分享:Y对无取向6.5%Si钢凝固组织、中温压缩变形和软化机制的影响
李民1,2, 王继杰1, 李昊泽,2,3, 邢炜伟2, 刘德壮2, 李奥迪2, 马颖澈2
利用EPMA、EBSD、XRD、TEM和热压缩测试,研究了Y元素对无取向6.5%Si钢铸态组织、有序相、中温变形和软化机制的影响。结果表明,当Y含量为0.017%和0.15%时,钢液中形成高熔点Y2O3 + Y2O2S/Y2O2S-YP复合稀土化合物,促进异质形核。凝固末期,枝晶间形成Y2Fe14Si3化合物,凝固组织得到明显细化。铸锭的基体有序度与Y含量呈反比关系。500℃压缩实验结果表明,不同Y含量铸锭的塑性变形均由位错滑移机制主导。含Y试样峰值应力对应的临界应变降低,加工软化提前,加工硬化率下降,动态软化作用增强。热压缩试样的位错密度正比于Y含量,低基体有序度和高形变诱导无序作用是含Y试样动态软化作用增强的主要原因。
关键词:
随着我国电力、电子和国防军工等领域的快速发展,对高性能电工钢的迫切需求日益增长。无取向6.5%Si钢(质量分数,下同)具有优异的高频软磁性能,如低铁损、高磁导率和接近零的饱和磁滞伸缩系数[1],一直备受人们关注。然而,随Si含量提升至6.5%,B2和D03有序相的形成使得高硅钢室温塑性差,易发生脆性断裂,几乎不能冷变形,严重制约了该合金钢的工业生产及应用。热轧硅钢受限于产品表面质量和磁性能等问题,早已被淘汰。因此,在高硅钢的规模化生产实验中,中温变形成为了与之最契合、最有效的一种制备工艺。
一直以来,稀土微合金化是无取向6.5%Si钢增塑研究的重点课题之一。稀土元素凭借独特的原子结构和物理化学性质,在改善高硅钢的微观组织、力学性能以及磁性能方面均具有重要影响。添加元素主要包括Ce[2~7]、La[4]、Y[4,8~10]和Hf[11]等,且相关报道主要集中在轻稀土Ce。Li等[3]研究了稀土Ce对薄带连铸无取向6.5%Si钢600℃拉伸塑性的影响,发现添加Ce有助于细化组织,提高晶间结合力,能够有效避免铸带发生沿晶断裂。Yu等[4]研究了稀土元素对6.5%Si钢有序结构和拉伸塑性的影响,发现添加Ce、La和Y均能够降低基体有序度,含Ce试样400℃断后延伸率由无Ce试样的7.3%提升至23.0%。Cai等[7]研究了稀土Ce对高硅钢在400~640℃中温压缩变形行为和力学性能的影响,将高硅钢力学性能的提升归因于添加Ce导致的有序度降低和位错组态转变。此外,Yu等[11]发现添加Hf元素能够阻碍6.5%Si钢有序化并提升其拉伸塑性,富Hf的fcc结构Hf-Fe-Si相的析出是抑制Fe-Si有序相形成的重要原因。
有关重稀土Y对无取向6.5%Si钢的增塑研究较少,且主要集中在Y元素对无取向6.5%Si钢高温变形的影响研究[8,9]。Liu等[8]研究了无取向6.5%Si钢在600~900℃下的热压缩变形行为,发现添加Y通过细化晶粒和有序相,能够改善无取向6.5%Si钢热变形塑性,减少微裂纹产生,扩大热加工工艺稳定区。然而,目前针对稀土Y对无取向6.5%Si钢中温压缩变形影响的研究尚未见报道,相关作用机制也有待阐明。
本工作重点研究了稀土Y对无取向6.5%Si钢凝固组织、中温压缩变形行为及软化机制的影响规律。通过对试样铸态组织、500℃压缩力学性能和变形组织的对比分析,澄清了稀土Y对改善无取向6.5%Si钢塑性变形能力和动态软化能力的作用机制。以期为稀土微合金化无取向6.5%Si钢的成分设计和加工工艺制定提供实验参考。
1 实验方法
使用25 kg真空感应熔炼炉制备出3种不同Y含量的无取向6.5%Si钢铸锭作为实验原始材料。初始铸锭横截面直径为100 mm,金相与热模拟试样均截取自铸锭半径的1/2处。其中,添加Y的含量采用iCAP6300电感耦合等离子发射光谱仪检测,3种试样详细的化学成分列于见表1,根据Y含量的检测结果,将其分别命名为0Y、0.017Y和0.15Y。
