分享:金属激光增材制造材料设计研究进展
宋波, 张金良, 章媛洁, 胡凯, 方儒轩, 姜鑫, 张莘茹, 吴祖胜, 史玉升,
激光增材制造被公认为是解决个性化、复杂化金属构件整体成形难题的有效技术手段。现有金属增材制造的研究主要从传统合金牌号出发,但基于平衡凝固过程设计的传统合金成分难以满足增材制造的非平衡冶金动力学特点,往往面临高裂纹敏感性、低韧低疲劳、各向异性等共性问题。因此,需要开展面向激光增材制造的新型材料成分设计研究,充分挖掘增材制造非平衡凝固特性的潜在优势与价值。本文综述了铝合金、钛合金、铁基合金、镁合金等不同材料现有合金牌号增材制造的技术瓶颈,以及面向增材制造的材料创新设计方法与新型合金及其复合材料发展的研究进展。最后提出了金属增材制造材料设计的未来发展趋势。
关键词:
金属激光增材制造(laser additive manufacturing,LAM)可制造出结构复杂、晶粒细小的高性能金属构件,但由于其独特的冶金热、动力学特点,仍面临一些共性问题,限制了LAM构件的进一步发展与应用。(1) 低韧、低疲劳[3,4]:非平衡凝固过程赋予了基体较高的过饱和度,合金元素固溶于基体中,产生晶格畸变;且快冷使得构件表现出较高的残余应力,降低了材料的塑性和疲劳性能。(2) 各向异性[5]:由于激光移动的方向性及熔池内较大的温度梯度,金属材料组织与性能往往表现出各向异性。(3) 高裂纹敏感性[6~8]:LAM高残余应力和柱状晶大大提高了裂纹敏感性,典型代表为锻造铝合金、镍基高温合金及TiAl、NiTi等金属间化合物。此外,目前国内外铝合金增材制造研究主要从传统合金牌号出发,基于平衡凝固过程设计的传统合金成分难以满足LAM的冶金动力学特点,物相组成与传统热加工方法差异显著,LAM的构件综合性能往往不及锻件。因此,需要开展面向LAM的新型合金成分设计研究,充分挖掘增材制造极端非平衡凝固特性的潜在优势与价值。目前,针对冶金缺陷抑制和组织性能调控的目标,材料成分改性与设计在新型合金开发上已取得了阶段性进展,初步解决了LAM金属材料的难成形难题和组织调控问题。但目前金属材料设计与改性方法十分单一,元素含量和种类的确定大多根据经验摸索或大量工艺验证,少有材料成分设计理论与方法的研究。
本文首先概述不同金属材料现有合金牌号增材制造的技术瓶颈与发展现状,针对上述技术难点,归纳报道面向增材制造的各类金属材料创新设计方法与新型合金发展的研究进展,最后提出金属增材制造材料设计的未来研究趋势。
1 LAM技术
金属增材制造采用激光、电子束和电弧等离子弧为热源[2]。LAM技术的主要优势在于激光热源适用材料范围广、能量密度高、成形精度高等。LAM主要包括基于粉末床的选区激光熔化(selective laser melting,SLM)技术和基于同步送粉的激光熔覆沉积(laser cladding deposition,LCD)技术,成形原理示意图分别如图1a和b所示。2种成形技术均有各自的特点和应用对象。SLM技术成形精度相对较高,但成形尺寸受到打印设备的限制,适用于小型金属构件的成形[9]。而LCD技术使用没有成形腔限制,激光能量高,成形效率更高,但尺寸精度较低,不适用于成形尺寸精度要求较高的精密构件。此外,LCD可以根据受损零件空缺部分的形状模型,以损伤零件为基体直接进行沉积,实现零件的快速修复[10]。
图1

2 LAM金属材料设计
2.1 铝合金
铝合金可分为铸造铝合金和锻造铝合金。与铁、钛合金相比,LAM铝合金的难点在于[6]:(1) 较高的激光反射率和热导率,成形时热量累积少;(2) 易氧化;(3) 铝合金粉末吸水性强,易产生氢气孔;(4) 热膨胀系数和凝固温度范围较高,快速凝固时产生的应力导致开裂、变形;(5) 铝合金中往往含有Mg元素和其他一些低熔点化合物,在激光作用下易造成合金成分的波动和烧损,影响材料成形质量与力学性能。
