分享:激光熔化沉积TiB2 增强TiAl基合金涂层的组织及力学性能
采用激光熔化沉积在TC4合金表面制备出不同TiB2含量(0、10%、20%、30%,质量分数)的TiAl基合金涂层,利用XRD、OM、SEM、显微硬度计、压痕法(断裂韧性)、磨损试验机以及激光共聚焦显微镜等,系统研究了TiB2含量对涂层微观组织与力学性能的影响。结果表明,涂层组织由底部沿厚度方向依次为平面晶、柱状晶和等轴晶,随着TiB2含量增加,柱状晶高度逐渐降低。TiB2/TiAl复合涂层由TiAl合金基体相(γ + α2)以及TiB2增强相组成,直接添加的TiB2颗粒大多没有熔化,但直接添加的TiB2颗粒外层与TiAl合金熔体发生溶解反应后原位析出初生TiB2和次生TiB2,初生TiB2呈块状,次生TiB2呈短棒状和条带状。随着TiB2含量由0增加至10%,涂层基体组织明显细化,但继续增加TiB2含量(20%、30%)并未产生进一步的细化作用。随着TiB2含量由0增加至30%,涂层的表面硬度由530.5 HV增加至738.4 HV,断裂韧性由7.75 MPa·m1/2降低至3.17 MPa·m1/2,磨损率由3.98 mg/mm2减少至0.42 mg/mm2,并且磨损面的磨损程度及其粗糙度也随之降低。未添加TiB2时,涂层的磨损机制以显微切削为主,多次塑性变形为辅;TiB2含量为10%时,涂层的磨损机制以显微切削为主,微观断裂为辅;随着TiB2含量增加,磨损机制逐渐转向微观断裂;TiB2含量为30%时,涂层的磨损机制以微观断裂为主,显微切削为辅。
关键词:
TiAl基合金(TiAl基金属间化合物)具有低密度、高比强度、耐腐蚀、优异的抗氧化以及抗蠕变等特性,是一种极具竞争力的新型轻质高温结构材料,在航空航天、汽车工业等领域的应用潜力巨大[1,2]。然而TiAl基合金的室温和高温脆性大,难以加工成形,是限制其作为结构材料大规模推广应用的主要瓶颈[3]。值得注意的是,采用表面工程技术在基材表面制备TiAl基合金涂层,即能充分发挥TiAl基合金的性能优势,显著提高基材表面耐高温、耐腐蚀等性能,又能克服TiAl基合金加工困难的问题,是一种有效的应用途径。目前制备TiAl基合金涂层的方法主要有:磁控溅射[4]、离子注入[5]、等离子喷涂[6]、电火花沉积[7]等。上述方法虽然拓展了TiAl基合金的应用领域,但也存在自身的局限性:磁控溅射和离子注入制备的涂层只能达到微米级,仅适合精密零件;等离子喷涂制备的涂层存在孔隙、夹杂、微裂纹等缺陷,并且与基材为机械结合,结合力较低;电火花沉积层的表面质量不易控制,工艺不稳定,生产效率尚有待提高。激光熔化沉积作为一种先进的表面强化技术,具有稀释率低、组织致密且细小、基材变形小、涂层与基材结合强度高、粉末成分容易调节等优点[8],因此采用激光熔化沉积制备TiAl基合金涂层具有重要的研究价值和广阔的应用前景。Carrullo等[9]利用激光熔化沉积在TC4合金表面制备出Ti-48Al-2Nb-2Cr (原子分数,%)合金涂层,涂层的高温抗氧化能力相较于基材提高10倍。
