分享:搅拌头转速对2507双相不锈钢搅拌摩擦加工组织及性能的影响
1.
2.
3.
通过对5 mm厚2507双相不锈钢进行搅拌摩擦加工,研究了在加工速率为100 mm/min时搅拌头转速对加工区域组织、力学性能和腐蚀性能的影响。结果表明,随着搅拌头转速的增大,搅拌区晶粒尺寸呈现先减小后增大的趋势。加工热循环和应力变形对加工区铁素体与奥氏体组织比例的变化影响不大,其铁素体含量仍保持在标准规范40%~60%之间。仅在搅拌头转速为200 r/min时,在加工区底部发现σ相析出。加工区显微硬度分布呈现“盆状”,其硬度最高值出现在搅拌区前进侧的底部,对应搅拌区晶粒尺寸最细小处。随着搅拌头转速的增加,搅拌区纵向拉伸强度呈现先增大后减小的趋势,而塑性则呈现先减小后增大的趋势。搅拌头转速为400 r/min时,搅拌区具有最优腐蚀性能。
关键词:
双相不锈钢是一种兼具铁素体和奥氏体性能优点的不锈钢,其固溶组织中铁素体和奥氏体比例接近1∶1,具有良好的耐腐蚀性能、力学性能和较好的焊接性能[1],已广泛应用于船舶桥梁、石油化工、海水淡化等行业[2,3]。双相不锈钢构件在服役过程中会面临表面产生应力腐蚀裂纹以及其他裂纹的问题,进而对构件的安全稳定性产生影响[4]。
搅拌摩擦加工技术是Mishra教授于1999年基于搅拌摩擦焊接原理提出的,通过工具的搅拌旋转作用使材料中产生热塑性流动,再结晶细化晶粒,达到裂纹自动修复填补的目的,同时提高材料的力学性能,可用于双相不锈钢构件的修复工程[5,6]。双相不锈钢的搅拌摩擦加工组织及性能对结构件的安全性有着重要影响,其中组织中析出相、加工区的力学性能和腐蚀性能的影响尤为重要。双相不锈钢在热加工过程中可能会产生各种析出相,其中σ相是最常见同时也是危害性最大的析出相,国内外学者对其产生的条件做了许多研究。陈万里[7]对2707双相不锈钢在不同搅拌头转速下的搅拌摩擦焊接接头组织和耐蚀性能进行了研究,发现在搅拌头转速为200和300 r/min时,接头有σ相生成,耐蚀性能较差,而转速为400和500 r/min时,接头区域无σ相生成,耐蚀性能较好。双相不锈钢结构件在服役过程中可能会受到不同方向的作用力,同时还存在着海水等介质的腐蚀作用,这对修复件不同方向的力学性能及腐蚀性能提出了更高的要求。刘兴龙[8]对2707双相不锈钢搅拌摩擦焊接接头组织及力学性能进行分析,发现随着搅拌头转速的降低,焊核区的晶粒尺寸逐渐减小,平均硬度逐渐增大。Esmailzadeh等[9]在研究双相不锈钢搅拌摩擦焊接头的横向拉伸时,发现不同参数下的接头均在母材处断裂,表明各参数下接头强度均高于母材,且焊核区晶粒尺寸随焊接速率的增加逐渐减小,同时焊接接头的强度和硬度提高。Santos等[10]则对纵向试样的拉伸性能进行测试,发现S32101及S32750接头焊核区的强度和延伸率均得到提高,而S32760接头焊核区存在析出相,导致延伸率明显下降。Mishra等[11]对2507双相不锈钢进行多次搅拌摩擦加工后的组织及其耐蚀性能进行研究,发现随着搅拌摩擦加工的次数增加,搅拌区的晶粒显著细化,强度和硬度提高,耐蚀性能相应提高。Magnani等[12]通过测试2205和2101双相不锈钢搅拌摩擦焊接头的电化学阻抗谱,发现2205双相不锈钢接头的耐蚀性高于母材,而2101双相不锈钢接头的耐蚀性相对母材有所降低。
搅拌摩擦加工技术对双相不锈钢裂纹的有效修复在工程机械领域存在着广阔的应用前景,可以以低成本获得更加安全可靠的结构件。然而目前的研究大多针对双相不锈钢的搅拌摩擦焊接,而对于双相不锈钢搅拌摩擦加工技术的研究相对较少。因此,本工作通过对2507双相不锈钢进行搅拌摩擦加工实验,研究了搅拌头转速对于加工区域的组织、力学性能和腐蚀性能的影响,为双相不锈钢搅拌摩擦加工修复的应用提供理论及实验基础。
1 实验方法
