Mn钢强塑积达到28.36 GPa·%,相较于工业生产采用冷轧板制备的980 MPa级Q&P Si-Mn钢,强塑积提高了约36%。热轧板制备Q&P Si-Mn钢具有更高的强塑积与其组织中不同形貌铁素体能调控相邻区域残余奥氏体形貌及稳定性相关。
关键词:
淬火-配分(quenching and partitioning,Q&P)钢是Speer等[1,2]提出的利用较廉价的Si-Mn低合金钢结合Q&P工艺开发的具有高强度和较高塑性的第三代先进汽车用钢。目前其工业生产通常采用传统热轧+冷轧工艺制备板坯后进行Q&P处理[3],整个工艺流程长、工序复杂、能耗高,不符合汽车用钢铁材料绿色低成本制造的发展趋势。随着钢铁制造业技术的发展,制备质量合格的薄规格热轧板代替冷轧板成为一种趋势,例如目前采用薄板坯连铸连轧(thin slab casting and rolling,TSCR)技术能制备出性能优异的薄规格热轧板,相关热轧产品已部分代替冷轧产品实现工业化应用[4,5]。采用薄规格热轧板替代冷轧板作为生产Q&P钢的坯料省掉了复杂的冷轧工序,大幅度缩短制造流程、降低制造成本,因而具有极好的应用前景。
Q&P钢的热处理工艺包括奥氏体化、一次淬火(淬火至马氏体转变起始温度(Ms)和马氏体转变终了温度(Mf)之间)、配分、二次淬火至室温等工序。目前大多数研究采用的Q&P钢坯料通常通过对实验室熔炼的钢锭进行热轧+冷轧处理进行制备,相关研究集中在化学成分[6,7]、奥氏体化温度[8~10]、淬火温度[11,12]或配分工艺[13,14]等因素对Q&P钢C配分、残余奥氏体稳定性及最终力学性能的影响,较少涉及到板坯轧制工艺对Q&P钢组织和力学性能的影响。事实上,有大量研究表明Q&P处理前板坯的初始组织会对Q&P钢的组织控制和力学性能产生重要影响。Zhang等[15]研究表明在奥氏体化前进行预淬火处理能提高Q&P钢残余奥氏体稳定性和加工硬化率。Ding等[16]通过对板坯进行奥氏体化、淬火、回火及冷轧处理获得回火形变马氏体组织,随后进行Q&P处理制备出超细晶(UFG) Q&P钢,相较于粗晶(CG) Q&P钢(未经过淬火和回火工序),UFG-Q&P钢具有更多的残余奥氏体和更高的抗拉强度。任勇强等[17]对比了不同前躯体组织下制备的Q&P钢的力学性能,发现采用马氏体作为前躯体组织制备的Q&P钢强塑积要高于前躯体组织为贝氏体+铁素体制备的Q&P钢。热轧板和冷轧板轧制工艺的差异会改变板坯的初始组织,从而影响Q&P钢热处理过程中的组织演变。例如,相较于冷轧板,热轧板存储能较小,这会导致热轧板在奥氏体化阶段铁素体再结晶和奥氏体相变行为与冷轧板存在着显著差异[18],这会对Q&P钢组织和最终力学性能产生影响。但目前基于热轧板初始组织下Q&P钢组织调控规律的相关研究较少涉及,Q&P热处理工艺对热轧板制备的Q&P钢组织和力学性能的影响规律尚不清晰。因此,本工作以Si-Mn钢热轧板为研究对象,深入分析奥氏体化温度对热轧板制备的Q&P钢组织和力学性能的影响规律,为采用热轧板制备性能优异的Q&P Si-Mn钢提供理论和实验依据。
1 实验方法
实验用钢采用商用2 mm厚Si-Mn钢热轧板,其主要化学成分(质量分数,%)为:C 0.2~0.3,Si 1.6~1.8,Mn 1.9~2.5,Fe余量。通过热膨胀法测定Si-Mn钢在近平衡状态下加热时先共析铁素体全部转化为奥氏体的终了温度(Ac3)、加热时珠光体向奥氏体转变的开始温度(Ac1)、Ms和Mf分别为900、662、358和213℃。根据各相变温度制定的热处理工艺如图1所示。奥氏体化处理在箱式电阻炉中进行,淬火和配分实验在盐浴炉中进行,盐浴炉的内径为190 mm、高300 mm。根据盐浴炉尺寸,在商用2 mm厚Si-Mn钢热轧板上随机切取5块100 mm × 150 mm的试样,然后分别加热到810、840、870、910和950℃保温180 s,之后在盐浴炉中淬火至260℃,随后在400℃的盐浴炉中保温50 s进行配分处理,最后水淬至室温。
图1
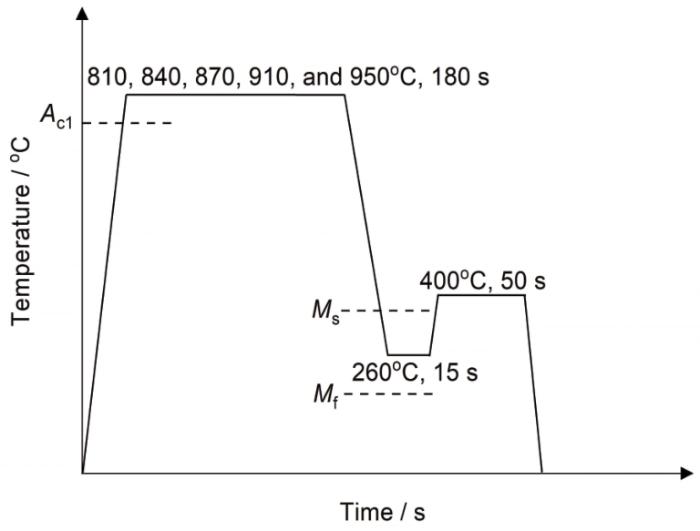
