分享:SiCf/TiAl复合材料界面反应及热稳定性
沈莹莹1,2, 张国兴1, 贾清,1, 王玉敏1, 崔玉友1, 杨锐
,1
1.
2.
采用真空吸铸法制备了SiCf/TiAl复合材料,利用SEM和TEM对制备态复合材料界面反应层进行元素扩散分析和产物确定。结果表明,制备态复合材料的界面反应产物主要由靠近碳层的等轴细晶TiC和靠近钛合金涂层的等轴粗晶TiC组成。对复合材料进行800℃热暴露实验,结果显示,界面反应层随热暴露时间的延长而增长,且在长大过程中出现了分层现象。根据热暴露后反应层厚度随时间的变化规律,绘制出800℃界面反应的动力学曲线,并推测出界面生长速率。热暴露200 h后的界面反应产物共有4层,从纤维一侧到基体一侧分别是细晶TiC层、粗晶TiC层、(Ti, Zr)5Si4层和Ti3Sn + Ti2AlC层。分别对制备态和热暴露态的SiCf/TiAl复合材料界面反应产物的形成机理进行了分析,得出热暴露过程中界面分层出现的主要原因是Ti2AlC新相的生成消耗了部分TiC相。
关键词:
随着现代航空、航天技术的发展,对材料的要求也越来越严苛。轻质、高强、耐热、抗疲劳、抗蠕变以及耐腐蚀等综合性能较好的材料逐渐成为航空材料的研究重点和热点。然而,传统的单一材料因各自固有的局限性而无法满足这些综合要求,具有优异综合性能的钛基复合材料(TMC)应运而生。自20世纪80年代起,技术发达国家都在致力于研究该类复合材料,且已成功制备出满足要求的航空航天部件[1,2]。例如,普惠公司(P&W)用钛基复合材料制备的航空发动机活塞,成功减重40%,且已在F119发动机上进行了试车[2];英国罗罗公司用钛基复合材料制备的发动机叶环成功减重30%[3]。遗憾的是,TMC受其基体合金的影响,其使用温度均在600℃以下[4]。与钛合金相比,Ti-Al系金属间化合物密度更低,高温力学性能更好,使用温度也更高。于是在TMC发展成熟的基础上人们开始了金属间化合物基复合材料(IMC)的研究,希望用Ti-Al金属间化合物代替钛合金基体制备新型复合材料以满足更高温度下使用航空部件的要求。Ti-Al二元系金属间化合物主要有3种:Ti3Al、TiAl和TiAl3[5]。其中TiAl因具有高比强度、高比模量以及优异的高温抗蠕变性能而成为最具有潜力的轻质高温材料[6~8],在航空航天、汽车制造等领域均已得到应用[9,10]。SiC纤维是一种高性能的陶瓷纤维,具有较高的比强度、比刚度,耐腐蚀等优点,同时高温下具有良好的抗氧化以及高热稳定性[11,12],且与金属之间有较好的相容性,是Ti-Al金属间化合物较理想的增强体材料。
