分享:基于飞秒激光时域热反射法的微尺度Cu-Sn金属间化合物热导率研究
周丽君1,2, 位松1,2,3, 郭敬东,1,2, 孙方远
,4, 王新伟5, 唐大伟5
1.
2.
3.
4.
5.
利用双波长飞秒激光时域热反射系统对微尺度Cu-Sn金属间化合物的热输运性能开展研究。利用回流与时效工艺制备Cu-Sn扩散偶,界面处生成均匀连续的Cu6Sn5和Cu3Sn金属间化合物,材料厚度均在微米量级且Cu6Sn5的(001)晶面具有明显的择优取向特征。由于实验参数对待测参量的敏感度会影响拟合精度,重点分析了铝传感层厚度与加热光调制频率对金属间化合物热导率测量敏感度的影响,以选定具体的实验参数。经测试,Cu6Sn5和Cu3Sn的热导率分别为47.4和87.6 W/(m·K),均略高于已有研究报道,分析认为主要是由于样品制备技术不同而导致的材料微观结构差异所致。讨论了加热光斑尺寸、铝传感层厚度及材料比热容的不确定性对热导率测量误差的影响,得到Cu6Sn5热导率误差为-6.8%~4.6%,Cu3Sn热导率误差为-7.1%~4.4%。本工作表明飞秒激光时域热反射技术在电子封装微尺度金属间化合物热输运特性研究方面具备适用性,所得实测数据对于电子封装热设计及可靠性评价有重要参考意义。
关键词:
近年来,随着电子封装技术逐渐向高密度、高频率和高速率的方向发展,双列直插封装、四方扁平封装、针栅/球栅阵列封装等传统封装技术愈发难以满足应用要求。在这种背景下,以芯片堆叠为主要特征的三维封装成为一种极具前景的封装技术[1~3]。在三维封装中,应用于芯片叠层的微连接技术最为关键,关系到芯片的高性能运算与长期可靠服役。目前,常见的微连接技术包括:钎焊连接、热压键合、黏接键合、超声波键合和瞬时液相键合等[1,4]。传统焊点结构以焊料成分为主,焊料与基板之间仅有一薄层金属间化合物(intermetallic compound,IMC);与传统连接技术不同,三维封装中微互连焊点的尺寸已经缩小到20 μm以下,焊点结构以金属间化合物为主,大部分或全部的焊料均已转化为金属间化合物[3,4]。考虑到微互连焊点在芯片与焊盘的电气和机械连接,以及作为散热通道实现芯片热量耗散等方面发挥着重要作用,焊点尺寸持续缩小所造成的焊点结构变化给电子封装行业带来了许多新的挑战。
在电子封装热设计方面,掌握准确的材料热输运参数是实现温度场精准预测的重要保障;然而,当前微互连焊点中金属间化合物的热输运参数严重缺失,严重影响电子封装结构的温度场与热应力分析预测[5,6]。出现这种情况的原因在于,常规材料热导率分析测试方法,如稳态热流法[7,8]、激光闪测法[9,10]或瞬态平面热源法[11,12]等,均要求样品具有毫米量级以上尺寸,难以用于微尺度材料的热输运特性评价,因此关于微互连焊点中金属间化合物热输运参数的研究鲜见报道。尽管少量研究采用惰性气体雾化技术制备金属间化合物粉体,再借助热静压粉体成型法得到大尺寸金属间化合物块体[13,14],以满足常规方法的分析测试需求;但是,在晶粒尺寸、数量、取向及缺陷等微观结构信息方面,基于上述粉末冶金技术获得的金属间化合物与实际情况下通过界面反应获得的金属间化合物存在巨大差异,而材料热输运特性对微观结构变化十分敏感,因此有必要加强面向微米乃至纳米尺度金属间化合物热输运特性的测量方法研究。
