分享:形核剂的添加方式对选区激光熔化成形含锆Al-Cu-Mg合金显微组织与力学性能的影响
采用选区激光熔化技术制备了含锆Al-Cu-Mg合金,研究了不同方式添加Al3Zr形核剂对试样显微组织和力学性能的影响。结果表明,直接添加Al3Zr和原位生成Al3Zr均能抑制该合金试样的热裂纹,当激光能量密度为370 J/mm3时,试样的平均晶粒尺寸分别由15.69 μm细化至1.88和1.28 μm。原位生成Al3Zr提供的形核剂均为亚稳态Al3Zr立方相(L12-Al3Zr),形核能力高于直接添加Al3Zr获得的Al3Zr颗粒和L12-Al3Zr形核剂。原位生成Al3Zr的Al-Cu-Mg合金综合力学性能更为优异,T6热处理态试样抗拉强度达(485 ± 10) MPa,伸长率比直接添加Al3Zr的合金高出30%。原位生成Al3Zr几乎无需通过高的激光能量密度增强Marangoni对流来实现晶粒细化剂的分散,可使Al-Cu-Mg合金适用于较高速率成形。
关键词:
选区激光熔化(selective laser melting,SLM)技术以增材制造思想为基础,根据零件的二维切片信息选区熔化金属粉末,并逐层堆叠,实现复杂结构件的高性能、高精度成形[1],在航空航天、生物医疗等领域具有广阔的应用前景[2, 3]。Al-Cu系高强铝合金的密度低、强度高、疲劳性能优良[4],常用于制造飞机骨架、航天器结构件等[5]。采用SLM技术制备Al-Cu系合金可简化复杂零件的制造过程,满足航空航天领域对轻质高强复杂结构件的需求,并能缩短研发周期[6]。但是Al-Cu系合金的凝固区间较宽,在SLM成形过程中易产生周期性裂纹,热裂问题亟待解决[7],相关研究较少。
微合金化法改性粉末能够显著细化SLM成形铝合金的晶粒,从而抑制热裂纹[8],是提高高强铝合金成形件性能的主要途径之一。目前,有关SLM成形高强铝合金的研究大多集中于工艺参数优化以及加入形核剂产生的晶粒细化机制和强化机制[9~15]方面,采用的形核剂主要通过直接添加(TiB2[15]、Al-Ti-C-B[13]等)或化合物原位反应(Al3Ti[14]、Al3Zr[9]、Al3Sc[12])获得。在有关SLM成形Al-Cu系合金的研究中,Zhang等[10]和Nie等[16]利用纯Zr粉原位生成形核剂Al3Zr和ZrO,制备出的Al-Cu-Mg合金高致密且无裂纹,扫描速率提升至250 mm/s时,抗拉强度达493 MPa,伸长率约为3%,塑性较低可能与ZrO的出现有关;Tan等[14]以Ti为晶粒细化剂,得到抗拉强度为432 MPa的热处理态2024铝合金,Al3Ti形核剂与α-Al晶格错配度低,可显著细化铝合金晶粒;Wang等[11]在Al-3.5Cu-1.5Mg-1Si合金中直接添加5%TiB2 (体积分数),沉积态试样的平均晶粒尺寸细化至2.5 μm,合金压缩屈服强度提升了约25%。在SLM成形Al-Cu系合金领域,不同方式添加形核剂均可不同程度细化晶粒、提升合金的力学性能,但是迄今鲜有研究报道对比直接添加形核剂和原位生成形核剂对SLM成形Al-Cu系合金的显微组织与力学性能的影响,其在晶粒细化以及力学性能和成形效率提升方面存在的异同也尚不明晰。
Al3Zr热稳定性高,与α-Al晶格错配度低于0.52%[9],是铝合金常用的形核剂,Al3Zr颗粒制备工艺相对简单[17,18],原位合成Al3Zr的晶粒细化剂(Zr[10]、ZrH2[9])成本也较低,因此本工作采用亚微米Al3Zr和ZrH2作为晶粒细化剂,分别用于直接添加Al3Zr颗粒和原位生成Al3Zr形核剂。采用低扫描速率(200 mm/s)和中高扫描速率(600 mm/s)制备SLM成形含锆Al-Cu-Mg合金,并对沉积态试样进行T6热处理。对比分析不同方式添加Al3Zr对SLM成形Al-Cu-Mg合金显微组织与力学性能的影响,为SLM成形Al-Cu系合金的研究提供实验依据。