复合材料在制备以及高温服役过程中,纤维与基体之间会发生化学反应和元素扩散,并随温度和时间的变化形成一定厚度的界面反应层,界面反应层中包含一种或多种反应产物,在SiC纤维增强TiAl金属基复合材料中,反应产物多为脆性相。如果复合材料的界面反应层较厚,在外力作用下,裂纹易在此处萌生,严重影响复合材料的力学性能[2,13,14]。另外,基体合金成分、纤维外部涂层成分以及制备工艺等均影响元素扩散路径,进而导致界面反应产物种类和分布状态存在差异[15~20]。因此,掌握界面反应层的长大规律对复合材料的应用具有重要意义。为了更好地设计和控制界面反应,研究复合材料复杂界面的形成和长大过程尤为重要。本工作采用真空吸铸法制备SiCf/TiAl复合材料,同时,为了避免纤维与基体合金液直接接触而使纤维受损,在所选用的SiC纤维表面用磁控溅射法溅射一层钛合金涂层。研究了SiCf/TiAl复合材料制备态及800℃热暴露态下界面元素扩散行为及界面反应产物的生成长大规律,同时对热暴露态复合材料的界面反应层长大速率及热稳定性进行了分析。
1 实验方法
本实验中所选取的TiAl基体合金成分为Ti-48Al-2Nb-2Cr (原子分数,%,下同)。基体合金采用真空电弧炉熔炼,每个锭子熔炼6次以保证合金成分均匀。采用化学气相沉积法(CVD)自主生产研制的SiC纤维,直径为100 μm,芯部钨芯直径约13 μm,外部碳层厚度约为2.3 μm。为防止液态合金与纤维之间发生严重的化学反应,用磁控溅射方法在纤维表面溅射约22 μm厚的钛合金涂层,靶材成分为Ti-5Al-2Sn-2Zr-4Cr-4Mo (TC17)。图1为纤维横截面示意图。
图1
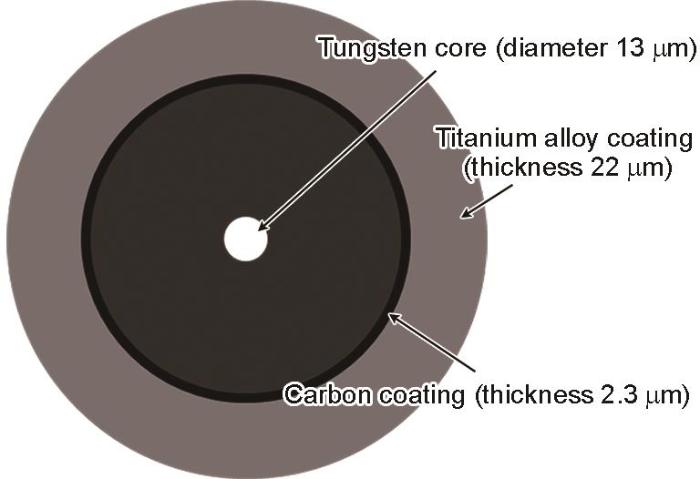
图1 带有钛合金涂层的SiC纤维横截面示意图
Fig.1 Schematic of the cross section of the SiC fiber coated with titanium alloy
SiCf/TiAl复合材料用真空吸铸法制备。制备流程为,首先将纤维提前在模具中排布并固定,合金锭置于熔炼室坩埚中。启动机械泵和分子泵进行抽真空。当真空抽至0.1 Pa以下,关闭熔炼室与吸铸室之间的连通阀,向熔炼室充入50 Pa高纯Ar气。关闭真空系统,并开启熔炼吸铸系统。电弧熔炼合金锭至完全熔透状态,打开两室之间的连通阀,合金液在两室之间压差及自身重力作用下快速流入模具中,与SiC纤维复合凝固成型。在该过程中,合金液充填温度约1500℃,合金液流入金属模具后迅速冷却凝固,待模具冷却10 min后将样品取出。制备好的复合材料尺寸(直径 ×
为探究该制备方法下复合材料界面反应层的长大规律以及热稳定性,对制备态的复合材料进行800℃高温热暴露实验。热暴露总时间为200 h,分别在热暴露25、50、100、150和200 h时取样分析。复合材料界面反应层厚度和纤维中碳层厚度在扫描电镜(SEM)下测量。具体测量方法为每个样品随机选取5根纤维,对于厚度较均匀的界面每根纤维随机测量10个点,然后取平均值作为测量结果;对于厚度不均匀的界面,根据凹面与凸起面大致所占整根纤维的比例,按比例随机测量每种界面的点数,测量总数也为10,最后求平均值。
