分享:压水堆主回路高温水中奥氏体不锈钢加工表面的腐蚀与应力腐蚀裂纹萌生:研究进展及展望
奥氏体不锈钢是制造压水堆主回路部件的重要结构材料。奥氏体不锈钢在压水堆核电站中的服役整体表现优异,但服役过程中仍然发生过应力腐蚀开裂事故。发生冷变形是奥氏体不锈钢部件出现应力腐蚀开裂事故的主要原因,而切削加工及加工表面的后处理是在部件表面引入冷变形的主要工艺过程。本文基于过去20年本领域国内外相关研究结果,综述了切削加工等工艺在奥氏体不锈钢表面引入的塑性变形区的显微组织与残余应力特征,以及表面变形对奥氏体不锈钢在压水堆主回路高温水环境中的腐蚀及应力腐蚀裂纹萌生行为影响的研究进展。基于这些研究,指出了不锈钢应力腐蚀裂纹萌生研究中存在的问题、可能的解决办法,并对其他亟待开展的研究做了展望。
关键词:
奥氏体不锈钢具有材料成本低、加工性好以及耐高温水腐蚀等特点,被广泛用于压水反应堆主回路各类部件的制造[1,2]。压水堆主回路高温水出口温度约为325℃,反应堆运行期间也会严格控制高温水中杂质的含量,但不锈钢等结构材料在高温水中暴露时依然会发生腐蚀。除了受到高温水腐蚀之外,部件在服役过程中还会承受复杂的应力,在堆芯中服役的构件还会面临强烈的中子辐照,因此主回路中材料服役环境恶劣。压水堆堆芯的不锈钢构件在服役过程中会发生辐照促进应力腐蚀开裂[3],其他不受中子辐照的奥氏体不锈钢部件服役整体表现优异[1,4]。然而在20世纪90年代以后,相关核电运营商,如法国电力集团,在做例行检查时发现多个不受辐照的不锈钢部件在服役过程中也发生了应力腐蚀开裂[5~7]。美国电力研究所的研究人员对各国压水堆核电站主回路不锈钢部件中发生的137起应力腐蚀开裂事件进行了统计分析,结果显示,约83%的应力腐蚀开裂事件的发生是由部件附近区域水循环不畅,导致杂质如Cl-、SO42-以及O的含量升高引起[8,9]。在其他水循环良好的区域,不锈钢部件发生应力腐蚀开裂的主要原因是其发生了冷变形[7]。此后,相关实验室的结果[6,10~12]也进一步证实,在水化学符合规范且循环良好的高温水环境中,冷变形是压水堆主回路中奥氏体不锈钢发生应力腐蚀开裂的必要条件。
反应堆部件上的冷变形多是在其制造过程中有意或无意引入的,有意引入冷变形主要是为了引入缺陷以提高材料强度[13]。而在反应堆部件制造与装配过程中,一些无法避免的制造工艺(焊接、切削加工等)则会无意间在部件的局部引入冷变形[4,14,15]。其中,焊缝熔池在凝固过程中会在其热影响区引入冷变形与拉伸残余应力。相关研究[16,17]显示,不锈钢焊缝热影响区冷变形的变形量为10%~20%。部件的切削加工及加工表面的后处理工艺,如磨抛、喷丸等,也总是会在部件表面引入冷变形[18]。表面是部件与高温水接触的最前沿,因此部件的切削加工及加工表面的后处理工艺都会对其腐蚀和应力腐蚀开裂行为有重要影响[18,19]。相关统计结果[6]也显示,压水堆核电站不锈钢部件中的应力腐蚀开裂多发生在部件表面硬度较高的区域。针对压水堆高温水环境中不锈钢的应力腐蚀开裂行为机制问题,相关核电制造商、核电站运营商和研究机构在过去20余年间开展了大量的研究[20~27]。从2015年至今,以铣削这一典型的切削工艺为例,作者[15,28~33]在不锈钢的加工表面状态、在高温水中的腐蚀与应力腐蚀裂纹萌生以及加工表面状态优化等方面也开展了一系列有针对性的研究。
本文基于过去20年本领域的相关研究,综述了典型表面加工制造工艺在奥氏体不锈钢表面引入的变形区的组织性能特征、表面变形对不锈钢在压水堆主回路高温水环境中的腐蚀及应力腐蚀裂纹萌生行为影响的研究进展。此外,指出了目前研究存在的一些问题、可能的解决办法,并对其他亟待开展的研究做了展望。
1 表面加工/加工表面后处理引起的变形与残余应力
1.1 切削加工诱发变形层的显微组织与残余应力
切削加工引入的塑性变形区的厚度主要取决于材料的强度和切削工艺[15,28,30]。对于奥氏体不锈钢,切削加工引入的变形层的厚度一般在几十到一两百微米之间,而变形层在切削表面的深度方向通常具有梯度的显微组织特征(图1a[15])。前期工作[15,29,30,32,33]显示,使用相近参数铣削的316L与304L不锈钢的表面变形层深度在50~100 μm之间,而经过低温锻造/轧制后的304L与316L不锈钢的变形层深度为15~30 μm。低温锻造/轧制的不锈钢变形层较薄的主要原因是,材料强度显著升高(退火不锈钢室温屈服强度为200~300 MPa,低温锻造/轧制不锈钢室温屈服强度为500~700 MPa[15,31]),导致铣削加工过程中的阻力增大。
