分享:高Cr铁素体耐热钢与奥氏体耐热钢的异种材料扩散连接接头组织演变及力学性能
开展了高Cr铁素体耐热钢与TP347H奥氏体耐热钢的异种材料真空扩散连接实验,研究了扩散连接时间及焊后热处理工艺对扩散影响区组织演变和力学性能的影响。结果表明,随着扩散连接时间的延长,界面结合率逐渐增加。变形储存能差异与位错滑移的相互作用下,在扩散连接界面处发生动态再结晶形成了细小晶粒,最终演化成锯齿状的界面结合形态。扩散连接区晶界与晶粒内部析出细小弥散的MX、M23C6相。焊后热处理之后扩散连接区的晶粒进一步细化,位错相对稳定化,位错密度减少,小角度晶界增多,元素扩散更加充分。对获得的扩散连接试样进行不同温度的拉伸实验,断裂位置均位于基体中,说明获得了高质量的异种材料扩散连接接头。
关键词:
火力发电量在世界总发电量中占有重要的主导地位[1]。长期以来,我国电源结构中火电发电量超过80%,在未来相当长的时间内火电将继续成为我国的主体能源[2,3]。但是,火力燃煤发电不仅需要消耗大量煤炭资源,而且会排放出大量的SO2、CO2、NO x 等污染环境的气体[4],不仅会造成我国的经济损失,而且严重影响着国民的身体健康。因此,采用更先进的技术以提高燃煤发电机组的工作效率成为我国电力发展的紧迫任务。为了迎合以上发展需求,高效节能的超超临界机组己成为电力工业的研发方向。目前,各国纷纷开展大量的研发工作,不断突破火电站机组的运行参数,电厂的热效率随着蒸汽压力和蒸汽温度的升高而得到不断提升,同时蒸汽参数的升高对火力发电机组锅炉管道用钢的使用性能提出了更高的要求[5,6]。
超超临界火电机组内部温度略有差异,高温区域需要高温性能较好的奥氏体耐热钢。从经济角度出发,温度较低的部分可以采用价格便宜、高温性能稍弱的高Cr铁素体耐热钢,因此,超超临界火电机组中不可避免地会存在诸如高Cr铁素体耐热钢与奥氏体耐热钢异种材料连接接头。
高Cr铁素体耐热钢与奥氏体耐热钢部件之间的异种连接方式多种多样。如许鸿吉等[7]采用熔化极活性气体保护电弧焊(MAG)获得1.4003不诱钢/0Cr18Ni9不锈钢异种钢焊接接头,其接头的抗拉强度高于母材,弯曲性能良好。但铁素体不锈钢一侧热影响区的冲击性能较差,且随着温度的降低,其冲击性能显著降低。Muthupandi等[8]报道了利用电子束焊接(EBW)及钨极气体保护焊技术(GTAW)获得铁素体-奥氏体耐热钢异种接头,但焊接熔合区在枝晶内出现元素偏析,导致接头的耐蚀性和机械性能下降。Jang等[9]报道了利用GTAW与电弧焊技术(AW)获得低合金钢与316不锈钢异种接头,但金属焊缝中枝晶组织发达,枝晶区域内观察到明显的偏析和二次相沉淀。同时,传统的熔焊技术获得的焊缝厚度不均匀,造成了拉伸性能及显微强度的差异。Thakare等[10]报道了利用GTAW获得了P91马氏体钢与SS304L奥氏体钢异种材料焊接接头,焊缝熔合区析出物不均匀,存在明显的粗晶,并且沿焊接接头的硬度分布不均匀。因此,利用传统的熔焊技术获得的异种材料扩散连接接头在组织和性能方面存在一定的不足[11]。
固相扩散连接技术是解决异种金属高强度连接的有效方法,被作为关键新材料技术开发领域的热点在新材料制备中发挥着关键和核心作用[12]。Solonin等[13]通过扩散连接技术实现不锈钢/铝合金之间的连接,获得的焊接接头具有很高的焊接强度。Balasubramanian等[14]通过扩散连接技术实现了铝合金和镁合金有效扩散连接,建立了镁合金中Al含量与优化扩散连接参数之间的关系,以获得高质量的铝、镁合金焊接接头。Huang等[15]通过扩散连接技术成功地将W和低活化铁素体马氏体钢(RAFM钢)与Fe中间层扩散连接,W/Fe/RAFM钢接头在剪切实验中表现出较高的结合强度(> 240 MPa)和延展性。