图1 淬火-配分(Q&P) Si-Mn钢热处理工艺流程图
Fig.1 Schematic of quenching and partitioning (Q&P) Si-Mn steel heat treatments (Ac1—start temperature of pearlite transformed to austenite, Ms—initial temperature of martensite transformation, Mf—finish temperature of martensite transformation)
采用线切割机将原热轧板及不同Q&P Si-Mn钢试样切成尺寸为6 mm × 8 mm试样,将不同试样研磨抛光,随后采用4%硝酸酒精溶液(体积分数)侵蚀10 s。利用Axioplan2光学显微镜(OM)、Nova nano 400场发射扫描电子显微镜(SEM)观察组织形貌。采用电子背散射衍射(EBSD)分析Q&P Si-Mn钢各相形貌及分布,EBSD实验是在配备了Symmetry 100探测器的ThermoFisher Apreo S HiVac场发射SEM中进行,测量步长50 nm。EBSD试样制备采用电解抛光方式去除残余应力,将研磨后的试样浸入5%HClO4 + 95%C2H5OH (体积分数)中,电解电压28 V,电流0.6 A,时间为30 s。采用JEM-2100透射电镜(TEM)进一步观察Q&P Si-Mn钢微观组织,TEM试样制备方法为:首先通过研磨方式将试样减薄至60 μm,随后用圆片打孔机将打磨好的试样冲出直径为3 mm的小圆片,最后在-25℃的高氯酸酒精溶液中进行电解双喷减薄,电压设置为30~50 V。同时借助PANslytical, NETHER-LANDS X射线仪(XRD)分析不同Q&P Si-Mn钢试样的残余奥氏体体积分数及C含量,其制样方式与EBSD相同。XRD采用Cu靶,扫描角度为35°~100°,工作电压为40 kV,电流为40 mA,步长为0.033°,扫描速率为1°/min。残余奥氏体体积分数根据下式计算[19]:
式中,V为残余奥氏体体积分数;Iγ 为fcc相(200) γ 、(220) γ 和(311) γ 衍射峰的积分强度;Iα 是bcc相(200) α 和(211) α 衍射峰的积分强度;G是每个组合对应的系数。
残余奥氏体中C含量可用下式计算[20]:
式中,αγ 为奥氏体的晶格常数,nm;xC和xMn分别为C和Mn在奧氏体中的质量分数,%。
最后根据GB/T228.1-2010标准在制备的不同Q&P Si-Mn钢板坯上每块加工3个板拉伸试样,拉伸试样总长度98 mm,平行段长度35 mm,宽度12.5 mm。拉伸实验在CMT5304拉伸试验机上进行,拉伸应变速率为5 × 10-4 s-1。
2 实验结果
2.1 Si-Mn钢热轧板组织
Si-Mn钢热轧板组织的OM像和SEM像如图2所示。可以看出,Si-Mn钢热轧板组织主要为铁素体(F)、贝氏体(B)和马氏体(M)。其中铁素体组织呈块状(BF)和带状(LF) 2种不同形貌。连铸坯热轧后通常会通过层流冷却的方式进行快速冷却,同时,钢的Mn含量较高,这些因素能抑制冷却过程中珠光体转变。此外,热轧后快速冷却工艺会对铁素体形貌产生影响。有研究[21]表明,采用层流冷却方式制备的ZJ330B钢热轧板坯的铁素体存在一定程度尺寸不均匀及随变形拉长的现象。这可能归因于热轧后高的冷却速率下部分铁素体晶粒来不及长大成块状,其仍保留热轧后的带状形貌,从而导致Si-Mn钢热轧板中铁素体呈现块状和带状2种不同形貌。
图2

图2 Si-Mn钢热轧板显微组织的OM像和SEM像
Fig.2 OM (a) and SEM (b) images of the Si-Mn hot-rolled plate (B, F, M, BF, and LF refer to bainite, ferrite, martensite, blocky ferrite, and lath-like ferrite, respectively)