飞秒激光时域热反射法(time-domain thermoreflectance,TDTR)是一种较为前沿的材料热输运特性研究手段,其原理为:利用一束超快脉冲激光加热待测材料,引发材料表面温度和反射率发生变化,再借助另外一束延迟时间可调控的脉冲激光探测材料表面反射率的实际变化情况,然后将实验采集数据与理论计算数据对比,通过调整理论模型的待测参量使2者差异最小化,最终得到待测材料热物性参数。TDTR技术具有测试影响因数少、所需样品尺寸小、数据准确度高等优点,现已应用于电子声子耦合机理[15,16]、薄膜导热特性测量[17,18]、材料界面热阻评价[19~21]等方面的相关研究。本工作自主搭建TDTR测试平台并针对电子封装中微尺度金属间化合物的热导率开展细致研究。
目前,应用于芯片叠层微连接的材料体系包括Cu-Sn[22]、Cu-In[23]、Ag-Sn[24]、Au-In[25]、Ni-Sn[26]等,其中Cu-Sn体系具有生产工艺成熟、键合效率高和经济性良好等优点,因而应用领域最为广泛。而随着三维封装及异构集成中微互连焊点尺寸缩小至微米尺度,实际Cu-Sn体系焊点结构以Cu6Sn5、Cu3Sn金属间化合物为主[4,22],锡基焊料已经消耗殆尽,为此本工作采用Cu6Sn5和Cu3Sn作为研究对象,分析讨论TDTR技术在电子封装微尺度金属间化合物热导率研究方面的适用性,以期为电子封装热设计及可靠性评价提供一定的参考与指导。
1 实验方法
1.1 TDTR实验系统
对于金属材料而言,表面反射率与温度近似成线性关系[18,20],TDTR系统正是利用这一现象分析材料热输运特性。TDTR系统采用钛宝石激光器作为光源,激光波长800 nm,脉冲宽度约100 fs,重复频率80 MHz。一束激光经过光隔离器、1/2波片和偏振分光器后分离为2束相互垂直的激光,利用竖直偏振激光作为加热光,水平偏振激光作为探测光。其中,加热光经过电光调制器后转化为特定频率的方波或正弦波,利用光电探测器监控实际调制情况。然后,利用三硼酸铋(BiB3O6)晶体使加热光频率加倍得到400 nm波长蓝光,需使用滤光片滤除原有800 nm波长红光。另外,探测光经过偏振分光器进入机械延迟平台,在此之前使用扩束器将激光直径放大3.3倍,以防激光在传播过程中光斑尺寸发生变化进而对测量信号产生影响。接着,使用冷光镜将加热光与探测光合为一束,经过10倍物镜聚焦于样品表面。最后,使用1/4波片将携带样品表面温度信息的探测光分离出来,经过偏振分束器的完全反射,利用平凸透镜将探测光聚焦于感应探测器,配合锁相放大器实现信号的采集与分析。值得注意的是,在光电探测器前放置蓝光滤光片,能够有效规避加热光的干扰;此外,需通过反射镜将光线传导至电荷耦合器件相机,以便进行样品表面质量及加热光与探测光重合度的观察。TDTR实验系统示意图如图1所示。
