分享:铸造Mg-RE合金晶粒细化行为研究现状与展望
1.
2.
轻质高强耐热的镁稀土(Mg-RE)合金大型复杂铸件在航空航天、国防军工装备轻量化等方面展现出独特的优势。对铸造Mg-RE合金进行晶粒细化处理能够显著改善合金的强度、塑韧性以及铸造工艺性能,对拓宽其应用领域意义重大。本文首先基于成分过冷和异质形核,探讨了稀土元素及外加颗粒对镁合金晶粒细化的影响。归纳了适用于铸造Mg-RE合金的化学、物理细化方法及其作用机制,并系统论述了晶粒细化对铸造Mg-RE合金铸造工艺性能、力学性能及腐蚀性能的影响。最后面向Mg-RE合金的实际应用需求,对其细化处理方面存在的不足和发展趋势进行了探讨。
关键词:
航空航天、国防军工等领域的跨越式发展对装备轻量化提出了越来越严苛的要求。镁合金是目前实际工程应用中最轻的金属结构材料,其具有密度低、比强度和比刚度高、阻尼减振性好等特点[1]。相比较于传统AZ、AM系列镁合金而言,镁稀土(Mg-RE)合金绝对强度更高、耐热性能更好,已被成功应用于运载火箭舱体、发动机机匣等关键零部件,实现了飞行器有效减重和机动性能的显著提升[2,3]。
然而,Mg的晶体结构是hcp结构,有效滑移系少,其塑性较铝合金、钛合金等材料差。目前已开发的抗拉强度大于350 MPa的高强铸造Mg-Gd系列合金,其延伸率大都不超过5%[4~6];而抗拉强度大于400 MPa的Mg-Gd系列合金的延伸率往往低于3%[7~9]。可见,高强铸造Mg-RE合金较低的塑韧性已经成为限制该系列合金发展和应用的短板。当前航空航天大型复杂Mg-RE合金构件主要采用砂型铸造工艺成型,砂铸冷却速率缓慢导致合金晶粒粗大,进一步恶化了Mg-RE合金的塑韧性[10,11]。此外,Mg-RE合金的强度主要源于其较高的RE添加量,而提高RE元素含量会增加合金在凝固过程中的热裂倾向,严重降低其铸造工艺性能,限制了Mg-RE合金在关键结构件上的推广应用[12]。
晶粒细化是改善和解决上述问题的主要途径之一。晶粒细化不仅能够同时提高Mg-RE合金强度和塑韧性,还能够通过调整合金在凝固过程中的枝晶形貌和晶间残余液相的分布来降低合金的热裂倾向性[13,14],这对拓宽该系列合金在航空航天、国防军工等领域的进一步应用意义重大。
本文基于经典的晶粒细化理论,归纳了适用于铸造Mg-RE合金的不同晶粒细化方法及其作用机制,系统论述了晶粒细化对铸造Mg-RE合金铸造工艺性能、力学性能及耐蚀性能的影响。最后,面向Mg-RE合金的实际应用需求,对本领域的发展趋势进行了展望。
1 铸造镁合金晶粒细化机制
当前,镁合金晶粒细化的理论研究主要集中在2个方面。一是有关晶粒细化的理论模型研究,包括用生长限制因子来判断溶质元素对晶粒生长的抑制作用[15];用自由生长模型预估形核颗粒尺寸及其所需临界形核过冷度[16];而相互依存理论则综合考量了异质形核及溶质元素的生长限制效应对晶粒尺寸的影响[17]。二是关于形核颗粒与基体的晶体结构,尤其是相界面的位向关系研究,如形核颗粒与基体的晶格匹配度[18]以及面-面、边-边匹配理论等[19,20]。根据理论研究可高效筛选出潜在的晶粒细化剂,避免实验试错的盲目性。
1.1 基于RE元素的成分过冷
在合金的凝固过程中,固/液界面前沿会因溶质偏析而产生成分过冷。当溶质偏析所提供的过冷度(ΔTC)大于形核所需要的临界过冷度(ΔTn)时,可以通过促进新晶粒的形核以抑制原有晶粒的继续生长。Easton和StJohn[20]利用生长限制因子(growth restriction factor,GRF,也称之为Q)定量描述了镁合金中不同溶质元素对其晶粒生长的抑制作用,表达式如下:
式中,i为不同的溶质元素,mi 为液相线斜率,Ci 为溶质元素浓度,ki 为溶质平衡分配系数。Q越大,则晶粒细化效果越好。在镁合金中,RE元素的Q如表1[21]所示,可见Nd元素对镁合金的晶粒细化效果最好。
表1 RE元素在镁合金中的液相线斜率(m)、溶质平衡分配系数(k)和生长限制因子(Q) (溶质元素浓度Ci = 1.0%,质量分数)[21]
Table 1
Element | m / (oC·%-1) | k | Q / oC |
---|---|---|---|
Nd | -3.557 | 0 | 3.557 |
Sm | -3.4 | 0.135 | 2.943 |
Pr | -2.909 | 0 | 2.909 |
La | -2.895 | 0 | 2.895 |
Yb | -3.098 | 0.133 | 2.685 |
Eu | -2.49 | 0 | 2.49 |
Tb | -2.99 | 0.306 | 2.073 |
Ce | -1.725 | 0 | 1.725 |
Y | -1.624 | 0 | 1.624 |
Gd | -2.595 | 0.605 | 1.025 |
Ho | -2.196 | 0.608 | 0.86 |
Dy | -2.349 | 0.647 | 0.828 |
Tm | -1.58 | 0.647 | 0.557 |
Er | -2.157 | 0.757 | 0.524 |
