分享:高铁转向架用钢G390NH在模拟海洋和工业大气环境下的腐蚀行为及产物演化规律
宋嘉良1,2, 江紫雪1,2, 易盼3, 陈俊航1,2, 李曌亮1,2, 骆鸿,1,2, 董超芳1,2, 肖葵
,1,2
1.
2.
3.
通过周浸实验结合腐蚀动力学、常规电化学、微观形貌及腐蚀产物成分分析等方法,研究了在模拟加速海洋和工业大气环境下高铁转向架用钢G390NH的腐蚀行为和产物层的演化规律。结果表明,与
关键词:
全球每年因腐蚀造成的损失超过4万亿美元[1],其中大气腐蚀作为材料最常见的腐蚀形式,普遍存在于交通运输、基础设施等领域。耐候钢的开发与应用在一定程度上平衡了选材的经济性与服役寿命2方面[2]。学者们普遍认为,Cr、Ni、Cu等耐蚀性合金元素可提高耐候钢的抗大气腐蚀性能[3,4]。然而,当耐候钢暴露在实际的腐蚀性环境中,尽管存在耐蚀性合金元素,但它们仍然会遭受严重的腐蚀[5,6]。对于大量应用耐候钢的高速铁路转向架,需要长期在海洋、污染、湿热、严寒等不同的大气环境中进行服役[7~10],不同的环境会导致其产生差异性的腐蚀结果,系统研究转向架用钢在某些典型环境中的腐蚀行为,揭示其腐蚀机理就显得十分迫切。
大量的研究[5,11~13]表明,低碳钢在大气腐蚀过程中形成的产物主要为γ-FeOOH、α-FeOOH、β-FeOOH、Fe(OH)3和Fe3O4,它们可以以定型态或非定型态结构存在于锈层中。其中,α-FeOOH是最稳定的腐蚀产物[13],可以有效降低耐候钢的腐蚀速率。γ-FeOOH会在腐蚀初期形成,在受到金属内合金元素与大气的干湿交替等影响后,部分将会转变成稳定的α-FeOOH[2,14,15]。
有关环境因素对耐候钢腐蚀的影响已有较多的研究。Singh等[14]在研究气候条件对结构钢的腐蚀影响中发现,SO2和NaCl显著改变了金属表面锈层的结构和防护特性,并且长期腐蚀速率由其原始表面暴露的初始阶段形成的锈层类型控制。根据Yamashita等[11]的研究结果,在
目前对于高铁转向架用钢在以NaCl为主的海洋大气和以NaHSO3为主的工业大气环境下的腐蚀行为和腐蚀机理方面的研究尚未展开,因此揭示Cl-和
1 实验方法
1.1 实验材料
实验材料为G390NH钢。钢材在真空感应炉中熔炼,经过锻造得到钢坯,最后轧制成为12 mm厚的钢板。其化学成分(质量分数,%)为:C 0.067,S 0.0016,P 0.014,Si 0.32,Cu 0.30,Cr 0.47,Mn 1.22,V 0.030,Nb 0.014,Ni 0.20,Fe余量。其主要力学性能参数为:屈服强度487 MPa,抗拉强度542 MPa,屈强比0.817,延伸率29.39%,低温冲击韧性(-40℃) 216 J/cm2。
通过线切割得到尺寸为50 mm × 25 mm × 2 mm的挂片试样,将试样表面粗糙度用砂纸打磨至800号,用无水乙醇清洗、冷风吹干。用游标卡尺测量试样的原始尺寸,采用精度为0.1 mg的天平称量试样的原始质量,并记录保存。电化学试样加工尺寸为10 mm × 10 mm × 2 mm,将其中一个正方形面选作实验用,其背面与铜导线进行焊接,之后通过环氧树脂将实验面之外的5个面进行密封,电化学试样表面粗糙度用砂纸打磨至2000号,以同挂片试样的方法进行保存。
1.2 腐蚀加速实验