图1
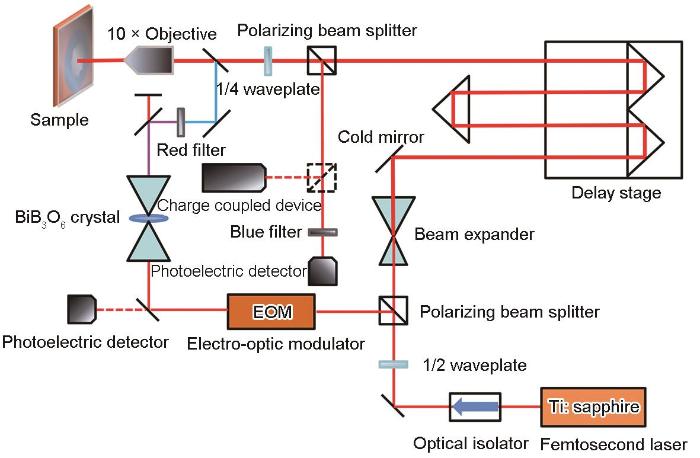
图1 飞秒激光时域热反射(TDTR)实验系统示意图
Fig.1 Schematic of femtosecond laser time-domain thermoreflectance (TDTR) system
1.2 样品制备与表征
本工作采用高纯电解Cu与纯Sn颗粒(纯度99.99%)作为Cu-Sn金属间化合物制备原料。首先,将铜块切为直径6 mm、厚度3 mm的圆柱体,经过研磨与抛光使铜块表面呈现镜面,再使用无水乙醇和10%H2SO4 (质量分数)除去油污和氧化膜,去离子水洗净待用;然后,采用精密电子天平称取锡粒50 mg,在铜块表面涂抹适量的松香助焊剂,并将锡粒置于铜块上表面;接着,设定回流峰值温度为275℃,将上述样品放入回流炉中,使锡粒在铜块表面发生重熔、铺展及界面反应;继而,将样品置于恒温炉中,200℃时效处理120 h,促进金属间化合物继续生长;之后,利用研磨抛光工艺除去样品表面的纯Sn金属,露出铜块表面的微尺度Cu-Sn金属间化合物;最后,采用电子束蒸镀法在样品表面制作铝膜作为传感层,以获得良好的光热反射信号。
采用Supra 55场发射扫描电子显微镜(SEM)观察金属间化合物微观形貌,利用配套的能谱分析仪(EDS)检测材料元素成分,利用背散射电子衍射仪(EBSD)获得晶体取向信息,使用D/MAX2400 X射线衍射仪(XRD)进行金属间化合物物相鉴定,最后采用自主搭建的TDTR实验系统分析测试Cu-Sn金属间化合物的热输运特性。
1.3 热输运模型
TDTR测试系统锁相放大器采集的有效信号Z(ωo)为:
式中,β为传感层的光热反射系数,Qpump和Qprobe分别为单个加热激光脉冲和探测激光脉冲的能量,T为激光脉冲间隔,ωo和ωs分别为调制频率和采样频率,τ为加热激光相对于抽运激光的延迟时间,m为任意整数。H(ω)为频域下材料对单位能量脉冲加热的响应:
式中,Rpump和Rprobe分别为加热激光和探测激光在材料表面的光斑半径;ω为频率;k为积分变量;C(ω)和D(ω)为样品传递矩阵的2个子项,包含样品热物性信息的参数,详细推导见文献[27,28]。在特定测量频率ωo下,假定C和D已知,则可以通过H(ω)和Z(ωo)计算得到与实验测量信号对应的理论模拟信号,通过拟合C和D可以最终得到待测量样品的相关热物性参数。
2 实验结果与讨论
2.1 材料微观结构
考虑到材料的热输运特性对微观结构十分敏感,本工作模拟电子封装钎焊连接技术并利用回流与时效工艺制备样品,得到与实际产品类似的微尺度金属间化合物,进而开展材料显微组织、元素成分、物相种类及晶粒取向等研究。Cu-Sn扩散偶界面处微观结构的SEM像、EDS分析和XRD谱如图2所示。SEM像显示界面附近从上到下依次为纯Sn焊料、反应区域和纯Cu基板,其中界面反应区域存在2层金属间化合物(图2a)。