分享:增材制造镁合金技术现状与研究进展
镁合金具有轻质、比强度高、阻尼减振、生物相容性好、体内可降解等优点,在航空航天、汽车轻量化、生物医疗等领域应用潜力巨大。然而传统的镁合金铸造成形和变形加工技术在制备一体化复杂结构件上具有一定的局限性,制约了镁合金在上述领域的应用普及。增材制造是一种根据三维模型数据逐层熔化沉积的先进技术,有望成为镁合金复杂构件制备的重要技术途径。本文概述了近年来增材制造镁合金的研究进展,重点对选区激光熔化(SLM)和电弧增材制造(WAAM) 2种主要增材制造的工艺研发现状和影响因素、微观组织、力学性能及耐蚀行为进行分析与总结。研究表明,工艺优化后SLM和WAAM等技术均可获得致密度> 99%的镁合金试件,并且能够获得与传统制造镁合金相当的力学性能和耐蚀性能,增材制造镁合金表现出极大的工程应用潜力。最后,从材料优化、工艺改进及性能评价等方面对增材制造在镁合金中的未来发展趋势与研究方向进行了总结与展望。
关键词:
由于能源消耗、环境污染等问题日益严重,镁合金作为轻量化结构材料逐步进入人们的视线。镁合金具有密度低、比强度高、阻尼减振、生物相容性好、体内可降解等优点,在航空航天、汽车工业、生物医学等领域应用潜力巨大[1,2]。为了满足现代制造业对低能耗、高效率和高性能的需求,生产薄壁异形等复杂结构的零件成为镁合金应用的重要趋势。但拥有复杂结构的整体结构件难以通过传统铸造方式制造,因此需要开发新的镁合金部件成型技术。
增材制造(又称3D打印)技术因无需模具、实现复杂设计、成形精度高等优点作为第三次工业革命的代表性技术之一,受到了工业界和商业界的广泛关注[3]。美国材料与试验协会(ASTM)在2009年成立的3D打印技术委员会(F42国际委员会)对3D打印有明确的定义:3D打印是依据三维计算机辅助设计(CAD)模型数据将材料逐层累加制作物体的过程。3D打印技术集成了CAD技术、计算机辅助制造(CAM)技术、计算机数控(CNC)技术、激光技术和材料技术等多门学科[4,5],逐渐成为近年来世界各国研究的热点和重点技术[6,7]。
现阶段镁合金增材制造技术的研究主要集中在选区激光熔化(selective laser melting,SLM)技术和电弧增材制造(wire and arc additive manufacturing,WAAM)技术方面。与传统铸造相比,增材制造镁合金具有无需模具、复杂成形、节省原材料、智能化及轻量化等优点[7],尤其在具有复杂拓扑结构设计的医疗器械产品以及大尺寸航空航天异型构件的制备中具有独特优势[8~11]。然而,镁合金由于具有高反射性,导致能量吸收率低,并且粉末原材料具有易燃易爆的本征特性,大大限制了镁合金增材制造技术的发展。与钢、铝合金、钛合金、高温合金等其他常用合金相比,有关镁合金增材制造的研究起步较晚,技术发展还非常有限。因此寻求一种能够安全稳定实现复杂结构成形的方法是增材制造镁合金研究领域亟需攻克的难题。鉴于此,本文调研镁合金增材制造技术的发展和应用现状,聚焦增材制造镁合金材料性能及工艺优化方面的研究进展,并从材料成分设计、工艺等方面对未来发展趋势进行展望,旨在为促进镁合金增材制造研发提供研究思路和参考。
1 镁合金增材制备技术发展现状及应用
目前SLM和WAAM是镁合金增材制造最常采用也是发展最为成熟的2种技术。致密度通常作为检验成形质量和优化工艺参数的手段,也可用于预防不适当的加工条件导致成形缺陷。成形件内部的缺陷会影响镁合金成形件整体力学性能[12,13]。因此可以通过更稳定的生产过程及增加致密度来获得更好的成形质量[14]。采用增材制造技术已经能够制备相对密度高达99.9%以上的镁合金[15,16]。下面对几种主要的镁合金增材制造技术研究进展加以论述。
1.1 SLM技术研究进展
SLM作为一种新型的激光增材制造技术,以激光为热源、金属粉末为原材料,采用逐点、逐线、逐层的成形方式,制造出生产周期短、灵活性好、精度高且形状复杂的小批量个性化定制零件。因其在成形时具有较大的温度梯度,可获得细小的显微组织,通过细晶强化改善镁合金内部组织和材料性能。SLM成形的主要步骤如图1a所示,首先在CAD软件上对零件进行分层并设计逐层扫描轨迹;随后将镁合金粉末平铺在成形基板上,逐层成形直至最终完成零件的制造。成形过程中充入保护气氛,防止镁合金在增材制造过程中发生氧化和烧结。层与层之间的扫描策略对成形质量和微观组织产生显著影响,当层内和层间的扫描方向都相同的情况下,堆积效应较为明显,试样的组织中出现沿打印构建方向的粗大柱状晶组织,且材料的织构也较为明显。SLM常用的扫描策略如图1b所示。目前激光增材制造镁合金主要采用往返扫描策略,相邻层扫描方向旋转45°、67°或90°以获得良好的致密度。然而由于Mg的特性,在SLM工艺过程中主要有以下2方面缺陷需要改善:(1) Mg的沸点较低(约1093℃)、饱和蒸气压高,打印过程中比其他金属粉末更易出现金属蒸气,影响后续激光能量输入;(2) Mg粉末化学性质活泼,容易生产氧化物夹杂,影响样件层间结合力。
图1

图1 选区激光熔化(SLM)成形过程示意图及其在镁合金研究中的常用扫描策略
Fig.1 Illustration of the selective laser melting (SLM) process (a) and general scanning strategy used for SLMed magnesium alloys (b)
SLM技术已用于制备多种镁合金,如纯Mg、Mg-Al、Mg-Zn、Mg-Al-Zn及Mg-RE (RE:稀土元素)[17~25]等。通过控制原材料粉末、成形工艺参数和开发后处理工艺等,不断获得了低缺陷、高致密度的成形质量。如胡国文[26]研究了Mg粉的颗粒尺寸对SLM镁合金性能的影响,发现粒度为400目(中值粒径D50 = 25.85 μm)的Mg粉比粒度为250目(D50 = 43.32 μm)的Mg粉所需激光能量更低,2种试样的相对密度均超过95%。通过拓扑分析、致密度和显微硬度的比较得出,250目粉末制成的块状镁合金试样比400目粉末有更优的成形性和力学性能。在相同能量输入条件下,细粉末较高的熔池温度容易导致更严重的氧化现象。粉末原材料尺寸还会影响打印过程中的激光反射率,粗颗粒较细颗粒具有更高的激光反射率,目前,研究中使用的激光增材制造镁合金粉末多为球状粉末,粉末粒度在30~100 μm之间。添加高激光吸收率材料(如碳纳米管(CNT)、石墨烯)可以有效提高镁合金粉末对激光的吸收率。Wu和Wang[27]通过SLM制造了CNT/AZ31B复合材料,发现将1.5% (质量分数)的碳纳米管混合到AZ31B合金粉末中,激光吸收提高了7.9%,从而在较低的温度下实现了CNT/AZ31B复合材料熔池的完全熔融状态。
