分享:预拉伸变形对欠时效7N01铝合金板材疲劳断裂的影响
田妮,1,2, 石旭1, 刘威1, 刘春城3, 赵刚1,2, 左良2,4
1.
2.
3.
4.
针对工业化生产的7N01铝合金板材,采用拉伸实验、疲劳实验和微观组织结构表征等手段研究了预拉伸变形对欠时效态7N01铝合金板材疲劳性能和疲劳断裂特征的影响。结果表明,预拉伸变形量增大至20%,欠时效态7N01铝合金板材中合金相粒子的形状、尺寸、数量、分布以及薄带状晶粒的尺寸和形状基本保持不变。然而,板材表现出明显的加工硬化效应,其屈服强度、抗拉强度和显微硬度分别由181 MPa、233 MPa和95 HV增大至254 MPa、271 MPa和117 HV,延伸率从23.2%降低至5.2%。在应力175 MPa、应力比R = 0的疲劳循环加载条件下,随预拉伸变形量的增加,欠时效态7N01铝合金板材的疲劳寿命呈现出先缩短再延长又缩短的趋势。未预拉伸变形试样的疲劳寿命为6.06 × 105 cyc,5%预拉伸变形可将铝板的疲劳寿命延长75%,达到了1.06 × 106 cyc,而3%和20%的预拉伸变形将铝板的疲劳寿命分别缩短至4.21 × 105和2.89 × 105 cyc。5%~16%预拉伸变形使欠时效态7N01铝合金板材基体中形成均匀分布的高密度位错或位错胞的显微组织,可将合金板材的疲劳寿命延长23%以上。
关键词:
中强可焊7N01铝合金不但具有较高的强度、塑性和韧性,同时具有良好的焊接性和热加工性,其作为关键承力结构材料被广泛应用于轨道车辆和航天飞行器等领域[1~3]。材料在生产和装配过程中通常会产生一定程度的预变形,预变形会影响材料服役过程中的循环塑形行为,从而影响材料的耐久性[4~6]。然而,目前有关预变形对金属材料疲劳性能的影响结论不尽相同。针对钢铁材料,Gustavsson和Melander[7]认为高预变形(15%以上)有利于提高铁素体-马氏体双相钢的疲劳强度,但Uemura[8]认为预变形对低碳钢的低周疲劳寿命不利而对其中高周疲劳寿命无明显影响。对于铝合金而言,较多研究结果表明预拉伸变形会恶化其疲劳性能。Al-Rubaie等[9]发现,1%~7%的预拉伸变形在7050-T7451铝合金中形成的滑移晶粒和驻留滑移带(persistent slip band,PSB)对合金的疲劳性能不利,合金的疲劳寿命(S-N)曲线随预变形量增大而整体下移。Schijve[10]对2024-T3 铝合金施加3%的拉伸变形,发现合金的屈服强度由428 MPa提高到480 MPa,但是根据近似公式
本工作针对欠时效态7N01铝合金板材,研究了预拉伸变形对其高周疲劳性能及疲劳断裂行为的影响,旨在揭示预拉伸变形引入的位错与铝合金晶界、析出相(precipitate)粒子协同作用对7N01铝合金板材疲劳裂纹萌生、疲劳裂纹扩展的影响规律及作用机制,为最终改善7N01铝合金疲劳性能提供实验数据和理论依据。
1 实验方法
实验材料为工业化生产的12.5 mm厚7N01铝合金热轧板,其化学成分(质量分数,%)为:Zn 4.67,Mg 1.04,Mn 0.28,Cu 0.13,Zr 0.17,Cr 0.17,Fe 0.13,Si 0.03,Ti 0.05,Al余量。沿板材轧制方向按照图1所示的尺寸切取拉伸和疲劳试样。所有试样在循环风热处理炉中进行470℃、90 min固溶处理后水淬,室温停放1 h后在空气炉中进行120℃、1 h人工时效处理(欠时效态)。分别采用Shimadzu AG-X型250 kN电子万能试验机和QBG-100高频疲劳试验机进行室温拉伸和室温疲劳实验。预拉伸变形量分别为3%、5%、8%、12%、16%以及20%,应变速率为0.001 s-1。疲劳加载应力为175 MPa,应力比R = 0,载荷波为正弦波。拉伸和疲劳实验的平行试样均为3个。