1 实验方法
采用粒径较粗的ZrH2 (图1a)与高纯Al粉(图1b)为原料,利用热扩散反应法合成Al3Zr,并通过高能球磨法细化Al3Zr,制备过程均为Ar气气氛保护。Al3Zr颗粒的XRD谱如图1c所示,显微组织如图1d所示,其平均粒径约为500 nm。原位晶粒细化剂ZrH2采用高能球磨法制得,平均粒径约为500 nm,显微组织如图1e所示。Al-Cu-Mg合金粉末是采用组合雾化法制备的2024铝合金粉末,显微组织如图1f所示,平均粒径约为28 μm,其化学成分(质量分数,%)为:Cu 4.28,Mg 1.72,Mn 0.60,Si、Fe、Zn、Cr、Ti微量,余量为Al。采用低能球磨组装修饰法制备Al3Zr/Al-Cu-Mg和ZrH2/Al-Cu-Mg合金复合粉末,Al3Zr和ZrH2颗粒的添加量均为0.45% (原子分数)。复合粉末的显微组织如图2所示,复合粉末球形度良好,亚微米颗粒均匀分布于铝合金球形粉表面。
图1
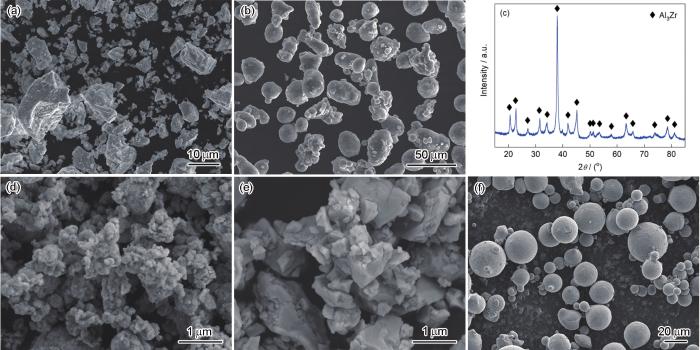
图1 原材料的显微组织以及Al3Zr颗粒的XRD谱
Fig.1 Morphologies of coarse ZrH2 particles (a), high-pure Al powders (b), Al3Zr particles (d), fine ZrH2 particles (e), and Al-Cu-Mg alloy powders (f), and XRD spectrum of Al3Zr particles (c)
图2

图2 Al3Zr/Al-Cu-Mg和ZrH2/Al-Cu-Mg合金复合粉末的显微组织
Fig.2 Low (a, c) and high (b, d) magnified morphologies of Al3Zr/Al-Cu-Mg (a, b) and ZrH2/Al-Cu-Mg (c, d) alloy composite powders
采用EOS-M290选区激光熔化设备成形Al-Cu-Mg合金,设备额定激光功率400 W,成形空间为250 mm × 250 mm × 325 mm。激光束的体能量密度公式(E,J/mm3)为[19]:
式中,P为激光功率,v为扫描速率,h为扫描间距,t为铺粉层厚。200 mm/s低扫描速率和600 mm/s中高扫描速率匹配的激光功率分别为200和250 W,扫描间距为90 μm,铺粉层厚为30 μm,激光能量密度则分别为370和154 J/mm3,扫描策略选用相邻铺粉层旋转67°,基板预热为180℃,保护气为Ar气。
T6热处理工艺为:试样在TNX1100-20箱式热处理炉内进行520℃、1 h固溶处理,水淬至室温;在DF-101S恒温油浴锅进行时效处理,时效温度150℃,时效时间10 h,空冷至室温。
试样打磨至金属光泽,采用Archimedes排水法根据实际密度/理论密度推导试样的相对致密度(W),计算公式为:
式中,m1为试样在空气中的质量,m2为试样在去离子水中的质量,ρ1为去离子水的密度,室温下为0.9982 g/cm3,ρ2为试样的理论密度。根据混合法则计算合金的理论密度,Al-Cu-Mg合金取2024铝合金的理论密度,为2.78 g/cm3,ZrH2的理论密度为5.60 g/cm3,Al3Zr颗粒的理论密度为4.10 g/cm3。对试样进行粗磨、抛光后,在DM 15000M光学显微镜(OM)下观察试样内部缺陷。采用搭载背散射电子衍射(EBSD)探头的NOVA NANOSEM 430场发射扫描电子显微镜(SEM)观察试样的显微组织、晶粒取向等,采用SEM自带的能谱仪(EDS)分析物相成分,利用HKL Channel 5软件计算晶粒的相关数据。显微组织观察的试样采用Keller试剂腐蚀15 s,EBSD测试的试样通过离子抛光消除表面因机械抛光引起的应力。采用D8 Advance X射线衍射仪(XRD)分析试样物相,采用JEM-2100F场发射透射电子显微镜(TEM)观察试样的物相及分布。采用UTM5105电子万能试验机测试试样的室温拉伸性能,试样平行段尺寸为14 mm × 3 mm × 1.5 mm,拉伸速率为1 mm/min,测试3次取平均值,并在SEM下观察试样的断口形貌。
2 实验结果
2.1 成形质量
添加与未添加Al3Zr形核剂的SLM成形Al-Cu-Mg合金的横截面显微组织如图3所示,致密度见图4。试样成形的激光能量密度为370和154 J/mm3。添加形核剂消除了SLM成形Al-Cu-Mg合金中常见的热裂纹,试样内部存在孔隙。当激光能量密度为370 J/mm3时,无晶粒细化剂以及晶粒细化剂为Al3Zr和ZrH2的试样的致密度分别为98.2%、98.7%、97.2%;激光能量密度减小,致密度降低。在SLM成形过程中,熔池湍流吸入的少量气体(保护气以及低熔点金属蒸气等)在熔池的高凝固速率下来不及逸出,致使试样均不完全致密[20]。另外,ZrH2于540℃左右开始分解析出H2,从而导致试样孔隙增多[21]。
图3

图3 不同激光能量密度成形的不同成分沉积态Al-Cu-Mg合金的横截面显微组织的OM像
Fig.3 Cross-sectional OM images of as-built Al-Cu-Mg (a, d), Al3Zr/Al-Cu-Mg (b, e), and in-situ Al3Zr/Al-Cu-Mg (c, f) alloys prepared with the laser energy density of 370 J/mm3 (a-c) and 154 J/mm3 (d-f)
图4
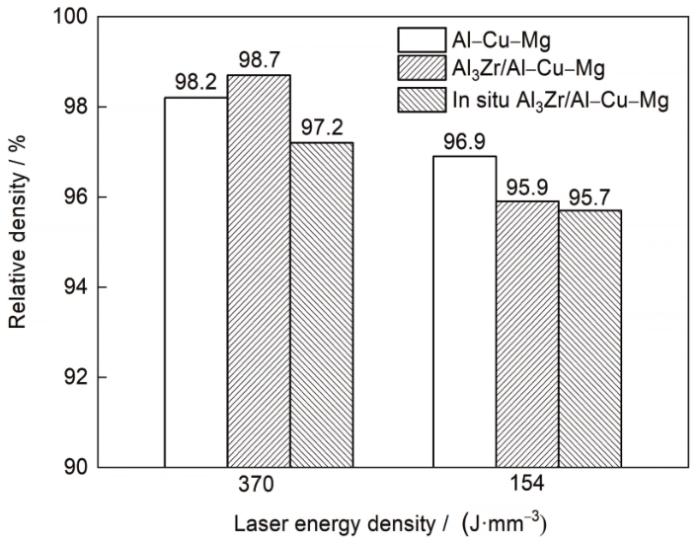
图4 添加与未添加形核剂的沉积态Al-Cu-Mg合金的相对致密度
Fig.4 Relative densities of as-built Al-Cu-Mg alloys with or without nucleating agents
2.2 显微组织
添加与未添加Al3Zr形核剂的SLM成形Al-Cu-Mg合金的纵截面显微组织如图5所示。由图5a和d可知,沉积态Al-Cu-Mg合金的粗大柱状晶贯穿整个熔池,熔池底部存在少量等轴晶。如图5b、c、e和f所示,添加形核剂后,试样组织晶粒细化显著,少量短柱状晶在熔池内部沿竖直方向生长,部分熔池内部完全凝固为等轴晶。在SLM成形过程中,熔池底部高温液相与已凝固的固相接触产生一定过冷区,促进α-Al形核;熔池内部的凝固速率较低,等轴晶形成受到抑制。
图5
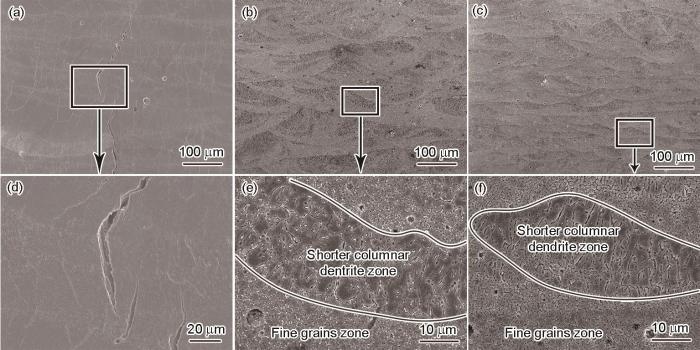
图5 370 J/mm3激光能量密度成形的不同成分沉积态Al-Cu-Mg合金的纵截面显微组织
Fig.5 Microstructures of vertical-section in as-built Al-Cu-Mg (a, d), Al3Zr/Al-Cu-Mg (b, e), and in-situ Al3Zr/Al-Cu-Mg (c, f) alloys prepared with the laser energy density of 370 J/mm3