综上所述,当采用传统熔化焊技术(如激光焊、氩弧焊等)时,由于冷却速率过快经常导致形成脆性组织甚至出现裂纹,同时也会引入N、O、H等杂质元素,从而降低接头的性能,而固相扩散连接更易获得室温和高温强度良好的接头,并且连接接头能够在保证良好质量的前提下,保持均质母材或者合金原有的主要性能。在合适的参数条件下,扩散连接接头邻近区域都具有高的强度和优良的塑性。因此,扩散连接是一种相对理想的焊接方法,目前对于高Cr铁素体耐热钢/奥氏体耐热钢异种材料固相连接方面的研究尚不够成熟。同时,电站焊接施工大多数情况是在现场执行,真空扩散连接工作很难得到开展,如果车间或工厂采用扩散连接的方式将高Cr铁素体耐热钢与奥氏体耐热钢异种材料连接接头焊好,那么现场异种钢焊接将变成同种钢连接(高Cr铁素体耐热钢/高Cr铁素体耐热钢和奥氏体耐热钢/奥氏体耐热钢焊接),会大大降低施工难度。
因此,本工作开展了高Cr铁素体耐热钢与TP347H奥氏体耐热钢的异种材料真空扩散连接实验,研究了扩散连接时间及焊后热处理工艺对扩散连接区组织与力学性能的影响。通过澄清扩散连接区组织演化规律及界面结合行为,为高Cr铁素体耐热钢/奥氏体耐热钢异种材料扩散连接工艺优化提供理论指导与实验支撑。
1 实验方法
实验用高Cr铁素体耐热钢与TP347H奥氏体耐热钢的实际成分如表1所示。取直径为15 mm、高度为25 mm的高Cr铁素体耐热钢与TP347H奥氏体耐热钢的圆柱样品若干。真空扩散连接前,用磨床将所有试样的连接表面进行磨削,以获得均匀的表面粗糙度(Ra = 0.912 μm)。用丙酮超声脱脂30 min,乙醇清洗30 min,然后用20%HNO3 + 5%HF + 75%H2O (体积分数)的混合溶液对圆柱形样品进行酸洗,去除氧化膜。采用最高真空度为1.33 × 10-3 Pa的Gleeble 3500热模拟试验机进行真空扩散连接,升温与降温速率均为150℃/min。已知真空扩散连接温度通常控制在(0.6~0.8)Tm (Tm为母材熔点)范围内,高Cr铁素体耐热钢熔点为1312~1745℃,TP347H奥氏体耐热钢熔点为1398~1427℃,因此将扩散连接温度设定为1050℃,扩散连接时间分别为5、15、30、60和120 min,施加15 MPa单轴压力以保证连接界面紧密接触,扩散连接工艺曲线如图1a所示。焊后热处理工艺为1050℃正火30 min,750℃回火90 min,升温速率为10℃/min,工艺曲线如图1b所示。
表1 实验用材料的化学成分 (mass fraction / %)
Table 1
Material | C | Cr | W | Mn | Si | V | Ta | P | Mo | Ni | Nb | N | Fe |
---|---|---|---|---|---|---|---|---|---|---|---|---|---|
High Cr F | 0.092 | 8.87 | 1.71 | 0.28 | 0.01 | 0.19 | 0.002 | < 0.005 | - | - | - | - | Bal. |
TP347H | 0.059 | 17.6 | - | 1.59 | - | - | - | 0.024 | 0.116 | 10.71 | 0.54 | 0.013 | Bal. |
图1
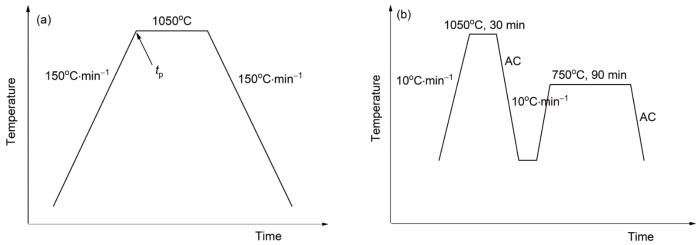
图1 实验工艺曲线示意图
(a) diffusion-bonding (tp—the time to apply pressure) (b) post weld heat treatment (PWHT) (AC—air cooling)