图1

图1 拉伸及疲劳试样尺寸
Fig.1 Specimen size for tensile and fatigue tests (unit: mm)
采用Wilson MH-500型数显Vickers硬度计测定显微硬度,外加载荷25 g,加载时间10 s,每个试样均测试10个点,取平均值。采用JSM-6510A型扫描电子显微镜(SEM)观察疲劳断口表面形貌。采用GX71光学显微镜(OM)和JEM-2100F透射电镜(TEM)进行显微组织观察,观察位置为板材厚度中心层。TEM样品制备先用砂纸减薄至65~70 μm厚,随后进行电解双喷减薄,双喷液是体积比为1∶3的硝酸甲醇溶液,电压为10~15 mV,电流50~60 mA,温度控制在-30~-25℃。
2 实验结果
2.1 显微组织
图2所示为欠时效态7N01铝合金板材金相显微组织三维立体图和未经预变形、分别经3%~20%预拉伸变形后板材的纵截面显微组织的OM像。可见,经不同程度预拉伸变形后的铝板中均存在许多沿轧向呈碎链状分布的微米级深灰色条块状过剩结晶相粒子,以及大量尺寸细小且弥散分布的浅灰色点状合金相(constituent)粒子。结合板材三维立体金相组织照片(图2a)以及Hodgson等[13]和Adrien等[14]的研究结果可知,微米级合金相粒子空间形貌为不规则颗粒状,其主要是α-Al (FeMn)Si不可溶过剩结晶相粒子(图2b箭头所示);尺寸极其细小的合金相粒子主要是AlZnMg(Si)弥散相(dispersoid)粒子(图2d圆形框内)。经不同程度预拉伸变形后的铝板中合金相粒子的形状、尺寸、分布和数量无明显差异,说明预拉伸变形对欠时效态7N01铝合金板材中过剩结晶相粒子和弥散相粒子组态无明显影响。图3所示为欠时效态7N01铝合金板材晶粒组织三维立体图和未经预变形、分别经3%~20%预拉伸变形后铝板的纵截面晶粒组织。可见,经470℃、90 min固溶水淬及120℃、1 h人工时效处理后,铝板的晶粒仍具有明显的纤维状特征,结合未经预拉伸变形的铝板晶粒组织三维立体图可知,铝板的晶粒组织为长薄带状(图3a),说明铝板未发生再结晶。经3%预拉伸变形后,铝板薄带状晶粒的厚度略有减薄,继续增大预拉伸变形量至20%,铝板的晶粒未出现继续减薄拉长的现象。说明仅当预拉伸变形程度较小时可使欠时效态7N01铝合金板材薄带状晶粒厚度略微减薄。
图2

图2 欠时效态7N01铝合金板材及其经不同程度预拉伸变形后显微组织的OM像(纵截面,未腐蚀)
Fig.2 OM images of under-aged 7N01 aluminum alloy plate and after different pre-tensile deformations (along longitudinal section, non-etched)
(a) three-dimensional diagram, undeformed(b) undeformed (c) 3% (d) 5% (e) 8% (f) 12% (g) 16% (h) 20%
图3

图3 欠时效态7N01铝合金板材及其经不同程度预拉伸变形后的晶粒OM像(纵截面)
Fig.3 OM images of grains of under-aged 7N01 aluminum alloy plate and after different pre-tensile deformations (along longitudinal section) that were observed by polarized light microscope
