分享:纳米金属结构材料的韧化
金属结构材料因其独特性能(高强韧、耐高温等)在航空、航天、航海、军工、核电、化工、建筑和桥梁等领域具有广泛的工业应用。当前金属结构材料面临着挑战和发展机遇,而我国金属结构材料行业亦面临发展优势和不足。纳米金属结构材料因其高强度而在有节能减重要求的领域(如交通运输)具有工业应用前景,但其低的断裂延伸率限制了工业应用。纳米金属低的拉伸塑性是由其低的应变硬化率导致,而低的应变硬化率进一步由纳米金属过小的晶粒尺寸难以积累位错所致。经过20多年的研究,纳米金属低的断裂延伸率可通过纳米析出、孪晶界、多尺度晶粒分布、孪生、相变、降低位错密度、纳米梯度结构、异构等组织调控得以改善,这些韧化方案提高了纳米金属位错积累能力和应变硬化率,并最终提高了韧性。纳米金属结构材料的拉伸性能除了与其微观结构密切相关,还与变形温度、应变速率、拉伸样品尺寸及加载应力状态相关。
关键词:
金属结构材料是国防军工和国民经济建设的基材,在交通运输、楼宇桥梁、三航武器、核电化工、医疗器械等领域均有不可替代的重要应用,其力学性能指标的优异性和使役过程中的稳定性决定了上述工业领域的先进性和安全性。比如,上海中心高632 m,用钢105 t,是由钢结构撑起的摩天大楼。2018年开通的港珠澳大桥有15 km是全钢结构钢箱梁,是世界最长、最重的钢铁大桥;主体桥梁总用钢量达到了4.2 × 105 t,相当于10座“鸟巢”或60座埃菲尔铁塔的用钢量。
图1
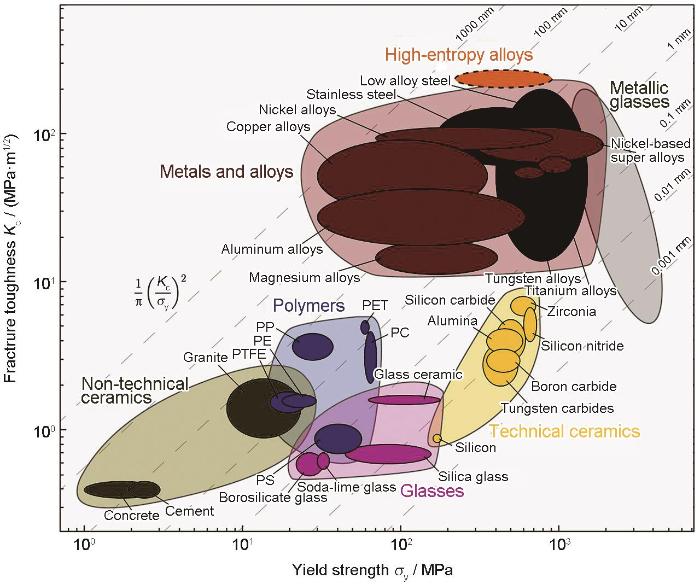
目前我国金属的结构材料行业优势与不足并存。我国的钢铁、Al、Mg、Ti等有色金属以及稀土金属多年来产量世界第一,但是金属行业多而不精、大而不强、多量少质。先进钢材(高端轴承钢、高强耐蚀不锈钢和超高强韧航空用钢)和高温合金是我国“卡脖子”的金属材料。同时,我国钢材、铝材等金属在中美贸易战中被首批加征关税。
目前我国的年钢铁产量近9 × 108 t (实际产能1.25 × 109 t,人均近1 t),占世界钢铁年产量的一半以上,连续13年居世界第一位;尽管如此,我国每年仍需要进口特种钢近1 × 107 t。我国电解铝产量近4 × 107 t,占世界产量60%,多年位居全球第一。此外,我国同时是世界上稀土资源最丰富的国家,稀土储量超过全球总储量的一半,提供了全球稀土需求量的90%;但仍需要拓展具有高附加值的高科技稀土产业链。我国Mg年产量(106 t)占世界80%,Ti (近105 t)、Au (400 t)、Ag (近104 t)、In (400 t)、W (储量世界第一、年产数百吨)等稀有金属产量均连续10年以上位居世界第一。
尽管如此,我国金属行业低端产品严重产能过剩,高端产品却严重不足、多依赖进口。以金属Ti为例,我国的钛工业处于高低端供需状况迥异的结构性失衡状态。我国是钛矿资源的储量大国,但纯度较高的钛精矿仍需依赖进口;我国海绵钛产量已位列全球第一,海绵钛总体供给量远远大于需求,但航空航天级高端海绵钛产能仍然不足;在钛材加工领域,高端钛材产能相对匮乏,民机用钛几乎全部来自进口,而较为低端的工业用钛竞争亦日益激烈。
1 金属结构材料面临的挑战、机遇和新要求
当前,传统金属结构材料的发展面临着2大挑战和2大机遇。
挑战(一):来自高分子材料和陶瓷材料的崛起。近年来,高分子材料(尤其是工程塑料)原料丰富、价格便宜、产量以惊人的速度增长;先进陶瓷材料也崭露头角。材料领域从以往的金属材料“一统天下”的局面转变为金属、陶瓷、高分子材料“三足鼎立”的新格局。比如,美国波音787客机所用有机高分子复合材料比重为50%,而波音777复合材料比重仅为12%;金属结构材料的比重为45%,其中轻质铝合金占比为20%,而波音777铝合金占比达50%。大量轻质、高强韧复合材料的使用使波音787燃油效率提高了20% (图2)。