采用Apreo热场发射SEM对制备态和热暴露态复合材料界面反应层形貌和周围组织进行观察和分析,并用其附带的能谱仪(EDS)对界面处元素分布进行分析。金相试样沿垂直于纤维方向切取,经机械研磨抛光后在5%HF + 10%HNO3 + 85%H2O (体积分数)的腐蚀液中进行腐蚀。采用Tecnai G2 20透射电子显微镜(TEM)观察制备态和热暴露态复合材料界面反应产物形貌,并根据选区电子衍射(SAED)花样测定反应产物的种类。制备态复合材料TEM样品制备方法为离子减薄法,具体制备流程为:用线切割沿垂直于纤维方向切取厚约0.4 mm的薄片,机械研磨至厚度0.05 mm以下,然后在凹坑仪上进行凹坑,凹至中心厚度约10 μm时,在离子减薄仪上对样品进行减薄。热暴露态的复合材料由于界面反应产物较多且较脆,在用上述方法制备过程中界面反应层很容易脱落,故采用聚焦离子束切割方法制备。切割方向同样沿垂直于纤维方向,切割范围包括部分SiC纤维、整个界面反应层和部分钛合金涂层。
2 实验结果
2.1 制备态SiCf/TiAl复合材料界面反应层形貌及元素扩散
图2所示是制备态SiCf/TiAl复合材料中纤维横截面形貌的SEM像。可以看出,纤维保持完整,与基体合金结合较好。纤维周围灰白色层为界面反应层,其厚度约为1.21 μm。黑色层为剩余碳层,经测量其厚度约为2.12 μm,说明与原始纤维中的2.3 μm的厚度相比,仅有0.18 μm厚的碳层参与界面反应。反应层周围无显微裂纹。钛合金涂层中可以观察到许多细小的针状α相。
图2
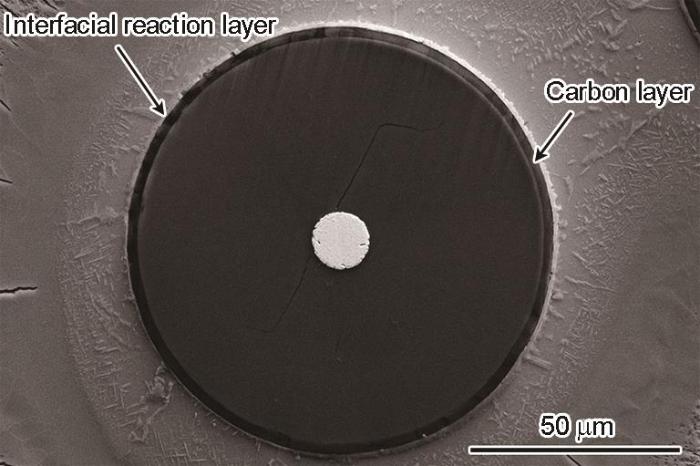
图2 真空吸铸法制备的SiCf/TiAl复合材料横截面形貌的SEM像
Fig.2 Cross-section SEM image of SiCf/TiAl composite prepared by vacuum suction casting
为探究SiCf/TiAl复合材料在复合成型过程中纤维、涂层以及基体之间的元素扩散规律,用SEM附带的EDS进行元素线扫描分析,扫描区域从纤维一侧到基体合金一侧,结果如图3所示。其中I区为界面反应层,II区为钛合金涂层,III区为钛合金涂层与基体合金的过渡层,IV区为TiAl基体合金。可以看出,纤维中的C元素和Si元素已扩散到II区钛合金涂层中,但扩散距离有限,仅在靠近I区附近有所分布。由于钛合金涂层的存在,基体合金与纤维间隔较远,基体合金中的元素仅与钛合金涂层之间有互扩散,产生了过渡层III。从图中也能看出钛合金涂层中的元素均有向纤维一侧扩散的趋势,但仅有Ti、Al、Sn、Zr 4种元素扩散至界面反应层中。其中Sn元素已明显地穿过界面反应层和碳层扩散至SiC中。
图3
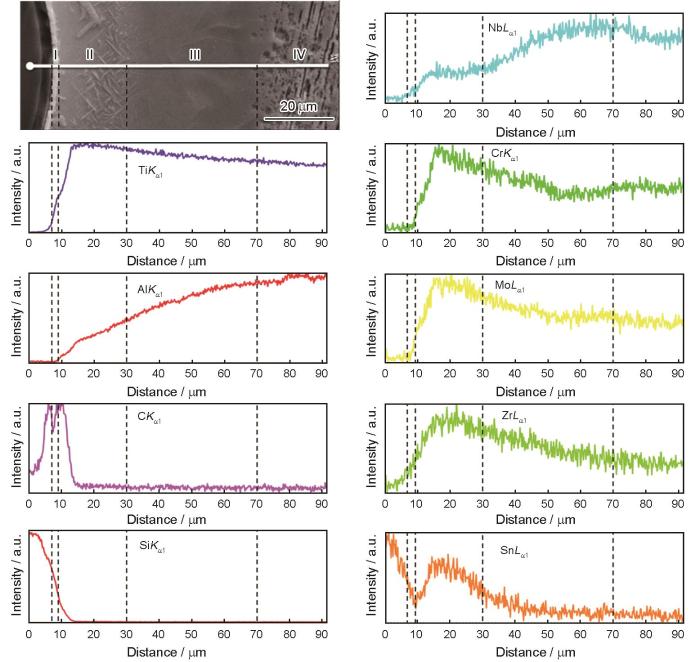
图3 制备态SiCf/TiAl复合材料SEM像及纤维到基体端元素线扫描结果
