分享:核级镍基合金焊接材料失塑裂纹研究现状
1.
2.
镍基合金及其焊接材料因具有优异的耐蚀性和高温力学性能,成为核电站关键设备中的关键材料,其焊接质量关系到核电站的安全运行。失塑裂纹(ductility-dip crack,DDC)是镍基合金中常见的一种微观缺陷,常常出现在多层多道焊中,因其尺寸小(长100 μm左右)、难检测,成为核电站运行安全的潜在威胁。本文简要地回顾了核级镍基合金及其焊接材料的发展历程,从镍基600系列合金发展到690系列合金,解决了焊接接头晶间腐蚀裂纹问题,但对之引起的焊接DDC问题,从成分设计角度,开发了以Inconel 52、Inconel 52M和Inconel 52MSS为代表的焊接材料,焊接接头的DDC敏感性逐步降低,但此问题至今并未完全解决。介绍了DDC的微观特征及其敏感性评价方法,总结了目前比较认可的DDC开裂机制,从成分和微观组织角度分析了其影响因素,最后进行了展望。
关键词:
核能是人类解决能源危机、实现可持续性发展的可行方案之一。截止2020年底,全球有21个国家的核电发电量占比超过10%,其中法国占比高达70%左右,而我国境内仅5%左右[1]。核能与其他能源方式的最大不同之处在于其安全性。特别是经历了2011年日本福岛核安全事故后,全世界对利用核能的态度更加审慎。能否攻克核能技术安全涉及的每一个难题,保证核电站整个运行周期内的高安全性,对于落实国家战略、缓解我国的能源危机具有重大意义。
焊接是核电站建造中必不可少的关键工序,也是影响核电装备制造质量的决定性因素。绝对高可靠、高安全、长寿命的核电服役要求,对关键装备的焊接制造质量提出了极高的要求。Ni-Cr-Fe系镍基合金具有优异的高温强度、耐腐蚀性能和热稳定性,满足核电站结构材料的需求,已广泛应用于核电站一回路、二回路关键设备及其零部件的制造,如压力容器管道及焊接接头、安全端异种金属接头等[2,3]。然而,近几十年的研究和工程应用经验表明,由于核电关键结构壁厚大、拘束度高,在表面堆焊和多层多道环缝对接过程中,镍基合金易出现失塑裂纹(ductility-dip crack,DDC)。该裂纹沿晶分布,尺寸小(长100 μm左右),难以采用常规无损方法检测,虽然短期对核电结构安全性无明显影响,但从核电站服役60年的长周期来看,DDC可能成为疲劳裂纹或应力腐蚀裂纹源,潜在安全隐患大[4]。因此,数十年来,国内外科研工作者围绕镍基合金DDC问题开展了大量的研究,本文对这些前期工作进行了简要的回顾。
1 核级焊接材料发展历程及问题
