分享:新型Ni-Co基高温合金塑性变形连接中界面组织演化及愈合机制
任少飞1,2, 张健杨2, 张新房,1, 孙明月
,2,3, 徐斌2,3, 崔传勇4
1.
2.
3.
4.
为解决镍基高温合金的焊接难题,以新型Ni-Co基高温合金为实验材料,采用塑性变形连接的新方法,实现了新型Ni-Co基高温合金的连接。通过OM、EBSD、TEM等分析手段探究了界面的再结晶行为及界面的愈合机制。结果表明,1150℃进行塑性变形连接时,合金的变形抗力小,不易开裂。不同变形量的连接实验表明,在40%的变形量下,合金可以实现界面的完全愈合,其力学性能达到基体同等水平。在塑性变形过程中,界面附近的粗大晶粒首先发生细化,随着变形量的增加,细化的晶粒在连续动态再结晶的辅助作用下,通过界面晶界的迁移消除了原始连接界面,实现界面的愈合。
关键词:
新型Ni-Co基高温合金作为一种Al + Ti含量高达7.5%以上的难变形沉淀硬化型合金,传统的钨极氩弧焊(TIG)和惰性气体保护焊(MIG)由于焊接接头存在较大的裂纹敏感性并不适用于新型合金的焊接[13]。随着航空发动机热端关键部件结构越来越复杂,尺寸越来越大,电子束焊、摩擦焊、扩散焊等焊接技术在实际应用过程中也存在一定的局限性,已不能满足高温合金部件的制备需求。Han等[14]和Osoba等[15]分别研究了K465和Haynes282镍基高温合金的电子束焊接接头组织,发现接头焊缝中均存在Ti和Al元素的偏析,被认为是K465接头产生裂纹的主要原因,严重影响了合金的力学性能。Ravisankar等[16]研究了SU263镍基高温合金固态扩散焊的接头组织,表明界面孔洞和第二相的存在抑制了合金界面的愈合,接头的机械性能远低于母材。Sah等[17]和Zhang等[18]的研究也发现了相同的现象。Xiong等[19]对GH4099扩散焊接头连接行为的研究表明,焊接界面析出的碳化物阻碍了界面的愈合,导致界面存在大量孔洞。此外,固态扩散焊需要进行长时间的保温以保证焊接质量。旋转摩擦焊只适用于形状规则合金的焊接,对于异形构件的焊接存在一定的困难,同时旋转摩擦焊在焊接过程中存在界面受热不均匀现象,不适合大体积合金的焊接[20]。因此需要探索一种新的焊接方法解决镍基高温合金在焊接领域存在的问题。
塑性变形连接作为一种新型的焊接方法,主要应用于不锈钢、铝合金的焊接,并取得了良好的连接效果[21,22]。塑性变形连接是在固态扩散焊的基础上对合金施加大变形,在热力耦合的作用下,通过界面原子的互扩散实现合金的连接[23,24]。Zhou等[25]研究了14YWT合金的塑性变形连接,表明提高温度和增加变形量有利于合金界面的愈合。Zhang等[26]研究了Cu的塑性变形连接过程,结果表明界面晶界的迁移有利于消除连接界面,实现Cu的连接,且界面不存在有害相。Xie等[27]研究了316LN不锈钢在塑性变形连接过程中界面氧化物对不锈钢连接质量的影响,表明界面形成的氧化膜在后续保温过程中发生分解,界面的氧最终以纳米级的Al2O3氧化物颗粒形式弥散分布于界面附近,对界面的愈合没有明显的影响。上述结果表明塑性变形连接作为一种新型焊接方法可用于Ni-Co基高温合金的焊接。
