分享:钛合金及其扩散焊疲劳特性研究进展
本文主要对钛合金及其扩散焊疲劳特性研究进展进行了综述,总结了钛合金及其焊接后疲劳裂纹萌生和扩展的规律。概述了钛合金的化学成分和分类,以及常用焊接方法,重点介绍扩散焊的特点和优势。描述了循环载荷作用下滑移带形成和位错的运动现象,阐明疲劳裂纹萌生的机制。钛合金微观组织的选择是优化力学性能的常见方法,现有研究表明,制备层合结构是降低钛合金疲劳裂纹扩展速率的一种重要调控手段。不合适的焊接工艺参数会导致接头缺陷的形成,后续热处理能够降低接头缺陷,并提高焊接构件的疲劳寿命和疲劳强度。最后,简述了扩散焊制备多层和异种钛合金层合结构来实现构件高损伤容限的可行性。
关键词:
现代飞机对高机动性、轻质、长寿命和高可靠性等技术性能提出更高的要求。而钛合金因具有一系列优异的综合性能,已经发展为现代飞机主体结构的重要材料,其应用水平甚至成为衡量飞机结构选材先进性的重要标志之一。Ti及钛合金是20世纪50年代发展起来的一种多用途金属结构材料,具有高的比强度,优良的耐蚀性、耐热性、生物相容性,以及无毒无磁等优点,但因其价格显著高于钢和Al,因此,更多被应用于航空航天、石油化工、海洋和生物医学等高端领域[1?3]。美国第三代某型号飞机的钛合金用量占总结构材料的26.1%,第四代某型号飞机的钛合金用量占比达到41%[4],另外,Ti及钛合金在商用飞机结构件中的用量也逐年增长(图1[5])。然而钛合金的疲劳实验研究表明,其损伤容限较差,疲劳裂纹一旦萌生,裂纹扩展速率往往较高,高的裂纹敏感性使得钛合金构件裂纹扩展寿命降低,严重影响飞机的长期安全使用。2007年美国空军某三代机飞行过程中因上纵梁疲劳断裂,导致整机解体和坠毁。多种飞机因零部件或连接处的局部疲劳损伤,引发整个机身断裂或飞机坠毁,造成多人受伤或丧生。2002年,波音747-200型客机的机尾蒙皮累积磨损致疲劳失效,造成飞机的机尾脱落并失控,最后因舱体突然失压,结构解体,全机225人全部遇难。以上事例表明,疲劳断裂给航空工业以及人类社会的发展带来了巨大损失。因此,飞机钛合金结构中疲劳裂纹快速扩展的难题亟待关注和解决[6]。为改善钛合金结构件的疲劳裂纹快速扩展的特性,目前,已研制出损伤容限较好的新型钛合金材料,如国内自主研发的TC4-DT、TC21钛合金、美国Ti-6-22-22S钛合金。经过长期的探索,钛合金材料成分体系已经日渐成熟。与此同时,构造能提高损伤容限性能的钛合金结构形式也是较为有效的途径。
图1

图1 商用飞机中Ti的使用量随时间推移不断增加(气泡大小表示飞机载客量)[5]
Fig.1 A increase in consumption of titanium in commercial aircraft over time (Bubble size represents the passenger capacity of the aircraft)[5]
1 钛合金及其焊接
钛合金中添加的合金元素依其稳定组织类型可分为以下3类。(1) α稳定元素,能够大量固溶且稳定α-Ti
Table 1
Titanium alloy type | Domestic | Similar foreign brand | Nominal chemical composition | Heat treatment | Tensile |
---|---|---|---|---|---|
brand | (mass fraction / %) | strength | |||
MPa | |||||
α type | TA1 | USA, Ti-40 | Ti | Annealing | 300 |
Near α type | TA18 | USA, Ti-3-2.5 | Ti-3Al-2.5V | Annealing | 620 |
TA15 | RUS, BT20 | Ti-6.5Al-2Zr-1Mo-1Al | Annealing | 930 | |
α + β type | TC4 | USA, Ti-6-4 / RUS, BT6 | Ti-6Al-4V | Annealing | 895 |
TC18 | RUS, BT22 | Ti-5Al-5Mo-5V-1Cr-1Fe | Double annealing | 1080 | |