根据EDS和XRD分析结果,能够判断2层金属间化合物分别为Cu6Sn5和Cu3Sn (图2b和c)。可以看出,Cu6Sn5层平均厚度为4.2 μm,Cu3Sn层平均厚度为5 μm,常规材料热导率分析测试方法难以胜任这种微尺度材料的热输运特性评价。纯Sn焊料与纯Cu基板的反应符合多元体系热力学与动力学[2,22],在回流过程中重熔的纯Sn焊料与纯Cu基板发生接触,由于原子浓度梯度的存在,Cu原子迅速地溶解于纯Sn焊料,从而在界面处达到非常高的浓度。然后,过多的Cu原子会在Cu基板处析出,纯Sn焊料中Cu原子减少至亚稳态溶解度状态。在亚稳态溶解度下,因为Cu、Sn原子之间具有很大的化学反应驱动力,Cu6Sn5以异质形核方式形成于纯Sn焊料与Cu基板界面处。另外,根据Cu-Sn二元相图[29],Cu3Sn金属间化合物也会同时出现。在时效过程中,一方面Cu原子会与Sn原子继续反应生成Cu6Sn5,另一方面Cu原子会与Cu6Sn5反应生成Cu3Sn,随着界面反应进行,金属间化合物晶粒的尺寸逐渐变大而数量逐渐减少,但是反应速率相较于回流时大为降低,而且在回流过程中形成的不同形貌的金属间化合物逐渐转变为层状结构。
图2
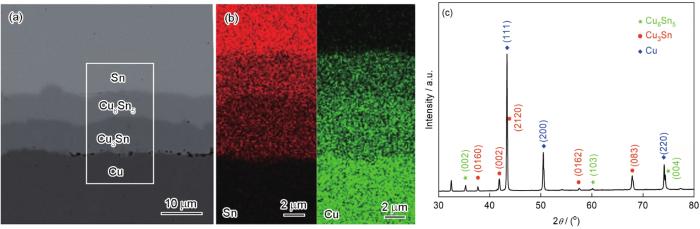
图2 Cu-Sn扩散偶界面处微观结构的SEM像、EDS分析及XRD谱
Fig.2 Microstructure analyses of the interface for Cu-Sn diffusion couple specimens
(a) SEM image of microstructure
(b) EDS element maps of square region in Fig.2a
(c) XRD spectrum of Cu-Sn specimen
通过EBSD技术获取材料晶粒取向信息,有利于深入了解金属间化合物的结构特点。根据上文XRD分析结果可知,Cu6Sn5为hcp结构(空间群:P63/mmc),Cu3Sn为单斜结构(空间群:Cmcm),据此在EBSD系统中选择合适的材料晶体结构以便分析。图3为Cu6Sn5的晶粒取向分布情况。可以看出,Cu6Sn5晶粒分布较为均匀,平均晶粒尺寸约为10 μm (图3a和b)。另外,在轧向(rolling direction,RD)与横向(transverse direction,TD)平面垂直方向,Cu6Sn5晶粒颜色较为一致,说明Cu6Sn5晶粒在该方向取向相近,可能存在织构(图3c)。为进一步分析Cu6Sn5晶粒取向特点,通过EBSD数据处理获得Cu6Sn5的极图(图3d~f)。可以看出,在(001)极图中,Cu6Sn5取向主要分布在极射赤道面圆心附近,说明Cu6Sn5的(001)晶面存在明显的择优取向特征,且(001)晶面垂直于RD-TD平面。根据EBSD系统试样坐标系与晶体坐标系之间的关系,可知Cu6Sn5的(001)晶面倾向于垂直Cu-Sn扩散偶界面。已有研究[30]也发现了类似现象,其原因可能是Cu6Sn5的(001)晶面表面能较低,在界面反应过程中能够稳定生长。另外,在(100)极图和(301)极图中,Cu6Sn5取向分布散漫,不存在明显的择优取向分布。图4为Cu3Sn的晶粒分布及取向情况。可以看出,Cu3Sn晶粒分布较为均匀,平均晶粒尺寸约为1 μm (图4a~c);在(001)、(100)和(301)极图中,Cu3Sn晶粒取向分布散漫,整体密度很低,不存在明显织构(图4d~f)。