目前,铝合金增材制造的研究多集中在AlSi7Mg、AlSi10Mg及AlSi12等铸造Al-Si合金。这是由于上述Al-Si合金的成分处于共晶点附近,结晶时温度范围较小,不易开裂[11]。而锻造铝合金具有极高的裂纹敏感性,难以通过LAM获得理想的显微组织和力学性能。通过对铝合金成分改性与设计,成功解决了上述难题。美国的HRL (Hughes Research Laboratory)实验室[12]在LAM过程中引入控制凝固的ZrH2纳米颗粒,成形时原位生成的细小Al3Zr颗粒可作为形核剂诱导形成等轴晶组织,最终制备出高抗拉强度的6061和7075合金。这种Zr/Sc改性的方法为高裂纹敏感性锻造铝合金的LAM提供了重要的思路,已经成为了新型锻造铝合金成分设计的主要手段。例如,Zhang等[13]采用2%Zr (质量分数,下文若非单独说明,均代表质量分数)改性Al-Cu-Mg合金,与改性前相比,工艺窗口显著拓宽,抗拉强度为450 MPa,但延伸率仅为3%。当Zr含量降低到0.6%时,Zr改性Al-Cu-Mg合金的延伸率提高到11%以上,抗拉强度也达495 MPa[14]。Li等[15]设计了一种新型合金Al-8.0Mg-1.3Si-0.5Mn-0.5Sc-0.3Zr,最终抗拉强度和延伸率分别达到497 MPa和11%。时效处理后,抗拉强度达到550 MPa,延伸率在8%~17%之间。Jia等[16]报道了一种高强度Al-Mn-Sc合金(Al-4.52Mn-1.32Mg-0.79Sc-0.74Zr-0.05Si-0.07Fe),所开发的合金具有较高的热稳定性,经300℃热处理后,屈服强度达560 MPa,延伸率为18%。如图2[17]所示,Zhang等[17]通过裂纹敏感因子、生长抑制因子及相图等热力学计算,发现Ti元素改性铝合金也可显著促进细小等轴晶的形成,并计算出最优Ti添加量为1.5%,为面向增材制造的合金成分设计提供了理论指导。Ti改性后的2xxx铝合金抗拉强度可达426 MPa,延伸率为9.1%。
图2
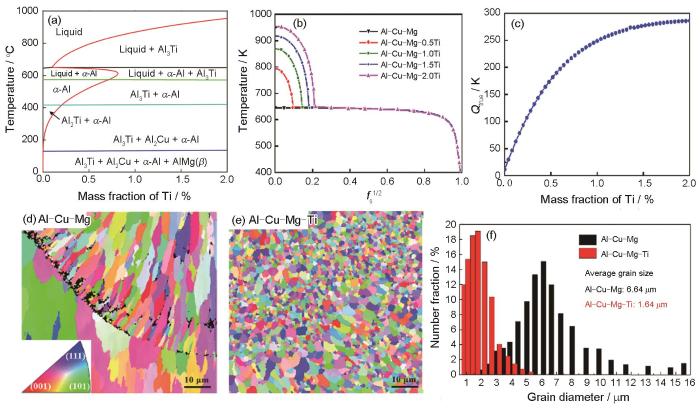
图2 Ti改性2xxx铝合金的相图、裂纹敏感因子、生长抑制因子、反极图和晶粒尺寸分布[17]
Fig.2 Thermodynamic calculation of phase diagram (a), crack susceptibility factor (fsis fraction solid) (b), and growth inhibition factor (Qtrue) (c), inverse pole figures (IPFs) of Al alloys before (d) and after (e) Ti modification, grain size distributions and average grain sizes (f) of Ti-modified 2xxx Al alloys[17]
另一种提升铝合金材料性能的方法是将陶瓷颗粒与合金粉末均匀混合后成形出铝基复合材料。现有研究分别利用静电自组装[12]、高能球磨[18~20]、气溶胶输送黏合剂[21]、气雾化[22]和超声振动分散技术[23,24]分别合成了ZrH/Al7075、TiC/AlSi10Mg、SiC/AlSi7Mg、TiB2/AlSi10Mg、碳纳米管/AlSi10Mg和TiN/AlSi10Mg复合材料粉体。与未经增强的合金材料相比,复合材料具有更好的成形性能和细小的微观结构,可显著提高硬度、耐磨性和抗拉强度。例如,Li等[22]采用气雾化法合成TiB2/AlSi10Mg复合粉体,其抗拉强度为530 MPa,延伸率为15.5%。Wang等[20]采用高能球磨的方法制备了nano-SiCp/AlSi7Mg纳米复合材料,当nano-SiCp含量为2%时,抗拉强度和延伸率分别为502.94 MPa和10.64%。
综上所述,目前国内外铝合金及其复合材料的金属增材制造研究大多从传统合金牌号出发,虽然部分研究在新型铝合金的开发上已经取得了阶段性进展,初步解决了铝合金的高裂纹倾向和柱状组织粗化的问题,但目前改性方法仍较为单一,材料成分设计理论不完善。
2.2 钛合金