随着TiAl基合金激光沉积涂层应用的逐步开展,将不可避免地涉及到润滑、摩擦和磨损等问题。但是,TiAl基合金涂层的耐磨性能较差,难以在恶劣、复杂的工况条件下长期服役[10],因此提高TiAl基合金涂层的耐磨性能显得尤为重要。在TiAl基合金中引入硬质相可以有效提高材料的耐磨性能以及力学性能。例如,He等[11]通过在TiAl基合金中添加TiC硬质相的方法,显著提高了合金的硬度和耐磨性。众所周知,TiB2陶瓷硬质相具有硬度高、摩擦系数低、化学稳定性好等特点,并且TiB2与TiAl基合金具有相近的密度和热膨胀系数以及良好的相容性[10],同时B元素又能显著细化TiAl基合金的晶粒尺寸,因此TiB2是TiAl基合金复合材料中最具吸引力的硬质相之一。Cheng等[12]采用粉末冶金法制备TiB2/TiAl复合材料,随着TiB2含量增加,其耐磨性能也随之增加。然而截止目前,关于激光熔化沉积制备TiB2/TiAl基合金复合材料的研究尚未见报道,因此本工作以Ti-48Al-2Nb-2Cr合金作为基体材料,利用激光熔化沉积在TC4合金表面制备TiB2增强TiAl基合金复合涂层,为进一步探索TiAl基合金复合材料在表面工程中的应用提供理论参考和实验范例。
1 实验方法
沉积材料由Ti-48Al-2Nb-2Cr预合金粉末和TiB2颗粒组成,混合粉末中TiB2的加入量分别为0、10%、20%、30% (质量分数)。Ti-48Al-2Nb-2Cr预合金粉末采用电极感应熔炼气雾化法制备,形状主要为球形(见图1a),粒径范围53~150 μm;TiB2颗粒为不规则的块状(见图1b),粒径范围45~75 μm。基材为TC4合金,基材表面经砂纸逐级打磨后,用无水酒精和丙酮清洗以去除油污。实验前将混合均匀的复合粉末以及基材放入100℃的干燥箱中烘干0.5 h,去除水分。
图1

图1 TiAl合金粉末和TiB2颗粒的SEM像
Fig.1 SEM images of TiAl powders (a) and TiB2 particles (b)
激光熔化沉积设备由六轴联动机器人、IPG-YLS-6000光纤激光器、DPSF-2双筒四路同轴送粉器、控制系统以及水冷系统等组成,其中IPG-YLS-6000光纤激光器的最大功率6 kW,波长1070 nm,保护气和送粉气均为高纯Ar气,沉积参数为:激光功率1400 kW,扫描速率5 mm/s,送粉率15.6 g/min,送粉气流量为7 L/min,保护气流量为15 L/min,预热温度为350℃。
用线切割切取金相试样,试样经磨光、抛光、Kroll试剂腐蚀后,在GX51型金相显微镜(OM)上分析涂层形貌。采用GeminiSEM 300型扫描电子显微镜(SEM)观察试样的微观组织,并使用能谱仪(EDS)对涂层微区成分进行分析。物相结构分析在D8 Advance型X射线衍射仪(XRD)上完成。使用EM500-2A型显微硬度计测量涂层截面的硬度分布,载荷500 g,持续时间10 s,同一深度的区域随机选取3个点,取平均值。采用Vickers硬度压痕法在涂层截面上诱发裂纹,载荷为30 kg,通过测量裂纹长度间接计算涂层的断裂韧性[13]:
式中,KIC为断裂韧性(MPa·m1/2),HV为Vickers硬度(N/mm2),FV为载荷(N),??L为4个压痕尖角的裂纹总长度(mm)。通过
涂层的二体磨粒磨损实验在ML-100型销盘式磨损试验机上进行,试样直径3 mm,载荷7 N,转速120 r/min,进给量2 mm/r,磨损时间5 min,对磨材料为80 μm砂纸。使用FA2004型电子天平(精度0.1 mg)精确测量磨损失重量,同一成分涂层共进行3次磨损实验,以磨损率评价涂层的耐磨性能:
式中,ω为磨损率(mg/mm2),m0为磨损前的质量(mg),m1为磨损后的质量(mg),s为磨损面积(mm2)。
采用Quanta650型扫描电镜(SEM)观察磨损形貌,分析磨损机理;采用VL2000DX-SVF17SP型3D激光共聚焦显微镜表征磨损表面的三维形貌,并计算粗糙度。
2 实验结果与分析