Fig.1 Sketch diagrams for the process curves
将不同扩散连接时间获得的接头垂直于连接界面进行机械加工。采用DMI8光学显微镜(OM)、S4800扫描电子显微镜(SEM)和JEM-2100F透射电子显微镜(TEM)对扩散连接区的微观组织进行表征,计算扩散连接界面结合率。为观察金相组织,依次使用400~2500号的SiC砂纸进行机械抛光,用2 g CuCl2 + 40 mL HCl + 80 mL C2H5OH混合溶液腐蚀试样。对TEM样品进行机械抛光,然后进行离子束减薄。用20%HClO4 + 10%C3H5(OH)3 + 70%C2H5OH (体积分数)的混合溶液电解抛光制备电子背散射衍射(EBSD)样品,并用MTEX软件分析EBSD数据。使用能谱仪(EDS)对扩散连接区的元素分布进行定性分析。采用Instron 5565双立柱电子万能试验机在25和600℃下进行小尺寸拉伸实验,拉伸试样尺寸示意图如图2所示。采用OM和SEM对试样的宏观及微观断口形貌进行观察。
图2

图2 25和600℃拉伸试样示意图
(a) 25oC (b) 600oC
Fig.2 Schematics of tensile specimen (unit: mm, Ra—roughness)
2 实验结果与讨论
2.1 实验用原材料显微组织
高Cr铁素体耐热钢显微组织由δ-铁素体和板条马氏体组成,其中δ-铁素体面积分数为6%左右,如图3a所示。室温下抗拉强度为1215~1230 MPa。TP347H奥氏体耐热钢显微组织为单相奥氏体组织,如图3b所示。室温下抗拉强度为610~615 MPa。
图3
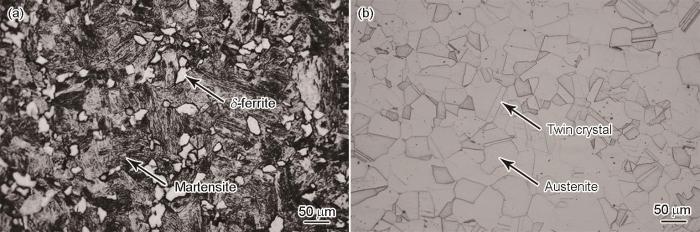
图3 扩散连接试样母材的OM像
(a) high Cr heat-resistant steel sample
(b) TP347H austenitic heat-resistant steel sample
Fig.3 OM images of the parent metals for diffusion-bonding
2.2 扩散连接接头的界面结合与孔洞闭合行为
图4显示了在1050℃、15 MPa压力下,在不同扩散连接时间下扩散连接接头的OM和SEM像。真空扩散连接时间为5 min时,界面处可以明显看到只有少量界面紧密结合在一起,如图4a1~a3所示。这一阶段为塑性变形阶段[16,17]。由于连接表面存在粗糙度,凹凸不平的表面第一次接触以及外部载荷集中作用,导致大的应力集中,从而诱发材料发生塑性变形,随着变形继续,接触面积增加,最终降低了局部应力,减缓了塑性变形。连接界面所受的压力小于材料屈服强度时,塑性变形停止。塑性变形阶段实际接触界面要比名义上的接触面积小很多,是塑性变形的瞬间作用,与扩散连接的时间无关[18]。扩散连接时间延长至15和30 min时,接头处的孔洞形状变得越来越趋近于圆形,如图4b3和c3所示,此为表面源扩散阶段[19]。由于界面孔洞曲率存在差异,孔洞表面的化学势不同,使得原子能够很快沿着孔洞表面进行迁移,大曲率处的物质流向小曲率处,导致孔洞形状发生变化。当孔洞的表面曲率相同,即为圆形时,表面源机制停止。由此可见,表面源扩散阶段作用的驱动力为孔洞表面所存在的曲率差,这一阶段可以忽略孔洞的体积变化。扩散连接时间进一步延长至60 min时孔洞数量减少,逐渐形成良好的扩散连接接头,如图4d1~d3所示,此为界面源扩散阶段[20,21]。这一阶段主要受随后的扩散和晶界迁移控制。沿连接界面观察到新生成的细小晶粒,导致晶粒细化。