分享:连铸结晶器内高温熔体多相流模型化研究进展
1.
2.
连铸结晶器内高温熔体多相流的运动状态强烈地影响高品质钢的洁净化、均匀化和精细化。该高温熔体多相流为非稳态湍流,同时耦合传热、传质、相变、反应、电磁力等诸多过程,形成了十分复杂的非稳态、非线性、非平衡多物理场,很难通过现场测试对其内部的各种物理量进行在线测量。在确保流动和凝固过程相似的情况下,开展物理模拟实验以及对其多尺度传输现象的数值模拟,已成为阐述连铸坯各类缺陷形成机理的首选。然而,与传统流体力学问题相比,冶金高温熔体多相流的突出特点是物性变化大、本构关系式复杂、相界面影响因素多及边界物理量梯度大等,且连铸结晶器内多物理场存在连续相大界面变形、离散相颗粒输运以及连续相-离散相转变等复杂多变的多尺度界面现象,以及多尺度的湍流涡结构,这些都给高温熔体多相流模型化研究带来极大困难。相比于单相流,多相流具有相界面拓扑形状变化的特征,本文从离散流界面尺度分布性、混合流界面跨尺度性、凝固界面多尺度性、以及湍流在揭示多尺度相界面结构中的作用等4方面回顾了连铸结晶器内高温熔体多相流模型化的研究进展,并展望了未来可能的研究方向。
关键词:
高品质连铸宽厚板和大圆坯是重要的战略资源,主要用于国防大型舰艇、核电站安全壳、深海钻井平台、高压锅炉管、轴承套、高速列车轮等领域。探伤缺陷是连铸宽厚板的主要质量缺陷,形成原因包括气泡/夹杂物、夹渣、氢致裂纹、中心偏析和疏松等[1~8],通过分析现场大量钢板探伤检测图谱,发现目前最不受控的是非稳态、非均匀的气泡/夹杂物和夹渣缺陷[9~14],它们已成为制约连铸宽厚板质量进一步提高的瓶颈。目前大圆坯主要采用模铸的方法制备,但模铸的生产效率、金属收得率较低。用连铸代替模铸能够实现模具钢制备的高效率和高收得率,但随着连铸坯截面扩大,单位长度铸坯热容量增大、散热面积减小,凝固方式由快速凝固向慢速凝固转变,造成芯部钢液的热对流和溶质元素的再分配过程加剧[15,16],一些由凝固速率慢导致的溶质元素宏观偏析及疏松缩孔等问题也越发突出。
向炼钢反应器中喷吹惰性气体搅拌钢液已成为现代冶金的重要技术手段。塞棒或上水口吹Ar作为保障连铸结晶器顺行的关键技术,其作用是防止水口堵塞、防止吸气、促进非金属夹杂物上浮,从而提高钢坯质量。但小气泡和黏附在其表面的非金属夹杂物一旦被凝固坯壳捕捉,就会造成铸坯“气泡类”缺陷,恶化产品质量;吹Ar还会造成渣/金界面剧烈波动并可能发生乳化,以致于液渣在上回流或漩涡的作用下被卷入钢液中,形成卷渣。连铸过程中高温熔体(钢液、熔渣、惰性气体)多相流的运动状态强烈地影响高品质钢的洁净化、均匀化和精细化。结晶器内的高温熔体流动为非稳态湍流,同时耦合传热、传质、相变、电磁力、多相流等诸多过程,形成了十分复杂的非线性、非平衡多物理场,如图1所示。该场存在连续相(渣/金界面、凝固前沿等)大界面变形、离散相(气泡、夹杂物、渣滴、等轴晶粒等)颗粒输运以及连续相-离散相转变(大气团的形成与破碎、渣滴的形成与再融合等)等复杂多变的多尺度界面现象,以及多尺度的湍流涡结构,常规的宏观连续理论和方法对描述这类多尺度相界面共存及转变问题面临根本性困难。
图1
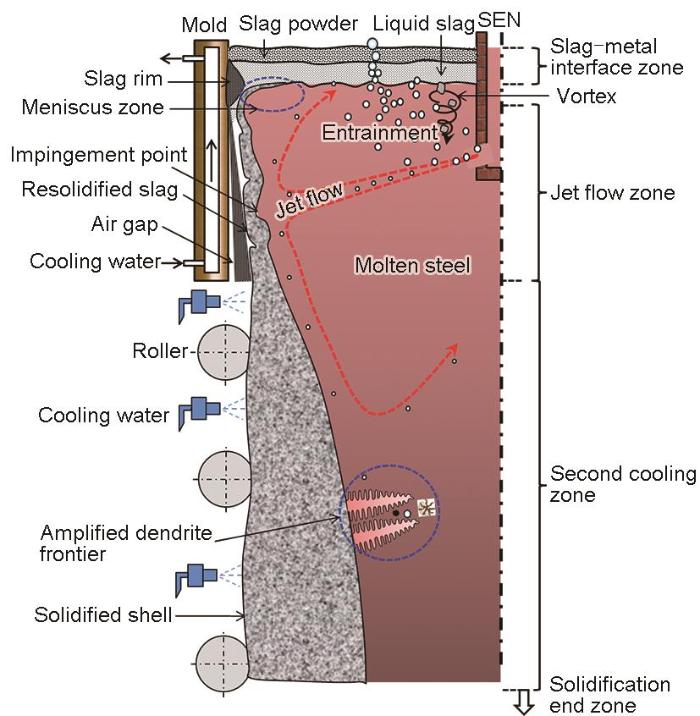
图1 结晶器内多相、多物理场、多尺度特征
Fig.1 Multiphase, multi-physics, and multi-scale characteristics in the mold (SEN—submerged entry nozzle)
大尺寸的宽厚板和大圆坯造价高,加上连铸过程复杂的高温动态环境,直接的实验研究既不经济、难度也极大。针对宽厚板和大圆坯研制长期以来过度依赖“制备-测试-制备”反复循环的“试错法”,致使研制周期长、耗费高、效率低等问题,在确保凝固过程相似的情况下,开展凝固过程的热模拟实验,以及对其多尺度传输现象的数值模拟,已成为阐述宽厚板和大圆坯各类缺陷形成机理的首选。相比于单相流,多相流具有相界面拓扑形状变化的特征,其复杂多变的界面结构,在瞬态时间上具有宽广的空间尺度范围,即表现出时间和空间2个方面的多尺度特征[17]。根据流动形态与界面尺度的关系,连铸结晶器内的高温熔体多相流的界面多尺度通常涉及几个方面的问题:离散流界面尺度分布性、混合流界面跨尺度性、凝固界面多尺度性、以及湍流在揭示多尺度相界面结构中的作用等。