2.1 涂层的物相结构
图2为不同TiB2含量涂层的XRD谱。TiAl合金涂层主要由γ-TiAl相以及α2-Ti3Al相组成。添加TiB2后,复合涂层由TiAl合金基体相(γ + α2)以及TiB2相组成,在XRD的测试精度内没有发现其他物相。随着TiB2含量增加,TiB2衍射峰的强度逐渐增加,基体相(γ + α2)衍射峰的强度逐渐减弱,这说明TiB2含量增加,致使基体相(γ + α2)的相对含量不断降低。
图2

图2 不同TiB2含量涂层的XRD谱
Fig.2 XRD spectra of coatings with different TiB2 contents
2.2 涂层中部的微观组织
由TiAl合金涂层中部的OM像(图3a)和背散射电子像(图3b)可以看出,其微观组织为树枝晶,由白色枝晶组织和灰色枝晶间组织构成。添加TiB2颗粒后(图4),复合涂层的微观组织由TiAl合金基体相和不同形态的第二相组成,基体组织由粗大的树枝晶转变为尺寸较小的等轴晶,晶粒尺寸明显细化,第二相形态主要包括尺寸不同的块状(尺寸在20~75 μm之间的大块标记为A,尺寸在2~10 μm之间的小块标记为B)、短棒状(标记为C)以及弯曲的条带状(标记为D),并且随着TiB2含量增加,第二相数量也逐渐增加。对上述第二相分别进行EDS分析,结果见表1。综合EDS和XRD结果(图2)可知,这些第二相为TiB2。大块TiB2的尺寸(20~75 μm)和形状接近原始颗粒,这说明在激光沉积条件下直接添加的TiB2颗粒大多没有熔化。TiB2颗粒的熔点(3225℃)和熔化焓(83.94 kJ/mol)均较高,在激光束短暂的辐射过程中难以被迅速熔化。但是直接添加的TiB2颗粒的外层可以与TiAl合金熔体发生溶解反应[14]:TiAl合金熔体(L) + β + TiB2↔L + β (0.5%TiB2,1485℃),L + TiB2 ↔ L (1%TiB2,1600℃),使得溶解出来的Ti和B进入熔体。B在TiAl合金中的固溶度极低,在γ相和α相中的固溶度分别为0.011%和0.003%[15] (原子分数,后文所有元素含量均为原子分数),所以B在TiAl合金中大多以硼化物的形式存在,主要包括TiB和TiB2。TiAl合金中硼化物的类型与Al含量密切相关,当Al含量≤ 44%时,形成TiB,随着B含量增加,硼化物由TiB逐渐向TiB2过渡,当Al含量> 44%时,仅形成TiB2[16]。本工作采用的TiAl合金属于后一种情况,因此TiB2颗粒发生溶解反应后再次析出的硼化物为TiB2。综上所述,块状(2~10 μm)、短棒状及条带状TiB2从尺寸和形貌上都明显区别于直接添加的TiB2颗粒,因此可以推断其为“溶解-再析出”机制下原位合成的产物。
图3
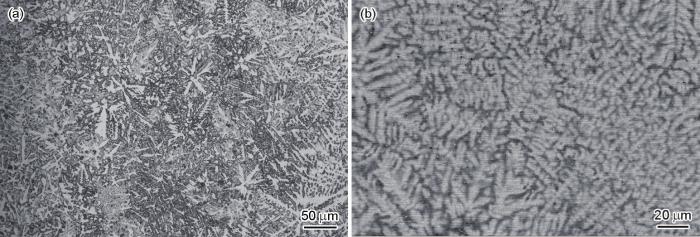
图3 TiAl合金涂层中部的显微组织
Fig.3 OM (a) and back-scaterred electron (BSE) (b) images of middle region of the TiAl alloy coating
图4

图4 不同TiB2含量涂层截面中部的背散射电子像
Fig.4 Low (a-c) and high (d-f) magnified BSE images of middle region of coatings with 10% (a, d), 20% (b, e), and 30% (c, f) TiB2