表1 不同Y含量铸锭的化学成分 (mass fraction / %)
Table 1
Sample | C | S | O | N | P | Y | Si | Fe |
---|---|---|---|---|---|---|---|---|
0Y | 0.0070 | < 0.001 | 0.0005 | 0.0008 | 0.002 | < 0.0005 | 6.35 | Bal. |
0.017Y | 0.0086 | < 0.001 | 0.0006 | 0.0009 | 0.002 | 0.017 | 6.43 | Bal. |
0.15Y | 0.0081 | < 0.001 | 0.0005 | 0.0009 | 0.002 | 0.15 | 6.50 | Bal. |
使用电火花线切割切取直径10 mm、长15 mm的铸态试样,在Gleeble 3800型热模拟试验机上进行单道次压缩实验,各实验用钢测试3支平行试样,并获得真应力-真应变曲线。试样以10℃/s的升温速率加热到500℃,保温4 min后开始变形,应变速率为1 s-1,压缩率为40%,变形后立即取出水冷,保留变形组织。
铸态试样和压缩变形试样经逐级打磨、抛光后,采用4 g CuSO4 + 20 mL HCl + 20 mL H2O的混合溶液进行腐蚀,使用GX53光学显微镜(OM)获取金相组织,采用截线法测量平均晶粒尺寸,裂纹长度、数量使用OLYCIA m3软件——几何测量工具进行统计。使用JXA-8530F场发射电子探针(EPMA)对铸锭枝晶进行微区元素分析。使用装备Nordlys Max3型电子背散射衍射(EBSD)分析系统和Ultim MaxN硅漂移型能谱仪(EDS)的MIRA3型场发射扫描电镜(SEM)对铸锭枝晶界稀土化合物进行EBSD相鉴定分析和EDS分析。使用Image-Pro Plus软件对铸锭中晶内和晶界稀土化合物的数量、尺寸和面积进行测量统计。
采用SmartLab多功能X射线衍射仪(XRD)对铸态试样进行有序结构分析,扫描速率为10°/min。将直径3 mm的铸态试样和变形试样打磨至50 μm厚,使用TenuPol-5电解双喷仪在电压为30 V和温度为-20℃的条件下进行化学减薄,双喷液采用5%HClO4 + 95%C2H6O (体积分数)混合溶液,然后使用Talos F200透射电镜(TEM)进行选区电子衍射(SAED)分析。使用Velox软件测量有序相{010}衍射斑与基体{020}衍射斑的相对强度比。
EBSD试样通过电解抛光制备,电解液采用13%HClO4 + 87%C2H6O (体积分数)混合溶液,电压为30 V,温度为-20℃。使用配备Symmetry EBSD探测器的MERLIN Compact场发射扫描电镜检测变形试样纵剖面的微观组织,相关EBSD数据使用配备的HKL Channel 5软件分析处理。
2 实验结果与讨论
2.1 铸锭微观组织
图1为3种铸锭的宏观组织和对应的高倍SEM像。由低倍组织(图1a~c)可以看出,铸锭表层存在明显的激冷层,形成了明显的细晶区。0Y铸锭表层存在1~2 cm的柱状晶区,而3种铸锭半径的1/2处和中心均为等轴晶组织。随Y含量提高,凝固组织得以显著细化。经过统计,3种铸锭的平均晶粒尺寸分别为(1770 ± 126)、(748 ± 56)和(204 ± 10) μm。铸锭的SEM像(图1d~f)显示,0.017Y和0.15Y铸锭的枝晶内和枝晶界出现了稀土化合物。
图1

图1 0Y、0.017Y和0.15Y铸锭的宏观组织和SEM像
Fig.1 Macrostructures (a-c) and high magnified SEM images (d-f) of the as-cast 0Y (a, d), 0.017Y (b, e), and 0.15Y (c, f) ingots (Insets in Figs.1e and f show the magnified images. GB—grain boundary, IGC—intragranular rare-earth compound, IDC—interdendritic rare-earth compound)