图1
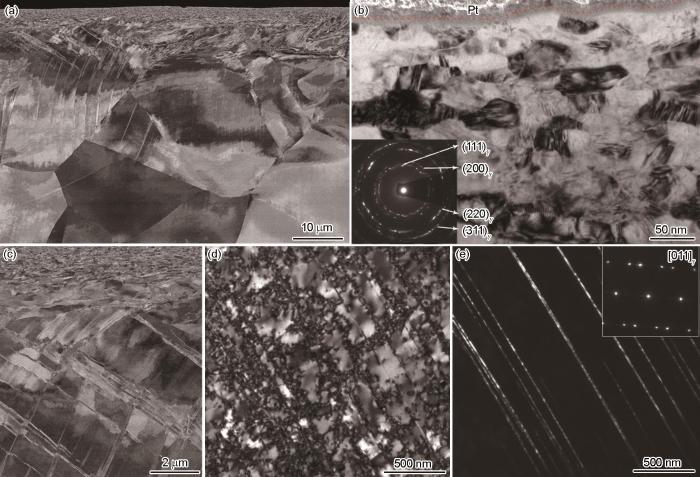
Fig.1 Back-scattered electron (BSE) image of the machined layer of austenitic stainless steels (ASSs) (a)[15]; bright field-transmission electron microscopy (BF-TEM) image and corresponding selected area electron diffraction (SAED) pattern (inset) of the topmost ultrafine-grained layer (b)[32]; BSE image showing the details of the twins-intersected region (c)[15]; BF-TEM image (d) and dark field-TEM (DF-TEM) image (e) of the deformation twins (Inset in Fig.1e shows the SAED pattern)[32]
切削表面的正下方通常是一个厚度为几微米的高度变形的纳米晶/超细晶层(图1a[15]和b[32])。细晶层下方区域显微组织特征为变形孪晶、变形孪晶的交叉(图1c[15]、图1d[32]和图1e[32])。而随着与表面距离的增加,变形层显微组织会由多个方向且发生弯曲的变形孪晶交叉逐渐演化为单个方向的变形孪晶,变形孪晶的密度也随之逐渐减小(图1a和c[15])。此外,奥氏体不锈钢在变形过程中会有发生马氏体转变的倾向,但切削加工过程中材料的升温会抑制马氏体转变。作者[32]在研究304L和316L不锈钢的铣削加工变形层时未发现马氏体。然而也有例外,如Zhang等[36]在车削加工304不锈钢的变形层中发现了大量马氏体。
切削加工变形层中的残余应力与材料强度、切削参数以及切削过程中的冷却条件有关[15,24,37],残余应力在加工表面的深度方向一般呈梯度分布。切削引起的剧烈塑性变形使材料的强度和硬度显著提升,因此切削表面的残余应力有时会显著高于基体材料的屈服强度[35],但其会在深度方向急剧下降,从而与所在区域的强度相匹配。相关研究结果[37]显示,退火316L不锈钢经过铣削后,其表面上的残余应力达到400~1000 MPa,且垂直进刀方向的残余应力一般大于进刀方向的残余应力。铣削加工在冷轧或温锻的不锈钢上引入的残余应力通常低于在退火的不锈钢上引入的残余应力[28,32],这可能与加工变形层较薄有关。切削加工表面的拉伸残余应力在样品的深度方向会逐渐降低、演化成压缩残余应力,最后趋于无应力,见图2[38]。
图2

1.2 切削加工细化晶粒的作用机制
在对铣削不锈钢的变形层进行显微组织观察时,发现其表层超细晶区与孪晶交叉区之间通常会存在一个明显的界面(图1a和c[15])。切削加工过程中,刀具与材料发生剪切作用会引起材料升温。根据相关的模拟结果[39],切削过程中变形层中的温度呈梯度分布并呈指数下降。基于这些结果,作者认为,切削引起的材料剧烈塑性变形和温度升高共同作用诱发了近表面区域的动态再结晶,在近表面区域形成了纳米晶/超细晶层。然而,切削带来的剪切作用不会在细晶层发生完全再结晶后就即刻停止。而之后引入的变形由于变形量较小,不足以再次诱发再结晶,最终被保留在晶粒内部。超细晶/纳米晶层下方区域材料硬度和强度升高,主要原因是这些区域发生了孪晶变形,一定程度上细化了晶粒。Zhang等[24]、Wang等[25]和Das等[40]在铣削316L不锈钢上,以及Yan等[41]在车削304L不锈钢上观察到的结果也与作者的观察基本一致。切削加工在不锈钢表面引入塑性变形的同时也提高了变形层的强度,反映在变形层硬度显著高于基体[32,41,42]。
1.3 其他表面处理引入的变形与残余应力