图6为添加与未添加Al3Zr形核剂的沉积态Al-Cu-Mg合金的反极图(IPF)和晶粒尺寸分布图,试样SLM成形的激光能量密度为370 J/mm3。由图6a和d可知,沉积态Al-Cu-Mg合金的晶粒多为[001]晶向,沿打印方向织构明显,平均晶粒尺寸约为15.69 μm,晶界存在数百微米长裂纹。图6b和e表明直接添加Al3Zr削弱了试样的[001]织构,试样平均晶粒尺寸细化至1.88 μm。而含有原位生成Al3Zr的试样平均晶粒尺寸更小,约为1.28 μm,晶粒无择优取向,如图6c和f所示。
图6
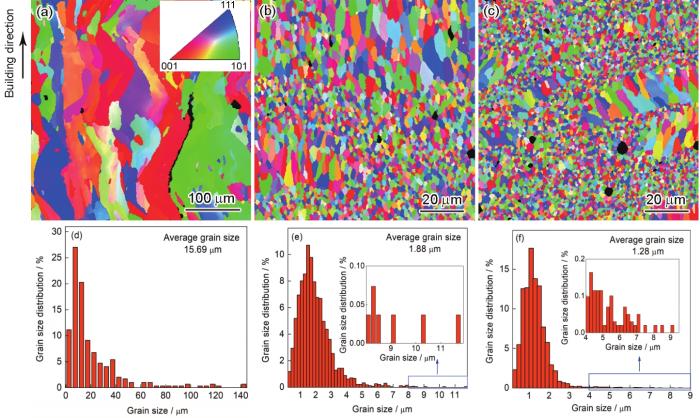
图6 370 J/mm3激光能量密度成形的不同成分的沉积态Al-Cu-Mg合金纵截面的反极图和晶粒尺寸分布图
Fig.6 Inverse ploe figures (IPFs) (a-c) and grain size distribution images (d-f) of the vertical-section of Al-Cu-Mg (a, d), Al3Zr/Al-Cu-Mg (b, e), and in-situ Al3Zr/Al-Cu-Mg (c, f) alloys prepared with the laser energy density of 370 J/mm3 (Insets in Figs.6e and f are partial enlarged figures)
2.3 物相
添加与未添加Al3Zr形核剂的沉积态Al-Cu-Mg合金的XRD谱如图7所示。除α-Al外,沉积态合金中均可见θ-Al2Cu相和S-Al2CuMg相衍射峰,其他物相含量较少,难以辨别,可认为θ相和S相是沉积态Al-Cu-Mg合金的主要第二相。
图7
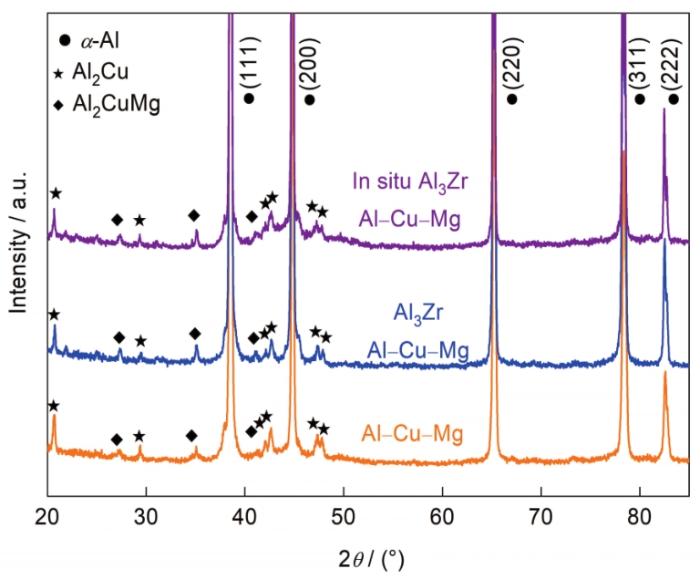
图7 添加与未添加形核剂的沉积态Al-Cu-Mg合金的XRD谱
Fig.7 XRD spectra of as-built Al-Cu-Mg alloys with or without nucleating agents
图8为直接添加Al3Zr颗粒的沉积态Al-Cu-Mg合金的TEM像、选区电子衍射(SAED)花样和EDS元素分布图,试样的成形激光能量密度为370 J/mm3。在合金内部,第二相Al3Zr的形貌分为立方状和不规则颗粒状。立方状Al3Zr为fcc结构的L12-Al3Zr相,与α-Al晶格错配度低,L12-Al3Zr与α-Al界面的SAED花样显示部分L12-Al3Zr在基体中作为α-Al的形核衬底,与α-Al保持良好的位向关系(图8b)。而未能充当形核质点的L12-Al3Zr大多分布于晶界,与α-Al位向差较大(图8c)。图8a中不规则颗粒相由数个小颗粒构成,不易构建衍射斑点,EDS结果(图8d)说明其富含Zr元素,推测含有外加Al3Zr颗粒相,除Al外不规则颗粒相处也存在只含有Cu元素以及同时含有Cu、Mg元素的物相,很可能是θ相和S相。因此,不规则颗粒相不完全由外加Al3Zr颗粒相组成。文献[22,23]中也存在类似现象,可认为Al3Zr颗粒为θ相和S相提供了析出位点。
图8
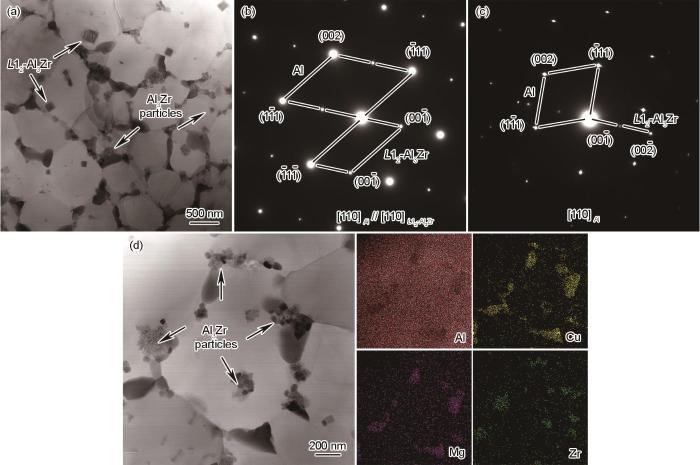
图8 370 J/mm3激光能量密度成形的直接添加Al3Zr的沉积态Al-Cu-Mg合金TEM像、SAED花样和EDS元素分布图