影响SLM成形的主要工艺参数包括激光功率、扫描速率、扫描间距和铺粉层厚度等,这4个参数可统一化为体积能量密度(η,J/mm-3),其公式表达为[28,29]:
式中,
图2
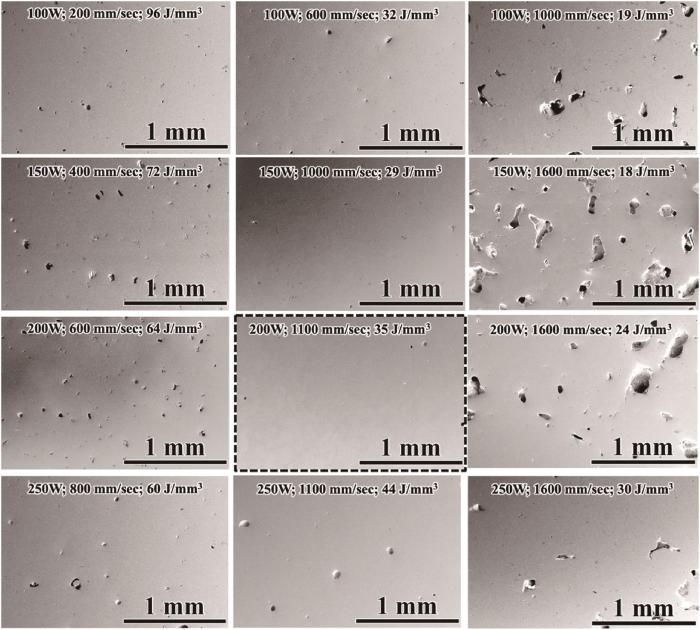
图2 不同激光功率和扫描速率对WE43合金内部缺陷的影响[23]
Fig.2 SEM images from WE43 samples produced with various laser powers (P) and scan rates (v) of SLM[23]
控制激光能量密度可以有效控制镁合金的硬度,并且硬度与晶粒尺寸间呈线性关系。在相同晶粒尺寸条件下,连续激光束制备的镁合金硬度低于脉冲激光束。增加能量密度会导致SLM制备镁合金表面粗糙度增加、晶粒粗化以及材料平均硬度降低等现象[20,34]。图3[35]为激光增材制造Mg-Al合金工艺参数窗口的研究过程图。通过观察制备过程中的现象,将工艺参数分为多个窗口,研究激光工艺参数以及对应的能量密度对激光增材制造镁合金的影响[35]。结果表明,当激光功率高到一定程度时激光作用区内粉末材料急速升温,能量来不及扩散形成金属蒸气,金属蒸气容易与粉末材料中的空气作用形成飞溅现象,如图4a[24]所示。并且局部区域能量密度高,容易生成大尺寸熔池,凝固后易在表面形成凹凸不平的烧结界面。激光功率较低时致使能量不足以熔化粉末层,容易产生熔融不充分等凝固缺陷,样件层间容易产生宏观裂纹,如图4b[24]所示。此外,激光光斑停留时间长,使局部区域充分熔融,降低
图3
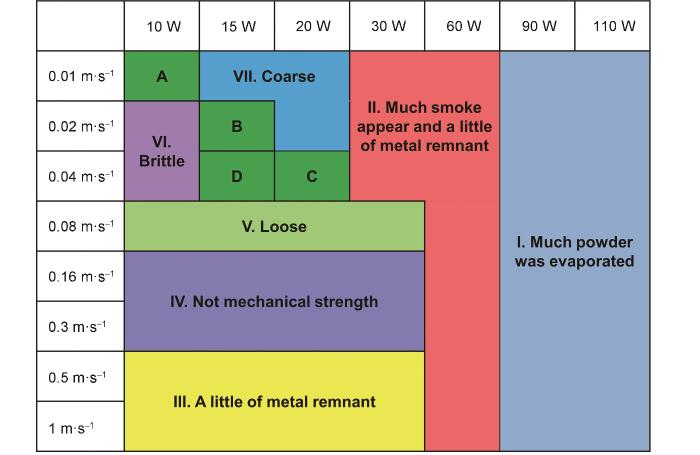
图3 激光功率和扫描速率对Mg-9%Al合金影响的研究过程[35]
Fig.3 Process map for Mg-9%Al, results as function of the range of laser power and scan rate[35]
图4
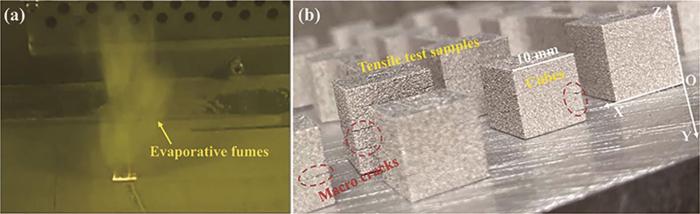
图4 SLM过程中镁金属蒸气及样件宏观裂纹现象[24]
Fig.4 Evaporative fumes during the SLM process of Mg vapor (a) and macro cracks observed on the as built samples (b)[24]
表1[21~25,35~42]总结了近年来SLM成形镁合金的研究进展,包含了主要镁合金牌号和对应制备的最优工艺参数。从表中数据可以看出,SLM制备镁合金的致密度大部分可达到98%以上,但不同合金体系之间存在差异,如Mg-Al和Mg-Zn体系合金的致密度普遍低于激光烧结制备的Mg-RE体系合金,不同工作报道的WE43合金的致密度均已达到99.4%以上。此外,SLM镁合金成形质量受控于多种影响因素,合金粉末质量、激光源、保护气体、不同品牌设备等均会造成额外影响,导致表中同牌号镁合金的最佳工艺参数存在较大差异。综上所述,在将来一段时间内,SLM镁合金研究仍需考虑各影响因素之间的综合作用,以及产品质量和生产效率等因素,进一步完善和优化工艺参数窗口区间。
表1 文献中Mg与镁合金SLM过程参数优化情况[21~25,35~42]
Table 1
Material | Laser power | Layer thickness | Hatch spacing | Scan rate | Relative density | Ref. |
---|---|---|---|---|---|---|
W | μm | μm | mm·s-1 | % | ||
Mg | 90 | 30 | 100 | 100 | 96.13 | [36] |
AZ31 | 75 | 50 | 100 | 125 | > 99.50 | [37] |
AZ61 | 150 | 40 | 60 | 400 | 99.40 | [21] |
Mg-9Al | 15 | 50 | 80 | 20 | 82.00 | [35] |
AZ91D | 200 | 40 | 90 | 330 | 99.52 | [22] |
AZ91D | 50 | 30 | 30 | 200 | 98.10 | [38] |
ZK60 | 50 | 100 | 100 | 500 | 97.40 | [39] |
ZK60 | 50 | 20 | 80 | 600 | 98.00 | [40] |
WE43 | 300 | 30 | 40 | 1200 | 99.40 | [41] |
WE43 | 195 | 30 | 200 | 800 | 99.60 | [42] |
WE43 | 200 | 40 | 130 | 1100 | 99.70 | [23] |
GZ112K | 80 | 30 | 100 | 300 | 99.95 | [25] |
GWZ1031K | 80 | 30 | 100 | 200 | 97.85 | [24] |
1.2 电弧增材制造技术研究进展
WAAM技术是与SLM技术同时发展的另一种镁合金增材制造技术,成形时主要以电弧为热源,根据零件的实体模型规划成形路径,通过送丝系统在机械臂等位移设备下带动焊枪,按规划好的路径自下而上逐步成形[43]。如图5[44]所示,WAAM以丝材为原材料,避免了金属Mg粉末易燃易爆的风险,具有高沉积速率、低设备成本、高材料利用率和成本低廉等优势,对于大型零件的制造潜力巨大,因而在镁合金领域具有独特优势[45]。WAAM常用Ar作为保护气,因为其具有相对更大的电离势能,有利于提高电弧温度并增加冷却速率[46]。表2[47]对比总结了WAAM与SLM技术各自在镁合金增材制造方面的特点,WAAM较SLM具有更高的成形效率和更高的材料利用率,成形零件由全焊缝构成,化学成分均匀且致密度高,开放的成形环境对成型件尺寸无限制,成形速率可达2 kg/h以上[48]。但WAAM仍面临控形能力差且容易生成粗大晶粒等缺点,成形件的精度和性能往往低于SLM技术,需要二次机加工。