Inconel 600镍基合金及其焊接材料的应力腐蚀裂纹问题与晶界附近贫Cr导致的耐腐蚀性下降有关[14]。20世纪60年代末,为改善Inconel 600镍基合金的耐腐蚀性能,Cr含量提高到了30%左右(质量分数,下同),开发了Inconel 690镍基合金。研究[15~18]表明,在氧化性高温液体环境中,Inconel 690镍基合金表现出优异的耐应力腐蚀能力,应力腐蚀开裂风险大大降低。20世纪80年代末,Inconel 690镍基合金及其焊接材料,包括Inconel 52焊丝(ERNiCrFe-7)和Inconel 152焊条(ENiCrFe-7),逐步取代了Inconel 600系列镍基合金,成为第三代核电站的首选镍基材料,相继应用到核电设备制造中。
虽然Inconel 690镍基合金可以抵抗晶间腐蚀裂纹,但在其焊接过程中(如采用Inconel 52作为填充材料),容易产生DDC[19~27]。如图1[28]所示,奥氏体材料的高温塑性变化规律(图1[28]中虚线)与一般材料不同(图1[28]中实线),在(0.5~0.8)TS (TS为固相线温度)温度区间内会产生明显的塑性降低,因此,该温度区间被称为失塑温度区间(DTR),图中的BTR表示脆性温度区间。此时,当外应变高于临界应变时,产生晶界开裂,也就是DDC[29~34]。DDC尺寸非常小,为微米级,常出现在热影响区或多层多道焊的再热影响区,射线探伤等常规无损检测方法很难检测到该类型裂纹,且因其易成为晶间腐蚀裂纹或疲劳裂纹的裂纹源[4],是焊接接头可靠性的潜在威胁。为解决Inconel 52易产生DDC的问题,研究者在其成分中添加了0.84%Nb,开发了Inconel 52M (ERNiCrFe-7A),相比于Inconel 52,DDC敏感性降低,但并未彻底解决DDC问题[35~37]。2000年以后,美国特种材料公司在Inconel 52的基础上增加2.48%Nb和4.0%Mo,开发了Inconel 52MSS焊丝(ERNiCrFe-13),DDC敏感性显著降低。但是,随着Nb和Mo元素含量的增加,焊缝金属凝固过程中成分偏析加剧,容易在枝晶间形成低熔点共晶相,从而引起偏析裂纹,如凝固裂纹和液化裂纹[35,38~41]。目前,国内使用的核级镍基焊材主要是Inconel 52和Inconel 52M,而Inconel 52MSS并未得到应用。
图1
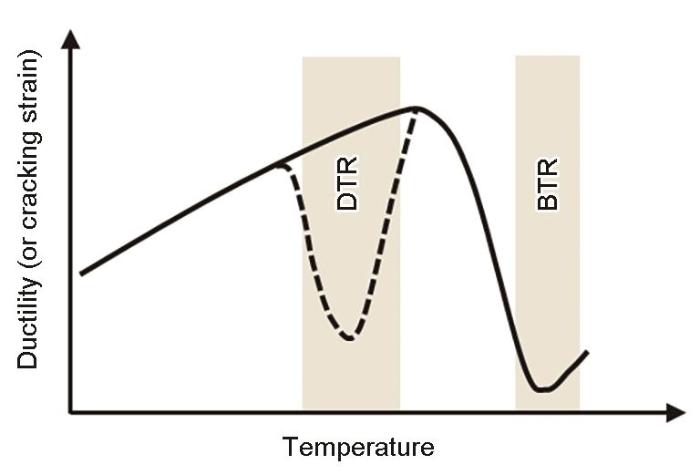
2 DDC的特征
图2