目前增材制造成形钛合金的研究主要围绕Ti-6Al-4V合金开展显微组织与力学性能的调控。LAM成形Ti-6Al-4V合金的显微组织主要为针状马氏体(α′),抗拉强度为1000~1300 MPa,但延伸率普遍小于12%[25~27] (图3a[27])。由于传统牌号钛合金的激光增材成形性能较好,因此对于新型钛合金材料设计的研究十分有限。现有关于工艺调控与优化的研究表明,在SLM的极端非平衡凝固条件下很难形成等轴晶粒。与其他常见的工程合金(如铝合金)相比,目前还没有商业化的细化剂能够有效地细化晶粒。为了解决这一挑战,Zhang等[28]报道了一种面向SLM工艺的Ti-Cu合金,这种成分的合金在凝固过程中具有较高的成分过冷能力,可消除增材制造中高温度梯度的负面影响。在没有后处理的情况下,制备的Ti-Cu合金试样具有等轴细晶微观结构,与传统合金相比具有较高的屈服强度和延伸率(图3b[28])。
图3

关于增材制造制备钛基复合材料,目前通常采用TiB[29~31]和TiC[32]作为陶瓷增强相强化基体。Attar等[30]采用高能球磨法将纯Ti与纳米TiB2均匀混合后,采用SLM技术制备复合材料,Ti和TiB2在成形过程中发生原位反应,生成的针状TiB颗粒均匀分布在基体上,形成TiB/Ti复合材料。TiB/Ti复合材料的显微硬度、压缩屈服强度和极限抗压强度均大于纯Ti (CP-Ti)和Ti-6Al-4V合金,力学性能的提高归因于TiB颗粒的强化效应和α-Ti晶粒的细化。SLM成形的TiC/Ti复合材料,由于纳米TiC增强体的弥散强化效果,其硬度和弹性模量约为未增强Ti的22.7倍和2.4倍[32]。Han等[33]在纯Ti中加入不同含量的B4C原位制备(TiB + TiC)/Ti双相增强复合材料,样品致密度均大于97.8%。如图4[33]所示,随着B4C含量的增加,材料的微观结构发生了从板条状(0)到树枝状(1%)再到胞状+树枝状结构(2%~5%)的演化。分散强化和晶粒细化强化的协同作用使复合材料的力学强度显著提高。添加1%B4C的复合材料的极限抗拉强度为946 MPa,屈服强度为762 MPa,弹性模量为128 GPa,分别比Ti基体高62.4%、49.2%和15.3%,但延伸率不足5%。
图4

综上所述,由于传统钛合金的LAM工艺较为成熟,加工性能较好,因此鲜有关于新型材料设计的研究。然而,SLM固有的凝固特点赋予钛合金马氏体组织、缺少有效形核剂等组织调控难题仍需从粉末成分源头上提供解决思路。因此,钛合金及其复合材料的增强增韧方法的探究,应是SLM成形钛基材料的重点。
2.3 铁基合金
铁基合金是LAM中研究的较为成熟的一个材料体系,研究材料涉及现有牌号的钢材,如AISI 304 L不锈钢[34]、AISI 316L不锈钢[35]、AISI 420不锈钢[36]等常用钢材。在增材制造过程中,通过对现有牌号的合金粉末工艺调控,可以降低材料缺陷,获得高致密度的合金材料。Wang等[37]通过SLM制备了高强度高塑性的316L不锈钢,强度可达640~700 MPa,延伸率达36%~59%。但是随着对合金性能的要求逐步升高,工艺参数优化对材料的性能影响有限,为此出现了针对粉末成分的调控方法。在原有材料的基础上通过成分调整,引入新元素、加入新物相等方式改变材料的原有特性,面向增材制造的新型铁基合金改性主要是通过成分设计、元素调控、颗粒增强3种方法实现。
图5

图5 LCD制备的Fe19Ni5Ti试样及其拉伸测试[38]
Fig.5 Fe19Ni5Ti samples prepared by LCD and tensile tests [38]
(a) schematic of section temperature during forming (Ms—martensite start temperature)
(b) OM image of sample
(c) hierarchical structures of microstructure characteristics under different length scales