TC11 | RUS, BT9 | Ti-6.5Al-3.5Mo-1.5Zr-0.3Si | Annealing | 1030 | |
TC21 | USA, Ti-6-22-22s | Ti-6Al-2Sn-2Zr-3Mo-1Cr-2Nb-xSi | Double annealing | 1100 | |
Near β type | TB6 | USA, Ti-1023 | Ti-10V-2Fe-3Al | Solution and aging | 1105 |
Metastable β type | TB5 | USA, Ti-15-3 | Ti-15V-3Cr-3Sn-3Al | Solution and aging | 1080 |
TB8 | USA, β21S | Ti-15Mo-3Al-2.7Nb-0.2Si | Solution and aging | 1250 |
图2

图2 Mo当量钛合金类型示意图
Fig.2 Schematic of titanium alloy types with Mo equivalent (Tβ —critical temperature of completely α phase to β phase transformation; Ms and Mf—martensite transformation start and finish temperatures, respectively; C1—the highest Mo equivalent concentration of alloying element for complete martensitic transformation, C2—the lowest Mo equivalent concentration of alloying element without martensitic transformation)
经过近70年的研究和发展,我国航空航天用Ti及钛合金牌号已经达到29个[10]。我国飞机用结构钛合金体系随分级设计需求而发展的趋势如图3所示。飞机结构钛合金的发展设计经历4代,依次是静强度设计、疲劳寿命设计、破损安全设计、损伤/耐久性设计。第一代主要为低强度TA1、TC2、TA7等Ti和钛合金(抗拉强度低于700 MPa)以及中强度TC4、TA15、TC18等钛合金(抗拉强度介于700?1000 MPa之间)。这类Ti及钛合金的合金元素含量低、冶炼技术成熟、生产成本低,且具备优良的塑性和韧性。第二代主要为高强度TC16、TC18、TB5、TB6等钛合金(抗拉强度介于1000?1250 MPa之间)。该类钛合金中β稳定性合金元素含量明显提高,常用的热处理方式是双重退火、退火+时效或固溶+时效。通过精确控制热加工和热处理工艺能够使该类合金获得优异的疲劳寿命和疲劳强度。第三代主要为超高强度TB8、TB19等亚稳β钛合金(抗拉强度高于1250 MPa)。该类钛合金中β稳定性合金元素含量大幅增加,加热至Tβ (Tβ 为α相全部转变为β相的温度)以上,获得全部β相,经水冷或空冷至室温,稳定的高温β相能够全部保留下来,随后的时效处理析出细小和弥散的α相,析出强化是最主要的强化机制。该类近β和亚稳β钛合金经固溶+时效热处理,能够获得超高的强度和较好的塑性和断裂韧性。第四代主要为高强度TC21和中强度TC4-DT等高损伤容限型钛合金。TC4-DT合金抗拉强度介于825?900 MPa之间,具有高的断裂韧性(KIC ≥ 90 MPa·m1/2)、较低的疲劳裂纹扩展速率、较高的疲劳裂纹扩展门槛值ΔKth (TC4-DT合金在应力比R = 0.5时,ΔKth ≈ 4.5 MPa·m1/2,而普通TC4合金的ΔKth ≈ 3.6 MPa·m1/2)[14]。另外,TC21合金抗拉强度介于1030?1100 MPa之间,具有较高的断裂韧性(KIC ≥ 70 MPa·m1/2)、较低的疲劳裂纹扩展速率、较高的ΔKth (TC21合金在R = 0.5时,ΔKth ≈ 2.7 MPa·m1/2)[11]。近年来,随着钛合金加工和热处理新工艺以及新化学成分的深入研究,钛合金的强韧性和抗疲劳性能进一步提高。Mantri等[15]对TB8钛合金的研究表明,通过调控固溶处理后的低温预时效时间,可以提前析出大量弥散分布的纳米级ω相,ω相在随后的高温时效过程中促进α相的形核和生长,最终合金的抗拉强度可达1.8 GPa,断后延伸率为6%。