凝固组织中的晶界类型如图3a[45]所示。其中,凝固晶界(solidification grain boundary)和迁移晶界(migrated grain boundary)均为大角度晶界,由不同生长方向的枝晶簇形成。凝固晶界因曲折度高,在冷却过程中,为降低晶界能而平直化,从而发生晶界迁移,形成迁移晶界。因迁移晶界具有平直的特征,有利于裂纹的萌生和扩展,DDC倾向于出现在迁移晶界上。凝固亚晶界(solidification subgrain boundary)则是相邻单个枝晶的界面,是小角度晶界。区别于焊接过程中因液相薄膜撕裂产生的凝固裂纹和液化裂纹,DDC产生在热影响区或再热焊缝区,是一种高温固相开裂的行为。图3b[28]示意了DDC出现的位置,图中,TL表示液相线温度,TR表示再结晶温度,TX表示其他某一温度。
图3

图3 镍基合金焊接凝固组织晶界类型示意图[45]及失塑裂纹(DDC)敏感区域[28]
Fig.3 Schematic illustration of grain boundaries in nickel-based weld metals (a)[45] and susceptible region of ductility-dip crack (DDC) (TL is liquid temperature, TS is solid temperature, TR is recrystallization temperature, and TX represents a certain temperature) (b)[28]
图4
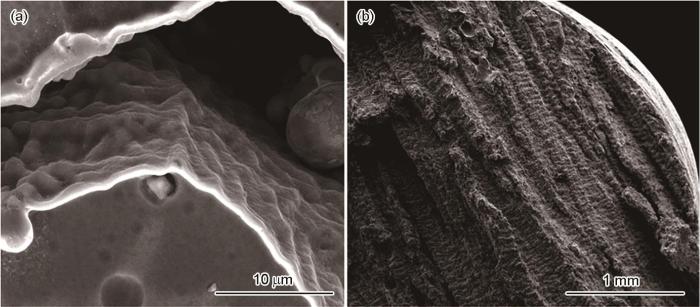
3 DDC的评价
目前对失塑裂纹敏感性的评价主要是基于力学性能测试结果中的应力和应变指标,这些方法包括应变致裂(strain-to-fracture,STF)实验、可调拘束实验、高温拉伸实验、原位高温拉伸实验等。
3.1 STF实验
STF实验的优点在于,能够精确控制热循环的峰值温度,确保实验过程处于固态阶段,避免了凝固裂纹和液化裂纹对DDC辨别的影响,可以比较准确地获得材料的失塑温度区间和DDC的临界应变。因操作方法简单,STF实验成为目前应用最广的一种DDC敏感性评定方法。但STF实验也存在诸多不足,由于测试样品进行了点焊重熔,导致焊接残余应变以及组织特征变化对DDC产生影响;其次,应变测量标距远大于DDC的长度,造成平均应变与DDC区域的应变集中差别较大,从而临界应变的准确性不足。
图5
3.2 可调拘束实验
可调拘束实验的优点在于模拟了真实的焊接热循环,但缺点是会同时产生凝固裂纹、液化裂纹和DDC。特别地,液化裂纹和DDC很难区分。同时,该实验方法获得的是整个试样的弯曲应变,无法准确得到DDC发生位置的局部应变。因此,可调拘束实验只能间接地比较不同材料的DDC敏感性,但由于能够评价不同类型的热裂纹敏感性,成为了一种综合的热裂纹敏感性评价方法,
3.3 高温拉伸实验