(d) tensile curves of two kinds of Fe19Ni5Ti (mass fraction, %) steel samples (Insets are the light microscope diagrams of two kinds of samples)
Zhang等[39,40]选用Fe43.7Co7.3Cr14.7Mo12.6C15.5B4.3Y1.9(原子分数)非晶增强不锈钢,利用Y元素吸收成形腔中的O2并上浮至表面,采用其余元素对材料的组织进行调控。图6a[39]中可以看到,原始上表面有一层沿着熔池边界分布的白色带状物,检测其物相为Y2O3,由Y元素氧化产生,经过层层熔化最终浮在表面。上表面抛光后,未观察到明显的其他相,元素成分分布均匀(图6b[39]),非晶改性后,显微组织显著细化(图6c和d[39])。316L不锈钢的拉伸强度为819 MPa,对其改性后的材料拉伸强度提升至1090 MPa。与不锈钢材料相比,加入非晶后的新材料具有更加优异的钝化膜、更好的耐蚀性,点蚀电位从0.918 V提升到1.013 V,双电层电容(Cdl)从6.17 μF/cm2降低到2.15 μF/cm2,点蚀时间从488 s提升到1688 s (图6e和f[40])。
图6

图6 SLM成形不锈钢和铁基非晶/不锈钢材料微观组织及腐蚀性能[39,40]
Fig.6 Microstructures and corrosion properties of SLM-fabricated stainless steel and Fe-based amorphous/stainless steel
(a, b) microstructures before (a) and after (b) polishing[39] (Inset in Fig.6a is the energy spectrum of point 1, and the insets in Fig.6b are the surface energy spectrum and elements distribution) (c, d) IPFs before (c) and after (d) modification[40] (e, f) comparisons of potentiostatic polarization test[40] (I—corrosion current; T1, T2—start time of pitting corrosion; K1, K2—initial slope of the curve; SS—stainless steel)
2.4 镁合金
镁合金具有低密度、高比强度和比刚度、优良的减震阻尼和电磁屏蔽性能以及优越的生物相容性,应用广泛[52,53]。目前,镁合金LAM研究主要难点如下[54]:(1) Mg对氧的高亲和力会迅速形成球状氧化层,降低成形件的强度;(2) Mg在沸点和熔点之间的温度范围较小(440℃),高激光功率输入会导致Mg元素蒸发。因此,表面粗糙度增加,出现孔隙和热裂纹等缺陷。对于上述难点,现有解决方案如下:(1) 对于氧化问题,可以通过添加活性元素、钝化元素和RE元素来解决。例如,在Mg-Al[55]和Mg-Be[56]合金中,活性金属元素可以在Mg之前被氧化。根据钝化效应,加入过渡金属元素(如Fe、Mn、Cu、Ni)对Mg与氧之间的表面活性有负面影响,从而减缓甚至抑制氧化过程[57]。此外,RE元素可富集,提取镁合金中的氧,抑制基体氧化;(2) 对于蒸发问题,合金化处理可以有效地提高镁合金的熔点和沸点温度范围。因此,对镁合金进行合金元素改性,设计和开发其他适合SLM工艺的新型镁合金体系尤为重要。
Al是镁合金中有效的增强合金元素,通过固溶强化和细化晶粒提高镁合金的力学性能[55]。Shuai等[58]研究发现,当Al含量小于3%时,金属间化合物β-Mg17Al12沉淀并分散,随着Al含量的进一步增加,晶粒尺寸得到细化,β-Mg17Al12沿晶界连续沉淀;当Al含量增加到7%时β-Mg17Al12形成网格状,引起了严重的镀锌腐蚀。此外,金属间化合物β-Mg17Al12的存在会影响镁合金的力学性能。β-Mg17Al12的立方晶体结构与镁合金晶体结构缺乏相干性,导致了拉伸应力下裂纹的形成和传播。因此,在SLM工艺中引入Al时,Al的添加量应控制在一个合理的范围内,以减少金属间化合物β-Mg17Al12的沉淀,减少镀锌腐蚀和晶间裂纹的增长。