图3
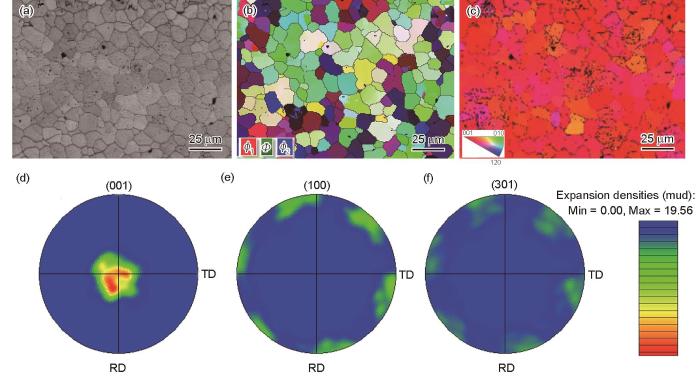
图3 Cu6Sn5晶粒取向分布情况
Fig.3 Orientation distributions of Cu6Sn5 grains
(a) band contrast image (b) Euler color image (?1, Φ, ?2—Euler angles)
(c) orientation color image perpendicular to RD-TD plane (RD—rolling direction, TD—transverse direction)
(d) (001) pole figure (e) (100) pole figure (f) (301) pole figure
图4
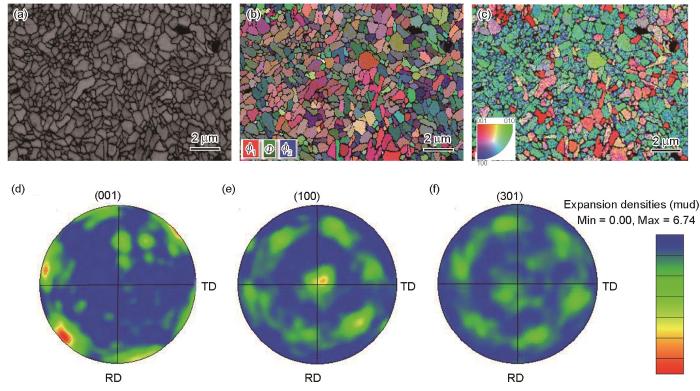
图4 Cu3Sn晶粒取向分布情况
Fig.4 Orientation distributions of Cu3Sngrains
(a) band contrast image (b) Euler color image
(c) orientation color image perpendicular to RD-TD plane
(d) (001) pole figure (e) (100) pole figure (f) (301) pole figure
2.2 测试敏感度分析
TDTR方法是通过调整热输运理论模型中的待测参量,借助最小二乘法拟合实现理论数据与实验数据差异最小化,进而获取待测物质的热物性参数。实验参数对待测参量的敏感度将会影响拟合精度,即待测参量的敏感度越高,则拟合结果误差越小。本工作中锁相放大器采集信号对被测参量的敏感度决定了结果准确度,测试敏感度的数学表达式为[31]:
式中,x为待拟合参数,Y为锁相放大器采集信号,Sx 为采集信号Y对x的敏感度(Sx 为幅值信号、相位信号或复数信号)。考虑到TDTR测试过程中可调实验参量为铝传感层厚度和加热光调制频率,本工作主要分析这2项参量对Cu6Sn5和Cu3Sn热导率测量敏感度的影响。
图5为铝传感层厚度和加热光调制频率对Cu6Sn5和Cu3Sn热导率测量所得相位信号敏感度的影响。可见,在绝大部分测试延迟时间段,铝传感层厚度越大则TDTR相位信号的敏感度越高(图5a和b),因此应尽可能选择更厚的铝传感层以获得更高的材料热导率测量敏感度,但是在电子束蒸镀工艺中增加铝传感层厚度容易使样品表面变得粗糙,从而导致实际测量信号信噪比降低,所以本工作最终选择厚度为100 nm的铝传感层。另外,在整个测试延迟时间段,加热激光调制频率越高则TDTR相位信号的敏感度越高(图5c和d),因此应尽可能选择更高的加热光调制频率,但是TDTR系统可用调制频率受到许多其他因素的制约,例如光电探测器带宽、高频电磁噪声等,所以本工作最终选择调制频率为5 MHz的加热脉冲激光。