(a) three-dimensional diagram, undeformed
(b) undeformed (c) 3% (d) 5% (e) 8% (f) 12% (g) 16% (h) 20%
图4为欠时效态7N01铝合金板材经不同程度预拉伸变形后显微组织的TEM像。可见,铝板中存在许多尺寸约100 nm的弥散相粒子,晶界及晶内均未观察到明显的析出相粒子。未经预拉伸变形时Al基体中位错很少(图4a),随预拉伸变形量增大,Al基体中位错密度逐渐增大。值得注意的是,经3%预拉伸变形后Al基体中位错分布非常不均匀,位错或阻滞于弥散相粒子前沿,或阻滞于晶界前沿,形成排列成墙的位错塞积群(图4b箭头所示),而在晶内其他区域几乎没有观察到位错。Branco等[4]在经过一定程度预拉伸变形后的7050铝合金中也观察到了这种位错分布不均匀的现象,位错主要出现在滑移带上,导致滑移线密度增大。经受5%、8%以及12%预拉伸变形后的铝板晶内位错密度逐渐增大,位错整体呈均匀的网状分布,并出现位错缠结,形成了位错胞(图4c~e)。当预拉伸变形量达到16%时,铝板中位错密度进一步增大,并形成了尺寸约200 nm的胞状亚结构(图4f)。预拉伸变形进一步增加至20%,铝板晶内位错密度极高,位错胞状亚结构尺寸细化(图4g)。
图4

图4 欠时效态7N01铝合金板材经不同程度预拉伸变形后组织的TEM像
Fig.4 TEM images of under-aged 7N01 aluminum alloy plate and after different pre-tensile deformations
(a) undeformed (b) 3% (c) 5% (d) 8% (e) 12% (f) 16% (g) 20%
2.2 力学性能
图5是欠时效态7N01铝合金板材的力学性能随预拉伸变形量的变化曲线。可见,随预拉伸变形程度增加,铝板的显微硬度、抗拉强度和屈服强度均呈单调递增的趋势,而延伸率随预拉伸变形量增加而逐渐降低。说明室温拉伸变形时,欠时效态7N01铝合金板材表现出明显的加工硬化效应。未预拉伸变形时,铝板的显微硬度、屈服强度、抗拉强度和延伸率分别为95 HV、181 MPa、233 MPa和23.2%;当预拉伸变形量增大至8%时,铝板的屈服强度和抗拉强度迅速增大至237和263 MPa,板材的延伸率降低至15.2%。继续增加预拉伸变形量时,铝板的屈服强度和抗拉强度增速变缓。当预拉伸变形量增大至20%时,铝板的抗拉强度和屈服强度分别为271和254 MPa,延伸率显著降低至5.2%。当预拉伸变形量小于8%或大于12%,铝板的显微硬度增速较缓慢,但是,当预拉伸变形量从8%增大至12%时,铝板的显微硬度迅速增大,从104 HV增大至113 HV。
图5

图5 欠时效态7N01铝合金板材经不同程度预拉伸变形量后的力学性能
Fig.5 Mechanical properties of under-aged 7N01 aluminum alloy plate after different pre-tensile deformations
(a) microhardness
(b) yield strength, tensile strength, and elongation
2.3 疲劳寿命