表1 图4复合涂层中第二相的EDS结果 (atomic fraction / %)
Table 1
Mass fraction of TiB2 / % |
Position | Ti | B* |
---|---|---|---|
10 | A | 20.82 | 79.18 |
B | 18.74 | 81.26 | |
C | 15.76 | 84.24 | |
D | 14.99 | 85.01 | |
20 | A | 15.87 | 84.13 |
B | 17.75 | 82.25 | |
C | 16.84 | 83.16 | |
D | 15.81 | 84.19 | |
30 | A | 14.73 | 85.27 |
B | 15.44 | 84.56 | |
C | 17.69 | 82.31 | |
D | 16.14 | 83.86 |
TiB2为六方晶系,在理想状态下生长成以(0001)为底面、{1010}为棱面的六棱柱状形貌[17]。而本工作所得原位生成TiB2的形态呈现块状、短棒状及条带状,这主要归因于Ti-Al-B合金的成分以及激光熔化沉积的快速凝固过程。本工作所选基体合金的初生相为β相,其凝固路径为[18]:L → L + β → α → α + γ → α2 + γ。根据Ti-Al-B三元相图液相面的部分投影图[16]可知,Ti-Al-B合金熔体在降温过程中会发生共晶反应:L → β + TiB2,由于本工作所选基体合金的Al含量为48%,因此平衡条件下基体合金发生上述共晶反应的B含量大致为1%。在实际凝固过程中,TiB2/TiAl复合涂层激光熔池中总是存在成分起伏、结构起伏以及能量起伏。由前文可知,直接添加的TiB2颗粒外层会与TiAl合金熔体发生溶解反应,释放出的B原子不断进入TiAl合金熔体。凝固初期,由于熔体中B含量较高,并且B在TiAl合金熔体中扩散能力较差,极易在固/液界面前沿富集[19],此时容易析出初生TiB2。这些形核较早的初生TiB2晶核具有较长的生长时间,并且周围的温度梯度、溶质条件等动力学因素较为稳定,生长环境近似自由生长,其生长形态主要由TiB2的晶体结构决定,因此生长成近似六棱柱状形貌,其断面呈块状(图4中的B)。随着凝固的进行,B原子不断被消耗,当B含量降低至1%时,发生共晶反应L → β + TiB2,析出次生TiB2,次生TiB2与基体β相共同耦合生长,其生长受到β相的限制,最终形成短棒状(图4中的C)和条带状(图4中的D)。研究[16]表明,在快速冷却条件下,TiAl合金中的TiB2多呈现弯曲的条带状,因此涂层中条带状TiB2的出现与激光熔化沉积的快速凝固过程也密不可分。综上所述,TiB2/TiAl复合涂层中TiB2的析出路径为:L→L +初生TiB2→初生TiB2 + β +次生TiB2,在此路径下,初生TiB2在熔池中自由生长,呈现块状;熔池中剩余的B原子以次生TiB2的形式与β相共同耦合生长,呈现短棒状和条带状。
对比TiAl合金组织(图3b)和TiB2/TiAl复合涂层的基体组织(图4a~c)可以看出,随着TiB2含量由0增加至10%,复合涂层中部的基体组织由粗大的树枝晶转变为尺寸较小的等轴晶,晶粒明显细化,但继续增加TiB2含量(20%、30%)并未产生进一步的细化作用。Han等[20]在研究真空电弧炉制备不同含量TiB2的TiAl合金时也发现类似现象,并认为TiB2对TiAl合金的细化作用存在一个阈值,当TiB2含量低于阈值时,没有明显的细化作用,当TiB2含量超过阈值时,晶粒细化明显,但TiB2含量继续增加对晶粒的影响不大。