2.2 不同奥氏体化温度下热轧板制备的Q&P Si-Mn钢的组织
图3为不同奥氏体化温度下制备的Q&P Si-Mn钢显微组织的SEM像。Q&P Si-Mn钢中不同组织经过腐蚀后会呈现出不同形貌[16,22]。当奥氏体化温度在810和840℃时(图3a和b),Q&P Si-Mn钢试样主要组织为F、残余奥氏体(RA)、一次马氏体(M1)和二次马氏体(M2)。一次马氏体形成于一次淬火阶段,经过配分阶段C配分,马氏体中C含量降低,类似于回火处理,因而也称为回火马氏体。二次马氏体形成于二次淬火至室温阶段,未经过配分工序,也称为未回火马氏体。奥氏体化温度为810℃时(图3a),钢中M1含量较少,有大量M2/RA存在。类似于热轧板初始组织,钢中铁素体呈块状和带状2种不同形貌。不同形貌铁素体相邻区域残余奥氏体存在一定差异,块状铁素体相邻区域残余奥氏体形貌以块状为主,而带状铁素体相邻区域残余奥氏体形貌呈薄带状。当奥氏体化温度升高到840℃时(图3b),M1含量显著增多,铁素体含量及M2/RA岛数量减少。随着奥氏体化温度升高至870℃时(图3c),铁素体含量及M2/RA岛数量急剧减少,M1含量进一步增多。当奥氏体化温度达到910和950℃(图3d和e)时,铁素体和M2/RA岛基本消失,试样中存在大量板条状马氏体。不同奥氏体化温度下制备Q&P Si-Mn钢的XRD谱、残余奥氏体体积分数及其C含量如图4所示。由图4a可知,随着奥氏体化温度的升高,(111) γ 、(200) γ 、(311) γ 等对应的峰强度逐渐降低(图4a)。结合峰的强度及式(
图3

图3 奥氏体化温度为810、840、870、910和950℃下制备Q&P Si-Mn钢显微组织的SEM像
Fig.3 SEM images of the Q&P Si-Mn steels under austenitizing temperatures of 810oC (a), 840oC (b), 870oC (c), 910oC (d), and 950oC (e) (RA, M1, and M2/RA refer to retained austenite, primary martensite, and secondary martensite/retained austenite island, respectively)
图4

图4 不同奥氏体化温度下制备Q&P Si-Mn钢的XRD谱、残余奥氏体体积分数及其C含量
Fig.4 XRD spectra (a) and volume fraction and carbon content of retained austenite (b) of Q&P Si-Mn steels under different austenitizing temperatures
图5为奥氏体化温度为810、870和950℃下制备Q&P Si-Mn钢的EBSD像,其中绿色组织为残余奥氏体,灰色组织为铁素体或一次马氏体,黑色组织为二次马氏体。可以看出,随着奥氏体化温度的升高,残余奥氏体含量逐渐降低。奥氏体化温度为810℃时(图5a),钢中残余奥氏体呈现块状和薄带状2种形貌,其中薄带状残余奥氏体主要沿带状铁素体长度方向分布,块状残余奥氏体主要分布在块状铁素体晶界处。随着奥氏体化温度升高到870℃(图5b),残余奥氏体含量明显减少。当奥氏体化温度提高至950℃时(图5c),可发现部分块状残余奥氏体分布在原始奥氏体晶界处。需要说明的是,分布在马氏体板条之间的薄膜状残余奥氏体宽度通常在几纳米到几十纳米之间,受限于EBSD数据采集步长,采用EBSD很难测定板条状马氏体之间的薄膜状残余奥氏体,这也是EBSD测定的残余奥氏体含量会明显小于XRD测定结果的原因。
图5

图5 奥氏体化温度为810、870和950℃下制备Q&P Si-Mn钢的EBSD像
Fig.5 EBSD images of the Q&P Si-Mn steels under austenitizing temperatures of 810oC (a), 870oC (b), and 950oC (c) (The green, gray, and black structures represent RA, F or M1, and M2, respectively)