图3

图3 我国飞机结构钛合金发展趋势示意图
Fig.3 Schematic of development trend of titanium alloys for aircraft structure in China
Ti及钛合金在加热时易与H、C、N、O反应,焊接过程中,300℃快速吸H,600℃快速吸O,700℃快速吸N,高于1000℃时其与C形成化合物[16],这些杂质气体的吸入,使得杂质原子与Ti原子反应形成化合物,导致Ti及钛合金脆化。为了保证焊接接头的质量,Ti及钛合金往往在Ar气氛围或真空环境下进行焊接。目前Ti及钛合金的主要焊接方法包括激光焊、电子束焊、等离子弧焊、扩散焊、搅拌摩擦焊和钎焊等[17?20]。
激光焊是基于高能量密度的激光束作为热源的一种焊接方法。激光焊Ti及钛合金时必须施加惰性气体作保护,保护气体在500℃应保持稳定。激光焊也适用于高温钛合金的连接,其接头的强度和塑性较好。钛合金的导热系数小(15.24 W/(m·K),约为钢铁的1/5),对红外线光吸收率比较高,因此钛合金的激光焊较容易实现深穿透焊。电子束焊是指加速和聚焦的电子束流轰击焊缝的一种焊接方法。真空电子束的功率密度可达106 W/cm2以上,电子束焊Ti及钛合金的焊缝和热影响区都很窄,且焊缝和热影响区不会出现粗大的片状α相,选择合理的电子束焊参数能够保证良好的接头处微观组织和力学性能。由于电子束焊热影响区小、接头强度高且有真空保护等优点,电子束焊已经大量应用于Ti及钛合金薄板和精密零件的连接。等离子弧焊是利用等离子弧高能量密度束流作为热源的一种熔焊的方法。2.5?15.0 mm厚的Ti及钛合金板材采用穿孔型或小孔方法可一次焊透,并可防止气孔产生。采用3?10 A的电流能够很好地完成0.08?0.60 mm厚Ti及钛合金薄板的微束等离子弧焊。搅拌摩擦焊是通过高速旋转的焊具与工件摩擦产生的热量使被焊材料局部熔化,焊缝处材料在转动摩擦力作用下流向后部,并在焊具的挤压下完成结合的一种固相连接技术。一般而言,搅拌区发生了动态再结晶,晶粒为比母材还细小的等轴晶,而热影响区只发生较低温度的退火。整个焊缝处的硬度和抗拉强度要低于母材,且搅拌区的硬度最低。钎焊指钎料(其熔点低于焊件材料的熔点)和焊件同时加热到钎料熔化的温度后,液态钎料填充焊件的缝隙,冷却后完成连接的一种焊接方法。钛合金钎焊接头的性能取决于钎料与钛合金的反应产物,这关系到钎料类型和焊接热循环参数,钛合金钎焊的钎料主要为银基和Ti-Zr基钎料。
扩散焊是将2个或多个待焊材料叠放在一起,并置于真空或保护气氛炉内,在一定温度和压力作用下,待焊接表面微小的凹凸处发生局部塑性变形后,接近一半的待焊表面紧密接触,在持续的保温保压的时间段内界面附近原子相互扩散而形成冶金连接的一种固相焊接方法[21,22]。扩散焊具有以下优点:(1) 接头质量好,同种材料接头的显微组织和性能与母材接近或相同;(2) 焊件变形小、尺寸精度高;(3) 可同时连接结构复杂、多接头的结构件;(4) 可以连接异种材料和薄厚尺寸相差较大的工件。本课题组致力于钛合金[17]、铝合金、不锈钢和镁合金等材料的扩散焊研究,并通过引入中间层、钛合金热氢处理[23]、电流辅助加热等技术提高扩散焊界面质量和焊接效率。将置氢0.2% (质量分数)的Ti2AlNb基合金与TC4合金快速加热至850℃进行扩散焊实验,扫描电镜分析表明,异种合金接头具有分层结构,依次是Ti2AlNb母材、连续β相层、非连续α相层、等轴β相层及双态TC4母材,良好的接头剪切强度达到711 MPa (图4[24] )。通过设计加工脉冲电流辅助扩散焊Ti2AlNb合金板材装置,对不同电流密度下的板材温度分布进行了实验研究,在?电流密度4.58 A/mm2下成功地实现了Ti2AlNb合金的完全冶金键合,并讨论了微观组织演变和微孔隙周围电流的绕行效应[25,26]。
图4

图4 置氢的Ti2AlNb/TC4异种钛合金扩散焊界面SEM微观组织表征、EDS分析与接头强度[24]