Ca作为骨科植入材料中的合金元素,将Ca引入镁合金中可以显著提高镁合金的可塑性、耐腐蚀性和整体性能[59]。Yang等[60]报道称,Ca的加入形成了一个新的金属间化合物,可作为牺牲阳极保护Mg基体,改善了Mg-Al-Mn合金的腐蚀行为。在镁合金中引入的CaO将与Mg和Al反应,形成(Mg, Al)2Ca相,导致电位差降低,耐腐蚀性增强[61]。Shuai等[62]将0~12%CaO引入SLM成形的Mg-Al-Zn (AZ61)合金中,研究表明,CaO加入含量为3%~6%时,沉淀相较离散,形成细长的枝状结构;CaO含量增加到9%时,金属间化合物形成沿晶界分布的连续网状结构;CaO含量达到12%时,沿晶界分布的连续网状结构明显粗化。
Zhang等[63]的研究发现,随着Zn含量的增加,析出相经历了连续的跃迁:MgZn→MgZn + Mg7Zn3→Mg7Zn3,当采用不同的制造工艺时,镁合金中的最佳Zn含量是不同的,但Zn元素的加入,通过晶粒细化、固溶强化和沉淀强化能够提高SLM成形镁合金的耐蚀性和力学性能。
RE元素Dy对SLM成形镁合金的降解速率有双重影响[64]。一方面,RE元素可以细化镁合金晶粒,减少元素偏析,从而降低合金的降解率;另一方面,大量的第二相会引起严重的电偶腐蚀,从而加速镁合金的降解。因此,细化晶粒与第二相之间的良好平衡能保持较低的降解速率。迄今为止,大多数报道的生物医学镁合金都含有RE元素,在选择RE元素改性镁合金时,RE元素的含量应控制在适当的范围内,并且需要考虑潜在的毒性效应。
2.5 NiTi形状记忆合金
NiTi合金的成形和加工是形状记忆合金应用的一大难题。NiTi合金主要的功能特性为超弹性和记忆效应,这2种效应均源于热弹性马氏体相变,若其常温下物相组成为热弹性马氏体,则其展示出来的性能为形状记忆效应;若其常温下组成为奥氏体,呈现出一种略有延迟的超弹性。在NiTi形状记忆合金中,合金的成分设计至关重要,合金成分从根本上决定了NiTi合金在室温下稳定的相组成,决定了其功能特性。
Haberland等[65]对比研究了工艺参数对4种Ni含量不同的形状记忆合金性能的影响(Ni原子分数分别为49.7%、50.2%、50.5%、50.7%),发现Ni / Ti原子含量比的变化导致NiTi合金中相变路径和相变温度发生明显变化,富Ni相的相变温度低于等原子比,而富Ti相的相变温度则更低。使用SLM制造的富Ni的NiTi合金样品具有明显的超弹性效应,并且其超弹性效应可以被时效热处理提升[66]。贫Ni的NiTi合金相变温度明显高于室温,展现出明显的形状记忆效应[67,68]。Tan等[69]以Ti54.8Ni45.2为原材料使用粉床LAM技术制造了具有高致密度的NiTi试样,其致密度超过99%,但激光能量密度较高时会导致大量的Ni蒸发和明显的裂纹。Xue等[70]以Ni51.1Ti48.9和Ni50.3Ti49.7为原材料,在较大的工艺参数窗口内成功地制备了全致密的NiTi零件,并且制备的零件的延展性达到16%。由于熔化过程中Ni的蒸发,导致采用富Ni材料(即Ni50.8Ti49.2)制备的NiTi零件的相变温度随着能量密度的提高而单调上升。因此,通过改变工艺参数,可以精确地调整富Ni的NiTi形状记忆合金的化学成分和性能。用近等原子比成分打印的零件,其形状记忆效应的可恢复应变达到了6%;采用富Ni成分打印的零件,其超弹性可恢复应变达到了4%。结果表明,只有当Ni含量足够高时才会形成足够多的Ni4Ti3析出相,从而明显降低相变温度。Zhang等[71]采用SLM技术以Ni50.4Ti49.6预合金粉末为原材料,制备了具有较高的拉伸性能和较高可恢复应变的形状记忆合金试样,其拉伸应变达到15.2%,并且在预变形4%和6%时,形状回复率分别为97.7%和92.5%。
