分享:粉末粒径对AlSi10Mg合金选区激光熔化成形的影响
王孟, 杨永强, Trofimov Vyacheslav, 宋长辉, 周瀚翔, 王迪,
通过模拟仿真与实验结合研究粉末粒径对选区激光熔化(SLM)可加工性的影响。以3种粒径AlSi10Mg粉末为对象,基于离散元和流体力学数值模拟方法研究SLM铺粉和粉末熔化/凝固介观行为,并对成形样品进行宏观成形质量检测。结果表明,铺粉过程中,粒径小于20 μm的粉末剧烈团聚形成大量空隙,粒径大于53 μm粉末易形成少量大的空隙,中等粒径粉末床相对密度比细粒径和大粒径分别高7.69%和3.17%。单层粉末床熔融时,铺粉质量不均匀,细粒径与粗粒径熔道不规则。但经历多层熔化后,细粒径熔道缺陷部分缓解。随着粒径的增加,熔道表面平整度下降,细粒径粉末样品存在较多孔隙,粗粒径粉末存在少量未熔合缺陷。中等粒径粉末SLM可加工性最好,样品相对密度达到99.8%,比细粒径和粗粒径分别高1.4%和0.4%。
关键词:
选区激光熔化(SLM)是一种高精度增材制造技术,通过激光束定向熔化铺设在基板上的粉末床,实现高自由度构件成形[1]。由于铺粉工艺特性以及激光光斑小,SLM通常使用直径15~53 μm的粉末,粒径15 μm以下的粉末少有使用,53 μm以上的粉末则在定向能量沉积中应用广泛。
微米级粉末流动缺少合适的观察手段。离散元方法(DEM)通过Newton定律显式计算颗粒间相互作用力和运动,为研究粉末流动提供了重要手段,学者们[2~5]借助DEM模拟了介观尺度颗粒流动过程。Si等[2]在DEM模型中引入了堆积密度、结构均匀性、归一化层厚和表面均匀性来定量表征粉末床质量。Han等[6]分析了单层和多层粉末沉积过程中粉末厚度对粉末床特性的影响。Chen等[7]基于DEM系统研究铺粉过程中团聚、壁面、渗透效应,揭示了粉末床铺粉密度变化机理。Yao等[8]研究了铺粉工艺参数、粉辊形状、粉末尺寸对粉末床质量的影响。
对于不同粒径SLM铺粉差异,文献[9,10]采用DEM分析了细粒径粉末团聚效应与几何效应的竞争机制,指出适当的团聚黏附可改善粉末床均匀性。文献[11,12]通过实验测量了不同粒径粉末扩散密度、吸湿性、表面能、内聚功等粉末属性,采用粉体流变仪(FT4)、漫反射光谱(DRS)方法定量描述粉末床流动性、激光吸收率差异,系统研究了粒径对实际层厚、成形致密度、尺寸精度、显微硬度、组织演变的影响,指出粗粉更利于SLM成形。将铺粉过程和粉末熔化过程相结合,可以研究粉末床质量对SLM成形的影响。Gu等[13]采用DEM对多种粒径粉末铺设固定层厚粉末床,并将粉末床导入流体模型进行熔化/凝固模拟,结果表明粒径25 μm的粉末能够形成更加平滑和致密的熔道。然而不同的粉末粒径具有不同的铺粉密度,导致实际层厚存在显著差异,激光熔化/凝固过程也存在差异。
为此,本工作以3种粒径(0~20 μm (PSD1)、20~53 μm (PSD2)、53~105 μm (PSD3)) AlSi10Mg粉末为对象,基于DEM的内聚模型建立SLM铺粉模型,考虑粉末层厚仅与粒径相关,研究不同粒径的铺粉行为差异。通过建立DEM与计算流体力学(CFD)模型单向耦合,研究单层粉末床质量对熔道温度、形貌的影响,揭示粒径对于熔化/凝固的影响规律。并开展相关实验验证,进一步研究粉末粒径对SLM成形的影响规律。