为进一步确定晶内稀土化合物的种类,使用EPMA分析了晶内稀土化合物的化学成分。如图2所示,在0.017Y和0.15Y铸锭枝晶内观察到了颗粒状的富Y相,尺寸约为2 μm,稀土化合物的芯部富集Y、O和S元素,外层富集Y和P元素。根据稀土化合物的Gibbs形成自由能[12]可知,由于稀土Y与O、S、P具有较强的化学亲和力,钢液中添加Y可以形成高熔点Y2O3、Y2O2S、Y2S3、YS或YP。综合铸锭晶内稀土化合物的元素富集情况和化学成分(图2和表2),推断在本实验条件下0.017Y和0.15Y铸锭在熔炼过程中形成了稀土Y的复合型化合物,化学组成略有差异。复合稀土化合物的形成受钢液中Y与杂质元素反应热力学的影响,与Y含量有关。0.017Y铸锭中晶内稀土化合物芯部主要为Y2O3和Y2O2S,表层为YP。0.15Y铸锭中晶内稀土化合物芯部为Y2O2S,表层为YP。这种复合型稀土化合物的形成说明在当前熔炼条件下,Y元素与钢液中的O、S具备更高的化学亲和力,首先化合形成复合稀土化合物的核心,然后以此为形核基底,Y元素进一步与钢液中的P化合形成表层的YP。
图2
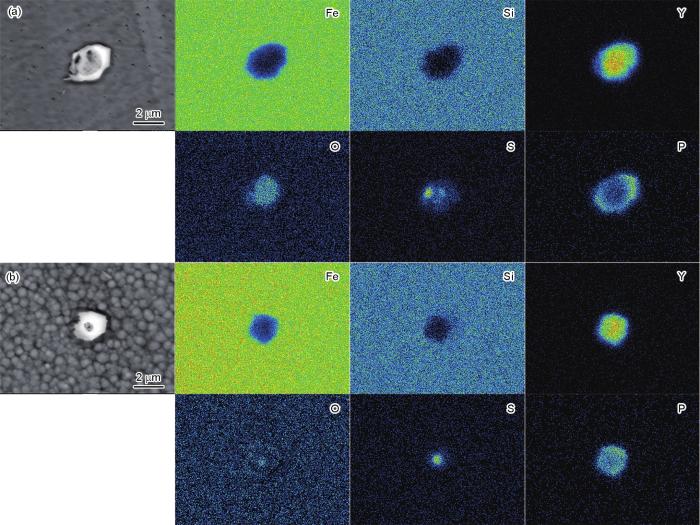
图2 0.017Y和0.15Y铸锭的SEM像和EPMA元素面分布图
Fig.2 SEM images and the corresponding EPMA elemental maps of the intragranular rare-earth compounds in the as-cast 0.017Y (a) and 0.15Y (b) ingots
表2 铸锭晶内稀土化合物的EDS结果 (atomic fraction / %)
Table 2
Sample | Fe | Si | Y | O | S | P |
---|---|---|---|---|---|---|
0.017Y | 2.64 | 1.17 | 30.60 | 63.68 | 0.82 | 1.09 |
0.15Y | 18.40 | 2.15 | 35.85 | 28.73 | 11.08 | 3.79 |
0.017Y和0.15Y试样细化的凝固组织与复合稀土化合物的形成有关。高熔点稀土化合物通常与基体具有低晶格错配度,能够促进钢液异质形核,细化凝固组织。本工作基于Bramfitt[13]提出的错配度计算方法,验证了复合稀土化合物表层的YP能否作为有效的形核剂促进异质形核:
式中,(hkl)s和(hkl)n分别为基体和形核剂的低指数晶面;[
表3 晶格错配度计算结果
Table 3
[ |
[ |
|
|
θ / (o) |
|
δ |
---|---|---|---|---|---|---|
[ |
[001]YP | 0.2845 | 0.2826 | 0 | 0.2845 | 0.67% |
[ |
[ |
0.6969 | 0.6922 | 0 | 0.6969 | |
[ |
[ |
0.4023 | 0.3997 | 0 | 0.4023 |
图3和4分别为0.017Y和0.15Y铸锭枝晶界稀土化合物的SEM像、Kikuchi花样和EDS元素面分布图。如图3a~c和图4a~c所示,枝晶界稀土化合物的Kikuchi花样与Y2Fe17相的[001]晶带轴花样高度吻合。元素面扫描结果(图3d~f和图4d~f)显示,枝晶界稀土化合物富集Y和Si元素。根据Fe-Si-Y的三元相图[14]可知,在富Fe区的Fe-Si-Y体系中Y2Fe17相是最可能优先形成的化合物。研究[15]表明,Si原子能够置换Y2Fe17相中某些占位结点的Fe原子形成Y2Fe17 - x Si x 型化合物,并且随Si原子的化学计量数增大(xmax = 3),Y2Fe17 - x Si x 的晶体结构不变,晶格参数几乎不变。因此,综合枝晶界稀土化合物的Kikuchi花样和化学成分(表4),确定枝晶界稀土化合物为Y2Fe14Si3化合物,具有六方点阵的Th2Ni17型晶体结构。