图6所示为奥氏体化温度为810、870和950℃下制备Q&P Si-Mn钢的TEM像。可以看出,奥氏体化温度为810℃时(图6a和b),钢中铁素体呈现块状和带状2种形貌,而板条状马氏体数量较少,同时,残余奥氏体呈现薄带状和块状2种不同形貌,薄带状残余奥氏体分布在带状铁素体之间,其宽度通常在100 nm以上,块状残余奥氏体分布在块状铁素体相邻区域。当奥氏体化温度提高到870℃时(图6c和d),铁素体含量急剧减小,马氏体含量增多,部分残余奥氏体呈薄膜状分布于马氏体板条之间或原始奥氏体晶界处,其宽度在10~100 nm之间。当奥氏体化温度提高至950℃时(图6e和f),组织以板条状马氏体为主,并有少量的薄膜状残余奥氏体分布在马氏体板条之间,此外,在马氏体板条中存在大量的针状碳化物。
图6

图6 奥氏体化温度为810、870和950℃下制备Q&P Si-Mn钢的TEM像
Fig.6 TEM images of the Q&P Si-Mn steels under austenitizing temperatures of 810oC (a, b), 870oC (c, d), and 950oC (e, f) (Insets in Figs.6b and d show the selected area electron diffraction patterns of blocky RA and film-like RA, respectively)
2.3 不同奥氏体化温度下热轧板制备Q&P Si-Mn钢的力学性能及应变硬化行为
图7为不同奥氏体化温度下Q&P Si-Mn钢的工程应力-应变曲线。曲线没有明显的屈服平台,表现为连续屈服特征。不同试样的力学性能如图8所示。奥氏体化温度由810℃提高到870℃时,试样的屈服强度和抗拉强度分别由658和1046 MPa分别增加到1152和1320 MPa,但延伸率由27.11%下降到18.28%,强塑积由28.36 GPa·%下降到24.13 GPa·%。当奥氏体化温度进一步提高到910℃时,抗拉强度、屈服强度呈缓慢增加趋势,延伸率和强塑积缓慢下降。但当奥氏体化温度提高到950℃时,延伸率和强塑积进一步下降至16.32%和21.89 GPa·%。
图7

图7 不同奥氏体化温度下制备Q&P Si-Mn钢的工程应力-应变曲线
Fig.7 Engineering stress-strain curves of Q&P Si-Mn steels under different austenitizing temperatures
图8

图8 不同奥氏体化温度下制备Q&P Si-Mn钢的屈服强度、抗拉强度、延伸率及强塑积
Fig.8 Yield strength (a), tensile strength (b), elongation (c), and product of strength and elongation (d) of Q&P Si-Mn steels under different austenitizing temperatures
图9为奥氏体化温度为810、870和950℃下制备Q&P Si-Mn钢的真应力-真应变和应变硬化率曲线图。应变硬化率曲线的变化可分为3个阶段,分别是初期快速下降阶段(Stage I)、中期缓慢下降阶段(Stage II)及颈缩期的快速下降阶段(Stage III)。不同试样应变硬化率曲线不同阶段对应的真应变范围如表1所示。可以看出,随着奥氏体化温度提高,Stage I对应的真应变范围随之增大,Stage II和III对应的真应变范围减小。
图9

图9 奥氏体化温度为810、870和950℃下制备Q&P Si-Mn钢的真应力-真应变曲线和应变硬化率曲线