1 数值模拟方法
1.1 铺粉数值模拟
通过DEM建立小尺度粉末铺设物理模型。本工作中,直径0~5 μm的AlSi10Mg粉末会带来极大的计算消耗,因此舍去,其余粒径与实际粒径分布一致,此外细粒径颗粒间存在的Van der Waals力不可忽略[9]。因此采用DEM中Hertz-Mindlin with Johnson-Kendall-Roberts (JKR)模型[14],通过对邻近区域颗粒施加法向引力来考虑Van der Waals力的影响,有效模拟颗粒团聚现象。JKR法向引力(FJKR)由表面能密度(γ)、粒子间临界距离(δ)决定[14]:
式中,E为等效Young's模量,R为Hertz-Mindlin定义的等效半径,a为粒子间接触半径。
DEM模型中,粉末颗粒间恢复系数(rs)、滑动摩擦系数(μs)和滚动摩擦系数(μr)均影响铺粉动态行为。受实验条件限制,仅对部分参数进行标定。金属颗粒具有较高的强度、硬度和球形度,滚动过程中阻力非常小[15],因此μr设置为0.09。采用休止角(粉末堆积斜面与底面夹角,AOR[16])方法对rs、μs和γ进行参数标定,休止角标定模型如图1a所示。
图1
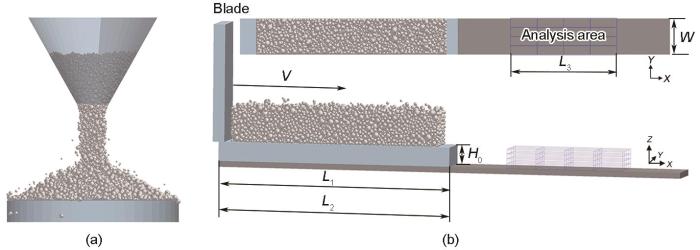
图1 休止角和铺粉离散元方法(DEM)物理模型
Fig.1 Physical model of discrete element method (DEM) for angle of repose (AOR) (a) and powder spreading (b) (V—speed of blade, W—width of substrate, H0—height of layer thickness, L1—length of powder platform, L2—length of substrate, L3—length of analysis area)
铺粉物理模型如图1b所示。初始粉末堆在粉末平台生成,刮板沿X方向铺粉,台阶处高H0为铺粉层厚。不同粉末粒径所需层厚不同,实际铺粉层厚一般为设置层厚的1倍以上[17]。提取分析区域粉末堆积形貌、堆积密度作为分析对象。为了减小时间步长,将Young's模量缩小了100倍,在DEM模拟领域是可以接受的,对结果影响较小[3]。
1.2 粉末熔化/凝固数值模拟
采用CFD方法建立高能激光束作用下单层粉末颗粒熔化/凝固介观模型,分析粉末粒径对SLM过程成形轮廓、温度的影响规律。熔池流动遵循质量守恒、动量守恒和能量守恒定律,考虑金属固/液转变,控制方程见文献[18]。激光束采用Gaussian分布的等效热源模型[19]:
式中,Slaser为吸收的激光能量,A为激光吸收率,P为激光功率,r为激光束半径,t为时间,vlaser为激光扫描速率,(xi, yi )为激光焦点中心的初始位置。热源直接施加于粉末上表面,通过有限体积(VOF)方法捕获该界面。激光只发生一次吸收,不考虑激光反射、折射和透射。
熔池内温度超过液相温度甚至蒸发温度,且上、下区域存在保护气、基板,因此需要考虑熔池对外围区域的能量损失(Eloss)边界条件[20,21]:
式中,Evap为蒸发热损失,Erad为辐射热损失,Ecov为对流热损失。
