分享:稀土Ce对非调质钢中硫化物特征及微观组织的影响
刘洁1, 徐乐,1, 史超2, 杨少朋1,3, 何肖飞1, 王毛球1, 时捷1
1.
2.
3.
通过稀土Ce微合金化手段,采用SEM、EDS和ASPEX等手段对不同Ce含量的非调质钢中的夹杂物形貌、数量和尺寸以及实验用钢的显微组织进行了表征,结合Thermo-Calc热力学软件对含Ce硫化物夹杂的形成过程进行了分析,并通过三维原子探针(3DAP)对晶界和相界面处的元素分布进行表征。结果表明,Ce在1800℃与S结合形成Ce3S4夹杂,1480℃转变为Ce2S3夹杂,1480℃以下形成Ce2S3为内核,Ti4C2S2和MnS包覆生长的复合夹杂物;添加Ce元素的实验用钢中90%以上的夹杂物的长径比小于2.5;Ce含量为0.019% (质量分数)时,实验用钢的组织最细,平均晶粒尺寸为4.17 μm。3DAP的结果证明了Ce在晶界和相界处存在明显偏聚,阻碍了C扩散,抑制晶粒长大,另外,高温区形成的细小弥散含Ce夹杂物提供了形核质点,2者共同作用细化了非调质钢的组织。
关键词:
非调质钢是在传统碳钢的基础上加入Nb、V、Ti等微合金化元素,采用控锻(轧)控冷等强韧化方法,达到或接近调质钢力学性能的一类优质结构钢[1,2]。非调质钢因其生产工艺简单、产品成材率高、节能环保等优点而被广泛应用于汽车曲轴和连杆等汽车零部件的制造[3,4]。其中易切削非调质钢在汽车整车使用量约占汽车总重量的2.1%,居汽车用钢铁材料的第三位[5]。据国际汽车制造商协会数据显示,我国2019年汽车年产量约2140万辆,随着我国汽车工业的迅速发展,国内对于非调质钢的需求量不断增长。在非调质钢中S元素发挥着非常重要的作用,MnS夹杂是非调质钢中存在的最典型的夹杂物[6]。硫化物的形态、数量和分布影响了钢材的加工性能和各项异性[7]。针对硫化物的改性,目前的研究主要集中于向非调质钢中添加Ca、Mg和稀土等对硫化物进行改性[8~11]。Ca元素用于夹杂物改性的成分范围较窄,Ca含量较低无法起到改质效果,较高又会在浇铸过程中存在堵水口的问题;Mg元素的加入面临的主要问题是易氧化,精炼过程中难以控制,收得率较低[9];而随着氧控制技术的进步,稀土元素收得率大大提高,可稳定控制,稀土可以和钢中的O、S、P等元素相互作用,起到净化晶界和夹杂物改性的目的[12]。
稀土Ce具有很强的化学活性,可与钢中的O、P、S等元素反应,被广泛应用于钢液净化和氧化物夹杂改质上[12,13]。针对钎具钢和H13钢中Ce对MgAl2O4的改质过程和机理,研究[14,15]发现Ce可以将MgAl2O4改质为Ce-O、Al-O和MgO的共生相,Ce的加入改变了钢液凝固过程中夹杂物的形成途径,从而改变夹杂物的类型[16]。