图6是欠时效态7N01铝合金板材经不同程度预拉伸变形后,在最大应力为175 MPa (低于未预拉伸变形的欠时效态铝板屈服强度181 MPa)、R = 0条件下的疲劳寿命。可见,随预拉伸变形程度增大,铝板的疲劳寿命呈现出先缩短后延长再缩短的趋势。未经预拉伸变形时铝板的平均疲劳寿命约6.06 × 105 cyc,经3%预拉伸变形后铝板的平均疲劳寿命缩短至4.21 × 105 cyc;承受5%预拉伸变形的铝板平均疲劳寿命最长,达到1.06 × 106 cyc,是未预拉伸变形铝板的疲劳寿命的1.75倍;继续增大预拉伸变形量,铝板的平均疲劳寿命逐渐缩短,当预拉伸变形量达到20%时,铝板的平均疲劳寿命最短,仅为2.89 × 105 cyc。值得注意的是,承受5%~16%预拉伸变形板材的平均疲劳寿命比未预拉伸变形板材的疲劳寿命延长了23%以上,说明适当程度的预拉伸变形有利于延长欠时效态7N01铝合金板材的疲劳寿命,这与目前大部分学者[4,9,10]得出的预拉伸变形对铝合金疲劳性能不利的研究结果并不一致。
图6

图6 欠时效态7N01铝合金板材经不同程度预拉伸变形后的疲劳寿命
Fig.6 Fatigue life of under-aged 7N01 aluminum alloy plate after different pre-tensile deformations
2.4 疲劳断口形貌
图7是欠时效态7N01铝合金板材经不同程度预拉伸变形后,在应力级别为175 MPa、R = 0条件下疲劳断口表面疲劳源处的SEM像。可见,经不同程度预拉伸变形后,铝板的疲劳裂纹均萌生于试样表面或近表面粗大过剩结晶相粒子处,说明预拉伸变形程度对疲劳裂纹萌生位置无明显影响。断口表面疲劳裂纹源处均可观察到大尺寸过剩结晶相粒子或明显的孔洞,这是由于在循环载荷作用下,位错滑移至粗大过剩结晶相粒子界面前沿塞积形成应力集中,导致过剩结晶相粒子与基体的结合面分离而形成孔洞。未经预拉伸变形的铝板裂纹源处的过剩合金相粒子尺寸相对较小,断口表面较粗糙(图7a)。经5%和8%预拉伸变形铝板的疲劳裂纹源区域过剩结晶相粒子尺寸相对粗大、断口表面起伏程度较大,裂纹具有明显的放射状特征(图7c和d)。经3%和16%预拉伸变形后的合金疲劳断口表面与裂纹源紧邻的疲劳裂纹扩展区域凹凸不平且存在大量高低不平的结晶学平面和撕裂棱,但是经3%拉伸变形后试样的疲劳断口表面中裂纹源处的结晶学平面特征相对于经16%拉伸变形后试样的疲劳断口表面中裂纹源处的结晶学平面特征更显著(图7b和e)。经20%预拉伸变形的铝板疲劳断口表面裂纹源区域的形貌较为平滑,可观察到明显的疲劳辉纹,辉纹宽度约为0.9 μm (图7f),并且每隔数条小辉纹还存在类似台阶状的宽大辉纹。
图7
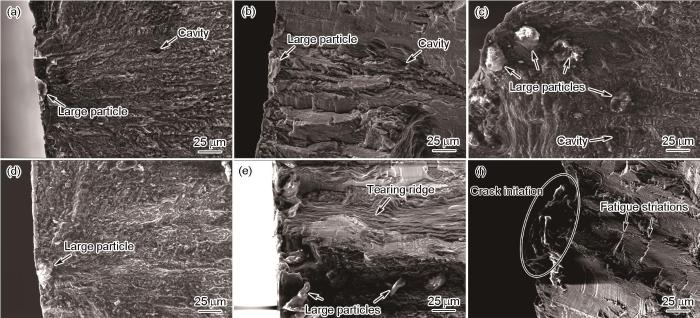
图7 欠时效态7N01铝合金板材经不同程度预拉伸变形后的疲劳断口表面裂纹源处SEM像
Fig.7 SEM images of fatigue sources of under-aged 7N01 aluminum alloy plate after different pre-tensile deformations
(a) undeformed (b) 3% (c) 5% (d) 8% (e) 16% (f) 20%
图8是欠时效态7N01铝合金板材经不同程度预拉伸变形后,在应力175 MPa、R = 0条件下疲劳断口表面疲劳裂纹扩展区形貌的SEM像。可见,未预拉伸变形以及分别经5%和8%预拉伸变形的铝板疲劳断口扩展区表面形貌较为粗糙,表面主要由极其细小的波浪状条纹和撕裂棱构成,具有明显的河流花样特征,且存在多条长犁沟状二次裂纹,断口表面起伏明显,其中经5%和8%预拉伸变形后试样疲劳断口裂纹扩展区中存在大量较长的分布式二次裂纹(图8c和d),表明疲劳裂纹在扩展过程中发生了多次偏转。经受3%预拉伸变形试样的疲劳断口裂纹扩展区表面形貌虽然也具有河流花样特征,但同时可以清楚地观察到许多曲折的疲劳辉纹和少量二次裂纹(图8b)。