图5
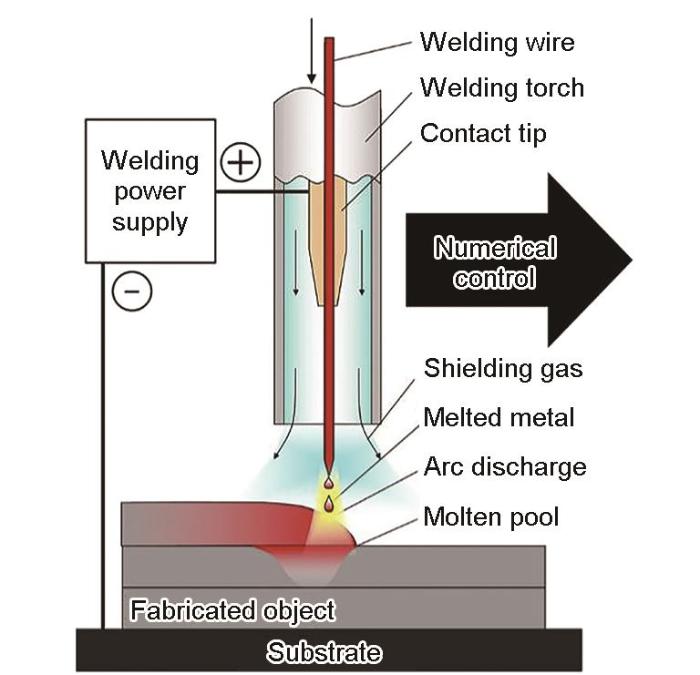
图5 镁合金电弧增材制造(WAAM)成形工艺示意图[44]
Fig.5 Schematic of wire and arc additive manufacturing (WAAM)[44]
表2 SLM和WAAM技术特点对比[47]
Table 2
Method | Raw material | Deposition rate | Material | Manufacturing | Manufacturing | Subsequent | Applicable |
---|---|---|---|---|---|---|---|
kg·h-1 | utilization | cost | accuracy | machining | workpiece | ||
rate | mm | ||||||
SLM | Mg powder | 0.1-0.2 (low) | 10%-60% | High | 0.05 (high) | Unnecessary | Complex, |
(low) | small workpieces | ||||||
WAAM | Mg filler | > 2 (high) | 90% (high) | Low | 0.2 (low) | Necessary | General, |
wire | large workpieces |
目前,用于镁合金电弧增材制造研究的热源方式主要有钨极惰性气体保护焊(tungsten inert gas welding,TIG)和熔化极气体保护焊(melt inert gas welding,MIG) 2种。TIG技术基础是填丝钨极氩弧多层多道焊,由稳定的钨极氩弧提供电弧熔化热,同时具备配合独立于焊接设备的同步侧向送丝系统,具有飞溅较小、独立控制热源等优点。而MIG技术则具备金属丝与电弧同轴的优势,可确保送丝与运动方向的相位关系,可搭配高自由度的机械臂进行复杂结构件成形。其中,基于MIG技术发展的冷金属过渡(CMT)技术近几年在电弧增材制造领域受到广泛关注。相比传统MIG,CMT技术在数字控制方式下实现了断电弧和焊丝间断输送的监控,具有低热输入、无飞溅等特点。其送丝运动与熔滴过渡过程可进行数字化协调,被认为是完善电弧增材制造技术的一个主要技术方向[49]。
WAAM成形的工艺参数主要有电流、波形、送丝速率、焊接速率等,通过对这些工艺参数的调控,可以优化加工过程中的热输入、温度梯度、冷却速率、层宽、层高等参数,进而实现对组织、性能和缺陷的控制[47]。制备高性能镁合金一直都是镁合金增材制造技术的目标之一,而合理的电弧增材成形工艺参数是影响成形质量的关键因素,研究者们针对工艺参数优化进行了大量工作。相比SLM技术,电弧增材镁合金的影响参数较多且起步较晚,当前工艺参数的研究主要仍通过试错法,镁合金的WAAM成形工艺参数尚未建立成熟的技术积累和理论认识,一般都以结合金属焊接的理论体系来解释WAAM成形合金中的微观组织特点。Guo等[50]基于TIG技术成功制备了致密的AZ31镁合金样件,并重点研究了电流脉冲频率对镁合金样品的影响,结果表明提高脉冲频率将导致熔池共振,进而影响镁合金凝固速率,其中在5~10 Hz范围时可达到最佳的晶粒细化效果。Ying等[51]在对TIG成形AZ61镁合金进行工艺参数优化过程中发现,过高的焊接电流会导致晶粒变大缺陷增多,并指出焊接电流和焊枪进给速率的优化组合对改善微观组织、提升合金性能的有效性。通常,电流增大直接提升熔化速率,而提高送丝速率则缩短焊丝熔化的时间。最近,Guo等[52,53]采用TIG工艺成功制备了多层AZ80M镁合金单道焊壁并保持良好形状,如图6[53]所示,指出TIG堆焊层间温度对沉积层宽度有着重要影响,在电弧增材过程中镁基板急剧升温并稳定在150℃,而沉积宽度亦在前几层增大之后保持稳定。
图6
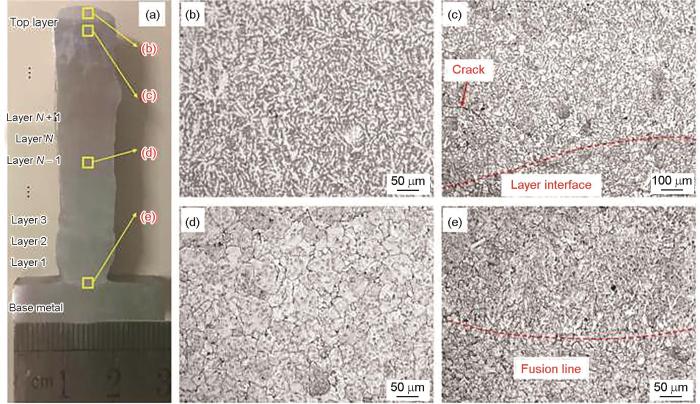
图6 WAAM成形AZ80M样品沉积壁横截面的微观组织[53]
Fig.6 Cross-section view and microstructures of the TIG-based WAAM AZ80M wall[53] (TIG—tungsten inert gas welding)
(a) overall microstructure (b) top arc zone
(c) interlayer transition region (d) intermediate zone (e) bottom zone
在MIG技术方面,Takagi等[44]开展了AZ31B镁合金成形工艺参数优化研究,获得几乎无缺陷的成形质量,CT扫描数据结果显示40 mm × 60 mm × 35 mm的打印样件孔隙率不足0.01%。该工作表明焊枪进给速率是影响WAAM镁合金成形质量的关键参数,过低的焊枪进给速率会导致成形件缺陷增多;提升焊枪进给速率能够降低单位面积的热量输入,抑制晶粒长大从而得到更精细的微观组织。Wang等[54]通过控制CMT电流和电压研究能量输入模式对AZ31沉积焊缝效果的影响,如图7[54]所示。可见,在能量相近情况下,输入模式会影响镁合金焊缝的表面效果、熔深及润湿度等。使用具有强脉冲的输入模式(characteristic 1)可获得具有良好润湿性及热影响区较小的沉积焊缝,对提升镁合金WAAM的控形能力和零件成形质量均有积极作用。Ying等[51]对CMT电弧增材工艺参数进行了探究,结果表明采用较低的输入电流及电压(130 A,12.6 V),以及相对慢的送丝速率(820 mm/min)可实现高致密度AZ61镁合金样件制备,孔隙率仅为0.03%左右。Bi等[55]在AZ91电弧增材过程中,电弧采用三角式前进的扫描策略,借助CMT电弧较大的电磁力给予熔池搅拌的效果,打碎熔池中的枝晶并使熔池温度均匀化,从而成功制备了等轴细晶和无缺陷的样件。
图7

图7 冷金属过渡(CMT)能量输入模式对AZ31单道沉积焊缝外观及形状尺寸的影响[54]
Fig.7 Effect of CMT characteristics on energy input process (a) and subsequent weld appearances (left) and weld geometries (right) (b-d) of the deposited weld beads (CMT—cold metal transfer, α—wetting angle)[54]