Adabavazeh等[17]通过对低碳钢中的含Ce夹杂物进行研究发现,4~7 μm的CeO2夹杂可以作为针状晶内铁素体的形核点。但是,目前的研究主要集中在定性分析Ce对夹杂物的影响现象,缺乏工业生产所需的量化数据,且对于稀土Ce对硫化物夹杂的改性机制及其对组织的影响规律认识尚不清楚。本工作以中碳高硫非调质钢为研究对象,对比分析不同Ce含量下钢中硫化物的形成过程及成分、尺寸、形态特征,并结合Thermo-Calc等热力学软件对硫化物的形成进行热力学分析。通过三维原子探针(3DAP)对Ce元素在钢中的分布状态进行表征,揭示稀土Ce对非调质钢硫化物及微观组织的影响机理,为稀土微合金化非调质钢的工业生产提供基础理论。
1 实验方法
实验所用材料是在35MnVS的基础上降低V元素,添加Ti元素以及不同含量的Ce元素。实验用钢采用50 kg镁质真空感应炉冶炼,浇铸成39 kg、直径约110 mm圆型铸锭,铸锭经1200℃、2 h加热,锻造成直径20 mm的棒材,开锻温度为1180℃,终锻温度不低于850℃,锻后自然空冷。实验用钢的具体化学成分如表1所示。首先,根据GB/T 10561-2005《钢中非金属夹杂物含量的测定-标准评级图显微检验法》沿锻造方向切取20 mm × 15 mm × 4 mm的夹杂物分析试样,采用ASPEX夹杂物分析仪,对夹杂物的分布,组成及尺寸进行测定,扫描面积为20~25 mm2。利用Quanta-650FEG扫描电镜(SEM)和X-Max50能谱仪(EDS)对夹杂物的形貌和成分进行分析。切取金相试样,试样经磨抛后,采用浓度2%的硝酸酒精溶液腐蚀3~5 s以显示组织和晶界,并在DMI8A光学显微镜(OM)下进行观察,采用SISC- IAS8.0软件进行图像采集。将实验材料加工成直径3 mm、长10 mm的试样,在Formastor-F II全自动相变仪上采用热膨胀法对相变点Ac1和Ac3 (Ac1为加热时开始转变为奥氏体的温度,Ac3为加热时铁素体结束转变为奥氏体的温度)进行测定。并通过LEAP 5000XR 3DAP对晶界处的元素分布进行分析。
表1 实验用钢的化学成分 (mass fraction / %)
Table 1
Steel | C | Si | Mn | P | Alt | S | V | Ti | Ce | Fe |
---|---|---|---|---|---|---|---|---|---|---|
R0 | 0.37 | 0.48 | 1.35 | 0.0060 | 0.005 | 0.059 | < 0.005 | 0.063 | - | Bal. |
R1 | 0.38 | 0.46 | 1.36 | 0.0042 | < 0.005 | 0.051 | < 0.005 | 0.059 | 0.010 | Bal. |