镍基高温合金作为一种低层错能材料,在塑性变形过程中,合金中以位错形式存储的应变储能会以动态再结晶形式消除。而由于塑性变形的引入,推测在合金的塑性变形连接过程中也存在动态再结晶现象。然而,由于塑性变形连接过程中连接界面的存在,可能会使合金的再结晶行为变得复杂。因此有必要对塑性变形连接过程界面组织的演化行为进行研究,探究新型Ni-Co基高温合金在塑性变形连接过程中界面的再结晶行为,并阐述界面愈合机制。
本工作以新型Ni-Co基高温合金为研究对象,采用光学显微镜(OM)、电子背散射衍射(EBSD)、透射电子显微镜(TEM)等手段研究了不同变形参数下界面的再结晶行为,对塑性变形过程中的再结晶机制进行了探究,同时采用室温拉伸实验评估了界面的结合强度,并对界面的愈合机制进行探讨,为后续的工程化应用奠定基础。
1 实验方法
1.1 实验材料
实验材料为经真空感应熔炼+电渣重熔熔炼+真空自耗熔炼制备的新型Ni-Co基高温合金铸锭,化学成分(质量分数,%)为:Co 25.3,Cr 13.93,Al + Ti 7.7,Mo + W 3.8,C + B + Zr 0.04~0.11,Ni余量。为改善合金的变形能力,对合金铸锭进行高温均匀化处理(1160℃、3 h + 1200℃、1.5 h)。
1.2 塑性变形连接实验
首先采用电火花线切割从均匀化态的合金上切取8 mm × 8 mm × 6 mm的方形试样,然后将2个待连接试样的表面进行机械磨抛和超声清洗处理,以消除表面的氧化膜和污染物。随后将2个试样采用铜胶带固定并放置于Gleeble 3500热模拟机中,将K型热电偶焊在试样界面的中心部位,如图1a所示。塑性变形连接的应变速率为0.001 s-1,变形温度为1000~1200℃,变形量为5%~40%,真空度为0.133 Pa。试样以5℃/s的加热速率升温至目标温度后保温5 min,以使试样受热均匀,随后进行塑性变形连接。为减少试样与机器接触面的摩擦力,在试样两端分别放置了钽片、高温润滑脂和石墨片。
图1
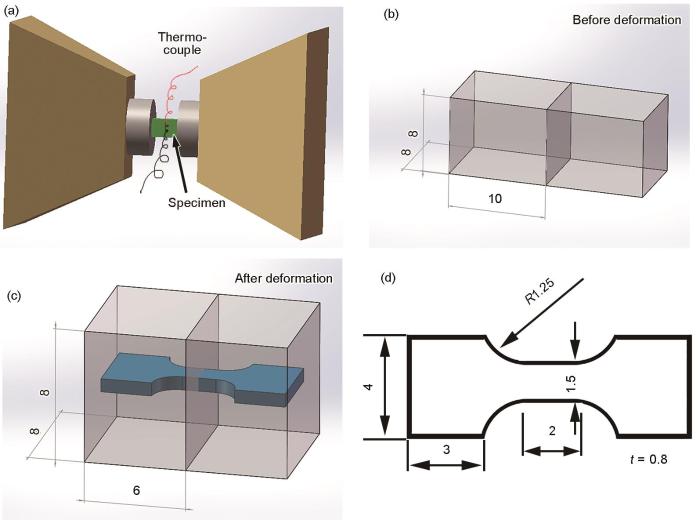
图1 实验原理示意图
(a) schematic of plastic deformation bonding (b, c) schematics and location of tensile specimen processing (unit: mm) (d) dimensions of the tensile test specimen (t—thickness) (unit: mm)
Fig.1 Schematic representation of the experiment
