分享:显微组织和应变速率对TC4合金动态力学性能和绝热剪切带的影响
陈伟1, 章环1, 牟娟,1, 朱正旺2, 张海峰2, 王沿东1
1.
2.
通过热处理成功获得了等轴、片层和双态3种组织结构的TC4合金,并研究了其动态力学性能及变形机制。通过对比硬化-软化转变临界剪切应变率、最大抗剪切强度、萌发绝热剪切带的临界剪切应变速率和承载时间4个指标评估了3种组织合金的动态力学性能。结果表明,片层组织TC4合金具有较高的抗剪切强度和临界剪切应变速率以及最低的绝热剪切敏感性,其动态力学性能最佳。进一步的微观结构分析表明,3种组织合金中所形成的绝热剪切带均为脆性剪切带,且剪切带宽度随剪切应变速率的增大而减小。当剪切应变速率相同时,3种组织合金的剪切带宽度由大到小依次为:片层组织、双态组织、等轴组织。
关键词:
Ti及钛合金具有比强度高、耐蚀性及耐热性好、冲击韧性好等优点,被誉为钢铁、铝材之后处于发展中的“第三金属”和“战略金属”,广泛应用于航空航天、海洋、汽车、国防等领域[1~4]。Ti-6Al-4V (TC4)合金具有综合性能好和制造成本低等优点,因此在航空工业领域中的应用最为广泛[5~7]。合金的服役环境决定了其承受载荷的种类。TC4合金在航空航天中的应用,主要受到准静态载荷的作用,相关组织结构和性能的关系已得到了非常广泛的研究和关注[8,9]。但是,在国防军事领域,TC4合金作为装甲材料主要受到高应变率载荷的作用。与准静态加载相比,在高应变率载荷下,TC4合金由于受到瞬时高过载的作用,容易形成剪切局域化而产生热塑性失稳,从而出现绝热剪切现象(绝热剪切现象是指在局域化剪切变形过程中,积累在材料内部的热量在短时间内来不及散失,使整个变形过程可以看作绝热状态的一种现象[10,11]。在绝热剪切变形过程中材料内部会伴随着一个剪切变形高度局域化的窄带区(绝热剪切带)形成)[10],导致材料的承载能力快速下降[10~12]。绝热剪切被认为是材料断裂失效的前兆[13,14],因此前期人们对TC4合金中的绝热剪切现象做了大量研究。Peirs等[15]在对近α态TC4合金的强迫剪切实验中,观察到了剪切带的演变和裂纹的形成,表明微裂纹和微孔隙在剪切带内的起始位置不同。Lee等[16]通过对不同片层间距的TC4合金魏氏组织进行动态扭转实验,结果表明,剪切带宽度随片层宽度的增大而减小。Zheng等[17]通过对TC4合金的动态压缩实验,发现双态组织β转变区中片层α相片层越宽,组织的绝热剪切敏感性越低。