Lu | -0.68 | 0.82 | 0.123 |
孙明[22]制备了不同梯度Gd和Y含量的Mg-RE合金,并基于
图1

图1 镁合金晶粒尺寸与RE元素Q的关系[22]
Fig.1 Dependence of grain size of Mg alloys on the Q of the RE elements[22]
(a) measured curves(b) fitted curve of all data
随着RE溶质含量增大,Q相应变大,d减小。但当Q较高时,继续提高RE元素含量对晶粒细化的作用效果变得不再明显。
1.2 基于外加颗粒的异质形核
1.2.1 基于表面能的晶格匹配原则
除了RE元素的成分过冷效应外,异质形核也对Mg-RE合金晶粒细化非常关键。目前,对Mg-RE合金中异质形核颗粒的研究主要集中在Zr和Al2RE等。凝固理论认为,颗粒的异质形核效力与颗粒/基体界面的界面能紧密相关,颗粒与基体之间的晶格错配度越小,则两相界面能越低,颗粒的异质形核效力越强。用于计算两相界面晶格错配度的模型主要包括:错配度模型、面-面匹配模型和边-边匹配模型[18~20]。其中Turnbull和Vonnegut[23]首先对基体与形核质点间的晶格错配度进行了理论化研究,并提出了错配度(δ)公式:
式中,Δa0为基体与颗粒在低指数晶面上晶格常数的差值,a0为基体相的晶格常数[18]。该模型指出,当δ ≤ 15%时,形核质点有效。但该理论只考虑了具有相似原子排列的晶面,所以在实际应用过程中有严格的限制。Bramfitt[18]建立了二维点阵错配度模型,使形核颗粒与基体相的低指数晶面重合,能适用于具有不同原子排列的两相晶面间错配度的计算,其二维错配度
式中,下角标s为基底,n为形核颗粒;(hkl)是低指数晶面;[uvw]是低指数晶面上的低指数晶向;d[uvw]s和d[uvw]n分别为沿对应晶面及晶向上的原子间距;θ为[uvw]s与[uvw]n的晶向夹角。该理论指出,当δ < 6%时,异质形核有效;若δ = 6%~12%,中等有效;若δ > 12%,则颗粒无法作为异质形核核心。采用此模型计算出Mg3Sb2与Mg2Si间的面错配度为2%[24],Al4C3与Mg基体的面错配度约为4.05%[25]。后续实验表明,Mg3Sb2和Al4C3颗粒分别对初生相Mg2Si和Mg-Al系合金具有良好的晶粒细化效果,充分验证了面-面匹配模型的有效性。根据二维错配度公式计算了Zr/Mg低指数晶面的错配度[22],4个低指数位向(0001)Zr // (0001)Mg、(0001)Zr // (
Bramfitt[18]点阵错配度模型停留在二维层面,仅适用于简单晶格的计算,而从严格意义上讲,匹配应是界面上的原子匹配而非晶格点阵的匹配。据此,Zhang等[19]提出了边-边(edge to edge model,E2EM)匹配模型,该模型的计算包含2个部分,分别是两相密排面或近密排面的面间距的错配度(fd),以及密排面上密排方向或近密排方向上的晶格错配度(fr),具体计算公式如下:
式中,dm和dp分別为两相各自密排面(或近密排面)的面间距;rm和rp分别为两相各自密排方向上(或近密排方向)的原子间距。当满足fr < 10%和fd < 6%时,异质颗粒能够作为有效的异质形核核心。
Qiu等[26]最早借助E2EM模型计算了Al2Y颗粒与α-Mg之间可能存在的3组位向关系,如图2a[26]所示。结果表明,Al2Y是镁合金的有效细化剂。其后续通过向Mg-10Y合金中加入Al元素并原位反应生成Al2Y颗粒,成功实现了合金晶粒的显著细化。同时Qiu和Zhang[27]还定量计算了其他Al2RE颗粒与α-Mg的fr与其相界面能的关系。从图2b[27]可以发现,除Al2La和Al2Sc外,其他几种Al2RE颗粒与α-Mg的原子错配度小于2%,界面能较低,能够与α-Mg完全润湿,其具备作为镁合金晶粒细化剂的潜力。
图2
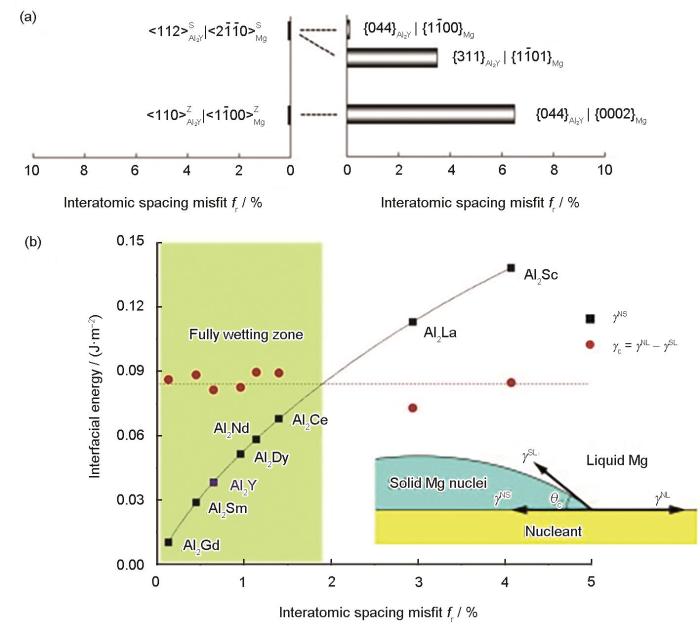
图2 Al2Y颗粒与α-Mg基体的位向关系[26]以及Al2RE/α-Mg之间的错配度与其相界面能的关系[27]
Fig.2 Possible orientation relationships between Al2Y particles and α-Mg matrix calculated by edge to edge model (E2EM) (a)[26] and the relation between atom spacing mismatches and interface energy of Al2RE particles and α-Mg (b)[27] (γNS—interfacial energy between nucleant and solid Mg, γNL—interfacial energy between nucleant and liquid Mg, γSL—interfacial energy between solid Mg and liquid Mg, θc—contact angle at the interface between nucleant and solid Mg, γc—the difference between γNL and γNS)