加速实验前使用4% (体积分数)硝酸酒精溶液对机械抛光后的试样表面进行侵蚀,并利用KEYENCE VHX-2000显微镜(OM)观察G390NH的金相组织。
周期浸润加速实验参照TB/T 2375—1993《铁路用免涂装钢周浸腐蚀实验方法》进行,2组各设置4个周期,分别在24、120、240以及360 h时取样。周浸实验每个循环的时间为60 min,其中浸泡时间12 min,溶液温度45℃,干燥时间48 min,干燥温度65℃。每个周期4片平行样与3个电化学试样。实验溶液分别选用3.5%NaCl (质量分数,下同)和0.01 mol/L NaHSO3,在Cl-环境中测量pH值约为7,保持中性;在
实验后,采用失重法计算2种环境下不同周期试样的腐蚀失重。具体的过程为:采用标准除锈液(500 mL 浓盐酸+ 500 mL去离子水+ 3.5 g六次甲基四胺)去除试样表面铁锈,然后经去离子水及无水乙醇清洗,吹干后置于干燥箱中保存24 h称重,并对失重数据进行计算(每组取3个平行试样,取平均值),计算方法[18]为:
式中,D为单位面积的质量损失,g/m2;W0为试样腐蚀前的质量,g;Wt为试样腐蚀除锈后的质量,g;S为试样表面积,m2。
1.3 电化学测试
使用Princeton V3电化学工作站对G390NH在2个环境中各周期的试样进行极化曲线测试。采用三电极体系,试样为工作电极,暴露面积为1 cm2,铂片为辅助电极,参比电极选择Ag/AgCl电极,测试温度为室温(25℃),腐蚀介质同周浸实验,分别为3.5%NaCl和0.01 mol/L NaHSO3溶液。电化学测试前,先将锈层试样在溶液中浸泡30 min,待开路电位(OCP)稳定后开始进行动电位极化曲线的测量。选择相对开路电位± 500 mV的测量范围,扫描速率0.33 mV/s。
1.4 腐蚀形貌及产物分析
使用EOS 6D数码相机对每周期烘干后的试样进行宏观分析,试样的微观形貌和锈层截面使用Quanta 250环境扫描电镜(SEM)进行观测,并利用SEM配套的能谱仪(EDS)对截面进行面扫,观察对比元素分布。对于每周期试样腐蚀产物的分析,首先通过物理手段剥离开内外锈层,在干燥24 h后,采用Dmax-RC旋转阳极X射线衍射仪(XRD)进行物相分析,CuKα,管压40 kV,电流150 mA,扫描范围20°~100°,步宽0.02°,扫描速率10°/min。使用Jade 6软件通过RIR方法对XRD测试数据进行半定量分析[19]。
2 实验结果
2.1 腐蚀动力学
腐蚀实验前对G390NH显微组织进行观察分析,如图1所示,微观组织主要是由块状铁素体及少量珠光体组成,其中由于材料在成型过程中经过轧制处理,钢中的珠光体呈带状析出。
图1

图1 G390NH显微组织的OM像
Fig.1 OM image of microstructure for G390NH
为了研究G390NH在3.5%NaCl和0.01 mol/L NaHSO3溶液周浸实验中的腐蚀动力学,利用质量损失公式,计算试样在不同实验周期后的腐蚀失重,并根据
图2
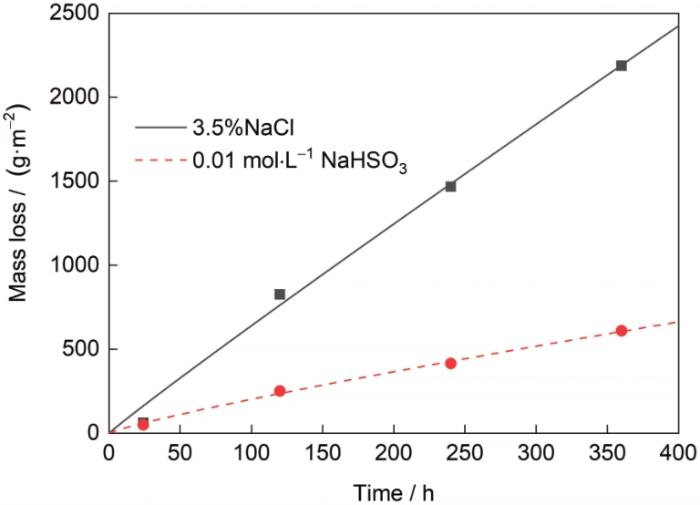
图2 G390NH在3.5%NaCl和0.01 mol/L NaHSO3溶液中的腐蚀失重曲线
Fig.2 Corrosion mass loss curves of G390NH in 3.5%NaCl and 0.01 mol/L NaHSO3 solutions