分析认为,本工作中TiB2颗粒细化TiAl合金的机制主要包括:(1) TiB2与β相之间的错配度为11%,TiB2作为β相异质形核核心的有效性为中等[21]。未熔化的TiB2以及初生TiB2领先于β相存在于熔池中,在凝固过程中可以有效提高β相的形核率,起到细化晶粒的作用。(2) 次生TiB2与β相共同耦合生长,次生TiB2对β相的长大具有阻碍作用,进一步细化了晶粒。(3) B在TiAl合金熔池中缓慢的扩散速率以及B在固、液两相中溶解度的差异,导致B容易在固/液界面前沿产生成分过冷[19],并在固/液界面前沿聚集形成富B的边界层,该边界层能够阻碍β相晶粒长大,进而细化组织。
2.3 涂层界面附近的微观组织
图5为不同TiB2含量涂层界面附近的OM像。可以看出,4种涂层的组织致密,未发现裂纹、气孔等冶金缺陷,基材与涂层之间存在一条连续的白亮结合带,结合带下方为TC4合金基材的热影响区,上方为涂层的柱状晶区,基材与涂层实现了良好的冶金结合。由于激光熔化沉积特殊的快速加热、快速冷却特点,涂层组织形态呈现明显快速凝固生长特征,由底部沿厚度方向依次为平面晶、柱状晶和等轴晶。根据凝固理论[22],涂层的组织形态受控于温度梯度(G)与生长速率(R)之比(G / R)。熔池底部,由于基材的激冷作用,使得G极大,但该处的瞬时R趋近于零,因此G / R极大,晶体以稳定的平面状态生长,进而形成平面晶;随着凝固的进行,熔池的G逐渐减小,R逐渐增大,G / R逐渐降低,并且溶质元素富集导致成分过冷区域不断扩大,致使组织形态逐渐转变为柱状晶甚至等轴晶。
图5
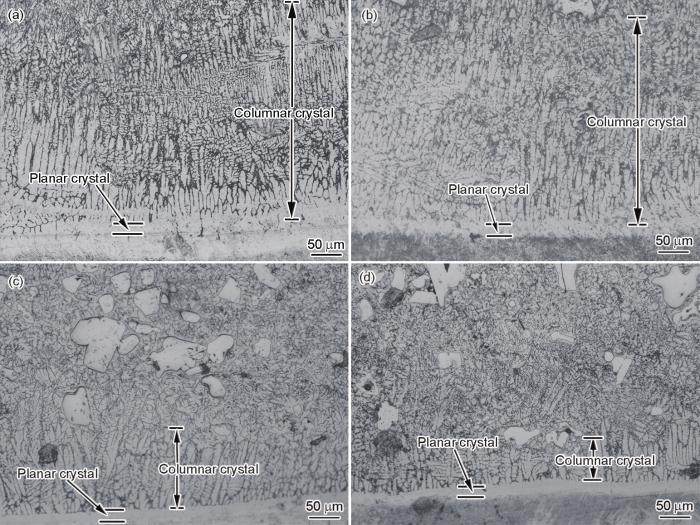
图5 不同TiB2含量涂层界面附近的OM像
Fig.5 OM images near the interface of coatings with different TiB2 contents
(a) 0 (b) 10% (c) 20% (d) 30%
由图5还可以看出,随着TiB2含量增加,界面附近柱状晶高度逐渐降低。究其原因:(1) 随着TiB2含量增加,未熔化的TiB2以及初生TiB2数量增加,异质形核作用增强,等轴晶数量上升。当大量等轴晶位于柱状晶前沿时,能够阻碍柱状晶生长,促进柱状晶转变为等轴晶[23]。(2) 随着TiB2含量增加,熔池中B含量升高,使得液相中更多的B被排斥到固/液界面前沿,造成溶质浓度增加,成分过冷区域扩大,晶体自由生长能力增强,以致柱状晶不能持续长大而在尖端出现分叉,逐渐转变为等轴晶。(3) 随着TiB2含量增加,涂层与基材间的G减小,G / R降低,弱化了柱状晶的生长趋势。激光沉积过程中涂层与基材间的G可以表示为[24]:
式中,K为材料的热导率,T为熔体的液相线温度,T0为基材温度,η为激光吸收率,P为激光功率。随着TiB2含量增加,在相同工艺参数下熔化相同厚度涂层所需要的激光能量降低,使得熔池温度上升,T0也随之升高,进而导致G降低(
2.4 TiB2 含量对涂层显微硬度的影响
图6为不同TiB2含量涂层截面显微硬度分布曲线。可见,硬度由涂层至基材呈现阶梯式分布,分别对应涂层、热影响区以及基材。随着TiB2含量增加,涂层硬度逐渐增加,其中表面硬度由530.5 HV增加至738.4 HV。分析认为,其强化机理主要包括:(1) Orowan强化,不同形态的TiB2分布在TiAl合金基体上可以阻碍位错运动,导致位错在增强相附近形成堆积和缠结,使得位错开动的外应力增加,硬度得以提高;(2) 细晶强化,添加TiB2颗粒后,基体合金的晶粒明显细化。依据Hall-Petch效应,晶粒越小,晶界越多,合金硬度也越高。此外,从图6可以看出,TiB2/TiAl复合涂层的硬度均出现一定幅度的波动,而TiAl合金涂层的硬度却相对平稳,这主要归因于TiB2在复合涂层深度方向上分布的不均匀。