Fig.3 SEM image and EDS line scanning results of as-processed SiCf/TiAl composites from the fiber to the matrix (Area I is the interfacial reaction layer, area II is the titanium alloy coating, area III is the transition layer between the titanium alloy coating and the matrix alloy, and area IV is the TiAl matrix alloy)
2.2 制备态SiCf/TiAl复合材料界面反应产物
图4为制备态SiCf/TiAl复合材料界面反应产物组织的TEM像和SAED花样。可见,界面反应产物由2层组成,靠近碳层的等轴细晶层(I)和靠近钛合金涂层的等轴粗晶层(II)。细晶层厚约100 nm,包含许多细小的等轴晶粒。粗晶层厚约1000 nm,且仅由一层晶粒组成。根据SAED花样确定这2层中的反应产物均为TiC。
图4
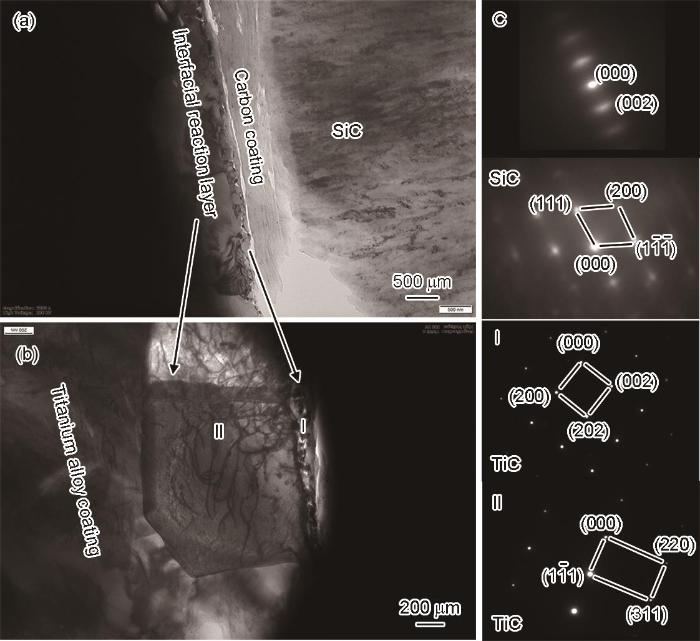
图4 制备态SiCf/TiAl复合材料界面反应产物组织的TEM像及选区电子衍射(SAED)花样
Fig.4 TEM images of the reaction products and the corresponding selected area electron diffraction (SAED) patterns of as-prepared SiCf/TiAl composite
(a) TEM image of SiC fiber and interfacial reaction layer and corresponding SAED patterns
((b) local enlarged view of the interfacial reaction products and corresponding SAED patterns
2.3 800℃热暴露SiCf/TiAl复合材料界面反应层长大规律及周围组织变化
图5为800℃不同热暴露时间之后复合材料界面反应层形貌。表1为所测量的界面反应层厚度和碳层厚度。从图5及表1中都可以看出,随热暴露时间延长界面反应层厚度增加,碳层厚度则逐渐减小,但界面反应层厚度的增加量明显小于碳层的消耗量,故而说明反应层主要是向钛合金涂层一侧长大。由于在热暴露过程中界面反应主要受原子扩散控制,故其界面反应层的生长遵循生长动力学规律,其反应层厚度可以用公式x = kt1/2 + x0来表示,其中,x为界面反应层厚度,x0为初始界面反应层厚度,t为热暴露时间,k为界面反应长大速率常数。由前文可知x0 = 1.21 μm,将所有数据带入到公式中,得到图6所示的界面反应层长大动力学曲线。拟合之后得到拟合直线斜率k = 5.02 × 10-10 m/s1/2,即为反应长大速率常数。这与文献[21,22]中报道的相同温度下的其他SiCf/Ti基复合材料热暴露界面反应长大速率常数的数量级相同。
