分享:SA210C无缝中碳钢管带状组织的评定方法
蔡 煜,张 伟,戴敏明,葛 强
(江苏常宝普莱森钢管有限公司,常州 213200)
摘 要:在锅炉厂的产品验收工作中,锅炉和过热器用 SA210C 无缝中碳钢管带状组织的评定比较重要.但 GB/T13299-1991中对带状组织评级的描述比较模糊,实际应用存在困难,试验结果为界限值时易出现争议.而 ASTM E1268-01(2016)的方法尽管计算复杂,但能够定量评定材料的带状程度,在遇到争议时使用该方法可有效减少误判.SA210C为 ASME(美国机械工程师学会)钢种,在实际工作中选用 ASTM E1268-01(2016)作为检验标准更为准确.但考虑到推广困难,可在日常工作中采用先依据 GB/T13299-1991 对带状组织进行评级,遇到争议时再依据ASMEE1268-01(2016)进行验证的方法.
关键词:SA210C钢管;带状组织;评定方法;GB/T13299-1991;ASTM E1268-01(2016)
中图分类号:TG115.2 文献标志码:A 文章编号:1001G4012(2017)05G0322G03
在锅炉和过热器用 SA210C 无缝中碳钢管中,带状组织是一种常见的显微组织,表现为铁素体与珠光体沿变形方向交替成条带分布.带状组织的存在会使钢的组织不均匀,形成各向异性,降低钢材的塑性和韧性.因此锅炉厂在技术条件中规定了带状组织级别,按照 GB/T13299-1991«钢的显微组织评定方法»[1](以下简称国标),选取最严重的视场采用与标准图片比对的方法进行评级,但这种方法受人员主观影响较大,重复性与再现性大于1级,容易出现争议,尤其是当评定结果在界限值的时候.ASTM E1268-01(2016)Standard Practicefor Assessing the Degree of Banding orOrientationof Microstructures[2](以下 简 称 美 标)也对带状组织的评级方法进行了规定,该标准运用类似晶粒度评定中的截点法及数理统计的方法,来实现钢中带状组织级别的定量评级.笔者依据该标准对SA210C热轧无缝中碳钢管中的带状组织级别进行了评定,并与使用国标评定的结果进行了对比,以此给锅炉厂的验收工作提供参考.
1 美标评定带状组织级别
1.1 视场及网格线的选择
在实际检验中发现,SA210C 钢管内壁的带状组织比较严重,因此在视场选择过程中可以在内壁选择5~6个视场.以 SA210C 钢管内壁的其中一个视场进行分析,如图1所示,可以看出铁素体(白亮区)与珠光体两相呈明显的带状分布.
图1中的网格是利用ZEISSImager.A2M 型金相显微镜的晶粒度评级软件功能得到的,平行线与垂直 线 的 间 距 一 致,长 度 均 为 780 μm ×13=10140μm,即实际测试线的总长度为 20.28 mm.
显微形貌 放 大 倍 数 为 100 倍,即 测 试 线 的 长 度 为2028mm,满 足 标 准 中 网 格 线 总 长 度 不 小 于500mm的要求.可根据试样的实际情况改变放大倍数,对于较细的晶粒建议可在放大200倍下进行分析,但不建议使用更高的放大倍数,会导致测量线穿过的晶粒或块状物数量偏少,而加大测量误差.
1.2 计数规则
ASTM E1268-01(2016)中使用测试线截取显微组织的特征物数(N,即网格线所截取的独立颗粒、晶粒或碎片的个数)和特征物交点数(P,即网格线所截取的异相边界和连续边界的交点数)的示意图如图2所示,图2(a)代表垂直于变形方向,图2(b)代表平行于变形方向.T 代表网格线与特征物相切,E代表网格线结束于网格内.由于实际应用中计算交点数的工作量很大,失误也会很多,因此该分析以计数 N 为例.N 的计数规则有以下4点:①如果测试网格线。
穿过两个或多个连续的颗粒、晶粒或相(穿过的颗粒间无任何其他的相或组分),则将它们计为一个特征物(N=1);②当测试线与颗粒、晶粒相切时,N 计为0.5;③当测试线末端在特征物内时,N 计为0.5;④当测试线完全在特征物内时(此情况经常发生在严重带状材料中),N 计为0.5.
1.3 计算结果
根据上述规则对图1中的特征物珠光体进行计数,选择珠光体为特征物的主要原因是珠光体比铁素体少,计数方便.垂直线截取特征物(珠光体)的截段数总和 N⊥ =506个,平行线截取特征物(珠光体)的截段数总和 N∥ =160个,计算垂直和平行方向 单 位 长 度 上 的 特 征 物 数 量 NL⊥ 及 NL∥ ,即NL⊥ =N⊥/Lt=506/10.14=49.90个/mm,NL∥ =N∥/Lt=160/10.14=15.78个/mm,Lt 为实际测试线长度10.14mm,从而计算出各向异性指数(带状级别)AI=NL⊥/NL∥ =49.90/15.78=3.16.其余视场(共选择5个视场进行测量)计算同上,相应参数如表 1 所 示,其 中 S 为n 次 测 量 的 标 准 偏 差,95%CI 为95%置信区间,RA 为相对精度,SB⊥ 为带状或趋向性相的平均带宽,计算方法见式(1)~(3).相对精度RA 是对受视场影响的数值每次测量误差的评价,RA ≤30%为适当值,否则需要增加测量次数来降低RA.