高温拉伸实验是对焊缝进行综合力学评估的一种最常用的实验方法。采用该实验方法,通过分析不同温度拉断试样的延伸率或断面收缩率,判定高温失塑区间的大小,可间接地比较不同材料的DDC敏感性[51]。高温拉伸实验的优点在于其操作简单,能够快速获得材料的综合力学性能数据及其变化规律,但缺点是无法准确量化DDC的临界应变。
3.4 原位高温拉伸实验
图6
4 DDC形成机制
4.1 类蠕变的晶界滑移诱发开裂机制
Rhines和Wray[59]最早报道了镍基合金的中温脆化现象,认为与其低塑性温度区间内的低应变速率引起的扩散蠕变有关。在应力作用下,空洞出现于大角度晶界;随着应力的增加,大角度晶界滑移,引起剪切作用,造成孔洞合并产生微裂纹,从而塑性下降。研究者[23,28~30,46,51]利用STF实验获得了DDC的敏感温度和最小临界应变,发现Inconel 690焊缝金属的DDC敏感温度比其他镍基合金的中温开裂温度更高,进而发展了晶界滑移诱发DDC的机制,包括3种情况,如图7[23]所示:(1) 对于平直晶界,其三叉晶界位置因晶界滑移而产生应变集中,导致开裂;(2) 当平直晶界存在析出相时,析出相会抑制晶界滑移,同时在析出相附近产生应变集中,当应变集中到一定程度时,析出相附近形成空洞;(3) 当曲折的晶界上存在析出相时,曲折晶界和晶界析出相均能分担应变,应变集中程度得到缓解,从而提高了DDC临界应变。
图7
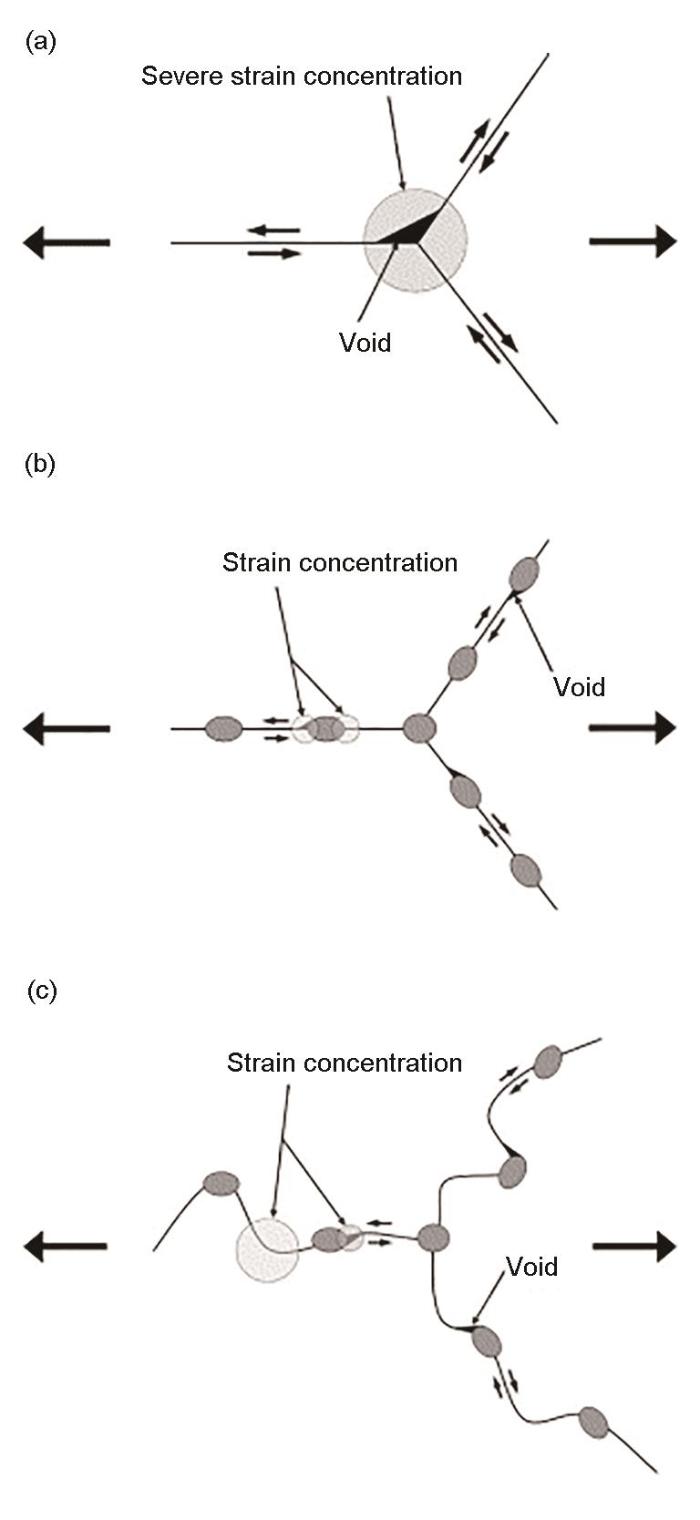
4.2 杂质元素偏析引发的晶界脆化机制
研究[27,60~64]认为,Inconel 690焊缝金属中,杂质元素S和P等在中、大角度晶界处的偏析是DDC产生的主要原因。因为S和P倾向于向晶界扩散,减弱晶界结合力,增加晶界脆性。Yamaguchi等[65]通过可调拘束实验发现,随着合金中S和P含量的增加,Inconel 690焊缝金属的失塑温度区间随之线性扩大。通过对Ni-S二元体系的研究,发现S元素减弱了大角度晶界的结合力,从而造成脆性断裂。当S和P的含量控制在30 × 10-6以下,可避免产生DDC。然而,Li等[4]在DDC处采用聚焦离子束制备样品,并通过透射电镜(TEM)和三维原子探针层析方法表征了DDC附近的元素分布,并未发现S和P元素的偏析。因此,杂质元素偏析引发的晶界脆化机制也不能完全揭示DDC产生机理,需进一步深入研究。
4.3 晶界析出相诱发开裂机制
5 DDC影响因素及调控方法
根据DDC的开裂机制,对其敏感性影响因素和调控方法的研究主要集中在合金元素、晶界碳化物和晶界特征等方面。
5.1 合金元素的影响
镍基合金中存在很多元素,有些能够抑制DDC,而有些会增加DDC敏感性。