1.2.2 自由生长模型
除界面结构外,Greer等[16]表示形核颗粒尺寸是影响其异质形核效力的关键因素,颗粒尺寸满足
式中,dn是颗粒直径(假设为球状),
受限于实际铸造工艺能够提供的过冷度,颗粒必须满足一定尺寸要求才能作为有效的形核核心。如统计[28]发现,在Mg-RE合金常用的晶粒细化剂Mg-Zr中间合金中,能够作为异质形核核心的Zr颗粒尺寸范围为1~5 μm,依据
1.3 相互依存模型
StJohn等[17]提出的相互依存理论模型综合考虑了形核颗粒与溶质元素对晶粒细化的共同作用。相互依存理论表示,先形核的晶粒在长大过程中由于在固/液界面前沿造成了溶质富集而为下一个晶粒的形核提供了所需的形核过冷度。最终的晶粒尺寸(dgs)由3部分组成,包括初始形核区尺寸(Xcs)、固/液界面到成分过冷区域之间距离(Xdl)以及无形核区到下一个有效形核位点的距离(Xsd),表达式如下:
其具体的表达式为:
式中,D为溶质元素在液相中的扩散系数,zΔTn为激发下一个形核所需要的过冷度的增量,v为固/液界面生长速率,
2 铸造Mg-RE合金的化学细化
铸造Mg-RE合金的化学细化是指向Mg-RE合金熔体中加入晶粒细化剂,增加合金在凝固过程中异质形核核心的数密度,或是通过提高合金元素的成分过冷效应以抑制枝晶生长,从而达到细化晶粒、提高合金力学性能的一种细化方法。针对Mg-RE合金而言,常用的化学细化主要有加Zr细化和加Al细化2种方法。
2.1 铸造Mg-RE合金的Zr细化法
2.1.1 Zr细化行为
Zr在镁合金中一般有2种存在形式:溶解的溶质原子Zr和未溶解的颗粒Zr[31,32]。根据Mg-Zr二元相图,室温下Zr在Mg基体中的固溶度较低。尽管溶质Zr和颗粒Zr均能对镁合金产生明显的晶粒细化效果,但是其作用机制却完全不同。溶质Zr在镁合金中主要通过在固/液界面前沿产生强烈的成分过冷来抑制枝晶生长以实现晶粒细化[33]。在镁合金常见的合金化元素中,Zr的Q高达38.3℃[34],远高于RE元素,因此其晶粒细化效果更加显著。颗粒Zr的细化机制主要有包晶反应机制和异质形核机制2种。Emley[35]认为颗粒Zr主要通过包晶反应与液相生成一层富Zr的Mg固溶体以提高Mg晶核的形核率来实现晶粒细化。其证据是经Zr细化的镁合金中有富Zr晕圈的存在,晕圈中心存在一颗或者几颗纯Zr颗粒,如图3a[22]所示。然而当Zr含量远低于包晶成分时,合金中仍然能够发现Zr晕圈,且此时Zr的细化效果更明显[36],这说明Zr晕圈应该还有其他的形成机制。田倩[37]采用高温液淬的办法将Mg-RE-Zr熔体直接滴注在铜模表面(冷却速率> 100℃/s),在快速凝固的合金组织中仍然可以发现明显的Zr晕圈,这说明富Zr晕圈在高温液相中早已存在。结合现有证据,富Zr晕圈的形成应该既与高温液相中因Zr颗粒溶解扩散而形成的Zr溶质富集区有关,也与包晶反应生成Zr浓度较高的Mg固溶体有关。异质形核机制则认为,因Zr与Mg的晶体结构均为hcp结构且2者的晶格常数非常接近(aMg
图3
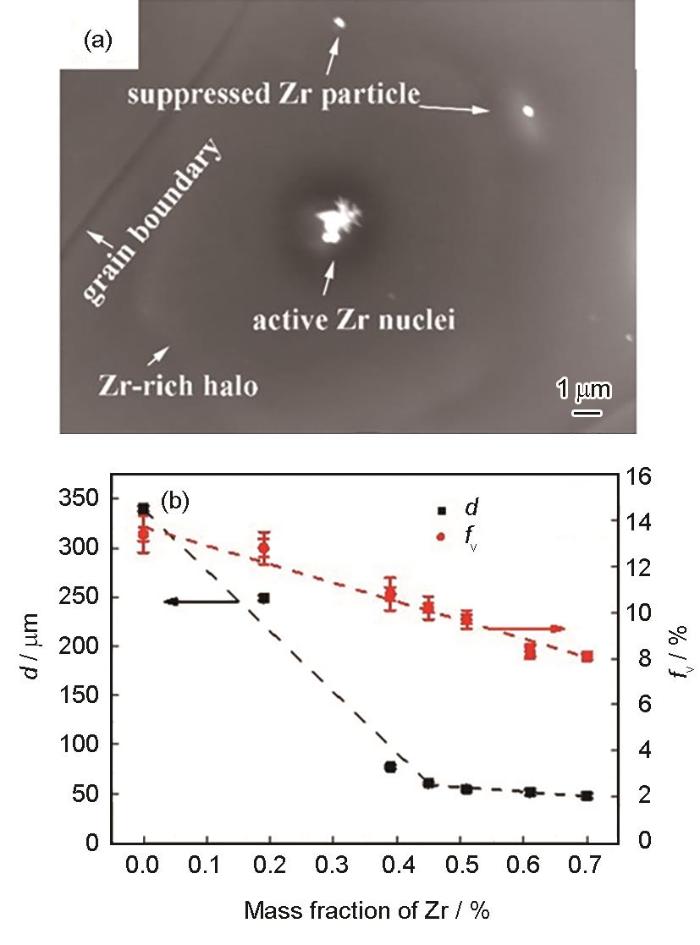
图3 含Zr镁合金中的Zr晕形貌[22]及Mg-10Gd-3Y-xZr合金晶粒尺寸与共晶相体积分数随Zr含量的变化[36]
Fig.3 Microstructure of the Zr halo in Mg alloy containing Zr (a)[22], changes of grain size (d) and eutectic phase's volume fraction (fV) with Zr content in the Mg-10Gd-3Y-xZr alloy (b)[36]
溶质Zr和颗粒Zr不仅对镁合金的晶粒细化机制不同,其作用效果也完全不同。目前广泛认为溶质Zr的晶粒细化效果较颗粒Zr更强。如砂型铸造的Mg-Gd-Y-Zr合金的晶粒尺寸与Zr含量之间存在分段线性关系[36]:当Zr含量低于0.45% (质量分数,下同)时,合金晶粒尺寸随着Zr含量的增加而显著下降,但当Zr含量高于0.45%后,继续增大Zr含量对晶粒细化效果不明显(图3b[36])。Sun等[39]在金属型铸造的Mg-Gd-Y-Zr合金中也发现了类似的规律,这表明随着Zr含量的提高,其晶粒细化机制发生了改变:Zr含量较低时,Zr主要以溶质Zr的形式存在,其主要的晶粒细化机制为成分过冷;当Zr含量超过0.45%后,部分Zr因过饱和而以未溶解的颗粒Zr形式存在,其主要通过异质形核实现晶粒细化。因此,为了促进Zr颗粒充分溶解扩散以获得更好的细化效果,在实际熔炼过程中常需对熔体在780~800℃的高温下进行反复搅拌[40]。
2.1.2 Zr加入方式