Fig.4 Joint microstructures and element distributions by SEM and EDS as well as shear strength of hydrogenated Ti2AlNb/TC4 alloys by diffusion bonding[24]
(a) overall joint microstructure
(b) corresponding element distribution across the interface (Inset shows the local joint microstructure. I, III—β phase layers; II—α phase layer; IV—α + β phase layer; V—B2 + O phase layer)
(c) fracture morphologies of hydrogenated sample (cleavage rupture marked by black rectangle)
(d) variation of joint shear strength with diffusion zone width (microstructural observations of unhydrogenated sample in the inset)
2 疲劳裂纹形核
疲劳破坏是指在交变循环的应力(低于屈服强度)或应变作用下,材料的局部结构逐渐引起变化和内部缺陷损伤累积,经一定循环周次后,由于局部塑性变形致使疲劳微裂纹萌生和扩展,随后微裂纹会逐步发展为宏观裂纹,宏观裂纹继续扩展,最终工件被完全断裂破坏。疲劳破坏是各种工程结构件失效的重要形式之一,大约90%的断裂都是由疲劳损伤引起的[27]。总的来说,材料的整个疲劳破环过程主要包括疲劳裂纹的萌生、扩展和瞬时断裂3个阶段[28]。钛合金的疲劳特性与微观组织有着密不可分的联系,包括相组成、相分数、形貌、晶粒或集束的尺寸、织构、晶粒取向等。另外,焊接过程中热源的能量比较集中,接头处因快速加热和冷却引起的微观和宏观缺陷,热量分布不均匀带来的复杂微观结构和组织,都会直接或间接地增加疲劳裂纹萌生的可能性[29]。
高周疲劳过程中裂纹萌生寿命(包括微米级裂纹的萌生及扩展寿命)占全寿命的绝大部分,甚至达到90%[30]。金属材料疲劳破坏的起源常在材料的自由表面或内部缺陷处,因为这些区域易引起较高的局部应力,进而引起局部微观组织塑性变形。TC4是目前使用量和应用面最广泛的钛合金,通过控制机械加工和热处理工艺能够获得不同的微观组织,包括等轴组织、双态组织、网篮组织和片层组织。Gilbert和Piehler[31]以及Ivanova等[32]研究了等轴和双态TC4合金分别在低周和高周疲劳条件下的疲劳裂纹萌生,观察到裂纹总是在具有准解理面的初生α晶粒中萌生。Oberwinkler等[33]研究了锻造的双态TC4合金正循环拉伸应力下疲劳裂纹的形成,发现疲劳裂纹仅在柱面和基面滑移系的初生α晶粒中萌生,且这些初生α晶粒的Schmid因子非常高。Meng等[34]研究了片层组织的TC4合金拉伸应力下疲劳裂纹的萌生,指出疲劳裂纹萌生主要沿着接近基面滑移系的界面α相上进行。Man等[35]利用透射电镜观察发现,平行的驻留滑移带(persistent slip bands,PSBs)被束状结构的位错分开,在基体上形成类似梯子的结构。此外,PSBs中的位错墙和基体结构中的位错密度都比较高[35,36]。疲劳损伤的典型过程如图5[36]所示,外力加载过程诱导局部微观塑性变形,位错沿着滑移面和滑移方向运动至材料表面,且卸载过程位错并不会返回加载前位置,这样会在材料表面留下一个不可恢复的滑移台阶,这种大量累积的滑移台阶可造成表面粗糙化,循环饱和的过程出现了PSBs,PSBs内的局域化应变以挤入挤出带的形式沿着PSBs运动到材料表面释放,造成局部挤入挤出带的应力和应变集中,最终在材料表面的挤入挤出带位置萌生微裂纹。
图5

图5 梯形结构的驻留滑移带内部结构与产生的表面凹凸的关系示意图[36]