以上工作多是针对某一组织结构状态TC4合金的绝热剪切现象开展的研究,而对于不同组织状态TC4合金的绝热剪切现象的系统研究报道相对较少。因此,本工作通过不同的热处理制度获得了等轴、片层和双态3种微观组织特征的TC4合金,并进一步采用分离式Hopkinson压杆进行不同剪切应变速率下的强迫剪切实验,系统分析了组织特征和剪切应变速率对TC4合金动态力学性能和绝热剪切敏感性的影响,以期为TC4合金的工程应用提供指导。
1 实验方法
实验采用12 mm 厚的TC4钛合金板,其化学成分(质量分数,%)为:Al 5.5~6.8,V 3.5~4.5,Fe ≤ 0.3,C ≤ 0.1,N ≤ 0.005,H ≤ 0.015,O ≤ 0.2,Ti余量。采用不同的热处理制度,对TC4钛合金板进行退火处理,具体的热处理工艺为:HT1:950℃保温4 h、炉冷;HT2:1050℃保温0.5 h、空冷;HT3:950℃保温1 h、水冷 + 550℃保温4 h、炉冷。热处理后的合金采用电火花线切割切成帽形试样,其尺寸如图1所示。利用分离式Hopkinson压杆进行强迫剪切实验,实验装置及其数据采集处理系统参见文献[18]。强迫剪切实验过程中,在室温下通过调节气压实现剪切应变速率在1.0 × 103~1.0 × 104 s-1 范围内对试样进行动态加载。采用9 kW辐射光源为单色CuKα 的Smartlab X射线衍射仪(XRD)分析样品的物相组成,扫描范围为20°~80°,扫描速率为10°/min。采用JSM-7001F场发射扫描电子显微镜(SEM)观察样品的微观组织。扫描样品经机械研磨抛光后,利用配比为1 mL HF + 2 mL HNO3 + 60 mL H2O的腐蚀液进行腐蚀,腐蚀时间为10 s。此外,利用金相分析软件Image J估算两相的体积分数。利用金相分析软件Nano measurer 测量α相晶粒尺寸和剪切带的宽度。
图1
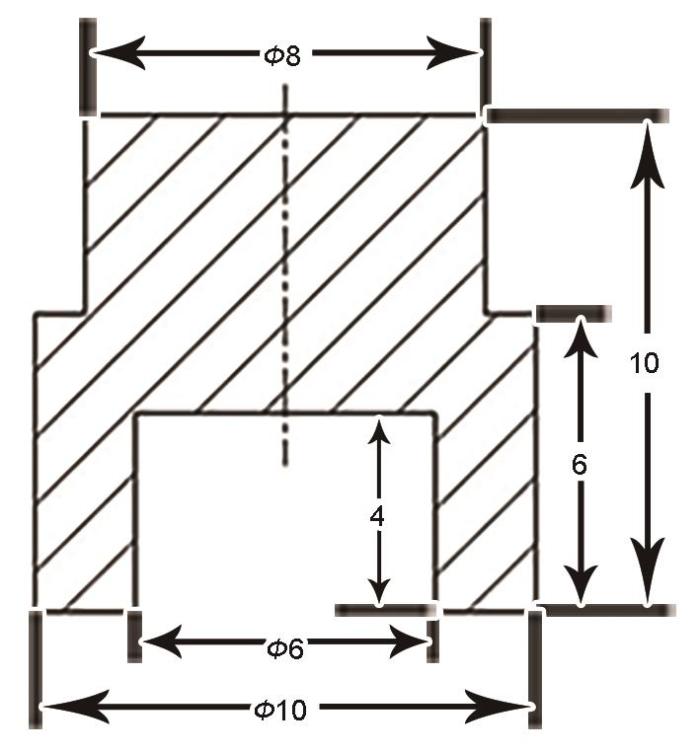
图1 帽形试样尺寸示意图
Fig.1 Schematic of size of the hat-shaped sample (unit: mm)
绝热剪切带形成的难易程度可以用绝热剪切敏感性来定量表示。本工作中采用剪切带萌发的临界剪切应变速率和承载时间表征不同组织TC4合金的绝热剪切敏感性。其中根据剪切应力-应变曲线的特征可以得出剪切带萌发的临界剪切应变速率。当剪切应力-应变曲线出现应力平台时,材料内部产生剪切带,反之则无剪切带形成。郭小汝等[19]和陈洋等[20]采用动态加载时间表征了材料的绝热剪切敏感性。该方法根据一维应力波理论,当子弹以速率C0撞击入射杆时,在入射杆内产生一近似的压缩方波,方波的时间宽度(t)为[21]:
式中,L为子弹长度;C0为压杆中纵波的传播速率。
本工作所采用分离式Hopkinson压杆的压杆材质为马氏体时效钢;子弹长度为300 mm;压杆中纵波速率约为5000 m/s。由
2 实验结果与分析
2.1 热处理后微观组织分析
图2为TC4合金原始试样以及经过不同热处理后3种试样的XRD谱。从图中可以看出,4种试样的XRD谱均由9个尖锐的衍射峰组成。通过与标准的PDF卡片对比可知,4种试样均由hcp结构的α相和bcc结构的β相组成。此外,可以发现α相的主峰(101)明显高于β相主峰(110),说明4种试样均以α相为主相。结合后续对样品显微组织结构特点分析(详见图3及相关描述),经HT1处理后得到的组织为等轴组织,经HT2处理后得到的组织为片层组织,经HT3处理后得到的组织为双态组织。通过对比4种组织TC4合金的衍射峰发现,β相主峰强度由强到弱依次为:等轴组织、原始组织、片层组织、双态组织,表明等轴组织TC4合金中β相含量最高。
图2
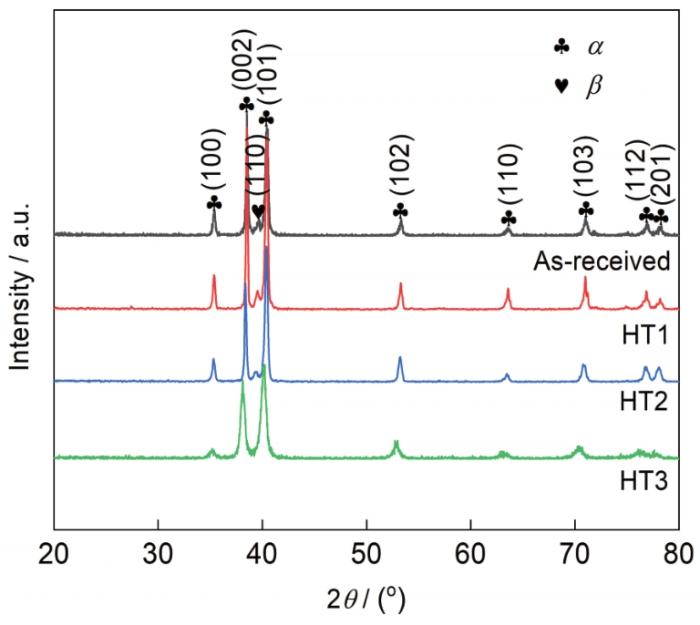
图2 TC4合金原始试样和经过不同热处理后的XRD谱
Fig.2 XRD spectra of TC4 alloy as-received and after different heat treatments
图3
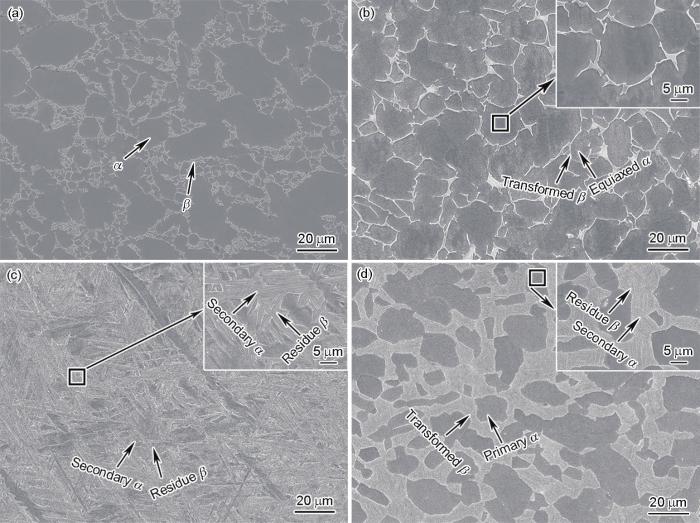
图3 不同组织TC4合金的SEM像
Fig.3 SEM images of TC4 alloy with different microstructures (Insets show the magnified images)
(a) as-received (b) equiaxed microstructure
(c) lamellar microstructure (d) bimodal microstructure
图3为不同组织TC4合金的SEM像。从图中可以看出,原始试样的显微组织由晶粒尺寸相差较大的α相和晶间β相组成(图3a)。经过HT1处理后,试样的显微组织主要由等轴状α相和分布在α相晶间的β转变区组成,为等轴组织(图3b);经过HT2处理后,试样的显微组织由沿不同取向排列的片层状或针状α相以及分布在α相内部和晶界处的β相组成,为片层组织(图3c);经过HT3处理后,试样的显微组织由初生等轴状α相和β转变区组成,其中β转变区主要是由次生片层状α相和少量残余β相组成,为双态组织(图3d)。