图3
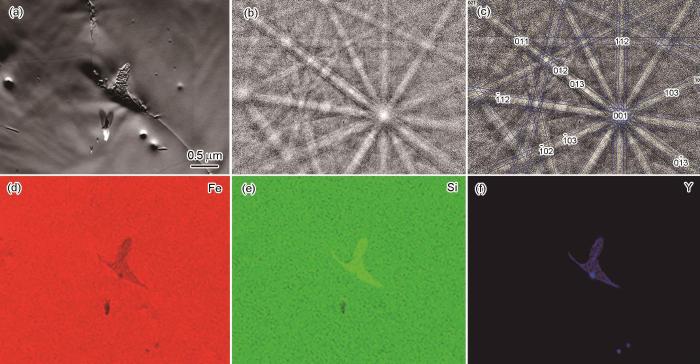
图3 0.017Y铸锭晶界稀土化合物的SEM像、Kikuchi花样和EDS元素分布图
Fig.3 SEM image (a), the corresponding Kikuchi patterns (b, c), and EDS elemental maps (d-f) of the interdendritic rare-earth compounds in the as-cast 0.017Y ingot
图4
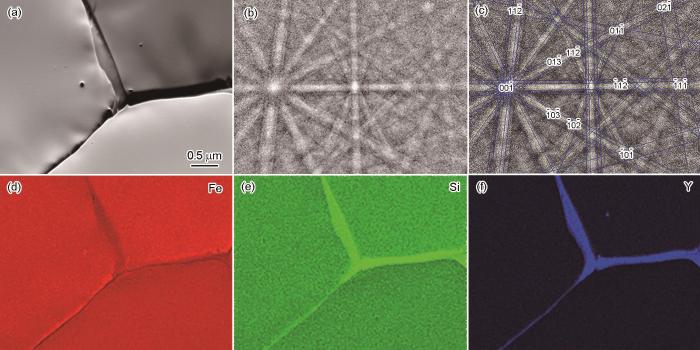
图4 0.15Y铸锭晶界稀土化合物的SEM像、Kikuchi花样和EDS元素分布图
Fig.4 SEM image (a), the corresponding Kikuchi patterns (b, c), and EDS elemental maps (d-f) of the interdendritic rare-earth compounds in the as-cast 0.15Y ingot
表4 图3和4中晶界稀土化合物的EDS分析结果
Table 4
Sample | Position | Atomic fraction / % | ||
---|---|---|---|---|
Fe | Si | Y | ||
0.017Y | Matrix | 88.16 | 11.84 | 0 |
Rare-earth compound | 77.01 | 15.33 | 7.66 | |
0.15Y | Matrix | 87.96 | 12.04 | 0 |
Rare-earth compound | 75.64 | 16.27 | 8.09 |
为了定量统计铸锭中晶内和晶界稀土化合物含量与添加Y含量之间的关系,对稀土化合物的个数、尺寸和面积进行测量,分别通过
式中,fv-IGC为晶内稀土化合物的体积分数,N为稀土化合物的数量,A为测量照片的面积,d为稀土化合物的平均直径。
式中,fa-IDC为晶界稀土化合物的面积分数,A0为稀土化合物的面积。统计结果表明,0.017Y和0.15Y铸锭中晶内稀土化合物的体积分数分别为0.01%和0.05%,晶界稀土化合物的面积分数分别为0.11%和0.90%,2者均随添加Y含量的增加明显提高。
基于上述实验结果,图5给出了添加Y的无取向6.5%Si钢凝固过程示意图。当熔体处于高于基体熔点的一定温度时,高熔点、颗粒状的富Y复合稀土化合物优先在熔体中形成(图2)。随后,熔体温度降低达到一定过冷度,基体开始形核结晶。其中,稀土化合物的异质形核机制是含Y铸锭凝固组织细化的主要原因。随基体进一步结晶长大,由于Y原子较大的原子半径和较低的固溶度[17],仅有少量Y原子固溶于基体中,而大多数Y原子将逐渐偏析至固-液界面前沿。这种偏析可能产生一个成分过冷区域,从而通过溶质效应进一步导致晶粒细化[18,19],这是含Y铸锭凝固组织细化的另一个原因。此外,Fe、Si和Y的电负性分别为1.83、1.90和1.22,Y-Fe和Y-Si之间的电负性差值分别为0.61和0.68,这表明Y原子与Si原子具有更大的亲和力。因此,Y的偏析可能吸引更多的Si原子向固-液界面扩散,使残余熔体中Y、Si原子浓度逐渐提高。最终,凝固末期铸锭在枝晶间形成Y2Fe14Si3化合物(图3和4)。
图5