图5
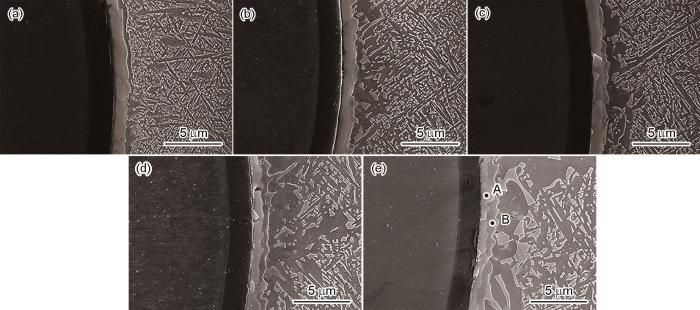
图5 800℃热暴露不同时间后SiCf/TiAl复合材料界面反应层及周围组织形貌的SEM像
Fig.5 SEM images of interfacial reaction layer and matrix of SiCf/TiAl composite after thermal exposure at 800oC for 25 h
(a), 50 h (b), 100 h (c), 150 h (d), and 200 h (e)
表1 800℃热暴露不同时间后SiCf/TiAl复合材料界面反应层厚度和碳层厚度
Table 1
Thermal exposure time / h | Thickness of the interfacial reaction layer / μm | Thickness of the carbon layer / μm |
---|---|---|
25 | 1.312 | 2.003 |
50 | 1.376 | 1.982 |
100 | 1.472 | 1.912 |
150 | 1.573 | 1.897 |
200 | 1.620 | 1.869 |
图6
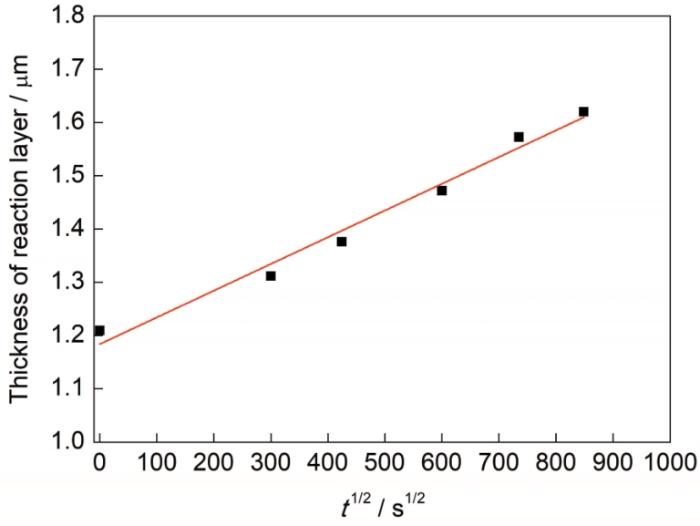
图6 SiCf/TiAl复合材料800℃界面反应层长大动力学曲线
Fig.6 Interfacial reaction kinetic curves of SiCf/TiAl composites at 800oC (t—thermal exposure time)
从图5还能观察到,随着热暴露时间的延长,界面反应层以及周围组织均发生了变化。热暴露后期,界面反应层中出现了分层现象,且随着热暴露时间的延长,分层现象越明显,而在其他SiCf/TiAl复合材料的热暴露过程中并没有观察到这种分层现象。同时随着热处理时间的延长,界面周围钛合金涂层中α相和β相逐渐长大,且越靠近界面反应层长大越明显。表2是热暴露200 h后靠近碳层一侧(A)和靠近钛合金涂层一侧(B)界面反应层的EDS分析结果。可以看出,2层反应层中的元素含量相差较大。靠近碳涂层的内层A点处主要含有Ti、C以及少量的Si、Al元素。而外层B点Ti为主要的元素,C和Si元素含量显著降低,Al元素含量大幅增加。除此之外微量元素Sn含量增加较明显。
表2 图5e中点A、B处的EDS分析结果 (%)
Table 2
Element | Point A | Point B | ||
---|---|---|---|---|