Fig.8 Bright field TEM image (a), SAED patterns of L12-Al3Zr/Al with (b) or without (c) coherent interface, and EDS element maps (d) of as-built Al3Zr/Al-Cu-Mg alloys prepared with the laser energy density of 370 J/mm3
原位生成Al3Zr的沉积态Al-Cu-Mg合金的明场像和SAED花样如图9所示,试样的成形激光能量密度为370 J/mm3。利用ZrH2原位反应得到的Al3Zr均为L12-Al3Zr,试样内部存在更多分布于晶内的L12-Al3Zr,该部分L12-Al3Zr大多可作为α-Al异质形核的有效衬底(图9b和c)。此外,试样内部未发现不规则颗粒状Al3Zr,从侧面证明了图8a和d中含Zr不规则颗粒相并非在SLM成形过程中析出,为外加Al3Zr颗粒。
图9
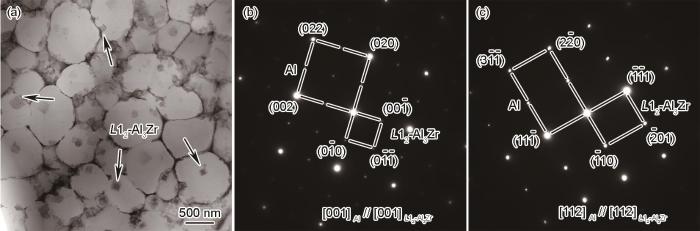
图9 370 J/mm3激光能量密度成形的含原位生成Al3Zr的沉积态Al-Cu-Mg合金的TEM像及SAED花样
Fig.9 Bright field TEM image (a) and SAED patterns of L12-Al3Zr/Al interface along [001]Al (b) and [112]Al (c) of as-built in-situ Al3Zr/Al-Cu-Mg alloys prepared with the laser energy density of 370 J/mm3
图10为采用不同激光能量密度成形的含锆Al-Cu-Mg合金沉积态试样的SEM背散射像。从图中也可以看出基体中分布有L12-Al3Zr相。当激光能量密度降至154 J/mm3时,在直接添加Al3Zr颗粒的试样中存在尺寸可达20 μm的团聚相(图8c),EDS结果显示其Al与Zr的原子比约为3∶1 (表1),可认为是Al3Zr晶粒细化剂未完全分散所致。亚微米颗粒表面能较高,易团聚,低能球磨可初步分散亚微米颗粒;在SLM成形过程中,熔池内的Marangoni对流能进一步使晶粒细化剂分散。但是随着扫描速率增大,激光能量密度降低,Marangoni对流减弱[24],部分团聚态Al3Zr颗粒分散受阻,残留于基体。而ZrH2的分散对Marangoni对流的依赖较小,几乎不受激光能量密度的影响,ZrH2的起始分解温度约为540℃,低于铝合金熔点,不易保留于基体,逸出的H2也能起搅动熔池的作用。
图10
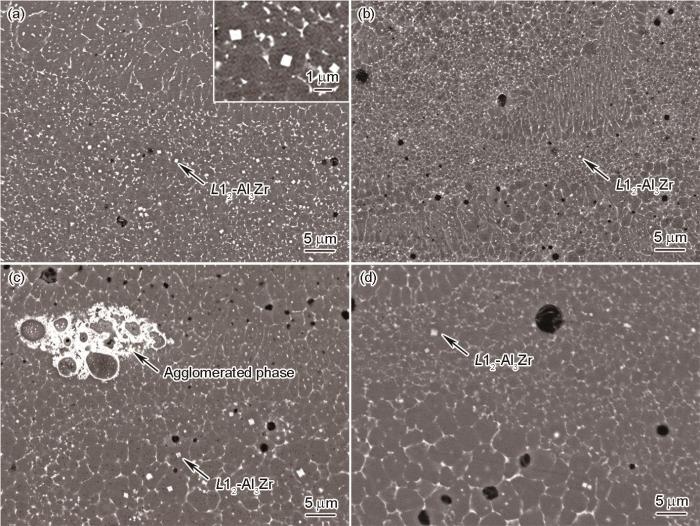
图10 不同激光能量密度成形的不同成分沉积态含锆Al-Cu-Mg合金的SEM背散射像
Fig.10 SEM backscatter images of as-built Al3Zr/Al-Cu-Mg (a, c) and in-situ Al3Zr/Al-Cu-Mg (b, d) alloys prepared with the laser energy density of 370 J/mm3 (a, b) and 154 J/mm3 (c, d) (Inset in Fig.10a shows the L12-Al3Zr precipitates)
表1 图10c中团聚相的EDS分析结果 (%)
Table 1
Element | Mass fraction | Atomic fraction |
---|---|---|
Al | 52.86 | 78.41 |
Cu | 2.63 | 1.66 |
Mg | 0.34 | 0.55 |