选择尺寸为250 mm×100 mm×5 mm的2507双相不锈钢板材进行搅拌摩擦加工,其化学成分(质量分数,%)为:Cr 24~26,Ni 6~8,Mo 3~5,Si ≤ 0.8,C ≤ 0.03,S ≤ 0.02,P ≤ 0.035,N 0.24~0.32,Fe余量。力学性能为:抗拉强度867~880 MPa,屈服强度663~675 MPa,显微硬度270~290 HV,延伸率42.8%~44.8%。在板材进行搅拌摩擦加工前,需用砂纸对板材表面进行打磨,去除表面氧化物等杂质,再用丙酮对板材进行擦洗,去除油污,然后通过自制的夹具将板材固定在加工工作台表面。
采用自制的LQH-G15龙门式搅拌摩擦焊设备,实验时主轴倾角为3°,采用循环水进行冷却,Ar气作为保护气,防止加工区域在高温时被氧化,加工过程如图1所示。本实验选用的搅拌头材料为W-25Re (质量分数,%),搅拌针为锥形设计,针长度为2.8 mm,轴肩直径为15 mm。实验中的加工参数为:加工速率固定为100 mm/min,搅拌头转速分别为200、300、400、500和600 r/min。
图1
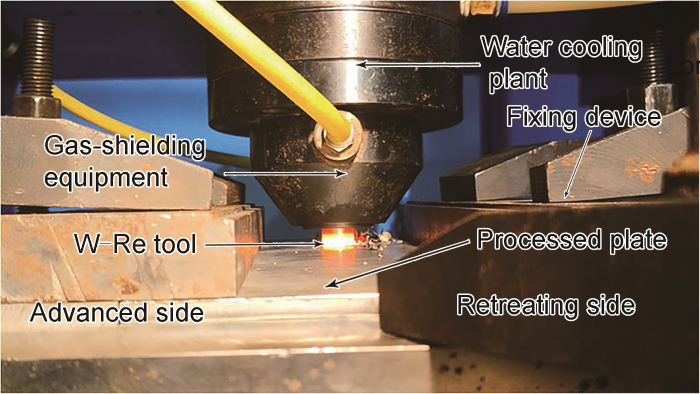
图1 搅拌摩擦加工过程示意图
Fig.1 Schematic of friction stir process
在加工区域截取适量长度的金相试样,在水砂纸上打磨至1500号,用粒度为1 μm的金刚石抛光剂抛光至试样表面无划痕。用40%NaOH溶液(质量分数)对抛光试样进行电解腐蚀,待腐蚀完成后用酒精溶液冲洗加工试样表面腐蚀产物,并吹干备用。采用DSX510光学显微镜(OM)观察并分析加工试样截面形貌及微观组织,并采用Image-Pro软件对显微组织进行分析,测量其相比例及晶粒尺寸;采用MERLIN Compact场发射扫描电子显微镜(SEM)并结合能谱(EDS)对加工区微观组织、拉伸断口形貌及腐蚀形貌进行观察分析;采用电子背散射衍射(EBSD)技术对加工区微观组织、晶粒尺寸等进行分析;采用D/max-2500 X射线衍射仪(XRD)对加工区底部进行物相分析。加工区截面显微硬度分布特征采用ARTCAM-300SSI-C数字转塔显微硬度计进行测试,纵向拉伸试样的室温拉伸实验采用INSTRON 5967试验机进行,加载速率为3 mm/min,拉伸试样尺寸及截取位置如图2所示。腐蚀性能通过Zahner工作站及配套的Thales电化学软件对腐蚀试样进行电化学测试和电化学阻抗谱(EIS)测试,均采用三电极体系,选用待测工件试样作为工作电极(WE),选用Pt电极和饱和甘汞电极分别作为辅助电极(CE)和参比电极(SCE),测试溶液为3.5%NaCl溶液(质量分数)。由于搅拌摩擦加工过程主要是对材料进行表面改性,且针对实际应用环境中上表面与外界环境接触的情况,因此针对不同工艺参数下搅拌区上表面的耐蚀性展开研究。电化学测试试样选取为搅拌摩擦加工上表面区域,测试面积为1 cm2,EIS测试前,需将电化学试样在测试溶液中静置20 min以稳定开路电位测试,试样截取示意图如图2所示。
图2
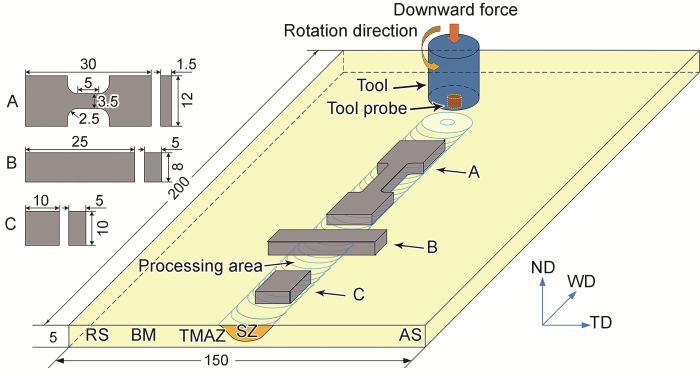
图2 纵向拉伸试样、组织分析及硬度测试试样和腐蚀测试试样截取示意图
Fig.2 Schematic of sample interception (unit: mm; A—longitudinal tensile test sample, B—microstructure analysis and hardness test sample, C—corrosion test sample, RS—retreating side, BM—base material, TMAZ—thermo-mechanically affected zone, SZ—stir zone, AS—advancing side, ND—normal direction, WD—welding direction, TD—transverse direction)