图2
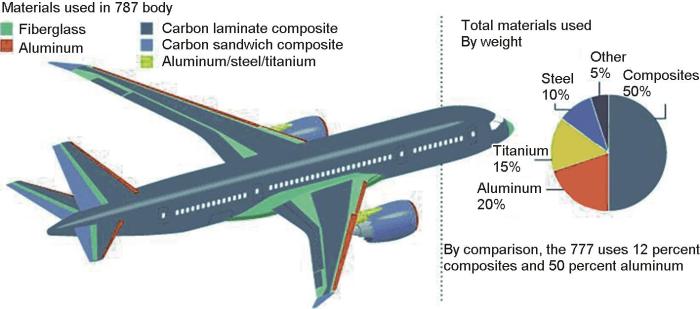
图2 美国波音787客机所用复合材料和金属结构材料的比例
Fig.2 Proportion of composite and metallic structural materials used in the U.S. Boeing 787 airliner
挑战(二):来自金属结构材料自身的不足。主要是能源、资源和环境3个方面:金属材料经过近百年的大力发展,多种金属矿产资源日渐紧张;同时,金属工业是能源的重要消耗者,也是环境的污染者。
机遇(一):新型高端金属结构材料的出现给传统金属结构材料的发展带来了机遇。近年来出现的块体纳米金属、非晶和高熵合金具有更高的强度、耐磨性等优异力学性能,可大幅提高金属结构材料的比强度,从而节省资源、节约能源、减少污染。因此,发展高端金属结构材料及其制备技术是解决我国金属行业存在问题的关键,也是衡量国家科技水平和综合国力的重要标志,更是我国突破相关领域技术壁垒的保证。
机遇(二):国际和国内对金属结构材料的支持政策给传统金属结构材料的发展带来了机遇。国际上,欧盟“欧洲冶金计划”、俄罗斯“2030年前材料与技术发展战略”等相继出台;同时,我国的“十四五”国家战略与新兴产业发展规划等均制定了高端金属结构材料的制造和研究计划。国家科技中长期发展规划明确把“新材料、高技术改造提升电子信息、航空航天、能源设施、船舶舰艇、交通运输等传统产业”列入重点发展的技术产业,而这些关键产业的发展不但与先进金属结构材料的发展密不可分,同时对金属结构材料的综合性能提出了更高的要求。比如,航空航天和交通运输领域需要更高比强度和比刚度的金属材料来节约能源和资源。
我国国防工业及国民经济建设主战场对新型金属结构材料提出了轻、刚、强的需求。新型轻质、高强金属结构材料是支撑各类高性能武器装备的“骨骼”:轻,是指材料被动抵抗地球引力的能力(比强度)要大;刚,是指材料在外力作用下抵抗变形的能力(弹性模量和屈服强度)要大;强,是指材料在外力作用下抵抗破坏的能力(韧性)要大。因此,纳米金属结构材料韧化具有重大意义。
航天和航空发动机、电力和原子能等能源领域用燃气轮机(简称“两机”)是国家高新技术水平及科技实力的重要标志,也是一个国家综合实力的体现。现阶段,我国内燃机应用市场基本被美国通用、德国西门子、日本三菱等国外燃机机组所垄断。未来“两机”对其高温核心部件(如工作叶片、涡轮盘、轴承、燃烧室等)用高温材料更是提出了轻质、高强韧、耐疲劳、抗冲击、耐高温、高可靠性等的迫切需求。在航空航天领域,随着高性能发动机对提高推重比(推力/重量,thrust weight ratio,TWR)和降低耗油率(单位耗油量,specific fuel consumption,SFC)的持续要求,发动机涡轮前燃气温度(turbine inlet temperature,TIT)已由20世纪40年代的大约800℃发展到现在的大约1700℃,未来推重比约20的发动机将会超过1900℃。涡轮盘合金的承温要求也由大约550℃提高至现在的大约700℃,未来将会超过800℃。在蒸汽和燃气轮机领域,随着对提高热机效率及减少污染排放物(PM 2.5/10,SO2)的强烈需求,发电机组的核心部件的温度要求也由现在的大约560℃提升至约760℃。未来的高温环境要求超出了目前高温合金的使用极限,比如,镍基合金承温能力由于γ'析出相的粗化和回溶而无法跨越750℃,多晶TiAl合金因在700℃、3000 h组织分解而只能用于700℃以下的服役环境。这让人们不得不寻找和研制新一代耐高温材料,显然,新一代耐高温材料是国家“卡脖子”的核心材料,也是每个国家的关键战略材料。