表1 G390NH在3.5%NaCl和0.01 mol/L NaHSO3溶液中的腐蚀动力学拟合结果
Table 1
Salt solution |
|
|
|
---|---|---|---|
3.5%NaCl | 7.664 | 0.961 | 0.991 |
0.01 mol/L NaHSO3 | 3.926 | 0.856 | 0.995 |
式中,A表示初始腐蚀质量损失,g/m2;t为实验时间,h;n为拟合常数,与锈层保护性能有关。
分析腐蚀动力学拟合结果,基于2次拟合优度均为
图3

图3 G390NH在3.5%NaCl和0.01 mol/L NaHSO3溶液中经过不同周期周浸后的腐蚀速率及其比值
Fig.3 Corrosion rate and ratio of G390NH after different cycle immersion in 3.5%NaCl and 0.01 mol/L NaHSO3 solutions
综上分析,G390NH在酸性
2.2 电化学性质
对周浸实验后的G390NH试样进行电化学测试,得到其不同周期的电化学极化曲线,如图4所示,拟合结果如表2所示。对比图4a和b的曲线,可以看出在NaCl环境中阳极段出现明显的类钝化区间。Pan等[20]在研究碳钢大气腐蚀行为时测量极化曲线也发现同样的规律,阳极电化学反应的控制步骤为扩散控制步骤,随实验时间的延长,特点越明显。其原因可能是随着腐蚀的进行,表面的锈层厚度不断增加,使得在金属发生溶解的反应中金属离子扩散受到阻碍,而对于极化曲线的阴极段而言却没有明显的变化,且始终保持较高的反应速率,这说明锈层厚度的增加不会影响尺寸较小的阴离子通过,进而在NaCl环境中金属始终保持较高的腐蚀速率。在NaHSO3环境中,随着时间延长,极化曲线的形状几乎没有变化,且阴极段和阳极段速率基本相同,这说明腐蚀反应中阴极反应和阳极反应发生的速率也基本相同,控制步骤为扩散和电荷转移混合控制,腐蚀形成的锈层可以很好地抑制阴阳极反应离子在内部发生扩散,另外合金的腐蚀电位也相对较高,体系活性较低,因此在NaHSO3环境中腐蚀程度明显较低。
图4
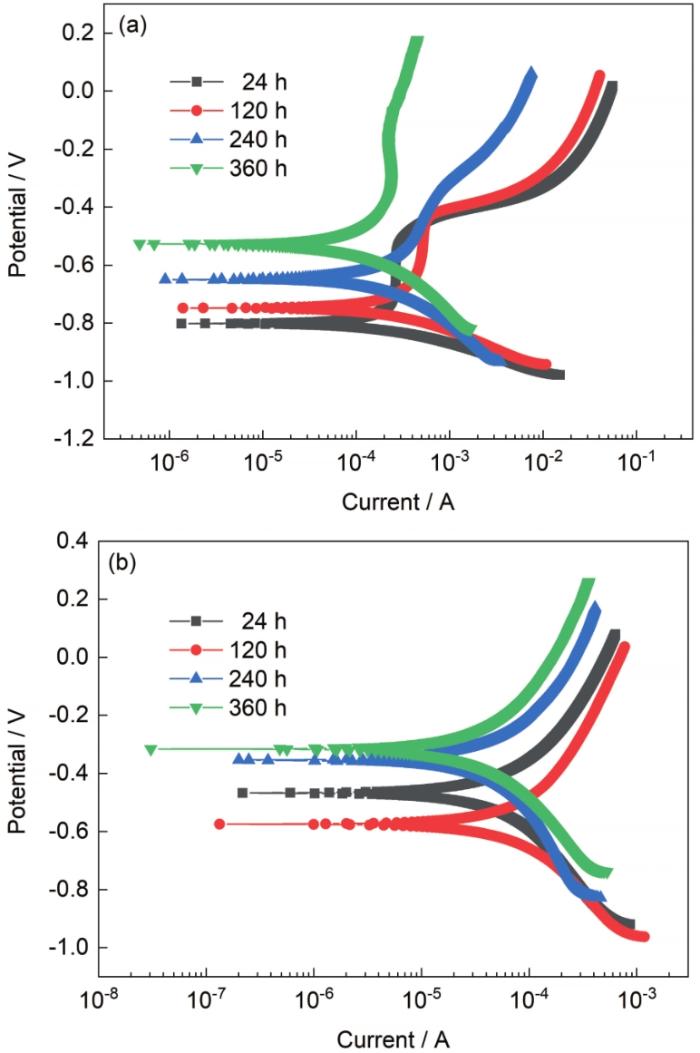
图4 G390NH在2种环境中的电化学极化曲线
Fig.4 Electrochemical polarization curves of G390NH in 3.5%NaCl (a) and 0.01 mol/L NaHSO3 (b) solutions
表2 G390NH在3.5%NaCl和0.01 mol/L NaHSO3溶液中的极化曲线拟合结果
Table 2
Salt solution | Test period / h | Ecorr / V | Icorr / μA |
---|---|---|---|
3.5%NaCl | 24 | -0.800 | 214.934 |
120 | -0.748 | 272.736 | |
240 | -0.652 | 287.560 | |
360 | -0.526 | 167.710 | |
0.01 mol/L NaHSO3 | 24 | -0.465 | 43.269 |
120 | -0.574 | 69.919 | |
240 | -0.346 | 30.411 | |