1 离散流界面尺度分布性问题
离散流界面尺度分布性问题源于离散气泡或非金属夹杂物的聚并和破碎效应,造成离散气泡或非金属夹杂物具有较大的尺度范围,并表现为小尺度相界面的不连续性。例如,初始均一粒径(近似) Ar气泡经上水口弥散砖或塞棒进入水口后,由于受到钢液湍流的作用,气泡间会发生强烈的聚并和破碎现象,造成进入结晶器内的Ar气泡具有较广的粒径范围,在结晶器内形成复杂的多尺度泡状流。冷态物理实验被广泛用于研究结晶器内的多尺度泡状流[18~25],研究者[22~25]采用水模型实验分别测量了不同参数影响下的水口或结晶器内的气泡粒径分布,揭示了吹Ar连铸结晶器中气泡的分布及运动规律,发现水模型中可采集的气泡平均粒径范围在0.5~5 mm之间。近期,Wu等[25]采用高速摄像机和ImageJ软件识别并成功提取了不同粒径气泡的运动轨迹,如图2[25]所示。采用低熔点合金和惰性气体模拟连铸结晶器中的多尺度泡状流也是常用的研究方法之一[26~31],如陈芝会等[26]采用Pb-Sn-Bi合金研究了低频行波磁场下磁感应强度、拉速、吹Ar量对气泡运动行为及分布的影响;Timmel等[27,28]利用X射线技术测量了GaInSn合金熔液中Ar气泡的数量和粒径分布,发现气泡粒径在1~10 mm之间;Ren等[29]采用液态Hg和超声Doppler测速仪研究了电磁场对结晶器流场及液面波动的影响。然而这些实验均采用冷态水模型或低温合金实验,实际高温钢液内的Ar气泡运动状态仍不可直接观察和测量。目前,实际连铸坯中的气泡缺陷只能通过对铸坯成品进行检测得到,部分学者[12,32~34]采用X射线技术、铸坯刨层检测等手段在凝固后的板坯中发现了不同尺寸的气泡类缺陷,气泡粒径(Dm)在0.02~3 mm之间,并获得了气泡和非金属夹杂物在铸坯内的三维空间分布,如图3[12]所示。
图2

图2 不同粒径气泡的运动轨迹[25]
Fig.2 Trajectories of bubbles with different sizes[25]
(a) 1-1.5 mm (b) 1.5-2 mm (c) 2-2.5 mm (d) > 2.5 mm
图3
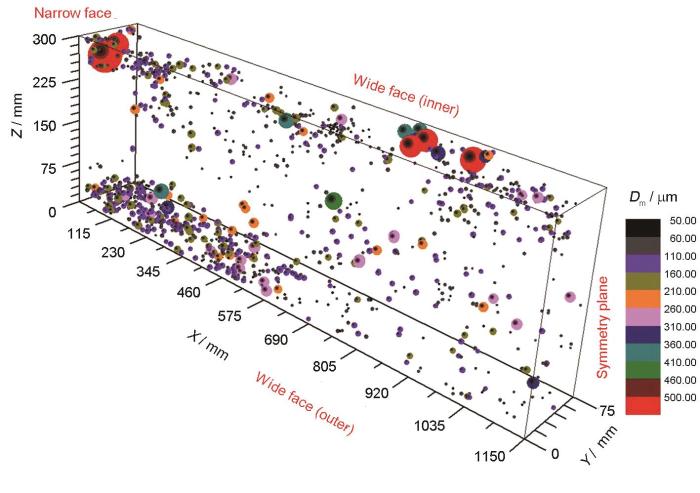
图3 实际连铸坯内气泡及夹杂物空间分布[12]
Fig.3 Spatial distributions of bubbles and inclusions in actual slab (Dm—bubble size)[12]
近期,本文作者通过水模型实验观察到了结晶器内离散气泡的群体运动特征,如图4所示,将气泡的运动分布分成2部分:气泡群和脱群气泡。气泡群内,两相运动由气泡群主导,气泡密度较大,易发生气泡间的碰撞聚并;气泡群外,脱群气泡的运动由钢液主导,气泡弥散分布,难以发生碰撞聚并。脱群气泡的数量决定了被凝固坯壳捕捉的气泡量,因此减少脱群气泡的产生对铸坯质量的提升至关重要。气泡的这种聚团效应实现了微观颗粒向宏观结构的转变,使系统行为发生质的改变,其传递性能与离散体系截然不同。一般而言,界面现象在这一尺度上发挥了重要作用。目前结晶器内两相流实验研究多偏重于从冷态、等温实验现象出发去探索泡状流中的一些表观参数变化规律,如流型图、液面波动、含气率、离散气泡的空间分布等;而对结晶器内气泡群存在的稳定性条件以及脱群气泡的产生机理仍缺乏深入的认识,有很多基本理论问题亟待解决。
图4

图4 结晶器内的气泡群与脱群气泡
Fig.4 Bubbles cluster and bubbles outside cluster