除了上述航空航天和能源领域对高温材料的迫切需求,火炮等身管武器对身管材料也提出了高强、高韧、耐烧蚀、抗冲击、耐高温、抗疲劳、耐磨损、抗氧化等极其苛刻的要求,这是因为弹药的发射对身管产生了高温、高压、高速冲击、磨损、烧蚀、疲劳、氧化等极端环境和条件,是热学、力学、化学、材料、机械、工程等多个学科的复杂耦合。目前,制备高寿命身管仍然是国际性难题和现代战争的迫切需求。我国身管武器的寿命和西方发达国家相比仍然落后,某些关键型号寿命仅为西方发达国家的一半。
2 金属结构材料的强韧化
2.1 概念
金属的强度是指金属抵抗永久变形的能力,而位错是金属的主要变形方式,所以对金属的强化始终围绕着位错进行:要么彻底避免位错的发生而使金属的强度接近其理论断裂强度,比如晶须强化;要么通过增加位错密度(加工硬化)、晶界分数(细晶强化)、析出相和弥散相分数(析出、弥散强化)、固溶原子浓度(固溶强化)来增加位错滑移阻力,实现金属的强化(图3)。
图3
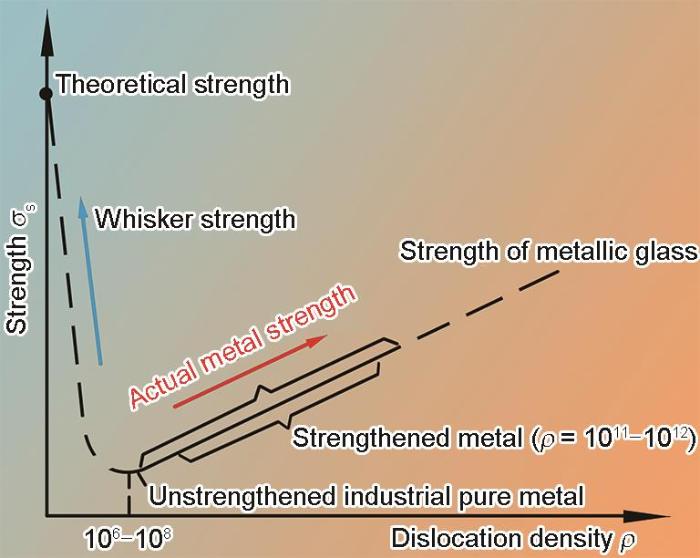
图3 金属强度和位错密度的关系
Fig.3 Relationship between metal strength and dislocation density
金属的韧性是指金属抵抗断裂的能力,可以用材料在断裂过程中吸收的能量来度量,主要包括断裂韧性、冲击韧性和静态韧性。其中,静态韧性是材料准静态拉伸曲线所包含的面积。如图4所示,静态韧性和金属的强度、断裂延伸率和加工硬化率密切相关,单一地增强、增塑未必能增韧。
图4
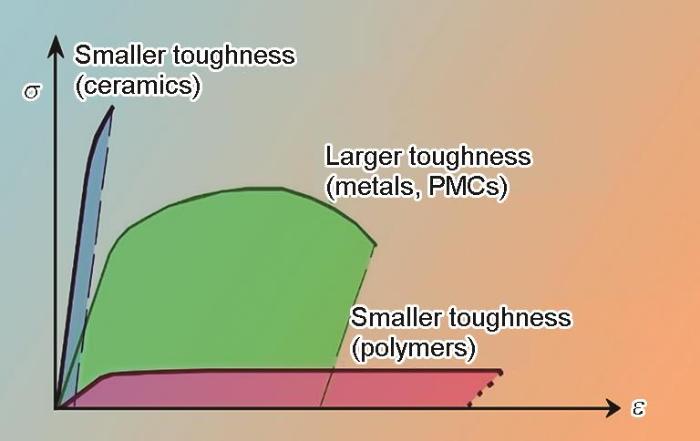
图4 陶瓷、金属和有机高分子材料拉伸曲线示意图以及静态韧性与强度、断裂延伸率、加工硬化率的关系
Fig.4 Schematic of tensile curves of ceramics, metals, and organic polymers and the relationship between static toughness and strength, fracture elongation, and work hardening rate (PMCs—polymer matrix composites; ε—strain, σ—stress)
2.2 块体纳米金属结构材料及其增韧
20世纪80年代德国材料科学家Gleiter[2]提出,如果将粗晶金属材料的晶粒尺寸降低到纳米尺度(100 nm以下,即纳米晶体材料或纳米结构材料)或者微米以下(100~1000 nm之间,超细晶结构材料),材料强度将可大幅度提高。纳米金属的强化仅通过细化材料的微观结构来实现,并不改变材料的成分,从而大大减少对合金元素的依赖。因此,纳米结构材料因其具有高比强度而有着潜在的工业应用前景,并很快在全世界范围内掀起了研究热潮。经过40余年的深入研究,人类在纳米/超细晶金属结构材料的制备、结构特征、力学性能及物理化学性能等方面取得了重要进展。