2 实验结果与分析
2.1 微观组织
不同搅拌头转速下2507双相不锈钢搅拌摩擦加工区截面形貌的OM像如图3所示。可以看出,不同搅拌头转速下加工区整体形貌变化不大,均呈“盆状”。如图3a所示,当搅拌头转速为200 r/min时,加工区内部可以观察到孔洞或隧道缺陷,这是因为搅拌头转速较低时,加工过程温度较低,在加工区下方的热塑性材料流动性较差,搅拌针从前进侧带走的材料得不到及时的补充。随着搅拌头转速增大,加工过程的热输入增大,材料的流动性得到增强,从而消除加工区的孔洞等缺陷,得到无缺陷的加工区。如图3d和e所示,当搅拌头转速进一步增大时,由于搅拌头的转速过高,热输入增大,导致加工区的材料黏度降低,搅拌头与热塑性材料的摩擦减小[13]。此时,在搅拌针后方区域,热塑性材料不能很好地被搅拌针从后退侧补充至前进侧,从而在加工区下方重新产生孔洞或隧道缺陷。
图3
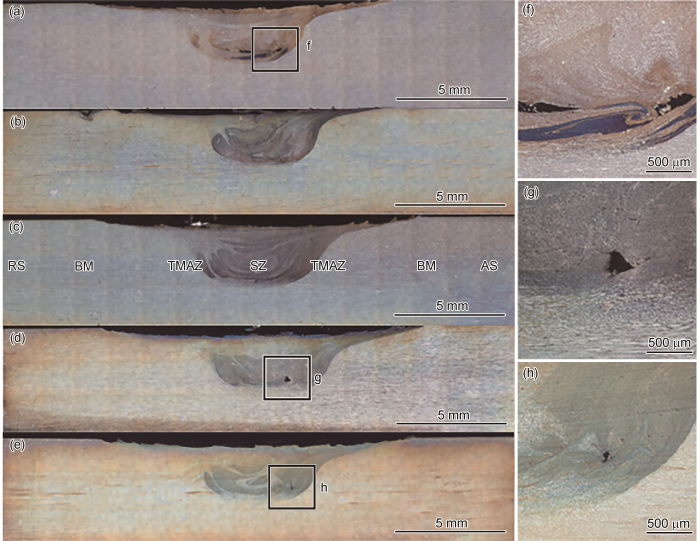
图3 不同搅拌头转速下2507双相不锈钢搅拌摩擦加工区截面形貌的OM像
Fig.3 Cross-sectional OM images of the processing zone of friction stir processed 2507 duplex stainless steel at different tool rotation speeds of 200 r/min (a), 300 r/min (b), 400 r/min (c), 500 r/min (d), and 600 r/min (e) and the locally enlarged morphologies of hole defects in the square areas in Fig.3a (f), Fig.3d (g), and Fig.3e (h)
按照组织特征,加工区截面主要可以分为3个区域:搅拌区(SZ)、热机影响区(TMAZ)和母材(BM),各区域典型微观组织的EBSD像如图4所示。图4a中,母材未受到热机作用,晶粒呈现轧制态,铁素体和奥氏体比例接近1∶1。图4b中,在加工过程中热机影响区受到搅拌头的剪切带动作用和一定程度的热循环,导致铁素体与奥氏体组织发生一定程度的扭曲,晶粒沿着特定方向发生弯曲变形,晶粒尺寸相对于母材有一定的细化。图4c为搅拌区组织的EBSD像,其晶粒相对母材发生明显细化。这是由于在加工过程中,搅拌区受到搅拌头的剧烈搅拌作用,其组织经历了强烈的热机耦合作用,发生了充分的动态回复再结晶,从而导致晶粒细化。
图4
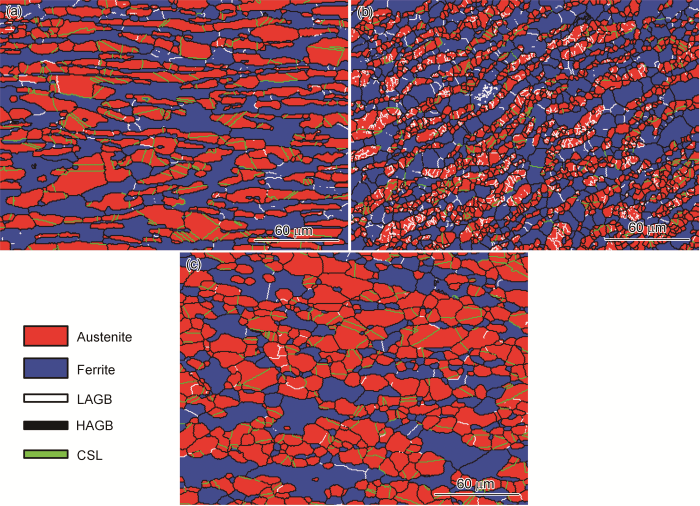
图4 搅拌头转速400 r/min时2507双相不锈钢搅拌摩擦加工区各区域微观组织的EBSD像
(a) BM (b) TMAZ (c) SZ
Fig.4 EBSD images of microstructure of various zones in the processing zone of friction stir processed 2507 duplex stainless steel at tool rotation speed of 400 r/min (LAGB—low angle grain boundary, HAGB—high angle grain boundary, CSL—coincidence site lattice)