360 | -0.310 | 28.516 |
图5所示为G390NH试样在电化学测试拟合后自腐蚀电位Ecorr和自腐蚀电流Icorr的变化趋势汇总。对比可以看出,随着实验时间的延长,G390NH的Ecorr在NaHSO3环境中呈现先降低后升高的趋势,在NaCl环境中不断升高。Icorr则均呈现先增加后降低的趋势,结果与腐蚀失重数据相符。由于腐蚀介质中酸碱性具有明显区别,结合极化曲线可以得到,在中性NaCl溶液中,阴极反应主要发生的是氧去极化腐蚀,而在NaHSO3溶液中,受到H+的作用,阴极反应主要为析氢腐蚀。由于G390NH属于低合金钢,因此阳极反应均为金属溶解过程。反应式如下:
图5
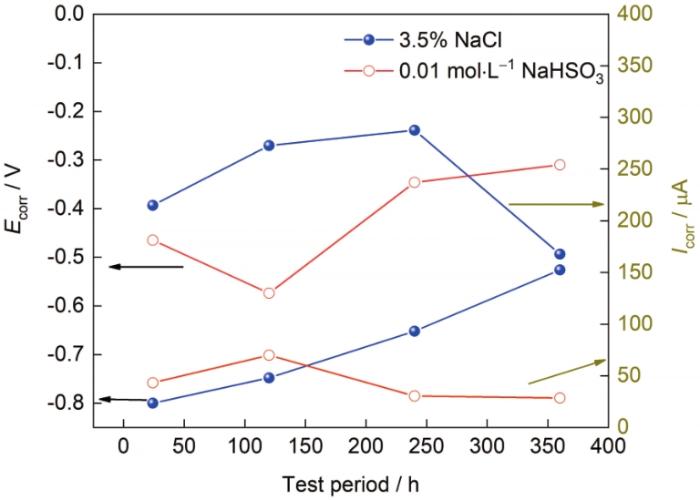
图5 G390NH在3.5%NaCl和0.01 mol/L NaHSO3溶液中极化曲线拟合自腐蚀电位(Ecorr)和自腐蚀电流(Icorr)的变化趋势
Fig.5 Polarization curves of G390NH in 3.5%NaCl and 0.01 mol/L NaHSO3 solution fits the change trend of Ecorr and Icorr
阴极:
NaCl溶液:
NaHSO3溶液:
阳极:
2.3 腐蚀形貌
图6所示为G390NH在3.5%NaCl和0.01 mol/L NaHSO3溶液中周浸实验后的宏观形貌。从图6a和e中可以看出,不同环境下试样均会在很短时间内首先形成一层均匀且致密的黑色锈层,没有较明显差别;到了第二周期120 h,在NaCl中性环境中试样(图6b)表面几乎被一层红色腐蚀产物所覆盖,但并不均匀、致密,对比在NaHSO3酸性环境中的试样(图6f),后者形成了一层黄色的锈层,且均匀覆盖整个表面。实验240 h后(图6c),NaCl溶液中的试样颜色逐渐加深,变为红褐色,且表面出现数个黑色凸起,另外由于试样在周浸实验中长期处于悬挂状态,干燥后的表面出现了明显的河流状痕迹,这也说明在Cl-中形成的腐蚀产物附着能力较差,容易发生溶解、流失,而在实验360 h后(图6d),试样表面颜色继续加深。试样在NaHSO3溶液中腐蚀240和360 h后(图6g和h)已经没有明显区别,表面锈层的颜色也已转变为红黑色,且非常致密、均匀,没有明显发生流失的痕迹。对比腐蚀后锈层的厚度,在酸性
图6
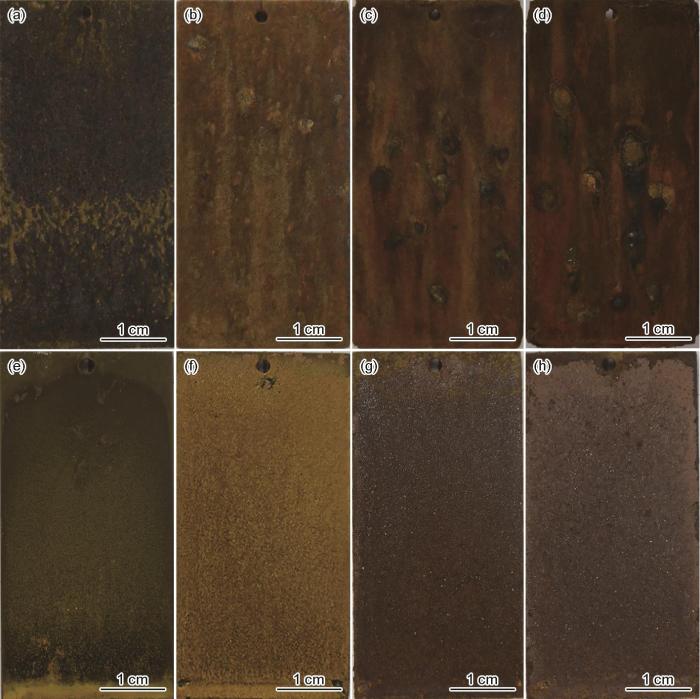
图6 G390NH在不同环境周浸实验后的腐蚀宏观形貌
Fig.6 Corrosion macromorphologies of G390NH in NaCl environment (a-d) and NaHSO3 environment (e-h) (a, e) 24 h (b, f) 120 h (c, g) 240 h (d, h) 360 h
图7所示为G390NH在3.5%NaCl和0.01 mol/L NaHSO3溶液中腐蚀后的微观形貌。在NaCl环境中,在腐蚀初期24 h后(图7a),样品表面覆盖尺寸不一的颗粒状产物;到了120 h后(图7b)表面已遍布一层较厚且密集的团簇状的产物,其中每个团簇由大量细小的针状物质所构成,且不同团簇间有较大空隙和裂纹;随着实验周期的增加(图7c和d),团簇体积不断变大,相互之间贴合也更加紧密。在NaHSO3溶液中,腐蚀24 h试样表面已经形成了一层致密的絮状产物层(图7e);随着腐蚀进行120 h后(图7f),产物逐渐转变成颗粒状,但粒径较小;随着实验周期的增加(图7g和h),颗粒逐渐变大,其之间逐渐结合,最终相互连接,锈层的孔隙尺寸和数量也明显减小。有研究表明这种针状的产物为γ-FeOOH,而颗粒状的产物更多是α-FeOOH[21,22],其中前者处于亚稳态,而后者的热力学稳定性更好[23]。