(a) macro-distribution of bubbles (b) 0 ms (c) 15 ms (d) 30 ms (e) 40 ms
由于多相流体系大多是非线性、非平衡的,从实验和理论的角度研究体系的时空多尺度相界面结构还有很大困难,而且高温钢液不易直接观察和测量,因此计算流体力学(computational fluid dynamics,CFD)成为研究高温熔体多相流不可或缺的关键手段,有助于从物理层面理解流动机制并为工程应用提供相关的分布型数据。基于连续介质假设的经典力学方法,存在Euler和Lagrange 2种体系,其中Lagrange体系如离散相模型(discrete phase model,DPM)能够相对容易地描述离散粒子的运动行为,因而在求解结晶器内非金属夹杂物、Ar气泡的运动行为及分布的研究中得到广泛应用[35~45],研究者[9~11,35~41]建立了不同机理的夹杂物/气泡捕捉模型,揭示了气泡/夹杂物在结晶器内的运动和捕捉位置,如图5[10]所示。Zhang等[44]和Yang等[45]通过在DPM中引入气泡的聚并和破碎模型,分析了结晶器内的多尺寸泡状流运动特征。但Lagrange体系存在2点不足:一是忽略了离散相颗粒体积,无法给出几何意义上的相界面;二是涉及大量粒子时对计算机性能要求过高。针对小尺度相界面(小于网格尺寸)不连续性问题,一种基于平均场的Euler-Euler双流体模型(two-fluid model,TFM)展示了较好的适用性,该模型简化了小尺度相界面的几何边界描述,并在源项中添加了相间作用项。部分研究者[46~53]采用单一气泡粒径的TFM研究了结晶器内气液两相流动行为,得到了气液两相流动的宏观相分布规律,如Liu等[51]通过模拟预测得到了与实际现场发现的渣眼现象吻合较好的预测结果,见图6[51]。
图5

图5 夹杂物在凝固坯壳上的捕捉位置[10]
Fig.5 Locations of captured inclusions on solidified shell[10]
(a) 1.5 s (b) 3.0 s (c) 10 s (d) 30 s (e) 100 s
图6

图6 结晶器上表面的渣眼分布[51]
Fig.6 Locations of exposed slag eyes on the top surface of the mold[51]
(a) industrial scene (b) numerical prediction (αg—gas volume fraction)
近年来,基于群数密度函数的群体平衡模型(population balance model,PBM)得到了快速发展,该方法根据弥散相气泡的微观行为机制建立气泡相群数密度平衡方程,将气泡的微观现象(破碎、聚并、长大等)与其宏观属性(粒径、表面积等)联系起来,是目前研究弥散相系统的有效工具。该方法采用内、外2个坐标系描述与气泡群相关的变量,内坐标系是指描述气泡尺寸、表面积等内部属性的坐标系,外坐标系是指由流体对流和扩散决定的气泡时间、空间坐标系。研究者将PBM与TFM相结合分别构建了多气泡组质量传递(MUltiple SIze Group,MUSIG)模型[54~58]和平均气泡数密度(average bubble number density,ABND)模型[59],考虑了不同的气泡聚并、破碎机制。2种模型的预测结果均能够揭示结晶器内气液两相流的动力学行为在空间、时间上的变化规律及气泡尺寸变化规律。如图7所示,分别给出了水模型实验及2种模型预测的浸入式水口内的含气率分布特征。通过定性比较,实验结果中的水口壁面低含气率特征和水口出口处高含气率特征能被较好地呈现在模拟预测结果中。
图7
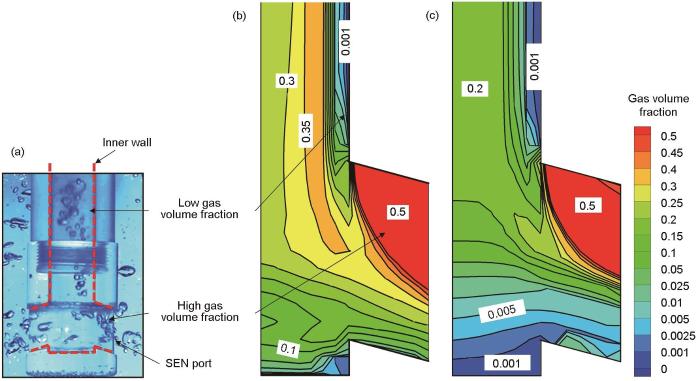
图7 实验与模拟水口内含气率分布对比