1.3 组织及性能表征
采用电火花线切割沿平行于压缩方向从试样中心剖开,试样经过机械磨、抛处理后,采用Lab. A1 OM进行组织观察,金相组织的腐蚀剂为CuSO4 (4 g) + HCl (20 mL) + CH3CH2OH (100 mL)。枝晶组织采用电解腐蚀,腐蚀液为CrO3 (15 g) + H3PO4 (150 mL) + H2SO4 (10 mL),腐蚀电压为5 V,腐蚀时间为15 s。采用MIRA3型SEM及其附带的EBSD探头对试样界面组织进行表征,EBSD试样采用电解抛光,电解抛光液为CH3OH (80 mL) + H2SO4 (20 mL),电解电压为25 V,抛光时间为25 s。EBSD扫描步长视晶粒尺寸采用1.5~2.5 μm,后续数据处理均采用Channel 5软件。采用Tecnai G2 20 TEM对塑性变形连接后的试样界面进行观察,TEM试样采用离子减薄制备,首先采用5 keV、8°参数减薄2 h,随后采用3 keV、4°参数减薄4 h,以保证在连接界面处存在可供观察的薄区。
为评估塑性变形连接试样的界面结合强度,采用Z2.5 TH型带有激光引伸计的小尺寸拉伸试验机对试样进行力学性能检测。值得注意的是,拉伸试样为8 mm × 8 mm × 10 mm的方形试样,同时为比较不同变形量下接头的力学性能,制备了8 mm × 8 mm × 20 mm的对照组,2类试样的变形量分别为20%和40%。变形后的接头经过固溶和时效处理后(1100℃、1 h + 760℃、4 h)采用电火花线切割进行拉伸试样的制备,取样位置及拉伸试样尺寸如图1b~d所示,拉伸试样取样位置为连接试样的中心部位,即大变形区域。
2 实验结果及分析
图2
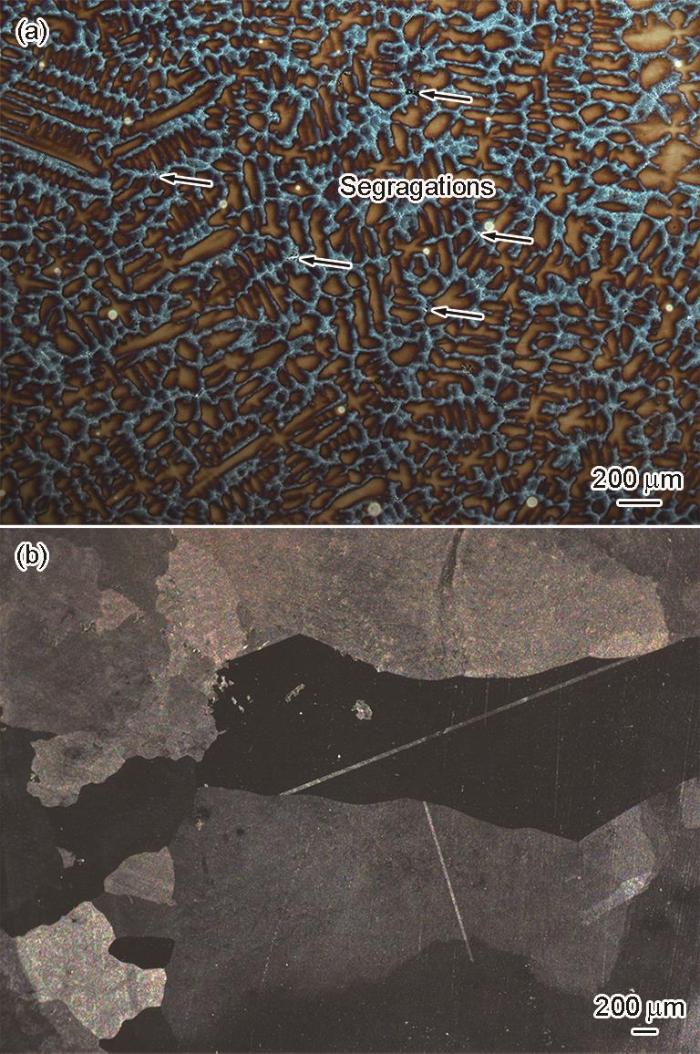
图2 Ni-Co基高温合金铸态组织及均匀化态显微组织的OM像
Fig.2 OM images of microstructures of as-cast (a) and homogenized (b) Ni-Co base superalloy
2.1 塑性变形连接工艺对界面组织的影响
2.1.1 不同变形温度下界面的演变
图3为Ni-Co基合金在应变速率为0.001 s-1时不同变形温度下显微组织的OM像及其流变应力曲线。当变形温度较低时,合金中的原始晶粒被拉长,合金的原始连接界面清晰可见,趋于平直,如图3a和b所示。随着温度升至1100℃时,在连接界面附近沿原始晶界出现了部分动态再结晶晶粒,但连接界面没有明显的变化,如图3c所示。然而当变形温度提高到1150℃,原本平直的界面发生弯曲,且在合金的连接界面附近发生了晶界迁移,部分界面被再结晶晶粒取代,如图3d所示。值得注意的是,当变形温度较低时,在变形合金中可以观察到部分沿晶界开裂的现象。