图6

图6 不同TiB2含量涂层截面的显微硬度
Fig.6 Microhardness distributions of coatings with different TiB2 contents
2.5 TiB2 含量对涂层断裂韧性的影响
图7为载荷30 kg下不同TiB2含量涂层压痕的形貌。压痕裂纹长度采用IPP软件进行统计,并利用
图7
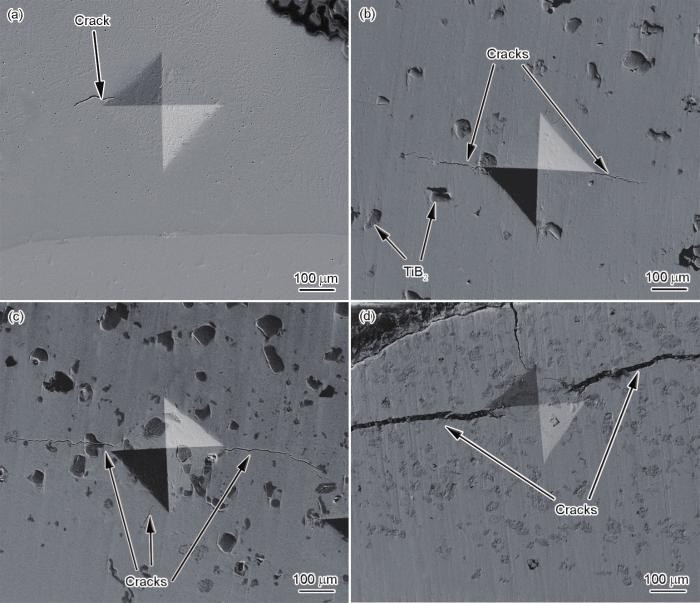
图7 不同TiB2含量涂层的压痕形貌
Fig.7 Indentation morphologies of coatings with different TiB2 contents
(a) 0 (b) 10% (c) 20% (d) 30%
表2 不同TiB2含量涂层的断裂韧性(压痕法)
Table 2
Mass fraction of TiB2 / % | Average crack length / mm | Fracture toughness / (MPa·m1/2) |
---|---|---|
0 | 0.195 | 7.75 |
10 | 0.545 | 5.02 |
20 | 1.204 | 3.49 |
30 | 1.672 | 3.17 |
2.6 TiB2 含量对涂层耐磨性的影响
2.6.1 TiB2含量对磨损率的影响
图8为不同TiB2含量涂层的磨损率。可见,随着TiB2含量增加,涂层的磨损率逐渐降低。未添加TiB2时,涂层中不含硬质相,无法有效阻碍磨粒的切削作用,耐磨性较差,磨损率高达3.98 mg/mm2。随着TiB2含量增加,涂层中硬质相数量增加,硬质相在二体磨粒磨损过程中可以充当耐磨骨架的作用,有效抵抗磨粒的切削作用,耐磨性能显著提高,TiB2含量为30%时,涂层的磨损率降低至0.42 mg/mm2,仅为TiAl合金涂层磨损率的11%,展现出优异的耐磨性能。
图8

图8 不同TiB2含量涂层的磨损率
Fig.8 Wear rates of coatings with different TiB2 contents
2.6.2 TiB2含量对磨损机制的影响
图9为不同TiB2含量涂层的磨损形貌。图9a为TiAl合金涂层的磨损形貌,磨损面存在大量连续平行且深而宽的犁沟,部分犁沟边缘出现层状折痕(如箭头所示),这说明涂层以显微切削为主,多次塑性变形为辅。当磨粒以滑动方式划过合金表层时,由于涂层硬度较低且没有硬质相的保护,磨粒在压应力与切应力的共同作用下,容易在涂层表面产生推挤变形和碾压变形,形成犁沟状磨损划痕。此外,由于磨粒的反复磨损与加载,材料的加工硬化效应不断增加,当材料无法通过塑性变形吸收能量时便会诱发裂纹,在随后的磨损过程中裂纹扩展导致材料脱离磨损面产生磨屑,同时在犁沟边缘形成层状折痕,层状折痕是多次塑性变形后的典型形貌。
图9

图9 不同TiB2含量涂层的磨损形貌
Fig.9 Wear morphologies of coatings with different TiB2 contents
(a) 0 (b) 10% (c) 20% (d) 30%