Mass fraction | Atomic fraction | Mass fraction | Atomic fraction | |
C | 16.20 | 42.66 | 3.61 | 12.50 |
Al | 3.29 | 3.85 | 9.64 | 14.86 |
Si | 2.78 | 3.13 | 0.47 | 0.69 |
Ti | 74.66 | 49.26 | 79.84 | 69.30 |
Cr | 0.50 | 0.30 | 0.39 | 0.31 |
Zr | 1.21 | 0.42 | 1.71 | 0.78 |
Nb | 0.00 | 0.00 | 0.09 | 0.04 |
Mo | 0.18 | 0.06 | 0.37 | 0.16 |
Sn | 1.17 | 0.31 | 3.89 | 1.36 |
2.4 800℃热暴露态SiCf/TiAl复合材料界面反应产物
图7为800℃热暴露200 h后SiCf/TiAl复合材料界面反应产物组织的TEM像及SAED花样。对反应产物的SAED花样进行标定,鉴别界面反应产物的种类。按反应产物的位置、形貌和种类将其分为4层(图中I~IV)。第I层为靠近碳层的细晶TiC层,由于晶粒较细小,对应图中A的SAED花样为多晶衍射环。与制备态不同的是,该细晶TiC层厚度明显较制备态厚,约200 nm。第II层为等轴粗晶TiC层,该层厚约1 μm,包含有2层TiC晶粒,分别如图中B、C所示。第III层则由等轴的(Ti, Zr)5Si4相组成,如图中D所示。第IV层包含2种反应产物,长条状的Ti3Sn相(图中E所示)和Ti2AlC相(图中F所示)。
图7
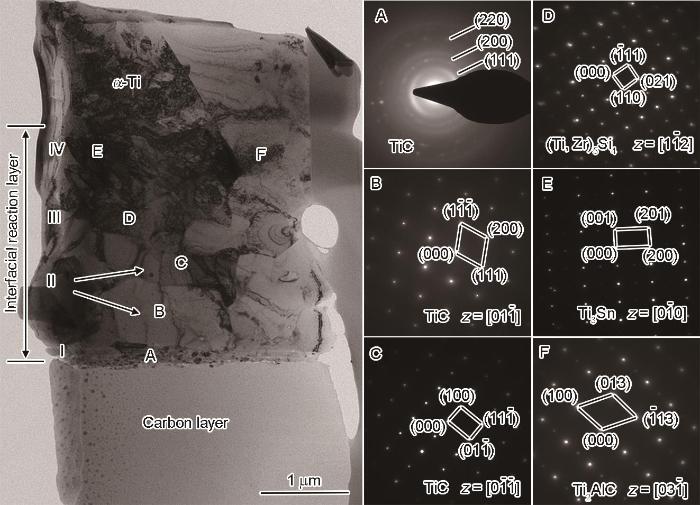
图7 800℃热暴露200 h后SiCf/TiAl复合材料界面反应产物组织TEM像及SAED花样
Fig.7 TEM image of the reaction products and the corresponding SAED patterns after thermal exposure at 800oC for 200 h
(I—fine-grained TiC layer, II—coarse-grained TiC layer, III—(Ti, Zr)5Si4 layer, IV—Ti3Sn + Ti2AlC layer)
3 分析讨论
3.1 制备态SiCf/TiAl复合材料界面元素扩散规律及反应产物生成过程
从图3的EDS结果可知,制备态下参与界面反应的主要是Ti、C、Si、Al 4种元素。热力学上,根据Ti-C、Ti-Si二元相图以及Ti-Al-C、Ti-Si-C三元相图可知这4种元素可以形成多种相[23]。然而反应产物的生成不仅要看热力学上是否可行,还要看在动力学上是否有利,即还需要考虑反应过程中元素的扩散速率、元素浓度分布等问题。在SiCf/TiAl复合材料制备的最初阶段,纤维碳层中的C元素和钛合金涂层中的Ti元素首先接触,发生化学反应Ti + C