这种光滑的疲劳断口形貌不同于承受较小预拉伸变形量的铝板,也不同于在7085、7175和7050铝合金材料中观察到的疲劳裂纹扩展区粗糙的表面形貌特征[15,16]。经16%和20%预拉伸变形后的铝板疲劳断口疲劳裂纹扩展区表面比较光滑,扩展路径中可观察到大量平直的疲劳辉纹和疲劳台阶,并伴有聚集型孔洞(图8e和f),疲劳辉纹间互相平行且具有规则的间距宽度,疲劳辉纹条带的法线方向几乎与该区域的裂纹扩展方向一致。这主要是由于7N01铝合金热轧板经固溶欠时效处理后晶粒仍保持薄带状特征,疲劳加载方向与薄带状晶粒的长轴方向一致,疲劳应力法线方向的晶粒厚度较薄,裂纹易沿着晶内塞积的高位错密度区快速穿透薄带状晶粒,因此裂纹扩展路径相对较平滑。另外,合金断口表面中均未观察到冰糖块状的沿晶断裂特征,这同样是与合金板材的晶粒呈薄带状有关。因为疲劳主应力与薄带状晶粒长轴一致,裂纹无法沿扁长的晶界扩展,只能沿着晶内某一个剪切面穿晶扩展。
图8

图8 欠时效态7N01铝合金板材经不同程度预拉伸变形后的疲劳断口表面裂纹扩展区形貌的SEM像
Fig.8 SEM images of fatigue crack propagation of under-aged 7N01 aluminum alloy plate after different pre-tensile deformations
(a) undeformed (b) 3% (c) 5% (d) 8% (e) 16% (f) 20%
3 讨论分析
由于预拉伸应力加载方向与薄带状晶粒长度方向一致,在预拉伸变形量较小(小于3%)时Al基体的变形抗力低,晶粒沿应力加载方向略微拉长而使得薄带状晶粒厚度略有减薄;当预拉伸变形量较大(超过3%)时,由于位错强化使基体变形抗力显著提高,塑性变形过程中主要通过晶粒内部的位错滑移释放形变能,因此当预拉伸变形量超过3%后,欠时效态7N01铝合金板材晶粒未出现继续减薄拉长的现象。
欠时效态7N01铝合金板材中固溶的Zn、Mg溶质原子主要以溶质原子团簇(即GP区)形式存在于基体中,运动位错大多以切割方式通过GP区[17]。铝板在预拉伸变形过程中,一方面位错不断增殖导致位错数量逐渐增多(图4),同时也伴随着异号位错相消或位错滑移至晶体表面湮灭,结合硬度、强度和延伸率变化规律,认为当预拉伸变形量不超过8%时,位错的增殖速率远大于位错的相消或湮灭的速率,铝板中位错密度快速增大,加工硬化效果显著,此时铝板的强度和显微硬度增幅较大(图5)。当预拉伸变形量达到12%时,铝板中位错密度非常高(图4e),铝板的变形抗力进一步增大,其屈服强度增加至244 MPa,塑性流变应力剧增。高流变应力下位错重排、相消和湮灭的几率逐渐增加,大量螺型位错交滑移或刃型位错攀移导致铝板流变应力-应变曲线进入抛物线硬化阶段[18],因此铝板的强度增速减缓。这与王芝秀等[19]研究预变形对2E12铝合金屈服强度的影响结论一致。
由图2~4结果可知,预拉伸变形对欠时效态7N01铝合金板材中第二相粒子及晶粒尺寸形貌无明显影响,其主要改变的是Al基体中的位错数量和分布。在疲劳加载条件相同的情况下,铝板的疲劳寿命或疲劳性能主要决定于Al基体中位错数量和分布。未预拉伸变形时,Al基体内位错很少,疲劳寿命约为6.06 × 105 cyc。承受了3%预拉伸变形的铝板疲劳裂纹萌生区无明显放射状特征(图7b),铝板经历较少的循环后即萌生了疲劳裂纹。因为铝板承受3%的预拉伸变形时变形不均匀,位错主要在大尺寸过剩结晶相粒子与Al基体的界面处萌生且局部塞积(图4b),疲劳加载过程中这种贯穿晶粒的位错墙极易成为疲劳微裂纹的萌生位置,并起到桥接主裂纹的作用,使得疲劳裂纹快速穿过晶粒向下一个晶粒继续扩展。另外,疲劳裂纹扩展路径上存在较多曲折的疲劳辉纹和少量二次裂纹(图8b),疲劳辉纹越明显、间距越宽,则疲劳裂纹扩展速率越高[20]。综上可知,经3%预拉伸变形后的铝板中不均匀分布的低密度位错不仅促进疲劳裂纹萌生,还有利于疲劳主裂纹的桥接和扩展,最终导致欠时效态7N01铝合金板材在应力级别为175 MPa、R = 0条件下的疲劳寿命大幅度缩短(约为4.21 × 105 cyc,铝板的疲劳寿命比未预拉伸变形时的疲劳寿命缩短了约31%)。