搅拌区作为受到搅拌针剪切作用和热循环最剧烈的区域,其晶粒、组织和各相的变化也更为明显。图5为不同搅拌头转速下2507双相不锈钢搅拌区微观组织的OM像,其晶粒尺寸和铁素体含量变化如图6所示。随着搅拌头转速从200 r/min增大至600 r/min,搅拌区晶粒尺寸呈现先减小后增大的变化规律。搅拌头转速的增加会同时影响材料的应变速率和加工热输入[14]。搅拌头转速的增加使搅拌作用更为剧烈,材料应变速率增大,再结晶作用增强,形核率增大,晶粒细化程度更加明显。因此在搅拌头转速增加至400 r/min时,搅拌作用引起的晶粒细化效果大于热输入增大引起的晶粒长大的效果,晶粒尺寸呈现减小的趋势;而当转速进一步增加时,热输入的增大导致再结晶晶粒长大趋势更为明显,导致晶粒尺寸呈现增大的趋势。
图5

图5 不同搅拌头转速下2507双相不锈钢搅拌区微观组织的OM像
Fig.5 OM images of microstructure of stir zone of friction stir processed 2507 duplex stainless steel at different tool rotation speeds of 200 r/min (a), 300 r/min (b), 400 r/min (c), 500 r/min (d), and 600 r/min (e)
图6

图6 不同搅拌头转速下2507双相不锈钢搅拌区晶粒尺寸和铁素体含量变化
Fig.6 Changes of grain size and ferrite fraction of stir zone of friction stir processed 2507 duplex stainless steel at different tool rotation speeds
搅拌区的铁素体含量同时受到加工过程的峰值温度和冷却过程的冷却速率的影响[15]。搅拌头转速的增加伴随着加工过程峰值温度的升高,同时也会使材料应变速率增加。加工过程峰值温度的升高会促进奥氏体向铁素体的转变[16],而应变会引入位错,从而促进铁素体向奥氏体发生转变,因此搅拌区铁素体的含量变化为峰值温度和应变速率综合作用的结果。当搅拌头转速为400 r/min时,搅拌区的铁素体含量最高,但仍保持在约40%~60%之间,符合双相不锈钢的相关标准。
双相不锈钢由于其合金元素含量较高,在热加工过程中容易发生各种复杂的冶金反应,从而析出Cr2N、χ相、σ相等。这些析出相大部分会降低不锈钢的力学性能和耐蚀性能,属于有害相,其中σ相为最常见且危害最大的析出相。通过观察不同转速下搅拌区组织,发现当搅拌头转速为200 r/min时,搅拌区底部位置存在细小黑色颗粒富集区域,如图7所示,而其他转速条件下则未观察到黑色颗粒。对该区域进行EDS分析,结果如表1所示,黑色颗粒为高Cr、Mo元素含量的σ相。文献[17]指出,在热加工或热处理过程中,σ相的形成通过2种相变反应机制形成:(1) 共析转变δ→σ + γ2;(2) γ→σ。其中第1种机制为主要反应机制,σ相最终在铁素体/奥氏体界面处形核,同时由于铁素体含有较多的Cr、Mo元素,在高温作用下这些元素在铁素体中扩散更快,进一步促进σ相的形核长大,σ相向铁素体内部长大的同时消耗着铁素体相,因此σ相主要存在于2个相邻奥氏体相之间,如图7a所示。然而,如图7b所示,在奥氏体内部也存在着大量黑色颗粒状σ相,这是由于在搅拌摩擦加工过程中,搅拌区受到搅拌针的搅拌作用,发生了剧烈的塑性变形,从而使奥氏体直接转变成σ相,进而直接从奥氏体相中析出,与第2种机制结果一致。
图7

图7 搅拌头转速200 r/min时2507双相不锈钢搅拌区底部析出相的SEM像