3种组织状态的形成与命名与之前TC4合金的相关报道[13,23~26]一致。经金相分析软件测量得出,原始组织中α相体积分数约为97%,平均晶粒尺寸为(11.30 ± 6.83) μm。等轴组织中α相体积分数约为85%,平均晶粒尺寸为(13.50 ± 6.10) µm,说明该组织以α相为基体,这与XRD分析结果相吻合。片层组织中片层α相平均宽度为(380.0 ± 35.7) nm。双态组织中α相体积分数约为95%,其中初生α相晶粒平均晶粒尺寸为(11.9 ± 5.63) µm。
2.2 剪切应力-应变关系
图4为不同组织TC4合金的剪切应力-应变曲线随剪切应变速率的变化。从图中可以看出,3种组织TC4合金在强迫剪切变形过程中,都经历了3个阶段。具体以等轴组织TC4合金在剪切应变速率为7467 s-1时的剪切应力-应变曲线为例详细说明(图4d):a~b阶段,剪切应力随应变的增加而快速增加,此阶段应变硬化效应占主导;根据不稳定变形的最大应力准则[27],b点为不稳定变形的起始点和绝热剪切带的萌发点;b~c阶段,随着剪切应变的增加,剪切应力快速减小,此阶段热软化效应占主导;c~d阶段,剪切应力变化较小,形成了应力平台,这是热软化效应产生的绝热温升与应变硬化效应之间相互竞争的结果。这与Wang等[28]对Ti-5Mo-5V-8Cr-3Al合金的强迫剪切变形过程的划分相吻合。
图4
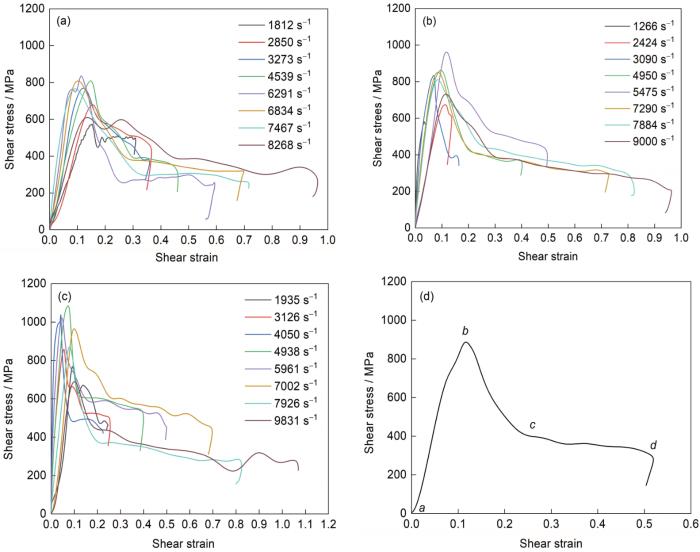
图4 不同组织TC4合金在不同剪切应变速率下的动态剪切应力-应变曲线
Fig.4 Dynamic shear stress-strain curves of TC4 alloy with different microstructures at different shear strain rates
(a) equiaxed microstructure (b) lamellar microstructure
(c) bimodal microstructure (d) the shear strain rate of equiaxed microstructure is 7467 s-1
