分享:热障涂层高熵合金粘结层材料研究进展
热障涂层是现代高性能航空发动机的关键材料和技术,能够显著提升热端部件(比如涡轮叶片)的工作温度,同时保护热端部件不受高温氧化和腐蚀。金属粘结层作为热障涂层的关键组成部分,直接决定了热障涂层体系的服役性能和寿命。然而,传统MCrAlY粘结层因为存在抗氧化性能不足、粘结层-基体互扩散严重以及高温强度不足等问题,导致服役温度不足1100℃,无法满足下一代超高温热障涂层的应用温度要求。基于传统MCrAlY粘结层中存在的关键问题,本团队提出高熵合金粘结层的设计思路,旨在突破传统粘结层的应用温度局限。本文重点介绍了Y/Hf-NiCoCrAlFe高熵合金的抗氧化与抗热腐蚀性能,同时也对此高熵合金粉体与粘结层的抗氧化性能进行了阐述,最后对高性能高熵合金粘结层的发展方向进行了展望。
关键词:
热障涂层广泛应用于航空发动机和地面燃气轮机燃烧室与涡轮叶片等热端部件的高温防护,结合先进的气膜冷却技术,能够显著提高热端部件工作温度,大幅提升发动机工作效率和服役寿命[1~3]。热障涂层结构是一个复杂的多层涂层体系,其包括具有优异高温力学性能的高温合金基体、提供抗氧化性能的金属粘结层、保证隔热效果的陶瓷顶层以及在高温氧化之后在金属粘结层和陶瓷顶层之间生成的氧化层[4,5]。热障涂层失效通常发生在陶瓷层-氧化层界面或氧化层-粘结层界面处,通过界面裂纹的萌生、扩展,使得涂层发生剥落[6,7]。金属粘结层在热障涂层中发挥承上启下的作用,直接控制氧化层的生长以及涂层之间的界面结合性能。因此,金属粘结层的性能是影响热障涂层服役寿命的关键[7~9]。金属粘结层在热障涂层系统中主要起到如下作用:(1) 在高温服役过程中,其表面形成连续致密的α-Al2O3阻氧层,保护高温合金基体不被氧化;(2) 作为中间层,缓解高温合金基体与陶瓷顶层由于热膨胀系数不匹配而形成热失配现象。因此,粘结层材料需要具备以下特性:(1) 充足的Al供应,能够形成致密的α-Al2O3阻氧层;(2) 与高温合金较为相近的热膨胀系数,从而充分缓解热失配现象;(3) 高温化学稳定性;以及(4) 与高温合金部件良好的界面结合,并且与陶瓷顶层不发生化学反应等特性。
传统MCrAlY (M = Ni、Co或NiCo)粘结层因具有良好的抗氧化性能和抗热腐蚀性能成为目前最常用的金属粘结层材料,也是应用比较成熟的粘结层材料[10~15]。Ni、Co通常是金属粘结层的基体元素,起到抗氧化和抗热腐蚀的作用,Co还能改善涂层的界面结合;Cr元素的添加能够降低形成α-Al2O3所需的临界Al含量,促进致密阻氧层的快速形成,Cr含量一般高于20% (质量分数,下同);通常Al含量控制在8%~12%,以保证充足的Al供给从而形成致密的α-Al2O3层,也不会因为Al含量过高而增加涂层的室温脆性;Y的存在(一般含量小于1%)可以抑制氧化层-粘结层界面孔洞的形成,改善界面结合能,降低氧化层生长速率,从而提高粘结层的抗氧化性能[4,16~18]。MCrAlY通常是由β-NiAl与γ-Ni(CoCr)两相所组成,其中前者保证了合金的强度,后者提供了韧性,通过调控两相的相对比例,从而获得合适的力学性能和抗氧化性能[9,19,20]。MCrAlY粘结层在1050℃以下能保证较为优异的抗氧化性能,但是在1100℃或更高温度下因为存在氧化速率过快、界面缺陷生长以及界面杂质偏析(比如S偏析)等严重问题导致其过早失效[10,14,21]。