熔池匙孔处蒸发气体对熔体产生反作用力,熔池表面的高温度梯度导致Marangoni效应,同时熔体表面存在表面张力等,考虑熔池的力边界条件[22,23]:
式中,Fdrive为熔池驱动力总和,Fpr为蒸汽反冲压力,Fst为表面张力,Fm为Marangoni力,Fdamp为凝固糊状区的曳力,G为重力,Fbuo为浮力。
提取DEM模拟的粉末床几何信息,包括颗粒中心坐标和颗粒直径,初始化该几何区域为金属相,实现DEM至CFD单向耦合[23]。激光照射至粉末床的深度有限,为了综合考虑3种粒径粉末熔化过程,统一设置流体模型的粉末床厚度80 μm,模拟单层粉末熔化过程。计算域尺寸为600 μm × 300 μm × 160 μm,包括50 μm厚基板,粉末床和110 μm厚保护气区域。PSD1采用2.5 μm网格,PSD2和PSD3为3 μm网格,时间步长1 × 10-7 s。AlSi10Mg物性参数参考文献[24]。
2 实验方法
采用与仿真相同的参数开展相关SLM实验,进一步验证和分析仿真结果。实验使用配备500 W光纤激光器的DiMetal-100H金属3D打印机。实验材料为气雾化法制备的3种不同直径AlSi10Mg粉末,其化学成分如表1所示,采用LA960S激光粒度仪测量粉末粒径分布,结果如图2a所示。其中D10、D50和D90分别为累积粒度分布达到10%、50%和90%的颗粒直径,该分布信息直接用于DEM颗粒生成。通过实测获得3种粒径粉末PSD1、PSD2和PSD3休止角分别为36°、33°和32°,休止角标定DEM参数范围及最终使用参数见表2。
表1 不同粒径AlSi10Mg粉末的化学成分 (mass fraction / %)
Table 1
Powder | Zn | Si | Ni | Fe | Mn | Mg | Al |
---|---|---|---|---|---|---|---|
PSD1 | 0.011 | 10.24 | 0.022 | 0.14 | 0.01 | 0.35 | Bal. |
PSD2 | 0.010 | 9.66 | 0.020 | 0.10 | 0.20 | 0.42 | Bal. |
PSD3 | 0.009 | 9.74 | 0.003 | 0.10 | 0.03 | 0.28 | Bal. |
图2

图2 3种粒径AlSi10Mg粉末粒径分布及SEM像
Fig.2 Particle size distribution (a) and SEM images of PSD1 (b), PSD2 (c), and PSD3 (d) (D10, D50, and D90 indicate 10%, 50%, and 90% cumulative particle sizes, respectively)
表2 DEM模型使用参数及参数范围
Table 2
Parameter | Unit | Value | Variable |
---|---|---|---|
range | |||
Particle density ρ | kg·m-3 | 2680 | - |
Poisson's ratio ? | 0.3 | - | |
Young's modulus E | MPa | 750 | - |
Rolling friction coefficient μr | 0.09 | - | |