对比图9b~d可以发现,随着TiB2含量增加,犁沟的数量、深度以及宽度逐渐减小,犁沟边缘并未出现层状折痕,但磨损面均出现剥落坑,这表明TiB2/TiAl复合涂层的磨损机制为显微切削和微观断裂,而不存在多次塑性变形。上述剥落坑的尺寸和形状接近未熔化的TiB2颗粒,并且数量随着TiB2含量的升高而增加,这说明磨粒磨损条件下产生的剥落坑与未熔化的TiB2颗粒密切相关。为了探明剥落坑是否归因于未熔化TiB2颗粒的断裂或剥落,对磨粒磨损条件下出现的剥落坑进行高倍SEM观察,如图10所示。可见,剥落后的区域形成了较深的孔洞,未发生剥落的表面没有明显划痕,也未发生塑性变形,断口为平整的小平面(I处)。对未发生剥落的表面(I处)进行EDS分析发现,其具体成分(原子分数)为:Ti 23.23%,B 76.77%。综上可以判定剥落坑的产生主要归因于未熔化TiB2颗粒与基体的剥离,少数是由于颗粒本身的脆性断裂。TiB2的硬度和耐磨性均大于基体,基体率先被磨损,导致TiB2凸出于基体,在后续的磨损过程中充当耐磨骨架的作用。首先,未熔化的TiB2颗粒是直接添加进去的,与基体的界面处存在较多缺陷,结合强度较低,在磨损过程中容易在界面处诱发微裂纹,导致未熔化的TiB2与基体发生剥离形成剥落坑,而原位析出的TiB2与基体的界面纯净,且存在固定的取向关系,结合强度较高[20],在磨损的过程中很难发生剥离。其次,未熔化的TiB2颗粒为硬脆相,在磨粒反复的磨削作用下,容易萌生微裂纹,裂纹扩展后发生脆性断裂形成剥落坑。
图10

图10 磨粒磨损条件下产生的剥落坑的高倍形貌
Fig.10 High power morphology of the spalling pit produced by abrasive particles under abrasive conditions
研究[26]表明,材料发生显微切削磨损时,磨损率与硬度呈负相关,磨损率与硬度之间的关系为[26]:
式中,WC为显微切削造成的磨损率,FN为载荷,θ为圆锥形磨粒尖角角度的一半,
式中,WF为微观断裂造成的磨损率,d为磨粒直径。
综上所述,TiB2/TiAl复合涂层的磨粒磨损过程是显微切削和微观断裂共同作用的结果,复合涂层由于TiB2含量的不同而导致其硬度和断裂韧性有所差异,因此2种磨损机制所占权重也不同。TiB2含量为10%时,涂层具有低硬度、高断裂韧性的特点,因而磨损机制以显微切削为主,微观断裂为辅;随着TiB2含量增加,涂层硬度增加,断裂韧性降低,因此显微切削造成的磨损减少,微观断裂造成的磨损增加,磨损机制转向微观断裂;TiB2含量为30%时,涂层的磨损机制以微观断裂为主,显微切削为辅。
由前文分析可知,TiB2含量是决定复合涂层耐磨性的关键因素。其原因是:(1) 硬度是衡量耐磨材料的一项重要指标,拥有更高硬度的材料通常具有更优异的耐磨粒磨损性能[26],随着TiB2含量增加,涂层硬度逐渐增加,使得磨粒难以刺入复合涂层表面进行犁削运动,磨损程度随之降低;(2) TiB2具有较高的硬度和耐磨性,镶嵌在基体上可以阻碍磨粒的压入与切削,承担主要的载荷,起到耐磨骨架的作用,避免大量磨粒与基体的直接接触,降低2者之间的接触面积,减少磨粒对基体的磨损。TiB2的耐磨骨架作用与其平均间距密切相关。当TiB2含量较低时,TiB2的平均间距大于磨粒尺寸,磨粒容易刺入合金表面,进行长距离的犁削运动,形成大量深而宽的犁沟,随着TiB2含量增加,其分布更加均匀,平均间距也进一步减小,使得磨粒难以刺入合金表面,即使部分锋利且迎角合适的磨粒刺入合金表面,在其犁削一段距离后便会遇到坚硬的TiB2,迫使其离开犁沟,从而抑制犁沟的进一步扩展,显著降低磨损率。