Zr | 44.17 | 19.38 |
一般需要通过热处理提高Al-Cu-Mg合金的综合力学性能,图11为370 J/mm3激光能量密度成形的含锆Al-Cu-Mg合金热处理态试样的SEM背散射像。热处理后,不同方式添加Al3Zr的合金显微组织相似,组织中不连续的网状共晶相消失,存在颗粒状或针状第二相。固溶处理促使Cu、Mg等元素溶解于Al基体,因此晶界共晶相消失;人工时效处理促使S相、θ相等第二相均匀析出[14,15]。
图11
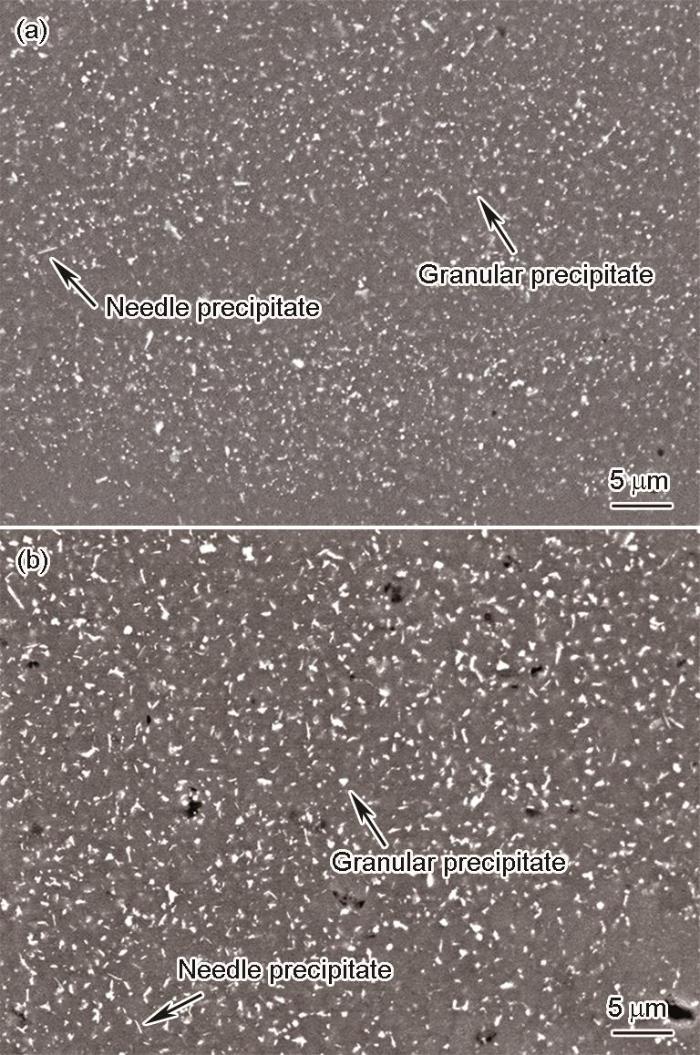
图11 370 J/mm3激光能量密度成形的热处理态含锆Al-Cu-Mg合金的SEM背散射像
Fig.11 SEM backscatter images of heat-treated Al3Zr/Al-Cu-Mg (a) and in-situ Al3Zr/Al-Cu-Mg (b) alloys prepared with the laser energy density of 370 J/mm3
2.4 力学性能与断口形貌
添加与未添加Al3Zr形核剂的Al-Cu-Mg合金沉积态与热处理态试样的室温拉伸性能如图12所示。沉积态Al-Cu-Mg合金为低应力脆性断裂,采用370 J/mm3激光能量密度成形的试样抗拉强度仅为(234 ± 7) MPa,伸长率为(3.4% ± 0.3%);而采用154 J/mm3激光能量密度成形的试样中存在大量热裂纹,几乎无拉伸性能。不同方式添加形核剂均可增强合金的综合力学性能,原位生成Al3Zr对合金性能的提升更为显著。当激光能量密度为370 J/mm3时,直接添加Al3Zr和原位生成Al3Zr的沉积态试样的抗拉强度分别为(358 ± 2)和(369 ± 9) MPa;当扫描速率增大,激光能量密度降至154 J/mm3时,抗拉强度分别下降了9.2%和3.8%。含原位生成Al3Zr合金的伸长率比含外加Al3Zr颗粒的合金高出30%。图12b显示在热处理后,试样的抗拉强度增加了约120 MPa,伸长率未有明显提升。其中,在高激光能量密度下,直接添加Al3Zr的试样强度最高,抗拉强度为(493 ± 2) MPa。图13为采用370 J/mm3激光能量密度成形的含锆Al-Cu-Mg合金沉积态和热处理态试样的断口形貌。含锆Al-Cu-Mg合金断口除了分布有孔隙外,均为韧窝特征,断裂方式为韧性断裂。原位生成Al3Zr的试样断口中韧窝更大、更深。在热处理后,合金韧窝内均可见大量第二相颗粒。
图12
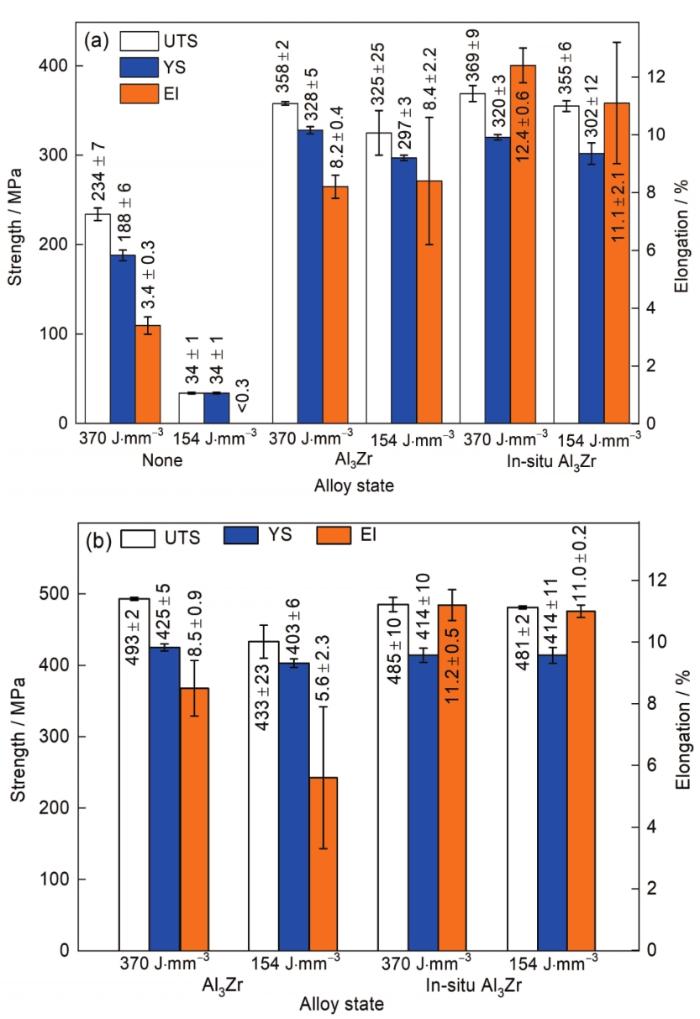
图12 采用不同激光能量密度成形的不同成分Al-Cu-Mg合金的沉积态与热处理态试样的力学性能
Fig.12 Mechanical properties of Al-Cu-Mg alloys with different components in as-built condition (a) and heat-treated condition (b) prepared with different laser energy density (UTS—ultimate tensile strength, YS—yield strength, El—elongation)
图13
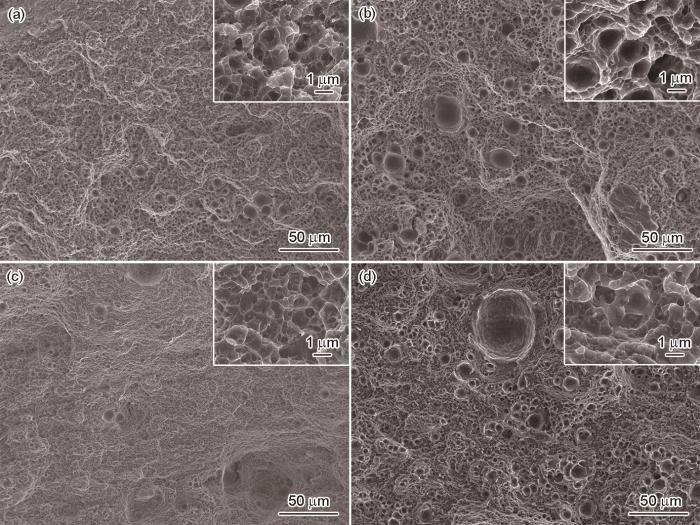
图13 370 J/mm3激光能量密度成形的含锆Al-Cu-Mg合金沉积态与热处理态试样的断口形貌