这些细化的晶粒通过提供许多界面促进晶界迁移,从而导致扩散连接过程中的扩散率增加,进而提高了扩散连接界面结合率。当扩散连接时间达到120 min时,在连接界面几乎看不到孔洞的存在,说明在扩散连接过程中获得了良好的扩散连接接头,如图4e1~e3所示,此阶段为幂定律蠕变机制控制阶段[22]。扩散连接过程中,金属的微观蠕变对孔洞的闭合也有影响。随着孔洞尺寸的变化,扩散连接界面附近的应力与应变速率也随之发生变化,孔洞在应力的作用下消失,形成可靠的扩散连接界面。因此,随着保温时间的延长,连接界面变得越来越模糊,有利于孔洞闭合,形成牢固的连接界面。
图4

图4 连接温度1050℃、连接压力15 MPa,不同扩散连接时间条件下扩散连接试样接头微观组织的低倍和高倍OM像及SEM像
(a1-a3) 5 min (b1-b3) 15 min (c1-c3) 30 min (d1-d3) 60 min (e1-e3) 120 min
Fig.4 Low (a1-e1) and high (a2-e2) magnified OM images and SEM images (a3-e3) showing the microstructures of the diffusion-bonding joints with the bonding temperature of 1050oC and bonding stress of 15 MPa, for the different bonding time
为了定量评估扩散连接接头的质量,图5给出了扩散连接时间与扩散连接界面结合率之间的关系。扩散连接界面结合率的计算公式为:
式中,ε为扩散连接界面结合率,L为界面总长度(μm),ΣLi 为未连接部分长度之和(μm)。结果表明,当扩散连接时间为5 min时,扩散连接界面结合率较低,随着扩散连接时间的延长,扩散连接界面结合率增大。当扩散连接时间为120 min时,扩散连接界面结合率高达98.32%。同时,由图5可以看出,扩散连接速率随扩散连接时间延长呈现降低的趋势,其原因为:(1) 真空扩散连接过程先经历表面源扩散机制,再经历界面源扩散机制,表面扩散克服势垒所需的能量要小些,元素扩散速率较快;(2) 真空扩散连接进行至一定的阶段,2种基体之间元素浓度差减小,降低了元素扩散速率。
图5
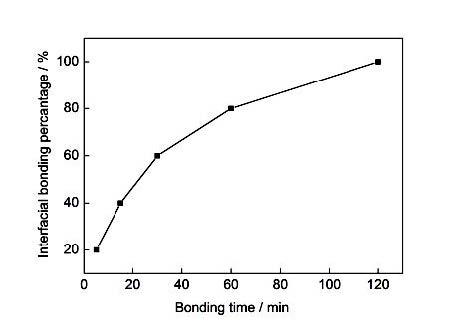
图5 不同扩散连接时间的界面结合率
Fig.5 Interfacial bonding percentage as a function of the diffusion-bonding time
2.3 扩散连接区的组织与演化
合适的焊后热处理工艺可以改善扩散连接接头的组织和力学性能,消除焊接接头的内应力,有利于获得优质的扩散连接接头[23,24]。图6显示了扩散连接时间为120 min时扩散连接试样扩散连接区焊后热处理后的SEM像。与图4e3对比可以看出,经焊后热处理后,试样扩散影响区组织晶粒更加细小,这是由于焊后热处理使得元素扩散更加充分,母材中含有Nb等强碳氮化物形成元素,它们和C、N都有极强的亲和力,与之形成相应的极为稳定的化合物弥散分布在试样中,对位错起到钉扎作用,从而达到一定的晶粒细化作用[25]。
图6

图6 连接温度1050℃、连接压力15 MPa、连接时间120 min的扩散连接试样扩散连接区经焊后热处理后的SEM像
Fig.6 SEM images of the diffusion-bonding joints with the bonding temperature of 1050oC, bonding stress of 15 MPa, and the bonding time of 120 min after PWHT