Nb元素:Nb元素在镍基合金基体中有一定的固溶度,可起到固溶强化的作用,从而提高力学强度。Inconel 690焊缝金属在凝固过程中,当Nb含量超过0.55%时,会偏聚于枝晶间。由于Nb和C有很强的亲和力,能形成NbC相,具有很高的热稳定性[55]。同时,随着Nb含量的增加,焊缝组织中的一次枝晶变短,枝晶间析出物由Ti(C, N)和Ti-Al-O的化合物向NbC转变[66,67];当枝晶间Nb含量很高时,形成低熔点Laves相(Ni2Nb)[26,57]。Nb 降低了M23C6的初始析出温度, 减缓了M23C6的析出, 并且NbC的形成消耗了大量C原子,从而减少晶界处M23C6析出相。另一方面,随Nb含量增加,M23C6由多列连续分布转变为单列离散分布[64,68]。Nb含量高于2.45%时,可有效降低焊缝金属的DDC敏感性[69]。并且,Nb含量的增加扩大了固液区间温度范围,确保焊缝中的氧化物和夹渣浮出[24]。但当Nb的含量超过3.35%后,引起Laves相的大量析出,增加了材料的液化裂纹倾向,会导致塑性下降[37,38,67,70,71]。
B元素:B元素在焊接过程中倾向于偏析到晶界,形成M2B,降低凝固温度,促进M23C6在晶界处的偏析。因此,B会增加液化裂纹和DDC敏感性[78]。
Si元素:Si元素会促进低熔点共晶化合物的形成,降低凝固温度,增大脆性温度范围,影响晶界的结合强度,从而增加DDC敏感性[84]。
Bi元素:Chellali等[85]对比研究了纯Ni和Ni-Bi二元合金发现,随着温度的升高,纯Ni在高温变形过程中不会出现脆性断裂,而Ni-Bi会出现低塑性区间。其原因为,Bi元素扩散到晶界,引起晶界脆性增加。
S元素:如4.2节所述,S元素为杂质元素,扩散到晶界后,减弱晶界结合力,增加脆性,从而增加DDC敏感性。Rapetti等[86]发现S含量越高的镍基合金,DDC敏感性越高,尽管在晶界上没有表征到S,但在断口表面发现了S。他们认为,塑形变形加速了S向裂纹尖端的扩散,形成了一个动态晶界脆化现象,从而裂纹持续快速扩展。
C元素:C元素是碳化物形成的主要元素,其对DDC的影响主要反映在碳化物对DDC的影响上,具体见5.2节。
5.2 晶界 M23C6 碳化物的影响
镍基合金基体中的C元素很容易扩散到晶界,与晶界附近的Cr原子形成M23C6,在晶界上析出。M23C6的析出造成了晶界局部贫Cr [11]。根据Cr的扩散方程可以预测晶界M23C6的析出数量与晶界附近Cr浓度的变化规律[88]。Jiao等[89]对Inconel 690合金进行了650、715和800℃下不同时间的热处理,研究晶界附近的碳化物平均尺寸和数量的变化规律,如图8[89]所示。可见,在650℃下,随着时间的延长,碳化物数量略有增加并倾向于紧密分布;在715℃下,随着时间的延长,碳化物的数量变多,并且尺寸增大;而在800℃下,经过5和10 h时效,碳化物逐渐粗化。