图5
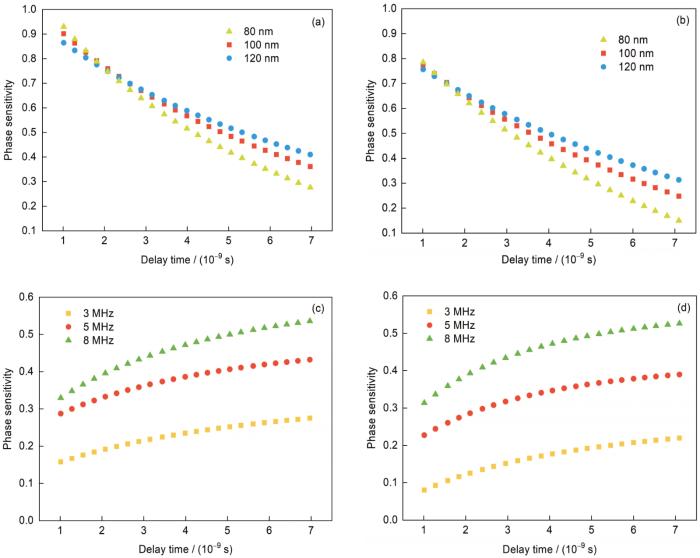
图5 铝传感层厚度和加热光调制频率对Cu6Sn5和Cu3Sn热导率测量所得相位信号敏感度的影响
Fig.5 Influences of aluminum transducer thickness (a, b) and pump laser modulation frequency (c, d) on phase signal sensitivity in thermal conductivity measurement for Cu6Sn5 (a, c) and Cu3Sn (b, d)
2.3 测试结果与分析
常温下Cu6Sn5和Cu3Sn热导率的相位与幅值信号实际测量数据与理论拟合曲线如图6所示。可见,实验测量数据与理论拟合数据吻合良好,最终拟合得到室温下微尺度Cu6Sn5和Cu3Sn金属间化合物的热导率分别为47.4和87.6 W/(m·K)。根据已有研究,通过粉末冶金技术制备的Cu6Sn5和Cu3Sn热导率分别为34.1和70.4 W/(m·K)[14]。与之相比,本工作中Cu6Sn5热导率测量值高约39.0%,Cu3Sn热导率测量值高约24.4%,这是由于样品制备技术不同而直接导致的材料微观结构差异所致。利用粉末冶金技术制备的块体金属间化合物内部存在大量孔隙缺陷,这些孔隙缺陷会引发严重的声子电子散射;而根据上文对材料微观结构的观察与分析,发现采用回流与时效技术模拟真实工艺得到的材料内部缺陷较少,因此本工作中微尺度Cu-Sn金属间化合物具有更为优异的热导率。此外,本工作制备的Cu6Sn5金属间化合物(001)存在择优取向,且(001)垂直于材料热导率测试方向;考虑到Cu6Sn5为hcp晶体结构,各项性质均具有强烈的各向异性,故推测在Cu6Sn5在(001)垂直方向的热导率远高于其他位向。
图6

图6 Cu6Sn5和Cu3Sn热导率测量的相位与幅值信号实验数据与理论拟合曲线
Fig.6 Experimental data of thermal conductivity measurement and the fitting curves of phase angle signal (a, b) and amplitude signal (c, d) for Cu6Sn5 (a, c) and Cu3Sn (b, d)
2.4 测试误差分析
采用TDTR技术测量微尺度Cu-Sn金属间化合物热导率的误差主要来源于以下物理量的不确定性:激光光斑尺寸、铝传感层厚度及测试材料比热容,本节主要分析这些因素对材料热导率测量误差的影响。