综上,影响NiTi合金相变温度的因素不仅仅有成分,还有LAM的工艺参数,激光功率和扫描速率都会影响其Ni的蒸发,而Ni含量是影响NiTi形状记忆合金相变温度的直接原因:相变温度随着Ni含量的升高会有所降低,当Ni原子分数小于50.6%时,合金表现出形状记忆性能;当Ni原子分数大于50.6%时,则表现出超弹性。
传统的NiTi形状记忆合金相变温度不高,并且即使通过改变Ni含量提高相变温度也很难使其相变温度突破150℃。为了保持NiTi形状记忆合金在高温下的功能特性,近些年来研究人员提出用合金化手段改善NiTi合金高温下服役性能,形成了以Ni-Ti-X (X = Pd、Hf、Pt、Au)为代表的NiTi基三元高温形状记忆合金。其中X元素多以取代Ni原子的形式进入体系。然而,目前增材制造技术成形NiTi基多元形状记忆合金的研究鲜有报道,由于增材制造技术加工过程中可以有多种手段调控成形试样内部冶金组织,所以适用于成形内部成分及物相较为复杂的体系,在这方面值得研究人员大量挖掘。
在陶瓷改性方面,Lu等[72]使用机械球磨法将La2O3纳米颗粒和Ni50Ti50的NiTi预合金粉末粉体混合,采用LAM技术,成功地细化了增材成形的等原子比NiTi合金的晶粒,并且与NiTi合金样品对比,发现La2O3使NiTi试样的可恢复超弹性应变提升了约1%。目前关于增材制造技术制备陶瓷颗粒改性NiTi合金方面的研究较少,综合传统工艺来看,陶瓷颗粒改性NiTi形状记忆合金主要围绕以下几个方面进行:提高压缩和拉伸性能,改善相变特性,降低材料的密度以减轻重量,提高其超弹性可恢复应变及弹性模量。
2.6 高温合金
镍基、钴基为最常见的2类高温合金。但Co元素在地球储量较少,制备成本更高,因此在工业应用上较少。目前LAM镍基高温合金研究的内容主要有:各类工艺参数对成形件质量的影响,熔凝组织的形成规律与控制,热处理工艺对组织性能的影响以及成形材料的力学性能等。例如华中科技大学快速制造中心团队[73]对Inconel 625合金开展了大量工艺研究,发现成形件内部存在长度小于100 μm的微裂纹,(γ + Laves)共晶凝固和成形过程中的高温度梯度是形成微裂纹的主要原因。Inconel 718合金几乎不存在裂纹等缺陷,但其在室温(25℃)和高温(650℃)拉伸中均表现为低强度和高塑性,其高温拉伸缺陷的开裂机制主要有2个:一是熔池中心呈现性能弱区,二是熔池边界迁移不协调。
鉴于LAM传统牌号合金综合力学性能欠佳,人们将目光转向了材料成分的创新设计,利用添加剂改性来降低工艺的复杂化。研究[74,75]发现,一些元素的添加可提高LAM成形Inconel 718合金的高温性能。Kakehi等[74]的研究表明,在常规Inconel 718合金中,高硬度δ相的生成是降低合金的塑性、促进裂纹产生的主要原因。通过添加适量的Y元素,利用Y代替Al形成氧化物,可抑制δ相的生成,提高材料的高温抗蠕变性能和延展性。王海丽[75]也做了类似的研究,结果表明,Re元素的添加也具有相同的作用。除此之外,Re元素被氧化后可形成稳定的酸性氧化物Re2O7,从而阻碍熔盐碱性的升高,提高合金的高温耐腐蚀性能。但不适当的元素改性也会降低材料性能。例如Al元素的添加会形成金属间相AlNi,降低材料的强度[76];W元素的添加会粗化γ'相,且W元素在合金中的分布极不均匀,不管是由于其贫乏导致固溶强化较差,还是其富集导致难溶元素Nb减少,都会造成合金高温抗蠕变性能的减弱,同时降低合金高温耐热腐蚀性能[75]。
目前改性高温合金使用较多的陶瓷增强相主要有石墨烯[77]、TiB2[78]和TiN[79]等,这些陶瓷颗粒的添加可以起到细化晶粒和钉扎位错的作用,从而显著提高材料的显微硬度和抗拉强度。相比于未添加陶瓷颗粒的Inconel 718试样,纳米TiC/Inconel 718试样的摩擦磨损性能和高温抗氧化性能都有了一定程度的提高。Chen等[76]利用SLM制备了TiC/Inconel 625复合材料。分析发现,纳米TiC的添加提高了合金的高温强度、热稳定性和抗氧化性。其主要原理如下:在细化晶粒方面,一方面TiC的导热系数高于Inconel 625,添加纳米TiC陶瓷颗粒可以提高制备过程中熔池的冷却速率,细化胞状枝晶;另一方面基体中Ti原子的增加,能促进强化相γ'的生成;在抗氧化方面,高温条件下TiC易氧化形成TiO2,阻碍Fe、Ni原子的扩散,减缓外层铁、镍氧化物的生长,促使Cr2O3层更加致密(图7[76])。