Fig.7 Comparisons of gas void fraction profiles inside the SEN between experiment (a) and MUltiple SIze Group (MUSIG) model (b) and average bubble number density (ABND) model (c) simulations
PBM能否准确地预测气泡粒径分布,关键在于是否能够建立合理的气泡聚并和破碎模型。然而气泡的聚并和破碎机理相当复杂[60~63],其中,气泡聚并机理主要有:湍流涡机理和大气泡尾涡机理;气泡破碎机理主要有:湍流涡碰撞机理、液相剪切力拉伸机理和大气泡表面不稳定性机理。而且,以上这些机理模型均是基于常温水模型推导而来,是否适用于高温熔体当中的Ar气泡聚并和破碎行为,还有待于进一步深入研究。
2 混合流界面跨尺度性问题
混合流界面跨尺度性现象源于流动形态的转化,即连续相大尺度界面与离散相小尺度界面的相互转变。在连铸结晶器内,当渣/金界面钢水流速过快、剧烈波动或出现漩涡时,保护渣会被卷入钢液形成渣滴(即卷渣),造成了从连续相渣/金界面向离散相渣滴的转变;反之,渣滴在钢液流场的影响下会上浮,当再次到达渣/金界面后很容易与原渣层融合,实现离散相渣滴到连续相渣/金界面的转变。大量的冷态实验被用于研究结晶器内的卷渣现象和卷渣机理。其中,结晶器液面波动与卷渣行为联系密切,可以较好地反映卷渣程度且易于观测,因此关于卷渣的早期研究集中在液面波动强度的量化。Teshima等[64]经过大量实验数据分析,提出了液面波动指数(F数),涉及钢液密度、出钢量、射流冲击速率、射流倾角、冲击深度、结晶器断面尺寸等参数,可间接评价卷渣程度。之后,研究者[65~67]对于不同的钢种和操作工况归纳出了相应的F数适用范围。经过大量的工业实践和实验研究,发现卷渣机理主要分为3类[68~73]:剪切卷渣、漩涡卷渣和气泡冲击卷渣。其中,剪切卷渣是最为常见的卷渣形式,其实质是渣层和钢液间剪切流动引起的相界面不稳定性,因此对剪切卷渣影响最为直接的因素是钢液表面流速,研究者[72,74~77]通过大量实验研究给出了引起剪切卷渣的临界表面流速。漩涡卷渣是由结晶器两侧不对称流动引起的,在流动较弱的一侧会形成漩涡,漩涡强度较大时,可将保护渣抽吸进入钢液,如图8[78]所示,形成原因主要与滑动水口、水口倾角、水口偏斜度、水口结瘤、塞棒位置、中间包底部非对称流动、水口两侧吹Ar不均等因素有关[69,79~86]。气泡冲击卷渣是指当气泡进入渣层并在渣/金界面或渣层内破裂时,产生的冲击力致使保护渣剧烈波动并进入钢液[87,88],这一作用与上升气泡簇的流速相关,而气泡簇流速与吹气量直接相关,因此部分研究者将产生卷渣时的吹气量定义为临界吹Ar量[88]。
图8
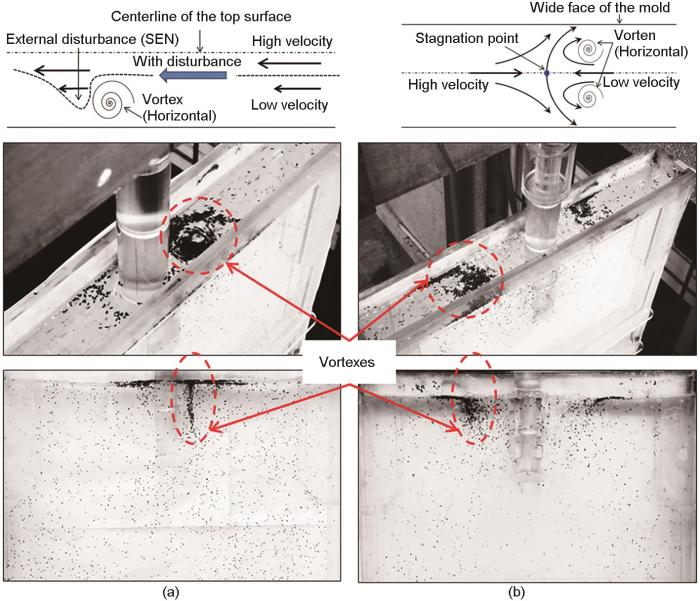
图8 水模型实验中的漩涡卷渣现象[78]
Fig.8 Vortex slag entrapment phenomenon observed in water model experiment[78]
(a) near SEN (b) near the quarter width
另外,结晶器渣/金界面乳化现象将会显著降低渣/金界面的界面性质(浸润性和表面张力等),从而加剧卷渣,恶化铸坯质量。Chung等[89]和Han等[90]采用X射线成像技术动态观察了气泡在金属液和熔渣中的传输过程,考察了气泡、金属液滴在渣相中的乳化现象。乳化行为与渣/金、渣/气界面处的剪切力分布息息相关[91~94],剪切力引发的熔渣乳化与卷渣有3种不稳定机制[68,73,74],即Kelvin-Helmholtz不稳定性、Tylor-Saffman不稳定性和Fluid流动不稳定性。部分研究者[92,93]通过理论和实验分析定量描述了结晶器内的乳化和卷渣行为,但主要针对等温的冷态水模型,而实际高温熔体渣/金界面处存在较大的温度梯度和浓度梯度,由此引发的Marangoni效应[95] (因界面张力梯度引起的流动)在渣/金界面处变得突出,进而影响乳化和卷渣行为。Zhou等[96]采用实际高温熔体实验剖析了渣/金界面润湿行为和界面张力之间的内在相互影响机理,其结果也反映了Marangoni效应在渣/金界面处的作用。Liu等[51,52]采用水模型实验观察到了渣金界面附近的乳化现象,发现主要是由气泡聚集造成的,或可称为气-渣乳化现象,如图9[51]所示。