Fig.13 Fracture morphologies of Al3Zr/Al-Cu-Mg (a, c) and in-situ Al3Zr/Al-Cu-Mg (b, d) alloys in the as-built condition (a, b) and after heat-treated condition (c, d) prepared with the laser energy density of 370 J/mm3 (Insets show the fracture morphologies at high magnifications)
3 分析讨论
SLM成形的熔池温度高、冷却速率大、尺寸小,沿竖直方向的温度梯度高达105~106 K/s[25],熔池内过冷区较窄,α-Al形核困难[26],易依附于已有晶粒沿温度梯度方向外延生长。SLM成形铝合金的熔池凝固速率(约为106 K/s[27])与温度梯度具有相同的数量级。虽然Hunt[28]指出温度梯度与凝固速率的低比值有利于促进等轴晶形成,但是相邻熔道通过重熔使得熔池表面的细晶区的晶粒重新长大,因此沉积态Al-Cu-Mg合金仍然主要由柱状晶构成。而Al3Zr形核剂在熔体中可作为α-Al的形核质点,使晶粒摆脱外延生长模式,平均晶粒尺寸仅为1~2 μm,合金的[001]织构显著削弱。根据Scheil-Gulliver凝固模型可知[26],柱状枝晶间交叉接触形成的封闭区域无法获得液相补缩,Al-Cu系合金凝固区间宽,在液相快速凝固过程中产生应力集中,热裂纹易萌生于晶界;在添加形核剂后,半固态熔体中的等轴晶通过旋转、变形更易促进液相补缩[9],避免产生空腔,缓解热应力,抑制了裂纹。
在高温铝熔体中,晶粒细化剂Al3Zr颗粒和ZrH2颗粒均利用Al3Zr形核剂促进α-Al形核,但是2者提供的形核质点有所差异,原位生成Al3Zr的试样晶粒更细。进一步探讨不同方式添加Al3Zr的合金中含锆相的演变,示意图见图14。如图14a所示,不同于传统铸造铝合金,在SLM成形过程中,铝合金熔池的最高温度超过1600℃[29,30],平衡相熔点约为1577℃的Al3Zr可通过溶解和熔化2种方式实现物相演变。在Al3Zr/Al-Cu-Mg复合粉末的SLM成形过程中,激光能量输入使Al-Cu-Mg粉末熔为液相,熔池温度升高,Zr元素扩散速率迅速增大[31],Al3Zr颗粒加速溶解;当熔池温度超过Al3Zr熔点时,Al3Zr开始熔化。高冷却速率使得Al3Zr颗粒溶解和熔化过程均无法充分进行,因此铝熔体中包含有Zr原子和残留的Al3Zr颗粒,又因为熔池温度超过Al3Zr熔点的时间极短,外加Al3Zr颗粒以溶解为主。L12-Al3Zr是Al-Zr合金体系中原位反应和沉淀析出的初生相[31],随着熔池温度降低,Zr原子以L12-Al3Zr形式析出,L12-Al3Zr在液相中与残留的Al3Zr颗粒均可促进α-Al形核。随着温度进一步降低,L12-Al3Zr开始在固相晶界处析出。而SLM冷却速率大,L12-Al3Zr来不及发生平衡相变而保留于基体内部[32]。如图14b所示,在添加ZrH2的试样中,L12-Al3Zr不仅通过过饱和的Zr元素沉淀析出。稳定性低的ZrH2在铝合金粉末未熔时即开始分解,形成的Zr单质随后被卷入熔池原位反应得到L12-Al3Zr,Zr的稳定性低,除了溶解于铝熔体外,均发生了原位反应。不完全溶解或不完全熔化的L12-Al3Zr保留于铝熔体中,此时,α-Al的形核衬底为液相中原位生成的L12-Al3Zr和后析出的L12-Al3Zr。L12-Al3Zr与α-Al晶格错配度较小[9],可降低临界过冷度[25],易促进α-Al形核;如XRD结果(图1c)所示,由于常规工艺条件下L12-Al3Zr不稳定,制备的外加Al3Zr颗粒为Al3Zr平衡相,Al3Zr平衡相的形核能力弱于L12-Al3Zr。ZrH2提供的形核质点完全为L12-Al3Zr,因此具有更好的形核效果。