除切削加工外,其他表面加工或加工表面后处理工艺,如机械磨抛[22]、砂纸磨抛[21,26,29,43,44]、机械喷丸、水喷丸[22,45]等都会在不锈钢表面引入冷变形与残余应力,其中砂纸磨抛在不锈钢表面引入的变形层的显微组织如图3[29,43]所示。然而,相对于切削加工,机械磨抛等工艺在不锈钢表面引入的变形层的厚度通常较小,显微组织也略有不同。作者[29]以及Iaffré等[43]的结果显示,砂纸磨抛在不锈钢表面引入的变形层的顶层具有纳米晶结构,晶粒尺寸比切削加工引入的更细,但纳米晶层的厚度只有几百纳米(图3[29,43])。Ming等[45]的结果显示,水喷丸在冷轧316L不锈钢表面引入变形层的近表面区域的显微组织为沿着表面拉长的纳米晶。然而,Kaneda等[22]则发现,水喷丸只会在退火不锈钢的表面引入纠缠的位错,不会引入纳米晶和变形孪晶。不同研究人员获得的实验结果有所不同可能与具体使用的工艺不同有关。相比水喷丸,机械喷丸会在材料中引入与铣削加工相似的纳米晶层和变形孪晶,同时变形层更厚[22]。水喷丸与机械喷丸都会在不锈钢表面引入压缩残余应力,残余应力大小受原材料的表面状态和喷丸工艺影响。对于水喷丸工艺,喷丸前材料的表面硬度越高,则喷丸能引入的压缩残余应力越大。这是因为,材料中存在残余应力的本质是其局部区域存在弹性变形,强度/硬度高的材料中能够存在比强度低的材料中更大的残余应力。相比铣削和机械喷丸,水喷丸不能引起材料的剧烈塑性变形和晶粒细化,因此水喷丸引入的压缩残余应力的大小就受限于喷丸前材料的强度。
图3
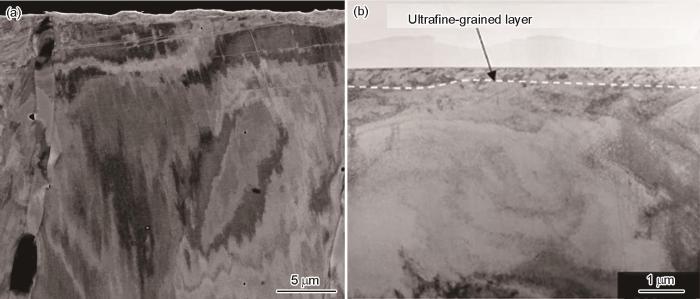
2 表面变形对不锈钢电化学特性及腐蚀行为的影响
2.1 不锈钢在高温水中的腐蚀及主要影响因素
在空气中,不锈钢的表面会形成一层厚度为几纳米、能够阻止材料与环境进一步接触和交互作用的致密钝化膜,该钝化膜的主要成分为斜方结构的Cr2O3[46,47]。当不锈钢暴露在高温水中之后,其在空气中形成的表面钝化膜就不能稳定存在,而会转变为具有尖晶石结构的双层氧化物[46]。不锈钢在高温水中暴露后形成的氧化物的典型形貌特征如图4a和b[30]所示。不锈钢在高温水中形成的外层氧化物为含少量Ni的Fe3O4,形态上为离散的晶体且之间有空隙,因此不具有保护基体的功能(图4a和b[30])。内层为连续的富Cr、Fe的尖晶石结构的氧化层,为多晶或纳米晶且相对比较致密(图4c和d[30])。不锈钢在高温水中形成的内层氧化物能有效隔绝高温水与基体材料,从而显著降低其腐蚀速率[48]。根据Ziemniak和Hanson[48]建立的模型,不锈钢在高温水中的腐蚀速率在动力学上服从抛物线规律。在高温水环境中,有多种因素影响不锈钢的腐蚀速率及其表面形成的氧化物的形貌特征,主要有:材料的成分(特别是Cr含量)[49,50]、水化学、材料的显微组织特征[51]、承受的应力状态[30,51]、内氧化层晶粒尺寸以及致密程度[48]等。
图4

图4 退火态316L不锈钢的抛光及铣削表面在高温水中形成的氧化物的表面形貌及其截面组织[30]
Fig.4 Surface morphologies (a, b) and cross-sectional microstructures (c, d) of the inner/outer oxide layers formed on the polished surface (a, c) and machined surface (b, d) of an annealed 316L stainless steel in simulated pressurized water reactor (PWR) primary water[30]
2.2 表面变形影响不锈钢腐蚀的规律及机理
众多研究[15,23,25,30,52]表明,在水化学符合规范的模拟压水堆主回路高温水中,无论是退火还是冷变形状态的不锈钢,其切削加工或机械磨抛表面的腐蚀速率都会明显高于抛光表面。切削加工或其他表面处理引入的近表面变形会影响氧化物的形貌特征,但不会改变其晶体结构。Ziemniak等[23]发现,通过电解抛光将304L不锈钢的铣削加工变形层去除一部分之后,其在260℃高温水中腐蚀速率降低30%以上。Ziemaniak等[23]认为,电解抛光后不锈钢腐蚀速率降低的主要原因是其去除了表面的不均匀变形层,使不锈钢在高温水中氧化更加均匀、形成的内氧化层更加致密,最终降低了离子在内氧化层中的传输速率。而Han等[52]以及Das等[40]的研究结果显示,不锈钢电解抛光过程中会在表面形成一层纳米级的富Cr层,引入富Cr层被认为是电解抛光降低不锈钢在高温水中腐蚀速率的另一个原因。