Sliding friction coefficient μs | 0.6 | 0.4-0.8 | |
Restitution coefficient rs | 0.64 | - | |
Surface energy density γ | mJ·m-2 | 1.2 | 0-15 |
L1 | mm | 2 | - |
L2 | mm | 4 | 2-6 |
W | 10D50 | 2D50-10D50 | |
H0 | 5D50 | 1D50-5D50 | |
L3 | mm | 1 | - |
V | mm·s-1 | 50 | - |
实验成形10 mm × 10 mm × 10 mm方块样件,P为200、230、260和290 W,vlaser为800、1050、1300和1550 mm/s,扫描间距(d)为0.08 mm,实际打印层厚(H1)为0.03 mm。应用Quanta250环境扫描电镜(SEM)观察成形样品表面形貌;采用VHX-5000超景深三维显微镜进行成形表面轮廓和粉末样品表征,观测面为样品上表面。3种粒径粉末的SEM像见图2b~d。抛光后通过DMi8光学显微镜(OM)观察上表面和竖直成形面的孔隙分布。采用Archimedes排水法测量方块密度。激光能量密度(Ev)采用下式计算[12]:
3 结果与讨论
3.1 SLM铺粉动态行为
如图3所示,当铺粉层厚为5D50,粉末在基板上前进时,斜坡与基板形成动态堆积角α。α可表征颗粒流动性,α越小,表明颗粒间相互作用力越小,流动阻力小,具有更好的流动性[25]。根据
图3

图3 DEM模拟铺粉过程的动态堆积角
Fig.3 Dynamic packing angles of PSD1 (a), PSD2 (b), and PSD3 (c) during powder spreading by DEM simulation
3.2 粉末床铺粉质量
铺粉完成后,得到DEM模拟的3种粒径粉末床切片和俯视图,如图4所示。提取粉末床中心区域作为分析区域,x方向长度1 mm,切片厚度为2D50,铺粉层厚为5D50。由于PSD1粒径过小,对PSD1粉末床放大1倍以便清晰展示,如图4a1和a2所示。
图4

图4 DEM模拟的3种粒径粉末床切片图和俯视图
Fig.4 Slices (a1-c1) and top views (a2-c2) of powder bed for PSD1 (magnified) (a1, a2), PSD2 (b1, b2), and PSD3 (c1, c2) by DEM simulation
对比3种粒径粉末床形貌可以发现,PSD1具有非常多的表层空缺和内部空隙,PSD2铺粉质量最好,PSD3铺粉存在少量空隙。从图4a1可见,PSD1中尺寸小于20 μm的粉末发生严重团聚现象,大于20 μm的颗粒未团聚。可见20 μm以下的粒径Van der Waals力主导了颗粒间相互作用力,低流动性抑制了颗粒的平动和转动,刮板刮过的区域均匀性较差,且小颗粒随之团聚,进一步降低了铺粉质量。团聚作用下,粉末床底部和顶部平整度非常差,z方向高度差达到(2~3)D50,不利于下层粉末稳定铺设。当团聚发生在粉末床内部时,将产生大量内部空隙,铺粉不均匀。从图4a2可知,不仅竖直平面存在空隙,水平面也存在大空隙。