当预拉伸变形量达到5%和8%时,欠时效态7N01铝合金板材的屈服强度分别达到222和237 MPa,抗拉强度分别达到256 和263 MPa,显微硬度分别为101和104 HV,表现出显著的应变强化特征。基体中位错分布较均匀,局部位错缠结,形成了位错胞(图4c和d)。这种位错组态使合金板材的疲劳寿命分别延长至1.06 × 106和8.63 × 105 cyc,相对于未预拉伸变形时的疲劳寿命分别提高了75%和42%。研究[21~24]认为,由于金属材料中的第二相粒子与基体在强度、刚度、塑性等均不匹配,疲劳裂纹经常萌生于第二相粒子与基体的界面处,相对于第二相粒子而言,Al基体的强度、硬度和刚度都很低,但塑性很高。5%和8%的预拉伸变形可使Al基体中出现高密度、均匀分布的位错,使Al基体强度和硬度提高,这在一定程度上弱化了合金相粒子与基体的不匹配程度,使铝板疲劳承载协调性增强。经5%和8%预拉伸变形铝板的疲劳断口裂纹源处表面起伏程度较大,具有明显的放射状扩散特征,塑性变形痕迹明显(图7c和d),说明铝板疲劳裂纹萌生较困难。而且铝板疲劳断口疲劳裂纹扩展区中还存在大量较长的分布式二次裂纹(图8c和d),表明已经具有较强位错强化效应的Al基体使得疲劳裂纹在扩展过程中发生了多次偏转。这些二次裂纹在疲劳裂纹扩展过程中会消耗主裂纹的扩展能量,有效释放主裂纹尖端应力,使疲劳裂纹扩展速率降低[25]。因为先经受一定程度预拉伸变形的铝板在交变载荷作用下,2个相邻裂纹面会发生转动,进而影响裂纹走向,当相邻晶粒的有利滑移系存在一定的角度,裂纹在扩展过程中则会偏转至相邻晶粒的有利滑移系继续扩展,也可能终止于晶界处,这样即造成了疲劳断口表面的高低起伏、凹凸不平,这与Jian等[26]观察到的实验现象一致。综上可知,均匀分布的高密度位错弱化了第二相粒子与基体间的不匹配性,不利于疲劳裂纹的萌生,因而起到了显著改善欠时效态7N01铝合金板材疲劳性能的作用。
当铝板承受的预拉伸变形程度达到16%时,基体中位错密度进一步增大,并出现明显的胞状亚结构(图4f),铝板的屈服强度、抗拉强度和显微硬度进一步增大至250 MPa、269 MPa和116 HV,但是板材的延伸率降低至9.6%。虽然拉伸变形程度已经很大,位错强化效应非常显著,但铝板的疲劳寿命仍然比未经受预拉伸变形时延长了23%。铝板疲劳断口表面裂纹源处具有大量高低不平的结晶学平面、撕裂棱等形貌特征(图7e),说明承受了16%预拉伸变形的Al基体对疲劳裂纹的萌生具有很强的抑制作用。但疲劳断口裂纹扩展区表面光滑,可明显观察到对应于每个周次疲劳循环加载时疲劳裂纹扩展所形成的平直的疲劳辉纹,比承受3%预拉伸变形的铝板疲劳断口疲劳裂纹扩展区的疲劳辉纹更平直且辉纹间距更大(图8e)。说明当欠时效态7N01铝合金基体中的位错密度非常高且开始出现明显的胞状亚结构时,这种微观组织对疲劳裂纹扩展的阻碍作用很小。铝板的疲劳寿命相对于未预变形时仍延长了23%的原因主要是由于疲劳裂纹萌生非常困难,铝板需承受很多疲劳循环周次以后才能萌生疲劳微裂纹,而对于无缺口试样的疲劳裂纹萌生及早期扩展所对应的疲劳寿命约占材料整个疲劳寿命的90%[20]。