其他研究者[25,41]在研究铣削、车削表面以及抛光表面在高温水中形成的氧化层形貌特征时也得到了类似的结果。不同工艺铣削的316L不锈钢表面的变形层厚度与残余应力虽有差异,但铣削表面在高温水中形成的外层氧化物的尺寸与密度、内层氧化物的厚度都远高于退火316L不锈钢的抛光表面(图4a和b[30]),其中铣削表面的内氧化层厚度比抛光表面高50%~60% (图4c和d[30])。显微组织观察结果显示,退火态316L不锈钢表面形成的内氧化层在靠近基体以及靠近外氧化层界面的区域有相对较多的孔洞(图5a[30])。此外,其内氧化层的选区电子衍射(SAED)花样表现为不均匀的衍射环(图5c[30])。利用(004)面衍射环的亮斑对内氧化层进行中心暗场成像时,发现在内氧化层中存在一些择优生长的柱状晶粒(图5b[30])。与抛光表面不同,铣削表面上形成的内氧化层的晶粒为随机取向的纳米晶,内氧化层的SAED花样分布相对均匀(图5d和e[30])。然而,在内氧化层的整个深度方向,特别是靠近金属基体和外氧化层的界面区域存在较多孔洞(图5d[30])。此外,利用高角度环形暗场扫描透射电子显微镜(HAADF-STEM)观察内氧化层与基体界面区域时,还发现内氧化层下方的超细晶区的晶界会被优先氧化(图5f[30])。基于这些结果,作者认为铣削加工提高不锈钢在高温水中腐蚀速率的作用机制主要有2个:(1) 铣削加工在不锈钢表面引入高度变形的纳米晶显微组织,促进了Fe、Cr元素在高温水中的氧化反应;(2) 变形层中的纳米晶氧化后形成的内氧化层晶粒细小且多孔,促进Fe2+和OH-在内氧化层中的运输。
图5
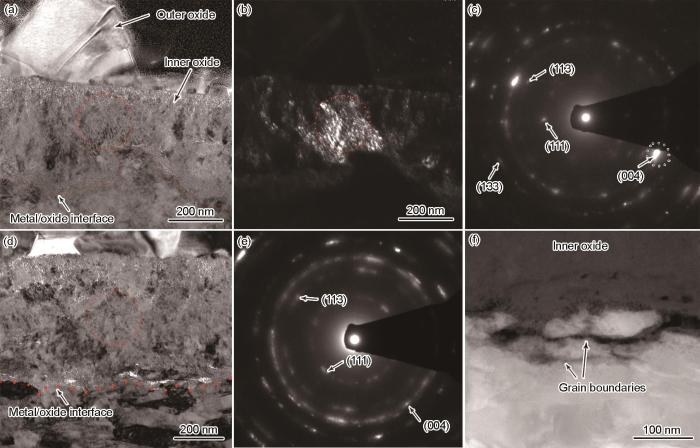
图5 退火316L不锈钢的抛光和铣削表面在高温水中形成的氧化层的显微组织[30]
Fig.5 BF-TEM (a) and DF-TEM (b) images of the oxide layers formed in the polished surface, and BF-TEM image of the oxides formed on the machined surface of annealed 316L stainless steel in PWR primary water (d); SAED patterns obtained from the circled regions in Figs.5a and b (c) and Fig.5d (e), respectively; and high angle annular dark field-scanning TEM (HAADF-STEM) image showing intergranular oxidation of the ultrafine-grains in the machined surface (f)[30]
切削加工改变不锈钢近表面区域的显微组织,从电化学的角度来看,显微组织的改变会改变材料的钝化膜(内氧化层)的形成过程以及膜的稳定性。Das等[53]利用双环电化学动电位再活化实验、恒电位阳极极化实验,研究了304L不锈钢铣削加工变形层不同深度区域的钝化膜稳定性。此外,还基于电化学阻抗实验和Mott-Schottky模型计算了铣削表面超细晶层以及基体在硼酸盐缓冲液中形成的钝化膜的阳离子空位密度。结果显示,铣削加工表面的超细晶层、细晶层下方的变形孪晶层的再活化能要远高于基体材料,且再活化能在变形层深度方向逐渐降低。基于电化学阻抗实验以及Mott-Schottky模型的计算结果[53]显示,铣削加工表面的超细晶层在硼酸盐缓冲液中形成的钝化膜的阳离子空位密度是未发生变形的基体的1.8倍以上,因此该钝化膜保护材料的作用大幅度降低。
3 表面变形对应力腐蚀裂纹萌生的影响
3.1 不锈钢应力腐蚀开裂发生的条件