R2 | 0.38 | 0.43 | 1.40 | 0.0050 | < 0.005 | 0.063 | < 0.005 | 0.059 | 0.019 | Bal. |
R3 | 0.38 | 0.47 | 1.39 | 0.0045 | < 0.005 | 0.064 | < 0.005 | 0.058 | 0.027 | Bal. |
2 实验结果
2.1 夹杂物的种类和形貌
未添加Ce的35MnVS钢中典型的夹杂物主要有3类:Al2O3夹杂,主要呈现尖角状,尺寸较小;单一的MnS和Ti4C2S2夹杂,MnS夹杂主要呈长条形,沿锻造方向分布,尺寸和长径比较大,是R0实验用钢中的主要夹杂;MnS-Ti4C2S2复合夹杂。添加Ce的实验用钢中夹杂物类型主要为单一的(Ce-S),或(Ce, Mn)S、(Ce-S)-Ti4C2S2和(Ce, Mn)S-Ti4C2S2复合夹杂。为更清楚地了解夹杂物的元素组成,对ASPEX数据进行归一化处理并绘制三元相图,结果如图1所示。
图1
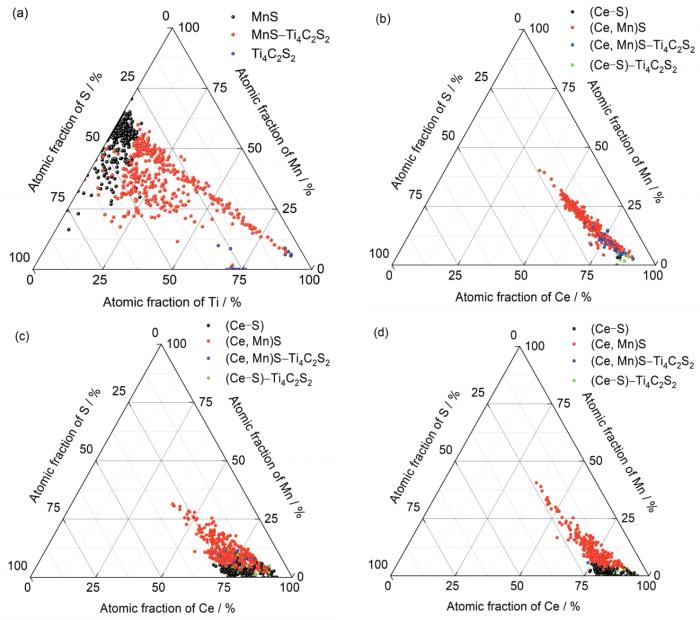
图1 实验用钢中夹杂物的组成
(a) R0 (b) R1 (c) R2 (d) R3
Fig.1 Compositions of inclusions in steel
对(Ce, Mn)S和(Ce, Mn)S-Ti4C2S2复合夹杂物进行面扫描EDS,结果如图2所示。可以看出,复合类夹杂主要呈球形和椭球形,且有明显的分区和聚集现象。Ce-S在扫描电镜下呈现灰白色,相对基体颜色较浅,主要呈球形分布。而MnS和Ti4C2S2主要呈现深灰色或黑色,相对基体颜色较深,主要分布在球形Ce-S夹杂的边部或内部。
图2

图2 钢中复合夹杂物面扫描分析
(a) (Ce, Mn)S-Ti4C2S2 (b) (Ce, Mn)S
Fig.2 EDS mappings of composite inclusions in steel
2.2 夹杂物的的数量和尺寸
加入稀土Ce后,不仅夹杂物的组成和形貌会发生改变,其尺寸和数量也会发生相应的改变。4种实验用钢中夹杂物的显微组织如图3所示。采用ASPEX夹杂物分析软件,对不同Ce含量的钢扫描面积内的夹杂物分布及尺寸进行统计,结果如图4 (图中X、Y分别表示夹杂物所在位置的横纵坐标)和5所示,实验用钢夹杂物长径比的统计结果如图6所示。
图3

图3 夹杂物显微组织的OM像
(a) R0 (b) R1 (c) R2 (d) R3
Fig.3 OM images of microstructures of inclusions
图4
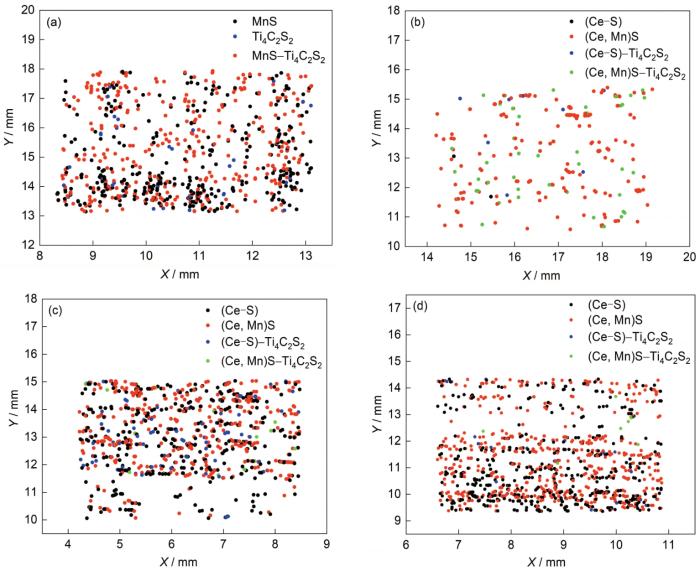
图4 钢中夹杂物分布
(a) R0 (b) R1 (c) R2 (d) R3