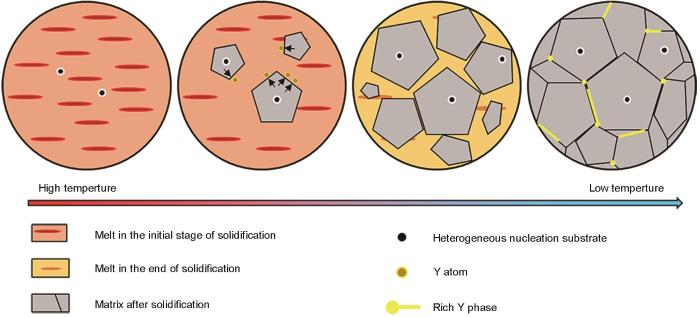
图5 添加Y的无取向6.5%Si钢凝固过程示意图
Fig.5 Schematic of the solidification process of non-oriented 6.5%Si electrical steel doped with Y
综上所述,当添加Y含量为0.017%和0.15%时,稀土Y在铸锭凝固组织中主要有3种存在方式,包括枝晶内高熔点的Y2O3 + Y2O2S/Y2O2S-YP复合稀土化合物,枝晶间的Y2Fe14Si3化合物以及固溶在基体中的少量Y原子。随Y含量增加,枝晶内和枝晶间稀土化合物的含量均逐渐提高。
无取向6.5%Si钢在760℃以上为A2结构,即具有bcc晶格结构的无序固溶体[20]。而随温度降低,A2相将发生有序化转变形成B2 (FeSi)和D03 (Fe3Si) 2种有序相[21]。图6为不同Y含量铸态试样的XRD谱。可见,3种试样中均检测到了B2相的衍射特征峰,说明铸锭冷却过程中均发生了有序相转变。相关文献报道[4,21],通过测量有序相特征衍射峰和基体衍射峰的相对强度比(IB2(100) / IA2(200))可以表征有序度,相对强度比越大,基体有序度越高。随Y含量增加,铸锭IB2(100) / IA2(200)的测量结果分别为2.39、1.38和0.40,基体有序度逐渐减小。此外,基体有序度还可以通过TEM有序相(100)和基体(200)衍射斑的相对强度比进行表征[20]。图7为铸锭[001]晶带轴的SAED花样,使用Velox软件统计了有序相(100)衍射斑与基体(200)衍射斑的相对强度比,0Y、0.017Y和0.15Y铸态试样中I
图6
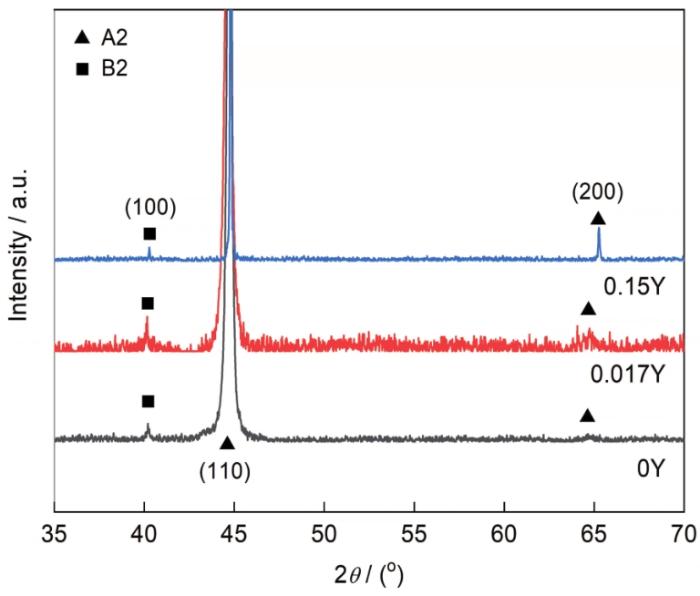
图6 不同Y含量铸锭的XRD谱
Fig.6 XRD spectra of the ingots with various Y contents
图7
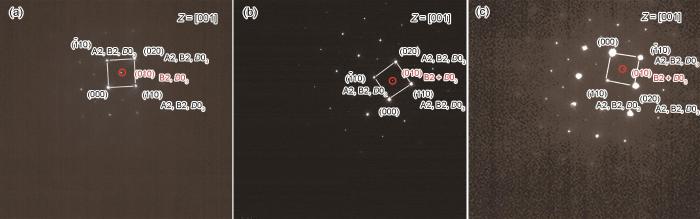
图7 不同Y含量铸态试样沿[001]晶带轴的SAED花样
Fig.7 SAED patterns along [001] zone axes of the as-cast 0Y (a), 0.017Y (b), and 0.15Y (c) samples
2.2 中温压缩力学性能(500℃)
图8为3种铸态试样500℃压缩的真应力-真应变曲线,均由弹性变形阶段、加工硬化阶段和加工软化阶段组成。材料发生屈服后,进入加工硬化阶段,由于位错积累,真应力随应变增加而增大。随后,当达到峰值应力后(最大应力),进入加工软化阶段,动态软化作用的增强使真应力随应变增加而减小。基于真应力-真应变曲线,加工硬化率可通过
图8
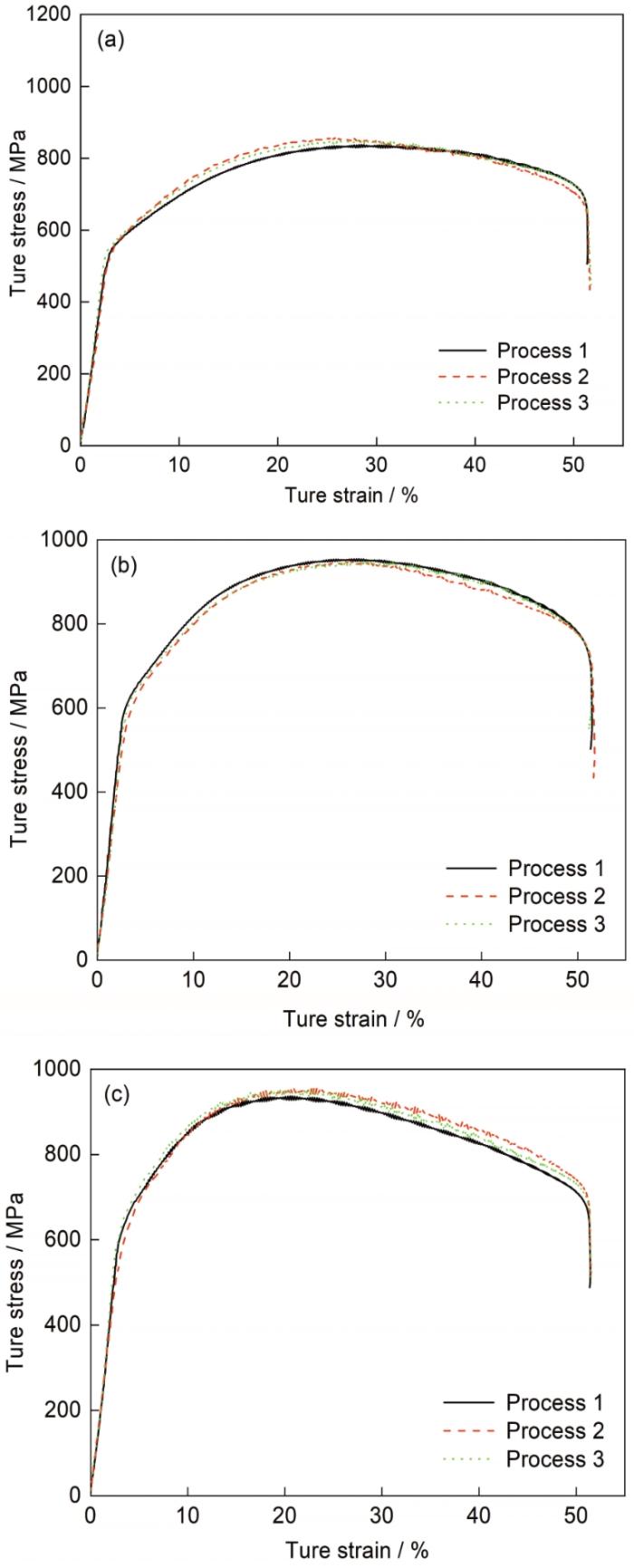
图8 不同Y含量铸态试样在500℃、1 s-1和40%压下量压缩的真应力-真应变曲线
Fig.8 True stress-true strain curves of the as-cast 0Y (a), 0.017Y (b), and 0.15Y (c) samples at 500oC with constant strain rate of 1 s-1 and constant reduction of 40%
式中,θ为加工硬化率,σ为真应力,ε为真应变,T为变形温度,
图9
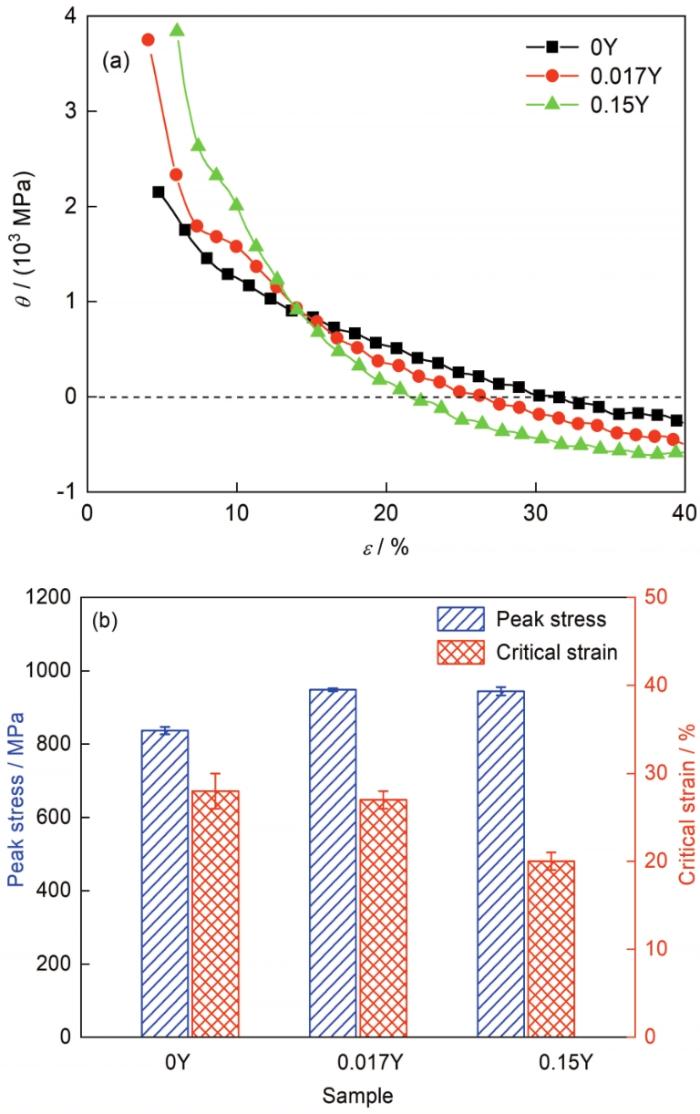
图9 不同Y含量铸态试样500℃压缩的加工硬化率-真应变(θ-ε)曲线、峰值应力和相应的临界应变