为了进一步验证适当的焊后热处理工艺可以细化晶粒,图7a显示了扩散连接时间为120 min时未经焊后热处理的扩散连接试样扩散连接区的EBSD像。可见,中间为扩散连接界面,上方为fcc结构的TP347H奥氏体耐热钢晶粒,主要由单一的等轴奥氏体晶粒组成,靠近扩散连接界面的晶粒尺寸较小,远离扩散连接界面的晶粒尺寸较大。下方为bcc结构的高Cr铁素体耐热钢晶粒,主要由板条马氏体组成。扩散连接界面处晶粒的取向发生变化,可以观察到细小的呈串联状分布的等轴晶粒,说明扩散连接过程中试样扩散连接区发生了动态再结晶。这是因为塑性变形的不断增加,晶粒内由于位错的交滑移与攀移形成大量亚晶,不同晶粒之间变形储存能存在差异,原本平直的晶界会产生锯齿状凸起。随着应变不断增加,晶界处凸起部分在位错滑移的协助下将会随之发生转动;而且随着应变增加,凸起部分与晶粒之间的取向差不断增加,凸起部分最终成为拥有较大角度晶界的动态再结晶晶粒,提高试样塑性变形后强度[26]。这些晶粒在铁素体晶界处形核、长大,扩散连接界面两侧相邻2个不同组织晶粒的晶界有相互连结的现象,即界面两侧的fcc结构晶粒与bcc结构晶粒通过晶界连结,最终演变成锯齿状的界面结合形态,如图7b所示。正是这样的界面特征,可保证扩散连接接头的结合质量。为了定量地分析晶粒尺寸的变化,绘制出扩散影响区EBSD像,如图7c所示,利用Image-Pro Plus 软件计算得到奥氏体平均晶粒尺寸为2.06 μm,铁素体平均晶粒尺寸为5.48 μm。图7a方框处扩散连接界面位错密度图如图7d和e所示(利用MTEX软件计算单位时间内的位错密度所得)。可见,高Cr铁素体耐热钢一侧的位错密度显著高于TP347H奥氏体耐热钢一侧,扩散连接影响区的位错密度高于试样基体。
图7

图7 焊后热处理之前扩散连接试样扩散连接区的EBSD分析
(a) EBSD image of joint area
(b) grain diagram of diffusion-bonding zone in rectangle area in Fig.7a
(c) phase diagram of diffusion-bonding zone in rectangle area in Fig.7a
(d) dislocation density diagram of diffusion-bonding zone of TP347H austenitic heat-resistant steel in rectangle area in Fig.7a
(e) dislocation density diagram of diffusion-bonding zone of high Cr ferrite heat-resistant steel in rectangle area in Fig.7a
Fig.7 EBSD analyses of the diffusion-bonding joint area before PWHT
图8a显示了扩散连接时间为120 min时扩散连接试样扩散连接区经焊后热处理的EBSD像。可见,焊后热处理之后试样扩散连接区的相分布与图7a相一致,不同的是,经过热处理后高Cr铁素体耐热钢一侧晶粒取向更趋向一致化,TP347H奥氏体晶粒更加细小。图8c所示为焊后热处理后扩散连接区的EBSD像,计算得到奥氏体平均晶粒尺寸减小至1.73 μm,铁素体平均晶粒尺寸减少至2.53 μm。可见,经焊后热处理之后试样扩散连接界面处晶粒得到细化。原因在于钢中形成了难溶于奥氏体的碳化物,分布在晶粒边界上,呈现弥散分布,阻止奥氏体晶粒的长大,对位错有一定的钉扎作用,从而细化晶粒。图8d和e显示了图8a方框处扩散连接界面位错密度图。可以发现,扩散连接影响区位错相对稳定化,位错密度减少。