此外,当工作温度高于1100℃时,MCrAlY粘结层与高温合金基体高温元素互扩散加剧,加速粘结层相变,从而在粘结层中引入过高的热应力。同时,由于MCrAlY粘结层高温强度不足,积累的热应力会导致粘结层界面变形,加速氧化层断裂或热障涂层界面分离[9,22]。综上所述,传统MCrAlY粘结层由于抗氧化性能差、粘结层-基体互扩散以及高温强度不足这3个关键问题,导致其应用温度低于1100℃。随着航空发动机温度的不断攀升,新一代超高温热障涂层成为国内外的研究热点,要求金属粘结层的应用温度超过1100℃,甚至达到1200℃[23]。只有解决了目前粘结层中存在的3大关键问题,才能突破传统金属粘结层的应用温度局限,满足未来超高温热障涂层的应用要求。为突破传统粘结层的应用温度局限,本团队提出了高熵合金粘结层的设计思路,并且取得了一系列原创性成果,因此本文系统介绍了本团队近2年在高熵合金粘结层材料方面的工作进展。
1 高熵合金粘结层材料设计依据
多主元高熵合金是近年来材料研究领域的重大突破之一,其颠覆了传统合金存在1种或2种主元素的设计理念,由5种或5种以上的等/近等原子比元素组成,并且倾向于形成fcc或bcc简单固溶体,而非金属间化合物或其他复杂有序相[24,25]。基于高熵合金独特的成分特点,其具有4大核心效应[26~30]:(1) 热力学上的高熵效应。高的混合熵增加了合金的固溶度,有利于固溶体相结构的形成;(2) 动力学上的迟滞扩散效应。不同组元间的相互作用以及晶格畸变,会对组元间的协同扩散产生影响,从而限制了有效的扩散速率;(3) 结构上的晶格畸变效应。高熵固溶体中各种原子随机占据晶体的点阵位置,引起晶格发生严重畸变,对合金的力学、热学乃至化学性能产生影响;(4) 性能上的鸡尾酒效应。各种元素的基本特性以及相互作用使得高熵合金呈现出一种复合的效应。高熵合金由于其独特的结构组成、优异的室温/高温力学等性能,得到了学术界的广泛关注。
本团队提出高熵合金粘结层的设计思路,以传统NiCoCrAl粘结层元素为基本,通过添加第五主元Fe实现多主元高熵化,同时添加微量活性元素改善界面结合,最终设计并制备出活性元素改性NiCoCrAlFe高熵合金粘结层材料。高熵效应能够提高金属粘结层的高温稳定性;动力学上的迟滞扩散效应有望减缓氧化以及降低粘结层-基体互扩散;严重的晶格畸变能够提高合金的高温强度,同时促进Al2O3的形成,提升粘结层的抗氧化性能。基于以上分析,通过粘结层的高熵化设计,有望解决传统MCrAlY粘结层中存在的抗氧化性能差、粘结层-基体互扩散以及高温强度不足3个关键问题,从而突破传统粘结层的应用温度局限。
2 Y/Hf-NiCoCrAlFe高熵合金抗氧化性能
本团队首先设计并制备了活性元素Y与Hf改性的等原子比NiCoCrAlFe高熵合金[31]。图1[31]为Y/Hf-NiCoCrAlFe高熵合金表面形貌透射电镜(TEM)分析。基于TEM高角度环形暗场像,结合TEM选区电子衍射结果可知,合金为自生的纳米共格结构,由A2与B2两相构成,其中A2相为FeCr富集,B2相为NiAl富集,Co在合金中均匀分布(图1[31])。纳米结构对粘结层抗氧化性能的增益作用在文献中被广泛报道,但是传统的纳米结构是由特殊的粘结层制备技术或后期加工获得,比如冷喷涂、磁控溅射或粉体球磨等[32~35]。