应力腐蚀开裂一般可分为裂纹萌生与扩展2个阶段。通常认为,应力腐蚀裂纹在萌生之前还会存在一个很长的孕育期,裂纹的孕育过程主要受材料或部件的表面状态和腐蚀行为的影响,而裂纹一旦萌生就会在拉伸应力的作用下以较快的速率扩展,如图6[19]所示。1997年之后,法国电力集团在其运行的压水堆核电站不锈钢部件上一共发现了9起应力腐蚀开裂事件,有7起发生在服役6 a后的部件中,其中5起发生在部件服役13 a之后[6]。此后,相关研究人员便在实验室模拟的高温水环境中开展不锈钢的应力腐蚀开裂行为机制的研究。恒定载荷拉伸实验是与反应堆实际运行工况条件最为接近的应力腐蚀裂纹萌生实验方法。然而相关结果[6,27]显示,在高温水环境中,使用恒定载荷拉伸实验很难在较短时间内使不锈钢表面萌生裂纹。而为了更好地研究不锈钢应力腐蚀开裂的行为机制,就需要使用能在相对较短时间内促进应力腐蚀裂纹萌生的其他加速实验方法。在不改变水化学的前提下,慢应变速率拉伸(slow train rate tensile,SSRT)实验是迄今为止最有效的不锈钢应力腐蚀裂纹萌生加速实验方法。根据经验[12,32],在符合规范的模拟压水堆主回路高温水中,以10-7~10-8 s-1的名义应变速率在样品中引入3%~4%的塑性变形可以有效地促进冷变形不锈钢萌生沿晶应力腐蚀裂纹。相似的实验条件也可用于冷变形或辐照后的镍基合金的应力腐蚀裂纹萌生研究[54~56]。
图6

3.2 退火及冷变形不锈钢在SSRT实验条件下的应力腐蚀裂纹萌生
退火态不锈钢的应力腐蚀裂纹萌生敏感性极低。作者[15,33]的研究结果显示,在300℃高温水中,以1.6 × 10-8~2.0 × 10-8 s-1的名义应变速率,在退火的316L及304L不锈钢板状拉伸样品中引入约4%的塑性变形,只会在样品的内氧化层中引入少量裂纹,且裂纹都会在内氧化层的内部停止,如图7a[15]所示。然而,也有研究人员[57~59]在SSRT实验过程中将样品拉伸至断裂,并通过比较不同样品的延伸率或断口上沿晶断裂百分比的方法来定性评价不同材料的应力腐蚀开裂敏感性。在将退火态不锈钢样品通过SSRT拉伸至断裂后,通常都会在样品断口附近发现沿晶断裂特征。然而,作者认为这些样品中发生应力腐蚀开裂的主要原因是其在SSRT过程中发生了冷变形,发生冷变形的样品在后续的SSRT过程中满足了应力腐蚀裂纹萌生的条件,因此这并不代表这些退火态的不锈钢对应力腐蚀开裂敏感。此外,也有研究人员[55]发现,退火不锈钢的紧凑拉伸样品在裂纹扩展实验过程中会出现沿晶应力腐蚀裂纹。然而其裂纹扩展速率比冷加工状态的不锈钢要低1~2个数量级[60],这也从侧面说明退火状态不锈钢的应力腐蚀开裂敏感性极低。
图7

图7 慢应变速率拉伸(SSRT)实验条件下退火态316L不锈钢内氧化层中出现的裂纹[15],冷轧316L不锈钢中萌生的沿晶应力腐蚀裂纹[28],以及冷轧316L不锈钢沿晶裂纹边缘晶界上的滑移台阶[65]
Fig.7 Cracks in the inner oxide layer of an annealed 316L stainless steel (a)[15], and intergranular stress corrosion crack initiated in cold-rolled 316L stainless steel during slow train rate tensile (SSRT) test (b)[28]; slip steps at the crack flank in cold-rolled 316L stainless steel sample (c)[65]
在SSRT实验条件下,冷变形不锈钢易萌生应力腐蚀裂纹已被广泛证实[6,31,61]。这主要有3个原因:(1) 冷变形过程中形成的形变孪晶、位错平面滑移在晶界上停止,导致晶界应力应变集中[62];(2) 冷变形引起的晶界附近的应力应变集中会促进晶界的氧化[50,51];(3) 冷变形提高了材料强度,导致材料在SSRT加载过程中承受更大的拉伸应力。在室温或者几百摄氏度对不锈钢进行轧制、锻造是研究不锈钢等材料应力腐蚀开裂行为时常用的冷变形工艺,常用的变形量在10%~30%之间[60,63,64]。在SSRT实验条件下,冷变形不锈钢萌生的应力腐蚀裂纹以沿晶模式为主(图7b[28])。在极少数情况下,如沿晶裂纹扩展到三叉晶界附近时,沿晶裂纹会转变为穿晶模式,但裂纹在扩展到下一个晶界时通常都会转变为沿晶模式。在开裂的晶界上,除了能观察到少量细小氧化物之外,通常都能观察到晶内变形产生的滑移台阶(图7c[65])。晶界表面的滑移台阶在SSRT样品以及紧凑拉伸试样的断口上都非常普遍[32,60,63]。样品在加载过程中发生的滑移与择优氧化的晶界之间的交互作用也是促进裂纹萌生和扩展的重要因素。