表3[44,50~57]汇总了已报道的镁合金电弧增材制造工艺参数优化情况,常见参数包括了送丝速率、电弧运动速率、输入电流、逐层堆焊的间隔时间以及保护气体流速。值得注意的是,由于镁合金较低的比热容,在电弧增材过程中容易升温软化,因此每层之间普遍需要间隔较长时间(90~180 s)以保证充分散热。此外,由于镁合金hcp结构变形加工困难的特性,镁合金丝材制备难度较高,目前研究用的镁合金丝材仅限于较易塑性变形的Mg-Al体系(如表3[44,50~57]所示);然而用于生物医疗的Mg-Zn系[9,10]和航天航空用Mg-RE系[1]镁合金丝材制备工艺还研究较少。因此若能突破更多种类镁合金丝材制备技术,将对推动镁合金增材制造技术的应用具有重要意义。
表3 文献中不同镁合金WAAM最优工艺参数[44,50~57]
Table 3
Method | Alloy | Wire feed rate | Travel speed | Peak current | Dwell time | Ar flow rate | Ref. |
---|---|---|---|---|---|---|---|
m·min-1 | mm·min-1 | A | s | L·min-1 | |||
TIG | AZ31 | 2.00 | 200 | 136 | - | 20 | [50] |
AZ61 | 0.82 | - | 130 | - | - | [51] | |
AZ80 | 1.15 | 300 | 100-120 | 160 | 17-20 | [52,53] | |
MIG/CMT | AZ31 | - | 600 | 350 | 180 | 18 | [54] |
AZ31 | - | 800 | 100 | 20 | 25 | [44] | |
AZ61 | 1.8 | 270 | 68 | 90 | 18 | [56] | |
AEX11 | 2.2 | 720 | 51 | - | 14 | [57] | |
AZ91D | 12 | 600 | - | 180 | 15 | [55] |
1.3 其他增材制备镁合金技术研究
2010年Ng等[58]首次报道了镁合金的增材制造研究,成功实现了纯Mg的单轨熔融沉积。随后,增材制造由于较高的尺寸精度和复杂的结构设计在镁合金研究领域引起了广泛的关注,除SLM和WAAM 2种技术之外,国内外研究者们还探索了其他镁合金增材制造技术。
选择性激光烧结(selective laser sintering,SLS)是另一种以粉末为原材料的增材制造技术,利用激光烧结粉末颗粒,使材料结合在一起形成固体结构[59]。SLS和SLM的主要区别在于后者采用激光热源将粉末颗粒完全熔化,而SLS中的粉末颗粒是部分熔化和再凝固。SLS技术目前主要在生物医用镁合金领域开展了少量研究。Tsai等[60]将硅酸镁钙(Mg-CS)粉末掺入聚ε-己内酯(PCL)中,采用SLS工艺制备三维多孔生物活性Mg-CS/PCL支架。Mg-CS粉的掺入提高了PCL的润湿性与降解率,且Mg-CS的添加显著促进了新生骨的生长。采用SLS工艺制备的掺杂MgO纳米颗粒(nMgO)的PLLA/3nMgO (PLLA—结晶型聚合物)支架被证实具有良好的结晶度和亲和性,抗拉强度、弹性模量和Vickers硬度分别比PLLA提高了38%、24%和11%[61]。此外,nMgO中和了PLLA的酸降解副产物,可以防止植入后局部组织的排异。Sun等[61]将硅灰石(CaSiO3)加入到Mg2SiO2中,通过SLS制备MgO-CaO-SiO2支架。构建的支架具有良好的多孔网络连接,细胞黏附和增殖良好,nMgO的存在赋予了支架强大的抗细菌活性。然而SLS工艺由于颗粒部分熔融,容易形成层状缺陷,成形质量较差,导致制备的医用材料力学性能相对较低。如上述SLS制备的MgO-CaO-SiO2支架,其最小成形精度约为1 mm,压缩强度为30~42 MPa[61]。目前SLS技术在镁合金结构件制备方面的研究报道还较少。
黏结剂喷射增材制造采用液态或固态的聚合黏合剂将粉末颗粒黏附,颗粒与选择性沉积的溶液反应,在特定区域粘接在一起[62]。与其他使用粉末原材料的增材制造方法相同,打印件在粉末床内是自支撑的,在该过程完成后将未黏结粉末移除。随后通过脱脂工艺去除黏结剂,然后进行烧结[63~65]、浸润和热等静压(HIP)[66]等致密化后处理工艺。Salehi等[67]开发了一种毛细管驱动的桥接方法,有助于将镁合金颗粒快速成形为复杂结构的3D打印件。该方法通过溶剂与Mg粉最外层的MgO膜发生化学反应,生成富含MgCO3·3H2O粒子间桥。在后续烧结过程粒子间桥将完全受热分解,消除了聚合物黏合剂对成形样品的影响,并成功制备了纯Mg结构件,如图8[67]所示。此方法最大的优点是不需要使用牺牲型黏合剂将粉末粘合,因此可省略黏合剂去除工序,并且不会有杂质残留影响成型件的合金成分。黏结剂喷射工艺制备的零件基本上是胶合在一起的颗粒,导致脆性结构增加和力学性能下降。在黏结剂喷射中,由于黏结的方法,材料的特性通常不适合结构部件,尽管成形的相对速率较快,但额外的后处理仍会增加整体制造时间。
图8
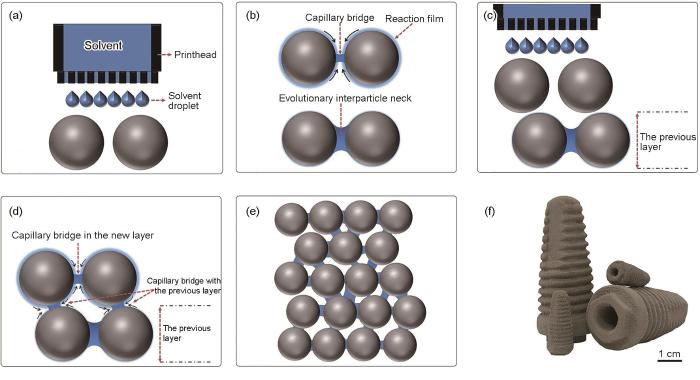
图8 基于毛细管驱动桥接的增材制造原理示意图以及该技术制备的纯Mg零件[67]
Fig.8 Schematics showing the principle of capillary-mediated binderless 3D printing (a-e) and macrograph of printed pure Mg parts (f)[67]
此外,间接渗透法可以作为一种间接增材制造方法用于镁合金的三维制造。此方法首先通过增材制造的方法获得具有理想结构的三维CAD模型的正聚模板,将NaCl浆糊浸润模板后通过加热去除模板,并将NaCl烧结形成负NaCl模板。施加压力将液态Mg浇注到模板中,然后溶解NaCl,最终得到合金成形件。Staiger等[68]利用渗透法成功制备了具有宏观特征精细结构的开孔多孔镁合金构件。Nguyen等[69]也制造了拓扑有序结构的多孔镁合金结构件,并且证实镁合金最终成形件的尺寸与CAD模型尺寸相差2.5%~8.3%。渗透法的优点是不需要使用具有挥发性和爆炸性的Mg粉,降低制备过程的危险性。然而渗透法制备成形件的几何形貌局限于宏观尺度,需要具有微米级孔隙和支板的开放多孔结构才能实现良好的综合性能,因此在很多应用中并不适用。此外,在间接制造镁合金结构的过程中,不同成形件之间的拓扑结构差异导致了孔隙尺寸和支撑厚度的差异,这极大地影响了力学性能的完整性。