图8
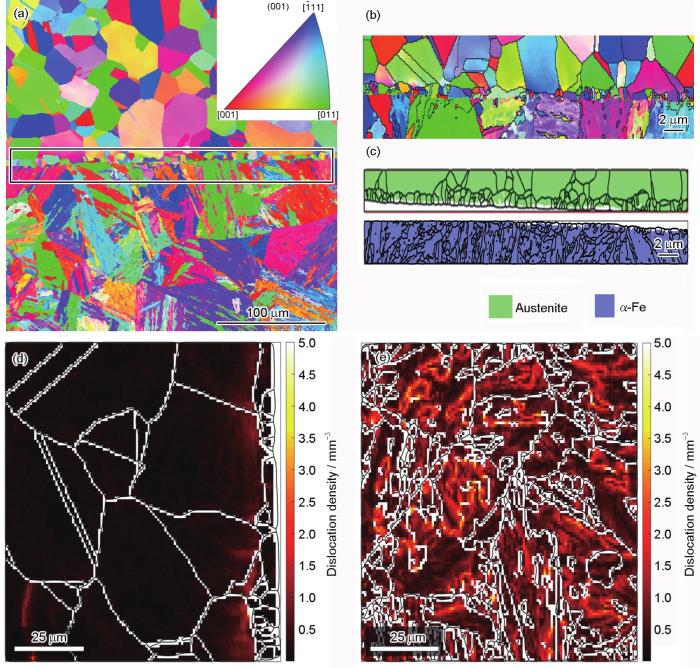
图8 焊后热处理之后扩散连接试样扩散连接区的EBSD分析
(a) EBSD image of joint area
(b) grain diagram of diffusion-bonding zone in rectangle area in Fig.8a
(c) phase diagram of diffusion-bonding zone in rectangle area in Fig.8a
(d) dislocation density diagram of diffusion-bonding zone of TP347H austenitic heat-resistant steel in rectangle area in Fig.8a
(e) dislocation density diagram of diffusion-bonding zone of high Cr ferrite heat-resistant steel in rectangle area in Fig.8a
Fig.8 EBSD analyses of the diffusion-bonding joint area after PWHT
图9a显示了扩散连接时间为120 min时未经焊后热处理的扩散连接试样扩散连接区的TEM像。虚线显示为扩散连接界面。通过选区电子衍射(SAED)花样可知,虚线左侧为晶带轴方向为[
图9
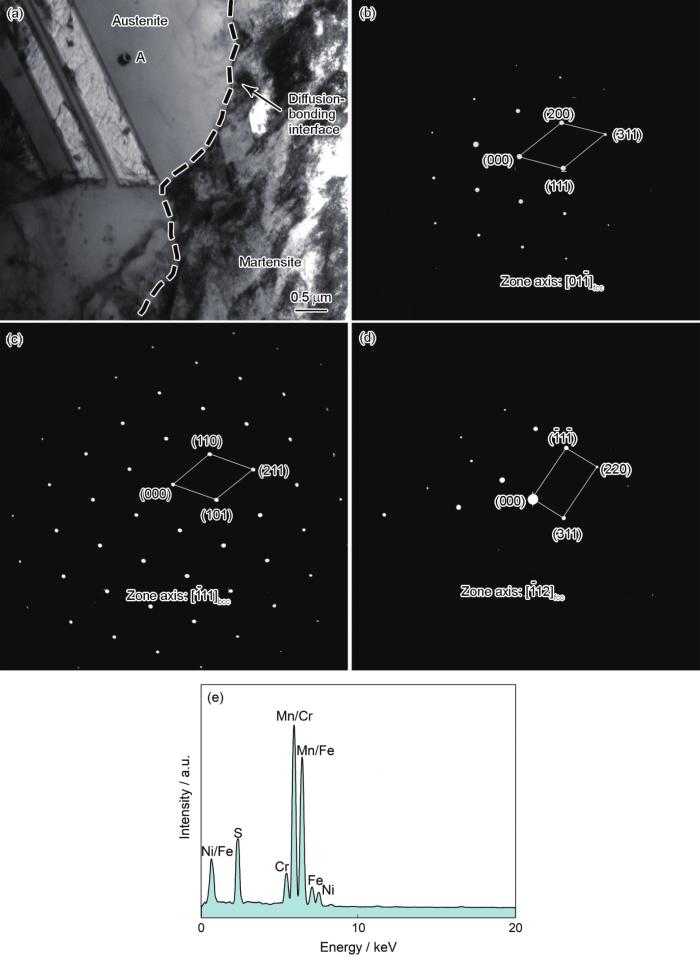
图9 焊后热处理之前扩散连接试样扩散连接区的TEM分析
(a) TEM image of the joint (b, c) SAED patterns of the joint for left and right sides of diffusion-bonding interface showed by dash line in Fig.9a, respectively (d) SAED pattern of the precipitate A in Fig.9a (e) EDS of the precipitate A in Fig.9a
Fig.9 TEM analyses of the diffusion-bonding joints before PWHT
图10a显示了扩散连接时间为120 min时扩散连接试样扩散连接区经焊后热处理的TEM像。与图9a比较发现,无论热处理与否,高Cr铁素体耐热钢一侧母材的显微组织均为板条马氏体,TP347H奥氏体耐热钢一侧母材的显微组织为奥氏体晶粒。所不同的是,经热处理后得到的板条马氏体更为细小,且奥氏体晶界较为清晰。扩散连接界面处与晶粒内部弥散着大量不同尺寸的碳化物颗粒。经SAED花样标定(图10d)与EDS分析(图10e)确定为M23C6相,这是因为Cr与Fe发生置换后,由于Fe与C的结合力低于Cr与C的结合力,Cr原子在扩散连接界面附近发生偏聚,如图11所示,形成富Cr的M23C6相,对扩散连接试样接头起到弥散强化及位错强化效果[27~29]。TP347H奥氏体耐热钢一侧靠近扩散连接界面处晶粒变得细小,但由于组织遗传性,仍有少量较为粗大的晶粒存在。
图10
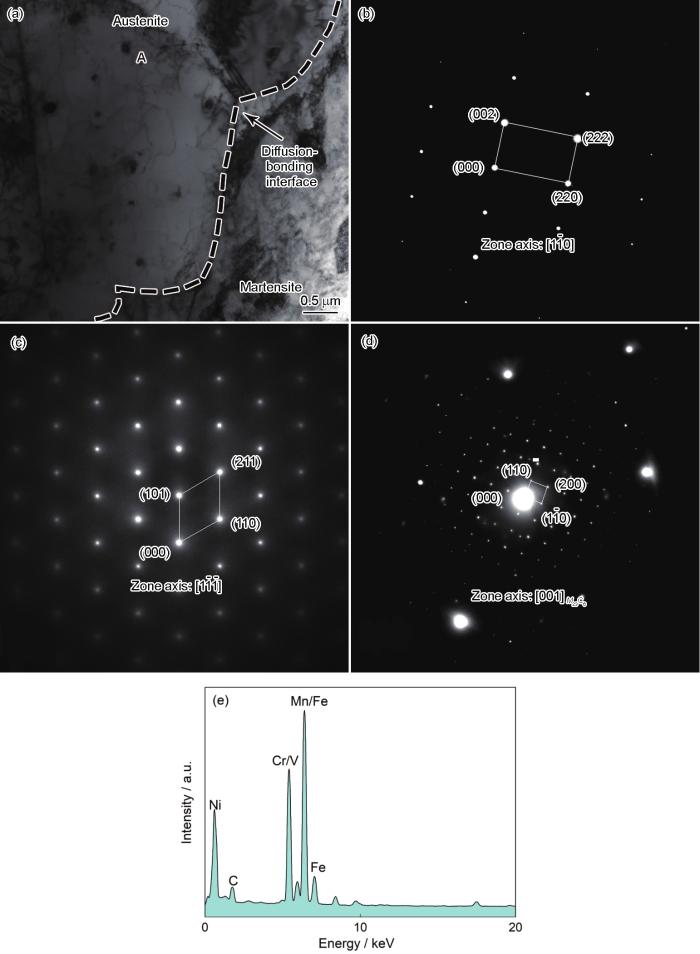
图10 焊后热处理之后扩散连接试样扩散连接区的TEM分析