图5为不同组织TC4合金的抗剪切强度随剪切应变速率变化曲线。从图中可以看出,3种组织TC4合金的抗剪切强度均随着剪切应变速率的增大呈现先增大后减小的趋势。在相同的剪切应变速率下,抗剪切强度由高到低的顺序始终为:双态组织、片层组织、等轴组织。将抗剪切强度为最大值时的剪切应变速率定义为硬化-软化转变的临界剪切应变速率。由图可见,对于不同的组织,硬化-软化转变的临界剪切应变速率不同。等轴组织TC4合金的硬化-软化转变的临界剪切应变速率约为6300 s-1,最大抗剪切强度约为835 MPa;片层组织TC4合金的硬化-软化转变的临界剪切应变速率约为5500 s-1,最大抗剪切强度约为960 MPa;双态组织TC4合金的硬化-软化转变的临界剪切应变速率约为5000 s-1,最大抗剪切强度约为1083 MPa。
图5
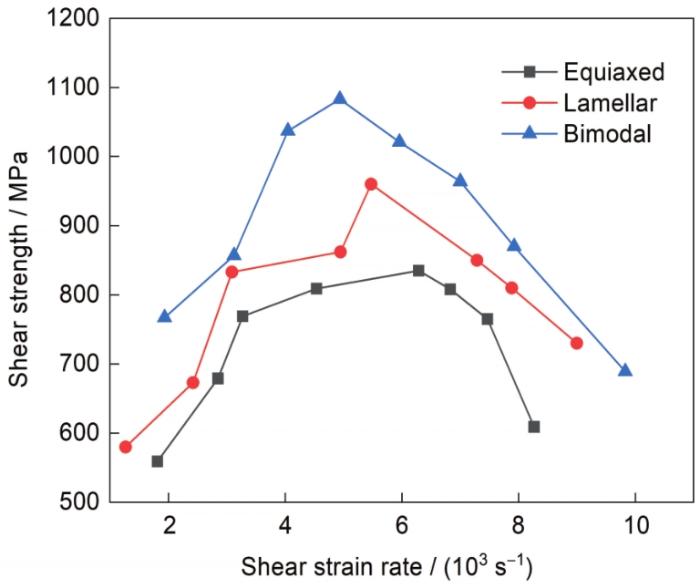
图5 不同组织TC4合金的抗剪切强度随剪切应变速率变化曲线
Fig.5 Variation curves of shear strength with shear strain rate of TC4 alloy with different microstructures
综合以上分析可得出,双态组织TC4合金具有高的抗剪切强度,低的硬化-软化转变的临界剪切应变速率。等轴组织TC4合金具有高的硬化-软化转变的临界剪切应变速率,低的抗剪切强度;而片层组织TC4合金具有相对较高的抗剪切强度和硬化-软化转变的临界剪切应变速率。因此在强迫剪切作用下,片层组织TC4合金表现出更优异的动态力学性能。
2.3 绝热剪切敏感性
当材料的热软化效应大于应变硬化和应变率硬化效应时,材料内部会形成绝热剪切带[29]。因此存在临界剪切应变速率使3种组织TC4合金中萌发绝热剪切带。由图4可知,对于不同的组织,绝热剪切带萌发的临界剪切应变速率不同。等轴组织TC4合金的临界剪切应变速率约为1812 s-1;片层组织TC4合金的临界剪切应变速率约为2424 s-1;双态组织TC4合金的临界剪切应变速率约为1935 s-1。由此可以得出3种组织TC4合金的绝热敏感性由低到高依次为:片层组织、双态组织、等轴组织。Recht[30]在研究中也利用临界应变速率表征了材料的绝热剪切敏感性。
图6为不同剪切应变速率下不同组织TC4合金的剪切应力-时间曲线。图中a点由于剪切带的萌发导致应力快速下降,为应力塌陷点,b点为剪切断裂失效点。将a~b定义为剪切断裂失效的承载时间,如表1所示。由图6和表1可以看出,在同一剪切应变速率下,3种组织TC4合金的承载时间由大到小,即3种组织TC4合金的绝热剪切敏感性由低到高依次为:片层组织、双态组织、等轴组织。这是由于等轴组织中β相含量高,晶粒尺寸大,导致等轴组织在压缩过程容易发生变形。