2.6.3 TiB2含量对磨损面粗糙度及其三维形貌的影响
利用3D激光共聚焦显微镜观察涂层磨损后的表面形貌,并计算粗糙度Ra和Rz,用于表征磨损程度(其中,Ra为轮廓算术平均偏差粗糙度,反映轮廓偏离基准面的程度,常用于表示表面粗糙度;Rz为轮廓微观不平度10点高度,即测量范围内5个最大轮廓谷深yvi与5个最大轮廓峰高ypi的平均值之和,反映轮廓的最大高度[28])。一般而言,Ra和Rz数值越小,说明磨损表面越光滑,磨损程度越小。不同TiB2含量涂层的Ra和Rz见图11。可以看出,TiB2含量为0时,Ra和Rz最大,分别达到3.797和77.256 μm,磨损程度最为严重;随着TiB2含量增加,Ra和Rz数值逐渐减小,磨损程度逐渐降低,TiB2含量为30%时,Ra和Rz分别降低至2.067和19.110 μm,磨损程度最小,与前文磨损实验结果相吻合。
图11

图11 不同TiB2含量涂层磨损表面的粗糙度
Fig.11 Roughnesses of wear surface of coatings with different TiB2 contents (Ra—contour arithmetic mean deviation, Rz—ten-point height average)
为了更加直观地反映磨损形貌,采用3D激光共聚焦显微镜对磨损表面的三维形貌进行表征,结果见图12。红色代表磨损轮廓的峰高区域,蓝色代表磨损轮廓的谷深区域,颜色差异越大,表示磨损程度越严重。可见,随着TiB2含量增加,磨损面的颜色差异逐渐减小,磨损程度逐渐降低,这说明复合涂层中的TiB2可以有效抵抗磨粒的切削作用,显著提升TiAl合金的耐磨性能。
图12

图12 不同TiB2含量涂层磨损表面的3D形貌
Fig.12 3D morphologies of wear surface of coatings with different TiB2 contents
(a) 0 (b) 10% (c) 20% (d) 30%
3 结论
(1) 采用激光熔化沉积在TC4合金表面成功制备出TiB2/TiAl复合涂层,涂层组织形态由底部沿厚度方向依次为平面晶、柱状晶和等轴晶,随着TiB2含量增加,柱状晶高度逐渐降低。
(2) TiB2/TiAl复合涂层由TiAl合金基体相(γ + α2)以及TiB2增强相组成,直接添加的TiB2颗粒大多没有熔化,但直接添加的TiB2颗粒外层与TiAl合金熔体发生溶解反应后原位析出初生TiB2和次生TiB2,其析出路径为:L→L +初生TiB2→初生TiB2 + β + 次生TiB2,初生TiB2在熔池中自由生长,呈现块状,次生TiB2与β相进行耦合生长,呈现短棒状和条带状。
(3) 随着TiB2含量由0增加至10%,涂层中部的基体组织由粗大的树枝晶转变为尺寸较小的等轴晶,晶粒明显细化,但继续增加TiB2含量(20%、30%)并未产生进一步的细化作用。
(4) 随着TiB2含量由0增加至30%,涂层的表面硬度由530.5 HV增加至738.4 HV,断裂韧性由7.75 MPa·m1/2降低至3.17 MPa·m1/2,磨损率由3.98 mg/mm2减少至0.42 mg/mm2,并且磨损面的磨损程度及其粗糙度也随之降低。
(5) 未添加TiB2时,涂层的磨损机制以显微切削为主,多次塑性变形为辅;TiB2含量为10%时,涂层的磨损机制以显微切削为主,微观断裂为辅;随着TiB2含量增加,磨损机制逐渐转向微观断裂;TiB2含量为30%时,涂层的磨损机制以微观断裂为主,显微切削为辅。
来源--金属学报