目前制备块体纳米/超细晶金属材料的方法按形成顺序大致分为2类:利用“自下而上(bottom-up)”原理的两步法和利用“自上而下(top-down)”原理的一步法[2~4]。bottom-up两步法包括惰性气体冷凝法[2]、机械合金化法(球磨粉末冶金)[5]等,即用小的结构单元(纳米颗粒或包含纳米颗粒的微米颗粒)堆积成宏观块体的方法,通常将目标金属先细化成微小粉末,然后采用热压将微小单元致密化并形成大块。此类方法可用来合成晶粒尺寸小于100 nm的块体纳米材料,但是样品尺寸相对较小,而且压制过程会在样品内部留有残余孔隙、杂质及微裂纹等制备缺陷,进而引起服役过程中的应力集中和脆性断裂。top-down一步法是将粗大的晶粒单元利用剧烈塑性变形(severe plastic deformation,SPD)[6]直接细化成细小晶粒单元的方法,此类方法能够制备密度高、界面清洁的大块纳米晶或超细晶金属。目前常用的SPD技术包括高压扭转(high-pressure torsion,HPT)技术[7]、等径角挤压(equal-channel-angular pressing,ECAP)技术[6]、累积叠加轧制(accumulative roll bonding,ARB)[8]、动态塑性变形(dynamic plastic deformation,DPD)[9]、表面纳米化(surface nanocrystallization,SNC)[10~12]和旋锻(rotary swage,RS)技术[13]等。
尽管纳米/超细晶金属结构材料拥有诸多制备方法,但由于其拉伸塑性差、热稳定性低、制备成本高等数个瓶颈难题,目前仍不能大规模工业应用。首先,纳米金属结构材料虽然强度高,但其拉伸塑性很低(通常小于5%),强度-塑性的“倒置”关系仍然存在[14];其次,纳米金属材料的结构稳定性和热稳定性低,在形变和加热条件下晶粒倾向长大;最后,目前可制备的纳米/超细晶金属结构材料样品宏观尺寸有限(仅为毫米和厘米量级)、结构和缺陷可控性差、制备技术工艺复杂、制备成本高。因此,解决上述限制纳米金属结构材料工业化瓶颈难题的关键在于:通过微观结构设计以增加塑性和韧性[15~21];通过成分和结构设计以增加热稳定性[22~31];发展先进制备技术以降低制备成本[32~46]等。
图5
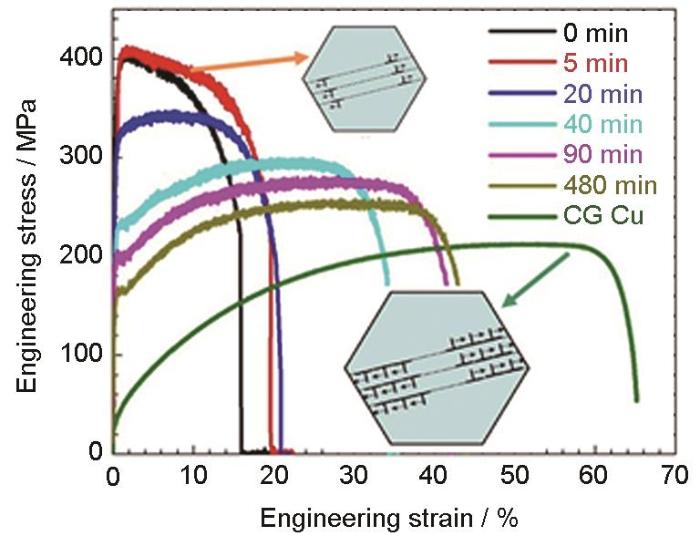
式中,
2.2.1 增韧方案(一):纳米析出相增韧
合金中的纳米析出相按其强度、尺寸以及与基体的位相关系,可同位错产生“切过(cut-through)”和“绕过(pass-by)”交互反应,2种反应机制均会迟滞位错滑移、增大位错积累。在析出过程的初期,析出相尺寸较小,与基体间为共格界面。在合金达到峰值时效状态前,共格强化机制起到重要作用,其作用机理为析出相与基体间保持共格或半共格的关系,使析出相的周围产生弹性应力场,应力场与位错产生交互作用,能够阻碍位错运动,提高基体强度。当析出相足够小且与基体有足够的共格性时,位错能够切过析出相使其随基体发生协调变形,即Kelly-Nicholson机制[54]。首先,原子序列强化所提供的屈服强度(ΔσOS)为[54]:
式中,γAPB为析出相的反相边界能,
式中,αε 为常数,δ为析出相与基体的晶格错配度,G为剪切模量,r为析出相的半径。此外,析出相与基体模量的错配也会引起强化作用ΔσMS[54]:
式中,ΔG为基体与析出相的剪切模量错配度,α为常数。
其中,v为Poisson比,L为析出相间距。
因此,如果保持析出相的体积分数不变,析出相对屈服强度的贡献与其半径的平方根成正比。当粒子半径达到临界值时,强化效果达到峰值,超过该值后,强化效果呈下降趋势(图6)。基于此,2006年Zhao等[56]提出了在超细晶晶粒里引入纳米析出相的增韧方案,并在7075铝合金中率先得以实现(图7[56])。作者首先将经过固溶处理的7075铝合金在液氮中淬火,得到Zn、Mg、Cu等溶质原子在Al中的过饱和固溶体(屈服强度145 MPa,断裂延伸率34%),进而通过液氮轧制制备出超细晶7075铝合金(屈服强度550 MPa,断裂延伸率4%),最后低温时效析出高密度的纳米析出强化相,同时增加了强度(615 MPa)和断裂延伸率(10%)。对比分析发现,拉伸变形后析出相周围积累了高密度的位错,从而增加了应变硬化率和断裂延伸率。该增韧方案随后在超细晶2024铝合金、6061铝合金、镁合金、钼合金、钒钇合金、碳锰钢以及高熵合金中得以证实[57~68]。除了原位析出,纳米强化相还可以通过机械混合、变形碎化等方法引入。