这个特点增加了应变的局域化,同时也有利于剪切带的扩展,所以等轴组织TC4合金表现出高的绝热剪切敏感性[31];片层组织TC4合金中片层组织纵横交错分布,导致绝热剪切带在片层组织TC4合金中扩展时,需要克服大量界面的阻碍作用,而不利于剪切带的扩展,所以片层组织TC4合金表现出低的绝热剪切敏感性[32];而双态组织是等轴组织和片层组织混合的组织,因此双态组织TC4合金的绝热剪切敏感性介于2者之间。此外,可以发现,同种组织在不同剪切应变速率下,承载时间随着剪切应变速率的增加而减小。因此可以得出3种组织TC4合金的绝热敏感性随剪切应变速率的增加而增加。这是由于随着剪切应变速率的增加,积累在试样内部的热量散失速率减慢,从而促进了试样内部温升,加速了绝热剪切带的形成[33]。
图6
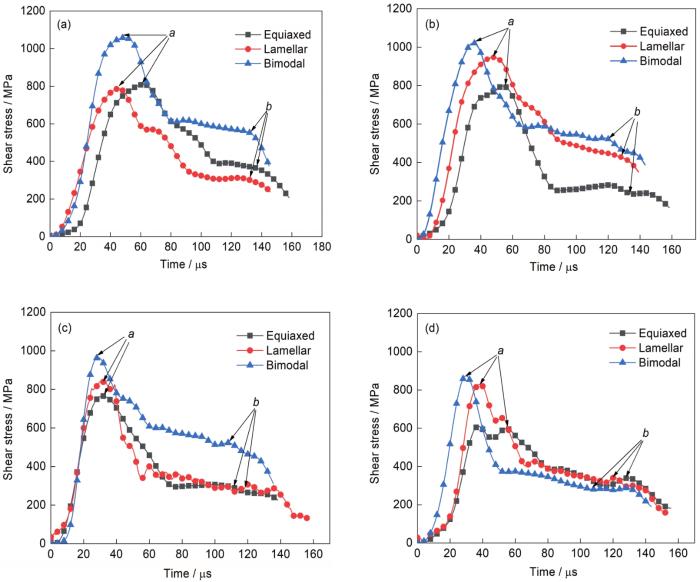
图6 不同剪切应变速率下不同组织TC4合金的剪切应力-时间曲线
Fig.6 Shear stress-time curves of TC4 alloy with different microstructures at shear strain rates of 5000 s-1 (a), 6000 s-1 (b), 7000 s-1 (c), and 8000 s-1 (d)
表1 不同组织TC4合金在不同剪切应变速率下的承载时间 (μs)
Table 1
Specimen | 5000 s-1 | 6000 s-1 | 7000 s-1 | 8000 s-1 |
---|---|---|---|---|
Equiaxed | 83 | 79 | 78 | 74 |
Lamellar | 98 | 87 | 84 | 82 |
Duplex | 86 | 84 | 80 | 77 |
2.4 剪切区域的显微结构特征
图7为不同组织TC4合金的剪切带宽度随剪切应变速率变化曲线。由图可见,随着剪切应变速率的增大,3种组织TC4合金的剪切带宽度逐渐减小。Wu等[34]在研究中也发现了剪切带的宽度随变形速率的增加而减小的变化趋势。Ran等[35]认为随着剪切应变速率的增大,材料的变形局域化加剧,导致绝热剪切带的宽度减小。此外,高剪切应变速率下,热量向周围基体扩散的作用时间缩短,也不利于绝热剪切带的宽化。当剪切应变速率相同时,3种组织TC4合金的剪切带宽度由大到小依次为:片层组织、双态组织、等轴组织。这是因为剪切带在片层组织TC4合金中萌发的临界剪切应变速率大,同时片层组织TC4合金中纵横交错的α相阻碍绝热剪切带的扩展,绝热剪切带继续扩展需要获取更多的塑性变形功。在这个过程中,大量积累的塑性变形功一部分用于绝热剪切带的扩展;另一部分(约90%)转化为热能,引起材料内部温度升高,导致绝热剪切带宽化。