此类方法获得的纳米结构在高温下容易粗化、稳定性较差,难以在粘结层的长期氧化过程中发挥作用。本团队提出的Y/Hf-NiCoCrAlFe高熵合金中的纳米结构是原位自生形成,不需要依靠任何特殊的制备或加工技术,因此具有优异的高温结构稳定性。Y/Hf-NiCoCrAlFe高熵合金在1100℃下表现出十分优异的抗氧化性能[31]。Al2O3层在长期氧化过程中均匀连续生长,氧化层厚度在氧化1000 h后只有约4.6 μm。此外,氧化层界面处无任何界面缺陷形成,保证氧化层具有优异的界面结合强度。同时,合金在1100℃下的氧化速率常数为3.4 × 10-14 cm2/s,比传统NiCoCrAlY合金氧化速率降低1个数量级以上[31,36,37]。氧化速率越低,表明到达临界氧化层厚度需要的时间越长,因此氧化层抗剥落能力越强[6,8]。
图1
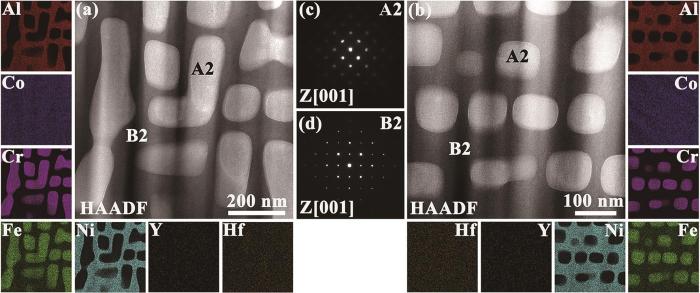
图1 Y/Hf-NiCoCrAlFe高熵合金(HEA) TEM分析[31]
Fig.1 TEM analyses of Y/Hf-NiCoCrAlFe high-entropy alloy (HEA)[31]
(a) high angle annular dark field (HAADF) STEM image of interdendritic region and corresponding EDX analyses
(b) HAADF STEM image of dendritic region and corresponding EDX analyses (c, d) selected area electron diffraction (SAED) patterns of A2 and B2 phases, respectively
粘结层中的Al含量直接影响其结构与抗氧化性能,本团队设计了具有不同Al含量的活性元素Y与Hf改性的NiCoCrAl x Fe (x = 0.7、1.0、1.3,原子分数,%)高熵合金,分别命名为Y/Hf-NiCoCrAl0.7Fe (HEA1)、Y/Hf-NiCoCrAl1.0Fe (HEA2)和Y/Hf-NiCoCrAl1.3Fe (HEA3),结构如图2[38]所示。通过调节Al元素含量,高熵合金呈现出不同的相组成和结构。HEA1合金呈现长条状的晶粒结构(图2a[38]),在单个晶粒内部,存在着大量的板状fcc相,其宽度为0.5~2 μm,而介于fcc板条相之间是纳米尺度A2与B2相共存的网状结构(图2d和g[38])。随着Al含量增加,HEA2与HEA3演变成典型的枝晶结构(图2b和c[38])。单个枝晶内部,包括枝晶干(DR)区域与枝晶间(ID)区域,均是由纳米尺度的A2和B2两相组成(图2e、f、h~k[38])。当x小于1时,增加Al含量能够增加NiCoCrAl x Fe高熵合金的混合熵,导致合金中的原子混乱度增加,晶格势能波动变大,原子协同扩散受到的阻力越大,因此合金结构纳米化的趋势愈加显著。当x等于1时,混合熵达到最大值,继续增加Al含量,混合熵会减小,但是晶格畸变程度会变大,因此合金仍然保持典型的纳米结构(图2g~k[38])[27,28]。随着Al含量的不断增加,高熵合金由三相结构转变成两相结构,且B2相的体积分数也不断增加,同时B2相的几何形状也由方形演变为球形(图2h~k[38])。