Fig.5 Schematics of the relation of the internal structure of a ladder-like structure of a PSBs and resulting surface relief (cv—vacancy concentration, b —Burgers vector, PSB—persistent slip band, PSM—persistent slip marking)[36]
(a) point defect production in PSB and their migration to the matrix
(b) resulting surface profile consisting of central extrusion and two parallel intrusions
3 疲劳裂纹扩展
在循环加载作用下,多数金属材料在发生断裂之前要经历宏观疲劳裂纹扩展阶段。疲劳裂纹扩展可用da / dN-ΔK (其中,a为疲劳裂纹扩展长度,N为疲劳循环次数,ΔK为应力强度因子幅)的双对数坐标下的裂纹扩展速率曲线来表示(图6)。由图可见,曲线分为3个区域:Ⅰ区为疲劳裂纹的萌生阶段,当ΔK小于或等于一个下限时,疲劳裂纹几乎不发生扩展,ΔK的下限称为疲劳裂纹扩展门槛值(ΔKth);Ⅱ区为疲劳裂纹稳态扩展阶段,ΔK和疲劳裂纹的扩展速率呈线性关系,利用这一线性关系可预测疲劳裂纹扩展寿命,也是疲劳裂纹扩展研究的重点阶段;Ⅲ区为疲劳裂纹扩展高速率区,当应力强度因子K趋近于材料的断裂韧度KC时,试样快速失稳断裂。
图6

图6 疲劳裂纹扩展速率与ΔK的函数曲线
Fig.6 Fatigue crack growth rate (da / dN) as a function of ΔK (a—fatigue crack length, N—number of load cycle, ΔK—stress intensity factor range, ΔKth—fatigue crack growth threshold, Kmax—maximum of stress intensity factor range, KC—fracture toughness, m—material constant)
1957年,裂纹尖端区域内应力分布参量概念(即K)的提出奠定了疲劳裂纹扩展规律和线弹性断裂力学研究的基础[37]。为了定量描述疲劳裂纹的扩展速率,Paris等[38]在此基础上提出了ΔK的概念,并指出K与裂纹尖端附近的应力和应变场类似,表征裂纹扩展速率的主要参量也应该是K,并提出:
式中,da / dN为每一次载荷循环中疲劳裂纹长度前进量,ΔK = Kmax - Kmin (其中,Kmax和Kmin分别是疲劳过程中单次疲劳应力循环应力强度因子的最大值和最小值),C和m为材料常数。不足的是,
式中,Cb和mb是材料常数。Forman等[39]在
除服役的外部条件外,疲劳裂纹扩展还与Ti及钛合金的微观结构有关。一些研究[41?47]报道了双态、层状和等轴晶粒等微观特征对钛合金的疲劳性能和行为的影响。Shi等[48]基于不同双退火工艺研究了不同网状组织的近β钛合金的疲劳裂纹扩展行为,指出长且宽的α片层最有利于提高裂纹扩展路径的弯曲度。另外,钛合金的组织和微观结构特征,如晶粒尺寸[49]、形态[50]、相分数[51]、晶粒取向[52]和织构[53]对疲劳裂纹扩展有明显的影响。Wang等[54]利用原位扫描电镜观察增材制造TC4钛合金的疲劳短裂纹扩展(图7[54]),指出持久滑移带促进了裂纹沿滑移线扩展。由于位错滑移的势垒效应,晶界能阻碍裂纹扩展。裂纹分叉和二次裂纹形成分散了主裂纹的扩展驱动力,降低了主裂纹的前进速率。石晓辉[55]还基于扩展有限元法,采用Maxps准则作为损伤起始判据,利用Abaqus软件计算了TC18合金标准紧凑拉伸(CT)件裂纹尖端损伤和扩展行为。结果表明,裂纹沿垂直于加载力的方向扩展,属于典型的Ⅰ型(张开型)裂纹扩展;后期裂纹尖端前形成45°剪切微裂纹,即转为Ⅱ型(滑开型)裂纹扩展。
图7

图7 基于同位扫描电镜观察增材制造TC4钛合金的疲劳裂纹扩展过程[54]