Fig.7 Low (a) and locally high (b) magnified SEM images of precipitated phase at the bottom of the stir zone of friction stir processed 2507 duplex stainless steel at tool rotation speed of 200 r/min
表1 图7b中点A~C的EDS分析 (mass fraction / %)
Table 1
Position | Cr | Ni | Mo | Fe | Possible phase |
---|---|---|---|---|---|
A | 24.89 | 7.70 | 2.28 | Bal. | γ |
B | 26.90 | 5.67 | 3.26 | Bal. | α |
C | 28.09 | 7.70 | 3.97 | Bal. | σ |
为进一步确定有无σ相的生成,对不同工艺参数下的搅拌区底部组织进行XRD表征。不同搅拌头转速下2507双相不锈钢搅拌区的XRD谱如图8所示。可以看出,搅拌头转速为200 r/min时,XRD谱中出现了与其他转速条件下不同的衍射峰,这些衍射峰分别对应σ相的(431)、(511)、(522)衍射晶面;而在搅拌头转速为300~600 r/min时,搅拌区由铁素体相和奥氏体相组成,无σ相出现。由此可见,搅拌头转速为200 r/min时,σ相在搅拌区底部存在一定量的析出。由2507双相不锈钢热力学平衡相图[18]可知,σ相的形成温度主要在500~1000℃之间,此时σ相形核的热力学倾向较大。因此,可以推测搅拌头转速为200 r/min时,搅拌区底部温度位于σ相析出温度区间,且由于加工过程搅拌头的剪切作用,原子之间扩散速率增大,从而在该区域析出一定量的σ相。当搅拌头转速增大时,热输入增大,各区域温度高于σ相析出温度区间,对σ相不敏感,因此搅拌头转速大于200 r/min时,搅拌区底部无σ相析出。通过合理控制热输入,使得加工区峰值温度规避σ相析出温度区间,可以有效避免σ相的生成。
图8

图8 不同搅拌头转速下2507双相不锈钢搅拌区的XRD谱
Fig.8 XRD spectra of the stir zone of friction stir processed 2507 duplex stainless steel at different tool rotation speeds
2.2 力学性能
不同搅拌头转速下2507双相不锈钢加工区域硬度分布如图9所示。可以看出,各参数下搅拌区的硬度分布均基本呈“盆状”,硬度值均高于母材的硬度,且显微硬度最大值位于前进侧搅拌区的底部,与文献[19]结果一致。这是由于在搅拌摩擦加工过程中,搅拌区发生了动态再结晶,晶粒发生明显细化,导致搅拌区的硬度高于母材。同时,在搅拌摩擦加工过程中,前进侧受到的搅拌头的剪切作用高于后退侧,应变速率更高,形核率增大,再结晶晶粒细化更加明显,且由于搅拌区底部组织散热较慢,冷却速率较小,晶粒来不及长大,进而使得前进侧搅拌区底部晶粒最为细小。随着搅拌头转速的增大,搅拌区的硬度呈先增大后减小的趋势,这是由于随着搅拌头转速的增大搅拌区晶粒尺寸先减小后增大。影响双相不锈钢强度和硬度的因素主要包括晶粒尺寸、铁素体与奥氏体比例及析出相等,通过前文可以看出,本工作中的相比例均在标准范围内,对搅拌区的硬度变化影响较小,且基本无析出相出现,故晶粒尺寸是本工作搅拌区强度的主要影响因素。研究[20~22]表明,晶粒尺寸越小,其强度和硬度越大。因此,前进侧搅拌区底部显微硬度具有最大值;随着搅拌头转速的增大,搅拌区显微硬度先增大后减小,对应着前文中晶粒尺寸先减小后增大的变化趋势。
图9

图9 不同搅拌头转速下2507双相不锈钢加工区域硬度分布