基于实验结果,在经典形核理论、Kolmogorov-Johnson-Mehl-Avrami定律和扩散理论的基础上,构建了碳化物析出与Cr原子扩散之间的动力学模型,Cr原子浓度的实测结果证实了该模型的有效性。进一步,基于碳化物间距与平均尺寸的关系,引入了不连续因子,研究了热处理过程中碳化物形貌和Cr浓度变化规律。
图8
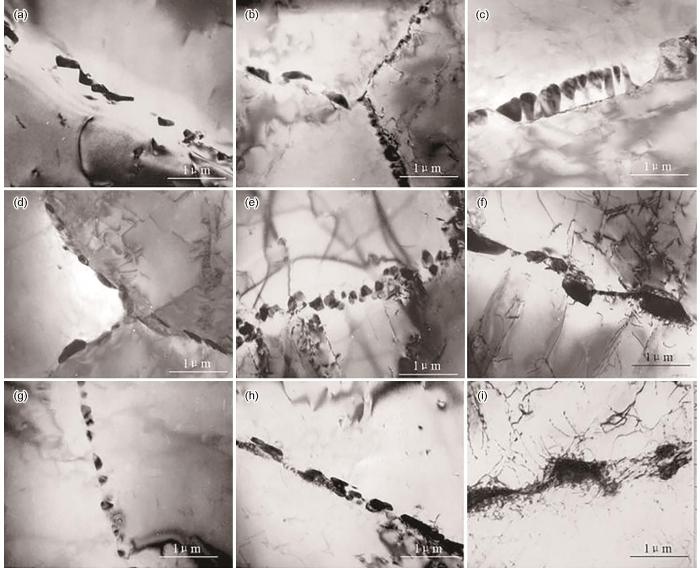
M23C6的析出与晶界特征和晶界能相关。Lim 等[90]对Inconel 690合金在720℃下进行了10 h的热处理,采用TEM研究了不同类型晶界上的M23C6析出特征,发现富Cr的M23C6相在较高晶界能的大角度晶界上表现出粗大和离散的分布特征,在小角度晶界上则为细小颗粒,在能量较低的非共格孪晶界上以针状析出,而在共格孪晶界上没有析出,如图9[90]所示。Sennour等[91]通过TEM和电子背散射衍射(EBSD)观察到M23C6出现在大于15°的晶界上。Li等[92~94]应用三维原子探针层析、高分辨TEM、SEM和EBSD等研究了碳化物在晶界析出时与基体的取向关系,发现Cr23C6形核前,C原子与Cr原子在690合金晶界的一侧形成共偏聚区。随后,Cr23C6在晶界处于高指数晶面的一侧形核,且与其形成共格关系。
图9
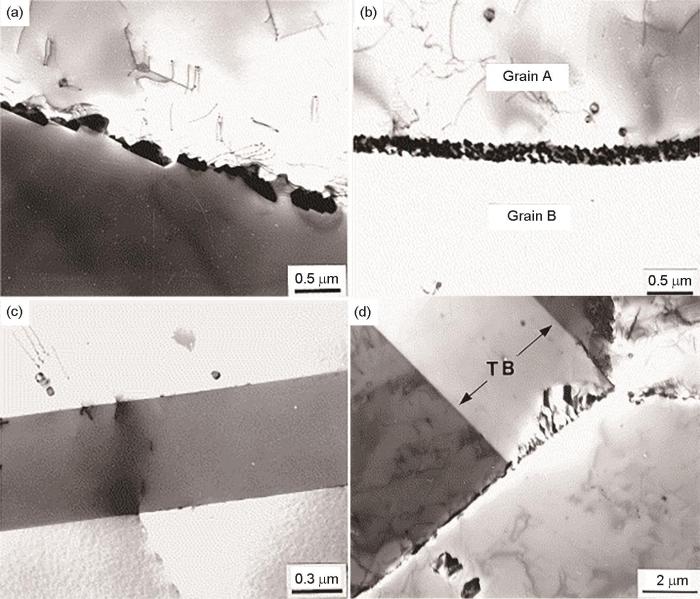
M23C6的析出引起了镍基合金晶界处的元素组分和局部性能的改变,进而影响材料的力学性能和开裂行为。Ramirez等[23]和Nissley等[75]在研究Inconel 690焊缝金属的DDC敏感性时发现,当晶界上M23C6数量较多时,会阻碍晶界的滑移,并在其附近引起应力集中,诱发DDC。Mo等[95]分析NiCrFe-7焊缝金属在600~930℃的高温性能时发现,在810~870℃范围内,随着M23C6的析出数量增加,晶界强度低于晶内强度,发生了沿晶开裂;而在810℃以下或者870℃以上时,由于M23C6的析出数量减少,晶界强度高于晶内强度,从而发生了韧性断裂。同时,DDC容易在M23C6与基体的结合处产生。Qin等[48,96]通过STF实验研究NiCrFe-7熔敷金属性能时发现,晶界上的M23C6在700~950℃会明显粗化,而当温度高于1000℃后发生溶解,认为这种演化行为是引起DDC裂纹的主要原因。Lee等[97]对Inconel 690合金管开展了700℃不同时效热处理,在时效16 h以内,随着M23C6的析出,材料的强度增加;而当超过16 h后,由于M23C6的粗化导致与基体的结合强度降低,引起沿晶开裂,导致强度和塑性下降。Li等[4]对Inconel 690焊缝金属DDC区域原位聚焦离子束制备样品,通过SEM观察,发现裂纹尖端边缘存在M23C6析出相。