这可能是因为合金初始晶粒尺寸比较大(图2b所示),粗大的晶粒导致合金各部分受力不均匀,从而导致合金的变形能力较差,容易发生开裂现象[28~31]。当变形温度达到1200℃时,合金发生了严重的沿晶界开裂现象(图3e),这是因为变形温度过高,强化相溶解,原本粗大的晶粒进一步长大,晶粒变形协调能力变差,导致变形过程沿晶界开裂,Liu等[29]在研究新型Ni-Co基高温合金的热变形行为时也发现了合金沿晶界开裂现象。图3f为不同温度下的流变应力-应变曲线,随着温度逐渐升高,流变应力不断减小,且峰值应力对应的峰值应变也逐渐降低,这表明温度升高有利于促进合金中原子的热激活运动,提高晶界的迁移速率,从而促进合金的动态软化,并将再结晶过程提前。同时,可以注意到当变形温度超过1150℃时,合金变形抗力明显减少,这是因为合金中γ'强化相发生溶解(γ'的初溶温度为1141℃)[29],位错运动的阻力降低。上述结果表明,当塑性变形连接温度为1150℃时,连接界面处晶界易发生弓弯现象,原始连接界面被再结晶晶粒取代,有利于界面的愈合。
图3

图3 应变速率为0.001 s-1,不同变形温度下Ni-Co基高温合金显微组织的OM像及其流变应力-应变曲线
Fig.3 OM images of microstructures at deformation temperatures of 1000oC (a), 1050oC (b), 1100oC (c), 1150oC (d), and 1200oC (e), and the true stress-strain curves (f) of the Ni-Co base superalloy at the strain rate of 0.001 s-1
2.1.2 不同变形量下界面的演变
图4a~e所示为塑性变形温度为1150℃时不同变形量下Ni-Co基合金显微组织的OM像。可以看出,随着变形量的增加,原始粗大的合金晶粒得到细化,这表明在塑性变形过程中合金组织发生了动态再结晶。如图4a和b所示,变形量较小时,原始连接界面保持平直,界面清晰可见。随着变形量增加,连接界面的部分晶界开始变得弯曲,原始连接界面逐渐模糊,如图4c所示,这通常被认为是应变诱导晶界迁移[32]。当变形量增加到30%,原始连接界面的晶界弯曲现象更加明显,原始连接界面难以辨认,如图4d所示。随着变形量继续增加,原始连接界面被再结晶晶粒取代,界面实现愈合,如图4e所示。图4f为采用截线法统计的Ni-Co基合金平均晶粒尺寸。可以看出,随着变形量不断增加,平均晶粒尺寸逐渐减小。合金原始粗大的晶粒在10%的变形量下快速细化,但此时的晶粒尺寸不均匀。随着变形的不断进行,合金晶粒尺寸没有明显变化,但晶粒分布趋于均匀。合金平均晶粒尺寸的减小是塑性变形过程中动态再结晶细化晶粒的缘故[33]。
图4

图4 塑性变形温度为1150℃,不同变形量下Ni-Co基高温合金显微组织的OM像以及平均晶粒尺寸统计