图2
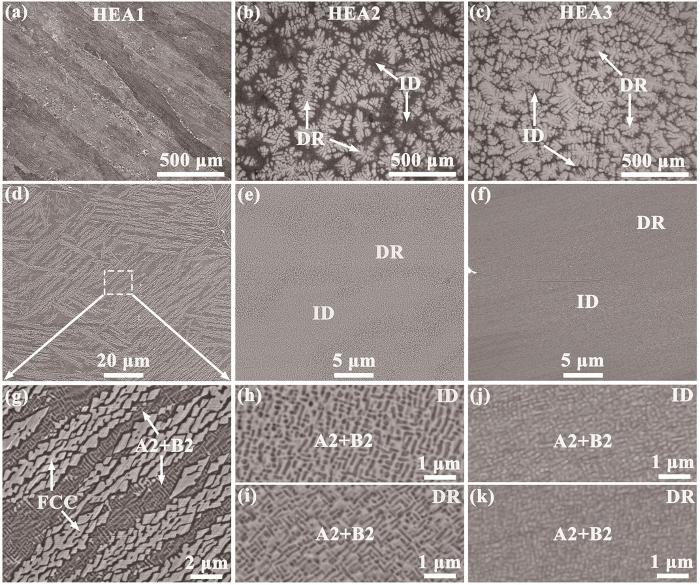
图3[38]展示HEA1、HEA2和HEA3 3种高熵合金在分别氧化250和1000 h之后的氧化层截面形貌。随着氧化时间增加,3种合金的氧化层均稳定缓慢生长,而且氧化层界面均无界面缺陷(包括内氧化、界面孔洞等)生成。同时,连续并均匀的贫Al层出现在氧化层-基体界面下方,说明Al在氧化过程未出现局部过度消耗的情况(图3a~c、g~i[38])。综上所述,无缺陷且稳定生长的氧化层/基体界面诱导合金极强的氧化层抗剥落能力。对于HEA1,虽然氧化层顶部的局部区域生长少量的尖晶石氧化物(Co, Ni)(Fe, Al)2O4,但是在长期氧化过程中,连续的α-Al2O3层仍然能够保持稳定生长(图3d和j[38])。HEA1中尖晶石氧化物的形成主要归因于尺寸相对较大且Al含量相对较低的fcc相(图3a、d、g和j[38]),一旦合金表面形成连续的氧化层,氧化层-基体界面氧分压将显著降低,此时尖晶石氧化物无法继续生长,因此在长期氧化过程中氧化层的增厚仍然以α-Al2O3生长为主。同时,因为尖晶石氧化物较快的生长速率,所以尖晶石区域的氧化层厚度略微高于无尖晶石氧化物区域(图3d和j[38])[39~41]。若不考虑HEA1表面形成的少量尖晶石氧化物,可以发现,随着Al含量增加,Al2O3的生长速率逐渐减慢。基于氧化层厚度,HEA1、HEA2和HEA3高熵合金的氧化速率常数分别为4.2 × 10-14、3.4 × 10-14和2.8 × 10-14 cm2/s。因为3种合金氧化层都是柱状晶为主的结构,O通过柱状晶晶界向内扩散导致氧化层的生长,因此柱状晶的晶界数量(晶粒宽度)成为影响α-Al2O3层生长速率的关键因素[38]。通过对3种合金氧化层断面结构的分析发现,随着合金中Al含量增加,α-Al2O3的柱状晶尺寸不断增加,从而显著减少O向内的扩散通道[38]。因此,增加高熵合金的Al含量能够增加氧化层柱状晶宽度,从而降低氧化层生长速率。但是,Al含量增加导致氧化层柱状晶宽度增加的原因尚且不清楚,需要设计系统的实验来深入研究。
图3
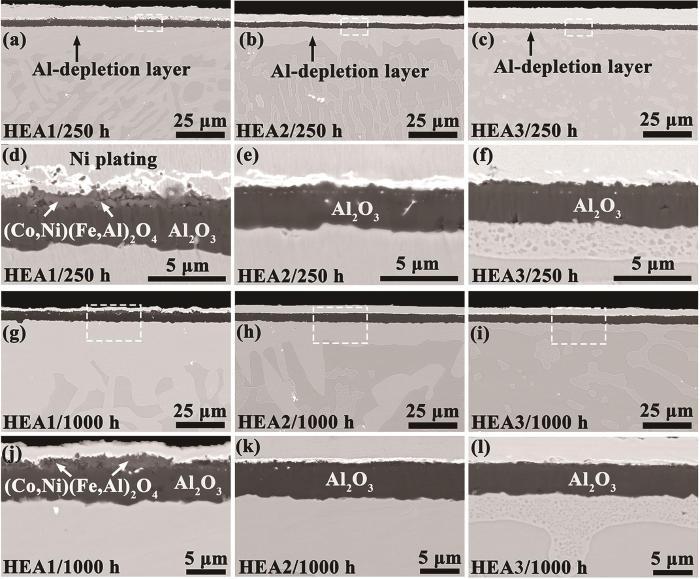
图3 HEA1、HEA2和HEA3 3种高熵合金在1100℃下氧化250和1000 h后的截面形貌[38]
Fig.3 Cross-sectional morphologies of three types of HEAs after oxidation at 1100oC[38]
(a-f) BSE images from HEA1, HEA2, and HEA3 after 250 h oxidation, respectively (g-l) BSE images from HEA1, HEA2, and HEA3 after 1000 h oxidation, respectively