Fig.9 Hardness distributions of processing zone of friction stir processed 2507 duplex stainless steel at different tool rotation speeds of 200 r/min (a), 300 r/min (b), 400 r/min (c), 500 r/min (d), and 600 r/min (e)
不同搅拌头转速下2507双相不锈钢搅拌区的纵向拉伸性能如图10所示。可以看出,各参数条件下搅拌区的强度均高于母材,但延伸率降低至约为母材的一半;随着搅拌头转速的增大,搅拌区强度大致呈先增大后减小的趋势,而延伸率大致呈现先减小后增大的趋势。这是由于在加工过程中,搅拌区晶粒发生了明显细化,晶界数量增多,在一定程度上抑制了拉伸过程中的位错滑移,材料加工硬化率增大,拉伸强度增大;但晶粒细化的同时降低了晶粒内部容纳位错的能力,拉伸过程中变形不均匀性使得材料塑性降低,延伸率下降。搅拌区的拉伸性能主要与晶粒尺寸相关,晶粒尺寸越大,其强度越低,而塑性越高。当搅拌头转速为400 r/min时,搅拌区的平均晶粒尺寸最小,为1.51 μm,对应的抗拉强度达到最大值1083 MPa,而延伸率则达到最小值20.8%。
图10

图10 不同搅拌头转速下2507双相不锈钢搅拌区纵向拉伸性能
Fig.10 Longitudinal tensile properties of stir zone of friction stir processed 2507 duplex stainless steel at different tool rotation speeds
不同搅拌头转速下2507双相不锈钢拉伸试样断口形貌的SEM像如图11所示。可见,断面上均布满大量尺寸不一的韧窝和撕裂棱,说明搅拌区仍有良好的塑性。其中搅拌头转速为400 r/min时,断面主要为小尺寸韧窝,而在其他参数下韧窝相对较大,其中母材韧窝尺寸最大。这是因为晶粒尺寸的不同使得搅拌区的塑性不同,而韧窝的形貌在一定程度上与材料的塑性有关,材料的塑性越好,对应的韧窝相对越大,与延伸率的变化一致。
图11

图11 不同搅拌头转速下2507双相不锈钢断口形貌的SEM像
Fig.11 SEM images of fracture morphologies of friction stir processed 2507 duplex stainless steel at different tool rotation speeds of 200 r/min (a), 300 r/min (b), 400 r/min (c), 500 r/min (d), and 600 r/min (e) and BM (f)
2.3 腐蚀行为
母材和不同搅拌头转速下2507双相不锈钢搅拌区表面极化曲线如图12所示,其特征值如表2所示。可以看出,不同参数下极化曲线形状相似,均分为活化区、钝化区和过钝化区,其中钝化区间较大,其值约为1.5 V,说明搅拌区材料耐蚀性良好。前文表明,搅拌区铁素体与奥氏体比例变化不大,且基本无析出相,故搅拌区的耐蚀性主要受该区域晶粒尺寸的影响。在实验参数条件下,除搅拌头转速为200 r/min外,搅拌区的自腐蚀电压相对于母材均正向偏移,自腐蚀电流减小,且点蚀电位升高,说明搅拌区的耐蚀性能优于母材。当搅拌头转速为400 r/min时,搅拌区维钝电流最小,且点蚀电位相对较高,说明其具有优良的耐蚀性。搅拌头转速为400 r/min时,搅拌区晶粒细化最为明显,晶粒的细化有利于更多的Cr3+通过晶界向表层扩散,提高了钝化膜的厚度和致密性,从而降低材料表面的腐蚀速率,提高了材料表面的耐蚀性[23~26]。总之,在不同搅拌头转速条件下搅拌区细化的晶粒有利于表面耐蚀性的提高。
图12

图12 母材和不同搅拌头转速下2507双相不锈钢搅拌区表面极化曲线