Fig.4 OM images of microstructures at true strains of 5% (a), 10% (b), 20% (c), 30% (d), and 40% (e), and statistics of mean grain size (f) of the Ni-Co base superalloy at the deformation temperature of 1150℃
2.2 界面性能
2.2.1 界面结合强度
上述结果表明,当变形温度为1150℃、变形量达到40%时,Ni-Co基高温合金塑性变形连接可取得良好的连接效果。为进一步评估接头的结合强度,对不同变形量下接头的室温拉伸强度进行测试,结果如图5所示。为了便于比较不同变形量下接头的结合强度,采用了相同变形量的母材作为对照。变形量为20%的接头的屈服强度仅有614 MPa,延伸率只有0.7%,力学性能远不及变形量为20%的母材。这表明即使界面已发生部分连接,但由于界面依然存在未愈合的部分,从而导致界面强度不能达到母材水平。而对于变形量为40%的接头,其屈服强度和抗拉强度可以达到同等变形条件下的母材水平,延伸率略低于母材。这表明随变形量的增加,合金的结合强度显著提高。一方面,变形量较低时,变形初期形成的氧化膜阻碍界面的接触,导致界面的结合强度和延伸率不理想;随着变形量的不断增加,界面氧化膜在应力的作用下发生破碎,且由于局部氧分压的降低,破碎的氧化物部分发生分解[27],促进了界面的相互接触,有利于界面的愈合。另一方面,由于应力的持续作用,界面处发生应变诱导晶界迁移[34],促进了界面晶界的弓弯和迁移,提高了界面的结合强度。
图5
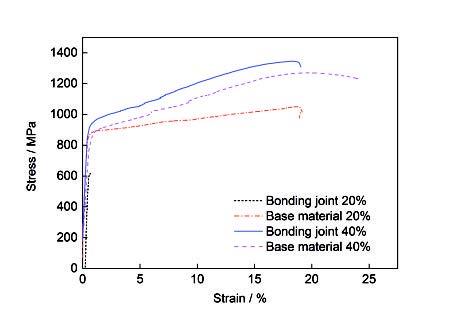
图5 不同变形量下接头的室温拉伸曲线
Fig.5 Tensile curves of the joints at room temperature under different deformations
2.2.2 接头拉伸断口形貌
图6所示为不同变形量下接头和母材的拉伸断口形貌。图6a和c分别为变形量20%和40%的母材断口形貌,可见在断面上存在大量小而浅的韧窝(图6a和c中的红色箭头),且在部分韧窝中存在γ'相(图中黑色箭头所示),可以判断这2种不同变形量的母材断裂方式均为韧性断裂。对于变形量为20%的接头,其断裂位置在界面连接处。如图6b中的矩形框所示,在断面上存在大量未连接的区域。而部分连接区域由于已经发生晶界迁移(图4c),从而在断口上呈现出弯曲、短小的撕裂棱,如图6b中的黑色箭头所示。这些表明该条件下接头的断裂模式为韧性断裂和脆性断裂的混合。Zhou等[25]的研究表明,塑性变形连接过程中弯曲的晶界可以部分阻碍裂纹的扩展,改善合金的结合强度。但由于20%变形量下,界面依然存在未愈合的区域,这意味着裂纹容易沿着未连接区域扩展,从而导致合金的结合强度明显降低。图6d为变形量40%的接头断口形貌,在断面上也存在与图6c相似的浅而小的韧窝,呈现韧性断裂的特征。这表明界面连接区域面积增加,显著提高了合金的阻碍裂纹扩展的能力,从而使接头强度达到了母材水平。