目前主要采用Mg-Zr中间合金向Mg熔体中加Zr细化。但Mg-Zr中间合金中的Zr主要以未溶解的颗粒Zr形式存在。加Zr细化处理后,Zr细化效果会随着静置时间的延长而发生衰退。其衰退机制主要有2点:首先,Zr的化学活性强,其与熔体中的Fe、Si、Mn等杂质元素及炉气中的O2、H2O、H2等气体发生反应损耗,尤其是采用铁坩埚熔炼时其细化衰退更为明显[41];其次,Zr颗粒的密度约是Mg熔体的4倍,Zr颗粒会在Mg液中发生沉降,导致采用Mg-Zr中间合金进行细化处理时Zr收得率低于30%[40]。Qian等[40]推导了Zr颗粒在Mg熔体中的沉降距离(S):
式中,g为重力加速度,ρZr为Zr颗粒的密度,ρMg和η分别为Mg熔体的密度和黏度,t为时间。可以发现,Zr合金化温度越高(熔体黏度越小)、Zr颗粒尺寸越大,则Zr颗粒的沉降速度就越大[22]。通过挤压[22]、轧制[42]、搅拌摩擦加工(FSP)[43]、等通道挤压(ECAP)[44]等大塑性变形方法对商用Mg-Zr中间合金进行预处理,能够破碎Zr颗粒团聚、细化Zr颗粒尺寸,有效改善Zr细化效果与衰退效应。经过细化实验验证,采用轧制、FSP和ECAP能够将Mg-Zr中间合金的细化效力分别提高30%、21%和16%。
向Mg-RE合金中加入低熔点的含Zr熔盐是另一种Zr合金化方法,该方法具有加Zr温度低、生成的Zr颗粒细小、成本低等特点。采用NaCl-KCl-K2ZrF6含Zr复合盐细化的Mg-10Gd-3Y合金晶粒尺寸能达到25 μm以下,但K2ZrF6与高温Mg熔体反应生成的MgF2夹杂易悬浮于熔体中难以去除,降低了合金的纯净度[45]。为避免MgF2夹杂的形成,Tong等[46]采用熔点低至437℃的ZrCl4作为细化剂,且在细化后合金中并未发现明显的夹杂物。ZrCl4与Mg的反应产物MgCl2本就是精炼剂的主要组元之一,其与MgO、Mg3N2等镁合金中常见的夹杂物润湿性极强,因此理论上MgCl2的形成对熔体纯净度的影响较MgF2小。由于ZrCl4的沸点较低,将其加入高温熔体后会迅速汽化,不仅加大了其与熔体的反应接触面积,有助于获得粒径更加细小、分布更均匀的Zr颗粒,同时还对熔体具有一定的精炼作用。在经ZrCl4细化的合金中发现了粒径约2 μm且与基体存在明显的位向关系([
2.1.3 Zr细化存在的问题
采用加Zr细化的方式操作简单,加入0.5%的Zr就能使铸造Mg-RE合金获得显著的细化效果。然而传统的Mg-Zr中间合金组织不均匀,存在大量Zr颗粒团聚,中间合金的品质有待进一步提高。尤其是在工程化应用中,RE合金化温度为740~760℃,随后需将合金熔体升温至780~800℃进行Zr细化(为了促进Zr的溶解扩散),最后需将熔体再次降温至740~760℃进行熔剂精炼[46]。由于采用Mg-Zr中间合金进行细化处理时所需温度高,合金熔体在制备过程中需反复升降温,不仅严重降低了合金的制备效率,还会对熔体质量造成影响。此外,在熔剂精炼后的静置过程中,大密度的Zr颗粒团聚极易与精炼剂/夹杂物同时沉降,这就造成了细化与净化效果相互制约的问题[47,48]。
采用锆盐进行加Zr细化能够达到与Mg-Zr中间合金相当的效果,但锆盐细化存在几个明显的技术难点:首先,锆盐主要通过与Mg熔体在高温下发生置换反应生成Zr,然而大量的反应副产物及残留的锆盐不易分离;其次,这些反应副产物与Zr颗粒同时生成,降低了Zr颗粒表面的洁净度,对Zr颗粒的异质形核作用产生影响;最后,部分锆盐易吸水潮解,化学活性强、挥发性强,其储存、运输均较为困难。
2.2 铸造Mg-RE合金的Al细化法
2009年,Qiu等[26]基于E2EM模型,针对镁合金筛选出了一种有效的细化剂Al2Y。研究表明,向Mg-10Y合金中添加0.6%~1.0%的Al元素后,熔体中能够发生如下原位反应:
如图4[26]所示,生成的Al2Y能够使合金晶粒尺寸从180 μm降低到36 μm,达到了与加Zr细化相当的效果。由于晶内、晶界均匀分布的高热稳定性的Al-Y化合物能够有效抑制晶界迁移,通过加Al细化的Mg-Y合金比Zr细化合金的组织稳定性更强。如图5[27]所示,采用聚焦离子束将α-Mg中的Al2Y颗粒切片并用于透射电镜(TEM)位向观察,可以发现Al2Y与基体之间存在3个不同的小平面F1、F2、F3,其中F1小平面与(0002)Mg和(
图4
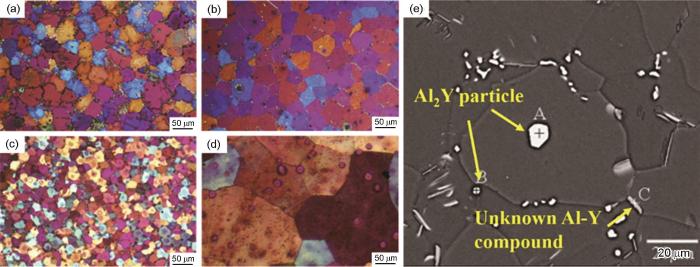
图4 采用Zr和Al2Y细化处理的Mg-10Y合金的显微组织[26]
Fig.4 Microstructures of Mg-10Y alloy grain-refined by Al (a, b) and Zr (c, d)[26]
(a, c) as-cast state (b, d) solution treated at 550oC for 48 h
(e) Al-Y phase observed in the cast Mg-10Y-Al alloy
图5
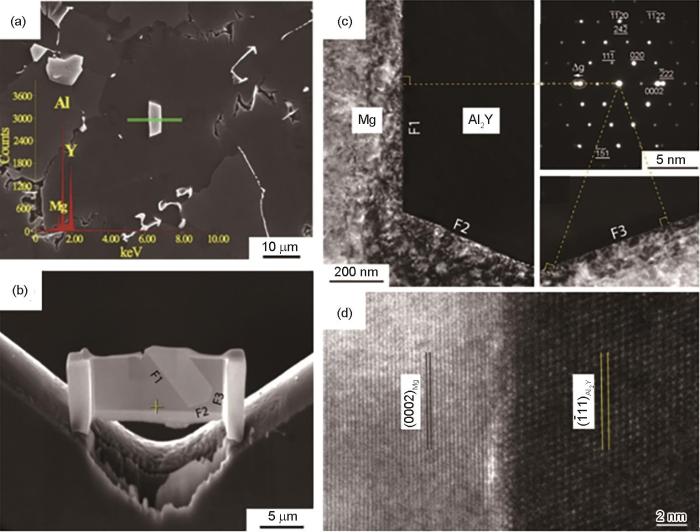