图6
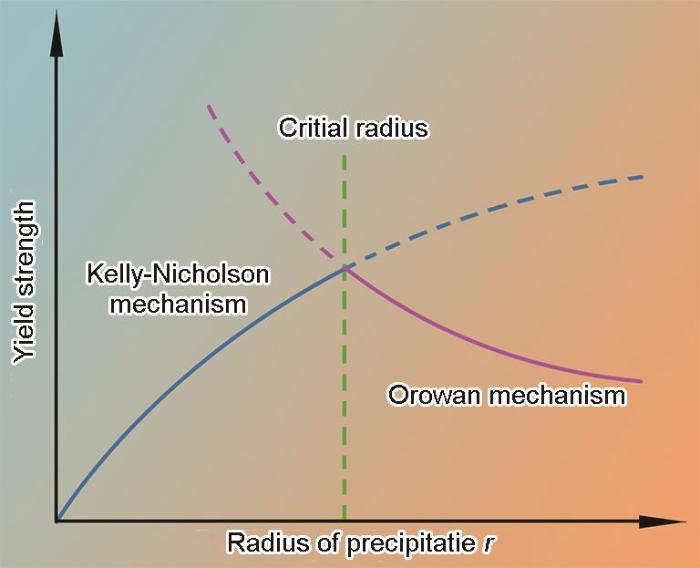
图6 析出相半径对屈服强度的影响
Fig.6 Dependence of the strengthening effect on the radii of precipitates
图7

图7 粗晶(CG)固溶、液氮轧制(NS)、低温时效(NS + P) 7075铝合金的拉伸曲线,拉伸后析出相附近的位错积累,及拉伸前的纳米析出相[56]
Fig.7 Tensile curves of CG solid solution, liquid nitrogen rolling (NS), and low-temperature aging (NS + P) 7075 aluminum alloys (a), dislocation accumulation near the precipitated phase after tension (b-d), and nano-precipitated phase before tension (e-g)[56] (The inset shows dimension of the tensile sample with a thickness of 1 mm)
2.2.2 增韧方案(二):孪晶界增韧
孪晶界可以与位错发生反应,进而积累和增殖位错[69~78]。2004年,Lu团队[79]通过电解沉积技术制备出了纳米孪晶Cu (在粗晶Cu的晶粒里分布着纳米生长孪晶层片),其屈服强度高达980 MPa,断裂延伸率为13%,导电率为粗晶铜的98%,这是因为孪晶界对自由电子的散射作用较小的缘故[80,81]。电镜观察揭示了拉伸变形后的孪晶界处积累了大量位错,从而增加了应变硬化能力和断裂延伸率[56]。电解沉积纳米孪晶铜样品厚度处于微米量级,难以满足大规模工业化应用需求。2006年,Zhao等[82]提出引入纳米孪晶界来增韧超细晶金属的方案,并运用SPD技术制备出了大块纳米孪晶Cu线。首先在室温通过ECAP技术制备晶粒尺寸为数百纳米的超细晶Cu (屈服强度410 MPa,断裂延伸率6%),随后通过液氮拉拔和轧制(ECAP + D + R)在超细晶Cu的晶粒里引入层片间距为数十纳米的变形孪晶(屈服强度500 MPa,断裂延伸率为12%),同时提高了强度和断裂延伸率(图8[82])。
图8

图8 等径角挤压(ECAP)和随后液氮拉拔、轧制(ECAP + D + R)超细晶Cu的拉伸曲线,液氮变形引入的纳米形变孪晶,及孪晶界和位错的反应[82]
Fig.8 Tensile curves of equal channel angular pressing (ECAP) and subsequent liquid nitrogen drawing and rolling (ECAP + D + R) of ultrafine grained (UFG) copper (a), nano deformation twins introduced by liquid nitrogen deformation (b), and interaction of twin boundaries and dislocations (c)[82] (Inset in Fig.8a shows dimension of tensile sample with a thickness of 0.1 mm, b—Burgers vector)