图6
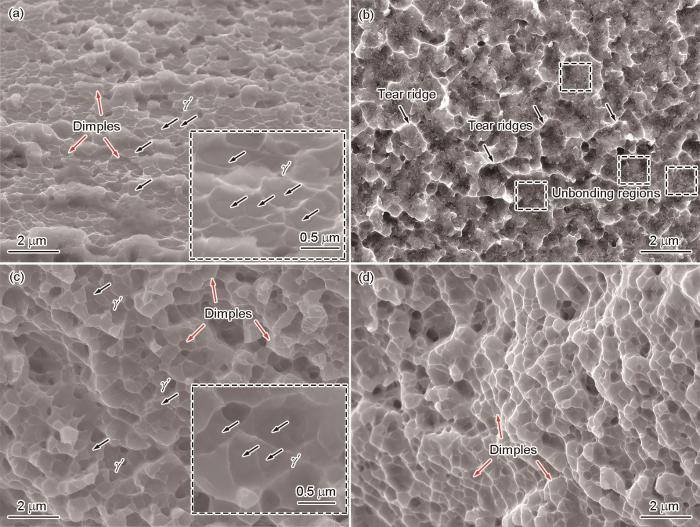
图6 不同变形量下接头和母材的拉伸断口形貌
Fig.6 Tensile fracture morphologies of base material (a, c) and joints (b, d) at different deformations of 20% (a, b) and 40% (c, d)
2.3 塑性变形过程合金的再结晶行为
2.3.1 不连续动态再结晶行为
Ni-Co基高温合金作为一种低层错能的合金,由于其扩展位错宽度很宽,难以通过交滑移和刃型位错的攀移进行动态回复[35],因此在合金塑性变形过程中动态再结晶是主要的软化机制。图7a和c显示了变形量分别为5%和10%的连接界面的反极图(IPF)。可以看出,初始晶体学取向随机分布的2个界面在小变形量的条件下,由于界面的局部接触形成结合界面,这种结合界面可以被认为是一种由复杂位错堆积形成的非稳定的大角度晶界,此时的连接界面由于未发生明显的塑性变形而保持平直。反观非连接界面区域的晶界则存在褶皱、弯曲的现象,有的晶界甚至嵌入了其相邻的晶粒,这通常被认为是应力诱导晶界迁移[32],即在变形初始,由于晶粒间变形的不协调性,以位错形式存储于变形合金内部的形变储能,会在晶界两侧产生位错密度梯度,如图7b和d所示,这种应变梯度会驱动晶界向位错密度较高的一侧移动,在宏观上表现为晶界的弓弯,而这些弓弯区域则为合金的再结晶提供形核质点,这是典型的不连续动态再结晶[36]。随着变形量增加到20%,原本平直的连接界面开始变得弯曲,界面处的晶界开始向对侧的晶粒弓出,如图7e所示。从图7f可知,连接界面两侧存在的应变梯度是界面晶界迁移的驱动力。同时也注意到,连接界面晶界的弓弯行为与非界面处的晶界迁移行为相比,存在一定的滞后性,这可能是因为平直晶界的迁移需要更高的能量,即需要较大的变形量为其提供驱动力。随着变形量增加到30% (图7g),原始的连接界面几乎已经消失,取而代之的则是通过不连续动态再结晶形核、长大的晶粒。结合图7h可知,连接界面处的晶粒仅存在少量的应变梯度,可认为在30%的变形量下,界面处发生了完全再结晶。当变形量增加到40%时,原始界面已完全消失,如图7i所示。结合图7h可以发现,在已发生再结晶晶粒的内部依然存在较高的应变梯度,这可能是因为由于应力的持续作用,在再结晶晶粒内部发生了二次应变集中现象,Xie等[36]在研究铸造镍基高温合金的再结晶行为过程中也发现了类似的现象。
图7
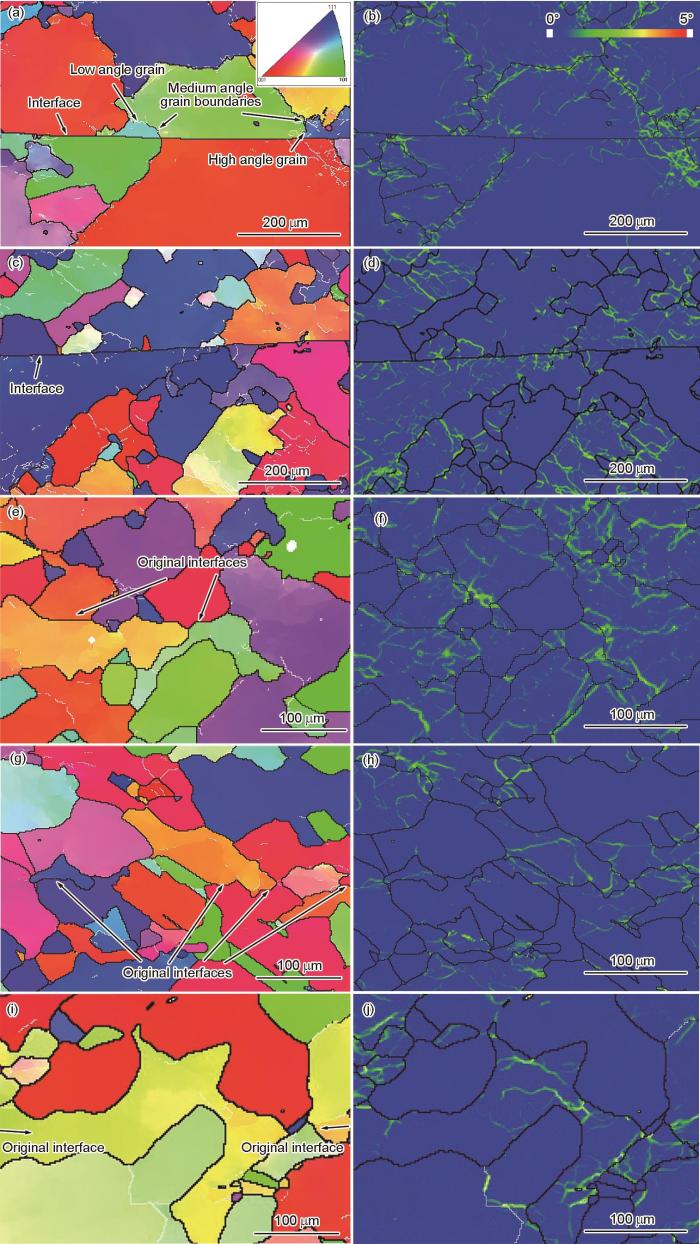