2 美标与国标评定结果的对比
对于图1,选取最严重的视场与国标中的标准图谱进行比对,如图3所示.从图3可以看出,贯穿视场的铁素体 珠光体条带较多,但铁素体并没有变形,说明该样品的带状级别小于4级,其珠光体为连续析出.在钢管轧制过程中铁素体沿变形方向呈方向性排列,按照国标根据变形铁素体的含量以及贯穿视场的程度来评级,没有变形铁素体则可以评为3级.但如果与标准图谱比对,可直观看出该视场的带状组织比3级标准图谱中的严重,也可判定为3.5级.如果某采购规程要求带状≤3.0级,则0.5级的差别就会引起争议,造成产品不合格,不能及时流转.从上述分析可看出,国标是对带状组织进行定
性分析,主要考虑带状贯穿视场的程度,3级的描述为等轴晶粒组成几条连续的、贯穿视场的铁素体 珠光体交替带.在标准图片的阐述方面比较含糊,并且实际试样的铁素体与珠光体含量与图谱的并不完全相同,会导致视觉误差,从而影响判断.引入美标可进行辅助判定,是一种定量判断.美标经过数理统计分析,降低了国标中人为评定引入的误差,得到的结果较国标的要精确,具有较高的科学性,尤其对于评定处于界限值的带状组织很有帮助.但该方法的计算量较大,比较耗时.上述案例根据美标进行评定,该试样其中一个视场的带状级别为3.2,且最终5个视场的平均级别为 3.16 级,由于结果大于3.0级,最终按照采购规程可判定该批产品不合格.
3 美标评定结果的准确性
为了验证美标评定结果的准确性,选取国标中的4级标准图谱按照上述方法进行评定,结果如表3所示,可见使用美标计算带状级别的准确性较高.
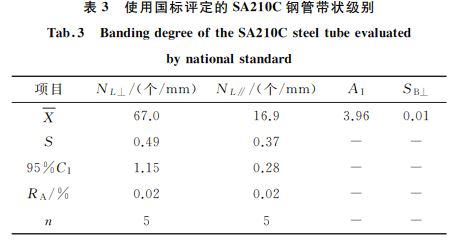
3.2 皮下夹杂的危害
皮下夹杂对轴承钢的危害主要体现在使轴承滚动体出现接触疲劳继而失效.接触疲劳的破坏过程为疲劳裂纹的萌生、扩展直至剥落[3].钢材内部存在皮下夹杂,处于表层下的最大动态切应力处,就会成为疲劳裂纹的起源而形成裂纹,继而扩展至表面,形成剥落.疲劳裂纹的扩展一般可分为3个阶段:第一阶段,从裂纹的萌生到形成可以自由扩展的裂纹尺寸;
第二阶段,裂纹扩展到可以形成剥落源;第三阶段,裂纹迅速扩展,第一个剥落产生.而皮下夹杂缺陷在应力作用下,已形成裂纹源,在滚动体工作时受到切应力的作用将会出现裂纹扩展,后续形成剥落失效.因而皮下夹杂缺陷直接影响着轴承的使用寿命,存在该缺陷的轴承滚动体,使用寿命将会大幅降低.
3.3 皮下夹杂的控制
从化学成分已判定出该模铸轴承钢的皮下夹杂缺陷是由模铸保护渣引起的.保护渣在浇铸过程中与钢液直接接触,通常由于保护渣的质量较轻,应浮在钢液的表面上.而皮下夹杂缺陷是由于保护渣被卷入至钢液中,未能有效排出引起,因此需控制保护渣与钢液的接触过程,以避免卷渣.
在钢锭模底部进行铺渣操作,在钢液与保护渣接触的初期,由于浇铸过程流场非常不稳,喷射、飞溅现象严重[4],易造成保护渣卷入钢液中.因而应改用吊渣操作代替铺渣操作,以防止浇铸初期由于流场不稳定使保护渣卷入钢液中.
此外,该炉钢生产时为雨季,保护渣容易吸收空气中的水分形成局部块状,在钢液与保护渣接触后,块状保护渣被卷入钢液中,而未能有效排出.基于上述分析,制作具有自动搅拌功能的保护渣烘烤装置,该装置使用后,可有效保证保护渣中的水分含量满足使用要求,同时消除保护渣因水分超标形成块状的可能,使用的保护渣生产时均为粉面状.由此解决了模铸轴承钢的皮下夹杂问题,使模铸轴承钢的质量稳定性提高,满足了重载、高速轴承滚动体的质量稳定性要求.
4 结论及建议
在水浸自动超声波检测某模铸轴承钢时,出现了连续横波报警,经综合分析确认为皮下夹杂缺陷.该轴承钢中的皮下夹杂是以硅、铝、钙的氧化物为主,并含有少量的钠、钾等氧化物,经过对炼钢过程及原辅材料分析,确认皮下夹杂是由模铸保护渣引起的.
通过吊渣代替铺渣操作及自动搅拌式保护渣烘烤装置的应用,可消除皮下夹杂缺陷,使轴承钢的质量更加稳定.
文章来源:材料与测试网