2 增材制造镁合金组织和性能研究进展
2.1 微观组织
增材制造镁合金的微观组织主要由原材料化学成分和工艺条件共同决定。与传统铸造相比,SLM凝固过程的冷却速率快,据测量可达103~104 K/s[22],导致在铝、钛、铜等合金中沿沉积方向普遍生成典型的柱状晶结构[28]。然而与上述合金不同,SLM镁合金在快速冷却条件下并未生成柱状晶,而仍以细小等轴晶为主。Zumdick等[70]对SLM制备的WE43镁合金微观组织进行研究,并分别与挤压态和铸态合金样品微观组织进行比较。通过不同截面方向观察确认,SLM镁合金微观组织呈均匀等轴晶形态,与铸态样品平均44 μm的晶粒尺寸相比,SLM法制备WE43的晶粒尺寸只有0.4~2.9 μm,如图9[70]所示。Wei等[22]报道了SLM制备的AZ91D镁合金具有细小等轴晶的现象,平均晶粒尺寸为1.2 μm,而压铸法制备的平均晶粒尺寸为57 μm。Zhang等[71]亦发现激光单道次重熔后的EV31镁合金晶粒尺寸从75 μm细化至3.5 μm。根据StJohn等[72,73]的相互依存理论,一方面镁合金中常用溶质元素如Al、Zn、RE及Zr等均可产生较高的成分过冷抑制晶粒生长,另一方面SLM的高温度梯度可激活更多的晶粒形核点,因此SLM镁合金中固有的晶粒细化是高冷却速率与高成分过冷共同作用的结果。
图9
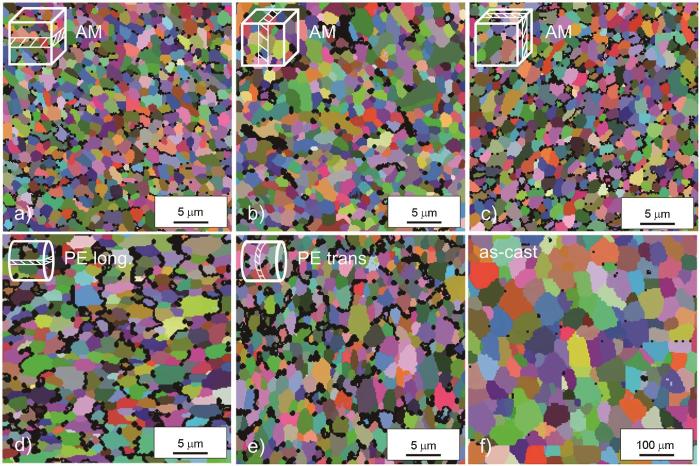
图9 SLM技术、粉末挤压及铸态WE43镁合金晶粒尺寸比较[70]
Fig.9 Electron backscatter diffraction images showing grain sizes of SLMed WE43 sample (a-c), powder extruded sample (d, e), and as-cast WE43 sample (f) (AM—additive manufacturing, PE—powder extruded)[70]
SLM制备的AZ91D镁合金微观组织如图10[22]所示。离散共晶相Mg17Al12均匀分布在α-Mg的晶界处,其中熔池重叠区域(OLR)的组织明显较熔池边缘区域(CST)更为粗大,这是由于OLR区域经历多次的热循环及较低的冷却速率,导致第二相粗化。此外,SLM制备的AZ91D合金经历了非平衡凝固过程,Al溶质在α-Mg基体中溶解度被扩大,其固溶体中Al含量显著高于传统压铸态合金[22]。SLM对WE43合金微观组织的影响被广泛报道,并且结果较为一致[23,42,70,74,75]。Zumdick等[70]比较了选择性激光烧结和铸态WE43合金微观组织,发现打印态WE43的微观组织不受打印方向影响,并且具有相比铸态更密集的第二相分布在基体中(图11[70])。Gangireddy等[42]表征结果表明,打印态微观组织主要由富含Y和Zr的氧化物、Mg-Nd沉淀相及Mg-Y沉淀相组成(图12[42]),氧化物呈薄片状和块状,在变形过程中将容易产生应力集中。Hyer等[23]进一步研究表明,圆球状Mg-Nd沉淀相为β1-Mg3Nd,但富Y的沉淀相却是Y2O3氧化物。
图10
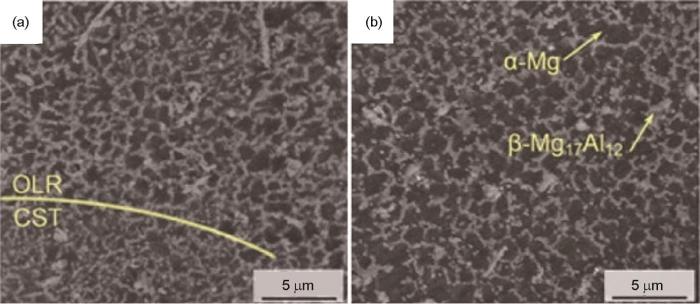
图10 166.7 J/m3能量密度下获得的AZ91镁合金微观组织的SEM像[22]
Fig.10 SEM images showing the cross section (a) and the vertical section (b) microstructures of the AZ91D sample built at 166.7 J/m3[22] (OLR—overlapping region, CST—center of scanning track)
图11

图11 SLM制备WE43合金不同方向截面微观组织与传统铸态WE43合金微观组织对比[70]
Fig.11 SEM images showing microstructures of SLMed WE43 sample (a-c) in compared with as-cast WE43 sample (d-f)[70]
图12
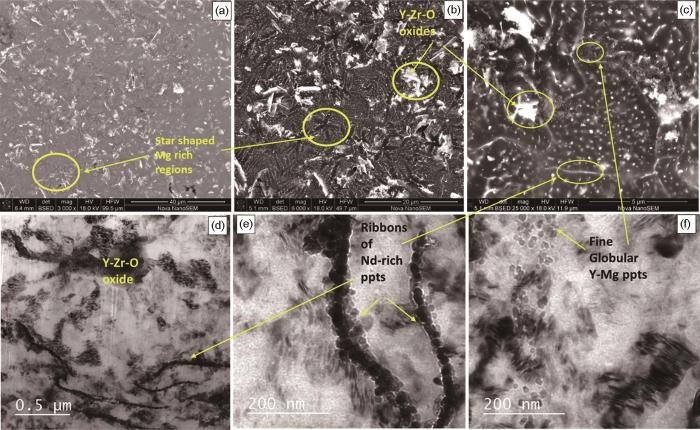
图12 SLM制备的WE43合金微观组织的BSE像以及TEM像[42]
Fig.12 BSE (a-c) and TEM (d-f) images of microstructures of SLMed WE43 sample[42] (ppts—precipitates)
与SLM技术相比,电弧增材成形的本质是微铸自由熔积成形,逐点控制熔池的凝固组织可减少或避免成分的偏析及凝固裂纹等缺陷[49]。但由于电弧热输入较高,WAAM成型过程中熔池和热影响区域(HAZ)尺寸较大,并且随着成形高度累积,散热条件变化导致每层热历程不尽相同,因而WAAM成形镁合金不同区域组织形貌具有较明显的差异。如Takagi等[44]采用MIG-WAAM技术制备AZ31B镁合金样件,观察到样品不同区域宏观形貌差异如图13[44]所示。底部区域由于热耗散条件最好,因而呈现细小晶粒,尺寸不足20 μm。而随着成形层厚增加,基体热沉作用减弱,温度梯度减小导致晶粒显著粗化。Yang等[76]对CMT-WAAM成形AZ31微观组织演变过程进行研究。其结果显示样品底部靠近基板至顶部晶粒形貌具有逐渐由柱状枝晶向等轴枝晶转变的现象,且平均枝晶间距由底部17 μm增至顶部39 μm,并认为产生该现象的原因是当熔池温度梯度逐渐降低时,一次枝晶臂会深入液体更长距离,并在横向也会发生成分过冷,使得二次枝晶臂出现在一次枝晶上,从而使得不同区域的晶粒组织产生差别。Wang等[54]亦在电弧增材AZ31熔积层中观察到平行于堆焊方向的柱状枝晶结构,如图14a[54]所示。然而与熔积层不同,图14b和c[54]显示热影响区晶粒更粗大,且柱状晶趋向于沿电弧移动方向生长。