Fig.9 Comparisons of θ-ε curves (a), peak stress and the corresponding critical strain (b) of the as-cast samples with various Y contents compressed at 500oC (θ—work hardening rate, ε—true strain)
2.3 变形组织与加工软化机制
图10为不同Y含量铸态试样500℃压缩后外表的宏观照片。可见,0Y和0.017Y试样表面凹凸不平,这表明2者变形时发生了塑性失稳。与此相反,0.15Y试样变形后呈典型的圆鼓状,说明其变形相对比较稳定。
图10
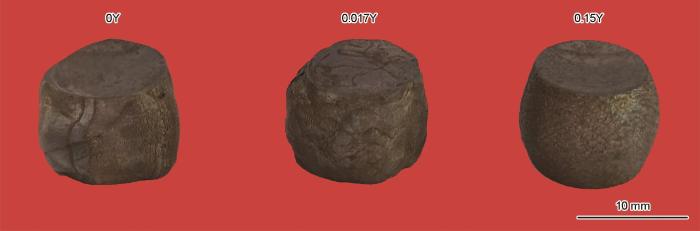
图10 3种铸态试样500℃压缩后的宏观照片
Fig.10 Macrographies of the as-cast samples with various Y contents after compression at 500oC
图11a~c为不同Y含量铸态试样500℃压缩后纵剖面组织的OM像。可见,试样表层区变形程度较小,晶粒仍保持等轴状态,并产生了明显的穿晶裂纹,这说明该区域塑性变形比较困难,所以该区域通常也被称为“死区”。相比之下,试样芯部晶粒垂直压缩方向(compression direction,CD)产生了明显伸长,且无裂纹,表明压缩时塑性变形主要集中发生在芯部区域。此外,对3种试样表层区的裂纹数量和长度进行了测量,结果绘于图11d。可以看出,随Y含量增加,裂纹的数量和总长度均减小,其中裂纹总长度的减小尤为明显,这说明添加Y后试样的裂纹萌生和扩展能力得到一定程度的抑制。
图11

图11 不同Y含量铸态试样500℃压缩后纵剖面组织的OM像和裂纹统计结果
Fig.11 Longitudinal OM images showing the micro-structures of the as-cast 0Y (a), 0.017Y (b), and 0.15Y (c) samples after compression at 500oC, and statistical results of cracks in the surface regions (d) (CD—compression direction)
如图12所示,进一步观察变形试样,可以看出芯部拉长晶的内部存在明显的变形带组织,这是由于局部不均匀变形所致[19]。研究[24]表明,在低温或高应变速率的条件下,6.5%Si钢在变形过程中易产生{112}<111>形变孪晶,变形机制可能为位错滑移和形变孪晶的联合机制。其中,{112}<111>形变孪晶与基体之间的转轴关系为绕<111>轴转动60°可得到Σ3的重合点阵界面[25,26]。然而,如图12d~f所示,变形带与基体的取向关系分析结果显示出,3种变形试样的变形带与基体之间均不具备Σ3-60°<111>的特殊取向关系,说明3种试样在变形过程中均未形成形变孪晶,所以500℃热压缩的变形机制均为位错滑移机制。此外,从该区域的元素面扫描图(图12g~i)可以看出,变形后0.017Y和0.15Y试样中晶界Y2Fe14Si3化合物逐渐沿变形方向延伸,部分Y2Fe14Si3化合物发生了破碎,沿晶界呈链状分布。由于Y2Fe14Si3化合物含量较少,且变形后并未在其与基体的界面处观察到显微裂纹的萌生和扩展,所以分析认为在当前实验条件下,Y2Fe14Si3的少量析出不会对含Y铸锭的中温加工塑性带来负面影响。图13示出了不同Y含量铸态试样压缩后的晶粒取向图和局部取向差(local misorientation,LM)图。LM表示定点与其最近邻点之间的平均取向差,它是评定应变分布和几何必须位错(geometrically necessary dislocation,GND)的重要指标[8,27]。如图所示,变形试样的表层晶粒LM较低,基本呈蓝色,为低应变区;芯部晶粒LM较高,基本呈绿色,为高应变区。比较3种变形试样的高应变区(图13b、d和f黑色方框区域),0Y和0.017Y变形试样芯部呈蓝绿相间,LM分布不均匀;而0.15Y变形试样芯部的LM分布更为均匀,说明0.15Y试样的应变分布相对均匀,晶粒间具有良好的变形协调能力。