2.2.3 增韧方案(三):多尺度晶粒增韧
2000年,Legros等[84]在温压惰性气体冷凝技术制备纳米Cu颗粒时发现,一定量的纳米晶粒会异常长大成粗晶晶粒(1~5 μm),进而将断裂延伸率从1%提高至3%,遂提出bi-modal概念及其增韧方案。2001年,Lavernia团队[85]运用液氮球磨和热挤压技术制备了超细晶和粗晶混合的5083铝合金(屈服强度高于400 MPa,断裂延伸率为9%),并从断裂机理角度阐明了粗晶晶粒对微观裂纹扩展的迟滞作用。2002年,Wang等[86]运用退火处理,在液氮轧制的超细晶Cu基体里引入了25% (体积分数)微米粗晶晶粒,其屈服强度高于300 MPa,断裂延伸率和粗晶Cu相当。2008年,Zhao等[87]运用Ceracon技术制备了高纯(> 99.7%)、致密(> 99.6%)的bi-modal和multi-modal镍(图9[87]),其屈服强度-断裂延伸率组合优于文献值。
图9
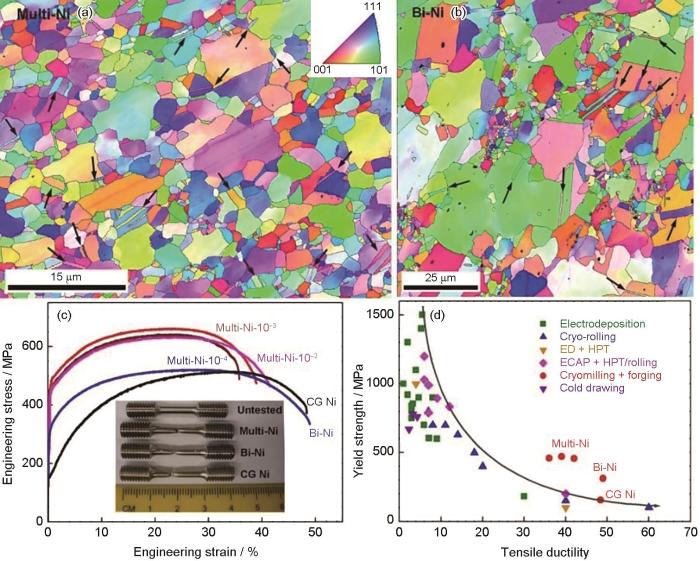
图9 高纯、致密bi-modal和multi-modal镍的微观结构和拉伸曲线以及屈服强度-断裂延伸率对比[87]
Fig.9 Microstructures (a, b) and tensile curves (c) of high-purity and dense bi/multi-modal nickel (Bi-Ni/multi-Ni) and review of yield strength-tensile ductility of nickel (d)[87] (The twins in Figs.9a and b are indicated by black arrows; the inset in Fig.9c shows the picture of the fractured tensile specimens; ED—electro-deposition, HPT—high pressure torsion)
2.2.4 增韧方案(四):TWIP/TRIP增韧
孪生诱发塑性(twinning-induced plasticity,TWIP)和相变诱发塑性(transformation-induced plasticity,TRIP)在高锰钢和不锈钢中有40余年的研究历史[88]。在拉伸过程中,单纯的位错滑移使应变硬化率单调下降,与之不同,孪生和相变可动态地引入孪晶界和相界,从而使应变硬化率先升高后下降,增加了材料的应变硬化能力和断裂延伸率。同理,孪生和相变也会增加纳米金属的应变硬化率和拉伸塑性,如超细晶Fe-Mn合金[89]、纳米hcp结构Co[90]、Cu-Zn合金[91]等。图10[89]为超细晶高锰钢的拉伸曲线,同粗晶相比,屈服强度提高10余倍,而断裂延伸率没有降低。X-射线衍射分析表明超细晶奥氏体相在拉伸过程中产生了马氏体相变,提高了应变硬化率[89]。
图10
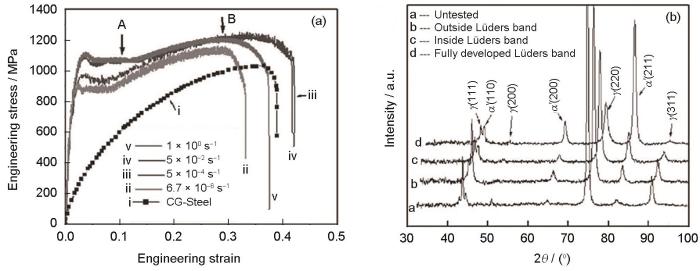
2.2.5 增韧方案(五):降低位错密度增韧
2.2.6 增韧方案(六):纳米梯度结构和异构增韧
图11
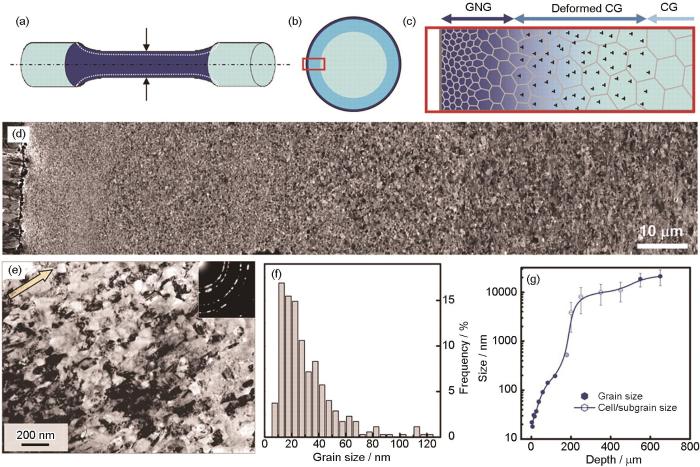
图11 滚压技术制备纳米梯度结构Cu[95]
Fig.11 Gradient nano-grained (GNG) structured copper prepared by surface mechanical grinding treatment[95]