本工作使用扫描狭缝式光束质量分析仪测量激光光斑尺寸,测试得到加热激光和探测激光的光斑直径分别为36和26 μm。在相同的不确定度条件下,加热激光的光斑直径不确定度对测量误差的影响大于探测激光。考虑到光束质量分析仪的测量精度为1 μm,将加热光斑直径上下浮动5 μm (5倍测试精度),观察拟合曲线的变化情况。图7a中实线和虚线分别对应Cu6Sn5和Cu3Sn测量信号的最佳拟合曲线,圆圈和三角分别为加热光斑直径上下浮动5 μm对拟合曲线的变化情况。可见,加热光斑直径的误差对拟合曲线的影响非常微小,并且小于实验信号的噪声。
图7
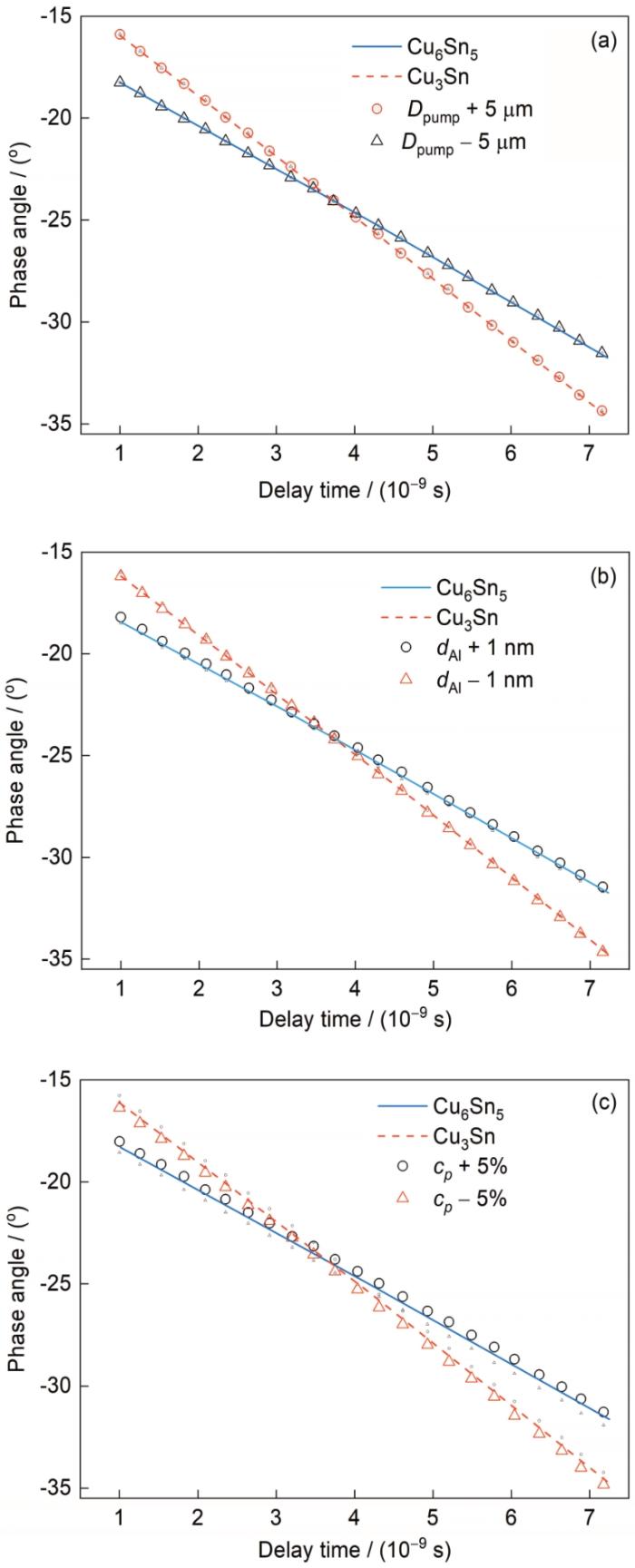
图7 加热光斑直径、铝传感层厚度和材料比热容对Cu6Sn5和Cu3Sn热导率测量结果的影响
Fig.7 Influences of pump laser diameter (Dpump) (a), aluminum transducer thickness (dAl) (b), and material specific heat (cp ) (c) on thermal conductivity measurement for Cu6Sn5 and Cu3Sn
本工作采用皮秒回声定位法测量铝传感层的厚度,测量精度为±1 nm,将铝传感层厚度上下浮动1 nm,观察拟合曲线的变化情况。图7b中实线和虚线分别对应Cu6Sn5和Cu3Sn测量信号的最佳拟合曲线,圆圈和三角分别为铝传感层厚度上下浮动1 nm对拟合曲线的变化情况。可见,传感层厚度误差对拟合曲线的影响非常微小,这是由于铝金属的传热特性较好所致。
本工作中Cu6Sn5和Cu3Sn比热容参考文献[14],Cu6Sn5的比热容误差为-2.1%~4.2%,Cu3Sn的比热容误差为-1.2%~4.1%。将Cu6Sn5和Cu3Sn比热容上下浮动5%,观察拟合曲线的变化情况。图7c中实线和虚线分别对应Cu6Sn5和Cu3Sn测量信号的最佳拟合曲线,圆圈和三角分别为比热容上下浮动5%对拟合曲线的变化情况。可以看出,比热容的变化使得相位信号产生明显的偏差,表明比热容的测量误差对实验数据的拟合结果有较大影响。
为了确认本工作测量数据的最大误差,针对Cu6Sn5和Cu3Sn的比热容误差(Cu6Sn5:+4.2%、-2.1%;Cu3Sn: +4.1%、-1.2%)、铝传感层测量精度(±1 nm)及加热光斑直径测量精度(±1 μm)调整对应参数,对实验数据进行拟合计算,以确认各项参数最大偏差值对测试结果造成的影响,进而得出误差范围。Cu6Sn5和Cu3Sn的热导率拟合计算结果及误差统计分别列于表1和2。可见,比热容误差、铝传感层测量精度及加热光斑直径测量精度对Cu6Sn5热导率的影响分别为-4.0%~2.1%、-1.8%~1.5%和-0.4%~0.4%,实验测量的随机误差为±0.6%,得到Cu6Sn5的热导率误差范围为-6.8%~4.6%。比热容误差、铝传感层测量精度及加热光斑直径测量精度对Cu3Sn热导率的影响分别为-4.0%~1.3%、-1.5%~1.5%和-0.2%~0.2%,实验测量的随机误差为±1.4%,得到Cu3Sn的热导率误差范围为-7.1%~4.4%。