本团队近期研究发现,Y/Hf-NiCoCrAlFe高熵合金在1200℃超高温下同样表现出十分优异的抗氧化性能[42]。Y/Hf-NiCoCrAlFe高熵合金在1200℃下氧化500 h之后,氧化层与合金基体紧密结合,未发生任何形式的氧化层剥落[42]。传统的NiCoCrAl-YHf合金在1200℃下氧化300 h之后则出现严重的氧化层剥落[43]。以上结果表明,即使在1200℃超高温下,Y/Hf-NiCoCrAlFe高熵合金仍然表现出极强的氧化层抗剥落能力,抗氧化性能远远优于传统NiCoCrAlYHf合金。此外,活性元素富集的氧化物(Y或Hf富集的氧化物)均匀地分布在Al2O3晶界处,说明活性元素在合金基体中高度均匀分布[42]。图4[42]显示Y/Hf-NiCoCrAlFe高熵合金在1200℃下氧化100和500 h之后的截面和断面形貌。随着氧化时间增加,氧化层均匀缓慢增厚,氧化层厚度从3.8 μm (100 h)增加到8.2 μm (500 h) (图4a、b、e~g[42])。基于氧化层厚度,该合金在1200℃下的氧化动力学常数为3.9 × 10-13 cm2/s。通过氧化层厚度与质量的换算,基于质量的氧化动力学常数为1.4 × 10-12 g2/(cm4·s)[31,44,45]。传统的FeCrAlYHf合金被认为是氧化速率最慢的抗氧化合金,其在1200℃下的氧化动力学常数约为5.6 × 10-12 g2/(cm4·s)[46]。综上分析可知,Y/Hf-NiCoCrAlFe高熵合金在1200℃下的氧化速率甚至低于传统的FeCrAlYHf合金。此外,Y/Hf-NiCoCrAlFe高熵合金在1200℃下长期高温氧化之后,仍然保持稳定的纳米结构,可能是由于温度越高,合金中高的熵值对降低Gibbs自由能的贡献就越大,因此合金的纳米结构就越稳定(图4c、d、h和i[42])。基于氧化层的断面结构可知,氧化层为完全的柱状晶结构,表明氧化层的生长由O向内扩散控制(图4j和k[42])[47,48]。
图4
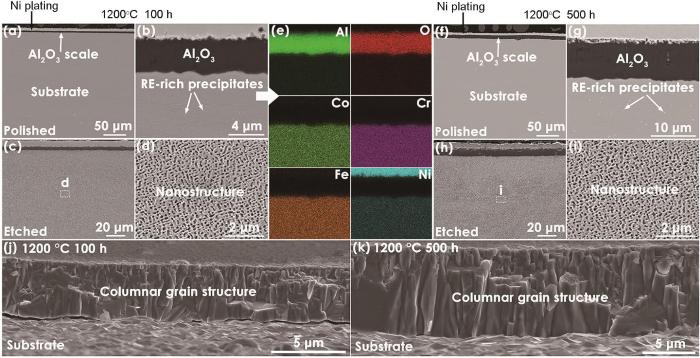
图4 Y/Hf-NiCoCrAlFe高熵合金在1200℃下氧化100和500 h后的截面与断面形貌[42]
Fig.4 Cross-sectional and fractural morphologies of Y/Hf-NiCoCrAlFe HEA after 100 and 500 h oxidation at 1200oC[42]
(a, b, e-g) BSE images (a, b, f, g) with the corresponding elemental maps (e) (c, d, h, i) BSE images after etching(j, k) SEM images after scale fracture
通过分析总结,Y/Hf-NiCoCrAlFe高熵合金具有远超传统高温合金的抗氧化性能,主要归结于以下3个原因:(1) 合金自生的纳米结构加速基体中的Al向外扩散,促进Al2O3保护层的快速形成,保证氧化层的结构稳定性;(2) 合金自生的纳米结构促进活性元素在基体中的均匀分布,增强活性元素效应,且温度越高,纳米结构越稳定,活性元素的增强效应越显著,更加有利于降低氧化速率;(3) 合金具有类似镍基高温合金的纳米共格结构,能够增加合金的高温力学性能,抑制粘结层的褶皱变形。
3 Y/Hf-NiCoCrAlFe高熵合金抗热腐蚀性能