图13

图13 电弧增材AZ31B镁合金不同区域宏观组织形貌以及晶粒尺寸结果[44]
Fig.13 Cross-section microstructure of WAAM fabricated AZ31B sample (a), trends in as-measured grain size of fabricated object corresponding to torch feed speed (b), and OM images showing the top layer (c), central part (d), and boundary (e) of fabricated object with processing parameter of 100 A, 10 V, and F = 400 mm/min (HAZ—heat affected zone)[44]
图14
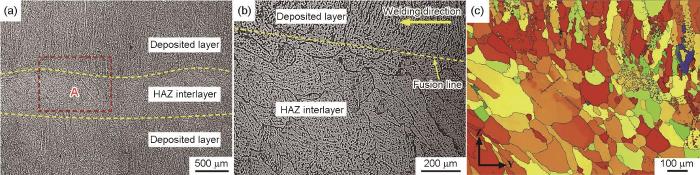
图14 CMT-WAAM成形AZ31镁合金熔积层与热影响区微观组织的OM和EBSD像[54]
Fig.14 OM images showing the interlayer microstructures of WAAM AZ31 component (a, b), and EBSD image corresponded to the area in Fig.14b (c)[54]
区别于AZ31镁合金,电弧增材AZ61[56]、AZ80[52]、AZ91[55]等镁合金所报道的微观组织均以等轴晶粒为主,且不同层数间、熔积层与热影响区之间组织差异更小。Klein等[56]研究结果显示电弧增材AZ61镁合金熔积层与热影响区微观组织一致,平均晶粒尺寸分别为27.3和29.2 μm。Bi等[55]在CMT电弧增材AZ91中亦观察到类似现象,不同层数区域之间显微组织为尺寸相近的等轴晶粒;上述结果表明随着镁合金中Al溶质含量增加,合金成分过冷增加,抑制了电弧增材过程中晶粒长大的作用增强。图15[51]进一步揭示了典型的电弧增材Mg-Al合金的微观组织特征。与传统铸造相比,WAAM Mg-Al合金第二相体积占比显著降低,只有少量球状Mg17Al12相及Al8Mn5相分布在晶界处。Guo等[52]报道了电弧增材制造AZ80M镁合金过程中温度变化过程,基板在邻近数层堆焊过程的温度峰值超过了Mg17Al12相的共晶温度(437℃),随后逐渐衰减稳定在150℃。该结果表明电弧增材的热沉作用对Mg-Al合金产生了近似固溶处理的效果,在反复受热过程Mg-Al第二相重新溶于Mg基体,体积占比减少。并且在受热过程,AZ系列镁合金缺乏热稳定相钉扎晶界,导致晶粒逐渐粗大。
图15
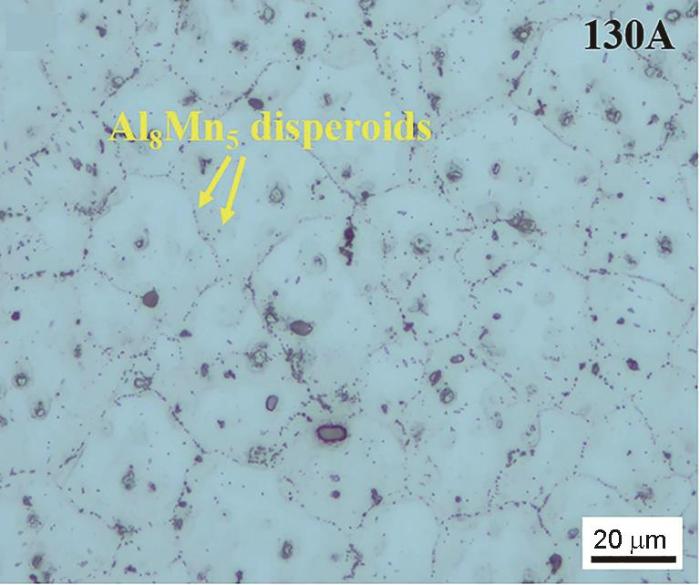
图15 电弧增材成形AZ61合金第二相的OM像[51]
Fig.15 OM image showing the microstructure of AZ61 alloy fabricated by WAAM[51]
2.2 力学性能
目前,大部分增材制造镁合金研究仍处于样件打印阶段,力学性能研究主要以拉伸性能表征为主。图16[21~25,51,52,54~57,76,77]汇总了文献报道的SLM和WAAM 2种主流增材成形技术制造的镁合金拉伸性能数据,同时囊括了同牌号的铸造及变形镁合金的性能数据以作比较。如上所述,增材制造由于快速凝固以及复杂的循环热历程等特性,使得成形镁合金微观组织有别于传统成形技术,对合金强度、韧性、延展性、硬度和耐蚀性等具有显著的影响。在SLM制备镁合金过程中,一方面固有的高冷却速率致使合金晶粒普遍较传统制备方法更细小,另一方面由于垂直于基板方向的热流梯度最大,选区激光熔化的hcp结构金属优先沿<
图16

图16 增材制造及传统制造镁合金拉伸强度与延伸率关系图[21~25,51,52,54~57,76,77]
Fig.16 Summary chart showing the yield strength (a) and ultimate tensile strength (b) vs elongation to failure for Mg alloys manufactured by different methods (Data extracted from Refs.[21-25,51,52,54-57,76,77], LD—longitudinal direction, TD—transverse direction)
在电弧增材制造方面,图16[21~25,51,52,54~57,76,77]汇总结果显示WAAM成形镁合金在韧性上具有一定优势,其延展性范围在10%~28%,但其强度偏低。其中,屈服强度区间在100~160 MPa,抗拉强度区间在220~305 MPa,与铸造镁合金持平但低于同牌号变形镁合金及SLM镁合金。结合2.1节中增材制造镁合金微观组织的表征结果,造成目前WAAM镁合金强度较低主要可归因于晶界强化相数量的显著减少以及成形过程中晶粒粗化现象。由图15[51]揭示的WAAM镁合金典型微观形貌可知,Mg-Al合金主要晶界强化相β-Mg17Al12含量相对铸态显著降低,只有少量球状相分布在晶界处,无法提供有效的强化效果。Guo等[52]研究发现增材制造镁合金受热的温度峰值超过了Mg17Al12相的共晶温度(437℃),然后逐渐衰减并稳定在150℃左右,表明大部分凝固析出的Mg17Al12相在电弧增材热沉作用下会重新固溶于Mg基体,因此晶界强化相含量减少,并且Al溶质在Mg基体中固溶强化效果极为有限,无法补偿Mg17Al12析出相的强化作用。此外,150℃亦接近Mg-Al合金退火温度,凝固过程中急速冷却积累的内应力在该温度下得到充分释放,合金强度、硬度亦伴随一定程度降低。另一方面,根据图13[44]所示,电弧增材AZ31镁合金底部平均晶粒尺寸不足20 μm,然而随着成形高度增加其晶粒尺寸逐渐增大至60 μm以上。这是由于镁合金比热容较小,在成形过程热耗散条件减弱,且Mg-Al合金缺乏热稳定相钉扎晶界,导致晶粒逐渐粗大,合金强度进一步降低。