图9

图9 水模型实验中的乳化现象[51]
Fig.9 Emulsifying phenomenon observed in water model experiment[51]
(a) top surface of slag layer
(b) wide face of the mold
多尺度相界面共存及不连续性的数学描述一直是多相流数值模拟面临的最大困难。针对大尺度相界面(远大于网格尺度)不连续性问题,一种基于标识函数的界面捕捉模型(interface-capturing model,ICM)被广泛采用,VOF和Level Set为当前主流的ICM。ICM直接从原始的Navier-Stokes方程出发,采用标识函数统一系统方程的描述,避开了平均场的处理,没有人为地丢失系统信息,被广泛应用于模拟结晶器内气-钢-渣三相界面行为[97~108],目前研究成果主要集中于捕捉渣/金界面的波动、渣眼分布、剪切卷渣等方面,如Liu等[51,52]和Li等[106~108]采用ICM方法计算了结晶器内钢-渣-气多相流,复现了卷渣、渣眼等现象,如图10[52]所示;并基于简化的管流模型提出了新的液面波动数——J指数。虽然采用ICM可以得到结晶器或钢包内的渣滴尺寸[106~108],但受到网格尺度的限制,无法捕捉小于网格尺度的渣滴;且界面以空间几何尺度显式的表征,无隐式的物理尺度表征。另外,ICM中多相速度共场的处理使其在相间作用的描述上凸显不足,尤其是在界面相间速度差较大时,需要补充界面摩擦力。如前面所述,TFM可描述小尺度相界面(小于网格尺度)的平均物理尺度,但对于大尺度相界面,由于数值扩散导致其无明确的相间几何边界。因此,2种模型都无法同时有效地描述混合流中大小尺度共存的界面结构。耦合ICM和TFM是解决混合流界面跨尺度性问题的思路,但关键是要澄清不同尺度间的相互作用关系和耦合的原则,建立控制系统的稳定性条件及调控机理。近期,Sun等[109]发展了多尺度气泡桥接模型,实现了ICM和DPM 2种方法的耦合,即Euler和Lagrange体系下的混合气泡共存及相互转变,并首先将其应用到电解铝领域,如图11[109]所示,期待未来将其应用到连铸领域。
图10

图10 数值模拟捕捉到的漩涡卷渣现象[52]
Fig.10 Vortex slag entrapment phenomenon predicted by numerical simulation[52]
(a) interface of slag and steel
(b) 20 mm below the slag-steel interface
(c) flow field in the mold
图11

图11 底部视角下的气泡聚并过程[109]
Fig.11 Transient dumbbell coalescence process from a bottom view[109]
(a) experiment (b) numerical simulation (DPM—discrete phase model, ICM—interface-capturing model)
3 凝固界面多尺度性问题