Fig.4 Distributions of inclusions in steel
图5
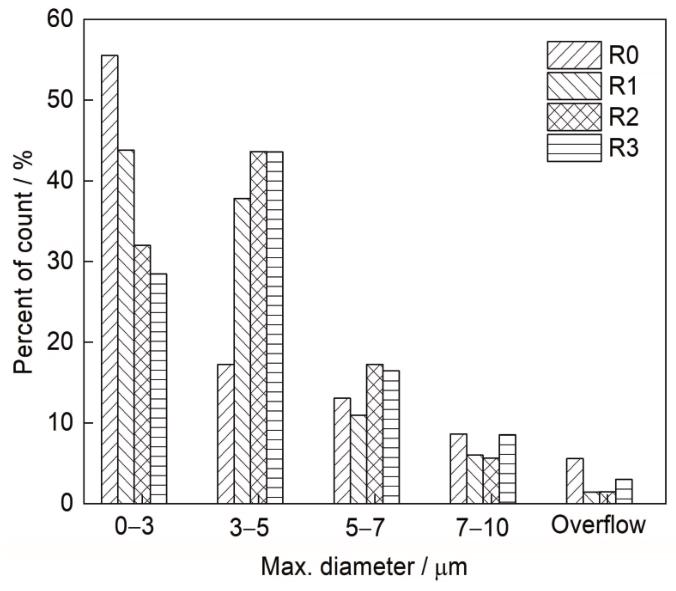
图5 钢中夹杂物的数量和尺寸
Fig.5 Numbers and sizes of inclusions in steel
图6

图6 钢中夹杂物的长径比
Fig.6 Aspect ratios of inclusions in steel
从图4中夹杂物的类型和分布可以看出,随着Ce含量的增加,钢中的夹杂物数量呈现出先减少后增加的趋势,当Ce含量从0增加到0.01%后,钢中夹杂物数量有了明显减少,且夹杂物类型由MnS和MnS-Ti4C2S2转变为以(Ce, Mn)S和(Ce, Mn)S-Ti4C2S2夹杂为主加少量的Ce-S夹杂。继续增加Ce含量,钢中的Ce-S夹杂物含量明显增加,这是由于钢中的S含量较高,继续增加Ce含量时,Ce和S结合形成更多Ce-S夹杂,如图4所示。与添加Ce的钢相比,未加Ce的R0钢的夹杂物在两端0~3 μm和> 10 μm范围内分布较多,分别为55.5%和5.6%;R1钢中0~3 μm的夹杂物数量占比最多,为43.8%,> 10 μm的夹杂仅占1.41%;R2和R3的夹杂物主要分布范围在3~5 μm,分别为43.62%和43.57%;R3实验用钢中> 10 μm的夹杂物较多,约占3%。结果表明,Ce含量为0.01%时,钢中的夹杂物数量最少,继续增加Ce含量,钢中夹杂物的密度明显增加,这会导致夹杂物的碰撞和聚集[18],钢中夹杂物的尺寸呈现出逐渐增大的趋势,如图7所示,在Ce含量为0.027%时,夹杂物出现明显的聚集现象。Ce的添加不仅会改变夹杂物的尺寸,从夹杂物形貌来看,其长径比也会发生改变。从图6中可以看出,实验用钢在添加Ce元素后,夹杂物的长径比有了明显减小。未添加Ce元素的钢中夹杂物的长径比主要分布在1~1.5和> 2.5的范围内。添加Ce含量的钢中夹杂物长径比主要分布在1~2之间,且随着Ce含量的增加,呈现逐渐减小的趋势,这主要与钢中的Ce-S夹杂有关。随着Ce含量的增加,钢中的Ce-S夹杂物含量明显增加,Ce-S夹杂物主要呈球形,因此,随Ce含量的增加,钢中夹杂物的长径比减小。
图7
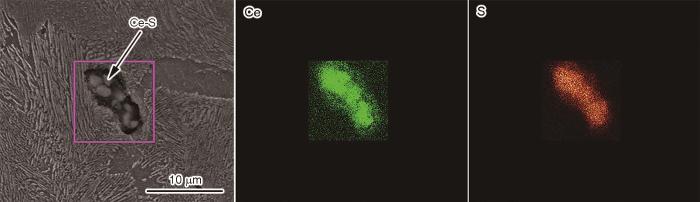
图7 0.027%Ce实验用钢(R3)中夹杂物聚集图
Fig.7 Inclusion accumulation diagram in test steel containing 0.027%Ce (R3)
2.3 晶粒尺寸