Fig.7 Observation of fatigue crack growth process of additively manufactured TC4 titanium alloy based on in situ scanning electron microscope (CTOD—crack tip opening displacement)[54]
(a) 11410 cyc (b) 12139 cyc (c) 17551 cyc (d) 19806 cyc (e) 20852 cyc (f) 21561 cyc
1990年,Clegg等[56]参考贝壳特殊的强韧化原理,首次提出建立层合结构提高韧性的方法,并在脆性材料中加入高韧性材料层,制备出了陶瓷基复合结构。层合结构主要是由韧性材料和脆性材料相互叠加,主要包括金属/金属间化合物[57]、金属/陶瓷[58]、金属/金属基复合材料等[59]层合结构。研究表明,层合结构不仅能够改善材料准静态载荷下的强韧性,而且所引入的连接界面能够改变疲劳断裂行为。Dong等[60]利用扩散焊技术制备了TC4钛合金层合结构,研究连接界面对疲劳裂纹扩展和准静态拉伸力学性能的影响,发现连接界面与基材的微观织构差异降低了疲劳裂纹沿厚度方向扩展的速率。He等[61]和Liu等[62]在TC4钛合金扩散焊层合结构中人为引入未焊合区,延缓了疲劳裂纹的扩展,提高了疲劳裂纹扩展阶段寿命,但是未完全焊合区域的存在会降低层合结构的准静态力学性能(图8[61,62])。通过同步辐射X射线扫描,Junet等[63]对扩散焊试样中心含有激光钻孔缺口的TC4柱状件的疲劳裂纹进行了表征,直接测试到试样内部裂纹扩展速率低于相同长度的表面裂纹时的扩展速率。Adharapurapu等[64]研究了韧性层厚度和体积分数对Ti/Al3Ti裂纹扩展速率的影响,指出随着韧性相Ti体积分数的增加,Ti/Al3Ti的疲劳裂纹扩展抗性增加。综合异种材料层合结构的疲劳性能研究发现,疲劳裂纹尖端在异质界面处钝化是抑制裂纹扩展的主要原因,次生裂纹的出现也可改善裂尖处的应力场和塑性变形场的分布。
图8

图8 TC4钛合金扩散焊层合结构疲劳断口形貌和裂纹扩展[61,62]
Fig.8 Fatigue fracture morphologies and crack growth of TC4 titanium alloy laminate by diffusion bonding
(a) fractography of the laminates with unbonded zones (x—width direction, y—thickness direction; A—the direction along x-axis, B—along -x-axis, C—along y-axis; a1—distance of the outmost point on the left crack front from y-axis, a2—distance of the outmost point on the right crack front from y-axis)[61]
(b) variation of fatigue crack growth rate with crack length and corresponding fractography (ar—half-crack length)[61]
(c) fatigue crack growth process of laminated structure with unbonded zones based on the extended finite element method (Red regions represent initial crack)[62]
近年来,研究人员[65?70]基于调控扩散焊参数,如温度、时间、压力,还有添加中间层,对异质金属或合金的扩散焊界面微观组织演化和力学性能进行了大量的研究。朱富慧[71]和贾国朋[72]致力于钛合金和钛基合金的扩散焊研究,完成了TC4/Ti2AlNb基合金、TA15/Ti2AlNb基合金、TC4/TB8合金等扩散焊工艺与机理的研究,如图9a[72]和b所示。将异种材料连接到一起,可以综合各材料的性能优势。异种材料扩散焊时,连接界面两侧的合金元素相互扩散,在界面处形成几微米至几十微米宽度的过渡层,过渡层处的化学成分、微观组织和力学性能不同于母材。Li等[73]还利用扩散焊工艺制备了TC4/TA15钛合金异质层合结构(图10[73]),通过控制扩散焊参数获得层间微观取向差异的α相,α相晶体学取向随机的TA15合金能减缓疲劳裂纹的扩展,同时层合结构的准静态拉伸性能与合金母材拉伸性能相当。因此,经过合理设计的异种钛合金层合结构不仅能保持材料静态载荷下的强韧特性,而且异质层材料能够改变疲劳断裂行为,在航空航天领域具有广阔的应用前景。