合金凝固过程是相界面热和溶质传输的过程,也是一个耦合扩散、热力学非平衡、结晶各向异性和对流多物理场作用的问题,涉及宏观(热溶质对流、外场强迫对流、夹杂物漂浮等)和微观(溶质析出/扩散、局部溶质再分配、晶粒形核和生长等)不同尺度间的传输,直接导致连铸坯内部缺陷的形成。在确保凝固过程相似的情况下,开展凝固过程的热模拟实验,是阐述铸坯凝固组织及内部缺陷形成机理的有效办法。但金属的不透明性阻碍了对凝固过程中液相流动的实时观测。研究[110~128]表明,某些水溶液(如NH4Cl)和有机透明物质(如丁二腈)的凝固过程与金属凝固过程非常类似,可以再现金属凝固过程中许多重要的物理现象。由于它们具有透明性并在接近室温的温度区间内凝固,因而便于实验条件的控制和对凝固过程的直接动态观测。Tsukamoto等[110]运用实时观察法对熔融过程中晶体的生长和形貌变化进行了研究。介万奇和周尧和[111]通过开展NH4Cl水溶液凝固过程的模拟实验,研究了柱状晶向等轴晶转变(columnar-equiaxed transformation,CET)的条件及规律。田陆等[126]通过开展有机透明混合溶液的凝固模型实验,发现凝固过程中存在着由凝固前沿的下降流和中心上升流组成的蝶形对流。还有部分学者采用某些低熔点金属(如Al-Cu合金)并辅助先进的测量技术进行了热态凝固实验研究。Li等[127]采用X射线成像技术实时观测了在磁场作用下定向凝固过程中枝晶的生长行为,发现热电磁流动将显著地影响凝固过程中的微观和宏观偏析。Niu等[128]和Liu等[129]搭建了一套水冷凝固可视化实验系统,采用NH4Cl、Na2S2O3等有机溶液考察了结晶器内晶粒微观结构及宏观凝固组织演化,发现中心加入冷源(模拟喂钢带)能显著降低结晶器内部温度和横向温度梯度,从中心发展的结晶雨促发柱状晶向等轴晶转变,有效阻碍冷却壁面柱状晶的生长,显著提升最终凝固组织中等轴晶比例,如图12[128,129]所示。
图12

Fig.12 Evolution of macroscopic solidification structure observed in solidification experiment
(a) device for solidification[129] (b) without inner cooler[128] (c) with inner cooler[128]
由于合金凝固过程的复杂性,对其多尺度传输现象的模型化已经成为研究凝固传输过程的主要手段。20世纪60年代末,Flemings等[130]基于固相无扩散和液相处于平衡状态的假设导出了著名的局部溶质再分配方程,标志着凝固过程溶质传输模型化的开始,该模型的贡献在于它首次给出了逆偏析、负偏析、正偏析和通道偏析的统一数学模型。20世纪80年代,Bennon和Incropera[131]采用经典混合物理论建立了描述二元系固-液相变过程动量、热量和溶质传输的连续介质模型,该模型假定凝固中的固相和液相充分混合,相与相之间不存在微观界面,整个凝固体系视为一连续介质。最近,Li等[132]利用连续焓-多孔介质模型,并考虑固相有限扩散,研究了3.3 t钢锭的凝固及偏析的形成过程。Beckermann和Viskanta[112]采用体积平均方法建立了描述二元合金凝固的体积平均模型(volume-averaged model,VAM)。随后,Ni和Beckermann[133]提出了两相VAM,标志着凝固传输模型的又一重大进展。该模型对凝固体系中的固相和液相分别采用一套微分方程描述其传输过程,其特点主要在于把微观组织和界面传输现象与宏观传输方程联系起来。Li等[134]采用两相VAM预测了钢铸锭凝固过程中的宏观偏析。但该类方法对固相的处理较为简化,为克服该缺点,Wu和Ludwig[135]将固相细分为柱状晶和等轴晶,提出了可描述柱状晶、等轴晶及液相混合凝固的三相VAM,但模型中假定柱状晶为柱状,等轴晶为球状,忽略了晶粒形貌的影响。为此,Wu等[136]又提出了考虑柱状晶、等轴晶、柱状晶间液相、等轴晶间液相及枝晶外液相等五相的VAM。该模型可用来预测铸锭的宏观结构,包括CET形成、各相体积分数及分布、宏观偏析等。但该模型引入了一些微观尺度上的参变量(凝固微观组织假定),其准确性还有待确定。凝固微观组织通常直接决定材料的最终力学性能和使用性能。通过对铸坯凝固微观组织演变的模拟[137~141],能很好地预测材料的性能。