表1 Cu6Sn5热导率拟合计算结果及误差统计 (W·m-1·K-1)
Table 1
Item | Raw data | 4.2% (cp ) | -2.1% (cp ) | 1 nm (dAl) | -1 nm (dAl) | 1 μm (Dpump) | -1 μm (Dpump) |
---|---|---|---|---|---|---|---|
Error | ±0.6% | -4.0% | 2.1% | 1.5% | -1.8% | 0.4% | -0.4% |
1 | 47.0 | 45.1 | 48.0 | 47.7 | 46.3 | 47.2 | 46.8 |
2 | 47.7 | 45.8 | 48.7 | 48.4 | 46.9 | 47.8 | 47.5 |
3 | 47.5 | 45.7 | 48.5 | 48.2 | 46.8 | 47.7 | 47.4 |
Mean | 47.4 | 45.5 | 48.4 | 48.1 | 46.7 | 47.6 | 47.2 |
表2 Cu3Sn热导率拟合计算结果及误差统计 (W·m-1·K-1)
Table 2
Item | Raw data | 4.1% (cp ) | -1.2% (cp ) | 1 nm (dAl) | -1 nm (dAl) | 1 μm (Dpump) | -1 μm (Dpump) |
---|---|---|---|---|---|---|---|
Error | ±1.4% | -4.0% | 1.3% | 1.5% | -1.5% | 0.2% | -0.2% |
1 | 89.3 | 85.7 | 90.4 | 90.7 | 88.0 | 89.5 | 89.1 |
2 | 87.1 | 83.6 | 88.2 | 88.4 | 85.8 | 87.3 | 86.9 |
3 | 86.5 | 83.0 | 87.5 | 87.8 | 85.2 | 86.7 | 86.3 |
Mean | 87.6 | 84.1 | 88.7 | 89.0 | 86.3 | 87.8 | 87.4 |
3 结论
(1) 采用回流和时效方法制备了Cu6Sn5和Cu3Sn薄膜,2种金属间化合物晶粒均呈等轴晶分布,其中Cu6Sn5晶粒尺寸约为10 μm,且(001)晶面具有明显的择优取向特征,Cu3Sn晶粒尺寸约为1 μm,晶粒取向分布散漫,不存在明显织构。
(2) 利用TDTR方法测量了Cu6Sn5和Cu3Sn的热导率,其中Cu6Sn5的热导率为47.4 W/(m·K),误差为-6.8%~4.6%,Cu3Sn的热导率为87.6 W/(m·K),误差为-7.1%~4.4%。
(3) TDTR技术具有测试影响因数少、所需样品尺寸小、数据准确度高等优点,适用于电子封装微尺度金属间化合物的热输运特性研究。
来源--金属学报