粒径增加到20~53 μm,Van der Waals力减弱,粉末流动性加强,粉末床均匀,也为下层铺粉提供了平整的基材环境。当然,由于刮板与颗粒间的壁面效应[7],SLM铺粉过程中刮板与粉末床之间必定存在表层空缺,即图4b1切片上方空缺区域,经过多层铺粉后,该空缺能够得到缓解。随着粒径增加至53 μm以上,Van der Waals力对颗粒间作用力可忽略不计。但球体形状导致相邻大颗粒存在50 μm以内几何间隙,由于PSD3粉末中直径小于50 μm的颗粒较少,大的几何间隙无法填充,如图4c1和c2所示,粉末床内部产生较大的空隙,降低了铺粉质量。
DEM模拟的3种粒径AlSi10Mg铺粉的相对密度如图5所示。由于团聚作用,PSD1在铺粉层厚为(1~4)D50时,团聚形成的小块粉末团厚度接近4D50,无法形成有效粉末床,铺粉相对密度为0,这与实验观察结果一致。仅在5D50厚度时形成粉末床(图4a),团聚导致的大量铺粉缺陷使其密度最低。铺粉层厚从1D50增加至3D50时,PSD2铺粉相对密度略低于PSD3,可能是由于中等粒径的AlSi10Mg颗粒质量轻,受壁面效应影响较强,表层空缺占比略大。4D50层厚时,层厚的增加使得空缺得到弥补,PSD2铺粉密度稳定增加并超过PSD3。5D50层厚时,PSD2铺粉相对密度为32.97%,比PSD1高7.69%,比PSD3高3.17%。AlSi10Mg粉末粒径低于20 μm时,Van der Waals力作用下,铺粉难以形成均匀粉末床。粒径介于20~53 μm的颗粒有良好流动性,但壁面效应降低了铺粉密度。粒径介于53~105 μm的颗粒能够弱化壁面效应,却存在较大的球体几何间隙。因此可以考虑在20~105 μm颗粒中定制粒径分布,以弱化壁面效应和减小几何间隙,实现高密度铺粉。
图5
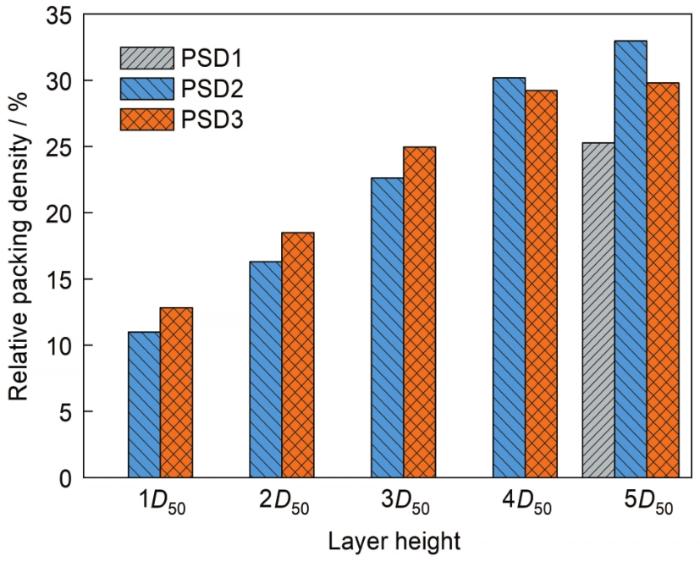
图5 DEM模拟的3种粉末床相对密度
Fig.5 Relative packing densities of powder bed by DEM simulation
3.3 SLM熔道轮廓与温度分布
图6a1~c1为80 μm铺粉厚度,激光功率290 W,扫描速率1300 mm/s的单层粉末熔化/凝固后熔道轮廓及温度分布。图6a1中PSD1熔道形状不规则,沿激光扫描方向呈现出“伪鱼鳞纹”,宽度变化较大。熔池内高温蒸汽对熔池内壁产生反冲压力,迫使熔融液体向熔池后部流动至熔道[26],同时,由于沿熔道方向及垂直方向温度梯度不同,冷却速率不同,熔融液体会形成锥形凝固形态,即鱼鳞纹。而AlSi10Mg热导率高达130 W/(m·K),黏度低且熔点低,实际熔道中鱼鳞纹较浅且间距大,非图6a1所示。PSD1中“伪鱼鳞纹”是由于粉末床不均匀导致的,颗粒团聚形成的粉团松散分布,激光扫描粉团区域时充分熔化并堆积,空腔区域只能通过液体流动填充,形成了凹凸不平的熔道。粉末床的团聚与空缺导致熔融液体体积发生变化,形成的熔道宽度不均匀。如图6b1所示,粒径增加至20 μm以上时,粉末床致密度高,表面平坦,内部空隙少,使得熔池表面平坦,熔宽变化小,熔池呈现良好的拖尾现象,可见铺粉质量对熔道形貌至关重要。当粉末粒径为53 μm以上时,图6c1中PSD3熔道产生欠熔合现象。由于激光扫描速率快,大颗粒熔液尚未完全流动便凝固,形成堆积形式的欠熔。颗粒间大的间隙分布不均匀,会被熔融液体填充,同时熔液也受大颗粒分布影响,因此PSD3熔道前进方向并不一定与激光扫描方向一致,熔道方向不稳定。此外激光扫描大粒径颗粒区域时,无法完全照射多个颗粒,并且Gaussian光束边缘能量密度低,导致熔道边缘存在部分未熔化大颗粒,不利于熔道搭接。