良好的抗热腐蚀性能是粘结层需要具备的关键性能,确保在腐蚀性条件下(如海洋环境或使用低品位燃料时)为热端部件提供足够的防护[49]。MCrAlY (M = Ni、Co或NiCo)系列合金是国内目前应用最广的粘结层材料,也单独作为热防护涂层用于燃气轮机热端部件,相对于β-(Ni, Pt)Al型和γ/γ'型另外2种涂层体系,NiCoCrAlY合金具有更优异的抗I类热腐蚀性能[50,51]。本团队以Y/Hf-NiCoCrAl高熵合金为参照,对比了HEA1、HEA2和HEA3在900℃涂覆Na2SO4-25%NaCl的热腐蚀行为,发现HEA2和HEA3的抗热腐蚀性能比NiCoCrAl合金更加优异,而HEA1则完全不耐热腐蚀[52]。HEA2和HEA3腐蚀过程中剥落较少,腐蚀产物主要为具有保护作用的Al2O3和Cr2O3。NiCoCrAl表面保护性氧化物易剥落,暴露出贫Al的合金本体后生成大量不具备保护作用的松散的(Ni, Co)(Al, Cr)2O4尖晶石。增重和失重曲线显示HEA2和HEA3在熔盐下的吸氧增重和样品剥落失重均优于传统NiCoCrAl,表明高熵合金具有更加优异的抗热腐蚀性能[52]。
HEA2和HEA3的内氧化程度远小于传统的NiCoCrAl合金(图5[52]),且具有不同的腐蚀路径。热腐蚀160 h后,NiCoCrAl合金氧化和硫化深度超过100 μm,腐蚀产物密集,主要沿β/γ相界面分布[53]。HEA3腐蚀产物较少,腐蚀深度远小于NiCoCrAl合金。相界是腐蚀介质短路扩散的主要路径,HEA1和NiCoCrAl合金的热腐蚀均沿相界侵入,腐蚀产物也主要分布在相界。HEA3和HEA2中A2与B2两相界面共格,有效减弱了腐蚀介质侵入;均匀细小的两相结构也减弱了表面腐蚀的不均匀性。HEA3具有更高的Al、Cr含量,贫Al区Al浓度低至4.5% (NiCoCrAl合金中为8.5% (原子分数)),有效Al含量较大幅度提高了抗热腐蚀性能[52,54]。
图5
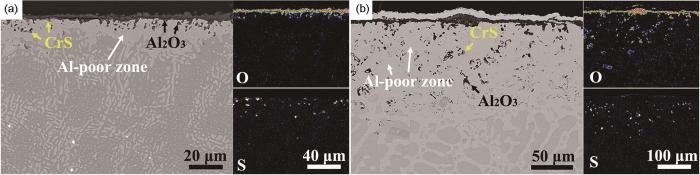
通过辉光放电光谱法(GD-OES)测定了腐蚀介质侵入深度,腐蚀160 h后,Na+在传统的NiCoCrAl合金中的存在深度超过150 μm,而HEA3中则不超过25 μm[52]。Na+侵入深度代表了合金内部形成贯通通道的深度,即合金失效的深度。除了Na元素,O和S的半定量深度在NiCoCrAl中的深度也远超HEA3。
综上分析,Y/Hf-NiCoCrAl x Fe (x = 1.0和1.3)高熵合金抗热腐蚀性能优异的原因有3点:(1) 保护性元素Al和Cr含量充足,且Al的利用率比NiCoCrAl中更高;(2) 共格的相结构降低了腐蚀介质在2种高熵合金中的扩散速率;(3) 细小的相结构促进Al和Cr均匀分布,限制了热腐蚀过程中选择性氯化、硫化和内氧化的深度,进而提高合金的抗热腐蚀性能。
4 NiCoCrAlFe高熵合金粉体抗氧化性能
喷涂粉体是制备粘结层的原料,粉体直接决定粘结层的结构和抗氧化性能。因为活性元素种类与浓度最优配比有待优化,本团队首先通过真空气雾化的方式试制了不含活性元素的NiCoCrAlFe高熵合金粉体,并对其结构与抗氧化性能进行了系统研究[55]。研究结果表明[55]:(1) 粉体具有高的致密度和球形度,通过粒径筛选,可以获得具有优异流动性的粉体,满足下一步热喷涂的需要;(2) 粉体为A2与B2的两相共格结构,与合金结构类似,说明真空气雾化过程不会改变合金的结构;(3) 粉体A2与B2的尺寸约在20 nm以内,远低于合金中的相尺寸(约100 nm),主要是因为真空气雾化过程的冷却速率高于104 K/s,限制了相尺寸的增大[56,57];(4) 不同于块体中的元素分布,粉体中Fe与Co均在基体中均匀分布,这也归结于较高的冷却速率。