图7 塑性变形温度为1150℃时,不同变形量下界面组织的反极图(IPF)及对应的局部取向差(LAM)图
(a, b) 5% (c, d) 10% (e, f) 20% (g, h) 30% (i, j) 40%
Fig.7 Inverse pole figure (IPF) maps (a, c, e, g, i) and local average misorientation (LAM) maps (b, d, f, h, j) of the interface microstructure under different deformations at 1150℃
2.3.2 连续动态再结晶
连续动态再结晶通常以亚晶的旋转为特征,从而促进小角度晶界之间的取向差不断增加,进而转变为大角度晶界[37]。图7中可以发现存在着一些不连续的大角度晶界,即大角度晶界和中等角度晶界相连或者小角度晶界和中等角度晶界相连,这些现象表明随着变形量的不断增加,亚晶不断发生转动,在变形的过程存在连续动态再结晶的行为[38]。为了更好地理解变形过程中连续动态再结晶机制,不同变形量下局部取向差分布如图8所示。从图8a可以看出,当变形量为5%时,小角度晶界的数量相对较高,而中等角度晶界的数量几乎为零。随着变形量的增加,小角度晶界的数量开始下降,大角度晶界的数量明显增加,而中等角度晶界的数量也有所增加,这表明在这个过程中存在着连续动态再结晶过程。此外,当变形量为40%时,依然存在许多小角度晶界,这是二次应力集中发生所致,与局部取向差(LAM)图的分析相一致。
图8
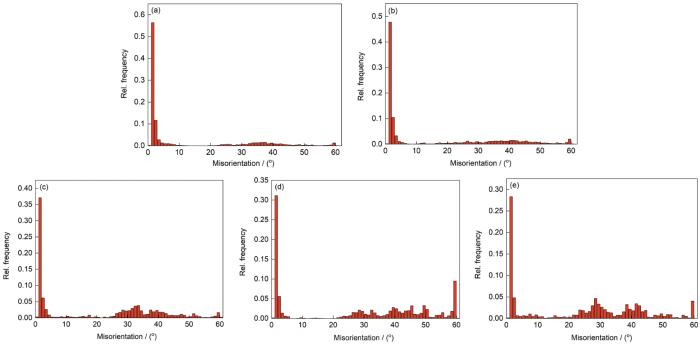
图8 塑性变形温度为1150℃,不同变形量下界面组织的取向差分布
(a) 5% (b) 10% (c) 20% (d) 30% (e) 40%
Fig.8 Misorientation distributions of the interface microstructures under different deformations at 1150℃
2.3.3 界面微观组织演化
图9
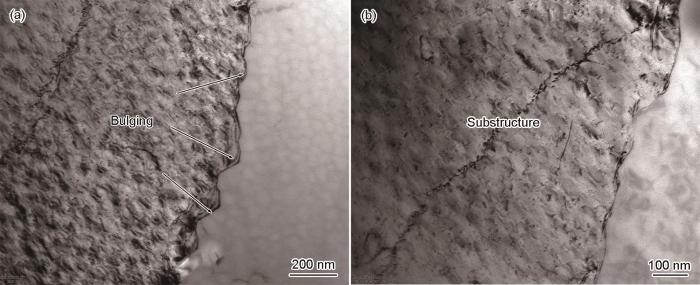
图9 变形温度为1150℃,20%变形量下界面组织的TEM像
Fig.9 TEM images of bulging of interfacial grain boundaries (a) and interfacial substructure (b) at a deformation temperature of 1150℃ and 20% deformation
2.4 界面愈合机制