图6
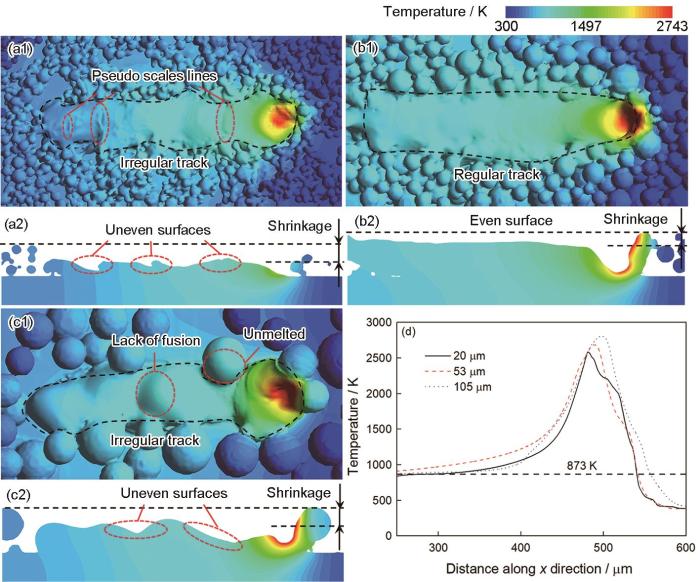
图6 计算流体力学模拟的选区激光熔化熔道形貌及熔池温度分布曲线
Fig.6 Molten track and temperature distribution (a1-c1) of PSD1 (a1, a2), PSD2 (b1, b2), and PSD3 (c1, c2); corresponding slices (a2-c2); and temperature distribution curves of molten pool (d)
图6a2~c2显示不同粒径的熔道表面平整度各不相同,与粉末床铺设质量密切相关。PSD1熔化/凝固后形成了与粉末床相似的大量凸起状轮廓,如图6a2所示。PSD1粉末床的低密度意味着粉末总质量小,只能形成较浅的熔池。粒径上升到20 μm以上时,粉末床表面平整,颗粒分布均匀,大部分颗粒受热过程稳定,形成了平坦的熔道表面,如图6b2所示,为下一层铺粉及熔化提供了较为平整的基材形貌。从图6c2可见,PSD3熔道表面存在较大的高低起伏。PSD3颗粒间大空隙区域被溶液填充,大颗粒由表至内的熔化产生了液体流动性差异,激光高速扫描导致表面冷却凝固,困住了内部液体流动,而外部流动液体不足以填充大空隙,形成了凹坑或斜坡轮廓。此外,受大颗粒不规则的空间分布影响,熔池形态与深度均不如PSD2好,导致熔道表面的不规则情况产生。
Gu等[13]在固定层厚下模拟了不同粒径镍基复合材料的熔道形貌,发现小粒径粉末团聚产生的大量空腔以及铺粉不均匀会导致熔池内金属蒸气或保护气难以从熔池逸出,形成气孔并保留在凝固基体内。同样的情况也发生在大粒径粉末SLM中。而AlSi10Mg具有良好的热导率、较低的熔点温度和动态黏度,相同温度下具有更好的液相流动性及足够的溶液量[27],使得空隙填充率高于镍基材料。因此,对于模拟单层AlSi10Mg熔化/凝固产生气孔的可能性低于镍基粉末,但是对多层粉末模拟而言,不规则表面形貌以及粉末分布,获得气孔分布是可能的。
此外,粉末熔化填充空隙会产生收缩现象,如图6中shrinkage。当功率密度足够的情况下,粉末全部熔化并形成实心的基材,空隙得到完全填充。通过收缩高度差(shrinkage)表征3种粉末熔化收缩率,PSD1收缩率最大,PSD3次之,PSD2收缩率最小,说明PSD2粉末具有最低的空隙率。当然,收缩率还受到其他因素影响,Yu等[28]模拟了不同激光功率下AlSi10Mg收缩率差异,发现400 mm/s扫描速率时,存在功率临界值(250 W),超过该值的功率增长会降低收缩率,低于该值的功率增长会提高收缩率。