图9

图9 异种钛合金[72]和钛基合金的扩散焊界面微观结构
Fig.9 Microstructures of diffusion bonded interface between heterogeneous titanium alloy and titanium-based alloy
(a) TA15/Ti2AlNb[72] (b) TC4/TB8
图10
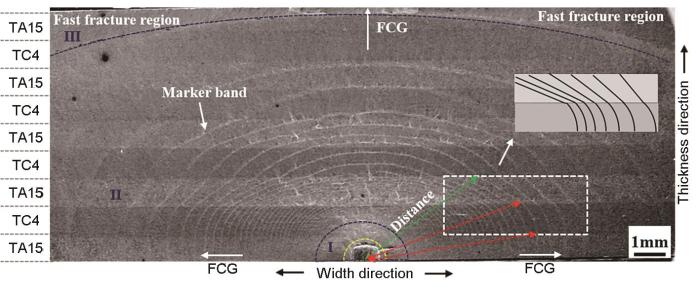
图10 扩散焊制备TC4/TA15合金异质层合结构疲劳裂纹扩展断面特征[73]
Fig.10 Fracture characteristics of dissimilar laminate of TC4/TA15 alloys by diffusion bonding (FCG—fatigue crack growth; red and green arrows present the distance between fatigue crack and central defect in the TC4 and TA15 layers, respectively; schematic illustration of fatigue crack in the white dotted square)[73]
Du等[74~76]在扩散焊制备多层结构件领域进行了研究,如基于超塑成型/扩散焊的方法制备Ti2AlNb基合金4层蜂窝状结构件、TA15钛合金4层中空结构件、热弯和扩散焊结合方法制备TiAl合金波纹夹芯结构件。徐芳菲[77]采用扩散焊技术成功制备了多层结构样件,共7层(3层Ti2AlNb/1层TC4/3层Ti2AlNb)的结构样件和42层膜盒结构样件(图11a和b[77])。薄壁窄筋中空结构作为一种典型的轻量高强结构(图11a),具有较好的气动外形、易设计的结构、良好的高温强韧性和耐冲击性、全寿命成本低、易于制成模块化结构、易检查维护并可进行损伤容限设计等优点,已在导弹的舵面和翼面等结构件上得到应用。目前,钎焊或电子束焊制备超多层结构件技术较为成熟,然而随层数的增多,焊缝数量急剧增多导致的生产周期长和焊缝质量难以保证等问题随之而来。因此,徐芳菲[77]提出一种多层结构局部扩散焊制备膜盒的方法,结果表明,该方法能够获得质量和结构尺寸良好的接头。
图11

图11 扩散焊层合结构样件[77]
Fig.11 Laminated structure samples by diffusion bonding
(a) three layers of Ti2AlNb / one layer of TC4 / three layers of Ti2AlNb hollow structure with thin walls and narrow ribs
(b) 42 layers of diaphragm[77]
4 疲劳强度与寿命
疲劳寿命评估方法总结起来主要有2类:一是基于传统的应力法,以应力-寿命(S-N)曲线计算寿命;二是以缺口应力评定为基础,应用应变疲劳进行寿命评估。一般规定在N达到107 cyc,材料不失效时的最大应力为该材料的疲劳极限。图12描述了N与应力幅之间的关系,并根据N将疲劳破坏分为超低周、低周、高周和超高周疲劳破坏。
图12

图12 疲劳循环周次与施加应力幅的关系
Fig.12 Relationship between fatigue cycle and applied stress amplitude