针对上述原因,Gneiger等[57]研究了添加微量Ca和富Ce稀土元素下电弧增材Mg-Al合金的强化现象,通过电弧增材制备的AEX11合金在时效处理后抗拉强度约为300 MPa。Gneiger等[57]认为强化机制主要来自于Al2Ca和Al-RE等热稳定相的弥散增强作用。此外,WAAM成形镁合金面临的另一个问题是性能的各向异性。Yang等[76]报道了电弧增材AZ31合金在LD方向的抗拉强度为210.5 MPa,延伸率为10.6%;而在TD方向的拉伸强度只有151.9 MPa,延伸率为7.5%。Guo等[53]制备的AZ80M镁合金在TD方向抗拉强度为308.7 MPa,而在LD方向只有237.3 MPa。后续研究[80]表明,采用固溶及时效等热处理可明显改善AZ80M镁合金的各向异性,但其机理未能充分阐述。
此外,在生物骨植入领域,成形件弹性模量与周围组织之间的弹性模量相差过大会导致应力屏蔽,进而造成骨萎缩和种植体过早失效等后果[81]。因此,将弹性模量调整到合适的值对于种植体设计至关重要。Zadpoor课题组[75,82]对可降解金属多孔结构的体外降解行为及力学性能进行了综合分析,通过设计孔隙率为67%的多孔WE43镁合金,将弹性模量降至约0.8 GPa,使得调控后的镁合金的刚度接近骨骼的水平。
2.3 增材制造镁合金耐蚀性能
生物可降解领域作为增材制造镁合金重要应用方向,增材制造镁合金耐蚀性的研究至关重要。根据Gollapudi理论[83],晶粒尺寸与腐蚀电流密度的关系为:
式中,
图17

图17 SLM成形与铸造成形WE43镁合金电化学反应测试结果比较[41]
Fig.17 Electrochemical response of SLM WE43 alloys in compared with as-cast WE43 alloy[41]
(a) open circuit potential (E) of WE43 in the cast, as-SLMed, and SLM + HIP + HT conditions in 0.1 mol/L NaCl for up to 10 min (HIP—hot isostatic pressing, HT—heat treatment)
(b) potentiodynamic polarisation curves of the same specimens tested in Fig.17a following exposure to 0.1 mol/L NaCl for a conditioning period
(c) the quantitative data on corrosion potential (Ecorr) and corrosion current density (icorr) acquired from the potentiodynamic polarisation analysis (Fig.17b)
近年来,研究人员开始关注增材制造镁合金的生物降解速率调控及生物相容性。Xu等[85]为制备出高性能抗菌ZK30-Cu合金,研究了ZK30镁合金的生物降解作用、Cu的抗菌作用和SLM成形晶粒细化的协同作用,发现Cu元素含量的增加可提高生物降解性。Li等[86]采用SLM技术成功制备了基于金刚石点阵结构的多孔WE43镁合金支架,测试结果表明该WE43支架不仅具有满足要求的生物降解速率(浸泡实验4周后体积损失约20%),并且具有较低的细胞毒性。Liu等[87]则通过在AZ61镁合金中加入稀土元素Y从而控制激光快速熔化降解速率,由于Mg17Al12相的还原和具有更活跃电位的Al2Y相的形成,降低了其与阳极基体相的耦合所引起的电偶联腐蚀,结果表明Y的加入延缓了AZ61镁合金的降解速率。通过调配合金组成也会对耐蚀性能产生影响。Shuai等[88]对不同成分的ZK60-xNd (x为质量分数,%)镁合金的腐蚀性能进行了研究,结果表明,ZK60-3.6Nd镁合金的腐蚀性能最佳,这主要是由于腐蚀生成的Nd2O3增加了表面膜的密度,蜂窝状金属间相抑制了腐蚀的扩散。除添加金属元素外,也将羟基磷灰石(HA)通过SLM加入到Mg-Zn合金中[89],其中Mg-3Zn、Mg-3Zn/xHA浸泡300 h后的析氢量分别为83、50~60 mL/cm2,经综合分析可得,随着腐蚀过程的进行,复合材料的生物降解性能提高,颗粒尺寸减小,形成了稳定的磷灰石保护层。金属间的析出相对激光增材制造镁合金耐蚀性亦有影响[90,91]。Shuai等[92]通过研究SLM成形Mg-Zn-xAl合金降解行为发现,当Al含量低于3%时,晶粒细化是影响耐蚀性能的主要因素。更细的晶粒创造了大量的晶界,使合金钝化,耐降解性能随之增强。Al元素含量进一步增加,金属间析出物体积分数增加并成为影响降解行为的主要因素。Yang等[93]将SiO2加入到SLM工艺制备的ZK60合金中,提高其耐腐蚀性能。由于SLM过程中升温和降温速率都很快,因此SiO2颗粒能均匀分布在Mg基体内部,并形成良好的结合面。
在SLM成形镁合金的氧化研究中,Shuai等[94]研究了镁合金粉末与O2间的相互作用,得到MgO薄膜可以在粉末上形核并生长的结论。由于氧化膜的生长速率受氧化物的固态扩散控制,镁合金氧化可以使用2种机制来描述,即增稠与升华。氧化膜形成是抑制致密化与诱导成球效应的主要原因,并破坏熔融颗粒之间的聚结。氧化物夹杂物通常会导致SLM镁合金零件的裂纹萌生并降低其力学性能[95,96]。氧化物夹杂物的形成主要可归因于熔池和氧化膜对O2的吸附,Ng等[97]的研究表明,在镁合金SLM成形过程中由于氧的吸附,会存在大量氧化物残留物。在SLM制备过程中,粉末氧化膜对材料的致密度、力学性能及腐蚀行为等方面都有影响,如何减弱这种影响也是众多镁合金研究者所关注的问题。
在WAAM成形镁合金的腐蚀性能研究方面,Han等[98]认为WAAM成形AZ91D镁合金比铸造合金具有更高的耐腐蚀性能,源于分散良好的第二相颗粒起到了腐蚀屏障的作用。然而类似的结论具有争议性,镁合金在晶粒细化后的腐蚀行为在学术界至今为止尚未形成共识,甚至存在相互矛盾的结论,因此各类理论解释也被不断提出。这在Li等[99]对WAAM镁合金的NaCl腐蚀研究中有所提及,他们认为晶粒尺寸是影响镁合金耐腐蚀性的重要因素,并将WAAM成形AZ31镁合金在耐腐蚀性能上比铸造合金表现出的劣化但相对稳定的行为归因于此。晶粒细化有利于提高整体腐蚀性能,但沿晶界分布的大量第二相颗粒导致了晶间腐蚀的发生,造成了WAAM镁合金的腐蚀加速。因晶粒细化使得合金耐腐蚀性被削弱的现象,Ralston等[100]指出还可能与腐蚀浸泡过程中所形成的薄膜有关。另外,Li等[99]还总结了镁合金的腐蚀机制,即大晶粒铸造合金的腐蚀机制主要是α-Mg和第二相之间的微电偶耦合,而当晶粒尺寸显著减小时,晶间腐蚀比微电偶腐蚀更为普遍。