图10为塑性变形连接过程中界面愈合机制的示意图。本工作中采用的是均匀化态试样,因此初始的晶粒尺寸粗大,如图10a所示。在塑性变形的初始阶段,由于各晶粒间变形不协调,在晶界附近积累了大量位错,从而导致应变诱导晶界迁移,晶粒发生局部弓弯。根据前述分析,在变形的初始阶段存在连续动态再结晶,即小角度晶界通过不断旋转,转变为大角度晶界,如图10b和c所示。在变形的初期主要是界面附近的粗大晶粒在连续和不连续动态再结晶的协同作用下发生细化。研究[30]表明,较小尺寸的晶粒在变形的过程中由于界面张力的作用更容易在扩散焊过程中发生迁移。因此,细化的晶粒在持续应变的作用下更容易发生弓弯,使得界面晶界发生迁移,促进连接界面的愈合。值得注意的是,在持续应变的作用下,晶界弓弯区域由于不均匀应变的作用,会在此处形成亚晶界,这些亚晶界随后逐渐转变为大角度晶界,从而促进弓弯部分从原始晶粒中脱离,成为再结晶晶核[40],占据原始的界面晶界,如图10d和e所示,钟茜婷等[41]在研究Incoloy 028合金的再结晶行为过程中也发现了相同的现象。上述分析表明在塑性变形连接过程中,原始粗大晶粒由于动态再结晶的作用首先发生细化,随后随着应力的持续作用,界面处细化的晶粒在连续再结晶的辅助作用下,通过界面晶界的迁移(不连续动态再结晶)消除了原始连接界面。最后,随着变形的进一步增加,原始连接界面完全被再结晶晶粒占据,界面实现完全愈合,如图10f所示。
图10
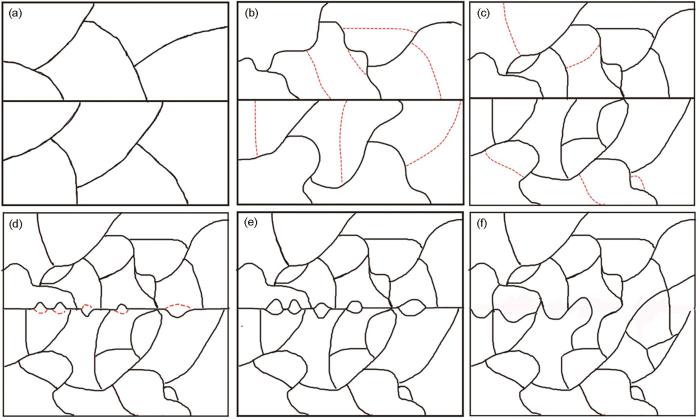
图10 塑性变形连接界面愈合机制
(a) original coarse grains (b, c) grain refinement near the interface (d, e) bulging of the interfacial grains (Fig.10e shows the recrystallization nucleation of interfacial grains) (f) bonding of the interface
Fig. 10 Interface bonding mechanism during plastic deformation bonding
3 结论
(1) 提高变形温度有助于Ni-Co基高温合金连接界面动态再结晶的发生,促进连接界面的愈合。当变形温度达到1200℃时,合金容易发生开裂现象。随着变形量不断增加,原始粗大晶粒发生细化并趋于均匀,同时应变诱导晶界迁移促进界面愈合,界面结合强度也相应提高。
(2) 1150℃是目前最优的塑性变形连接温度。1150℃变形时,合金的变形抗力小,开裂风险低。同时,为实现新型Ni-Co基高温合金的塑性变形连接,合金的变形量需达到40%以上,此时界面完全愈合,界面结合强度可达到母材同等水平。
(3) 在塑性变形连接过程中,界面附近原始粗大的晶粒在应力和温度的耦合作用下首先通过连续动态再结晶和不连续动态再结晶的协同作用使晶粒发生细化。随后,界面处细小的晶粒在连续动态再结晶的辅助作用下,通过不连续动态再结晶的作用,促使界面晶界发生迁移,消除原始的连接界面,实现界面的愈合。