元胞自动机有限元模型(cellular automat finite element,CAFE)是首个结合了宏观热流计算和微观晶粒生长的计算模型,Li等[140]和Wang等[141]采用CAFE模型对H13模具钢的电渣重熔过程进行了模拟,研究了电磁搅拌、晶粒形核密度和渣池温度对组织形貌的影响,结果与实验数据吻和较好。近期,Liu等[129]和Niu等[142,143]利用三相VAM等模型研究了有/无内部冷源情况下的凝固组织演变行为,发现内部冷源通过加速形核、增强对流和促进柱状晶向等轴晶转变等作用机制可提高凝固组织中等轴晶的比率,并建立了喂入冷源参数与等轴晶率的数学关系式,如图13[129]所示,该研究为连铸结晶器喂钢带技术的推广应用奠定了理论基础。目前研究人员对各个尺度上凝固现象的研究已相对成熟,但是如何实现宏-微观跨尺度凝固传输现象的耦合仍是一个难点。
图13
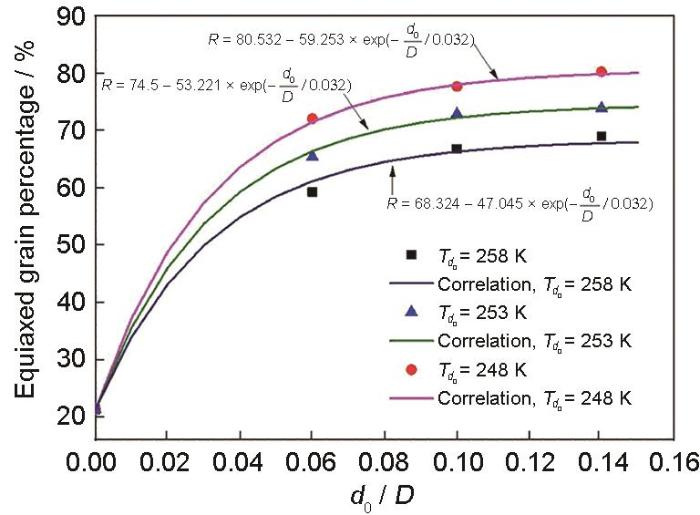
图13 钢带初始温度(
Fig.13 Relation between ratio of equiaxed zone and initial temperature of steel strip[129] (d0—initial thickness of steel strip, D—diffusion coefficient of solute,
4 湍流在揭示多尺度界面结构中的作用
连铸结晶器内的高温熔体流动处于强烈的非稳态湍动状态,相界面结构受各相物理量的湍流脉动及多尺度涡的控制,因此湍流模型的有效性也是多尺度相界面描述的关键。根据湍流数值模拟对不同尺度涡的处理方法,相界面可以分为3类:确定型、统计型和过滤型。表1给出了3种典型的湍流数值模拟方法。基于直接数值模拟(direct numerical simulation,DNS)的相界面属于确定型界面,但DNS除了受计算机容量的限制外,对于具有复杂边界问题的处理方法还未从理论上完全解决,目前难以应用于冶金工程尺度。基于Reynolds平均模拟(Reynolds-averaged Navier-Stokes,RANS)的相界面为统计型界面,它仍是目前结晶器内多相流研究的主流选择[40~44,48~51,144~151],但需要强调的是,此时相界面的微细结构以及湍流涡的多尺度效应被抹平,得到的是统计平均意义上的相界面,无法反映受不同尺度涡影响的界面运动和变形,例如,RANS k-ε (k为湍动能,ε为湍动能耗散率)模型预测的薄板坯连铸结晶器内的对称涡结构,与水模型实验的非对称结果不符[152]。大涡模拟(large eddy simulation,LES)通过过滤操作将湍流运动分解成大尺度涡和小尺度涡2部分,大尺度涡通过直接求解N-S方程获得,而小尺度涡则通过建立亚格子模型求解,因此得到的相界面属于过滤型界面。LES已成功地应用于结晶器内的单相流动计算[9~11,36,40,41,152~159],获得了钢液的瞬态非对称流场特征。研究者[22,35,36,50,100,107,108,160~164]分别将LES模型与ICM或TFM耦合,获得了结晶器内的气液两相瞬态流动特征,如图14[50]所示,解决了以往湍流模型无法捕捉气相对液相造成的湍流脉动压力的难题,改善了局部湍流速度参数、气体流动速率、液体运动参数的预测精度,与实验测量结果吻合较好。但目前发展的所有亚格子模型均假定流动为湍流、充分发展和各向同性,不能适应强各向异性湍流的计算。而且在结晶器泡状流中,气泡的脉动运动会对高温熔体的湍流脉动产生影响(如气泡尾迹增大流体小尺度湍流),目前的亚格子模型中未考虑该项的作用。因此,在LES的应用中,适用于复杂各向异性的多相湍流的亚格子模型还有待于从机理上进行更深入的研究。
表1 3种湍流数值模拟方法的基本方程和特点
Table 1
Method | Continuity | Momentum equation | Solvable scale | Model | Computation |