图7
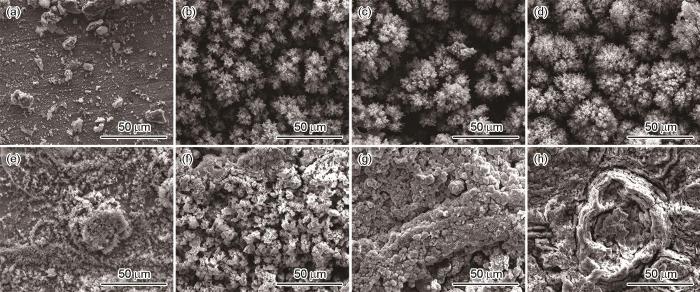
图7 G390NH在不同环境周浸实验后的腐蚀微观形貌
Fig.7 Corrosion microstructures of G390NH in NaCl environment (a-d) and NaHSO3 environment (e-h) (a, e) 24 h (b, f) 120 h (c, g) 240 h (d, h) 360 h
2.4 腐蚀产物及分布
图8所示为G390NH腐蚀360 h后的锈层截面形貌及元素分布,其中图8a和b分别为在NaCl环境中腐蚀360 h试样截面的低倍和高倍照片,而图8c是在NaHSO3环境中腐蚀的样品。可以看出,不同环境下内锈层与基体之间的结合非常紧密,其中NaCl环境中(图8b)的内锈层从形貌上看较为均匀,厚度在50 μm左右,但其内部存在着一定数量纵横交错的微裂纹;对于NaHSO3环境中(图8c)的内锈层,厚度在20~50 μm,与前者相比相差不大,可以明显看出其内部分布着与钢基体和锈层之间界面平行的纹路,这是在腐蚀过程中产物不断堆积所造成,同时也反映了产物在环境中溶解度较低且附着力较强的特点。对比图8a和c 2种环境下的外锈层,与内锈层之间均出现了剥离,这表明其已经对基体失去了保护作用,而且在周浸实验中,也会导致锈层间的水分无法在烘干阶段充分蒸发,进一步加大了潮湿时间;在NaCl溶液中腐蚀后形成的外锈层大约为800 μm,而NaHSO3环境中约为15 μm,2者厚度相差非常大,这也反映出前者腐蚀程度远高于后者。
图8
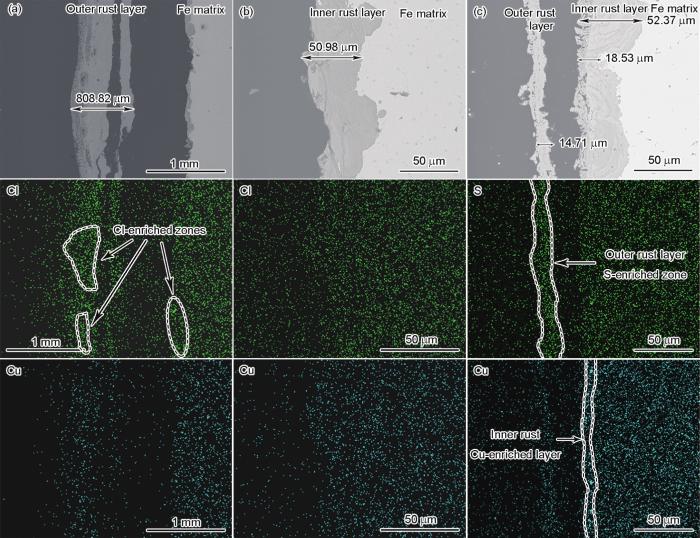
图8 G390NH腐蚀360 h锈层截面形貌及EDS面扫分析
Fig.8 Cross section morphologies and EDS mapping analyses of G390NH rust layer after 360 h corrosion (a, b) NaCl environment (c) NaHSO3 environment
进一步分析锈层中的元素分布,可以观察到图8a中G390NH的内外锈层均出现了Cl的富集区域,但并不连续,这表明Cl与材料的腐蚀密切相关,可以在内外锈层中随意分布和渗透,且并没有观察到有大量的耐蚀元素出现富集对其起到明显的阻隔效果;反观图8c仅有15 μm左右的外锈层成为了具有腐蚀性S元素的富集区域且均匀分布,并且在内锈层最外层区域形成了一层连续的Cu富集区。2种环境腐蚀后观察的结果说明了Cu无法在含Cl-环境中形成保护层,却可以在酸性
图9和10所示分别为G390NH在NaCl和NaHSO3环境中周浸实验后的腐蚀产物XRD测试结果,半定量分析结果分别如表3和4所示。其中由于NaHSO3环境中24 h试样产物过少,无法收集足够测试量,因此缺少此数据;而在该环境下120 h和NaCl环境中24 h试样表面产物也相对较少,且无法分离内外锈层,因此对其统一进行测试分析。