因为喷涂粉体为球形,比表面积大,会显著加速氧化过程中Al的消耗速率。因此,本团队选择900、1000和1100℃ 3个较低的温度,将氧化时间控制在48 h之内,以此来评估粉体的抗氧化性能。图6[55]显示NiCoCrAlFe高熵合金粘结层喷涂粉体在900、1000和1100℃下氧化48 h之后的截面形貌和元素分布。氧化层均匀覆盖在整个粉末表面,并且保持良好的界面结合。根据能谱分析,氧化层完全由Al2O3组成,未出现有害的尖晶石氧化物。传统无活性元素掺杂的抗氧化合金在氧化之后会形成大量的界面孔洞以及严重的氧化层剥落[47,58,59]。而NiCoCrAlFe高熵合金粉体在氧化之后并未出现界面孔洞以及氧化层剥落,说明NiCoCrAlFe高熵合金可能具有区别于传统合金的氧化机制,本团队将重点研究。此外,后期通过掺杂合适浓度的活性元素,可以进一步提升喷涂粉体的抗氧化性能,进而保证粘结层优异的抗氧化性能。
图6
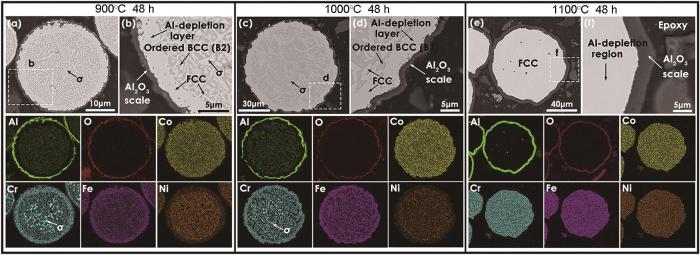
图6 NiCoCrAlFe高熵合金粉体氧化之后的截面形貌与元素分布[55]
Fig.6 Cross-sectional morphologies and elemental maps of NiCoCrAlFe HEA powder after oxidation[55]
(a, b) low magnification and locally amplifying BSE images after 48 h oxidation at 900oC (c, d) low magnification and locally amplifying BSE images after 48 h oxidation at 1000oC (e, f) low magnification and locally amplifying BSE images after 48 h oxidation at 1100oC
5 NiCoCrAlFe高熵合金粘结层抗氧化性能
近期,本团队利用活性燃烧高速燃气喷涂(AC-HVAF)技术在高温合金表面成功制备NiCoCrAlFeY高熵合金粘结层,同时制备传统NiCoCrAlY粘结层作为对照,如图7所示。同时,在NiCoCrAlFeY高熵合金粘结层与高温合金基体之间制备NiCoCrAlY中间层保证涂层界面结合。为避免涂层厚度与表面粗糙度对粘结层抗氧化性能的影响,2种粘结层的厚度均被磨抛至约200 μm (图7a和d)。传统NiCoCrAlY粘结层在1150℃下循环氧化200 h之后,氧化层厚度约为6.6 μm,由顶部尖晶石(Spinel)与底部Al2O3的双层结构组成,同时氧化层沿着界面出现严重的断裂和剥落(图7b和c)。然而,NiCoCrAlFeY高熵合金粘结层在1150℃下循环氧化200 h之后,氧化层厚度只有约4.9 μm,完全由Al2O3组成,并且氧化层与粘结层紧密结合,未出现任何形式的剥落(图7e和f)。