3.2 热暴露态SiCf/TiAl复合材料界面元素扩散规律及反应产物生成过程
与制备态下相比,热暴露态下界面反应层的形态以及反应产物均发生了较大的变化,这主要与元素的扩散反应有关。制备态下,由于复合材料的制备过程比较短,元素扩散时间不充分,使得参与界面反应的原子数较少,生成的界面产物种类和含量都比较少。而热暴露态下,元素扩散的激活能大大提高,扩散的时间也充分延长,可结合热暴露后界面反应产物形貌(图7)及对应的界面反应层形貌(图5e)来分析界面反应产物的形成过程及分层现象出现的原因。
在800℃热暴露下,制备态下界面反应层中未参加反应的C原子,继续与扩散而来的Ti元素反应生成TiC。且随着热暴露时间的延长,TiC界面层持续长大。从图5及表1中也可以看出,反应层主要是向钛合金涂层一侧长大。这主要是因为C原子的半径较小,且在TiC中的扩散系数较大,所以相同时间内穿越TiC层到基体一侧的C原子的数量远远大于扩散至纤维一侧的Ti原子的数量。仅有少量的Ti原子穿过界面反应层到碳层附近与C元素反应生成细小的等轴TiC。然而当TiC反应层越来越厚时,元素扩散的阻力也越来越大,界面反应层中C元素浓度也越来越低。而此时,由于C元素的扩散,在纤维和碳层中留下了许多空位,这些空位为Si原子的扩散提供了通道。所以随着TiC界面层的长大,越来越多的Si元素从纤维扩散至界面处,与界面反应层中的Ti元素反应生成Ti的硅化物。根据Ti-Si二元相图可知,Ti的硅化物主要有TiSi、TiSi2、Ti3Si、Ti5Si3和Ti5Si4。从热力学角度分析,反应生成Ti5Si4所需要的Gibbs自由能最小[26],故而生成Ti5Si4相最稳定,这与本工作中发现的Ti5Si4界面反应产物结果是一致的。然而在众多的SiC纤维增强钛合金、钛铝金属间化合物基复合材料中,Ti与Si形成的Ti的硅化物主要是Ti5Si3[2,27,28]。这是因为界面产物的生成不仅受热力学影响,还受原子浓度所对应相图中区域相控制[23]。已报道的复合材料制备温度都较低(< 1000℃),而本工作SiC纤维增强TiAl复合材料采用液态吸铸法来制备,其制备温度较高(TiAl合金液温度约1500℃)。高温为C—C键、Si—C键以及钛合金涂层中其他金属键的断裂都提供了较高的能量,释放出的原子数较传统制备法下要多。然而该方法制备复合材料的复合成型过程较快,这些原子并没有充分参与界面反应。热暴露过程中重新激发了这些原子,所以在热暴露过程中可扩散至界面反应层中的原子数量较多。当热暴露时间足够长时,充足的Si原子与Ti原子反应生成更稳定的Ti5Si4相。Zr元素在钛合金中属于中性元素,在热暴露过程中伴随着α相和β相的长大,被排挤进入到界面反应层中。但是由于其含量较少,在向界面反应层扩散的时候,Zr可部分取代Ti原子在Ti5Si4中的位置,即生成(Ti, Zr)5Si4相,对应于界面反应产物中的第III层界面反应产物(图7)。