实验用钢的显微组织如图8所示。可以看出,实验用钢的显微组织由白色的铁素体和黑色的珠光体组成。随着钢中Ce含量的增加,实验用钢的显微组织呈现出先细化后粗化的现象,且在Ce含量为0.019%时,显微组织最细,平均晶粒尺寸为4.17 μm。组织中铁素体的类型发生改变,由起初的网状铁素体转变为块状铁素体,随后又转变为网状铁素体。铁素体的含量也发生了相应变化,采用Image-Pro Plus软件对组织中铁素体的含量进行统计,结果如图9所示。可以看出,Ce含量为0.019%时,钢中铁素体含量最高,继续增加Ce含量,钢中铁素体的含量下降,当Ce含量达到0.027%时,钢中铁素体含量低于不添加Ce元素的钢。
图8
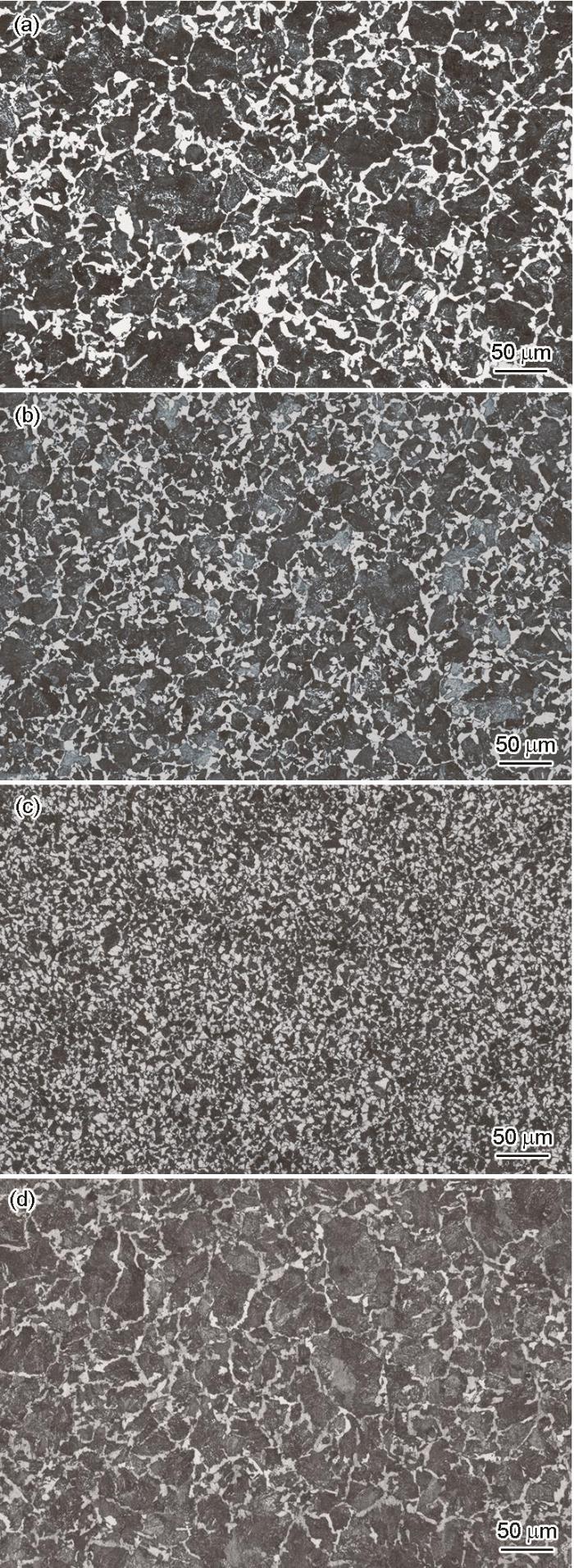
图8 实验用钢显微组织的OM像
(a) R0 (b) R1 (c) R2 (d) R3
Fig.8 OM images of microstructures of the test steels
图9

图9 实验用钢中的铁素体含量
Fig.9 Ferrite contents of the test steels
3 分析讨论
3.1 稀土Ce对硫化物的改质机理
为了研究稀土复合类夹杂物的形成机理,对含Ce的实验用钢进行热力学计算。利用Thermo-Calc热力学软件对R1钢的平衡凝固进行理论计算。系统总量取1 mol,计算结果如图10所示。铈类夹杂在钢液凝固前已经形成,在1800℃以上,Ce和S先结合形成Ce3S4,主要发生反应(1)。然后在1730℃左右生成的Ce3S4以及钢液中的Ce继续和S结合转变为Ce2S3,主要发生反应(2)和(3)。当钢液的温度下降到1600℃,钢中的Ce2S3含量基本不随温度的变化而改变。钢中的Ti4C2S2和MnS均在钢液凝固过程中,分别在1480和1430℃左右开始析出。由此可见,Ce2S3的形成温度要高于Ti4C2S2和MnS,因此,在钢液的冷却过程中,Ce2S3先析出,而后析出的Ti4C2S2和MnS只能在Ce2S3的边部析出。
图10
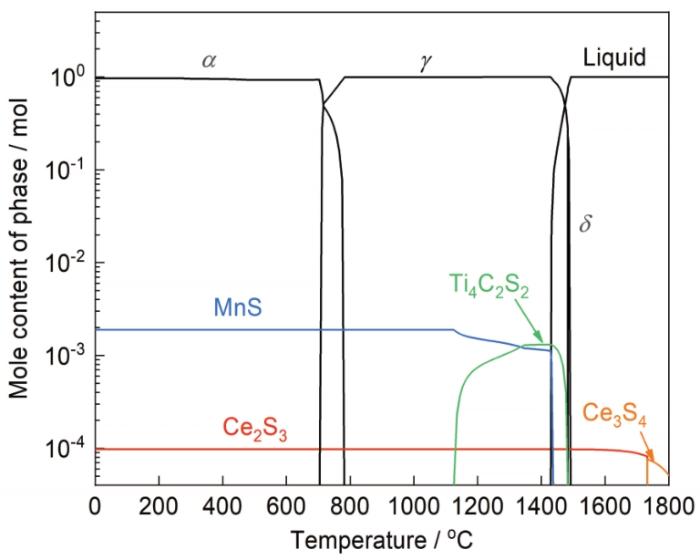
图10 R1钢的单轴平衡性质图
Fig.10 Uniaxial balance property diagram of R1 steel
根据以上的热力学计算和分析,并结合夹杂物成分与形貌显微分析表征结果,本实验用钢中铈基复合夹杂物的形成过程如图11所示。
图11
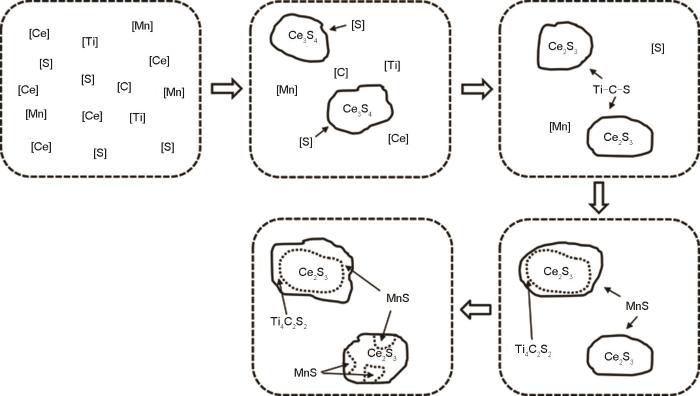
图11 铈基复合夹杂物的生成过程简图
Fig.11 The generation process diagram of cerium-based composite inclusions
3.2 稀土Ce对显微组织的影响