当预拉伸变形程度达到20%,铝板的塑形很差,延伸率仅为5.2%,晶内位错密度极高且遍布整个变形体内,并形成了大量尺寸极其细小的胞状位错亚结构(图4g),造成晶界及合金相粒子界面前沿应力集中过大,加速了疲劳裂纹萌生,疲劳断口表面中疲劳裂纹萌生区所占面积极小(图7f圆圈所示),说明承受了20%预拉伸变形的铝板在承受175 MPa脉冲疲劳加载时极易萌生疲劳裂纹。另外细小密集的位错胞壁在空间贯通桥接成为裂纹扩展的通道,有利于疲劳裂纹扩展,铝板疲劳断口表面中疲劳裂纹扩展区的疲劳台阶平直,疲劳裂纹扩展区域塑性变形痕迹较少(图8f)。因为当铝板承受的预拉伸变形程度过大时,位错强化效应使得Al基体硬度进一步增大但其塑性明显下降,疲劳裂纹尖端可越过多个晶粒,沿多个扩展面同时或交替进行,疲劳裂纹由一个扩展面转移至另一个扩展面,造成疲劳条带分布在不同高度的平面上,即形成了类似台阶的形貌[27]。经受了20%预拉伸变形的铝板疲劳失稳断裂前承受的疲劳循环周次很少,其疲劳寿命仅为2.89 × 105 cyc,说明极高位错密度以及极细小的胞状位错亚结构不仅有利于铝板的疲劳裂纹的萌生,也有利于疲劳裂纹的扩展,对铝板的疲劳性能不利。
由于疲劳裂纹瞬断撕裂区所对应的疲劳循环加载周次在板材整个疲劳寿命期内的占比极小,因此在粗略估算预拉伸变形程度对欠时效态7N01铝合金板材疲劳断裂行为的影响时可以忽略不计。则预拉伸变形对欠时效态7N01铝合金板材疲劳寿命的贡献值(λ)可半定量地由预拉伸变形量对疲劳裂纹萌生阻力的影响值(λi)及其对疲劳裂纹扩展阻力的影响值(λp)表述,即:
总结前述分析可知,承受16%预拉伸变形后的铝板中所具有的高密度位错形成的尺寸约200 nm的胞状亚结构微观组织对疲劳裂纹萌生的阻力最大,承受5%和8%预拉伸变形后的铝板疲劳裂纹萌生阻力较大,承受3%预拉伸变形后的铝板所具有的分布不均匀的低密度位错组态对疲劳裂纹萌生阻力较小,而承受20%预拉伸变形后的铝板所形成的极高密度、尺寸极其细小的胞状亚结构的微观组织对疲劳裂纹萌生非常有利。承受5%预拉伸变形后的铝板中所具有的均匀分布的适当密度的位错组态对疲劳裂纹扩展阻力最大,承受8%预拉伸变形后的铝板对疲劳裂纹扩展阻力较大,承受3%尤其是承受16%和20%预拉伸变形后的铝板位错组态对疲劳裂纹扩展起到桥接作用,因此铝板的疲劳裂纹扩展阻力极小。将不同程度预拉伸变形后欠时效态7N01铝合金板材λi、λp以及λ进行总结,结果如表1所示(“+”的数量越多代表贡献值越大)。
表1 不同程度预拉伸变形后,欠时效态7N01铝合金板材中疲劳裂纹萌生阻力贡献值(λi)、疲劳裂纹扩展阻力贡献值(λp)及疲劳寿命贡献值(λ)的分析结果
Table 1
Term | 0% | 3% | 5% | 8% | 12% | 16% | 20% |
---|---|---|---|---|---|---|---|
λi | + + + | + + | + + + + | + + + + | + + + + | + + + + + | + |
λp | + + | + + | + + + + + | + + + + | + + + | + | + |
λ | + + + + + | + + + + | + + + + + + + + + | + + + + + + + + | + + + + + + + | + + + + + + | + + |