图14
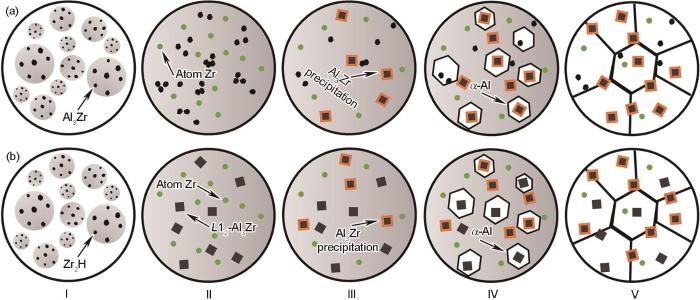
图14 沉积态含锆Al-Cu-Mg合金中含锆相演变的示意图
Fig.14 Schematics of Zr phase evolution in as-built Al3Zr/Al-Cu-Mg (a) and in-situ Al3Zr/Al-Cu-Mg (b) alloys
直接添加Al3Zr和原位生成Al3Zr均提高了沉积态Al-Cu-Mg合金的综合力学性能,原因除了与成功消除合金中热裂纹有关,也受到合金晶粒细化以及沉淀相和溶质原子数量增多的影响。以370 J/mm3激光能量密度成形的试样为例,由图6可知晶粒细化剂Al3Zr和ZrH2分别使沉积态Al-Cu-Mg合金的晶粒由15.69 μm细化至1.88和1.28 μm。合金屈服强度与晶粒尺寸的关系可用Hall-Petch公式表示,晶粒细化提升的强度(ΔσHall-Petch)为[11]:
式中,k为Hall-Petch常数(k取值0.13 MPa/m2 [16]),d1、d0为有、无晶粒细化剂试样的平均晶粒尺寸。因此,晶粒细化剂Al3Zr和ZrH2通过细化晶粒分别使沉积态试样屈服强度增加了约62和82 MPa,占各自屈服强度提升值的44.3%和62.1%。而Al3Zr第二相钉扎基体组织,可起弥散强化作用;过饱和Zr元素通过固溶强化提高了合金的变形抗力。同时,细晶组织促进合金内部晶粒间的协调变形,使合金塑性变形较为均匀,也改善了合金塑性。在热处理后,较多细小第二相(S相、θ相等)从基体中析出,可充当强化相,进一步提高了合金强度。
ZrH2虽然增多了合金的孔隙,但是提供的形核剂为原位生成的L12-Al3Zr和后析出的L12-Al3Zr,更有利于提高沉积态Al-Cu-Mg合金的综合力学性能。首先,利用ZrH2获得的形核质点均为L12-Al3Zr,形核效果更好,合金的变形抗力更大,合金的塑性提升也更为显著。其次,与外加Al3Zr颗粒相比,L12-Al3Zr与基体间的结合强度较高,更多数量的L12-Al3Zr更有利于提高合金的强度。此外,如图10所示,当扫描速率增大、激光能量密度降低时,晶粒细化剂Al3Zr颗粒分散受阻,在组织中作为较大硬脆相,致使试样强度下降较快;原位生成Al3Zr几乎无需强Marangoni对流分散晶粒细化剂,可适用于Al-Cu-Mg合金的较高速率成形。
4 结论
(1) 直接添加Al3Zr和原位生成Al3Zr分别使SLM成形Al-Cu-Mg合金的平均晶粒尺寸由15.69 μm细化至1.88和1.28 μm,均可消除热裂纹。
(2) 原位生成Al3Zr提供的形核剂具有更好的形核能力。利用ZrH2获得的形核质点均为形核能力较强的L12-Al3Zr,较易促进α-Al形核;而外加Al3Zr颗粒在铝熔体中的溶解和熔化过程均无法充分进行,提供的形核质点为L12-Al3Zr和形核能力较弱的外加Al3Zr颗粒。
(3) 含原位生成Al3Zr的SLM成形Al-Cu-Mg合金的综合力学性能更好,热处理态试样的抗拉强度可达(485 ± 10) MPa,伸长率为(11.2% ± 0.5%),直接添加Al3Zr的合金伸长率仅约为8.5%。原位生成Al3Zr几乎无需强Marangoni对流分散晶粒细化剂,可使Al-Cu-Mg合金适用于较高速率成形;外加Al3Zr颗粒的分散依赖于高的激光能量密度,致使采用600 mm/s扫描速率成形的沉积态试样抗拉强度仅为(325 ± 25) MPa。
来源--金属学报