图12
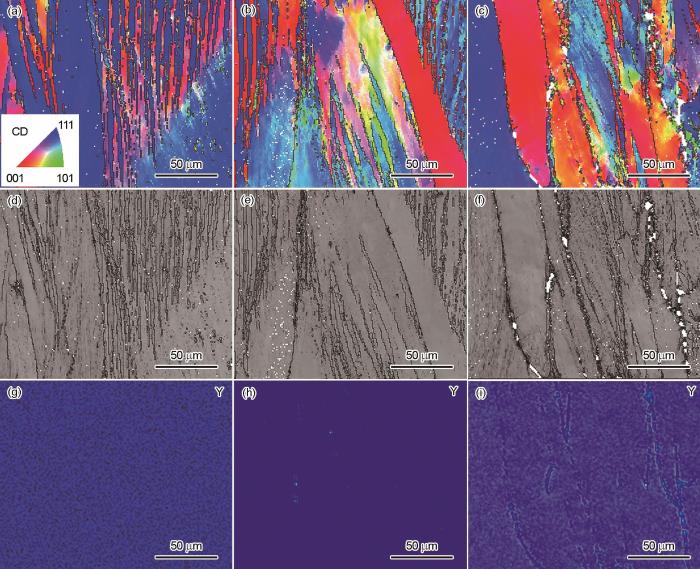
图12 不同Y含量铸态试样500℃压缩后的EBSD反极图、Σ3-60°<111>特殊晶界分布图及元素面扫描图
Fig.12 CD-inverse pole figures (IPFs) (a-c), Σ3-60°<111> special grain boundary distribution maps (d-f), and EDS elemental maps (g-i) of the as-cast 0Y (a, d, g), 0.017Y (b, e, h), and 0.15Y (c, f, i) samples after compression at 500oC
图13
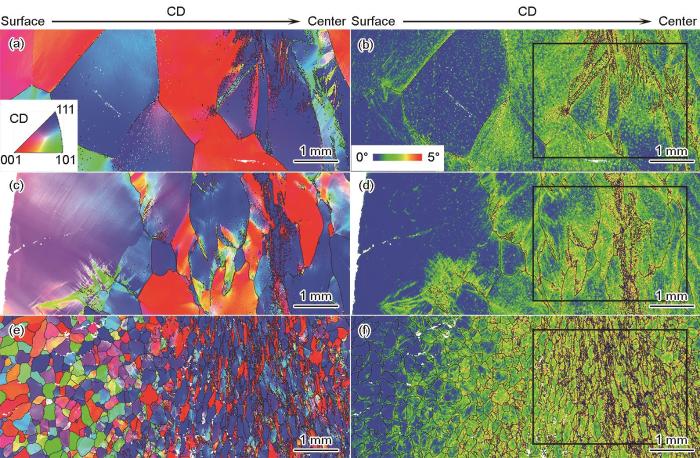
图13 不同Y含量铸态试样500℃压缩后纵剖面的EBSD晶粒取向图和局部取向差(LM)图
Fig.13 Longitudinal EBSD grain orientation maps (a, c, e) and local misorientation (LM) maps (b, d, f) of the as-cast 0Y (a, b), 0.017Y (c, d), and 0.15Y (e, f) samples after compression at 500oC
基于图13采集的EBSD数据,通过Gao等[28]以及Kubin和Mortensen[29]提出的应变梯度理论计算了GND密度,相关的计算公式为:
式中,
图14统计了图13黑色方框区域内3种试样芯部变形组织在0°~5°范围内的LM分布,黑线代表Gauss拟合曲线。可以看出,0Y和0.017Y试样芯部变形组织的LM分布相似,主要集中在0°~2°区间;而0.15Y试样芯部变形组织的LM主要分布于2°~4°区间,说明0.15Y试样在变形后晶粒内部的局部取向差更大,位错密度更高。通常,在计算GND密度时,排除大于3°的LM值,因为这些位置可能是变形的晶界或回复后的亚晶界,而并非是由位错积累造成的[30]。图14d示出了GND密度的计算结果,0Y和0.017Y试样芯部变形组织的GND密度相差不大,分别为1.17 × 1015和1.22 × 1015 m-2,而0.15Y试样的GND密度提高至1.73 × 1015 m-2。
图14

图14 不同Y含量铸态试样500℃压缩后芯部晶粒的LM分布图和对应的几何必须位错(GND)密度
Fig.14 LM distribution histograms of the as-cast 0Y (a), 0.017Y (b), and 0.15Y (c) samples after compression at 500oC, and the corresponding geometrically necessary dislocation (GND) densities (ρGND) (d) (R2—coefficient of determination)
图15为不同Y含量铸态试样500℃压缩后的TEM明场像和对应的SAED花样。首先,从图15a~c中可以明显看出,随Y含量增加,基体中位错密度逐渐增大,这与基于EBSD数据计算的GND密度变化趋势一致。其次,在3种试样的芯部变形组织中均未观察到再结晶晶粒或亚晶组织(图11a~c和图15a~c),表明3种试样在变形过程中仅发生中温回复,其回复机制主要与位错重组有关[20,31]。此外,沿[001]晶带轴的SAED花样(图15d~f)显示,3种变形试样仅出现基体衍射斑,而有序相的衍射斑全部消失,说明经500℃压缩后3种试样的芯部变形组织接近无序状态。基于上述分析,可以确定本工作中3种试样在500℃压缩过程中的软化机制由动态回复和形变诱导无序机制(deformation induced disordering,DID)[32,33]主导。