图9
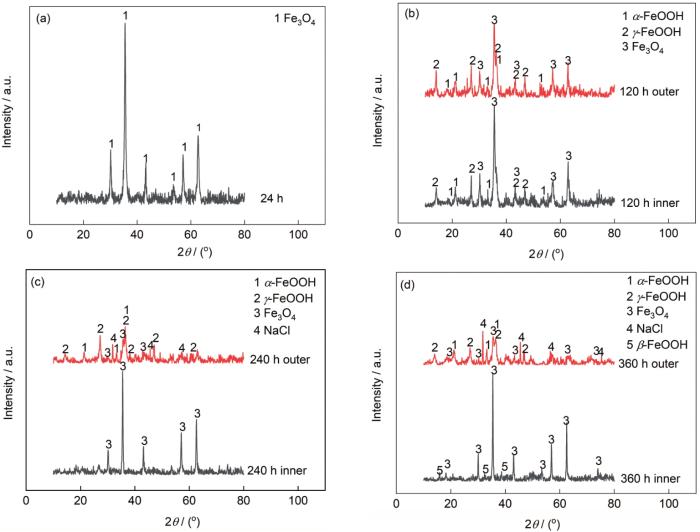
图9 3.5%NaCl环境中不同周期腐蚀产物XRD谱
Fig.9 XRD spectra of corrosion products in different periods in 3.5%NaCl environment
(a) 24 h (b) 120 h (c) 240 h (d) 360 h
图10
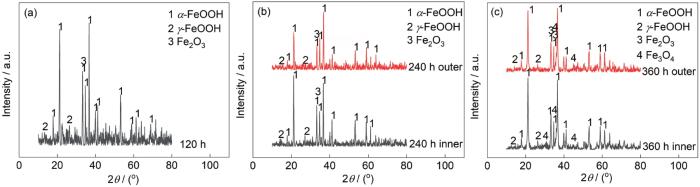
图10 0.01 mol/L NaHSO3环境中不同周期腐蚀产物XRD谱
Fig.10 XRD spectra of corrosion products in different periods in 0.01 mol/L NaHSO3 environment
(a) 120 h (b) 240 h (c) 360 h
表3 3.5%NaCl环境中不同周期腐蚀产物半定量分析结果
Table 3
Sample | Product analysis / (mass fraction, %) | α / γ | ||||
---|---|---|---|---|---|---|
α-FeOOH | γ-FeOOH | Fe3O4 | NaCl | β-FeOOH | ||
24 h | - | - | 100.0 | - | - | - |
120 h inner | 28.1 | 30.1 | 41.8 | - | - | 0.93 |
120 h outer | 35.0 | 44.5 | 20.5 | - | - | 0.79 |
240 h inner | - | - | 100.0 | - | - | - |
240 h outer | 32.0 | 43.3 | 9.8 | 14.9 | - | 0.74 |
360 h inner | - | - | 83.5 | - | 16.5 | - |
360 h outer | 37.0 | 28.6 | 10.8 | 23.6 | - | 1.29 |
表4 0.01 mol/L NaHSO3环境中不同周期腐蚀产物半定量分析结果
Table 4
Sample | Product analysis / (mass fraction, %) | α / γ | |||
---|---|---|---|---|---|
α-FeOOH | γ-FeOOH | Fe2O3 | Fe3O4 | ||
120 h | 80.0 | 5.6 | 14.4 | - | 14.29 |
240 h inner | 79.5 | 6.7 | 13.8 | - | 11.87 |
240 h outer | 79.8 | 7.7 | 12.6 | - | 10.36 |
360 h inner | 78.5 | 9.2 | - | 12.3 | 8.53 |
360 h outer | 77.9 | 8.8 | 9.9 | 3.4 | 8.85 |
图11为实验后G390NH各类腐蚀产物占比图。从半定量分析的结果可以看出,在NaCl环境中G390NH形成的腐蚀产物有α-FeOOH、γ-FeOOH、Fe3O4和β-FeOOH,其中内锈层的Fe3O4为主要腐蚀产物,外锈层主要为α-FeOOH、γ-FeOOH;而在NaHSO3环境中形成的锈层由α-FeOOH、γ-FeOOH、Fe2O3和Fe3O4构成,内外锈层中最主要的产物均为α-FeOOH。