(a) TEM image of the joint (b, c) SAED patterns of the joint for left and right sides of diffusion-bonding interface showed by dash line in Fig.10a, respectively (d) SAED pattern of the precipitate A in Fig.10a (e) EDS of the precipitate A in Fig.10a
Fig.10 TEM analyses of the diffusion-bonding joints after PWHT
图11
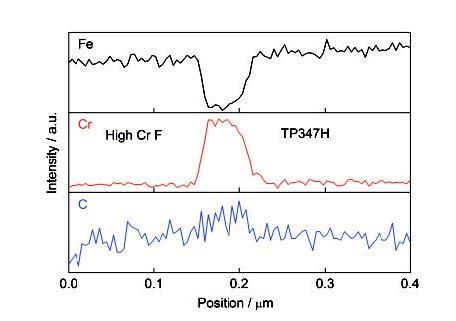
图11 焊后热处理之后的扩散连接试样扩散连接区EDS线扫描结果
Fig.11 EDS line scanning results of the diffusion-bonding joint after PWHT
2.4 扩散连接接头的力学性能分析
高Cr铁素体耐热钢与TP347H奥氏体耐热钢扩散连接时间为120 min时扩散连接试样焊后热处理前后不同温度拉伸实验结果如表2所示,图12为拉伸试样断裂后实物图。可见,25℃下,不管热处理与否,试样拉伸断裂位置均处于TP347H奥氏体耐热钢侧母材。600℃下,焊后热处理前试样拉伸断裂位置处于TP347H奥氏体耐热钢侧母材,焊后热处理后试样拉伸断裂位置处于高Cr铁素体耐热钢侧母材。
表2 焊后热处理前后扩散连接试样接头的拉伸实验结果
Table 2
Specification | Temperature / oC | Average tensile strength / MPa | Rp0.2 / MPa | Elongation / % | Shrinkage / % |
---|---|---|---|---|---|
Before PWHT | 25 | 601.68 | 263.56 | 33.05 | 50.66 |
600 | 322.45 | 153.79 | 21.79 | 47.62 | |
After PWHT | 25 | 558.82 | 249.37 | 24.74 | 31.69 |
600 | 290.45 | 153.38 | 12.26 | 29.34 |
图12
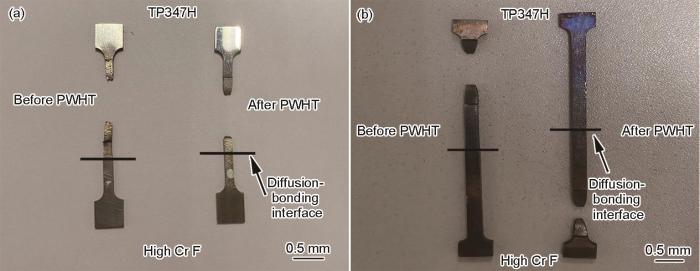
图12 拉伸断裂试样实物图
(a) 25oC (b) 600oC
Fig.12 Physical drawing of tensile fracture specimen
不同实验温度下拉伸断裂位置均处于母材中,表明实现了异种材料扩散连接接头的可靠连接。通过前文扩散影响区组织分析可知,扩散连接接头强化的原因有3点:(1) 塑形变形的进行使得不同晶粒之间变形储存能存在差异,原本平直的晶界会产生锯齿状突起,扩散连接界面两侧相邻2个不同组织晶粒的晶界有相互连结的现象,形成了锯齿状的界面结合形态,如图7b所示;(2) 在晶粒内位错滑移的协助作用下扩散连接界面附近发生动态再结晶,动态再结晶晶粒在铁素体晶界处形核、长大,呈现串联状等轴晶粒分布在扩散连接界面上,扩散连接界面上的晶粒得以细化;(3) 试样内Nb、Cr等元素充分扩散,与C原子结合在晶界与晶粒内部析出MX、M23C6相,抑制晶粒长大,导致晶粒细化,可对扩散连接界面起到细晶强化和弥散强化的效果,如图9和10所示。