从图8可以看出,向实验用钢中添加一定量的Ce,显微组织有了明显细化,Ce含量为0.019%时显微组织最细,且铁素体的含量随Ce含量的增加先增加后减少。晶粒细化的原因主要有2个方面[19~21]:① α相的形核率提高,增加γ → α的相变驱动力和α的形核质点均可提高α相的形核率;② 晶粒长大受到阻碍,最为常见的方法是通过钉扎晶界来阻碍新晶粒的长大。为研究Ce对γ → α相变的影响,测定了实验用钢的相变点Ac1和Ac3,结果如表2所示。可以看出,添加Ce可以降低铁素体相变的起始温度点,随着Ce含量的增加铁素体转变的开始温度呈现出波动现象。Ce含量在0~0.019%时,Ac1相变点逐渐降低。当Ce含量从0.019%增加至0.027%时,Ac1相变点明显提高。Ac1相变点温度越低,形核率越高,晶粒长大的速率越慢,组织越细小,铁素体含量也越多。因此在Ce含量为0.019%时,实验用钢的组织最细小,铁素体含量最多。铁素体和珠光体的相变由C与合金元素的扩散控制,Ce对相变影响的内在机制与其在钢种的分布状态及其对C元素扩散的影响密切相关。
表2 实验用钢的相变点
Table 2
Steel | Ac1 / oC | Ac3 / oC |
---|---|---|
R0 | 715 | 803 |
R1 | 705 | 780 |
R2 | 675 | 795 |
R3 | 710 | 785 |
Liang等[22]研究表明,贝氏体基钢中的稀土元素可以降低晶界的界面能,阻碍C原子的扩散。Jiang等[23]通过第一性原理计算发现,在低碳钢和低合金钢中,稀土的加入可以通过阻碍C扩散改变扩散相变的起始温度,从而细化铁素体组织。上述实验初步证实了Ce对组织的作用,但并未对Ce在钢中的分布状态进行表征。为此,选取Ce含量为0.019%的实验用钢,采用3DAP对晶界和相界面处的原子分布进行扫描,其中主要元素分布结果如图12所示。可以看出,Ce在α-α晶界处有偏聚,在α-P相界面上无法看到明显的原子偏聚。为进一步分析界面处的原子偏聚现象,分别在α-α晶界和α-P相界面处选取观察范围进行分析,结果如图13所示。其中,图13a为α-α晶界处选取的观察区域,图13b为α-P相界面处选取的观察区域;图13c为α-α晶界处Ce和S元素的分布,图13d为α-P相界面处Ce和S元素的分布。
图12
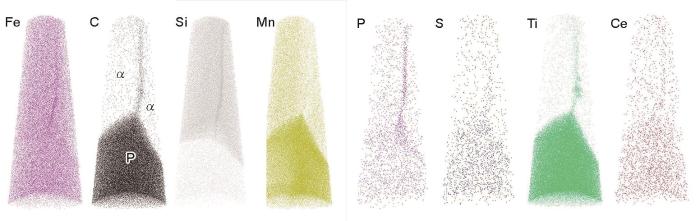
图12 晶界和相界面处的元素分布
Fig.12 Element distributions at grain boundary and phase interface
图13

图13 晶界及相界面处Ce和S的元素分布
(a) diagram of scanning position of α-α grain boundary (unit: nm)
(b) diagram of scanning position of α-P phase boundary (unit: nm)