(a) schematic of the tensile bar sample of which the gauge section was processed by means of surface mechanical grinding treatment (SMGT)
(b, c) schematics of the cross-sectional microstructure of the gauge consisting of a gradient nano-grained layer (dark blue) and a deformed coarse grained layer (blue) on a coarse grained core (light blue)
(d) a typical cross-sectional SEM image of a SMGT Cu sample
(e) a cross-sectional bright-field TEM image of microstructures 3 mm below the treated surface (The arrow indicates the processing direction, and the inset shows the electron diffraction pattern)
(f) a transversal grain size distribution from TEM measurements in the top 5-mm-deep layer
(g) variation of average transversal grain (subgrain or cell) sizes along depth from the surface (Error bars represent the standard deviation of grain-size measurements)
2014年,Wu等[96]运用翔实的力学实验揭示出纳米梯度金属的优异强韧性组合(图12a[96])源于其额外的加工硬化能力(图12b~d[96])。纳米层和粗晶层在变形过程中因相互不匹配而产生了复杂的三向应力和应变(图12e和f[96]),进而造成额外的位错积累和加工硬化。2015年,Wu等[97]制备出了高强韧层状钛;2017年,研究者将纳米梯度材料[97]、异质层状材料[98]、双峰晶粒尺寸分布材料[83]和核壳结构材料[99]四大类材料归纳为“异构”材料(heterogeneous materials)[100],并于2019年提出异变硬化(hetero-deformation induced (HDI) hardening)的概念及其位错塞积模型[101,102]。
图12
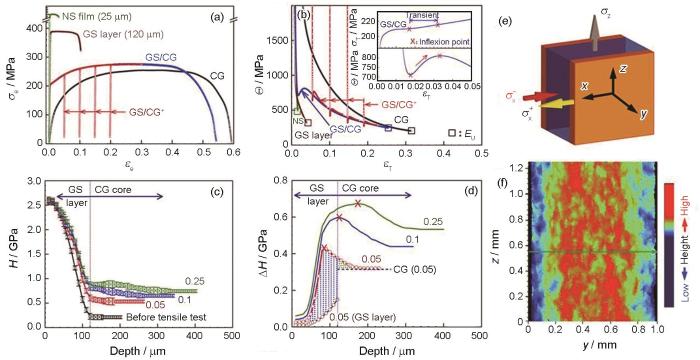
图12 纳米梯度不锈钢的拉伸曲线、应变硬化曲线及复杂应力状态[96]
Fig.12 Tensile engineering stress-strain (σe-εe) curves (a), strain hardening curves (b-d), and complex stress states (e, f) of nano-gradient stainless steel[96] (GS—gradient-structured, NS—nanostructured; Θ—strain hardening rate, εT—true strain, σT—true stress, H—microhardness, ΔH—H increment; inset in Fig.12b shows transient response on the σT-εT curve of the GS-CG sample between two inflection points marked by "×" corresponding to the Θ-up-turn on its Θ-εT curve)