图6d显示了熔池区域沿激光扫描方向温度分布曲线。可见,粉末床的不均匀导致熔池区域存在温度差异。PSD1熔池温度最低,PSD3最高,PSD2介于2者之间。虽然小粒径粉末具有较大的表面积以吸收更多的激光能量,但是松散的粉末床由于铺粉密度低,包含的颗粒总量较少,导致能量吸收不足。同时,粉末床中存在的大量空隙使得基板反射了部分能量,导致PSD1整体吸收能量较低,熔池温度低。PSD3大部分粉末粒径接近甚至超过光斑直径80 μm,激光照射颗粒时,大部分能量被单个颗粒吸收,并且AlSi10Mg与保护气的比热、热导率差异使得能量在大的空隙中扩散较慢,熔池温度高于其余2种粒径。PSD2粉末床均匀且粒径为激光光斑一半,其熔池温度介于2者之间,与AlSi10Mg蒸发温度相当。此外,沿激光扫描方向,PSD2高于液相线的熔道长度大于PSD1和PSD3,能够为金属液体铺展提供更大的润湿范围。因此,熔道形貌与温度分布对不同粉末粒径导致的粉末床均匀性较为敏感[26],中等粒径能够提供更好的SLM成形性。
3.4 实验结果
为了进一步分析粉末粒径对AlSi10Mg多层多道实际成形效果的影响,开展了系列成形实验。发现PSD1粉末初始铺粉过程非常不稳定,粉末堆呈现明显团聚并形成较高粉末堆,与图4a1和a2及文献[25]一致。前几层很少粉末铺设到基板上,5层之后开始有粉末团块非常稀疏地铺展,基板边缘缝隙的存在降低了粉末在该区域的停留。铺粉至30层左右,粉末基本铺设至基板表面。PSD3由于初始几层层厚小,大粒径粉末被刮出基板。PSD2和PSD3均在10层铺粉时达到稳定。SLM成形过程中,20 μm以下AlSi10Mg粉末质量非常轻,DiMetal-100H设备基板边缘靠近风循环系统的出风口,粉末易被吹走,导致边缘粉末不均匀,该区域未能进行有效铺展,易发生激光多次重熔样品表面,热量累积使表面发生翘曲,打印失败。
图7显示了通过超景深三维显微镜观察得到的几组表面质量较好的样品表面轮廓,其中功率290 W,扫描速率1300 mm/s,粒径20 μm以下粉末床致密度较低,实际熔化后凝固层厚度小,因此z方向高度差仅为15 μm。对比图6a1和a2单层熔化,可见多层熔化能够缓解表面粗糙现象,因为小粒径粉末实际熔融层厚小,热量可传导并熔化多个凝固层,改善表面质量。粒径增加至20 μm以上,熔融层厚增加,成形表面波动增加,伴随着飞溅强度同步增加,PSD2表面高度差扩大至35 μm。根据图6c1、c2与图7,PSD3由于大颗粒欠熔合,熔融液体扩散不及时,成形表面高度波动显著增加,达到75 μm。
图7

图7 3种粒径样品上表面轮廓高度和超景深三维显微镜像
Fig.7 Top surface contour heights (a1-c1) and images (a2-c2) of PSD1 (a1, a2), PSD2 (b1, b2), and PSD3 (c1, c2) samples showed by ultra-depth three-dimensional microscope
图8是未经任何磨样处理的样品上表面SEM像。图8a显示PSD1样品表面非常平坦,较小的熔融厚度使得熔道搭接不明显。PSD2熔融厚度的增加,提高了熔道高度,实验采用45°正交扫描策略,表面清晰可见交叉叠加的熔道,如图8b所示。粉末粒径增大时,PSD3熔道显著宽于前2种粉末,如图8c所示,过大的颗粒引导了熔道发展方向,颗粒欠熔导致熔道起伏波动大,粗糙度高。3种粒径成形样品上表面均未观察到明显的空隙等缺陷,说明AlSi10Mg粉末在自身高热导率和低熔点影响下,较高的熔融液体流动性使得铺粉缺陷在多层熔化/凝固后得到部分弥补,这是由粉末属性决定的。