---|---|---|---|---|---|
equation | requirement | ||||
DNS |
|
|
Eddies of all scales | No | Huge |
|
|||||
LES |
|
|
Eddies of large scales | Subgrid scale model | High |
|
|||||
RANS |
|
|
Eddies of average scale | Time-averaged turbulence model | Low |
|
图14
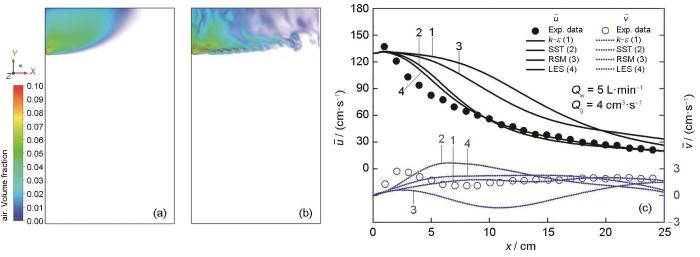
图14 结晶器内钢液-Ar气两相瞬态流场特征[50]
Fig.14 Characteristics of molten steel-argon gas two-phase transient flow field in the mold[50]
Color online
(a) RANS (b) LES
(c) comparison of numerical simulation with experiment (
5 结论与展望
连铸结晶器是控制钢水洁净度的最后环节,是连铸设备的“心脏”。结晶器内的多物理场存在连续相大界面变形、离散相颗粒输运以及连续相-离散相转变等复杂多变的多尺度界面现象,以及多尺度的湍流涡结构,形成了复杂的高温熔体多相流。连铸坯的各类质量缺陷与结晶器内高温熔体多相流传输现象密切相关。因此,研究结晶器内高温熔体多相流传输现象对于促进连铸坯质量的改进具有重要意义,是连铸领域一直以来的研究重点,受到广泛关注。然而,面对连铸过程复杂的高温动态环境,采用直接的实验研究既不经济、难度又极大。因此, 计算流体力学方法就显得极为重要。多年来,国内外研究人员围绕结晶器内的高温熔体多相流模型化开展了大量的研究工作,推动了连铸技术的快速进步。本文针对结晶器内高温熔体多相流的界面多尺度性,分别从离散流界面尺度分布性、混合流界面跨尺度性、凝固界面多尺度性以及湍流在揭示多尺度相界面结构中的作用等4方面回顾了近年来在该领域的研究现状。
随着新型高端装备向着“大型化、一体化、高性能化”发展,大截面连铸坯制造面临更复杂的合金体系和更苛刻的组织/缺陷控制要求。然而,随着连铸坯的截面扩大和高合金化,凝固方式由快速凝固向慢速凝固转变,造成芯部钢液的热对流和溶质元素的再分配过程加剧,进而导致连铸坯组织不均匀、宏观偏析、疏松/缩孔、热裂和杂质富集等非均质问题日益突出,已成为制约大截面高合金钢连铸坯质量进一步提高的瓶颈。为了满足冶金产品日益严格的洁净化、均匀化和精细化要求,亟需从基础层面继续深入开展连铸过程高温熔体多相流模型化研究,主要包括以下几个方面。
(1) 气泡聚并和破碎模型的研究。描述气泡聚并、破碎微观机制的数学模型是双流体群体平衡模型的关键。然而气泡的聚并和破碎机理非常复杂,目前气泡聚并和破碎模型中仍有许多不确定的可调参数,尤其是较宽的气泡尺寸分布范围以及不同气泡形状的影响很难进行定量描述。
(2) 混合流界面跨尺度性问题的研究。连铸过程涉及复杂的混合流界面跨尺度性问题,目前的数学模型尚不能较好地再现该过程。耦合ICM和TFM提供了解决该问题的思路,但关键是要澄清不同尺度间的相互作用关系和耦合的原则,建立控制系统的稳定性条件及调控机理。
(3) 凝固过程多相宏-微观跨尺度传输模型的研究。目前对宏观、微观上的凝固现象的研究已相对成熟,但是如何将不同尺度上的凝固传输现象耦合起来却是一个难点。需要建立能够准确表征相界面微观传输量的界面传输源项,进而实现宏-微观跨尺度凝固传输现象的双向耦合。
(4) 大涡模拟亚格子模型的研究。在气液两相流中,气泡的脉动运动会对液相的湍流脉动产生影响(如气泡尾迹增大流体小尺度湍流),目前的亚格子模型中未考虑该项的作用。因此,在大涡模拟的实际应用中,适用于复杂各向异性湍流及多相湍流的亚格子模型还有待于从机理上进行更深入的研究。
来源-金属学报