图7

图7 不同组织TC4合金的绝热剪切带宽度变化曲线
Fig.7 Variation curves of adiabatic shear band width (t) of TC4 alloy with different microstructures
图8为不同组织TC4合金在剪切应变速率5.0 × 103~6.0 × 103 s-1范围内的绝热剪切带显微组织形貌。从图中可以观察到,剪切带与基体存在明显的边界,同时剪切带内由于产生了应力集中,导致剪切带内晶粒严重变形而碎化。这与Ran等[36]在Ti-5Al-5Mo-5V-1Cr-1Fe合金的剪切区域观察到的现象一致。将图8与TC4合金热处理后的3种组织SEM像(图3)对比发现,靠近剪切带的α相沿着剪切方向被拉长细化。这是由于靠近剪切带的α相受到较大的剪切应力作用,从而沿着剪切方向发生了严重的剪切变形。
图8
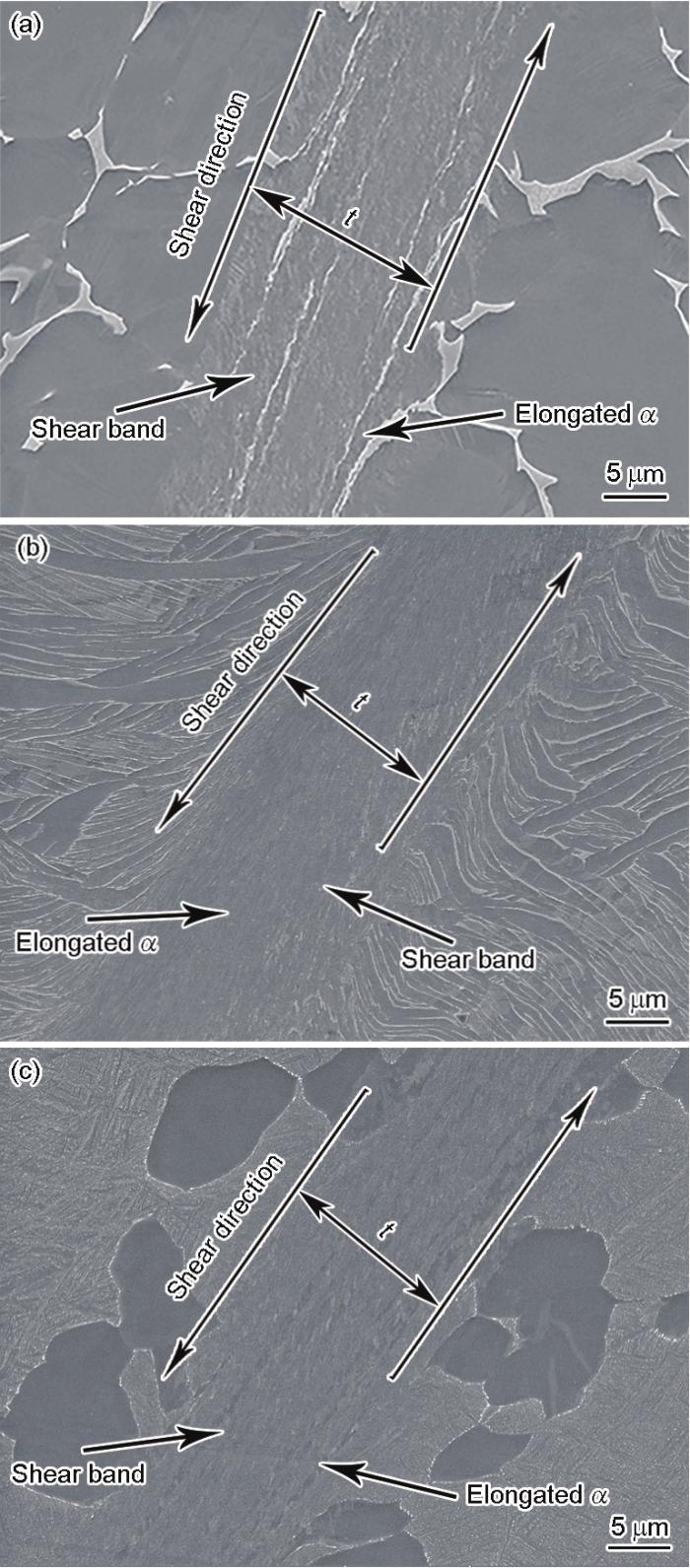
图8 不同组织TC4合金的绝热剪切带形貌
Fig.8 Adiabatic shear band morphologies of TC4 alloy with equiaxed (a), lamellar (b), and bimodal (c) microstructures
Dodd和Bai[37]根据剪切带内是否有微孔,将剪切带分为脆性剪切带(无微孔)和韧性剪切带(有等轴或椭圆孔)。值得注意的是,在本工作中的3种组织TC4合金的剪切带中均未观察到微孔,表明在高剪切应变速率下,3种组织TC4合金中形成的剪切带均为脆性剪切带。这与Xue等[38]以及Lee等[39]的研究结果不同,他们在TC4合金的剪切带中发现了微孔和微裂纹。但与Ran等[35]在Ti-55511合金中观察到的剪切带相一致。这可能与组织中α相和β相的含量有关。
2.5 绝热剪切断裂机理