图5 Al2Y颗粒的微观形貌及其与α-Mg基体的位向关系[27]
Fig.5 Microstructures of the Al2Y particle and its orientation relationship with α-Mg matrix[27]
(a) SEM image (b) cross section of the Al2Y
(c) TEM image showing the Al2Y/Mg interface with the selected area electron diffraction (SAED) pattern
(d) HRTEM image of Al2Y/Mg interface close to F1 facet in Fig.5c
Al2RE的异质形核效果与其颗粒尺寸、数密度紧密相关。通过优化Al元素含量、调整Al与RE元素添加量的比值、改变冷却速率等铸造工艺参数可以改善Al2RE的异质形核效果。为了探明Mg-RE合金的加Al细化机制,Chang等[52]基于热分析的方法研究了Mg-10(Al + Y)合金的凝固行为。研究表明,Al2Y的形成温度在690℃左右,生成的Al2Y随后能够与液相在635℃附近发生包晶反应(L + Al2Y→α-Mg)生成α-Mg相从而实现晶粒细化。随着Al含量的提高,Al2Y的数量逐渐降低,包晶反应消失。尽管包晶反应能够促进晶粒细化,但晶粒细化效率仍与Al2Y颗粒尺寸及合金的Q相关。当Al含量与Y含量之比大于0.2小于0.5时,先于包晶反应产生的Al2Y颗粒会发生粗化,晶粒细化效率降低。但当Al含量与Y含量之比大于0.5后,因Al元素对枝晶较强的生长限制作用,Mg-10(Al + Y)合金晶粒尺寸反而得到细化。可见,要想在Mg-RE合金中实现理想的加Al细化效果,务必对合金成分进行严格的限定。此外,冷却速率也对Mg-RE-Al合金的晶粒细化效果具有明显的影响。Dai等[49,53]通过向Mg-Gd-Y合金中加入Al,在基体内形成了较多的异质形核颗粒Al2(Gd x Y1 - x ),且当Mg-10Gd-2Y-1Al合金冷却速率从1.4℃/s提高到16.5℃/s后,Al2(Gd x Y1 - x )颗粒粒径显著减小且其数密度增加,合金晶粒发生进一步细化。
2.3 Zr细化法与Al细化法的对比
尽管Al细化与Zr细化对Mg-RE合金的晶粒细化效果相当,但这2种细化方式在细化机制方面存在本质不同。以Mg-Zr中间合金加Zr细化为例,Zr不与RE或Mg发生化学反应,而是通过颗粒Zr的异质形核或溶质原子Zr的成分过冷来实现晶粒细化;而在Al细化过程中,Al首先与RE元素在高温下原位反应生成Al2RE,Al2RE颗粒通过与液相发生包晶反应而实现晶粒细化。其次,Al2RE的密度(3.8 g/cm3)较Zr颗粒(6.52 g/cm3)小,因此加Al细化的衰退效应较Zr细化有所改善[54]。此外,热稳定性较强的Al-Y相对晶界还能起到强烈的钉扎作用,Mg-RE-Al合金在高温下的组织稳定性较Mg-RE-Zr强。但是,Al细化法会消耗部分RE元素,可能会对Mg-RE合金的力学性能造成影响。加Al细化还受合金成分和熔铸工艺严格限制,在冷速较慢(如砂型铸造或熔模铸造)的工艺条件下,加Al细化效果会受到一定影响。
3 铸造Mg-RE合金的物理细化
物理细化是指无需向合金中额外引入细化剂,仅通过热控法和动力学法实现晶粒细化的一种方法。热控法主要是通过快速冷却等方法提高熔体在凝固过程中的热过冷以满足临界形核过冷度并实现晶粒细化[55~57]。动力学细化法主要是通过施加机械搅拌、外加物理场等方法,向正在凝固的合金熔体施加外部能量以促进晶核提前形成,并使已有枝晶破碎,提高形核率。尤其是当物理细化与Mg-RE合金的Zr细化、Al细化联用时,能够有效分散Zr或Al2RE颗粒,进一步提升化学细化效果。
3.1 Mg-RE合金熔体搅拌细化
前已述及,铸造Mg-RE合金的异质形核晶粒细化效果主要由3个因素的相互作用决定:形核效率(以颗粒与基体的晶格错配度衡量)、颗粒尺寸和数密度。研究[58]表明,在合金液相线以上采用熔体强力剪切技术,能够实现晶粒的有效细化。这是由于在Mg熔体液膜中自然生成的MgO经熔体剪切得到有效破碎,分散成为尺寸50~300 nm的异质形核颗粒(图6a[59])。这种颗粒与Mg基体存在共格位向关系:(0
图6
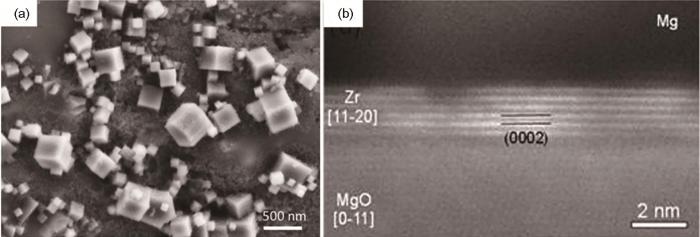
图6 强力熔体剪切后的MgO颗粒形貌[59]及MgO/Mg界面处Zr吸附层[60]
Fig.6 SEM image of MgO particles in Mg melt with intensive melt shearing (a)[59] and HRTEM image of Zr adsorption layer at MgO/Mg interface (b)[60]
3.2 Mg-RE合金外加能量场细化
适合于晶粒细化的外加能量场方法主要有超声场或电磁场。熔体在外加物理场的条件下发生对流、振动,使已形成的枝晶重熔或破碎,形成大量细小的形核核心,达到显著的细化晶粒效果[48]。