由于NiCoCrAlY粘结层在1150℃下循环氧化200 h之后仍存在富Al的β相,因此氧化层顶部的有害尖晶石是在初期氧化过程中生成,并非由于长期氧化过程中Al供应不足(图7c)[20]。对于NiCoCrAlFeY高熵合金粘结层,氧化层中并未观测到尖晶石的生成,说明粘结层在氧化初期能够快速生成Al2O3,抑制尖晶石的生长,主要原因归结于NiCoCrAlFe高熵合金自生的纳米结构(图1[31])[60]。对于热障涂层系统,由于尖晶石生长速率快且脆性高,易形成界面裂纹,从而弱化界面结合,加速热障涂层失效[7,39]。相比于传统NiCoCrAlY粘结层,NiCoCrAlFeY高熵合金粘结层在1150℃下的氧化层厚度下降约25%,即氧化速率明显降低。因为尖晶石为初期氧化生成,所以氧化层长期氧化的生长速率由Al2O3生长控制。然而,关于NiCoCrAlFeY高熵合金粘结层Al2O3生长速率显著降低的根本原因还有待进一步研究。综上所述,本团队利用低成本的AC-HVAF技术制备出高质量的NiCoCrAlFeY高熵合金粘结层。AC-HVAF技术焰流速率快、焰流温度低,能够保证在不破坏合金结构的前提下,实现高致密度、低氧含量粘结层的制备[61~64]。研究结果也表明,NiCoCrAlFeY高熵合金粘结层的抗氧化性能远优于传统NiCoCrAlY粘结层,主要表现为氧化速率更低、界面结合性能更加优异,因此该高熵合金粘结层有望成为未来超高温热障涂层金属粘结层候选材料。
图7
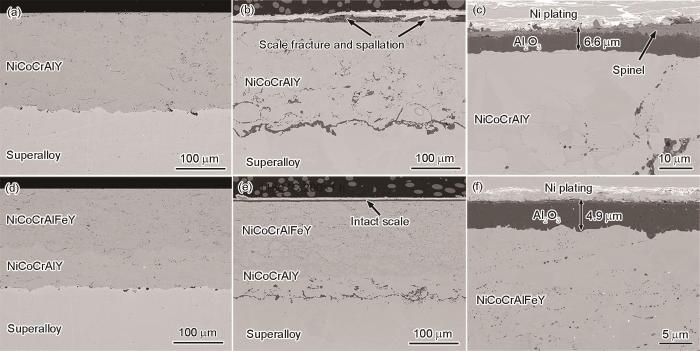
图7 传统NiCoCrAlY粘结层与NiCoCrAlFeY高熵合金粘结层在1150℃下循环氧化前后截面形貌
Fig.7 Cross-sectional morphologies of conventional NiCoCrAlY bond coat (a-c) and NiCoCrAlFeY HEA bond coat (d-f) before (a, d) and after (b, c, e, f) cyclic oxidation at 1150oC
6 总结与展望
本团队针对Y/Hf-NiCoCrAlFe高熵合金的抗氧化与抗热腐蚀性能进行了系统研究,研究结果表明,NiCoCrAlFe高熵合金的抗氧化与抗热腐蚀性能均显著优于传统NiCoCrAl合金。同时,利用真空气雾化成功制备出高球形度、低O含量的NiCoCrAlFe高熵合金粉体,并且此粉体也具有优异的抗氧化性能。最后,本团队利用AC-HVAF技术在高温合金表面成功制备高致密度且结构均匀的NiCoCrAlFeY高熵合金粘结层,热循环氧化测试结果表明,该粘结层的抗氧化性能远优于传统NiCoCrAlY粘结层。综合以上研究结果可知,NiCoCrAlFe高熵合金有望作为未来超高温热障涂层金属粘结层的候选材料,代替传统的MCrAlY粘结层。然而,研究过程中也发现了一些重要问题,后期需要深入研究:(1) 阐明增加Al含量降低NiCoCrAlFe高熵合金氧化速率的内在机制;(2) 揭示基于NiCoCrAlFe高熵合金独特成分与结构的活性元素微观作用机理,确定最优的活性元素种类与掺杂浓度;(3) 确定Fe元素之外的第五主元候选元素(比如Pt、Ta或Re等);(4) 建立模型预测高熵合金成分与结构之间的关联机制,从而更快筛选出抗氧化性能最优的高熵合金组分;(5) 基于高熵合金粘结层的热障涂层制备科学与失效机理研究。