(c) element distributions at α-α grain boundaries
(d) element distributions at α-P phase boundaries
Fig.13 Element distribution of Ce and S at grain boundary and phase interface
从图13可以看出,Ce原子在晶界和相界面处有明显的偏聚现象,而晶界和相界面处无明显的S元素偏聚。说明晶界和相界面上均存在固溶Ce原子的偏聚,其中相界面处的偏聚更为明显。Ce的相对原子质量较大,固溶于钢中的Ce容易产生晶格畸变,从而阻碍位错运动,晶界处的Ce偏聚会阻碍晶界运动,细化γ晶粒。亚稳奥氏体转变成铁素体和珠光体的过程中,会发生C原子的长距离运输。由于C在铁素体中的溶解度低,在边部成核的铁素体的生长伴随着奥氏体中C的排斥。相比于晶内,奥氏体晶界上的驱动力更高,C的扩散率更快。在相变过程中铁素体沿奥氏体晶界的长大速率远高于晶内,因此会形成一层网状铁素体并迅速覆盖整个晶界区域[24]。由于固溶的Ce对C元素的吸附作用,阻碍了C元素的扩散,从而阻碍了γ→α的转变过程中γ晶界上形成的α相的晶粒长大,阻碍了网状铁素体的迅速扩展。
向钢中添加Ce元素后,钢中的夹杂物长径比明显减小。当Ce含量超过0.019%时,95%以上的夹杂物长径比都小于2.5,而在未添加Ce的实验用钢中这一比例仅为56%。添加Ce元素的钢中尺寸在10 μm以上的夹杂数量少于未添加Ce的钢。这种细小弥散的夹杂物可以作为异质形核点,提供形核核心。这些夹杂物作为异质形核点需满足2个条件[16]:① 夹杂物和凝固相之间的晶格失配必须小于6%,且夹杂物尺寸在4~7 μm[17]之间才能作为凝固相的形核质点。研究[25,26]表明,稀土颗粒和钢基体之间的晶格失配小于6%,将降低形核势垒并促进新固相的凝固。Ce含量为 0.019%的实验用钢中4~7 μm之间的夹杂物数量最多,为35.1%。当Ce含量为0.027%时,> 7 μm的夹杂物尺寸明显增加,达到11.5%。② 夹杂物的熔点必须高于合金的熔点。从图10计算的性质图可以看出,设计钢的熔点在1430℃左右,而铈类夹杂物的熔点在1700℃以上,远高于合金的熔点。这种高熔点的类球型夹杂物弥散分布在钢液中,在钢液凝固过程中,作为异质形核点,促进铁素体晶粒形核,从而细化晶粒。如图14所示,在0.019%Ce含量的实验用钢中观察到了在复合类夹杂物周围形成的晶内铁素体(IGF)。
图14
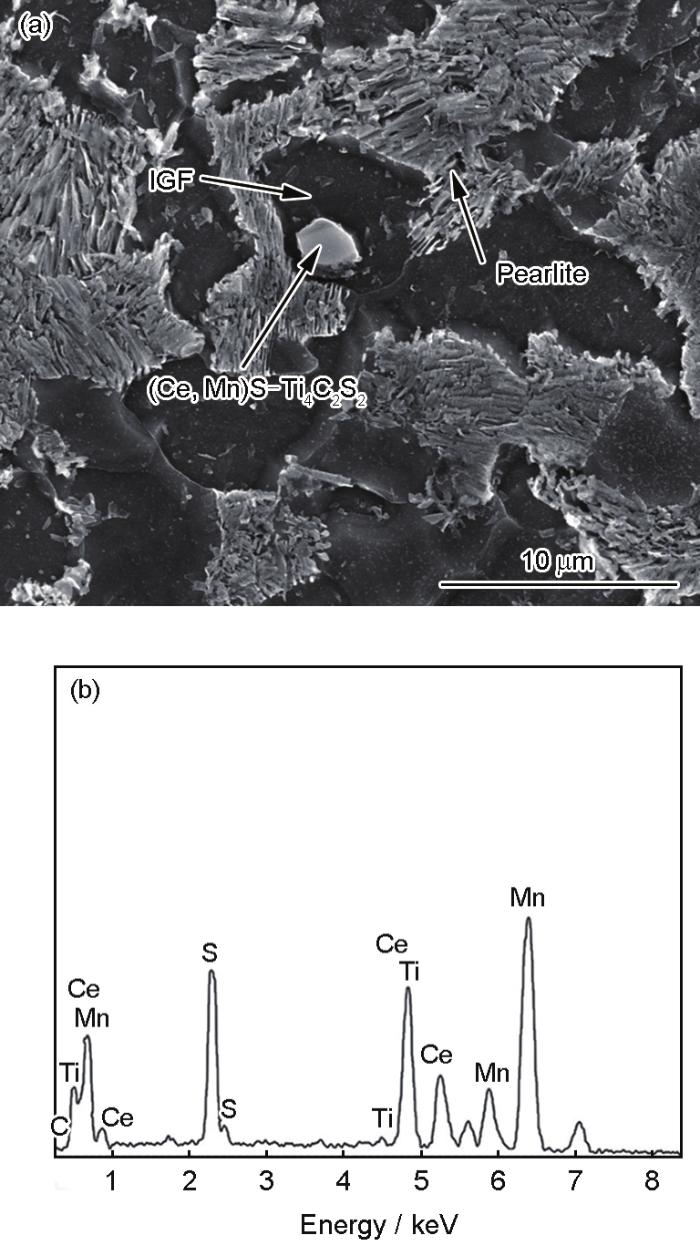
图14 复合夹杂物周围的晶内铁素体
(a) SEM image of tissue
(b) EDS point scanning of inclusions