图8

图8 3种粒径样品上表面形貌的SEM像
Fig.8 Top surface SEM images of PSD1 (a), PSD2 (b), and PSD3 (c) samples
图9显示了3种粒径样品内部缺陷分布的OM像。Van der Waals力作用下,小粒径粉末倾向于团聚成团块,粉末不易在粉末床完全铺展开,形成较多的空隙。同时,与大粒径粉末相比,其流动性较低,会在刮刀前方形成陡峭粉末堆,阻碍刮刀铺粉过程,进一步降低了粉末床致密度。因此,即使PSD1上表面平坦,内部必然存在较多的孔隙。从图9a1和a2可见,PSD1样品内部存在较多孔隙,虽然较薄的熔融层厚能够带来更多的热传导,但是粉末床内大量孔隙仍然受困,难以逸出至熔池表面。图9b1和b2显示PSD2样品内部仅有非常少量的孔隙,因为PSD2粉末床自身仅存在少量空隙,平整且均匀的粉末床为熔液流动和填充提供了良好的渗透环境。如图9c1和c2所示,PSD3样品内部存在少量孔隙和尺寸较大的未熔合缺陷。PSD3中粒径超过激光直径的大颗粒粉末稀疏分布在粉末床内,激光能量无法完全熔化该颗粒,形成非常不均匀的熔道,下层粉末熔化也未能完全填充该区域,从而降低了成形质量,并且粉末床内部的大空隙导致了样品孔隙增加。
图9

图9 3种粒径样品水平和竖直截面孔隙分布的OM像
Fig.9 OM images showing horizontal (a1-c1) and vertical (a2-c2) pore distributions of PSD1 (a1, a2), PSD2 (b1, b2), and PSD3 (c1, c2) samples
图10统计了几个不同能量密度下成形样品的相对密度。经过表面粗磨后,PSD2和PSD3相对密度均超过99%,其中PSD2相对密度可达到99.8%,比PSD3高0.4%,比PSD1高1.4%。PSD1因其内部较多的孔隙,成形密度最低,且能量密度为130 J/mm3时,密度明显下降,对能量密度变化更为敏感,说明AlSi10Mg粒径对SLM成形质量影响显著。
图10

图10 不同能量密度下3种粒径样品相对密度
Fig.10 Relative densities of samples with different energy densities
4 结论
(1) 开发了基于离散元方法的SLM铺粉物理模型和基于流体热力学的粉末熔化/凝固模型。细粒径粉末Van der Waals力主导了颗粒间相互作用力,粉末团聚程度加剧,流动能力减弱。铺粉将产生大量不均匀的空隙和空缺,严重降低粉末床密度。由于团聚效应,小粒径粉末铺粉所需的层厚至少为5D50。大粒径粉末由于球体间大的几何间隙无法得到填充,铺粉稳定后,粉末床致密度略低于中等粒径粉末。
(2) 不同粒径粉末床存在的缺陷在多层熔化/凝固过程中通过熔融液体流动扩散,可得到一定缓解。
(3) 细粉末样品具有最平坦的表面,但由于其粉末床内存在大量空隙,SLM成形时内部气孔无法全部逸出,形成较多孔隙,致密度最低。而粗粉末由于粒径接近或超过激光光斑直径,易产生成未熔,降低了致密度。
(4) SLM成形AlSi10Mg对粉末粒径敏感性强。中等粒径粉末SLM可加工性最好,相对密度可达到99.8%,分别比细粒径和粗粒径粉末高1.4%和0.4%。
来源--金属学报