Fig.12 Surface polarization curves of base material and stir zone of friction stir processed 2507 duplex stainless steel at different tool rotation speeds (E—potential, i—current density)
表2 不同搅拌头转速下搅拌区表面极化曲线特征值提取
Table 2
Sample | Ecorr / V | icorr / (10-7 A·cm-2) | ipass / (10-5 A·cm-2) | Epit / V |
---|---|---|---|---|
BM | -0.59 | 8.26 | 1.94 | 1.09 |
200 r·min-1 | -0.73 | 4.45 | 1.04 | 1.12 |
300 r·min-1 | -0.40 | 5.60 | 0.97 | 1.11 |
400 r·min-1 | -0.53 | 2.72 | 0.68 | 1.18 |
500 r·min-1 | -0.55 | 1.93 | 0.93 | 1.20 |
600 r·min-1 | -0.60 | 2.95 | 1.08 | 1.21 |
母材和不同搅拌头转速下2507双相不锈钢搅拌区在3.5%NaCl溶液中的EIS如图13所示。Nyquist图各曲线均表现为未完成的容抗弧,不同搅拌头转速下搅拌区的容抗弧半径随着搅拌头转速的增大先增加后减小,但均大于母材。容抗弧半径与表层钝化膜的电荷转移电阻相关,其半径越大,电荷转移电阻越大,抵抗外加扰动的作用越强,耐蚀性能越好。这说明搅拌区的耐蚀性能优于母材,且随着搅拌头转速的增大先增加后减小,对应着晶粒尺寸先减小后增大的变化趋势。当搅拌头转速为400 r/min时,容抗弧半径最大,说明对应的搅拌区耐蚀性最好。这是由于搅拌头转速为400 r/min对应的晶粒发生了明显的细化,晶界密度增大,降低了Cr元素向表面扩散的难度,材料的耐蚀性得到提升。Bode图各参数下对应的曲线形状相似,说明各试样电极反应机理未发生明显的变化,且阻抗模值的变化规律与容抗弧半径的变化一致。
图13
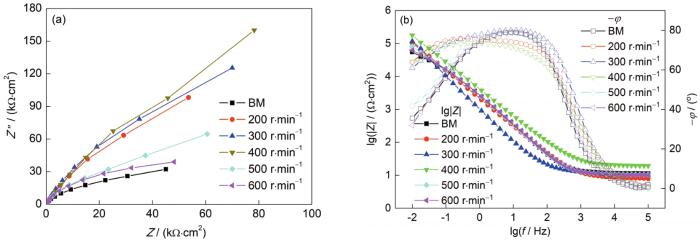
图13 母材和不同搅拌头转速下2507双相不锈钢搅拌区EIS
(a) Nyquist (b) Bode
Fig.13 Electrochemical impedance spectroscopies of base material and stir zone of friction stir processed 2507 duplex stainless steel at different tool rotation speeds (Z—real part of impedance, Z''—imaginative part of impedance, f—frequency, φ—phase angle)
3 结论
(1) 随着搅拌头转速的增加,2507双相不锈钢搅拌区晶粒尺寸呈现先减小后增大的趋势。搅拌摩擦加工过程对铁素体与奥氏体比例影响不大,各区域两相比例均处于40%~60%标准范围内。仅在搅拌头转速为200 r/min时,在加工区底部发现σ相析出。
(2) 2507双相不锈钢搅拌摩擦加工区显微硬度分布呈现“盆状”,其晶粒尺寸越细小,显微硬度越高,且在前进侧搅拌区下方达到最高值。搅拌区纵向拉伸强度要优于母材,但延伸率有所下降;且随着晶粒尺寸的减小,搅拌区拉伸强度增加,延伸率下降。
(3) 晶粒的细化使得表层钝化膜稳定性、致密性和再钝化性能增强,搅拌区表面的耐蚀性要优于母材
来源--金属学报