3 总结与展望
本文综述了镁合金增材制造领域的研究进展,详细介绍了现阶段镁合金增材制造技术发展现状和关键工艺因素,并对增材镁合金显微组织以及材料性能相互关系进行总结。SLM和WAAM是镁合金增材制造最主要的2种技术,SLM工艺以高精度及复杂结构成形能力在生物医用镁合金领域具有广阔应用前景,而WAAM技术则因沉积效率高、低成本以及规避了Mg粉末易燃易爆等风险,在一体化、大尺寸镁合金结构件成形上具有独特优势。总体上看,增材制造镁合金成型件的力学和腐蚀性能表现并不亚于传统成形方式制备的镁合金,展现了极大的工程应用潜力。然而相比于钢及铝、钛、铜等合金增材制造技术发展和产业化情况,现阶段镁基材料的增材制造研究仍非常有限,在近几年才开始得到广泛关注。为推动镁合金增材制造技术的快速发展及应用普及,在未来研究工作主要集中在以下方面。
(1) 适用于增材制造的镁合金材料设计
目前,对增材制造专用新型镁合金的研究较为缺乏,大部分工作仍是沿用传统镁合金牌号进行成形研究,与增材制造工艺不兼容而无法获得其最佳性能。因此,需要基于增材制造工艺特性,重新优化设计合金成分,改善其凝固行为和调控组织结构以获得高性能增材制造专用镁合金。激光和电弧增材过程中,镁合金蒸发烧损问题比较严重,且不同合金元素蒸发速率不同,对最终打印件成分具有较大影响,在材料设计时需对元素烧损进行补偿。在改善WAAM制备镁合金强度方面,若可添加合适元素生成热稳定第二相,热循环过程中在晶界保持稳定,一方面可增强合金强度,另一方面钉扎晶界防止晶粒粗大。另外可利用热循环特性,调控成分使得成形过程中引入高密度纳米析出相,通过沉淀强化提供合金强度。但由于镁合金化元素种类较多,元素之间存在较强交互影响,在高性能增材制造镁合金设计方面有大量工作需要开展。若可构建和完善增材制造镁合金专用数据库以及将高效的机器学习方法引入镁合金设计,建立定量描述材料成分-工艺-组织-性能的数学模型,可加速镁合金成分设计和优化进程[101]。
(2) 增材制造成形过程的缺陷控制及工艺改进
Mg熔点和沸点低、蒸发倾向高,SLM过程中Mg蒸发产生明显烟尘及其对熔池的反冲力会对熔化过程稳定性造成不利影响;此外Mg的化学性质活泼、易氧化、热膨胀系数较高、易产生热裂纹等诸多特性使得激光增材制造镁合金内部气孔、裂纹、氧化夹杂物等缺陷较多,难以获得高度致密微观组织,严重影响了成形件的韧性及一致性。对镁合金SLM成形过程缺陷控制仍为现阶段亟需解决的技术问题之一。目前已有研究主要侧重于调控SLM制备镁合金过程的输入能量密度 (即激光功率、扫描速率、扫描间距和打印层厚等参数),在一定程度上实现了组织缺陷问题的改善,然而一方面该方法需要大量不同梯度实验组、实验周期长,另一方面弱化了连续时间和空间对打印过程的影响,如间隔时间、扫描策略等。因此,未来需综合考虑影响熔池能力的连续参数以及控制熔池几何特征的非连续参数,建立无量纲工艺图,可更真实高效地优化参数,减少缺陷。
相比激光增材制造技术,电弧增材成形以丝材为原料,逐点控制熔池凝固组织,可避免凝固缩孔、裂纹等缺陷。然而镁合金电弧增材控形能力差,成形件力学性能较低,是未来镁合金电弧增材制造工艺需重点突破的方向。电弧热输入量大,加之镁合金比热容较低,随着成形高度增大每一层热耗散条件不尽相同,使得堆焊成形件控形困难,且性能较低。基于电弧增材的微铸锻复合工艺(hybrid deposition and micro rolling,HDMR)是潜在的解决方案之一,该工艺即在每层电弧增材成形后使用配备的轧辊辊压,如图18[102,103]所示。相比电弧自由成形,经过原位辊压的金属不仅可改善性能各向异性,细化晶粒,并且样件形状和尺寸精度得到大幅优化[104,105]。然而目前尚未有研究报道该工艺在镁合金电弧增材制造中应用,若完成该工艺在镁合金上的成功应用,将有望实现电弧增材制造镁合金的技术突破。
图18
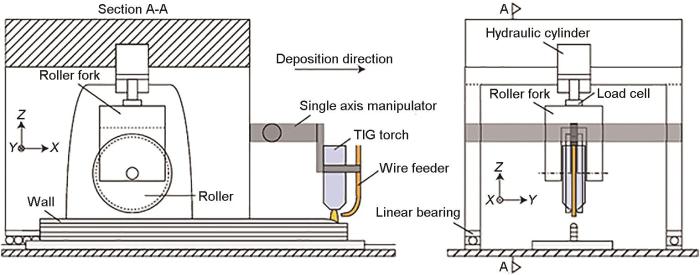
Fig.18 Schematic of hybrid deposition and micro rolling[102,103]
除微铸锻复合工艺以外,基于电弧增材外加激光、磁场及超声能场等多种复合制造方式亦展现了一定的技术优势,可作为进一步提高控形能力、提升沉积效率及调控组织的工艺发展方向,如激光-电弧复合焊接技术被证实可有效提高AZ31镁合金的焊接效率以及焊缝的力学性能,并且激光电弧2者协同作用还可防止熔滴过热,从而改善熔滴表面质量[106]。脉冲激光和电弧的复合效应可有效细化增材制造铝合金晶粒、抑制成分偏析及减少缺陷,获得力学性能优异的Al-Cu和Al-Zn-Mg-Cu体系铝合金[107,108]。利用焊接电弧产生的等离子体具有导电性和点准中心等特性,外加磁场可对电弧增材制造材料微观组织进行调控[109]。基于相似原理,外加超声能场辅助复合增材制造技术近年来也受到较多关注并得到发展,如利用大功率超声能场耦合激光增材制造可抑制钛合金大尺寸柱状晶粒生长[110]。超声能场产生的声空化和声流效应还被证实能够有效抑制WAAM制备7075铝合金的缺陷,实现组织的细化[111]。如上所述,复合制造技术是改善现有增材制造技术固有缺陷的有效途径,针对镁合金特性进行相应复合增材制造工艺探究及改进是重要的发展趋势和研究方向。
(3) 完善增材制造镁合金材料性能评价
现阶段增材制造镁合金研究处于起步阶段,对性能评价尚存在较大空白。镁合金作为密度最小的金属结构材料,广泛应用在汽车、航天航空领域等领域。虽然现有研究结果表明增材成形镁合金在室温强度性能上较传统铸造镁合金具有较大优势,但材料的疲劳行为、高温强度和蠕变等力学性能变化尚不清楚;对于生物医用增材镁合金的降解行为、生物相容性及动物体内实验数据积累较少,亦需要逐步完善。郑玉峰等[9]指出,可降解增材镁合金评价存在性能指标多、周期长及影响因素多等特点,亟需结合实验数据与数值模拟和机器学习等方法来建立高效可靠的评价方法。此外,增材制造在其独特的多孔结构或晶格结构的设计准则和方法上主要沿用于钛合金、铝合金等成熟案例,而在增材制造镁合金性能评价上较为缺乏,仍有大量工作需要开展。
来源--金属学报