Fig.9 True stress-true strain (a) and strain hardening rate (b) curves of the Q&P Si-Mn steels under austenitizing temperatures of 810, 870, and 950oC
表1 奥氏体化温度为810、870和950℃下制备Q&P Si-Mn钢应变硬化率曲线各阶段对应真应变范围
Table 1
TA / oC | Stage I | Stage II | Stage III |
---|---|---|---|
810 | ε < 0.015 | 0.015 < ε < 0.166 | 0.166 < ε < 0.207 |
870 | ε < 0.018 | 0.018 < ε < 0.112 | 0.112 < ε < 0.135 |
950 | ε < 0.020 | 0.020 < ε < 0.088 | 0.088 < ε < 0.109 |
3 讨论
3.1 奥氏体化温度对热轧板制备Q&P Si-Mn钢组织的影响规律
奥氏体化温度是影响Q&P钢组织和力学性能的重要因素。根据奥氏体化温度不同,可将奥氏体化过程分为铁素体-奥氏体两相区奥氏体化和完全区奥氏体化。通常认为,采用两相区奥氏体化+ Q&P处理存在两次C配分行为。首先,在两相区奥氏体化阶段,铁素体中C会向奥氏体中扩散,提高淬火前奥氏体中C含量及热稳定性。也有研究[23]表明,在此阶段Mn也会出现明显的配分现象,从而进一步提高奥氏体的热稳定性。第二次发生在配分阶段,淬火后形成的一次马氏体中C向未转变奥氏体中扩散。通过两次的C配分,能显著提高Q&P钢中残余奥氏体含量[24]。同时,由于两相区奥氏体化后会提高奥氏体的热稳定性,一次淬火后,形成的一次马氏体较少,具有高的热稳定性的奥氏体不会发生转变并保持原奥氏体形貌,由于受热轧板中铁素体形貌的影响,这部分奥氏体呈现块状和薄带状2种形貌。在配分阶段,由于形成的一次马氏体较少,部分块状奥氏体不能获得足够的C配分,会在二次淬火阶段形成二次马氏体。因而在较低奥氏体化温度下,Q&P Si-Mn钢中残余奥氏体主要形貌为块状残余奥氏体、薄带状残余奥氏体及一定数量的M2/RA岛。随着奥氏体化温度的升高,奥氏体化后铁素体含量逐渐减少,由铁素体扩散到奥氏体中的C含量减少,奥氏体热稳定性降低,一次淬火后形成的一次马氏体含量增加,块状和薄带状残余奥氏体数量减少,部分未转变奥氏体呈薄膜状分布在马氏体板条之间,薄膜状残余奥氏体在配分阶段会获得足够C配分,因而能稳定至室温阶段,且具有比块状残余奥氏体更高的C含量。因此,随着奥氏体化温度提高,Q&P Si-Mn钢中一次马氏体含量增加,残余奥氏体和二次马氏体含量减小,而且残余奥氏体形貌转变成以薄膜状为主。此外,碳化物在马氏体中形成会消耗一部分C,从而导致经过950℃奥氏体化后Q&P Si-Mn钢残余奥氏体含量进一步降低但残余奥氏体中C含量没有明显变化。
3.2 奥氏体化温度对热轧板制备Q&P Si-Mn钢力学性能的影响规律
相较于硬相马氏体,铁素体相具有较低的强度和较好的塑性变形能力,而残余奥氏体的形变诱导马氏体转变,即相变诱导塑性(transformation induced plasticity,TRIP)效应能降低局部应力集中,延缓微裂纹的形成,是改善Q&P钢塑性的关键因素。随着奥氏体化温度的升高,马氏体含量增加,铁素体和残余奥氏体含量下降,这导致了Q&P Si-Mn钢抗拉强度和屈服强度升高但延伸率下降。材料的应变硬化行为与形变过程的组织演变密切相关,通过分析应变硬化率曲线可探究材料塑化机理。Stage I的应变硬化率呈快速下降趋势,这与铁素体中可动位错增殖和滑移相关[25,26]。奥氏体化温度为810℃时,钢中存在较高含量的铁素体及块状残余奥氏体,位错首先在铁素体晶粒增殖和滑移,并在滑移过程中逐渐塞积,从而产生加工硬化,激发残余奥氏体发生马氏体转变。研究表明Q&P钢中块状残余奥氏体机械稳定性较薄膜状残余奥氏体低[27],而薄带状残余奥氏体宽度明显大于薄膜状,且其相邻组织为较软的铁素体相,导致其机械稳定性也低于薄膜状残余奥氏体。