随着TiC和(Ti, Zr)5Si4界面反应产物的生成,界面附近钛合金涂层中大量的Ti元素向纤维一侧扩散,导致周围Al浓度的升高。Al是α相稳定元素,所以使得靠近界面的钛合金涂层组织中α相的含量和尺寸随热处理时间延长而增加。界面周围Al浓度的升高迫使Al原子向浓度梯度减小的纤维一侧扩散。当其扩散至界面反应层时,与界面反应层中未参加反应的Ti原子首先生成TiAl金属间化合物,之后再与界面反应层中的TiC反应生成Ti2AlC:TiAl + TiC → Ti2AlC[29,30]。Ti2AlC的生成消耗了界面反应层中部分TiC层,即出现了图5中界面反应分层现象。且随着外层Ti2AlC层的生成,内层TiC层逐渐变薄。Ti2AlC相的生成消耗了界面周围的Al元素,反而进一步促进了界面周围β相的长大,正如图5中所示,界面分层之后,界面周围β相急剧长大。Sn元素的扩散在制备态下就已经开始了(图3)。随着热暴露时间的延长,α相和β相逐渐长大,在长大的过程中争夺对自身长大有利的元素,由于Sn在钛合金中也属于中性元素,既不参与α相的长大也不参与β相的长大,故而Sn也被排挤进入到界面反应层处。且Sn的熔点较低,可形成液态小熔池,加速其扩散。与界面反应层中未参与界面反应的Ti反应生成Ti3Sn相。
根据以上分析,热暴露过程中界面反应产物的生成和长大示意图如图8所示。这些复杂界面产物的生成不仅与热暴露温度和时间有关,同时也与热暴露过程中界面反应层周围的组织变化有关。热暴露过程中出现界面分层的主要原因是Ti2AlC新相的生成消耗了部分生成的TiC相。靠近碳层的界面反应层中界面反应产物是TiC和(Ti, Zr)5Si4,而外层中的界面反应产物是Ti3Sn + Ti2AlC。
图8

图8 热暴露过程中界面反应产物生成和长大的示意图
Fig.8 Schematic of the formation and growth of interfacial reaction products during thermal exposure
4 结论
用真空吸铸法所制备的SiCf/TiAl复合材料,复合成型过程较快,界面处元素扩散不充分,界面反应产物为单一的TiC相;800℃热暴露下,随着时间的延长,元素充分扩散,界面反应层逐渐长大,界面反应长大速率常数k = 5.02 × 10-10 m/s1/2。800℃、200 h热暴露后界面反应产物共有4层,从纤维一侧到基体一侧分别是细晶TiC层、粗晶TiC层、(Ti, Zr)5Si4层和Ti3Sn + Ti2AlC层。这些复杂界面产物的生成不仅与热暴露温度和时间有关,同时也与热暴露过程中界面反应层周围的组织变化有关。热暴露过程中界面出现分层的主要原因是Ti2AlC新相的生成消耗了部分生成的TiC相。靠近碳层的内层界面反应产物是TiC和(Ti, Zr)5Si4,而外层中的界面产物是Ti3Sn + Ti2AlC。
来源-金属学报