综合上述讨论分析,总结出预拉伸变形导致的位错组态对欠时效态7N01铝合金板材疲劳裂纹扩展影响示意图(图9)。未预拉伸变形的铝板中位错密度极低,几乎不会出现位错在粗大第二相粒子前沿或晶界前沿塞积的现象,疲劳裂纹一般容易在铝板近表面处的微米级过剩结晶相粒子界面萌生,由于硬度较低、塑性较好的Al基体对疲劳裂纹扩展的阻力较小,因此疲劳裂纹沿着最大剪切应力方向扩展,但是在主裂纹扩展路径上会常常诱发出偏折的二次裂纹,在一定程度上释放了主裂纹的能量(图9a);对于承受了3%预拉伸变形的铝板,由于预拉伸变形量较小,铝板变形不均匀,导致Al基体中出现许多贯穿薄带状晶粒厚度的位错墙,这些贯穿薄带状晶粒厚度并塞积于晶界前沿的位错墙不仅促进疲劳裂纹的萌生,而且还能促进疲劳微裂纹的桥接,从而促进了疲劳裂纹扩展,疲劳主裂纹扩展过程中出现的二次裂纹较少,位错不均匀分布的Al基体对疲劳裂纹扩展的阻力较小(图9b);当铝板承受的预拉伸变形量达到5%时,基体中形成了均匀分布的位错组态(图4c),这种位错组态对疲劳裂纹萌生的阻力较大,更重要的是这种均匀分布于Al基体中的位错不仅对Al基体有一定的强化作用,同时基体还具有良好的塑性,因此在疲劳主裂纹扩展路径上容易出现许多二次裂纹,有效释放了主裂纹前沿的应力集中,促进了主裂纹尖端钝化,促使疲劳主裂纹在扩展的过程中发生多次偏折,这种均匀分布于基体的位错组态最有利于铝板韧性的发挥,因此疲劳寿命最长(图9c);当铝板承受了8%、12%和16%的预拉伸变形时,虽然基体中位错的净增殖速率变缓,位错数量增加速度变缓,但位错缠结、交割的程度逐渐增大,逐渐形成明显的胞状位错亚结构,由于应变强化使Al基体硬度和强度进一步增加但同时塑性持续降低,基体与大尺寸第二相粒子的物理性质的匹配程度增大,因此疲劳裂纹萌生的阻力相应增大;然而,高密度缠结的位错胞胞壁对疲劳裂纹扩展的桥接作用逐渐增强,因此这种具有高密度缠结位错的Al基体对疲劳裂纹扩展的阻碍作用逐渐减弱,疲劳主裂纹扩展路径中出现的二次裂纹逐渐减少(图9d~f)。承受了16%的预拉伸变形的铝板疲劳主裂纹沿着薄带状晶粒的某一个解理面扩展(图8e),疲劳寿命逐渐缩短,但仍比未承受预拉伸变形时长。当预拉伸变形量进一步增大至20%时,铝板中存在极高的位错密度和大量尺寸极其细小的胞状亚结构的位错组态对疲劳裂纹萌生和扩展都非常有利(图9g),因此疲劳寿命显著缩短,远短于未承受预拉伸变形时的疲劳寿命。
图9

图9 欠时效态7N01铝合金板材经不同程度预拉伸变形后的疲劳裂纹扩展示意图
Fig.9 Schematics of fatigue crack propagation of under-aged 7N01 aluminum alloy plate after different pre-tensile deformations
(a) undeformed (b) 3% (c) 5% (d) 8% (e) 12% (f) 16% (g) 20%
4 结论
(1) 预拉伸变形量增大至20%对欠时效态7N01铝合金板材中合金相粒子形状、尺寸、数量、分布以及薄带状晶粒的尺寸、形状无明显影响。
(2) 随预拉伸变形量的增加,欠时效态7N01铝合金板材的屈服强度、抗拉强度和显微硬度分别由未预拉伸变形的181 MPa、233 MPa和95 HV增大至预拉伸变形量20%后的254 MPa、271 MPa和117 HV,延伸率由23.2%显著降低至5.2%,表现出明显的加工硬化效应。
(3) 随预拉伸变形程度增大,欠时效态7N01铝合金板材的疲劳寿命呈先缩短再延长又缩短的趋势。未预拉伸变形铝板的疲劳寿命为6.06 × 105 cyc,3%的拉伸变形造成的不均匀位错组态导致铝板的疲劳寿命缩短至4.21 × 105 cyc;5%的拉伸变形时基体内形成最优的位错组态,导致铝板的疲劳寿命显著延长至1.06 × 106 cyc;继续增大拉伸变形量,位错组态对疲劳裂纹扩展的阻力持续减小,当拉伸变形量达到20%,高密度位错对疲劳裂纹萌生和扩展均非常有利,导致铝板的疲劳寿命显著缩短至2.89 × 105 cyc。
来源-金属学报