因此,奥氏体化温度为810℃时,钢中块状和薄带状残余奥氏体更易被激发转变成马氏体,形成的马氏体会提高钢的应变硬化率,导致Stage I对应的真应变范围最小。奥氏体化温度为950℃时,钢中没有铁素体相,同时残余奥氏体主要呈薄膜状,因而具有更高的机械稳定性,需要在更大的应力和应变下才能发生形变诱导马氏体转变,因此其Stage I对应的真应变范围最大。奥氏体化温度为870℃时,钢中存在一定数量的铁素体和块状残余奥氏体,但2者含量均少于奥氏体化温度为810℃时的钢,因此其Stage I对应的真应变范围介于2者中间。Stage II应变硬化率呈缓慢下降的趋势,在此阶段主要发生铁素体塑性变形和残余奥氏体的TRIP效应[10,28]。随着奥氏体化温度升高,Q&P Si-Mn钢试样残余奥氏体和铁素体含量逐渐减小,因此,相应的Stage II所对应的真应变区间也逐渐减小。Stage III应变硬化率快速下降与材料发生颈缩相关,铁素体塑性变形和残余奥氏体的TRIP效应能在一定程度上减缓微裂纹的萌生及扩展,因而奥氏体化温度为810℃时Stage III对应的真应变范围最大。此外,相较于奥氏体化温度为870℃,奥氏体化温度为950℃时钢中马氏体板条较为粗大,而研究[29]表明,拉伸过程中的微裂纹更易从粗马氏体板条中萌生,因此奥氏体化温度为950℃时,Stage III对应的真应变区间最小。综上所述,奥氏体化温度为810℃时Q&P Si-Mn钢具有更好的延伸率与其具有更高含量的铁素体及残余奥氏体相关,在形变过程中铁素体的塑性变形和残余奥氏体的TRIP效应能有效缓解局部应力集中和抑制微裂纹的萌生及扩展,从而提高Q&P Si-Mn钢的塑性。
根据本工作的研究结果,采用热轧板在两相区温度奥氏体化制备的Q&P Si-Mn钢最佳强塑积达到28.36 GPa·%,相较于目前已报道的某钢铁企业采用冷轧板制备的980 MPa级Q&P Si-Mn钢(采用两相区奥氏体化处理),强塑积提高了约36%[3],也高于其他研究报道采用化学成分接近冷轧板并结合类似工艺制备的Q&P Si-Mn钢[30,31]。采用热轧板两相区奥氏体化制备的Q&P Si-Mn钢具有更高的强塑积,这可能归因于其铁素体形貌。热轧板制备的Q&P Si-Mn钢铁素体呈块状和带状2种不同形貌,而冷轧板制备的Q&P钢铁素体主要呈块状[30,31]。有研究[32,33]表明,相比块状铁素体,带状铁素体更有利于协调形变过程中的应力分布,延缓局部应力集中及微裂纹的萌生及扩展,从而能提高Q&P钢的塑性。此外,带状铁素体有利于薄带状残余奥氏体的形成,而块状铁素体相邻区域更易形成块状残余奥氏体[34]。相较于块状残余奥氏体,薄带状残余奥氏体与铁素体之间有更大的接触比表面积,这有利于C的扩散以及C在奥氏体中分布均匀化,因而薄带状残余奥氏体具有比块状残余奥氏体更高的机械稳定性。热轧板制备的Q&P Si-Mn钢存在块状和薄带状2种不同稳定性残余奥氏体,在形变过程中2种不同稳定性残余奥氏体的连续转变有利于提高材料的塑性[35~37]。而冷轧板制备的Q&P钢(两相区奥氏体化)残余奥氏体主要以块状为主[33],大量低稳定性残余奥氏体在形变初期极易发生转变,不利于Q&P钢充分利用残余奥氏体的TRIP效应来提高材料的塑性。
4 结论
(1) 随着奥氏体化温度由810℃升高至950℃,热轧板制备的Q&P Si-Mn钢屈服强度和抗拉强度均逐渐提高,延伸率、强塑积逐渐降低,其中在810℃奥氏体化后,热轧板制备的Q&P Si-Mn钢强塑积达到28.36 GPa·%。
(2) 810℃奥氏体化后的Q&P Si-Mn钢具有较高的残余奥氏体含量,同时铁素体呈块状和带状2种不同形貌,块状铁素体相邻区域残余奥氏体形貌呈块状,带状铁素体相邻区域残余奥氏体呈薄带状。随着奥氏体化温度的升高,Q&P Si-Mn钢残余奥氏体体积分数下降,残余奥氏体中的C含量先升高,随后基本保持不变。
(3) 热轧板制备的Q&P Si-Mn钢表现出比冷轧板生产的980 MPa级Q&P Si-Mn钢更高的强塑积与其组织中存在带状和块状2种不同形貌铁素体相关。
致谢
感谢武汉科技大学分析测试中心王贞老师在EBSD测试中给予的帮助。
来源--金属学报