图15
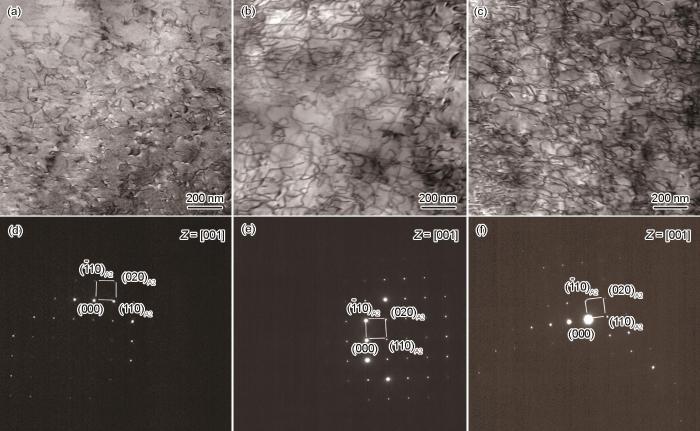
图15 不同Y含量铸态试样500℃压缩后的TEM明场像和对应的SAED花样
Fig.15 Dislocation configurations in bright-field TEM images (a-c) and the corresponding SAED patterns (d-f) along [001] zone axes of the as-cast 0Y (a, d), 0.017Y (b, e), and 0.15Y (c, f) samples after compression at 500oC
上述实验结果表明,添加Y对改善无取向6.5%Si钢的塑性变形能力具有重要影响作用。一方面,添加Y后铸锭凝固组织显著细化。从图13可以看出,变形过程中晶界是局部应力集中的主要区域,因为晶界作为位错运动的障碍易造成位错塞积,导致局部应力集中,最终发生塑性失稳。相反,晶粒细化不仅能够增大晶界总面积,阻碍裂纹扩展(图11),而且能够使塑性变形分散在更多的晶粒内进行,应力集中相对较小,塑性变形更加均匀。另一方面,添加Y后6.5%Si钢基体有序度降低(图6和7),这是位错密度随Y含量增加而增大的主要原因[8] (图14d和图15a~c)。有序相的塑性变形主要依靠超位错滑移,超位错受到反相畴的束缚难于交滑移[33~35]。位错密度提高有利于位错切割有序相[21],从而使DID作用增强。
高温压缩时,实验用钢真应力-应变曲线的变化特征取决于加工硬化作用和加工软化作用的相对强弱关系。变形前期,加工硬化阶段主要由有序强化和细晶强化主导。晶粒细化意味着晶界面积增大,易造成晶界处位错塞积;有序化导致位错运动困难,2者引起的强化作用与峰值应力呈正相关。随Y含量增加,铸锭晶粒细化,基体有序度降低。细晶强化作用导致0.017Y和0.15Y试样变形前期的加工硬化值和峰值应力明显高于0Y试样。而当Y含量增加至0.15%,试样基体有序度显著降低,所以其峰值应力的提高不再明显(图9b)。变形后期,加工软化阶段主要由动态回复和DID作用主导。与0Y试样相比,0.017Y试样的位错密度略微增大,0.15Y试样的位错密度明显增大(图15a~c)。添加Y使基体有序度降低,基体位错密度增大,导致了DID作用增强。因此,随Y含量增加,试样的临界应变和变形后期的加工硬化率逐渐减小。当Y含量增加至0.15%时,由于基体位错密度和DID作用最高,临界应变由0Y的28%和0.017Y的27%减小至20% (图9b)。综上所述,本工作将含Y试样加工软化作用的增强归因于基体有序度下降和DID作用的增强。
3 结论
(1) 在当前熔炼条件下,添加Y含量为0.017%和0.15%,无取向6.5%Si钢的枝晶内形成了高熔点的Y2O3 + Y2O2S/Y2O2S-YP复合化合物,促进了钢液异质形核,细化了凝固组织;枝晶间形成了Y2Fe14Si3化合物。随Y含量增加,枝晶内和枝晶间稀土化合物含量逐渐提高,基体有序度明显降低。
(2) 在500℃、1 s-1和40%压下量的单轴压缩条件下,含Y试样加工软化阶段对应的加工硬化率和临界应变降低,动态软化作用增强。随Y含量提高,压缩试样的裂纹数量减少,裂纹总长度减小。压缩试样的芯部出现晶内变形带,变形机制由位错滑移主导。
(3) 随Y含量增加,热压缩试样的基体位错密度逐渐提高,基体有序度下降和形变诱导无序作用的增强是含Y试样动态软化作用增强的主要原因。
来源--金属学报