图7
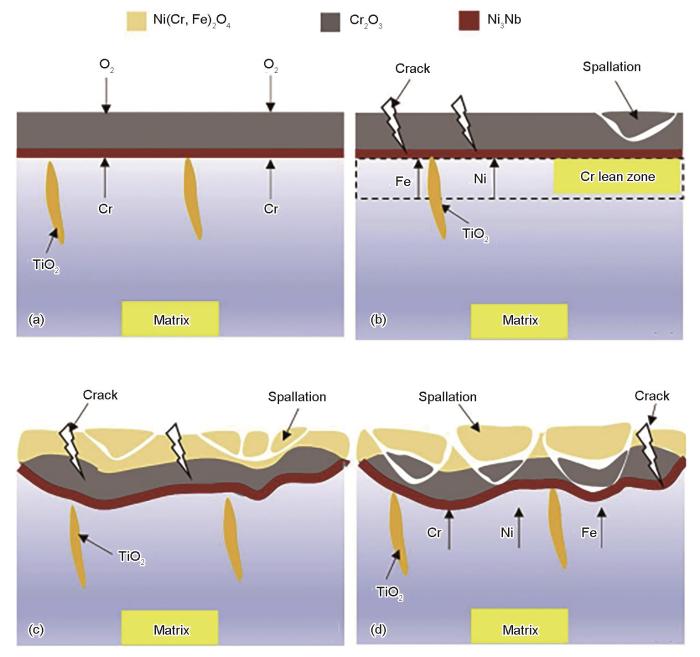
综上所述,对于LAM镍基高温合金,目前其沉积态试样的综合力学性能还达不到锻件水平,而且成形过程中易产生微裂纹等缺陷。通过添加合金元素或者陶瓷颗粒等对材料进行改性,可一定程度上提高材料的高温性能。
2.7 高熵合金
目前LAM成形HEAs主要有2大体系:CoCrFeNiMn和AlCoCrFeNi体系。Li等[85]使用SLM成形等原子CoCrFeMnNi HEAs,研究表明试样组织以fcc相为主,但仍存在少量的σ析出相及纳米孪晶,同时Mn元素在组织中发生了偏析。并且大量位错堆积、晶格畸变也使得CoCrFeMnNi HEAs力学性能得到提升,抗拉强度为601 MPa,延伸率为35.0%。Fujieda等[86]用Ti取代了Mn,制备出CoCrFeNiTi HEAs。结果表明,加入Ti元素后偏析现象得到抑制,没有析出Ni3Ti金属间化合物,进一步提高了此类HEAs的综合力学性能。Karlsson等[87]利用SLM成形等原子AlCoCrFeNi HEAs。研究结果表明,SLM成形的试样由于应力的积累不可避免会引起裂纹、空隙等微观缺陷。
在金属元素改性方面,可通过在难熔HEAs中添加熔点较低的V、Ti等元素来提高其SLM成形性、室温强度和塑性。Zhang等[88]利用NbMoTaX合金的凝固路径,对比了不同合金的裂纹敏感性指数,如图8[88]所示。研究发现,同时加入Ni和Ti元素,可以在不影响力学性能的前提下,抑制NbMoTa HEAs的裂纹产生,最终成形的NbMoTaTi0.5Ni0.5试样室温和高温(1000℃)抗压强度分别为2297和651 MPa。通过元素的调整或替换,改变合金内部的显微组织和元素偏析,有助于调整材料的性能。Sun等[89]将CrFeCoNi HEAs同Al粉混合,利用SLM成形了Al x CoCrFeNi (x = 0.1、0.5、1.0) HEAs,系统研究了Al的加入量对热裂行为的影响,其中Al0.5CoCrFeNi HEAs最为致密,未观察到孔隙与裂纹生成,试样微观组织为单相无序的fcc相,且相比于铸态或锻态合金来说有着更高的抗拉强度。在另外系列的研究中也通过SLM成功制备了AlCrCuFeN[90]、AlCrCuFeNi x (x = 2.0、2.5、2.75、3.0)[91]、AlCoCrCuFeNi[92]、AlCoCuFeNi[93]和AlCrFeNiV[94] HEAs,然而这些合金大部分在增材制造过程中具有很高的热裂纹敏感性,使得试样存在缺陷,致密度不高。目前许多研究旨在通过不同方式改善HEAs的SLM加工性能,得到无裂纹、力学性能优异的HEAs。
图8

综上,目前相当一部分HEAs在SLM工艺下都表现出明显的热裂纹敏感性,使得最终成形效果不佳。为此许多研究采用元素改性或添加增强相的方法,但是元素的偏析及蒸发、元素熔点不同、粉末掺入效率、增强相与HEAs基体适配性以及如何保持高塑性还缺乏科学指引。同时,利用SLM成形HEAs的体系并不完善,报道所涵盖的合金体系远远少于理论上HEAs体系,需要结合模拟、计算来进行成分设计,开发区别于常规合金的新型HEAs材料。
2.8 非晶合金
图9

图9 非晶合金的连续冷却转变曲线示意图及制备的铁基非晶合金结构[101]