5.3 晶界特征
当镍基合金的大角度晶界曲折度较高时,可以阻碍晶界的滑移行为,同时分散晶界滑移时引起的应力集中程度,使材料的高温塑性得到改善[23,27,35,98]。Jeng等[70,73]和莫文林等[69]均发现,随着Inconel 690焊缝金属中Mn、Nb和Mo等元素含量的增加,凝固过程中析出MC/MN的体积分数增加,提高了大角度晶界曲折度,增强了晶界的“咬合力”。同时,分散了晶界处的应力集中,降低了DDC倾向。Chen等[99]研究发现,DDC更倾向于出现在取向差角为45°左右的大角度晶界上。其原因为,大角度晶界的晶界能在取向差角为45°时达到最大,从而使结合能降低,造成延性下降,导致开裂。魏啸[45]通过STF实验也发现,组织中大于30°的晶界比例越高,对应DDC裂纹敏感性也越高。Wu等[100]发现,镍基合金焊缝的中高温脆性与晶界滑移有关,通过加入合金元素增加晶界曲折度后,可一定程度上恢复塑性。Wei等[101]采用分形维度法半定量地分析了晶界曲折度,进一步证实了晶界曲折度越高,越容易抑制DDC。
5.4 晶粒尺寸
5.5 动态再结晶
6 结论与展望
镍基合金失塑裂纹是一种沿晶固相裂纹,尺寸小(100 μm左右),难以采用常规无损方法检测,是核电关键设备长期安全服役的潜在隐患。以往通过材料成分的设计一定程度上改善了DDC敏感性,但焊接DDC问题并未完全解决。由于微裂纹形成于晶界,并沿晶界长大和扩展,因此晶界形貌和晶界脆性的改善是解决裂纹的关键。另一方面,核电关键设备的焊接以多层多道焊接为主,焊缝及热影响区的残余应变持续累积,再加上析出物和基体之间的晶格错配造成的畸变应力,导致多晶变形时局部区域应变集中,特别是在DDC敏感温度区间内,累积应变一旦突破了临界应变,就会导致形成DDC。根据镍基合金电弧激励超声钨极氩弧焊的前期研究发现,通过外场超声对焊接熔池的作用,促进了原子扩散,使元素分布更加均匀,减少并弥散了晶界偏析,改善镍基合金晶界高温脆性,从而降低了DDC敏感性。因此,镍基合金焊接DDC问题的解决,需要通过材料和工艺的持续改进和优化,以下几个关键问题还需进一步探讨:(1) 焊接DDC的萌生、生长和扩展全过程的观察和理论分析,对于更深入地揭示DDC机理非常关键;(2) 镍基合金晶界的中、高温(700~1200℃)脆化原因和机制需要进一步厘清,有利于更有效地提出焊接DDC问题的解决方案;(3) 深入揭示焊接外场作用对于改善晶界脆性、降低DDC敏感性的机理,是改进和发展核级镍基焊接工艺的基础。