一般而言,焊接接头的抗拉强度高于母材,然而由于接头韧性的下降或缺陷的存在使得它的疲劳强度和寿命常低于母材。Sanders等[78]研究了搅拌摩擦焊接TC4合金的接头疲劳性能,一般而言,在给定的循环应力水平下,接头寿命相对母材疲劳寿命降低约20%,这是因为焊接过程造成的损伤或缺陷留在疲劳试样的接头处,它们在相对缺口敏感的材料中起到应力集中的作用,诱发疲劳裂纹在此萌生,导致疲劳性能降低。Edwards等[79,80]比较了TC4合金搅拌摩擦焊的对接接头和角接头的疲劳性能,结果表明,焊接后试样的疲劳寿命降低至母材的19%左右,在焊接后进行适当的热处理,可以提高焊接件的疲劳寿命,使其达到母材的80%左右。Nakai等[81]发现,搅拌摩擦焊双相Ti531C钛合金时,增加退火工艺可以改善接头的高周疲劳性能,但疲劳性能仍低于母材,这主要是因为搅拌区β相中形成的少量等温ω相,以及混合区与母材之间的界面处不连续的微观结构,都是潜在的应力集中区,最终导致疲劳寿命降低。扩散焊在整个焊接过程中无材料的熔化,即实现了固态连接,可自由选择是否添加中间层辅助焊接。因此,扩散焊钛合金能够降低接头组织的恶化,扩散焊的钛合金构件已经成功地应用于航空航天等领域。谢佩玉等[82]在910℃、3.4 MPa、1 h条件下扩散焊连接TC4合金,结果表明,其焊接接头抗拉强度达到973 MPa,与母材相当,而接头S-N曲线明显下移,同载荷水平时下降约40%。Tuppen等[83]扩散焊TC4 (即Ti6/4)/Ti550异种钛合金,测试其低周疲劳载荷下的S-N关系。结果表明,与原始的普通热处理的TC4和Ti550合金相比,扩散焊试样显示出与较弱的TC4合金相当的低周疲劳响应(图13[83])。不同接头方向的试样表现出很接近的低周疲劳性能,且疲劳裂纹更多在接头处的局部非熔合缺陷处萌生。
图13

图13 Ti550/TC4合金扩散焊接头和疲劳性能[83]
Fig.13 Joints and fatigue properties of Ti550/TC4 alloys by diffusion bonding[83]
(a) cylindrical geometry of low cycle fatigue (LCF) specimens (unit: mm)
(b) microstructure of Ti550/TC4 (Ti6/4) titanium alloys
(c) LCF S-N curves of Ti550/TC4 specimens compared with the S-N curves of traditional TC4 (solid line) and Ti550 (dotted line) alloys (Nf—number cycle to failure, ST—solution treatment, NFD—non-fusion defect)
5 总结与展望
本文主要综述了钛合金与其扩散焊疲劳裂纹的形核、扩展以及疲劳强度的特性。钛合金的微观组织与其合金元素密切相关,通过控制化学元素和含量,进而可调控钛合金的微观组织和力学性能。在循环应力或应变作用下位错运动诱导驻留滑移带,金属表面形成挤入挤出滑移带,易于导致疲劳裂纹在此萌生。扩散焊制备的钛合金层合结构能够有效降低疲劳裂纹在厚度方向上的扩展速率。针对钛合金疲劳裂纹扩展速率快和损伤容限性能差的关键问题,提出异种钛合金扩散焊制备层合结构来减缓疲劳裂纹扩展速率。这是因为异质焊接界面和层间不同的材料性能易于调控,且不降低准静态拉伸性能。Ti及钛合金的传统真空扩散焊存在温度高、周期长等问题,通过对Ti及钛合金待连接的表层一定深度热氢处理,扩散焊完成后再真空热循环溢出剩余的H。H作为临时合金元素不仅能促进α向β相变,改善合金的高温塑性,大幅降低扩散焊所需的温度,而且能够优化组织形态,有效改善扩散焊接头的力学性能。添加中间层辅助扩散焊同质或异质钛合金,母材和中间层材料在接头处充分进行原子扩散,通过调控新相和微观结构的形成,最终降低扩散焊钛合金的疲劳裂纹扩展速率。同样,层合材料的脆性层材料和韧性层材料的厚度匹配,不仅影响准静态拉伸变形的应力-应变分配,也会影响疲劳裂纹的形成位置和扩展速率。实际工程应用不能只考虑层合结构件的单一性能,需要综合衡量力学性能,如强韧性、疲劳、冲击和压缩等性能,并且还要考虑层合结构的制造工艺稳定性和层间板材料的价格。因此,制造低成本和综合力学性能优异的层合结构件还需深入研究。
来源--金属学报