图9为不同组织TC4合金在剪切应变速率为5.0 × 103~6.0 ×103 s-1的裂纹形貌。可以看出,3种组织TC4合金的裂纹都分布在剪切带和基体的分界面上,并沿着剪切方向进行扩展。因此可以得出TC4合金的剪切断裂经历了微裂纹的形核、长大、聚合成宏观裂纹和裂纹扩展[40],如图10所示。首先在强剪切区域形成绝热剪切带(图10a)。其次是微裂纹的形核(图10b),由于剪切带与基体组织性能差异大,导致基体与剪切带的连接不稳定,因此微裂纹优先在剪切带与基体的分界面上形核。然后是宏观裂纹的形成(图10c),随着变形的加剧,材料内部的变形功增大,从而促进微裂纹的长大,同时相邻的微裂纹合并成宏观裂纹。严重的塑性变形会引起剪切带内以及剪切带和基体分界面发生位错塞积,形成位错胞,阻碍裂纹的扩展(图10d)。此时,裂纹改变方向继续扩展(图10e),如此循环下去,直到上下2条裂纹相聚,使材料发生断裂失效(图10f)。
图9
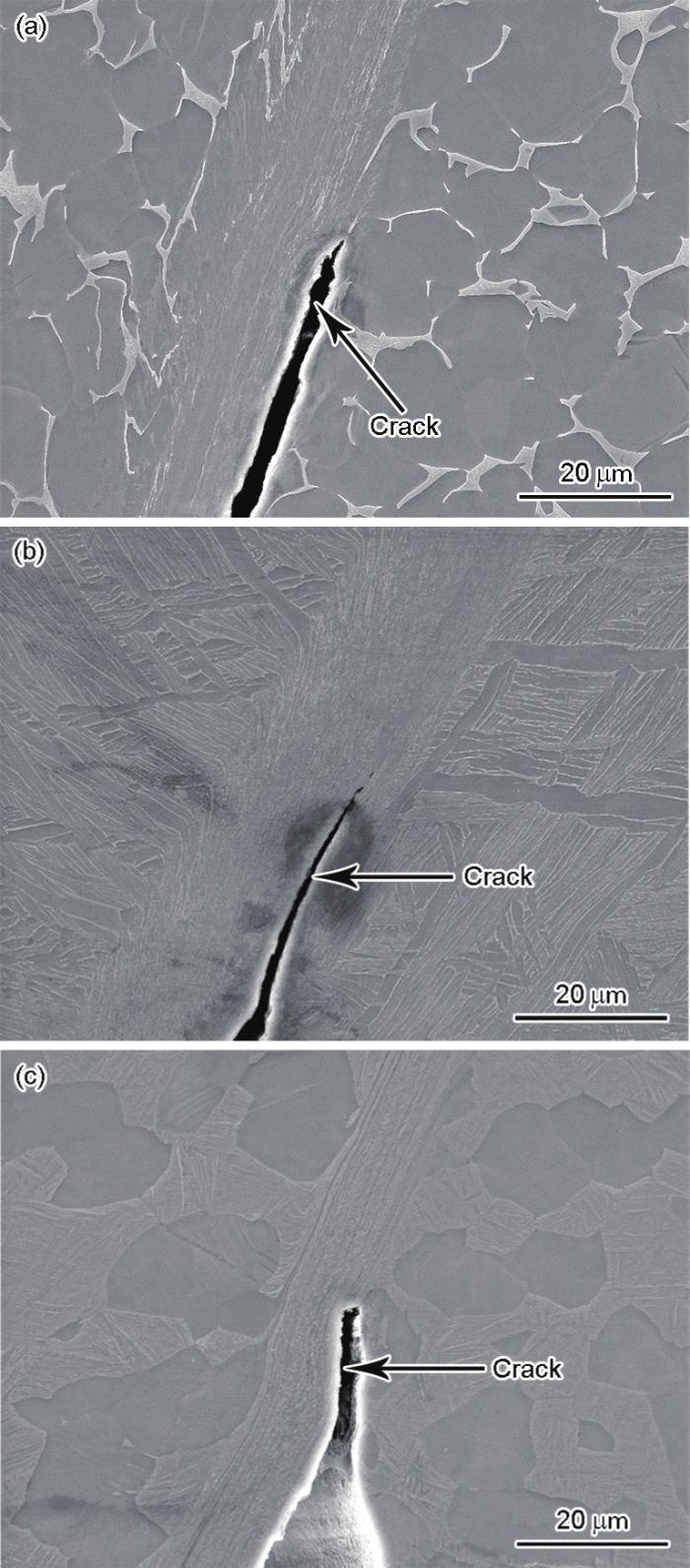
图9 不同组织TC4合金的裂纹形貌
Fig.9 Crack morphologies of TC4 alloy with equiaxed (a), lamellar (b), and bimodal (c) microstructures
图10
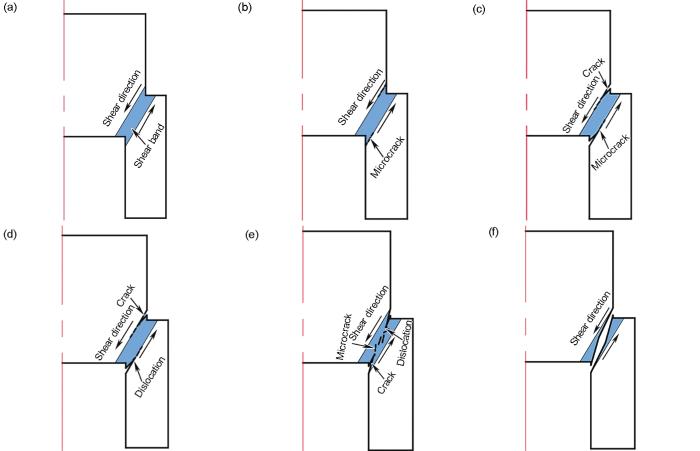
图10 TC4合金的断裂过程示意图
Fig.10 Schematics of fracture process of TC4 alloy
(a) adiabatic shear band formation (b) microcrack formation (c) macrocrack formation
(d) macrocrack steering (e) the crack continues to grow (f) two cracks converge
3 结论
(1) 强迫剪切实验结果表明,随着剪切应变速率的增加,3种组织TC4合金的抗剪切强度均表现为先升高后降低的趋势,硬化-软化转变的临界剪切应变速率和最大抗剪切强度分别为:等轴组织为6300 s-1和835 MPa;片层组织为5500 s-1和960 MPa;双态组织为5000 s-1和1083 MPa。综合考虑,片层组织TC4合金具有优异的动态力学性能。
(2) 利用剪切带萌发的临界剪切应变速率和承载时间2种方法评估了3种组织TC4合金的绝热剪切敏感性,结果表明绝热剪切敏感性由低到高依次为:片层组织、双态组织、等轴组织。此外,随着剪切应变速率的增大,绝热温升增大,导致3种组织TC4合金的绝热剪切敏感性均提高。
(3) 3种组织TC4合金中形成的绝热剪切带都为脆性剪切带,随着剪切应变速率的增加,3种组织TC4合金的剪切带宽度逐渐减小。
来源--金属学报