Fig.14 Intra-granular ferrite (IGF) around the composite inclusion
随着实验用钢中Ce含量的增加,钢中夹杂物的数量增多,尺寸逐渐增加。当Ce含量达到0.027%时,夹杂物尺寸有了明显增加,一部分尺寸较大的夹杂物在钢液凝固过程中不能作为形核质点。因此随着Ce含量的增加,钢中的有效形核质点的数量先增加后减少。当Ce含量达到0.019%时,其有效形核质点数量最多,当Ce含量达到0.027%时,钢中的有效形核质点数量下降。同时,文献[25]中提到当铈类夹杂物的尺寸< 2 μm时可以起到钉扎晶界的作用。Ce含量从0.019%提高至0.027%时,钢中< 2 μm的夹杂物由8.8%降至6.1%,夹杂物对于晶界的钉扎作用减弱。因此,随着Ce含量的增加铁素体晶粒尺寸先减小后增大。
4 结论
(1) 未添加稀土Ce的非调质钢中的夹杂物以长条状的MnS为主,含有少量的Ti4C2S2夹杂;含0.01%Ce的非调质钢夹杂物类型变为椭球形或球形的(Ce, Mn)S复合夹杂和(Ce, Mn)S-Ti4C2S2复合夹杂以及少量的单一Ce-S夹杂,继续增加Ce含量,钢中的Ce-S夹杂物含量增加。
(2) (Ce, Mn)S复合夹杂以及(Ce, Mn)S-Ti4C2S2复合夹杂主要呈椭球形或球形。热力学计算与微观成分分析表明,Ce和S在1800℃以上先结合形成Ce3S4,在1730℃时Ce3S4转变为Ce2S3,随后Ti4C2S2和MnS分别在1480和1430℃左右开始析出,形成了内核为Ce-S,MnS和Ti4C2S2包覆生长的复合夹杂。
(3) 随着非调质钢中Ce含量的增加,钢中的夹杂物数量先减少后增加。经ASPEX统计分析表明,夹杂物长径比减小至1~2.5之间。这主要与添加稀土Ce改变夹杂物类型有关,随着Ce含量的增加,钢中的Ce-S夹杂明显增加。Ce-S夹杂、(Ce, Mn)S复合夹杂以及(Ce, Mn)S-Ti4C2S2复合夹杂呈椭球形,降低了夹杂物的长径比。
(4) 随着钢中Ce含量的增加,钢的显微组织呈现出先细化后粗化的现象,相应的铁素体含量先增加后减少。当Ce含量为0.019%时钢的显微组织最细,平均晶粒尺寸为4.17 μm,铁素体含量达到39%。且铁素体也由网状铁素体变为块状铁素体,继续增加Ce含量至0.027%,铁素体恢复网状分布。3DAP结果证明了稀土Ce元素在晶界和相界处偏聚,大尺寸的Ce原子可阻碍C扩散,抑制晶粒长大与网状铁素体形成,同时高熔点的细小弥散的含Ce夹杂提供了形核质点,促进了晶内铁素体形核,2者共同作用细化了实验用钢的组织。当Ce含量增加到0.027%时,钢中夹杂物的尺寸增大、聚集,有效形核质点数量降低,同时对晶界的钉扎作用减弱,导致组织粗化。
来源--金属学报