由表2可知,随着实验温度的上升,试样抗拉强度下降,这是因为随着温度的升高,钢内的原子内能增加,促进原子运动,降低原子之间的结合力。试样断后伸长率与面积收缩率随温度的升高而降低,面积收缩率均大于断后伸长率。颈缩率越大,其抗颈缩能力越大,这是造成高Cr铁素体耐热钢与TP347H奥氏体耐热钢异种钢扩散连接接头高温拉伸断裂方式转变的主要原因。扩散连接试样拉伸应力-应变曲线如图13所示。可以看出,测试温度为600℃时拉伸应变降低,这是由于在较高的实验温度下,晶界弱化,试样内部析出的二次相阻碍位错运动,试样内部微孔萌生,优先断裂。图14和15显示了高Cr铁素体耐热钢和TP347H奥氏体耐热钢扩散连接时间为120 min时试样接头焊后热处理前后不同实验温度下拉伸断口形貌。可见,断口处存在大量的韧窝,属于典型的韧性断裂,断口边缘处出现颈缩现象,可进一步确认,接头的断裂方式为微孔聚集形断裂,即焊接接头在拉伸实验中经历了“微孔形核-微孔聚集-微孔长大”3个断裂阶段。
图13
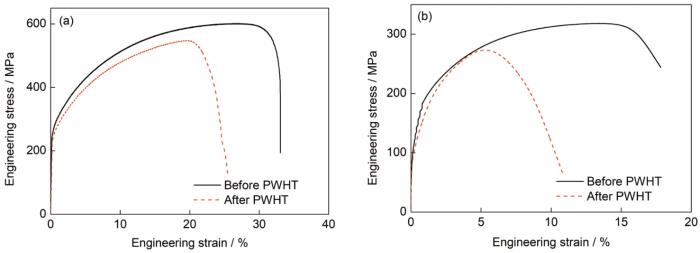
图13 不同测试温度下焊后热处理前后扩散连接试样的工程应力-应变曲线
Fig.13 Engineering stress-strain curves of the diffusion-bonding joints before and after PWHT under testing temperatures of 25oC (a) and 600oC (b)
图14
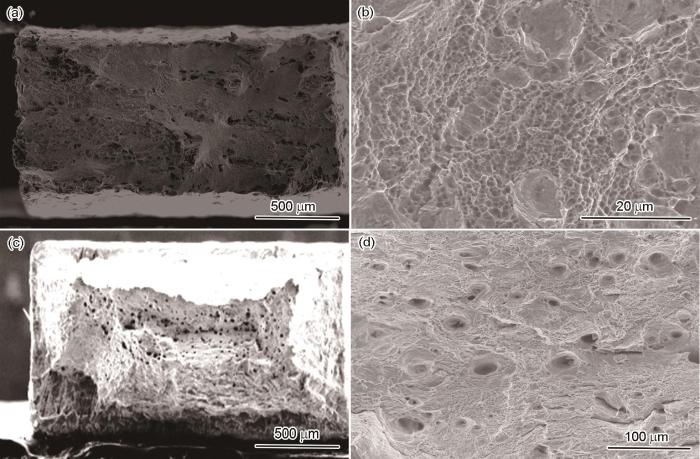
图14 焊后热处理前后扩散连接试样接头在25℃拉伸的断口形貌
Fig.14 Low (a, c) and high (b, d) magnified tensile fracture morphologies of the diffusion-bonding joints at 25oC before (a, b) and after (c, d) PWHT
图15
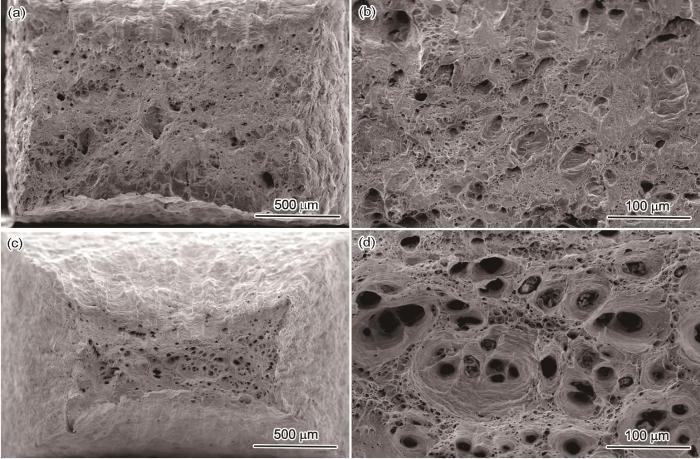
图15 焊后热处理前后扩散连接试样接头在600℃拉伸的断口形貌
Fig.15 Low (a, c) and high (b, d) magnified tensile fracture morphologies of the diffusion-bonding joints at 600°C before (a, b) and after (c, d) PWHT
3 结论
(1) 高Cr铁素体耐热钢与TP347H奥氏体耐热钢异种钢扩散连接界面处晶粒的取向发生变化,可以观察到细小的呈串联状分布的等轴晶粒,说明扩散连接过程中扩散影响区发生动态再结晶。这些晶粒在铁素体晶界处形核、长大,扩散连接界面两侧相邻2个不同组织晶粒的晶界有相互连结的现象,即界面两侧的fcc结构晶粒与bcc结构晶粒通过晶界连结,最终演变成锯齿状的界面结合形态。
(2) 将在1050℃、15 MPa、120 min条件下获得的扩散连接试样进行1050℃正火30 min,750℃回火90 min的焊后热处理,扩散影响区奥氏体平均晶粒尺寸由2.06 μm减小至1.73 μm,铁素体平均晶粒尺寸由5.48 μm减少至2.53 μm,位错相对稳定化,位错密度减少,小角度晶界增多,元素扩散更加充分。
(3) 由于元素的扩散与结合,在晶界与晶粒内部析出MX、M23C6相,但没有发现金属间化合物,析出相进一步抑制晶粒长大,从而导致晶粒细化,可对扩散连接界面起到细晶强化和弥散强化的效果。
(4) 不同实验温度下拉伸断裂位置均处于母材中,说明实现了异种材料扩散连接接头的可靠连接。
来源--金属学报