2.2.7 增韧方案(七):改变变形条件增韧
金属结构材料的拉伸性能除了与其微观结构密切相关,还与变形温度、应变速率、拉伸样品尺寸、加载应力状态相关。
图13
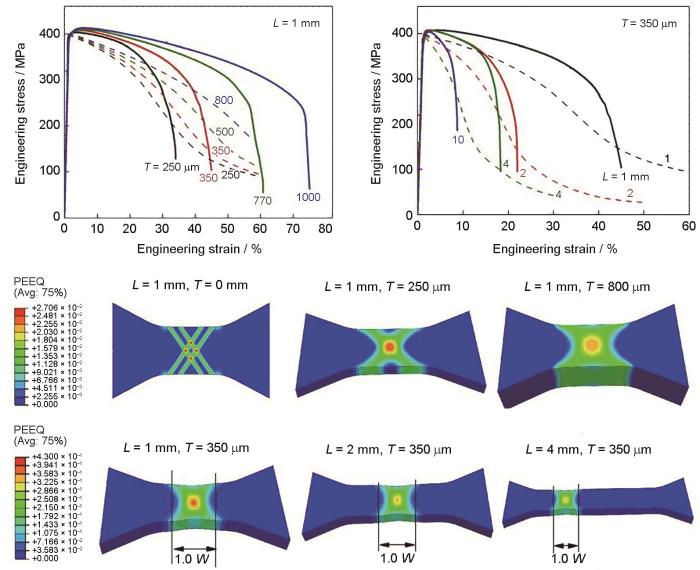
3 小结与展望
纳米金属结构材料因其高强度而具有工业应用前景,但其低的断裂延伸率限制了工业应用。纳米金属低的拉伸塑性是由其低的应变硬化率导致,可通过纳米析出、孪晶界、多尺度晶粒分布、孪生、相变、降低位错密度、纳米梯度结构、异构等组织调控得以改善。这些强韧化策略当中,多尺度晶粒分布、降低位错密度、纳米梯度结构、异构等具有普适性,适用于所有金属;而纳米析出、孪晶界、孪生、相变等具有特殊性,仅适用于失效强化合金和低层错能金属和合金。因此,本综述归纳的强韧化方案应该根据材料的物理特性和实际工艺有针对地选择,例如低层错能的金属可以适当提高孪晶界的引入,中高层错能也能够通过增加应变速率或者降低变形温度来引入孪生,但是对于具有低温脆性的材料,低温无法发挥作用;溶质原子在基体中溶解度较高时,很难实现纳米析出强韧化,此时应以其他强韧化策略为主。纳米金属结构材料的拉伸性能除了与其微观结构密切相关,还与变形温度、应变速率、拉伸样品尺寸、加载应力状态等相关。
尽管上述金属的强韧化方案可以或多或少改善纳米/超细晶金属结构材料低的断裂延伸率,但其低的热稳定性和高的制备成本目前仍然限制着大规模工业应用。因此,近年来很多研究试图提高纳米金属的热稳定性和发展先进制备技术以降低制备成本。对于前者,研究表明通过引入小角度晶界和孪晶界以及层片状晶粒来降低储存能、纳米晶界析出或反应来钉扎晶界迁移可以有效提高热稳定性,此外,最近的研究表明纳米高熵合金因为迟滞扩散效应而具有极高的热稳定性,这为纳米高熵合金在高温环境的应用提供了可能。
SPD方法已经被证明是一种有效的制备超细晶乃至纳米晶结构材料的方法,已广泛应用于各种金属材料的制备。但目前多数SPD方法可加工的工件尺寸往往很小,并且需要大功率的设备及昂贵的模具,以致于难以广泛应用于工业生产中,如ECAP和HPT工艺。对于纳米金属工业化的迫切需求,各种制备方法的工艺参数和材料参数对最终材料组织和性能的影响仍需系统化研究。此外,开发大块材料的SPD变形模具和工艺以获得更高应变量、提高细化晶粒的效率也是促进SPD工业化的途径之一。最后,除了现有的SPD方法,开发新的先进纳米金属制备技术以降低其制备成本也是解决目前纳米金属制备瓶颈难题的方法之一,如ARB技术和旋锻技术等。
纳米材料的塑性变形理论还有待进一步研究。首先,到目前为止,科学界的研究使用了大量的纯金属和商用合金。而这些合金往往是为粗晶材料设计和优化的,可能还不是实现纳米结构材料的最佳性能的成分配比。因此,目前最重要的方向是从底层出发,设计纳米结构材料,从微观组织的角度激活金属材料高强度和高延性的机制,以获得最佳的力学、磁学以及电学等诸多性能。其次,针对小尺寸纳米结构金属需要规范新的力学行为测试方法,譬如小/微型狗骨拉伸测试标准,以适用于整个材料科学界和新兴行业。再者,需要开发新的方法来提高纳米结构材料的强度和延性,需要更基础的研究来更好地理解延性-微观结构的本构关系。