3.3 加工表面在SSRT条件下的应力腐蚀裂纹萌生
根据前期结果[15],不锈钢铣削表面在高温水中会形成多孔、具有纳米晶粒显微组织的内氧化物层(图5d[30])。内氧化物层在SSRT过程中会产生裂纹并扩展到基体表面,并将基体暴露到高温水中。当铣削表面的残存纳米晶/超细晶暴露在高温水中之后,纳米晶/超细晶的晶界会发生择优氧化,氧化的晶界在拉伸应力作用下破裂,从而萌生微小裂纹[15]。表面细晶层中萌生的裂纹随后会在拉伸应力的作用下扩展到变形孪晶层之中。在对拉伸到4%左右塑性变形的铣削样品的观察中发现,铣削纹理与拉伸方向垂直的样品,其表面在SSRT过程中更容易萌生应力腐蚀裂纹,且裂纹一般会沿着加工纹路方向扩展(图8a[15])。在铣削316L不锈钢样品表面观察到的裂纹最大深度为3.5 μm,且所有裂纹都会在变形孪晶区域内停止(图8b[15])。表面纳米晶/超细晶层的晶界在高温水中会优先发生氧化[32],因此作者认为超细晶内的裂纹以沿晶裂纹为主。然而,当裂纹扩展到超细晶层下方的变形孪晶层之后,其扩展方式则转变为穿晶,并随着变形层硬度的降低最终停止扩展(图8b[15])。
图8
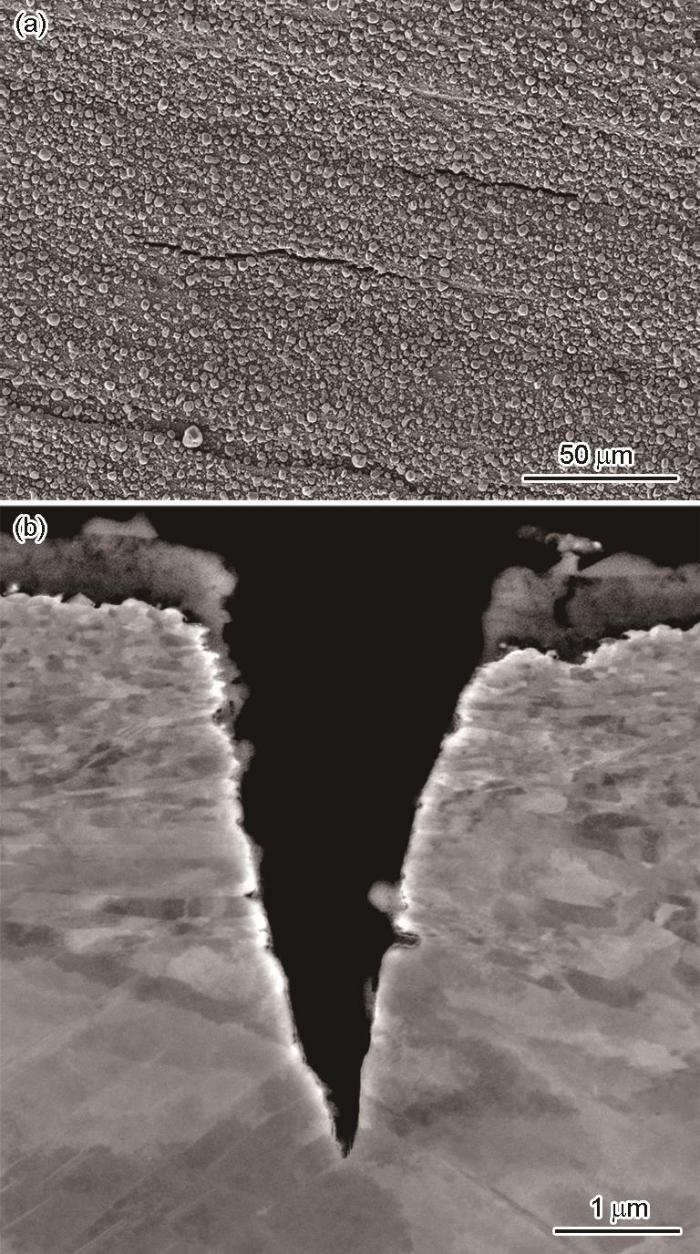
铣削对冷变形不锈钢的应力腐蚀裂纹萌生行为的影响与退火态材料不同[29,32,33]。研究结果[29,32,33]显示,在SSRT实验过程中,冷变形不锈钢样品铣削表面上萌生的裂纹的数量以及裂纹深度都远小于其抛光表面,如图9a和b[32]所示。由于存在高度变形的纳米晶/超细晶层,样品的铣削表面在实验过程中要承受远高于抛光表面的拉伸应力。因此,该实验现象也说明,在一定条件下,材料的显微组织特征在应力腐蚀裂纹萌生中起着比拉伸应力更大的作用。如3.2节所述,冷变形不锈钢在SSRT过程中易萌生应力腐蚀裂纹的主要原因是,其晶界在高温水中容易被氧化并在拉伸应力作用下破裂。冷变形不锈钢的铣削表面上虽然也存在高度变形的超细晶层,但大量超细晶的晶界的氧化在一定程度上会促进铣削表面相对均匀地氧化,从而延缓冷变形粗晶晶界的选择性氧化及裂纹萌生。因此,铣削表面超细晶层的存在会一定程度上提高冷变形不锈钢的应力腐蚀裂纹萌生抗力[28~30,32]。
图9

图9 温锻304L不锈钢的抛光及铣削表面在SSRT实验条件下萌生的裂纹及裂纹扩展路径[32]
Fig.9 Stress corrosion crack initiation in the polished (a) and machined (b) surfaces of a warm-forged 304L stainless steel during SSRT test (Inset in Fig.9b shows the magnified image of rectangle area); a crack propagated transgranularly (c) and a crack branched and then propagated both intergranularly and transgranularly after penetrating beyond the topmost ultrafine-grained layer (d)[32]
4 优化表面状态降低不锈钢应力腐蚀裂纹萌生敏感性的相关研究