图11

图11 G390NH各类腐蚀产物占比及α-FeOOH含量与γ-FeOOH含量之比(α / γ)
Fig.11 Proportions and α / γ values of G390NH corrosion products
在NaCl溶液中,初期腐蚀24 h的腐蚀产物几乎全部为黑色的Fe3O4,但腐蚀120 h的试样内、外锈层的产物均含有一定比例的α-FeOOH、γ-FeOOH和Fe3O4,区别仅为内锈层Fe3O4含量较多,而外锈层γ-FeOOH较多;实验腐蚀的中后期,240 h内锈层成分几乎均为Fe3O4,360 h时还出现了少量的β-FeOOH,外锈层之间没有明显区别,相比120 h试样Fe2O3比例不断减少,且随着实验进行锈层中出现了NaCl盐成分。
在NaHSO3溶液中,120、240和360 h形成的腐蚀产物中内、外锈层最主要的成分始终是α-FeOOH,且质量分数均保持在80%左右,但随着实验周期的增加,比例逐渐降低,γ-FeOOH不断增加,腐蚀前期主要是Fe2O3,后期从内锈层开始出现了少量的Fe3O4。
无定形态下的α-FeOOH常被认为是具有保护性锈层的主要成分。Hara等[24]在研究耐候钢锈层时将α-FeOOH含量与γ-FeOOH含量之比α / γ定义为锈层防护能力指数,Yamashita等[11]认定α / γ > 2是形成保护性锈层的必要条件。
对不同试样腐蚀产物α / γ的数值进行计算,结果见表3、4和图11。可以看出,在NaCl环境中α-FeOOH和γ-FeOOH往往集中在外锈层中,且α / γ值基本保持在1左右,整体呈增加趋势,但由于内锈层中没有聚集,因此从对基体的防护性能上来讲是较差的;NaHSO3溶液中试样内、外锈层的α / γ值均大于8,其中120和240 h试样大于10,呈减小趋势,但α / γ值远高于2,满足形成保护性锈层的条件,且α-FeOOH在锈层中所占比例基本没有明显减少,可以保证锈层的防护性能。
3 讨论
3.1 腐蚀机制对比
根据G390NH加速实验后的分析结果,对2种环境下的腐蚀机制进行研究。
在含有大量Cl-的环境中,G390NH的腐蚀速率在120 h前后达到峰值,之后便始终保持较高的腐蚀速率。众所周知,溶液中的Cl-是一个影响钢铁材料不断腐蚀的重要因素。由于Cl-体积较小,可以随溶液非常轻松穿透钢表面的锈层,并接触到基体[25]。在此过程中,由于其自身带负电,因此对于电荷的传递具有明显的优势。这也在极化曲线的测试中(图4a)可以看出,每个周期的阴极段并没有明显的改变,始终保持较高的电流密度,说明其中的锈层对Cl-及其他腐蚀介质并没有良好的阻碍效果。
从另一个角度来看,内锈层的截面存在着一定数量的裂纹,与
对于在酸性
综上所述,G390NH不管在Cl-还是酸性
3.2 腐蚀产物的演化
针对G390NH在NaCl和NaHSO3 2种不同环境中的腐蚀机制,分别分析和推导腐蚀产物的演化过程。
在NaCl溶液中,最初金属暴露于腐蚀介质中,首先会发生溶解,在溶液中基体附近形成少量的Fe2+:
溶于液体并呈现离子状态的Fe2+与Cl-发生作用:
Fe(OH)2发生电离后的Fe(OH)+将继续与O2发生反应:
最初在表面生成的FeOOH,由于无法牢固吸附在合金基体上,且较为不稳定,易与溶液中的Fe2+发生反应,在合金表面形成附着能力较好的Fe3O4:
对于腐蚀产物中形成的FeOOH,在检测结果中更多的是γ-FeOOH,仅有少部分是α-FeOOH和β-FeOOH,其中后者是仅在Cl-的作用下才能形成的产物[11]。
根据腐蚀产物分布及演化的过程,可以认为在最初合金发生腐蚀形成少量的FeOOH,但很快FeOOH与溶液中的Fe2+发生反应生成了与基体结合能力较好的Fe3O4。一段时间后,当基体表面几乎被黑色的Fe3O4所包裹后,FeOOH也开始在其外侧不断积累。起初较为稀疏和松散,在周浸实验悬挂过程中出现流失,但当其累积达到一定厚度时,合金表面就会形成明显的双锈层。此时,内层主要是Fe3O4与基体接触,外层主要是FeOOH与外界腐蚀介质直接接触。在周浸实验中,试样大部分时间在溶液中浸泡,此时内外锈层均保持全湿润状态,但在非浸泡的湿热阶段,由于环境温度较高外层产物中的水分会大量蒸发,而靠基体的内部则仍然可以保持湿润的状态,这将是内外锈层在腐蚀过程中环境条件存在的最大区别。
根据Evans和Taylor[29]的研究可以推断,在实验中浸泡与湿热两阶段存在着不同的化学反应。
浸泡阶段(完全湿润,且O2浓度低):
阳极反应发生在Fe和Fe3O4的界面上:
阴极反应发生在Fe3O4和FeOOH的界面上:
湿热阶段(外层湿度下降,但O2浓度上升):
O2穿过外锈层,反应发生在Fe3O4和FeOOH的界面上:
这说明了更多水分促使Fe不断生成新的Fe3O4,而FeOOH的形成则需要接触更多的O2。综合来看,在干湿交替的过程中加速了腐蚀的进行。Misawa等[2,30]在研究中发现了多次的干湿交替会使部分的γ-FeOOH转变为更加稳定的α-FeOOH,但实验中也发现其并非集中在内锈层,因此并不会对阻碍腐蚀的发生起到很好的作用。
对于材料在NaHSO3溶液中的腐蚀,起初
而
随后,FeSO4发生水解,再次形成H2SO4和羟基化合物:
此时整个腐蚀过程已构成循环,在这种循环过程中可以持续产生H2SO4[32],既作反应物又作产物,加速了腐蚀的发生。根据测试结果来看,产物FeOOH中绝大部分为α-FeOOH,而γ-FeOOH只占了一小部分。
另外在该过程存在钢中Cu的溶解,但由于内锈层物质流失小,使得溶解的Cu重新与锈层结合,在内锈层外层形成富Cu区域。Cu的存在可以促进溶解的Fe2+或Fe(Ⅱ)配合物转变为无定形的氢氧化物以及纳米尺寸的α-FeOOH[33,34],这将主要构成致密、无裂纹的内锈层。对于结合并不紧密的外锈层而言,Misawa等[15]从溶液化学角度提出,外锈层中首先沉淀出的铁锈是γ-FeOOH,后因环境中SO2等的存在使钢铁表面酸化,导致γ-FeOOH溶解,随后沉淀出无定型铁锈FeO x (OH)3 - 2x,这种铁锈经时效转变为α-FeOOH,最终形成的成分与内锈层差别较小。
随着腐蚀的不断进行,在酸性
4 结论
(1) G390NH在NaHSO3环境中表现出优异的耐蚀性能,呈现典型的耐候钢特性,腐蚀速率随时间延长而明显降低;而在NaCl环境中耐蚀性显著降低,腐蚀稳定后仍以较高的速率进行,且在Cl-环境中速率约为酸性
(2) 不同环境影响G390NH形成的腐蚀产物存在较大差别,在酸性
(3) 不同环境中的腐蚀机制也相差较大,在酸性