3.2.1 超声场
研究表明,超声处理可以降低Mg-RE系合金中的重力偏析和枝晶偏析[47],还能提高Al对Mg-RE合金的细化效率,从而显著细化Mg-5Sm-Al铸态合金晶粒[61]。由超声场产生的空化效应和声流效应不仅能够破碎正在生长的枝晶以提高自身的α-Mg晶核数量,还会显著降低Al2Sm颗粒的粒径,促进Al2Sm的异质形核效力。此外,超声在熔体中形成的局部压力会导致合金熔体的理论结晶温度提高[47],增加了合金熔体的热过冷,这些因素都会显著提高Mg-RE合金的晶粒细化效果[62]。图7[61]定量比较了超声场和Al2Sm颗粒对Mg-5Sm-xAl合金晶粒细化的贡献比率。当没有Al2Sm存在时,超声处理是晶粒细化的主要机制。而随着Al含量从0提高到3%,Al2Sm颗粒的异质形核作用对晶粒细化的贡献率逐渐增加。相比之下,超声处理对晶粒细化的贡献率却从89.26%下降到0。这从侧面反映出当异质形核核心数密度较低时,施加外场能够促进颗粒与熔体的润湿,以获得更优异的异质形核效果;而当异质形核核心数量充足时,外加物理场对晶粒细化的贡献会被显著降低。
图7
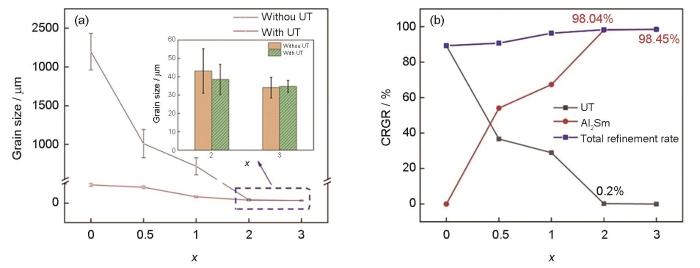
图7 Al2Sm颗粒和超声处理对Mg-5Sm-xAl合金晶粒细化的贡献[61]
Fig.7 Average grain sizes of Mg-5Sm-xAl alloy with and without ultrasonic treatment (UT) (a), contribution rate of grain refinement (CRGR) by Al2Sm particles and UT (b)
前已述及,加Zr可以显著细化铸造Mg-RE合金晶粒尺寸。然而,由于Zr颗粒与Mg液的密度差异大,Zr在合金熔体中分布极不均匀,沉降、团聚倾向大,不仅降低了Zr的收得率,还成为影响Mg-RE合金晶粒细化效果的主要原因[40],而通过传统的搅拌方法实现完全分散或破碎Zr颗粒仍具有挑战性。将Zr细化与超声处理相结合能大幅提高铸造镁合金的细化效率:在液相线温度以上施加超声波能够明显降低熔体内的温度梯度,促进晶粒在过冷熔体中的形核[63];其次,空化和声流效应促进了Zr颗粒的分散、破碎和溶解,提高了熔体中溶质Zr含量,大大加强了Zr对Mg-RE合金的细化作用[64,65]。
3.2.2 脉冲电场
在Mg-RE合金凝固过程中施加脉冲电场,可产生Lorentz力,使液态金属发生对流,获得均匀的温度场和浓度场,从而达到减少偏析、细化晶粒的目的,该方法已经成功应用于生产WE54等镁合金[66,67]。
此外,加Zr与脉冲电流复合处理的方法能进一步细化Mg-10Gd-3Y合金晶粒。通过热力学、动力学等计算分析,复合处理对Mg-10Gd-3Y合金的几种细化机制如下[36]:复合处理能在Zr细化的基础上进一步提高铸造Mg-Gd-Y合金中α-Mg的起始形核温度和形核过冷度,提高了形核驱动力。热力学计算分析表明,复合处理能提高砂铸Mg-Gd-Y合金液-固转变过程中体系自由能的变化、提高液态原子团簇的碰撞频率、增加α-Mg临界原子团簇数量(有利于提高晶胚数量)、降低液态原子团簇静电斥力势能(更易形成较大的α-Mg原子团簇)、降低α-Mg临界晶核尺寸,进而提高α-Mg形核率,从而细化晶粒。经动力学分析,Mg原子所受到脉冲电流产生的Lorentz力与在固/液界面迁移的Gd、Y、Zr溶质原子受到Lorentz力的方向相反,因此在复合处理后固/液界面处溶质原子黏度提高,扩散系数降低,溶质原子的迁移距离缩短,从而缓解砂铸慢冷条件下合金凝固组织中的溶质偏聚现象,使砂铸Mg-10Gd-3Y合金晶粒细化效率提高至26.1%。
3.2.3 脉冲磁场
现有研究表明,脉冲磁场细化晶粒的作用机制主要为磁制过冷效应[68]、对流效应[69]以及Joule热效应[70,71]。与前述脉冲电场作用相似,在Mg-RE合金中施加脉冲磁场会产生电磁振动和电磁搅拌的效果,Lorentz力使液态金属发生强迫对流,获得均匀的温度场和浓度场。由于凝固时间延长,游离的折断晶粒数目增大,最终实现晶粒细化。研究表明,施加脉冲磁场使Mg-Gd-Y-Zr[72]和Mg-Zn-Y[73]合金晶粒显著细化,其中Mg-Gd-Y-Zr合金的平均晶粒尺寸从未加脉冲磁场的65 µm细化至37 µm,晶粒细化的主要原因来源于脉冲磁场导致熔体磁过冷及熔体温度梯度的降低[72]。除了施加脉冲磁场,旋转磁场的引入也导致铸态Mg-15Gd-1Zn合金显著的枝晶碎裂和晶粒细化[74]。虽然脉冲磁场对Mg-RE合金的细化具有显著的效果,但是脉冲磁场细化金属凝固组织的研究才刚开始,相关理论机制还需深入探讨。
综上所述,施加物理场可显著细化Mg-RE合金凝固组织。相比较于化学细化方法,物理细化可以在不改变合金成分的条件下,实现更加绿色、高效的细化效果。但是超声、搅拌等方法在熔体中的作用范围有限,在实际工程应用中的适应性不高。除了施加单一物理场外,目前采用的新型复合细化方法已成为Mg-RE合金晶粒细化的重点关注方向,如“电磁场-超声复合处理”、“机械振动-超声复合处理”、“超声场-Zr细化复合处理”、“电磁场-Al细化处理”等,其相应的复合作用机制也需要进行系统深入的研究[75]。