综上,表面变形对不锈钢的应力腐蚀裂纹萌生有很大的影响。应力腐蚀裂纹的萌生有很长的孕育期,通过优化表面状态就有可能延长其孕育期,从而降低材料的裂纹萌生敏感性。前期结果[30,32]显示,铣削加工引入的纳米晶/超细晶能促进材料均匀氧化,从而延缓冷变形不锈钢的应力腐蚀裂纹萌生。然而,随着在高温水中暴露时间/实验时间增加,铣削表面最终会萌生应力腐蚀裂纹。主要原因是,铣削表面形成的高度变形超细晶层在拉伸残余应力以及高温水腐蚀的共同作用下,易被腐蚀并萌生裂纹。研究结果[28]显示,在650℃惰性气体保护环境中对铣削的冷变形316L不锈钢样品进行短时间热处理,能诱发其表面超细晶的回复与部分再结晶,从而降低表层的硬度和残余应力。同时,该热处理制度不会引起冷变形316L不锈钢的基体和变形层的敏化。在SSRT实验条件下,热处理后冷变形不锈钢铣削表面的应力腐蚀裂纹密度降低了40%,如图10[28]所示。此外,该热处理也不会改变不锈钢表面氧化物的成分与结构,以及裂纹扩展路径。
图10

图10 热处理前、后冷轧316L不锈钢表面的铣削超细晶层的HAADF-STEM像及表面萌生的应力腐蚀裂纹[28]
Fig.10 HAADF-STEM images of the ultrafine-grains in the machined layer of cold-rolled 316L stainless steel before (a) and after (c) heat treatment, and the surface stress corrosion cracks initiated on the machined surfaces during SSRT test before (b) and after (d) heat treatment (Cracks were colored in red in Figs.10b and d)[28]
5 使用SSRT研究加工表面应力腐蚀裂纹萌生行为的不足及可能的解决方案
SSRT是目前压水堆高温水环境中不锈钢、镍基合金等材料应力腐蚀裂纹萌生研究中最常用的加速实验方法。SSRT加速裂纹萌生的主要作用机制是:(1) 实验在样品的塑性变形阶段进行,因此使材料承受比屈服强度更大的载荷;(2) 实验过程中不断地引入塑性变形,样品变形过程中产生的滑移带会促进晶界应力应变集中;(3) 晶粒滑移与氧化的晶界发生交互作用,导致氧化物破裂。然而,SSRT实验也有其本征缺陷。反应堆部件通常在远低于其屈服强度的载荷下服役,因此SSRT实验条件与部件实际服役工况有较大差异,如图11所示。这就导致通过SSRT获得的实验结果不一定能够反映部件在真实服役工况下的应力腐蚀裂纹萌生行为。对于切削加工或通过其他方法进行表面处理的不锈钢样品,通过SSRT实验也不能获得加工引入表面残余应力对应力腐蚀裂纹萌生行为的影响规律。
图11
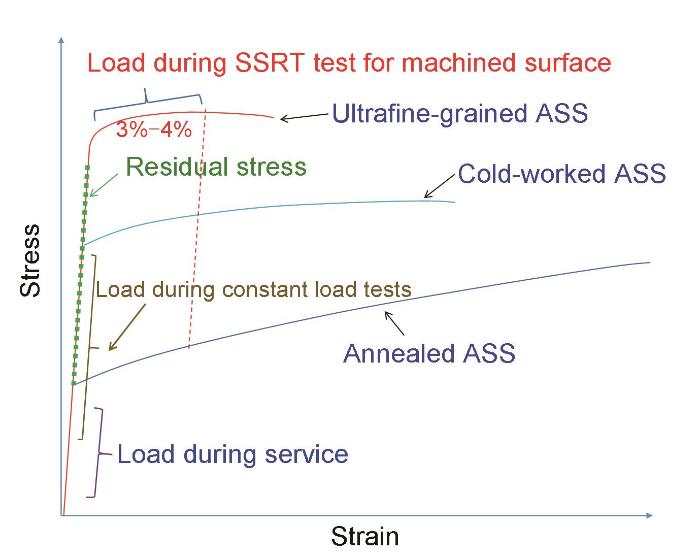
图11 反应堆工况、恒定载荷及慢应变速率拉伸实验过程中材料受力示意图
Fig.11 Schematic of the load that material bears during plant operation, constant load testing, and SSRT testing
对整体变形的材料,在裂纹萌生更快的环境中开展恒定载荷实验,或在高温水中开展长时间的恒定载荷实验,并建立实验结果与SSRT条件下获得的实验结果的关联,是解决SSRT条件下的实验结果与实际工况中材料应力腐蚀裂纹萌生行为偏差的可行办法。对于前者,需要保证在该环境中材料的腐蚀与应力腐蚀裂纹萌生行为机制不变。Volpe等[68~70]在高温H2与H2O蒸汽混合气体环境中开展了镍基合金氧化与应力腐蚀裂纹萌生行为的探索性研究,并取得了一些与高温水中相似的实验结果。高温H2与H2O蒸汽环境能有效加速材料的氧化与应力腐蚀裂纹萌生,该环境可能也适合于奥氏体不锈钢的应力腐蚀裂纹萌生的加速。而在高温水中开展长时间的恒定载荷实验,需要大量人员和时间的投入。近年来,Zhai等[71~73]在恒定载荷实验条件下开展了一系列镍基合金应力腐蚀裂纹萌生行为的研究,实验方法及相关结果都值得不锈钢应力腐蚀裂纹萌生行为研究借鉴。此外,基于现有实验室结果,综合考虑材料在不同加载条件下的应力与变形的变化从而开展计算模拟,也有可能为这个问题提供新的解决方案。