Fig.9 Schematic of continuous cooling transformation (CCT) curve of amorphous alloy (a) and Fe-based amorphous structure (b)[101] (Rc—critical cooling rate, Rcryst—crystallization cooling rate, RSLM—SLM cooling rate, TPF—thermoplastic forming, tp—maximum time to supercooled liquid region, t
现有LAM非晶合金的难点主要体现在缺陷和晶化上,易开裂的特性使得非晶合金的成形相对困难,显著影响成形块体的力学性能。非晶具有较高的强度和硬度,SLM成形中冷却速率也远高于临界冷却速率,可以很好地抑制结晶情况。但是高冷却速率却极易导致熔池不稳定,而非晶属于脆性材料,不稳定的熔池会加剧其开裂情况,导致成形失败,图9b [101]中可以观察到成形支架中的开裂情况。同时,非晶合金的断裂方式通常是脆性断裂,这使得样品的延展性较差。Li等[102]针对铁基非晶的成分进行调控,通过引入第二相Cu和Cu-Ni合金形成复合材料,利用SLM过程中第二相高密度位错的产生释放应变能,从而大大降低热应力,抑制了微裂纹的形成。如图10[102]所示,通过引入第二相,铁基非晶复合材料的强度和断裂韧性均有大幅提升,其中断裂韧性达到47 MPa·m1/2,是铁基非晶(2.2 MPa·m1/2)的20倍左右。此外,Gao等[103]研究SLM成形原位β相增强Ti/Zr基非晶合金基复合材料。采用SLM制备了(Ti0.65Zr0.35)90Cu10 (原子分数,%),其是由非晶相、β相和少量(Ti, Zr)2Cu相组成的复合材料,合金的微观结构有细、粗2种,且比传统工艺制备的合金的微观结构更细,其平均Vickers硬度达到4.1 GPa。
图10
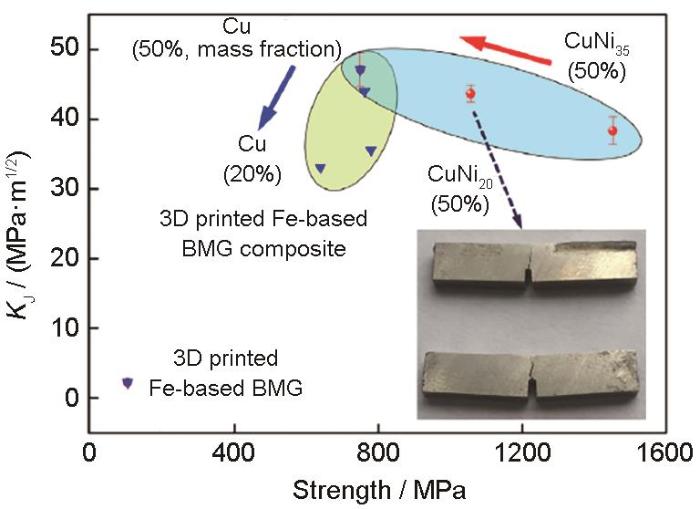
3 总结与展望
LAM技术已应用于铝合金、钛合金、铁基合金、镁合金、形状记忆合金、高温合金、高熵合金及非晶合金等不同金属材料的制备与成形,但大多研究仍采用传统合金牌号,其合金成分并不完全适用于LAM的非平衡冶金过程,常面临冶金缺陷难抑制、显微组织难调控、应力应变难控制、综合性能难提升等挑战。因此,需要开展面向LAM的新型材料成分设计研究,充分挖掘增材制造非平衡凝固特性的潜在优势与价值。
目前金属增材制造材料改性的方法大致可分为元素比例调控、合金元素改性及陶瓷颗粒改性等方法。上述方法的机理均来自于通过改变材料成分控制熔池的凝固过程,进而实现冶金缺陷的抑制及强韧化,例如引入形核剂、改变成分过冷条件、调控物相等,仍存在诸多挑战:
(1) 设计理论不完善:现有的材料改性方法大多依据铸造等工艺的经验摸索,再通过工艺优化及力学性能测试进行验证,尚未形成完善的材料设计理论体系,缺乏理论指导。少数研究开展了裂纹敏感性等热力学计算方法,用以设计新型合金,以提升材料的加工性能。但该方法尚未完全考虑LAM的非平衡凝固特点,工艺与设计匹配性较差,难以通过该方法实现材料成分精准设计。因此,需从LAM的工艺特点出发,完善材料设计的理论体系和方法论。
(2) 设计层级不全面:现有设计方法大多旨在提升加工性能,约束条件过于单一,应从材料的服役角度出发,实现材料的多层级、多因素设计。例如,对于结构材料,需实现面向材料的强韧化设计;对于形状记忆合金,需实现形变回复可控设计;对于特殊环境材料,需基于材料服役环境特点,实现其低温、高温、耐蚀、抗疲劳等可控设计。
(3) 材料体系不健全:现有材料设计理论与方法均在传统热成形的条件下进行约束管理、改进材料成分,这大大限制了材料体系的扩展。LAM极端非平衡凝固工艺赋予了材料设计更广阔的想象空间。结合LAM的工艺特点,开展高熵合金、非晶合金、准晶等材料的颠覆性设计,将在新材料领域开拓新的空间。
(4) 性能研究不系统:迄今为止LAM新材料的性能研究主要集中于室温拉伸性能,而对高温性能和疲劳性能的系统研究相对较少,上述性能研究的局限性严重限制了新材料的开发与应用。因此,在合金成分设计时,应不仅考虑新型合金的加工性能与拉伸性能,更应依据具体服役要求,针对性地开展特定性能的合金成分设计。