4 晶粒细化对铸造Mg-RE合金性能的影响
Mg-RE合金存在强度高、耐热性能好、抗蠕变能力强等优势,但其塑韧性还有待进一步改善。尤其是高RE含量的镁合金因其液固温度区间大,在铸造成型过程中易产生热裂纹,降低铸件成品率[76,77]。有效的晶粒细化处理能够提高Mg-RE合金的塑韧性,还能通过调整合金在凝固过程中的枝晶形貌和晶间残余液相的分布以降低其热裂倾向,提高合金的综合力学性能和铸造工艺性能。
4.1 铸造工艺性能
当Zr的加入量为0.2%时,Mg-10Gd-3Y合金熔体的流动性较未加Zr的合金提高了58%[78]。Zr合金化主要是从2方面提高合金流动性:一方面,Zr降低了合金的液相线温度,延长了合金在液相区的停留时间,从而促进了熔体流动;另一方面,Zr能提高合金在凝固过程中的形核率以促进晶粒从树枝晶向细小的等轴晶转变,降低了合金液在流动过程中的黏滞阻力,由此提高了合金的流动性。
除流动性以外,热裂倾向性也是Mg-RE合金在工程化应用中重要的考核指标之一。较低的热裂倾向性有助于成型大型复杂薄壁Mg-RE合金铸件,对推广Mg-RE合金在航空航天、国防军工等领域的应用至关重要。经典液膜理论[12]认为,在合金的凝固过程中由于凝固收缩会在铸件中产生拉应力。当固相体积分数在0.40%~0.90%时,应力可以得到释放。而在合金凝固后期,尤其是当固相体积分数大于0.90%而小于0.99%时,枝晶骨架开始大量闭合,此时枝晶间的液膜极易在应力作用下被撕裂而形成热裂纹。当向Mg-4.5Zn-0.4Y合金中加入0.5%的Zr后,合金的晶粒尺寸从433 μm细化至68 μm,合金的抗热裂性显著提高,如图8[12]所示。对于未细化处理的合金,热裂主要发生在枝晶骨架形成的糊状区,粗大的树枝晶的生长尖端在凝固早期就发生了接触,提高了合金在凝固过程中的补缩阻力,导致热裂倾向变大。加Zr细化处理后,合金中粗大的树枝晶被转变为细小的等轴晶,枝晶内部的补缩通道数量增加,凝固初期的部分热裂纹可以得到修复[79,80]。此外,细小的晶粒结构更有利于热变形的调整,进而降低合金热裂倾向性[81,82]。
图8
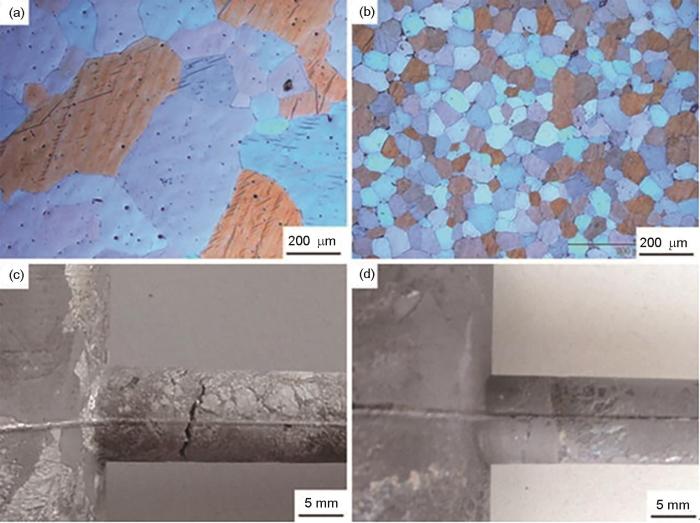
图8 加Zr细化处理前后的Mg-4.5Zn-0.4Y合金的组织及热裂倾向性[12]
Fig.8 OM images (a, b) and macro-photographs showing the effect of grain size on the hot tearing susceptibility (c, d) of Mg-4.5Zn-0.4Y (a, c) and Mg-4.5Zn-0.4Y-0.2Zr (b, d)[12]
Li等[83]研究加Zr细化对重力砂铸WE54合金缩松缩孔倾向性的影响。结果表明,尽管加Zr后晶粒得到了细化,但WE54砂铸试样中的缩孔缩松缺陷没有得到明显改善;而冒口补缩才是影响试样中缩孔缩松分布的直接因素。尤其是当冒口模数(mr)与铸件模数(mc)之比超过1.3后,WE54合金砂铸板(200 mm × 150 mm × 25 mm)中没有明显的缩松缺陷。模拟结果也表明,当Niyama值小于临界值0.4℃0.5·s0.5/mm时,砂铸WE54合金的缩松区域面积较小。
4.2 力学性能
通过对比研究Al2Y颗粒和Zr对Mg-3Y合金的组织和力学性能的影响表明,采用Al2Y颗粒和加Zr细化后的合金晶粒尺寸分别为53和40 μm[54]。Al2Y颗粒的引入不仅能细化晶粒,还能作为增强相颗粒提高合金的强度,细化后的Mg-3Y合金的抗拉强度和延伸率分别从117 MPa和3.3%提高到209 MPa和11.5%,与Zr细化后合金的力学性能相当。
部分学者[61]还研究了加Al和超声复合细化对Mg-RE合金组织和性能的影响。结果表明,随Al含量的增加和超声场的引入,Mg-5Sm合金的晶粒尺寸大幅降低,强塑性同时提升。当Al含量超过3%后,晶粒尺寸细化至40 μm以下,细化效果达到极限,此时超声场的施加对晶粒尺寸影响不再明显。超声处理能够有效分散原位生成的Al2Sm颗粒,因而复合处理后的合金延伸率大幅提高。Yin等[84]发现当Mg-4Y-xAl合金中的Al含量从1%增加到4%后,合金晶粒尺寸先增加后降低,而强度和延伸率均逐渐提高。这是由于随Al含量的增加,含Y的第二相由Mg24Y5向Al2Y和Al3Y转变:当Al含量从1%增加到2%时,对晶粒长大起抑制作用的Mg24Y5的体积分数从3.38%降低到0.15%;当Al含量从3%增加到4%时,Al2Y和Al3Y的体积分数分别达到1.79%和4.53。可见,采用加Al细化Mg-RE合金时,必须考量晶粒细化及Al对RE元素的反应消耗这2者对力学性能的综合影响。Dai等[85]比较了0.8%Al和0.4%Zr对Mg-10Gd-3Y合金组织和性能的影响,发现Mg-10Gd-3Y-0.8Al合金在铸态和固溶态时的拉伸强度均低于Mg-10Gd-3Y-0.4Zr,这正是由于Al与部分Gd、Y元素反应形成Al2Gd和Al2Y,削弱了RE元素的强化效果[86]。Li等[87]研究了Zr含量对Mg-10Gd-3Y-xZr合金室温/高温力学性能的影响,发现随Zr含量从0.3%增加到0.5%,晶粒尺寸由130 μm降低到40 μm。在低于250℃的测试温度下,合金的强度和延伸率均随晶粒尺寸的降低而升高,但当温度达到300℃时,晶粒尺寸对合金的强度影响不再明显。