对于有表面变形层的材料,恒定载荷实验也不一定适合研究加工引入的残余应力对材料应力腐蚀裂纹萌生行为的影响规律。这是因为,外加恒定载荷也会改变变形层中的残余应力状态。而在一些腐蚀性较强的介质中开展静态暴露实验,获得的结果则具有一定的参考价值。如Zhang等[24]在高温MgCl2溶液中对有不同残余应力的不锈钢铣削表面进行暴露。结果发现,只有当铣削表面的残余应力大于190 MPa时,样品在暴露过程中才会萌生应力腐蚀裂纹,且裂纹密度随残余应力增大而增大。Zhang等[74]也尝试了在添加0.001% Cl-的300℃高温高压水中研究铣削引入的残余应力与外加应力共同作用下不锈钢的应力腐蚀裂纹萌生行为。结果显示,在相当于恒定载荷实验的条件下,部分样品在高温水中暴露3600 h之后会萌生裂纹,但裂纹的萌生受加载方向与垂直方向应力的共同影响。在添加Cl-的高温水中通过恒定载荷拉伸实验获得的结果,能反映反应堆回路中高温水流通不畅的区域部件的应力腐蚀裂纹萌生行为。
6 总结与展望
奥氏体不锈钢是制造核电部件的重要结构材料,其在压水堆主回路高温水中的服役表现整体优异。然而,自20世纪末在一些压水堆核电站的不锈钢部件中发现应力腐蚀开裂事件之后,不锈钢的应力腐蚀开裂问题也得到了越来越多的关注。部件的切削加工及加工表面的后处理会改变不锈钢的表面状态,对不锈钢部件在高温水中的腐蚀与应力腐蚀裂纹萌生有重要影响。对不锈钢加工表面状态、腐蚀及应力腐蚀裂纹萌生行为的深入认识,对部件的长期安全服役与寿命管理都具有重要的意义。
过去20余年,包括作者在内的研究人员针对不锈钢表面状态、在高温水中腐蚀和应力腐蚀裂纹萌生行为等问题开展了一些研究工作。通过多尺度的显微组织与残余应力表征,明确了典型切削加工工艺、磨抛、喷丸等表面后处理工艺在材料表面引入的塑性变形与残余应力特征;通过高温水环境中的静态暴露以及应力加载实验,明确了不同表面状态不锈钢的腐蚀行为及在SSRT等加速实验条件下的应力腐蚀裂纹萌生行为;在认识应力腐蚀裂纹萌生行为规律的基础上,找到了一些能够降低不锈钢加工表面应力腐蚀裂纹萌生敏感性的方法。这些研究有效地推动了这一研究领域的进步。
然而,不锈钢加工表面的腐蚀与应力腐蚀裂纹萌生研究中仍存在一些问题需要解决,一些与部件制造和服役相关的研究也亟待开展,例如:
(1) 在水化学符合规范且循环良好的压水堆主回路高温水环境中,不锈钢萌生应力腐蚀裂纹的条件极为苛刻,目前只有SSRT实验能够在相对较短的时间内在冷变形不锈钢中引发应力腐蚀裂纹的萌生。然而,SSRT会在样品中引入塑性变形,改变不锈钢表面变形层中的显微组织与残余应力状态。因此,利用SSRT无法研究加工引入的残余应力对材料应力腐蚀裂纹萌生的影响规律。即使对于整体变形的材料,SSRT条件下材料的应力腐蚀裂纹萌生行为与反应堆真实工况下也必然存在差异,建立2者之间的有机联系才能使SSRT实验及相应结果被广泛接受。本文中对这个问题进行了讨论并对解决办法给出了建议。
(2) 对一些具体的现象,不同研究结果存在差异。例如,多数研究显示,切削、磨抛等表面加工/处理在不锈钢表面引入的变形会加速其在高温水中的腐蚀,但也有一些研究结果显示,表面磨抛会降低不锈钢的腐蚀速率。加强研究人员之间的沟通和合作,最终能在这些问题上获得共识。
(3) 此前报道的研究,多是在加工工艺得到较好控制条件下获得的材料表面上开展的,然而,实际部件的表面由于各种因素的影响,可能会存在如划伤、沾污、氧化等缺陷。开展这些有缺陷的实际表面的腐蚀与应力腐蚀开裂行为研究,对实际部件的服役与寿命管理非常重要。
(4) 文中提及的研究,多为在水化学符合规范条件下开展的,实际上,反应堆运行以及检修等环节都有可能在高温水中带来杂质离子。在高温水流动不畅的区域,这些离子浓度会显著升高,影响材料的腐蚀与应力腐蚀裂纹萌生。在高温水中有意添加杂质离子,如Cl-和SO42-等,并开展相关的实验是未来研究中的重要方向。
(5) 切削加工等工艺决定了部件的表面状态,从而影响部件的腐蚀与应力腐蚀裂纹萌生行为。切削加工等工艺也会一定程度上影响部件的制造成本与制造效率。然而,全世界目前对于核电部件在实际制造中使用的切削工艺与其在高温水中的腐蚀、应力腐蚀裂纹萌生行为之间关联的研究仍然缺乏,对部件表面状态的评价也缺乏合理的标准。通过核电装备设计、制造以及研究机构之间的合作交流,不断提升对不锈钢等核电部件的表面状态与服役行为的认识,在此基础上不断完善部件表面评价标准,是解决核电部件制造工艺技术与安全服役问题并促进核电制造技术发展最有效的方法。