4.3 腐蚀性能
Ralston等[88]指出,金属的耐蚀性能和晶粒尺寸之间存在类Hall-Petch关系,腐蚀电流密度(icorr)的定量表述如下:
式中,A为与腐蚀环境有关的常数,B是与合金成分及杂质含量有关的常数,gs为平均晶粒尺寸。对MEZ系Mg-RE合金的腐蚀研究[89]表明,含0.6%Zr合金的腐蚀萌生和扩展速率远低于不含Zr的合金,且随晶粒尺寸的降低,MEZ合金具有更低的阳极溶解和阴极析氢速率,实验结果与
晶粒细化在提升合金强塑性的同时,也会导致晶界密度、晶界取向和残余应力发生变化,这些变化会进一步影响合金的电化学行为与腐蚀敏感性。随晶粒尺寸减小,晶界体积分数增大,晶界-晶粒电偶腐蚀会加剧(当晶界富集低电位相时)或减缓(当晶界富集高电位相时)。选择合适的细化剂能协同调控合金的晶粒尺寸与耐蚀性能。研究[90]表明,随Al含量的增加,Mg-6Zn-8.16Y-2.02Mn合金的晶粒尺寸先减小后增大,腐蚀析氢速率同样先减小后增加。当Al含量为0.3%时,合金晶粒尺寸细化到30 μm并表现出最佳的耐蚀性能。Al的添加促进了高熔点的Al2(Y, Zn)相生成,其不仅能够作为形核质点细化晶粒,还可以使原本对晶粒长大有抑制作用的高电位的长周期有序堆垛(long period stacking ordered,LPSO)相(Mg12YZn)的含量大幅降低,提高合金整体的耐蚀性[91]。与常规的镁合金相比,Mg-RE合金中的腐蚀产物膜能有效阻止基体进一步被腐蚀[92,93]。
对加Zr细化的镁合金而言,当Zr含量较低时,合金腐蚀速率随着Zr含量增加而降低;而当Zr含量> 0.5%时,难溶Zr颗粒的存在导致合金腐蚀速率又有所升高[94]。加Zr细化提高镁合金耐蚀性的原因可能有:Zr消耗掉了Mg液中的Ni、Fe等杂质元素,较高的熔体纯净度促进了合金耐蚀性的提升;固溶进Mg基体的Zr稳定了Mg基体,延迟了局部腐蚀的萌生。Ben-Hamu等[95]也发现Zr细化能够明显提高Mg-2Y-3RE-0.5Zr合金的耐蚀性能,且晶内Zr晕圈处的耐蚀性明显优于其外围的贫Zr区。
不难发现,晶粒细化处理能够同时影响Mg-RE合金的强塑性、铸造工艺性能和耐腐蚀性能等。采用化学细化方法对Mg-RE合金进行晶粒细化处理后,合金不同性能的变化趋势也完全不同。因此,应针对Mg-RE合金的实际服役性能要求,选择合适的晶粒细化方法。
5 展望
轻质高强耐热的Mg-RE合金在航空航天、国防军工等领域的应用前景非常广阔。但受限于镁合金的晶体结构和铸造成型工艺,大型复杂的Mg-RE合金铸件塑韧性严重不足,极大制约了其在关键零部件上的进一步应用。晶粒细化能同时提高Mg-RE合金的综合力学和铸造工艺性能,对推广该系列合金的广泛应用意义重大。但是目前仍然存在较多亟待解决的问题:
(1) 现有Mg-RE合金晶粒细化效果严重依赖熔铸工艺条件,如Zr细化受Zr合金化温度与搅拌工艺影响,Al细化效果受Al与RE元素的相对含量及冷却速率等因素影响。此外,Zr、Al2RE等异质形核颗粒易在熔体中产生比重偏析,严重影响了熔体成分的均匀性,还导致了Mg-RE合金的净化、细化效果相互制约。以上问题不仅增大了对铸件组织、性能的调控难度,也成为了相关细化技术工业化应用的关键瓶颈。后续研究有必要重点考虑化学-物理复合的细化新思路,结合2种细化技术的优势,实现细化质点的快速分散,进一步改善其细化效果与衰退效应。
(2) 当前针对Mg-RE合金的晶粒细化手段繁多,但对细化机制的研究却不够系统深入,某些理论机制仍然存在一定争议,如Zr晕的形成机制及其对晶粒细化机制的影响仍不明确;新型细化剂的研发主要依靠试错法,其准确性和研发效率有待进一步提高。后续可结合同步辐射等先进原位表征技术,通过对合金的异质形核、枝晶生长等过程的追踪观察以完善现有的晶粒细化机制;此外,有必要基于晶粒细化模型(如E2EM模型等),结合大数据、数据挖掘和机器学习等技术手段,实现高效、稳定、抗衰退的新型细化剂的快速甄选。
(3) 现有的化学细化、物理细化、复合细化方法对铸造Mg-RE合金晶粒细化的极限仍然停留在数十微米,远不及大塑性变形的晶粒细化效果。后续需从界面冶金反应的热力学及动力学规律出发,探明形核质点与熔体界面能垒的影响因素,探寻突破界面能垒以显著提高形核核心细化孕育能力的新途径;在此基础上,有必要构建熔体细化效果与凝固工艺条件的关联特性与有效匹配关系,实现晶粒细化剂效果的最优化。
来源--金属学报